Measuring the Energy of Trains
Total Page:16
File Type:pdf, Size:1020Kb
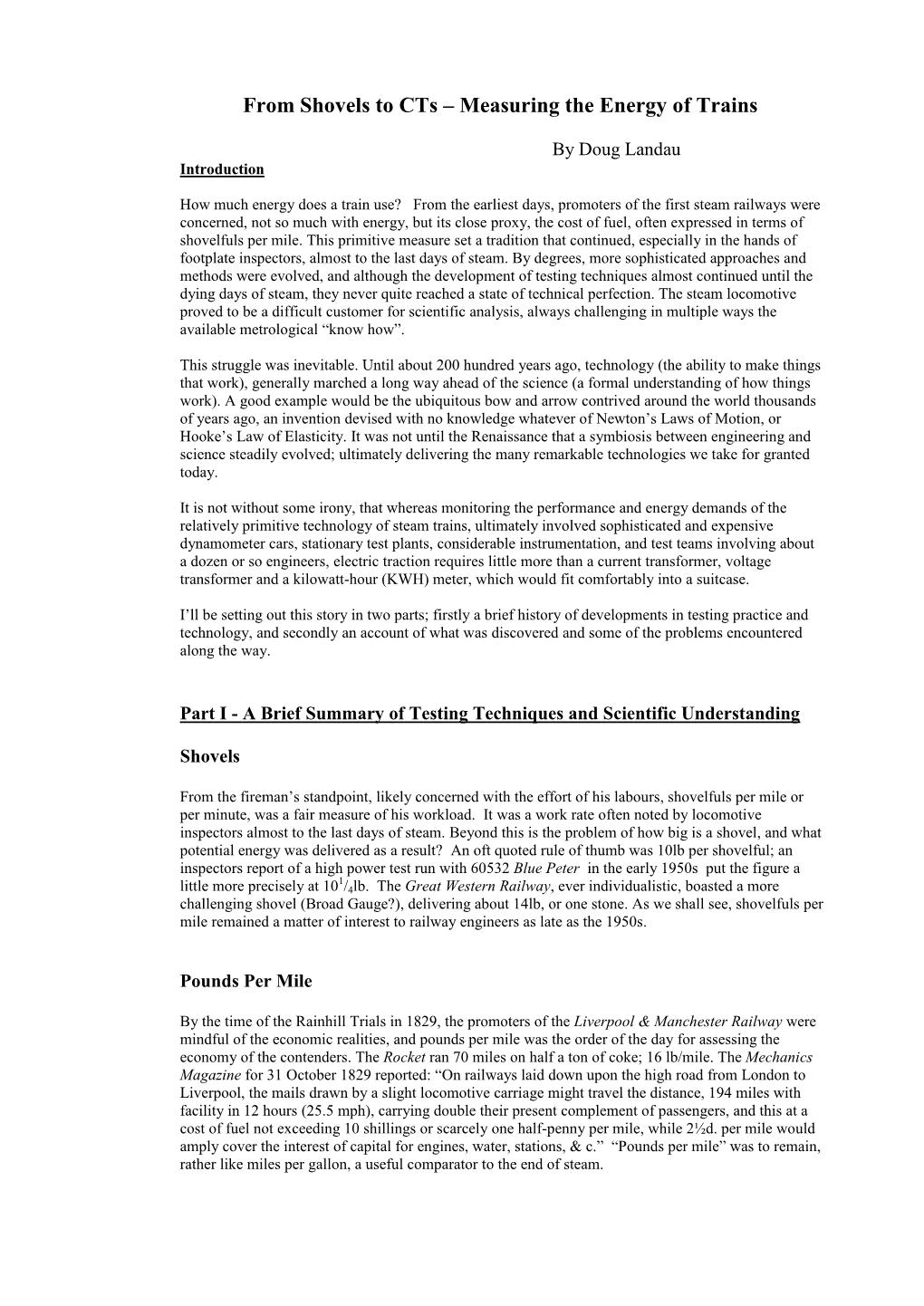
Load more
Recommended publications
-
Appendix: Statistical Information
Appendix: Statistical Information Table A.1 Order in which the main works were built. Table A.2 Railway companies and trade unions who were parties to Industrial Court Award No. 728 of 8 July 1922 Table A.3 Railway companies amalgamated to form the four main-line companies in 1923 Table A.4 London Midland and Scottish Railway Company statistics, 1924 Table A.5 London and North-Eastern Railway Company statistics, 1930 Table A.6 Total expenditure by the four main-line companies on locomotive repairs and partial renewals, total mileage and cost per mile, 1928-47 Table A.7 Total expenditure on carriage and wagon repairs and partial renewals by each of the four main-line companies, 1928 and 1947 Table A.8 Locomotive output, 1947 Table A.9 Repair output of subsidiary locomotive works, 1947 Table A. 10 Carriage and wagon output, 1949 Table A.ll Passenger journeys originating, 1948 Table A.12 Freight train traffic originating, 1948 TableA.13 Design offices involved in post-nationalisation BR Standard locomotive design Table A.14 Building of the first BR Standard locomotives, 1954 Table A.15 BR stock levels, 1948-M Table A.16 BREL statistics, 1979 Table A. 17 Total output of BREL workshops, year ending 31 December 1981 Table A. 18 Unit cost of BREL new builds, 1977 and 1981 Table A.19 Maintenance costs per unit, 1981 Table A.20 Staff employed in BR Engineering and in BREL, 1982 Table A.21 BR traffic, 1980 Table A.22 BR financial results, 1980 Table A.23 Changes in method of BR freight movement, 1970-81 Table A.24 Analysis of BR freight carryings, -
Daniel Gooch 1929 NE Coast Exhibition G AIA 2015 Report G Will’S Cigarette Factory from Maney to Taylor and Francis
INDUSTRIAL ARCHAEOLOGY 177 SUMMER NEWS 2016 THE BULLETIN OF THE ASSOCIATION FOR INDUSTRIAL ARCHAEOLOGY FREE TO MEMBERS OF AIA Restoration Grants G Lancashire Museums G Daniel Gooch 1929 NE Coast Exhibition G AIA 2015 report G Will’s Cigarette Factory From Maney to Taylor and Francis As AIA members will be very aware, the firm of firm which is also part of T&F and so of Informa. Maney of Leeds, with whom we set up a contract This is good for us as Routledge have long been to publish the Review many years ago, and who respected publishers of archaeology books – the INDUSTRIAL subsequently also took over our membership book I wrote with Peter Neaverson, Industrial administration, was sold in 2015 to the Taylor and Archaeology: Principles and Practice , was ARCHAEOLOGY Francis Group (hereafter T&F). To complicate published by Routledge so I am glad to know the matters till further, Taylor and Francis are part of name still exists. Under Maney, we benefited from NEWS 177 a much larger conglomerate, Informa, described IAR forming part of a package with other Summer 2016 on their website as ‘a leading business archaeology journals, MORE, which meant it was intelligence, academic publishing, knowledge and taken by academic libraries who might not have Honorary President events business, creating unique content and subscribed to it on its own. T&F have similar Prof Marilyn Palmer 63 Sycamore Drive, Groby, Leicester LE6 0EW connectivity for customers all over the world. It is arrangements with their Routledge archaeology Chairman listed on the London Stock Exchange and is a journals and so we hope to continue to benefit Keith Falconer member of the FTSE 100. -
