Condition Monitoring of Rail Transport Systems: a Bibliometric Performance Analysis and Systematic Literature Review
Total Page:16
File Type:pdf, Size:1020Kb
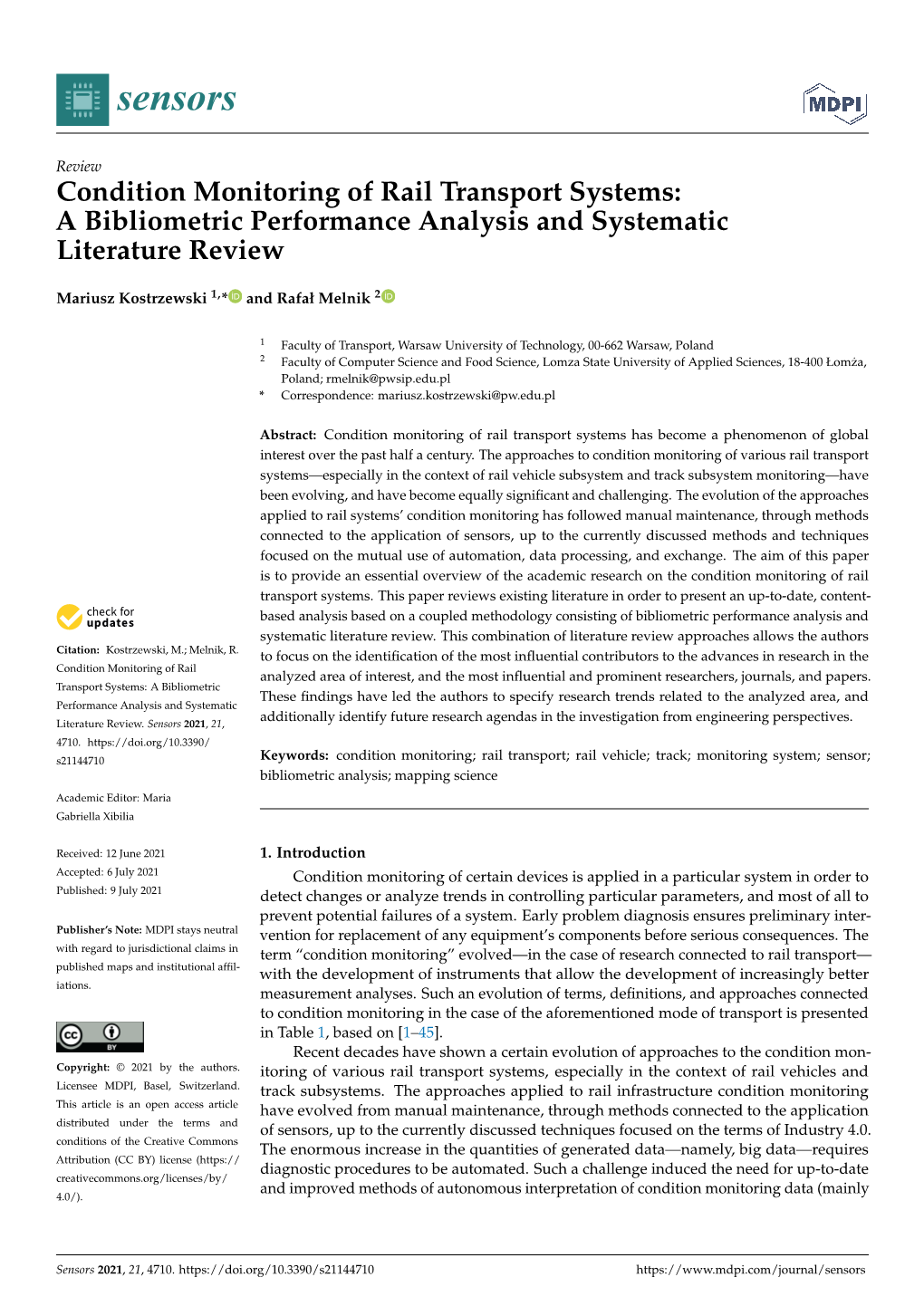
Load more
Recommended publications
-
Status of TTC 2015 06 Final.Pdf
Status of the Transportation U.S. Department of Transportation Technology Center - 2015 Federal Railroad Administration Office of Research, Development, and Technology Washington, DC 20590 DOT/FRA/ORD-16/05 Final Report March 2016 NOTICE This document is disseminated under the sponsorship of the Department of Transportation in the interest of information exchange. The United States Government assumes no liability for its contents or use thereof. Any opinions, findings and conclusions, or recommendations expressed in this material do not necessarily reflect the views or policies of the United States Government, nor does mention of trade names, commercial products, or organizations imply endorsement by the United States Government. The United States Government assumes no liability for the content or use of the material contained in this document. NOTICE The United States Government does not endorse products or manufacturers. Trade or manufacturers’ names appear herein solely because they are considered essential to the objective of this report. REPORT DOCUMENTATION PAGE Form Approved OMB No. 0704-0188 Public reporting burden for this collection of information is estimated to average 1 hour per response, including the time for reviewing instructions, searching existing data sources, gathering and maintaining the data needed, and completing and reviewing the collection of information. Send comments regarding this burden estimate or any other aspect of this collection of information, including suggestions for reducing this burden, to Washington Headquarters Services, Directorate for Information Operations and Reports, 1215 Jefferson Davis Highway, Suite 1204, Arlington, VA 22202-4302, and to the Office of Management and Budget, Paperwork Reduction Project (0704-0188), Washington, DC 20503. -
US Army Railroad Course Railway Track Maintenance II TR0671
SUBCOURSE EDITION TR0671 1 RAILWAY TRACK MAINTENANCE II Reference Text (RT) 671 is the second of two texts on railway track maintenance. The first, RT 670, Railway Track Maintenance I, covers fundamentals of railway engineering; roadbed, ballast, and drainage; and track elements--rail, crossties, track fastenings, and rail joints. Reference Text 671 amplifies many of those subjects and also discusses such topics as turnouts, curves, grade crossings, seasonal maintenance, and maintenance-of-way management. If the student has had no practical experience with railway maintenance, it is advisable that RT 670 be studied before this text. In doing so, many of the points stressed in this text will be clarified. In addition, frequent references are made in this text to material in RT 670 so that certain definitions, procedures, etc., may be reviewed if needed. i THIS PAGE WAS INTENTIONALLY LEFT BLANK. ii CONTENTS Paragraph Page INTRODUCTION................................................................................................................. 1 CHAPTER 1. TRACK REHABILITATION............................................................. 1.1 7 Section I. Surfacing..................................................................................... 1.2 8 II. Re-Laying Rail............................................................................ 1.12 18 III. Tie Renewal................................................................................ 1.18 23 CHAPTER 2. TURNOUTS AND SPECIAL SWITCHES........................................................................................ -
