Reims Cessna F150M, G-BDZC No & Type of Engines
Total Page:16
File Type:pdf, Size:1020Kb
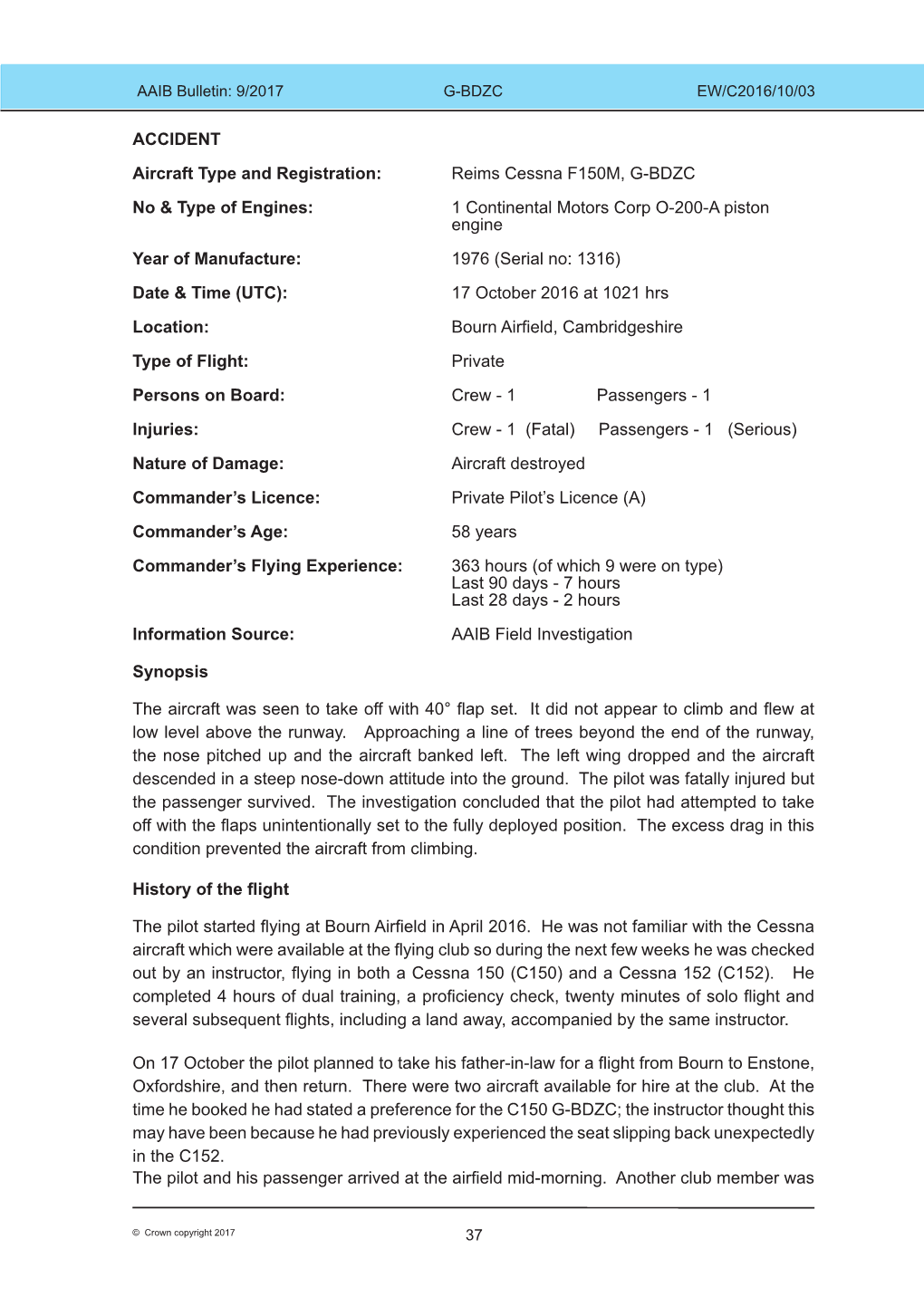
Load more
Recommended publications
-
NTSB/AAB-88/11 I PB88-916911 4 Ai~~~Kfta'a~C1'tfeti~T\N-Iefs - Brief Format U.S
JACK R. HUNT MEMORIAL LIBRARY DAYTONA BEACH, FLORIDA 32014 • 904-239-6595 TECHNICAL REPORT DOCUMENTATION PAGE 1. Report No. 2.Government Accession No. 3.Recipient's Catalog No. NTSB/AAB-88/11 I PB88-916911 4 Ai~~~kfta'A~c1'tfeti~t\n-iefs - Brief Format U.S. Civil and Foreign Aviation 1987 - 7 6.Performing Organization Calendar Year Issue Number Code 7. Author(s) 8.Performing Organization Report No. 9 Perforro.ir.LQ Qr~a.nizatiDn Name and Address 10.Work Unit No. 8ureau or tie1cruperat1ons National Transportation Safety Board Washington, D.C. 20594 11 .Contract or Grant No. 13.Type of Report and Apprbk~~at%~yr~o General 12.Sponsoring Agency Name and Address Aviation and Air Carrier Accidents Occurring in NATIONAL TRANSPORTATION SAFETY BOARD 1987 in Brief Format Washington, D. C. 20594 14.Sponsoring Agency Code 15.Supplementary Notes 16.Abstract This publication contains selected aircraft accident reports in Brief Format occurring in U.S. civil and foreign aviation operations during Calendar Year 1987. Approximately 200 General Aviation and Air Carrier accidents contai.ned in this publication represent a random selection. This publication is issued irregularly, normally eighteen times each year. The Brief Format represents the facts, conditions, circumstances and probable cause(s) for each accident. File Numbers: 1201 through 1400 17.Key Words 18.Distribution Statement Aviation accident, probable cause, findings, This document is available certificate/rating, injuries, type of accident, type to the public through the operating certificate, flight conducted under, National Technical Infor accident occurred during, aircraft damage, basic mation Service, Spring weather field, Virginia 22161 19.Security Classification 20.Security Classification 21 .No. -
Government Gazette Republic of Namibia
GOVERNMENT GAZETTE OF THE REPUBLIC OF NAMIBIA N$1.56 WINDHOEK- 31 January 1996 No. 1253 CONTENTS Page APPLICATION TO OPERATE AIR SERVICES......................... 1 APPLICATION TO OPERATE AIR SERVICES The following applications for Scheduled Air Transport Services, Non-sched uled Air Transport Services, Flying Training Air Services or Aerial Work Air Services indicate ( 1) reference number; (2) name of applicant and nature of application; (3) number and type of aircraft; (4) nature of proposed air service; and (5) routes over or area within which the proposed air services are to be rendered and are published in terms of section 5 of the Air Services Act, 1949 (Act 51 of 1949) as amended . Representations by interested parties in respect of the applications shall comply with the requirements of section 6 of the Air Services Act, 1949 (Act 51 of 1949) and shall be in ninefold in respect of each - application and shall be delivered by hand or sent by registered post to the ··- Secretary, Transport Commission of Namibia, Private Bag X12005, Windhoek to reach that office not later than 21 days after the date of publication of this Government Gazette . ,,• 2 Government Gazette 31 January 1996 No. 1253 WINDHOEK (1) 07/12/95 OOA00113 (2) KALAHARI EXPRESS AIRLINES -Application for a scheduled air transport service licence. (3) Two Fokker F28 Twin Engined Fan Jet (55 Seater) (4) Types of traffic to be conveyed: Passengers and their personal effects and fast freight. See Annexure D. (5) Area to be served: Namibia and Republic of South Africa. Routes and towns to be served: Windhoek (Eros)- Johannesburg International Airport. -