Download the Report Item 4
BOROUGH COUNCIL OF WELLINGBOROUGH AGENDA ITEM 4 Development Committee 17 February 2020 Report of the Principal Planning Manager Local listing of the Roundhouse and proposed Article 4 Direction 1 Purpose of report For the committee to consider and approve the designation of the Roundhouse (or number 2 engine shed) as a locally listed building and for the committee to also approve an application for the addition of an Article 4(1) direction to the building in order to remove permitted development rights and prevent unauthorised demolition. 2 Executive summary 2.1 The Roundhouse is a railway locomotive engine shed built in 1872 by the Midland Railway. There is some concern locally that the building could be demolished and should be protected. It was not considered by English Heritage to be worthy of national listing but it is considered by the council to be worthy of local listing. 2.2 Local listing does not protect the building from demolition but is a material consideration in a planning application. 2.3 An article 4(1) direction would be required to be in place to remove the permitted development rights of the owner. In this case it would require the owner to seek planning permission for the partial or total demolition of the building. 3 Appendices Appendix 1 – Site location plan Appendix 2 – Photos of site Appendix 3 – Historic mapping Appendix 4 – Historic England report for listing Appendix 5 – Local list criteria 4 Proposed action: 4.1 The committee is invited to APPROVE that the Roundhouse is locally listed and to APPROVE that an article 4 (1) direction can be made. -
Accident. Settle. 1960-01-21
MINISTRY OF TRANSPORT RAILWAY ACCIDENTS Report on the Accident which occurred on 21st January 1960 near Settle in the London Midland Region British Railways LONDON : HER MAJESTY'S STATIONERY OFFICE 1960 CONTENTS Page INTRODUCTORY ...... ... ... ... ... ... ... ... ... ... ... 1 1. GENERAL DESCRIPTION ... ... ... ... ... ... ... ... ... 2 11. THE DAMAGE TO THE TRAINS ... ... ... ... ... ... ... ... 2 111. THE BRITANNIA LOCOMOTIVE ... ... ... ... ... ... ... IV. THE DAMAGE TO THE TRACK AND THE CAUSE OF THE DERAILMENT V. THE RUNNING OF THE EXPRESS ...... .. ... ... ... ... W. EVIDENCE ...... ... ... ... ... ... ... ... ... ... VII. CONCLUSIONS, REMARKS, AND RECOMMENDATIONS ... ... ... DRAWINGS Fig. 1. Map of the Midland route: Glasgow-Leeds. Fig. 2. Profile of the line: CarlisleSettle Junction. Fig. 3. The site of the accident. Fig. 4. The Down track at the point of derailment. Fig. 5. The Britannia locomotive: engine diagram. Fig. 6. The Britannia locomotive: end view showing presumed position of the displaced motion during overturning, and later when damaging the Down track. Fig. 7. The Britannia locomotive: detail of the right hand motion. Fig. 8. Front slide bar bolt before modification. Fig. 9. Front slide bar bolt after modification. PHOTOGRAPHS 1. The Britannia engine: the displaced right hand motion assembly. 2. The Down track at the point of derailment. 3. Front end of slide bar assembly before modification. 4. Front end of slide bar assembly after modification. MINISTRYOF TRANSPORT. BERKELEYSQUARE HOUSE, LONDON,W.1. 19th April 1960. I have the honour to report for the information of the Minister of Transport, in accordance with the Order dated 22nd January, the result of my Inquiry into the accident which occurred at about 1.48 a.m. on 21st January 1960 near Settle on the former Midland Railway route between England and Scotland in the London Midland Region, British Railways. -