MÁV Central Rail and Track Inspection Ltd
MÁV Central Rail and Track Inspection Ltd. PATER TRACK DIAGNOSTIC EXPERT SYSTEM Besides the knowledge of quality the safe and economical maintenance of railway tracks plays an increasingly impor- tant role these days. The „PATER” track diagnostic ex- pert software is intended to fulfil this task. PATER is a computer program that keeps records of rail- way tracks, monitors their condition and performs mainte- nance planning duties. Its purpose is to assist track mainte- nance professionals in managing the data of the technical and measurement systems, presenting the condition of the track, planning track maintenance jobs depending on track conditions, selecting the appropriate technology and per- forming cost estimates. Rail defects revealed by various inspections This is a client-server based program that ensures that data and their qualification stored in the database can be accessed from anywhere and client users can use them through the internet in case of sufficient authorisation. This model makes it possible that all data is stored and updated in one location therefore the data available to users is always up-to-date. In the engineering practice the val- ues of the isolated defects and gen- eral qualifying indices are analyzed and these values are sufficient to judge the traffic safety and quality. Nowadays we use track geometri- cal, vehicle dynamical, ultrasonic, Space and time based graphical analysis Head Checking, rail profile and rail of track geometry data corrugation measuring devices. The PATER program adapts to the re- quirements of any railway company: unlimited new measuring system, parameter, measuring limit etc. can be integrated quickly and easily. -
the Swindon and Cricklade Railway
The Swindon and Cricklade Railway Construction of the Permanent Way Document No: S&CR S PW001 Issue 2 Format: Microsoft Office 2010 August 2016 SCR S PW001 Issue 2 Copy 001 Page 1 of 33 Registered charity No: 1067447 Registered in England: Company No. 3479479 Registered office: Blunsdon Station Registered Office: 29, Bath Road, Swindon SN1 4AS 1 Document Status Record Status Date Issue Prepared by Reviewed by Document owner Issue 17 June 2010 1 D.J.Randall D.Herbert Joint PW Manager Issue 01 Aug 2016 2 D.J.Randall D.Herbert / D Grigsby / S Hudson PW Manager 2 Document Distribution List Position Organisation Copy Issued To: Copy No. (yes/no) P-Way Manager S&CR Yes 1 Deputy PW Manager S&CR Yes 2 Chairman S&CR (Trust) Yes 3 H&S Manager S&CR Yes 4 Office Files S&CR Yes 5 3 Change History Version Change Details 1 to 2 Updates throughout since last release SCR S PW001 Issue 2 Copy 001 Page 2 of 33 Registered charity No: 1067447 Registered in England: Company No. 3479479 Registered office: Blunsdon Station Registered Office: 29, Bath Road, Swindon SN1 4AS Table of Contents 1 Document Status Record ....................................................................................................................................... 2 2 Document Distribution List ................................................................................................................................... 2 3 Change History ..................................................................................................................................................... -
Track Inspection – 2009