Aluminum Propeller Applications
SENSENICH FIXED-PITCH ALUMINUM PROPELLERS INSTALLATION GUIDE One attaching kit is furnished with each propeller. An attaching kit for the flanged shaft will be supplied for all installations unless otherwise specified. Tapered shaft installation must be specified. When ordering for Lycoming O-145 installation, specifiy 74CKL attaching kit. STATIC RPM MIN. DIA. AIRCRAFT ENGINE STANDARD CLIMB CRUISE DIAMETER LIMITS FOR REPAIR NOTES Aero Commander 100 Lycoming O-320 /150 74DM6-0-60 74 inches Aeronca 11AC Continental A-65 / 65 74CK-0-46 74 inches 2100-2250 72.5 inches 1 Aeronca 11BC Continental C-85 / 85 74CK-2-46 72 inches 2160-2380 70 inches 1 Aeronca 11CC Continental C-85 / 85 74CK-2-46 72 inches 2300-2465 70 inches 1 Aeronca 15AC Continental C-145-D 74DR-0-52 74DR-0-54 74 inches 2240-2490 72 inches Aeronca 65TAC, L3, O58, YO58 Continental A-65 / 65 74CK-0-46 74CK-0-44 74 inches 2050-2250 72 inches 1 Aeronca 65TL, 65LA, 65LB, 65TAL Lycoming O-145-B 74CK-2-36 72 inches 2250-2550 68 inches 2 Aeronca S11AC Continental A-65 / 65 74CK-0-40 74 inches 2070-2170 72.5 inches 1 Aeronca S11BC Continental C-85 / 85 74CK-2-40 72 inches 2280-2380 70 inches 1 Aeronca S11CC Continental C-85 / 85 74CK-2-40 72 inches 2300-2465 70 inches 1 Aeronca S15AC Continental C-145 74DR-0-48 74 inches 2380-2540 72 inches Aeronca S65TC, SO-58D Continental A-65 / 65 74CK-0-40 74 inches 2050-2250 72 inches 1 American General AG-5B Lycoming O-360 /180 76EM8S10-0-63 76EM8S10-0-61 76EM8S10-0-65 76 inches 76 inches Avions Pierre Robin DR400 / 118 Lycoming O-235-L2C 72CKS6-0-56 -
Name of Plan Wing Span Details Source Area Price Ama Ff Cl Ot Scale Gas Rubber Electric Other Glider 3 View Engine Red. Ot C
WING NAME OF PLAN DETAILS SOURCE AREA PRICE AMA POND RC FF CL OT SCALE GAS RUBBER ELECTRIC OTHER GLIDER 3 VIEW ENGINE RED. OT SPAN COMET MODEL AIRPLANE CO. 7D4 X X C 1 PURSUIT 15 3 $ 4.00 33199 C 1 PURSUIT FLYING ACES CLUB FINEMAN 80B5 X X 15 3 $ 4.00 30519 (NEW) MODEL AIRPLANE NEWS 1/69, 90C3 X X C 47 PROFILE 35 SCHAAF 5 $ 7.00 31244 X WALT MOONEY 14F7 X X X C A B MINICAB 20 3 $ 4.00 21346 C L W CURLEW BRITISH MAGAZINE 6D6 X X X 15 2 $ 3.00 20416 T 1 POPULAR AVIATION 9/28, POND 40E5 X X C MODEL 24 4 $ 5.00 24542 C P SPECIAL $ - 34697 RD121 X MODEL AIRPLANE NEWS 4/42, 8A6 X X C RAIDER 68 LATORRE 21 $ 23.00 20519 X AEROMODELLO 42D3 X C S A 1 38 9 $ 12.00 32805 C.A.B. GY 20 BY WALT MOONEY X X X 20 4 $ 6.00 36265 MINICAB C.W. SKY FLYER PLAN 15G3 X X HELLDIVER 02 15 4 $ 5.00 35529 C2 (INC C130 H PLAMER PLAN X X X 133 90 $ 122.00 50587 X HERCULES QUIET & ELECTRIC FLIGHT INT., X CABBIE 38 5/06 6 $ 9.00 50413 CABIN AEROMODELLER PLAN 8/41, 35F5 X X 20 4 $ 5.00 23940 BIPLANE DOWNES CABIN THE OAKLAND TRIBUNE 68B3 X X 20 3 $ 4.00 29091 COMMERCIAL NEWSPAPER 1931 Indoor Miller’s record-holding Dec. 1979 X Cabin Fever: 40 Manhattan Cabin. -
Shooting Down Civilian Aircraft: Is There an International Law Brian E
