The Synthesis of Transition Metal Silicide and Germanide Nanostructures Within the Solution- Based Solvent Vapour Growth System
Total Page:16
File Type:pdf, Size:1020Kb
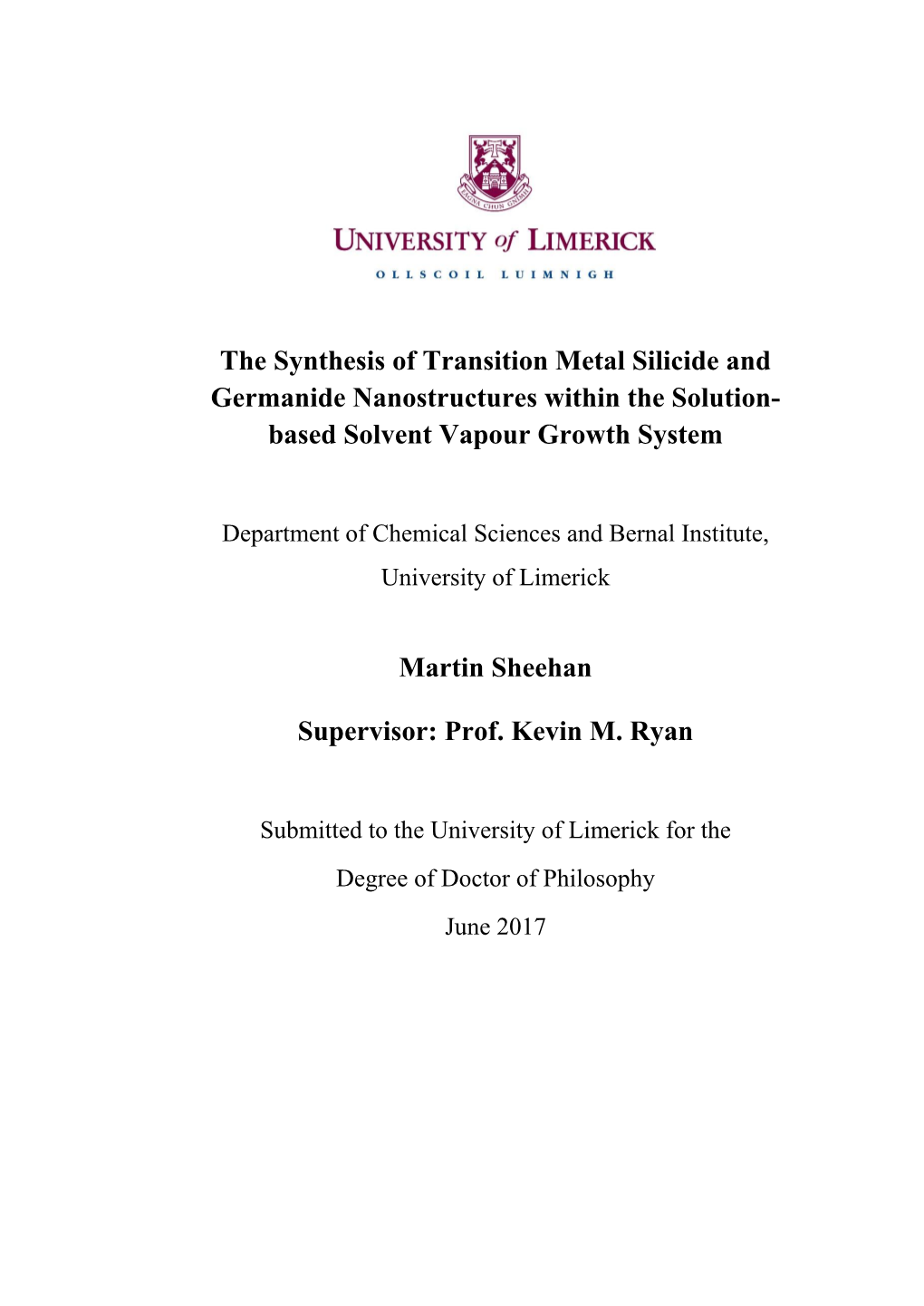
Load more
Recommended publications
-
Structural and Dynamical Trends in Alkali-Metal
Article pubs.acs.org/JPCC Structural and Dynamical Trends in Alkali-Metal Silanides Characterized by Neutron-Scattering Methods † ‡ † § ∥ † ∥ Wan Si Tang,*, , Mirjana Dimitrievska,*, , Jean-Noel̈ Chotard, Wei Zhou, Raphael̈ Janot, ⊥ † Alexander V. Skripov, and Terrence J. Udovic † NIST Center for Neutron Research, National Institute of Standards and Technology, Gaithersburg, Maryland 20899-6102, United States ‡ Department of Materials Science and Engineering, University of Maryland, College Park, Maryland 20742-2115, United States § National Renewable Energy Laboratory, Golden, Colorado 80401, United States ∥ Laboratoire de Reactivité ́et Chimie des Solides (LRCS), UMR 7314 CNRS, Universitéde Picardie Jules Verne, 33 rue Saint-Leu, 80039 Amiens Cedex, France ⊥ Institute of Metal Physics, Ural Branch of the Russian Academy of Sciences, Ekaterinburg 620990, Russia *S Supporting Information ABSTRACT: Structural, vibrational, and dynamical properties of the mono- and mixed-alkali silanides (MSiH3, where M = K, Rb, Cs, K0.5Rb0.5,K0.5Cs0.5, and Rb0.5Cs0.5) were investigated by various neutron experiments, including neutron powder diffraction (NPD), neutron vibrational spectroscopy (NVS), neutron- scattering fixed-window scans (FWSs), and quasielastic neutron scattering (QENS) measurements. Structural characterization showed that the mixed compounds exhibit disordered (α) and ordered (β) phases for temperatures above and below about 200− 250 K, respectively, in agreement with their monoalkali correspondents. Vibrational and dynamical properties are strongly influenced by the cation environment; in particular, there is a red shift in the band energies of the librational and bending modes with increasing lattice size as a result of changes in the bond lengths and force constants. Additionally, slightly broader spectral features are observed in the case of the mixed compounds, indicating the presence of structural disorder caused by the random distribution of the alkali-metal cations within the lattice. -
Doping Effects on Transition-Metal Silicides: Crystal Structures and Physical Properties of Aluminium Doped Rhenium Silicide
BearWorks MSU Graduate Theses Summer 2020 Doping Effects on Transition-Metal Silicides: Crystal Structures and Physical Properties of Aluminium Doped Rhenium Silicide Victoria DeCocq Missouri State University, [email protected] As with any intellectual project, the content and views expressed in this thesis may be considered objectionable by some readers. However, this student-scholar’s work has been judged to have academic value by the student’s thesis committee members trained in the discipline. The content and views expressed in this thesis are those of the student-scholar and are not endorsed by Missouri State University, its Graduate College, or its employees. Follow this and additional works at: https://bearworks.missouristate.edu/theses Part of the Inorganic Chemistry Commons, and the Materials Chemistry Commons Recommended Citation DeCocq, Victoria, "Doping Effects on Transition-Metal Silicides: Crystal Structures and Physical Properties of Aluminium Doped Rhenium Silicide" (2020). MSU Graduate Theses. 3563. https://bearworks.missouristate.edu/theses/3563 This article or document was made available through BearWorks, the institutional repository of Missouri State University. The work contained in it may be protected by copyright and require permission of the copyright holder for reuse or redistribution. For more information, please contact [email protected]. DOPING EFFECTS ON TRANSITION-METAL SILICIDES: CRYSTAL STRUCTURES AND PHYSICAL PROPERTIES OF ALUMINIUM DOPED RHENIUM SILICIDE A Master’s Thesis -