Santa Cruz County Regional Transportation Commission Track Maintenance Planning / Cost Evaluation for the Santa Cruz Branch Watsonville Junction, CA to Davenport, CA Prepared for Egan Consulting Group December 2009 HDR Engineering 500 108th Avenue NE, Suite 1200 Bellevue, WA 98004 CONFIDENTIAL Table of Contents Executive Summary 4 Section 1.0 Introduction 10 Section 1.1 Description of Types of Maintenance 10 Section 1.2 Maintenance Criteria and Classes of Track 11 Section 2.0 Components of Railroad Track 12 Section 2.1 Rail and Rail Fittings 13 Section 2.1.1 Types of Rail 13 Section 2.1.2 Rail Condition 14 Section 2.1.3 Rail Joint Condition 17 Section 2.1.4 Recommendations for Rail and 17 Joint Maintenance Section 2.2 Ties 20 Section 2.2.1 Tie Condition 21 Section 2.2.2 Recommendations for Tie Maintenance 23 Section 2.3 Ballast, Subballst, Subgrade, and Drainage 24 Section 2.3.1 Description of Railroad Ballast, Subballst, 24 Subgrade, and Drainage Section 2.3.2 Ballast, Subgrade, and Drainage Conditions 26 and Recommendations Section 2.4 Effects of Rail Car Weight 29 Section 3.0 Track Geometry 31 Section 3.1 Description of Track Geometry 31 Section 3.2 Track Geometry at the “Micro-Level” 31 Section 3.3 Track Geometry at the “Macro-Level” 32 Santa Cruz County Regional Transportation Commission Page 2 of 76 Santa Cruz Branch Maintenance Study CONFIDENTIAL Section 3.4 Equipment and Operating Recommendations 33 Following from Track Geometry Section 4.0 Specific Conditions Along the 34 Santa Cruz Branch Section 5.0 Summary of Grade Crossing -
Colchester – Package 1 Share with Pride
Colchester – Package 1 Share with Pride 23-Jul-14/ 1 Colchester Station – Project and Planning History PROJECT SCOPE Colchester Station is a key interchange on the Great Eastern Mainline (LTN1) and is historically difficult to block for engineering access. The route through Colchester carries mixed traffic, with large commuter numbers, the single point of access for Electric Freight to Felixstowe Port and a growing leisure market at weekends. The original scope was to deliver 36 Point Ends in Modern Equivalent Form and circa 4100 Linear Metres of Plain Line. The primary driver for the renewal was poor ballast condition leading to Track Quality issues and the associated performance issues. TRACK ACCESS The renewal work for the S&C and PL at Colchester was originally proposed to be delivered a number of years earlier (some elements as long ago as 2008/9). The original planning workshops with the Route, National Express and the Freight Operating Companies explored different vehicles for delivery: - 2x 8 Day Blockades – to complete all works. -1x 16 Day Blockade – to complete all works. - A series of “conventional” 28 and 52 hour Possessions – totalling 26x 52 hour weekends spread over 2 years. These options were discussed in detail with the TOCs and FOCs. There were a number of caveats concerning a blockade strategy. The FOCs would still have had to pass trains through Colchester due to a lack of capacity on the non electrified diversionary route and the TOCs requested to run a service in from both Country and London through the midweek elements of the blockade due to the physical number of passengers they needed to move. -
Conceptual Railway Signaling Online Live Training
