Automated Ultrasound-Based Inspection of Rails: Review
Total Page:16
File Type:pdf, Size:1020Kb
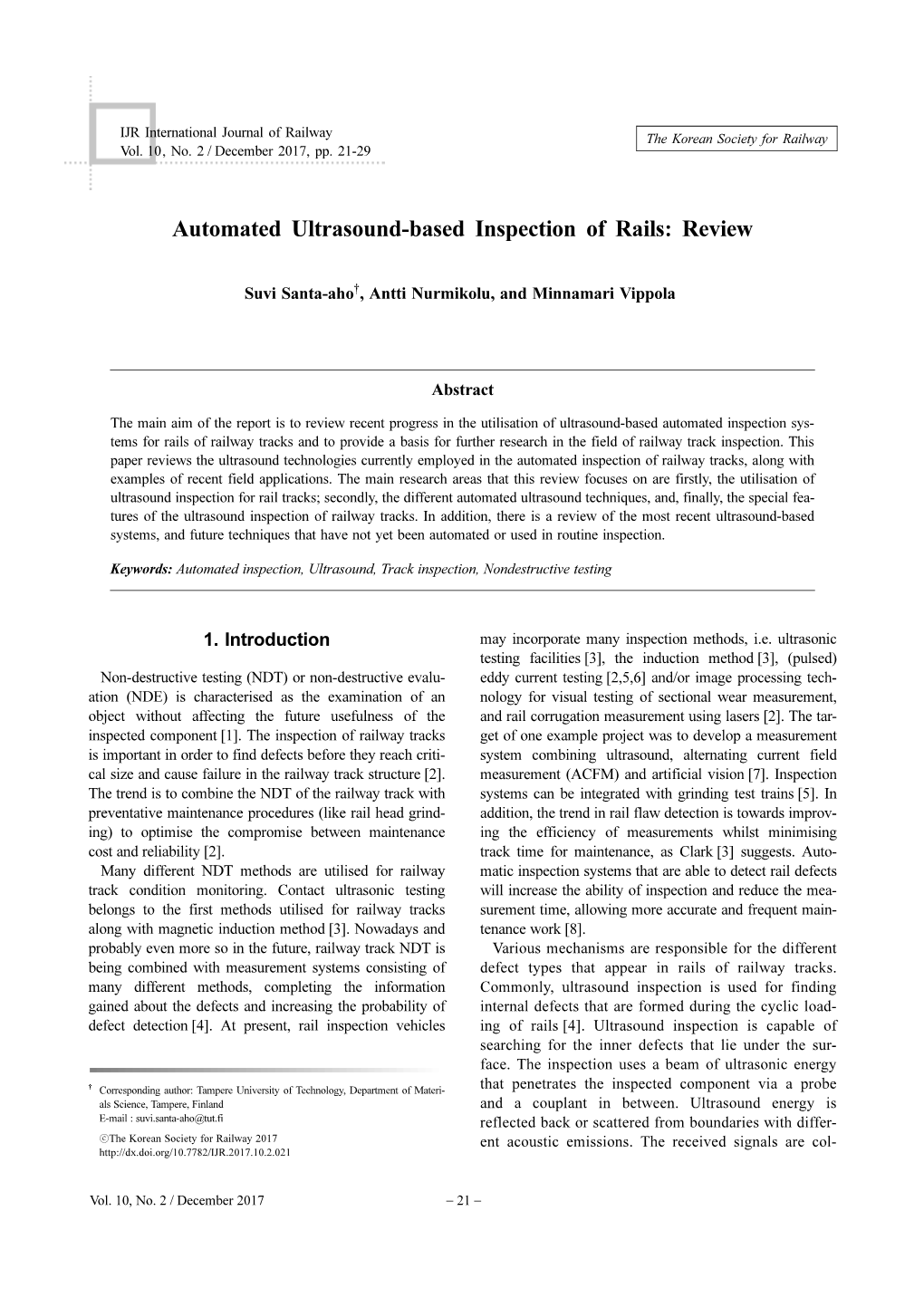
Load more
Recommended publications
-
MÁV Central Rail and Track Inspection Ltd
MÁV Central Rail and Track Inspection Ltd. PATER TRACK DIAGNOSTIC EXPERT SYSTEM Besides the knowledge of quality the safe and economical maintenance of railway tracks plays an increasingly impor- tant role these days. The „PATER” track diagnostic ex- pert software is intended to fulfil this task. PATER is a computer program that keeps records of rail- way tracks, monitors their condition and performs mainte- nance planning duties. Its purpose is to assist track mainte- nance professionals in managing the data of the technical and measurement systems, presenting the condition of the track, planning track maintenance jobs depending on track conditions, selecting the appropriate technology and per- forming cost estimates. Rail defects revealed by various inspections This is a client-server based program that ensures that data and their qualification stored in the database can be accessed from anywhere and client users can use them through the internet in case of sufficient authorisation. This model makes it possible that all data is stored and updated in one location therefore the data available to users is always up-to-date. In the engineering practice the val- ues of the isolated defects and gen- eral qualifying indices are analyzed and these values are sufficient to judge the traffic safety and quality. Nowadays we use track geometri- cal, vehicle dynamical, ultrasonic, Space and time based graphical analysis Head Checking, rail profile and rail of track geometry data corrugation measuring devices. The PATER program adapts to the re- quirements of any railway company: unlimited new measuring system, parameter, measuring limit etc. can be integrated quickly and easily. -
Track Inspection – 2009
Santa Cruz County Regional Transportation Commission Track Maintenance Planning / Cost Evaluation for the Santa Cruz Branch Watsonville Junction, CA to Davenport, CA Prepared for Egan Consulting Group December 2009 HDR Engineering 500 108th Avenue NE, Suite 1200 Bellevue, WA 98004 CONFIDENTIAL Table of Contents Executive Summary 4 Section 1.0 Introduction 10 Section 1.1 Description of Types of Maintenance 10 Section 1.2 Maintenance Criteria and Classes of Track 11 Section 2.0 Components of Railroad Track 12 Section 2.1 Rail and Rail Fittings 13 Section 2.1.1 Types of Rail 13 Section 2.1.2 Rail Condition 14 Section 2.1.3 Rail Joint Condition 17 Section 2.1.4 Recommendations for Rail and 17 Joint Maintenance Section 2.2 Ties 20 Section 2.2.1 Tie Condition 21 Section 2.2.2 Recommendations for Tie Maintenance 23 Section 2.3 Ballast, Subballst, Subgrade, and Drainage 24 Section 2.3.1 Description of Railroad Ballast, Subballst, 24 Subgrade, and Drainage Section 2.3.2 Ballast, Subgrade, and Drainage Conditions 26 and Recommendations Section 2.4 Effects of Rail Car Weight 29 Section 3.0 Track Geometry 31 Section 3.1 Description of Track Geometry 31 Section 3.2 Track Geometry at the “Micro-Level” 31 Section 3.3 Track Geometry at the “Macro-Level” 32 Santa Cruz County Regional Transportation Commission Page 2 of 76 Santa Cruz Branch Maintenance Study CONFIDENTIAL Section 3.4 Equipment and Operating Recommendations 33 Following from Track Geometry Section 4.0 Specific Conditions Along the 34 Santa Cruz Branch Section 5.0 Summary of Grade Crossing -
Taskload Report Outline