Appendix a of Final Environmental Impact Statement for a Geologic Repository for the Disposal of Spent Nuclear Fuel and High-Lev
Appendix A Inventory and Characteristics of Spent Nuclear Fuel, High-Level Radioactive Waste, and Other Materials Inventory and Characteristics of Spent Nuclear Fuel, High-Level Radioactive Waste, and Other Materials TABLE OF CONTENTS Section Page A. Inventory and Characteristics of Spent Nuclear Fuel, High-Level Radioactive Waste, and Other Materials ................................................................................................................................. A-1 A.1 Introduction .............................................................................................................................. A-1 A.1.1 Inventory Data Summary .................................................................................................... A-2 A.1.1.1 Sources ......................................................................................................................... A-2 A.1.1.2 Present Storage and Generation Status ........................................................................ A-4 A.1.1.3 Final Waste Form ......................................................................................................... A-6 A.1.1.4 Waste Characteristics ................................................................................................... A-6 A.1.1.4.1 Mass and Volume ................................................................................................. A-6 A.1.1.4.2 Radionuclide Inventories ...................................................................................... A-8 A.1.1.4.3 -
Low Temperature Chemical Vapor Deposition and Method for Depositing a Tungsten Silicide Film with Improved Uniformity and Reduced Fluorine Concentration
Europaisches Patentamt 19 European Patent Office Office europeen des brevets © Publication number : 0 591 086 A2 12 EUROPEAN PATENT APPLICATION © Application number : 93480132.5 © int. ci.5: H01L 21/3205, C23C 16/44, C23C 16/42, H01L 21/285 @ Date of filing : 10.09.93 The application is published incomplete as filed @ Inventor : Gow, Thomas Richard (Article 93 (2) EPC). The points in the 4 Lyman Drive description at which the omission obviously Williston, VT 05495 (US) occurs have been left blank. Inventor : Lebel, Richard John Box 2255A RD1 © Priority : 30.09.92 US 954783 Sheldon, VT 05483 (US) @ Date of publication of application : @ Representative : Klein, Daniel Jacques Henri 06.04.94 Bulletin 94/14 Compagnie IBM France Departement de Propriete Intellectuelle @ Designated Contracting States : F-06610 La Gaude (FR) DE FR GB © Applicant : International Business Machines Corporation Old Orchard Road Armonk, N.Y. 10504 (US) © Low temperature chemical vapor deposition and method for depositing a tungsten silicide film with improved uniformity and reduced fluorine concentration. © A tungsten silicide (WSix) film is formed by GROWTH RATE ( mg/m i n ) chemical vapor deposition using the reduction of tungsten hexafluoride (WF6) with dichlorosi- O — ro lane (SiH2CI2) referred to as DCS and a reduc- ing agent comprising silane (SiH4), hydrogen, or a mixture thereof. According to the method of the present invention, the WSix film is formed in a CVD reactor operating at a low pressure and at a wafer temperature between about 300 and 550°C. In the preferred embodiment, a thin nucleation layer is deposited before the WSix film. -