CONCEPTUAL RAILWAY SIGNALING ONLINE LIVE TRAINING MASTER TRAINER: NARAYAN PARVATIKAR RAILWAYACADEMY [email protected], +91 9810989077 Program Brief This program is a concept-based program and will usually be carried out in live mode delivered online by trainer. It shall cover the theory- based Principles of Railway Signaling and students will undergoing the course shall learn concepts of railway signalling and control systems in Indian Railway Context. Duration 30 sessions of 45 min live training classes in live group interaction with Railway Expert after each module Target Audiences • Fresh Engineering graduates looking for employment in Railway Sector • Working Professionals sponsored by Industry to upgrade skills • Self Sponsored working professionals looking for career in railways telecommunications Fee • INR 36,000/- (INR Thirty Six Thousand only) to paid in three installments) inclusive of GST o 1st installment: at the time of registration: Pay online https://imjo.in/PzM6eQ o 2nd installment: Before 9th class o 3rd installment: Before 15th class • One Time Payment Offer: INR 27,000/- (INR Twenty Seven thousand only) inclusive of GST: Pay online https://imjo.in/kAA3hs Trainer Profile: Narayan Parvatikar Railway Signal Engineer with 37+ years of experience with Indian Railways and other MNCs. More than 23 years of experience in Training. Program Syllabus Sl No Contents 1 • General information • Contents and self-introduction • Why separate signaling for railways • Topics covered • Takeaway • Feedback and queries 2 • Railway -
Customer Track Maintenance Guide Winter Safety
Customer Track Maintenance Guide Winter Safety Safety is of the utmost importance at CN, not only for our employees but Our goal is to move your products as quickly and safely as possible. also for you, our customers. Please contact your service delivery representative or account manager if you have any questions. We’ve developed this Customer Track Maintenance Guide in order to help bring attention to the additional hazards that are present during the winter Additional information on our seasonal safety guidelines can be found at: months, especially for our crews performing switching activities. www.cn.ca/seasonalsafety Winter is a challenging time for a railroad; many of the service disruptions are caused by accumulations of snow and ice. On the track, problems with switches and crossings are mainly caused by snow — so clearing the snow solves the problem. 3 Flangeways wheel flange Be particularly vigilant where flangeways can be become contaminated with snow, ice, or other material, or where any trackage is covered by excessive amounts of snow or ice, or other material. Ensure equipment can be carefully operated through flangeway over such track. flangeway Be especially aware at crossings, as these are prone to these types minimum of 1.5” clear rail of conditions. of ice, snow, mud, etc. At a minimum, flangeways must be cleared to a depth of 1.5”. Acceptable: Not acceptable: 4 Switches Be aware that switches can become very difficult to line due to cold weather and snow/ice build-up in the switch points. Attempting to line a stiff switch can and does lead to back, leg and arm injuries. -
Rail Accident Report
Rail Accident Report Derailment of a passenger train near Cummersdale, Cumbria 1 June 2009 Report 06/2010 March 2010 This investigation was carried out in accordance with: l the Railway Safety Directive 2004/49/EC; l the Railways and Transport Safety Act 2003; and l the Railways (Accident Investigation and Reporting) Regulations 2005. © Crown copyright 2010 You may re-use this document/publication (not including departmental or agency logos) free of charge in any format or medium. You must re-use it accurately and not in a misleading context. The material must be acknowledged as Crown copyright and you must give the title of the source publication. Where we have identified any third party copyright material you will need