Journal of Air Law and Commerce Volume 72 | Issue 3 Article 10 2007 Shooting down Civilian Aircraft: Is There an International Law Brian E. Foont Follow this and additional works at: https://scholar.smu.edu/jalc Recommended Citation Brian E. Foont, Shooting down Civilian Aircraft: sI There an International Law, 72 J. Air L. & Com. 695 (2007) https://scholar.smu.edu/jalc/vol72/iss3/10 This Article is brought to you for free and open access by the Law Journals at SMU Scholar. It has been accepted for inclusion in Journal of Air Law and Commerce by an authorized administrator of SMU Scholar. For more information, please visit http://digitalrepository.smu.edu. SHOOTING DOWN CIVILIAN AIRCRAFT: IS THERE AN INTERNATIONAL LAW? BRIAN E. FOONT* TABLE OF CONTENTS PRO LO G U E .............................................. 696 INTRODUCTION ......................................... 697 I. BACKGROUND .................................... 698 A. PRESIDENT TITO'S LETTER ...................... 700 II. SOURCES OF INTERNATIONAL LAW ............ 701 III. POST-WORLD WAR II INCIDENTS ............... 704 A. SOVIET UNION-SHOOT DOWN OF FRENCH COMMERCIAL AIRLINER .......................... 704 B. CHINA-SHOOT DowN OF CATHAY PACIFIC FLIGHT ......................................... 705 C. BULGARIA-SHOOT DowN OF ISRAELI EL AL PASSENGER JET .................................. 705 D. ISRAEL-SHOOT DowN OF LIBYAN AIRLINES PASSENGER JET .................................. 706 E. SOVIET UNION-SHOOT DowN OF KOREAN AIRLINES PASSENGER JET (FLIGHT 902) .......... 707 F. SOVIET UNION-SHOOT DowN OF KOREAN AIRLINES PASSENGER JET (FLIGHT 007) AND ARTICLE 3 BIS TO THE CHICAGO CONVENTION .. 707 G. UNITED STATES-SHOOT DOWN OF IRANIAN AIRLINES PASSENGER JET (FLIGHT 655) .......... 711 * The Law Offices of Brian E. Foont, PLLC; LL.M., Georgetown University Law Center; J.D., American University Washington College of Law; B.A., University of Rochester. -
358 August/September 2009
International Cessna 120/140 Association P.O. Box 830092 Richardson, TX 75083-0092 ISSUE 358 August/September 2009 In This Issue Officers & State Reps Info - Page 2 Upcoming Events - Pages 3 Building Up Some HorsePOWER, Victor Grahn - Page 4 0-200 Installation-Randy Thompson- Page 5-6 Cessna 120/140 Buyers Guide Intro-Chris Vehrs - Page 8-15 Alabama Convention Info Page 16-18 For Sale/Wanted - Page 21 Christian Vehrs in N2032V, his family’s 1947 Cessna 120 Serving the World of Cessna 120/140’s for over 32 years! Page - Aug/Sept 2009 #358 - Send photos/articles to [email protected] International Cessna 120/140 Association Officers & State Representatives “Quick List” 2009-2010 OFFICERS DELAWARE MONTANA TEXAS Ken & Lorraine Morris- President Hugh Horning-ILG Walter Bell-GGW Ken Dwight-DWH 302-655-6191 406-367-5472 281-440-7919 815-547-3991 [email protected] [email protected] [email protected] [email protected] FLORIDA NEW HAMPSHIRE Leonard Richey-58T Don Becker Terry Dawkins-54J Glenn Mori-NH69(pvt) 940-627-1883 Vice President 850-376-8284 603-539-8655 [email protected] [email protected] [email protected] Billy Shires-TDW 620-663-1148 Kenneth Gibson-ZPH NEW JERSEY 806-353-1177 [email protected] 813-949-6256 Jim & Diane Morton-WWD Orville Winover, Jr.-TYR Dick & Nicki Acker [email protected] 609-884-8723 903-939-1418 Secretary/Treasurer GEORGIA [email protected] [email protected] Bob Parks-WDR NEW MEXICO John “Vic” White 989-339-1009 770-962-6875 Ed Blevins-E06 830-438-5072 [email protected] [email protected] 505-399-2449 -