Tailoring of Transition Metal Silicides As Protective Thin Films On
THESIS FOR THE DEGREE OF DOCTOR OF PHILOSOPHY Tailoring of Transition Metal Silicides as Protective Thin Films on Austenitic Stainless Steel PUI LAM TAM Department of Materials and Manufacturing Technology CHALMERS UNIVERSITY OF TECHNOLOGY Gothenburg, Sweden 2011 Tailoring of Transition Metal Silicides as Protective Thin Films on Austenitic Stainless Steel PUI LAM TAM ISBN 978-91-7385-560-0 © PUI LAM TAM 2011 Doktorsavhandlingar vid Chalmers tekniska högskola Ny series nr 3241 ISSN 0346-718X Department of Materials and Manufacturing Technology Chalmers University of Technology SE-412 96 Gothenburg Sweden Tel: +46 (0)31-772 1000 Fax: +46 (0)31-772 1310 www.chalmers.se Printed by Chalmers Reproservice Göteborg, Sweden 2011 Abstract Transition metal silicide is an important material used in microelectronic devices and a possible candidate for high temperature application. The objective of this study is trying to make use of this material in a new way as protective thin films on engineering materials. The brittle nature of the silicides can thus be compensated by the ductile bulk material and the surface corrosion resistance can be improved. The choices of thin film constituents are targeted at the transition metal elements including titanium (Ti, Z = 22), chromium (Cr, Z = 24), iron (Fe, Z = 26) and nickel (Ni, Z = 28) in combination with silicon (Si, Z = 14) to form the binary-component intermetallic compounds by means of ion-beam sputter deposition, which was carried out in an ultrahigh vacuum (UHV) chamber at 10 -6 Pa. The chosen substrate material is AISI 304 stainless steel. Thin film characterisations were conducted by means of surface analysing instruments: X-ray photoelectron spectrometer (XPS) and grazing incidence X-ray diffractometer (GIXRD). -
The Mechanism Behind the Calcium Aluminum Silicide Ternary Structural Preference and the Origin of Its Semimetal Behavior
THE MECHANISM BEHIND THE CALCIUM ALUMINUM SILICIDE TERNARY STRUCTURAL PREFERENCE AND THE ORIGIN OF ITS SEMIMETAL BEHAVIOR by Torey Elizabeth Semi A thesis submitted to the Faculty and the Board of Trustees of the Colorado School of Mines in partial fulfillment of the requirements for the degree of Doctor of Philosophy (Applied Physics). Golden, Colorado Date Signed: Torey Elizabeth Semi Signed: D.M. Wood Thesis Advisor Golden, Colorado Date Signed: Dr. Thomas Furtak Professor and Head Department of Engineering ii ABSTRACT CaAl2Si2 is the prototype of the CaAl2Si2 class of Zintl structures established to be useful as thermoelectrics. We propose that CaAl2Si2 be interpreted as an ordinary covalently bonded, tetrahedrally coordinated quasi-semiconductor consisting of a large distortion of the wurtzite structure with the almost fully ionized Ca inserted at an interstitial site. We support this interpretation via a structural mapping and calculations for both a charged binary primitive cell and a Si4 primitive cell. Our intent is to explain the unusual structure of the CaAl2Si2 class of semiconductors, the origin of its semimetallic behavior, the basis for its stability and the effect of substituting other column II atoms for Ca on these properties. To be clear, this work does not examine the nature of the true band gap, or the transport coefficients of CaAl2Si2. GW corrections are not discussed, in view of the focus on the origins of stability of this peculiar structure. iii TABLE OF CONTENTS ABSTRACT . iii LIST OF FIGURES . vi LIST OF TABLES . xi ACKNOWLEDGMENTS . xii CHAPTER 1 INTRODUCTION . 1 1.1 Thermoelectric Materials . 2 1.2 Thermoelectric Efficiency . -