Track Inspection Time Study* U.S. Department of Transportation Federal Railroad * Required by Section 403 of the Rail Safety Improvement Act of 2008 (Public Law 110- Administration 432, Div. A.) Office of Railroad Policy and Development Washington, DC 20590 DOT/FRA/ORD-11/15 Final Report July 2011 NOTICE This document is disseminated under the sponsorship of the Department of Transportation in the interest of information exchange. The United States Government assumes no liability for its contents or use thereof. Any opinions, findings and conclusions, or recommendations expressed in this material do not necessarily reflect the views or policies of the United States Government, nor does mention of trade names, commercial products, or organizations imply endorsement by the United States Government. The United States Government assumes no liability for the content or use of the material contained in this document. NOTICE The United States Government does not endorse products or manufacturers. Trade or manufacturers‘ names appear herein solely because they are considered essential to the objective of this report. REPORT DOCUMENTATION PAGE Form Approved OMB No. 0704-0188 Public reporting burden for this collection of information is estimated to average 1 hour per response, including the time for reviewing instructions, searching existing data sources, gathering and maintaining the data needed, and completing and reviewing the collection of information. Send comments regarding this burden estimate or any other aspect of this collection of information, including suggestions for reducing this burden, to Washington Headquarters Services, Directorate for Information Operations and Reports, 1215 Jefferson Davis Highway, Suite 1204, Arlington, VA 22202-4302, and to the Office of Management and Budget, Paperwork Reduction Project (0704-0188), Washington, DC 20503. -
Rail Transit Track Inspection and Maintenance
APTA STANDARDS DEVEL OPMENT PROGRAM APTA RT-FS-S-002-02, Rev. 1 STANDARD First Published: Sept. 22, 2002 American Public Transportation Association First Revision: April 7, 2017 1300 I Street, NW, Suite 1200 East, Washington, DC 20006 Rail Transit Fixed Structures Inspection and Maintenance Working Group Rail Transit Track Inspection and Maintenance Abstract: This standard provides minimum requirements for inspecting and maintaining rail transit system tracks. Keywords: fixed structures, inspection, maintenance, qualifications, rail transit system, structures, track, training Summary: This document establishes a standard for the periodic inspection and maintenance of fixed structure rail transit tracks. This includes periodic visual, electrical and mechanical inspections of components that affect safe and reliable operation. This standard also identifies the necessary qualifications for rail transit system employees or contractors who perform periodic inspection and maintenance tasks. Scope and purpose: This standard applies to transit systems and operating entities that own or operate rail transit systems. The purpose of this standard is to verify that tracks are operating safely and as designed through periodic inspection and maintenance, thereby increasing reliability and reducing the risk of hazards and failures. This document represents a common viewpoint of those parties concerned with its provisions, namely operating/ planning agencies, manufacturers, consultants, engineers and general interest groups. The application of any standards, recommended practices or guidelines contained herein is voluntary. In some cases, federal and/or state regulations govern portions of a transit system’s operations. In those cases, the government regulations take precedence over this standard. The North American Transit Service Association (NATSA) and its parent organization APTA recognize that for certain applications, the standards or practices, as implemented by individual agencies, may be either more or less restrictive than those given in this document. -