Aviation Maintenance Alerts
ADVISORY CIRCULAR 43-16A AVIATION MAINTENANCE ALERTS ALERT AUGUST NUMBER 2004 313 CONTENTS AIRPLANES CESSNA ......................................................................................................................................1 LEARJET.....................................................................................................................................2 TIGER AIRCRAFT LLC (GRUMMAN AMERICAN AVIATION CORP.). ...........................3 HELICOPTERS BRANTLY...................................................................................................................................3 BALLOONS BALLOON WORKS INC. ..........................................................................................................3 POWERPLANTS AND PROPELLERS ENGINE COMPONENTS, INC..................................................................................................3 MC FARLANE AVIATION, INC. .............................................................................................4 TELEDYNE CONTINENTAL ...................................................................................................5 TEXTRON LYCOMING. ...........................................................................................................5 ACCESSORIES KELLY AEROSPACE. ...............................................................................................................5 AIR NOTES ELECTRONIC VERSION OF FAA FORM 8010-4, MALFUNCTION OR DEFECT REPORT ............................................................................5 -
The Restoration of 1968 Cessna C-150H N22507
The Restoration of 1968 Cessna C-150H N22507 By Mark van Wyk (Updated June 28, 2010) 1 On the cover of this article, there is a before and after comparison of my airplane: a 1968 Cessna C-150H tail number N22507. Maybe it looks pretty much the same now is it did before, but a lot of work was done and a lot of money was spent to upgrade and restore the airplane. Fortunately, it’s been a “flying work in progress,” meaning I was able to fly the plane pretty much the whole time that I was working on it. What inspired me to spend so much time and money fixing up the plane? The first clue that I needed to start thinking about some major re-working happened in November, 2007, when my old engine conked out in Death Valley National Monument, CA on my way to a C-150/152 Club fly-in, about nine miles south of Furnace Creek Airport. The exhaust valve in the #2 cylinder had disintegrated. The vibration and noise was bad, but the propeller continued to turn, and my altitude loss was not too severe. Fortunately, I landed safely, and miraculously, A&P mechanic Mr. Dick Tremaine, who is based in Dyer, Nevada, flew out his C-150, with tools and a spare used cylinder, and he managed to fix the plane, with me assisting, and make it flyable so that I could get home. Mr. Dick Tremain (right) and I (left) Repairing the Old Engine in Death Valley, CA About 100 hours of flying time later, the oil pressure began to drop noticeably, and metal particles were observed in the oil – definite signs that it was time for an engine overhaul – something every airplane owner should be prepared to do when the time comes. -