Critical Issues in the Heteroepitaxial Growth of Alkaline-Earth Oxides on Silicon J
Critical issues in the heteroepitaxial growth of alkaline-earth oxides on silicon J. Lettieri, J. H. Haeni, and D. G. Schlom Citation: Journal of Vacuum Science & Technology A 20, 1332 (2002); doi: 10.1116/1.1482710 View online: http://dx.doi.org/10.1116/1.1482710 View Table of Contents: http://scitation.aip.org/content/avs/journal/jvsta/20/4?ver=pdfcov Published by the AVS: Science & Technology of Materials, Interfaces, and Processing Articles you may be interested in Theoretical investigation of the alkaline-earth dihydrides from relativistic all-electron, pseudopotential, and density-functional study J. Chem. Phys. 126, 104307 (2007); 10.1063/1.2437213 Interface formation during molecular beam epitaxial growth of neodymium oxide on silicon J. Appl. Phys. 99, 074105 (2006); 10.1063/1.2188051 Hetero-epitaxy of perovskite oxides on GaAs ( 001 ) by molecular beam epitaxy Appl. Phys. Lett. 85, 1217 (2004); 10.1063/1.1783016 In situ observation of epitaxial growth of [Au/Co/Cu] and [Cu/Co/Au] superlattices and their magnetic interface anisotropies J. Appl. Phys. 90, 5104 (2001); 10.1063/1.1413230 Stranski-Krastanov growth of Al on Cr layers during molecular-beam epitaxial growth and its influence on the structure of epitaxial (001) Al/Cr superlattices J. Appl. Phys. 87, 159 (2000); 10.1063/1.371838 Redistribution subject to AVS license or copyright; see http://scitation.aip.org/termsconditions. Download to IP: 128.84.143.26 On: Tue, 16 Jun 2015 17:57:48 Critical issues in the heteroepitaxial growth of alkaline-earth oxides on silicon J. Lettieri, J. H. Haeni, and D. -
Dissolution and Clarification of Rertr Silicide Fuels*
DISSOLUTION AND CLARIFICATION OF RERTR SILICIDE FUELS* George C. Rodrigues E. 1. du Pont de Nemours Co. Savannah River Laboratory Aiken, SC 29808 XA04C1501 Abstract SRP may reprocess spent REM fuel as early as FY-85. Candidate RERTR fuels include uranium oxides, aluminides, and sicides. Much less is known about the behavior of uranium sicides during Purex reprocessing than either uranium oxides or aluminides. Studies were performed at SRL with RERTR silicide fuels to ensure their reprocessability. The results of dis- solution and head-end clarification studies with both unirradiated and irradiated fuel are presented. Introduction Highly enriched uranium fuels from a number of foreign and domestic research and test reactors are currently reprocessed at the Department of Energy's (DOE) Savannah River Plant (SRP). The objective of the Reduced Enrichment Research and Test Reactor (RERTR) program is to demonstrate on- version of these reactors to low enriched uranium (LEU) fuels to reduce the potential for diversion of highly enriched uranium. Ideally, this conver- sion should be accomplished without changing the fuel configuration or de- grading reactor performance. Conversion to LEU under these constraints requires that the new fuel elements contain up to 41/2 times as much total uranium. Advanced powder metallurgy fabrication techniques utilizing high density oxides, aluminides, and sicides should produce reliable fuels with uranium loadings in the desired range. Candidate silicide intermetallic compounds are U3Si, U3Si2, and U3SiAl. While a good deal is known about reprocessing oxides and aluminidesl,2, information on reprocessing sicides is limited and dissolution of some uranium sicides has proven difficult. In addition, dissolved silicon can disrupt solvent extraction2j3. -