WRF NL192 July 2018
WELLS RAILWAY FRATERNITY Newsletter No.192 - July 2018 th <<< 50 ANNIVERSARY YEAR >>> www.railwells.com Thank you to those who have contributed to this newsletter. Your contributions for future editions are welcome; please contact the editor, Steve Page Tel: 01761 433418, or email [email protected] < > < > < > < > < > < > < > < > < > < > < > < > < > < > < > < > < > < > < > < > < > < > < > < > Visit to STEAM Museum at Swindon on 12 June. Photo by Andrew Tucker. MODERNISATION TO PRIVATISATION, 1968 - 1997 by John Chalcraft – 8 May On the 8th May we once more welcomed John Chalcraft as our speaker. John has for many years published railway photographs and is well known for his knowledge on topics relating to our hobby. He began by informing us that there were now some 26,000 photographs on his website! From these, he had compiled a presentation entitled 'From Modernisation to Privatisation', covering a 30-year period from 1968 (the year of the Fraternity's founding) until 1997. His talk was accompanied by a couple of hundred illustrations, all of very high quality, which formed a most comprehensive review of the railway scene during a period when the railways of this country were subjected to great changes. We started with a few photos of the last steam locomotives at work on BR and then were treated to a review of the new motive power that appeared in the 20 years or so from the Modernisation Plan of 1955. John managed to illustrate nearly every class of diesel and electric locomotive that saw service in this period, from the diminutive '03' shunter up to the Class '56' 3,250 hp heavy freight locomotive - a total of over 50 types. -
Learning Project Term 5 Week 2 Year 2
Learning Project Term 5 Week 2 Year 2 Weekly Maths Tasks Weekly Reading Tasks (Aim to do 1 per day) (Aim to do 1 per day) Work on Times Table Rockstars – use Use Oxford Owl or Oxford Reading your individual login to access this Buddy: (https://www.oxfordowl.co.uk/ and (5 sessions on ‘studio’). https://www.oxfordreadingbuddy.com/uk) to Play on ‘The Mental Maths Train Game’ read a new book. Complete the quiz at - practise adding and subtracting. the end. Log ins and passwords are in https://www.topmarks.co.uk/maths- your books. games/mental-maths-train Listen to Mr Hicks read a book (see Practice subtracting these two digit Instagram for this story). Did you like numbers. Keep an eye on Instagram the story? What was your favorite part? for a tutorial on the number line and What parts didn’t you like? partitioning methods to help you. Find a poem you like and read it. You 26 - 12 = 34 - 15 = could have a look here: 36 - 22 = 44 - 16 = https://childrens.poetryarchive.org/) Discuss 45 - 34 = why you like it with an adult or sibling. Complete a page of your Maths SATs Does it have any rhyming words? revision books. Learn part of/all of your poem off by Here are some train parts that Brunel heart and perform it. You could record is going to share equally with his yourself and send it to your teacher on friend Daniel Gooch. Can you find out Instagram. how many they will both have each if The title of a story is ‘The Runaway they share the parts equally? Train’. -