Rolling Contact Fatigue: a Comprehensive Review Administration
U.S. Department of Transportation Federal Railroad Rolling Contact Fatigue: A Comprehensive Review Administration Office of Railroad Policy and Development Washington, DC 20590 DOT/FRA/ORD-11/24 Final Report November 2011 NOTICE This document is disseminated under the sponsorship of the Department of Transportation in the interest of information exchange. The United States Government assumes no liability for its contents or use thereof. Any opinions, findings and conclusions, or recommendations expressed in this material do not necessarily reflect the views or policies of the United States Government, nor does mention of trade names, commercial products, or organizations imply endorsement by the United States Government. The United States Government assumes no liability for the content or use of the material contained in this document. NOTICE The United States Government does not endorse products or manufacturers. Trade or manufacturers‘ names appear herein solely because they are considered essential to the objective of this report. REPORT DOCUMENTATION PAGE Form Approved OMB No. 0704-0188 Public reporting burden for this collection of information is estimated to average 1 hour per response, including the time for reviewing instructions, searching existing data sources, gathering and maintaining the data needed, and completing and reviewing the collection of information. Send comments regarding this burden estimate or any other aspect of this collection of information, including suggestions for reducing this burden, to Washington Headquarters Services, Directorate for Information Operations and Reports, 1215 Jefferson Davis Highway, Suite 1204, Arlington, VA 22202-4302, and to the Office of Management and Budget, Paperwork Reduction Project (0704-0188), Washington, DC 20503. 1. -
Railroad Track Condition Monitoring Using Inertial Sensors and Digital Signal Processing: a Review
This article has been accepted for publication in a future issue of this journal, but has not been fully edited. Content may change prior to final publication. Citation information: DOI 10.1109/JSEN.2018.2875600, IEEE Sensors Journal 1 Railroad Track Condition Monitoring Using Inertial Sensors and Digital Signal Processing: A Review Leonard Chia, Bhavana Bhardwaj, Pan Lu*, Raj Bridgelall and cost-efficiency of railroad operations [4]. Federal track Abstract— Inertial sensors such as accelerometers and safety regulation require railroads to inspect all tracks in gyroscopes have been widely used since the early 1990s to monitor operation as often as twice weekly. Railroad companies deploy the condition of transportation assets. Recent improvements in expensive and relatively slow methods using human inspectors their performance, a reduction in cost, and sensor miniaturization and expensive automated inspection vehicles to inspect and has resulted in a growing interest expanding their use. This monitor their rail tracks. The current practice is expensive and research is an extensive and systematic review of their application also decreases the rail productivity by reducing track time for considerations, challenges, and opportunities for improvements in railroad track condition monitoring. Research questions were railroad industry to perform inspection which also increases the developed to guide the selection of relevant articles from safety risk for railway inspection workers. databases. The authors report key findings in the areas of sensor Sensors such as inertial sensor, accelerometers, gyroscopic specification, sensor location, and sensor signal processing. sensors, and global position system (GPS), are carried on a Index Terms— Digital signal filtering, Sample rate, Sensors, railway vehicle to continuously monitor and inspect rail assets Track geometry monitoring to meet the growing needs of safety improvement, reliable and low-cost rail operations. -