150/152 Model History the Cessna Pilots Association Educational and Technical Center Santa Maria Public Airport 3940 Mitchell Rd
150/152 Model History The Cessna Pilots Association Educational and Technical Center Santa Maria Public Airport 3940 Mitchell Rd. Santa Maria, CA 93455 805/934-0493 Fax 805/934-0547 www.cessna.org 150/152 History page 1 ©Cessna Pilots Association — July 17, 2006 Model 150 History John M. Frank 1959 - 150 Serial Numbers: 17001 thru 17683 Base Price - $6,995, Average price as Delivered - $8,795 Cessna introduces the model 150 in October of 1958. It is a two place, side by side, all metal, high wing aircraft designed for the trainer market. Initially the Model 150 was offered in three versions, the bare bones Standard, the Trainer, which came with dual controls, brakes landing light, clock, sun visors, outside air temperature gauge, cigarette lighter, turn and bank indicator as well as a Narco Superhomer VOR with nine cyrstals. The Commuter had all of the above plus a vacuum system and attitude and direction indicators. Features of all models include: 1. Tricycle landing gear 2. 40 degree “Para-Lift” flaps 3. Continental O-200 A engine, 100 HP. This engine initially has a 600 hour TBO which was raised to 1800 hours late in the model year 4. 14 volt, 20 amp generator 5. Gross Weight 1500 lbs 6. Fuel Capacity 26 gallons 7. Optional wheel fairings 1960 - 150 Serial Numbers: 17684 thru 17999, 59001 thru 59018 Base Price - $7,250, Average Price as Delivered - $8,950 1. Propeller shortened 2. Larger fuel supply lines beginning at Serial Number 17770 3. Stall warning heat and Pitot heat optional 4. -
Preflight Inspection
STEP BY STEP IMPORTANT NOTE! . Many an aircraft accidents could have been prevented by the pilot completing an adequate preflight inspection of their aircraft before departure. The preflight inspection will initially be taught to you by your instructor and after they oversee you conducting it a few times it will become your responsibility to thoroughly check the aircraft before each flight. The inspection procedure is laid out in the POH for your aircraft. After reviewing the aircraft documents and confirming suitable weather for the trip, a thorough pre-flight inspection (or walk-around) is essential to confirm that your aircraft is airworthy. The following pre-flight inspection is an excerpt from the Cessna 152 Pilot Operating Manual. AIRCRAFT PREFLIGHT INSPECTION 3 STEP PROCESS . Best practise is to do three walkarounds: . In walkaround one, we put the master on and check the lights; pitot heat; the stall warning vane, oil and fuel. This way if we need to order fuel, it can be done now and will reduce any potential delays. In walkaround two, we select the flaps down. After they have been extended we turn the master off. In walkaround three, the master is now off thus conserving the battery, and we take our time to do a complete detailed pre-flight inspection of the aircraft as will be discussed in the ensuing pages. FLUIDS Fuel Quantity: . Check the fuel quantity for your aircraft using the dipstick stored behind the seat. Check the journey log or refueling stickers to verify if it has normal or long range tanks. You will inform your instructor regarding the fuel quantity in gallons and calculate the aircraft. -
Reims Cessna F150M, G-CSBM No & Type of Engines