Issue 1 Model Railway Express Emagazine
IN THIS ISSUE Welcome Simon Kohler Market Havering Station Building Trevor Wright A Day in the Life Of…….. Blair Robinson Modelling Around the World Neil Ward Paeroa to Waihi Review: Hot Wire foam & Terry Rowe Polystyrene Cutter Tombridge Junction & St Faith’s Graham Whiteley Branch N Gauge layout Railway Refreshments Cath Locke The Signalbox Inn Review: 5 in 1 Butane Gas Soldering John Locke Set Readers Letters West Kirby Joint Layout Bob Powell On30 Hand Car Shack Terry Rowe The 5.5mm Association Peter Blackham Memoirs of a Model Railway Widow Ann Onn Exhibition Review: Daventry Terry Rowe Model Railway Club 2016 Out & about: Appleby Frodingham Cath Locke Railway Preservation Society Product Release: On 30 Victorian EDM models Railways NQR narrow gauge wagons Review: Beko Lights David Scott Kohler Confidential Simon Kohler On My Workbench Oliver Turner Front cover: Tombridge Junction (photo by Graham Whiteley) Welcome to our project update feature, with the latest status of forthcoming 0151 733 3655 releases from all major manufacturers. 17 Montague Road, Widnes, WA8 8FZ Use it to see the progress of projects you Phone opening times Shop opening times are interested in. The web address in the Mon to Sat 7:30am-6pm Mon to Sun 9am-5pm “link” column can be used to view products Sun 9am-5pm online, and to place your preorders. Price Date CAD done In Tooling Seen 1st Decorated In On Board Released announced EP samples production Ship Wickham trolley car hattons.co.uk/wtc £67.96 Mar 2013 Stanier Mogul 2-6-0 hattons.co.uk/5p4f £127.46 Mar -
Toys for the Collector
Hugo Marsh Neil Thomas Forrester Director Shuttleworth Director Director Toys for the Collector 25th August at 10:00 GMT +1 Viewing on a rota basis by appointment only Special Auction Services Plenty Close Off Hambridge Road NEWBURY RG14 5RL Telephone: 01635 580595 Email: [email protected] www.specialauctionservices.com Bob Leggett @SpecialAuction1 Toy & Train Specialist @Specialauctionservices Due to the nature of the items in this auction, buyers must satisfy themselves concerning their authenticity prior to bidding and returns will not be accepted, subject to our Terms and Conditions. Additional images are available on request. Buyer’s Premium with SAS & SAS LIVE: 20% plus Value Added Tax making a total of 24% of the Hammer Price Buyer’s Premium with the-saleroom.com Premium: 25% plus Value Added Tax making a total of 30% of the Hammer Price 1. Motor Max 1:48 Scale WWII 7. Hobby Master 1:48 Scale WWII 13. Armour Collection 1:48 Scale Fighter Planes, a boxed group comprising Aircraft, a boxed collection from the Air WWII Aircraft, a boxed group of four, 76316 P-47 Thunderbolt (2), 76368 Zero, Power Series comprising HA7001 F2A-2 B11B567 98320 F6F5 Hellcat Kangaroos, 76369 P-40 Warhawk, 76355 F4U Corsair, Buffalo USS Saratoga (4), HA7006 limited B11B309 98167 Spitfire RAF France, 76365 P-38 Lightning, 76370 MKI Spitfire, edition F2A Buffalo USS Lexington (2), B11B293 98144 P47 Thunderbolt USAF 76336 P-51 Mustang, G-E, Boxes G-E, (8) HA7301 Grumann F3F-1 limited edition and 98006 P51 Mustang USAAF, G-E, £80-120 USS Saratoga (2), HA7101limited edition Boxes F-G, (4) Spitfire Johnnie Johnson 1945, HA7103 £80-120 2. -