ENSCO Rail, Inc
For more than 45 years, ENSCO’s team of engineers has led the rail industry in developing new, advanced technologies for transportation. ENSCO technology and services help customers improve the quality of their operations while making travel safer. ENSCO Rail, Inc. is a wholly owned subsidiary of ENSCO, Inc. Table of Contents Track Inspection Technologies 3 Vehicle Track Evaluation 23 Track Inspection Vehicles 4 Instrumented Wheel Set (IWS) 25 Track Measurement Systems 5 Vehicle/Track Interaction Consulting Services 26 Deployable Gage Restraint Measurement System Train Control Safety 27 (DGRMS) 6 Signal and Communication Inspection System (SCIS) 29 RailScan Lite Track Geometry Measurement System Next Generation Receiver Coil (NGRC) 30 (RSL-TGMS) 7 Track Imaging Systems 8 Rail Safety and Security 31 Vehicle/Track Interaction (V/TI) Monitor 10 Rail Emergency Evacuation Simulator 32 Autonomous Track Geometry Measurement System (ATGMS) 11 Portable Track Loading Fixture (PTLF) 12 Track Inspection Services 13 Track Data Management 15 Track Data Management Suite 16 Digital Track Notebook® (DTN) 3.0 17 TrackIT® 18 Automated Maintenance Advisor (AMA) 19 GeoEdit 8 20 Virtual Track Walk (VTW) 21 VAMPIRE® 22 ENSCO Rail, Inc. is a wholly owned subsidiary of ENSCO, Inc. Since 1970, ENSCO engineers have led the rail industry in developing new, advanced technologies for transportation. ENSCO technology and services help customers improve the quality of their operations while making travel safer. 2 Track Inspection Technologies ENSCO is an international leader in track inspection technologies. Our engineers have pioneered the use of technologies, such as advanced rail inspection sensors, high-resolution imaging technology, and autonomous inspection systems to improve track maintenance. -
Feasibility in Assessing the Dipped Rail Joint Defects Through Dynamic Response of Heavy Haul Locomotive
J. Mod. Transport. https://doi.org/10.1007/s40534-018-0159-9 Feasibility in assessing the dipped rail joint defects through dynamic response of heavy haul locomotive 1 1 1 1 2 Yan Quan Sun • Maksym Spiryagin • Qing Wu • Colin Cole • Wei Hua Ma Received: 10 January 2017 / Revised: 19 January 2018 / Accepted: 23 January 2018 Ó The Author(s) 2018. This article is an open access publication Abstract The feasibility of monitoring the dipped rail defects appear more often than ever before. Short-wave- joint defects has been theoretically investigated by simu- length wheel and rail defects such as wheel flats, squats on lating a locomotive-mounted acceleration system negoti- the rail top surface, rail welds with poor finishing quality, ating several types of dipped rail defects. Initially, a insulated rail joints, rail corrugations cause large dynamic comprehensive locomotive-track model was developed contact forces at the wheel–rail interface, leading to fast using the multi-body dynamics approach. In this model, the deterioration of the track. locomotive car-body, bogie frames, wheelsets and driving The development of squat defects has become a major motors are considered as rigid bodies; track modelling was concern in railway systems throughout the world. The also taken into account. A quantitative relationship findings of extensive field investigations into squat and between the characteristics (peak–peak values) of the axle related rail defects covering the Sydney metropolitan and box accelerations and the rail defects was determined interurban areas are reported [1]. The results of grinding rail through simulations. Therefore, the proposed approach, evidencing squats and the measures proposed to reduce the which combines defect analysis and comparisons with potential for further squat development are also reported. -