Formation of Gems and Precious Stones from Cheap and Plentiful Materials, and Other Somewhat Sensational Operations Which Had A
A4 PaAer firesenteed at lie 162d Meeti g of the Amzerican Institute of Electrical E-ngineers at Nez York, February 2&ti 1Q902. THE ELECTRIC FURNACE IN INDUSTRIAL CHEMISTRY. BY CHARLES B. JACOBS. In its early days the electric furnace labored under the burden of the prophecies of its wonderful possibilities and products, and seems to have been more or less associated in the popular mind with the production of diamonds from amorphous carbon, the formation of gems and precious stones from cheap and plentiful materials, and other somewhat sensational operations which had a tendency to obscure, for a time, the knowledge of its useful- ness in the field of industrial chemistry. Notwithstanding the fact that DeChalmot, the Cowles brothers and others, had been operating the electric furnace for some years in the production of alloys from very refractory ores, it was not until Acheson produced carbide of silicon, Willson obtained carbide of calcium in commercial quantities, and Moissan pub- lishbd his scientific investigations in Le Four Electrique, that the value of the electric furnace for the production of substances use- ful in the arts began to be generally recognized. Since that time, however, its field of usefulness has been steadily increasing until it is now obtaining recognition as an im- portant factor in industrial chemistry. Reference to the patent lists of the various countries will show an immense variety of electric furnaces, but they may all be classified under three general types which have been modified in numerous ways to meet the special requirements of the var- ious processes for which they are intended. -
BLABER- a Review of the Optical Properties of Alloys and Intermetallics for Plasmonics
A review of the optical properties of alloys and intermetallics for plasmonics M G Blaber, M D Arnold and M J Ford* Institute for Nanoscale Technology, Department of Physics and Advanced Materials, University of Technology Sydney, PO Box 123, Broadway, NSW 2007, Australia *[email protected] Abstract. Alternative materials are required to enhance the efficacy of plasmonic devices. We discuss the optical properties of a number of alloys, doped metals, intermetallics, silicides, metallic glasses and high pressure materials. We conclude that due to the probability of low frequency interband transitions, materials with partially occupied d-states perform poorly as plasmonic materials, ruling out many alloys, intermetallics and silicides as viable. The increased probability of electron-electron and electron-phonon scattering rules out many doped and glassy metals. Contents 1. Introduction 2. Plasmonic Materials: Definition and review of metals 2.1 Quality factors and the ideal plasmonic material 2.2 A review of the optical properties of metals 3. Alloys 3.1 Noble metal alloys 3.2 Transition metal alloys 4. Intermetallics 4.1 Alkali metal binary intermetallics 4.2 Noble metal binary intermetallics 4.3 Group 13 binary intermetallics 4.4 Other binary intermetallics 4.5 Ternary Intermetallics 5. Silicides 6. High pressure materials 7. Liquid metals and glassy/amorphous materials 7.1 Liquid Metals 7.2 Metallic Glasses and amorphous alloys 1. Introduction As nanofabrication techniques become increasingly fast and accurate, the performance of plasmonic systems relies less and less on structure fabrication and more on the fundamental limitations of the underlying materials. Plasmonics has seen an exponential growth, due mainly to the sheer diversity of applications, from optical cloaking [1] to superlensing [melville2005, pendry2000] as well as single molecule surface enhanced raman spectroscopy [2], parasite therapy [3] and optical circuits[4] with high speed optical switching[5, 6]. -