List of GWR Books Held at STEAM - Museum of the GWR, Swindon
List of GWR Books held at STEAM - Museum of the GWR, Swindon Title Author Publication Date Heavyweight Champion - Story of GWR No 2807 2807 Support Group 1997 Great Western Steam in the West Country 4588 Great Western Steam Miscellany 2 5079 Lysander Great Western Steam Miscellany 3 5079 Lysander Great Western Steam Miscellany 3 5079 Lysander Great Western Steam Miscellany 2 5079 Lysander Through the links at Southall and Old Oak Common Abear A E Through the lInks at Southall and Old Oak Common Abear A E Through the links at Southall and Old Oak Common Abear A E All Change at Reading Adam Sowan 2013 Isambard Kingdom Brunel Adams John and Elkin Paul 1988 Locomotive & Train Working in the latter part of the 19th Century Ahrons E L 1953 The G.W.R. in West Cornwall Alan Bennett 1995 Great Western Railway in East Cornwall Alan Bennett 1990 Great Western Railway in Western Cornwall Alan Bennett 1992 Great Western Railway Holiday Lines in Devon & West Somerset Alan Bennett 1993 Speed to the West - Great Western Publicity & posters 1923-1947 Aldo Delicta & Beverrley Cole 2000 Seldom Met with even on Mineral Lines - Caradon Raiilway permanent Way Alec Kendall Alec Kendall (with Iain Rowe & Lost Years of Liskeard & Caradon Railway Dave Ambler) 2013 Alec Kendall (with Iain Rowe, P Murnaghan, B Oldham & Liskeard and Caradon Railway -Moorswater to Trewint Dave Ambler) 2017 Alexandra Docks and Railway Newport Docks Company 1919 ABC of BR Locomotives - Western Region Allan Ian 1957 ABC of GWR Locomotives 1947 Allan Ian 1946 ABC of GWR Locomotives Allan -
Carlisle Railway Directory of Resources
SETTLE – CARLISLE RAILWAY DIRECTORY OF RESOURCES A listing of printed, audio-visual and other resources including museums, public exhibitions and heritage sites * * * Compiled by Nigel Mussett 2020 Petteril Bridge Junction CARLISLE SCOTBY 1942 River Eden CUMWHINTON 1956 Cotehill Viaduct COTEHILL 1952 Dry Beck Viaduct ARMATHWAITE Armathwaite Tunnel Armathwaite Viaduct Baron Wood Tunnels 1 (south) & 2 (north) LAZONBY & KIRKOSWALD Lazonby Tunnel Eden Lacy Viaduct LITTLE SALKELD 1970 Little Salkeld Viaduct Cross Fell 2930ft LANGWATHBY Waste Bank Tunnel Culgaith Tunnel CULGAITH 1970 Crowdundle Viaduct NEWBIGGIN 1970 LONG MARTON 1970 Long Marton Viaduct APPLEBY Ormside Viaduct ORMSIDE 1952 Griseburn Viaduct Helm Tunnel Crosby Garrett Viaduct Crosby Garrett Tunnel CROSBY GARRETT 1952 Smardale Viaduct KIRKBY STEPHEN Birkett Tunnel Wild Boar Fell 2323ft Shotlock Tunnel Ais Gill Viaduct Moorcock Tunnel Lunds Viaduct Mossdale Viaduct Dandry Mire Viaduct Appersett Viaduct GARSDALE Mossdale Rise Hill Tunnel HAWES 1959 Head Tunnel DENT Arten Gill Viaduct Blea Moor Tunnel Dent Head Viaduct Whernside 2415ft Ribblehead Viaduct RIBBLEHEAD Penyghent 2277ft Ingleborough 2372ft Ribble Viaduct HORTON-IN-RIBBLESDALE Little Viaduct Sheriff Brow Viaduct Taitlands Tunnel Whitefriars Viaduct SETTLE Stations - open Marshfield Viaduct Settle Junction Stations - closed, with dates of closure to passengers. River Ribble Crosby Garrett and Cotehill since demolished © Nigel Mussett 2019 © NJM 2018 Route map of the Settle—Carlisle Railway and Hawes Branch GRADIENT PROFILE Gargrave to Carlisle After The Cumbrian Railways Association ’The Midland’s Settle & Carlisle Distance Diagrams’ 1992. CONTENTS Route map of the Settle-Carlisle Railway Gradient profile Introduction A. Primary Sources B. Books, pamphlets and leaflets C. Periodicals and articles D. Research Studies E. Maps F. -