TCRP Report 71 –Track-Related Research, Volume 5
TRANSIT COOPERATIVE RESEARCH TCRP PROGRAM REPORT 71 Sponsored by the Federal Transit Administration Track-Related Research Volume 5: Flange Climb Derailment Criteria and Wheel/Rail Profile Management and Maintenance Guidelines for Transit Operations TCRP OVERSIGHT AND PROJECT TRANSPORTATION RESEARCH BOARD EXECUTIVE COMMITTEE 2005 (Membership as of March 2005) SELECTION COMMITTEE (as of February 2005) OFFICERS CHAIR Chair: Joseph H. Boardman, Commissioner, New York State DOT SHARON GREENE Vice Chair: Michael D. Meyer, Professor, School of Civil and Environmental Engineering, Sharon Greene & Associates Georgia Institute of Technology Executive Director: Robert E. Skinner, Jr., Transportation Research Board MEMBERS LINDA J. BOHLINGER MEMBERS HNTB Corp. ROBERT I. BROWNSTEIN MICHAEL W. BEHRENS, Executive Director, Texas DOT Parsons Brinckerhoff Quade & Douglas, Inc. LARRY L. BROWN, SR., Executive Director, Mississippi DOT PETER CANNITO DEBORAH H. BUTLER, Vice Pres., Customer Service, Norfolk Southern Corporation and Subsidiaries, Metropolitan Transit Authority—Metro North Atlanta, GA Railroad ANNE P. CANBY, President, Surface Transportation Policy Project, Washington, DC GREGORY COOK JOHN L. CRAIG, Director, Nebraska Department of Roads Ann Arbor Transportation Authority DOUGLAS G. DUNCAN, President and CEO, FedEx Freight, Memphis, TN JENNIFER L. DORN NICHOLAS J. GARBER, Professor of Civil Engineering, University of Virginia, Charlottesville FTA ANGELA GITTENS, Consultant, Miami, FL NATHANIEL P. FORD GENEVIEVE GIULIANO, Director, Metrans Transportation Center, and Professor, School of Policy, Metropolitan Atlanta RTA Planning, and Development, USC, Los Angeles RONALD L. FREELAND Parsons Transportation Group BERNARD S. GROSECLOSE, JR., President and CEO, South Carolina State Ports Authority FRED M. GILLIAM SUSAN HANSON, Landry University Professor of Geography, Graduate School of Geography, Clark University Capital Metropolitan Transportation Authority JAMES R. -
Visual Inspection of Railroad Tracks
University of Central Florida STARS Electronic Theses and Dissertations, 2004-2019 2009 Visual Inspection Of Railroad Tracks Pavel Babenko University of Central Florida Part of the Computer Sciences Commons, and the Engineering Commons Find similar works at: https://stars.library.ucf.edu/etd University of Central Florida Libraries http://library.ucf.edu This Doctoral Dissertation (Open Access) is brought to you for free and open access by STARS. It has been accepted for inclusion in Electronic Theses and Dissertations, 2004-2019 by an authorized administrator of STARS. For more information, please contact [email protected]. STARS Citation Babenko, Pavel, "Visual Inspection Of Railroad Tracks" (2009). Electronic Theses and Dissertations, 2004-2019. 3990. https://stars.library.ucf.edu/etd/3990 VISUAL INSPECTION OF RAILROAD TRACKS by PAVEL BABENKO M.S. University of Central Florida, 2006 A dissertation submitted in partial fulfillment of the requirements for the degree of Doctor of Philosophy in the School of Electrical Engineering and Computer Science in the College of Engineering and Computer Science at the University of Central Florida Orlando, Florida Fall Term 2009 Major Professor: Mubarak Shah © 2009 by Pavel Babenko ii ABSTRACT In this dissertation, we have developed computer vision methods for measurement of rail gauge, and reliable identification and localization of structural defects in railroad tracks. The rail gauge is the distance between the innermost sides of the two parallel steel rails. We have developed two methods for evaluation of rail gauge. These methods were designed for different hardware setups: the first method works with two pairs of unaligned video cameras while the second method works with depth maps generated by paired laser range scanners. -