UNITED STATES PATENT OFFICE Augustus F
Patented Jan. 27, 1931 1790,552 UNITED STATES PATENT OFFICE AUGUSTUs F. MEEHAN, OF CHATTANOOGA, TENNESSEE, ASSIGNOR TO MEEHANITE METAL CORPORATION, OF CHATTANOOGA, TENNESSEE, A CORPORATION OF TEN NESSEE ATLOY FOR MANUEFACTURE OF CAST IRON NoDrawing. Application filed August 39, 1928. Serial No. 303,889. The present invention relates to the treat produce a casting containing approximately ment of metals, and, more particularly, to 3% of combined carbon, and even in iron the treatment of molten metal in the manu containing less than 1% of combined carbon. facture of castings. By the statement that the silicide is sub 5 An object of the invention is to provide a stantially free from iron, is meant that the 55 process for the manufacture of castings of iron content of the treating agent or alloy special strength and uniformity, such as will is relatively inconsiderable. insure the quality sought in the finished cast I have also found that in the production of S. castings, the silicide agent may be accom O fretofore, when deemed essential, it has panied to advantage by a second alkaline 60 been the practice in the manufacture of grey earth metal, such as magnesium, strontium, iron castings to add to the molten metalia barium, etc. For example, an alloy agent of suitable agent in order to obtain the carbon in calcium, silicon and an inconsiderable the desired forms. amount of iron may also include to advan 5 In the breaking down of the iron carbide tage either magnesium or strontium or bari 65 in the metal during solidification, ferro-sili um, etc. -
Overview of Properties and Performance of Uranium-Silicide Compounds for Light Water Reactor Applications
Appendix 11: Oxidation Tests on U3Si2, UN and UO2 Pellets in Synthetic Air LWR Accident Tolerant Fuels—II 987 Overview of Properties and Performance of Uranium-Silicide Compounds for Light Water Reactor Applications A.T. Nelson, J.T. White, D.D. Byler, J.T. Dunwoody, J.A. Valdez and K.J. McClellan Los Alamos National Laboratory P.O. Box 1667 Los Alamos, NM, 87545 [email protected] INTRODUCTION focused on a more critical evaluation of their thermophysical properties to temperatures near their The uranium-silicon binary system possesses a range melting points. These compounds have seen limited of compounds that have been historically investigated and characterization at temperatures low relative to those utilized to a limited extent as nuclear reactor fuels. Of the anticipated of an LWR fuel, but even here appreciable multiple compounds, U3Si and U3Si2 are most familiar; scatter is present [2]. Lesser-studied compounds such as their high uranium densities have made them an intriguing USi and U3Si5 have received virtually no attention from choice for incorporation into composite plate fuels in previous researchers regarding their thermal conductivity, research reactors and other low power core redesigns heat capacity, and thermal expansion as a function of where retained neutronic performance was desired at temperature. Accurate knowledge of these properties is lower enrichments [1]. This increased uranium density essential to modeling of heat transport in reactor systems. compared with uranium dioxide (UO2) has made them The renewed focus on accident tolerance has also attractive to a new generation of nuclear fuels research emphasized consideration of the off-normal performance driven by the renewed push for accident-tolerant light of materials in nuclear reactor systems.