Report on the Collision Waterloo Southern Region
MINISTRY OF TRANSPORT RAILWAY ACCIDENT REPORT ON THE COLLISION which occurred on 11th April 1961 at WATERLOO in the SOUTHERN REGION BRITISH RAILWAYS LONDON: HER MAJESTY'S STATIONERY OFFICE : 1961 PRlrF IS 3d. NI, l SKETCH SHOWING PART OF THE LAYOUT AT WATERLOO NOT TO SCALL 31sr October, 1961. SIR, I have the honour to report, for the information of the Minister of Transport, in accordance with the Order dated 13th April, 1961, the result of my Inquiry into the collision between an electric passenger train and an engine, which occurred at 5.26 pm.. on 11th April. 1961, at Waterloo, in the Southern Region, British Railways. The 4.38 pm. 8-coach multiple unit electric passenger train from Effingham Junction to Waterloo (via Epsom) was approaching Waterloo on the Up Main Local line. It was to be stopped at the outer home signal (a colour light), which was at Red, for the engine to pass in the Down direction from the Down Main Through line across the Up Main Local line to the Down Main Local line, en route to the Motive Power Depot. The electric train, however, failed to stop at the signal and collided head on with the engine on the crossover which had been reversed for the latter, at a point about 195 yards beyond the signal. At the time of the collision the electric train was travelling at 20-25 miles per hour and the engine at about 12 m.p.h. The engine was running tender leading and its driver only became aware of the electric train at the last moment, and was unable to slacken speed. -
'Swindon and Its Railway Connections' by Reg Palk
IMechE Dorchester Area Lecture Review ‘Swindon and its Railway Connections’ by Reg Palk 18th June 2009, Weymouth College ‘Swindon and its Railway Connections’ presented by Reg Palk, a Swindon railway museum volunteer, held at Weymouth College on the 18th June 2009 was an informative and light hearted lecture for all those interested in Swindon and its railway heritage. The lecture commenced at 7pm and was well attended by an audience of approximate 30. With the aid of slides, Reg described the history of Swindon Railway Works which opened in January 1843 as a repair and maintenance facility for the new Great Western Railway (GWR). By 1900 the works had expanded dramatically and employed over 12,000 people and at its peak in the 1930s, the works covered over 300 acres and capable of producing three locomotives a week. The ‘STEAM - Museum of the Great Western Railway’, tells the story of the men and women who built, operated and travelled on the GWR, a network that through the pioneering vision of Isambard Kingdom Brunel (1806-1859) and others such as Sir Daniel Gooch (1816-1889) was regarded as the most advanced in the world. In 1840, Daniel Gooch, locomotive superintendent of the GWR, wrote to Isambard Kingdom Brunel, the railway's chief engineer. The letter he wrote proved decisive in Swindon's history changing it from the small market town of ‘Swindon on the hill’ with its associated canal junction into a town at the heart of the Industrial Revolution. The letter from Gooch put forward his proposal for the building of the Great Western's much-needed engine works at Swindon.