100 Part 213—Track Safety Standards
§ 212.233 49 CFR Ch. II (10–1–11 Edition) deemed to meet all requirements of PART 213—TRACK SAFETY this section and is qualified to conduct STANDARDS independent inspections of all types of highway-rail grade crossing warning Subpart A—General systems for the purpose of determining compliance with Grade Crossing Signal Sec. System Safety Rules (49 CFR part 234), 213.1 Scope of part. to make reports of those inspections, 213.3 Application. and to recommend institution of en- 213.4 Excepted track. 213.5 Responsibility for compliance. forcement actions when appropriate to 213.7 Designation of qualified persons to su- promote compliance. pervise certain renewals and inspect [59 FR 50104, Sept. 30, 1994] track. 213.9 Classes of track: operating speed lim- § 212.233 Apprentice highway-rail its. grade crossing inspector. 213.11 Restoration or renewal of track under traffic conditions. (a) An apprentice highway-rail grade 213.13 Measuring track not under load. crossing inspector shall be enrolled in a 213.15 Penalties. program of training prescribed by the 213.17 Waivers. Associate Administrator for Safety 213.19 Information collection. leading to qualification as a highway- rail grade crossing inspector. The ap- Subpart B—Roadbed prentice inspector may not participate 213.31 Scope. in investigative and surveillance ac- 213.33 Drainage. tivities, except as an assistant to a 213.37 Vegetation. qualified State or FRA inspector while accompanying that qualified inspector. Subpart C—Track Geometry (b) Prior to being enrolled in the pro- 213.51 Scope. gram the apprentice inspector shall 213.53 Gage. demonstrate: 213.55 Alinement. -
Visual Measurement System for Wheel–Rail Lateral Position Evaluation
sensors Article Visual Measurement System for Wheel–Rail Lateral Position Evaluation Viktor Skrickij 1 , Eldar Šabanoviˇc 1,* , Dachuan Shi 2, Stefano Ricci 3 , Luca Rizzetto 3 and Gintautas Bureika 1 1 Transport and Logistics Competence Centre, Transport Engineering Faculty, Vilnius Gediminas Technical University, Sauletekio˙ al. 11, 10223 Vilnius, Lithuania; [email protected] (V.S.); [email protected] (G.B.) 2 Institute of Land and Sea Transport Systems, Technical University of Berlin, Strasse des 17. Juni 135, 10623 Berlin, Germany; [email protected] 3 Dipartimento di Ingegneria Civile, Edile e Ambientale (DICEA), Sapienza Università di Roma, Via Eudossiana 18, 00184 Roma, Italy; [email protected] (S.R.); [email protected] (L.R.) * Correspondence: [email protected]; Tel.: +370-5-274-4805 Abstract: Railway infrastructure must meet safety requirements concerning its construction and op- eration. Track geometry monitoring is one of the most important activities in maintaining the steady technical conditions of rail infrastructure. Commonly, it is performed using complex measurement equipment installed on track-recording coaches. Existing low-cost inertial sensor-based measurement systems provide reliable measurements of track geometry in vertical directions. However, solutions are needed for track geometry parameter measurement in the lateral direction. In this research, the authors developed a visual measurement system for track gauge evaluation. It involves the detection of measurement points and the visual measurement of the distance between them. The accuracy of the visual measurement system was evaluated in the laboratory and showed promising results. The initial field test was performed in the Vilnius railway station yard, driving at low velocity on the straight track section.