AAIB Bulletin: 11/2020 G-CSBM AAIB-26778 SERIOUS INCIDENT Aircraft Type and Registration: Reims Cessna F150M, G-CSBM No & Type of Engines: 1 Continental Motors Corp O-200-A Year of Manufacture: 1977 (Serial no: 1359) Date & Time (UTC): 10 July 2020 at 1438 hrs Location: Winchfield, Hampshire Type of Flight: Private Persons on Board: Crew - 1 Passengers - 1 Injuries: Crew - None Passengers - None Nature of Damage: None Commander’s Licence: Private Pilot’s Licence Commander’s Age: 24 years Commander’s Flying Experience: 215 hours (of which 103 were on type) Last 90 days - 23 hours Last 28 days - 17 hours Information Source: Aircraft Accident Report Form submitted by the pilot and further enquiries by the AAIB Synopsis As the aircraft approached Blackbushe Airport the engine lost power and the pilot made a precautionary landing in a field. There was no damage to the aircraft and neither occupant was injured. The engine lost power due to fuel exhaustion. The pilot had used a fuel dipstick through a desire to measure the fuel onboard more accurately, but the dipstick used was not calibrated for the aircraft; this led him to overestimate the fuel onboard. History of the flight The pilot and a friend planned to fly a return trip from Blackbushe Airport (Blackbushe) in Hampshire to Sandown Airport (Sandown) on the Isle of Wight. He was aware that with the two people on board he could not completely fill the fuel tanks as this would put the aircraft above its maximum takeoff weight. He had calculated that he required 16 US gal of fuel for the return trip which included 5 US gal of reserve fuel. -
WEC Aircraft Use and Safety Handbook
AIRCRAFT USE AND SAFETY HANDBOOK FOR SCIENTISTS AND RESOURCE MANAGERS John C. Simon Peter C. Frederick Kenneth D. Meyer H. Percival Franklin DEVELOPED BY THE © University of Florida 2010 ABOUT THE AUTHORS John Charles Simon is a Research Coordinator for the University of Florida’s South Florida Wading Bird Project. He earned his private pilot’s certificate in 1986 and has flown over 750 hours as a passenger/observer in both fixed- winged and rotary aircraft conducting population and nesting surveys, habitat evaluations, following flights, and radio telemetry. Dr. Peter Frederick is a Research Professor in the University of Florida’s Department of Wildlife Ecology and Conservation. His research on wading birds in the Florida Everglades has used aerial survey techniques extensively and intensively, with over 1,500 hours flown in fixed-winged and rotary aircraft over 25 years. He survived one air crash in a Cessna 172 during the course of that work. Dr. Kenneth D. Meyer is Director of the Avian Research and Conservation Institute and an Associate Professor (Courtesy) in the University of Florida's Department of Wildlife Ecology and Conservation. Since 1981, Dr. Meyer's research on birds has involved fixed-wing and rotary aircraft for radio telemetry, population surveys, roost counts, nest finding, and following flights. Dr. H. Percival Franklin is Courtesy Associate Professor and Unit Leader of the Florida Cooperative Fish and Wildlife Research Unit. Its employees and cooperators, regardless of employment, are bound by strict aircraft training and use regulations of the Department of Interior. Dr Franklin has been a strong proponent of aircraft and other safety issues in the workplace.