to obtain permission from the copyright holders concerned. This document/publication is also available at www.raib.gov.uk. Any enquiries about this publication should be sent to: RAIB Email: [email protected] The Wharf Telephone: 01332 253300 Stores Road Fax: 01332 253301 Derby UK Website: www.raib.gov.uk DE21 4BA This report is published by the Rail Accident Investigation Branch, Department for Transport. * Cover photo courtesy of Network Rail Derailment of a passenger train near Cummersdale, Cumbria, 1 June 2009 Contents Preface 5 Key Definitions 5 The Accident 6 Summary of the accident 6 The parties involved 7 Location 8 External circumstances 8 The trains involved 10 Events preceding the accident 10 Events during the accident 10 Consequences of the accident 11 Events following the accident 11 The Investigation -
Trends in the Share of Railways in Transportation
www.cepal.org/transporte Issue No. 303 - Number 11 / 2011 BULLETIN FACILITATION OF TRANSPORT AND TRADE IN LATIN AMERICA AND THE CARIBBEAN This issue of the FAL Bulletin analyses the history of railways in modal distribution Trends in the share in Latin America, and puts forward recommendations for improving their functioning and making them a real, of railways competitive and sustainable transport option. The study is part of the activities being in transportation conducted by the Unit in the project on “Strategies for environmental sustainability: climate change and energy”, funded by the Spanish Agency for International Development Cooperation (AECID). The author of this issue of the Bulletin is Introduction Gonzalo Martín Baranda, Consultant for the Infrastructure Services Unit of ECLAC. For additional information please contact Railways flourished in the nineteenth century, becoming a key element [email protected] in the transport of goods and passengers For a number of reasons, Introduction however, their prominence has gradually diminished and they now have only a limited role, mostly in the transportation of certain bulk products. I. The rise of railways This document looks at the how the use of the railways for freight has II. Recent history of railways changed over the years, and puts forward a series of recommendations in Latin America to increase their use in present-day Latin America. III. Consideration of externalities and associated social costs I. The rise of railways for sustainable modal choices IV. The role of railways in modal shifts Railways rose to prominence in the nineteenth century, leading to a radical change in the surface transport of freight and passengers, and V. -
Investigation of Glued Insulated Rail Joints with Special Fiber-Glass Reinforced Synthetic Fishplates Using in Continuously Welded Tracks
CORE Metadata, citation and similar papers at core.ac.uk Provided by Repository of the Academy's Library POLLACK PERIODICA An International Journal for Engineering and Information Sciences DOI: 10.1556/606.2018.13.2.8 Vol. 13, No. 2, pp. 77–86 (2018) www.akademiai.com INVESTIGATION OF GLUED INSULATED RAIL JOINTS WITH SPECIAL FIBER-GLASS REINFORCED SYNTHETIC FISHPLATES USING IN CONTINUOUSLY WELDED TRACKS 1 Attila NÉMETH, 2 Szabolcs FISCHER 1,2 Department of Transport Infrastructure, Széchenyi István University Győr, Egyetem tér 1 H-9026 Győr, Hungary, email: [email protected], [email protected] Received 29 December 2017; accepted 9 March 2018 Abstract: In this paper the authors partially summarize the results of a research on glued insulated rail joints with fiber-glass reinforced plastic fishplates (brand: Apatech) related to own executed laboratory tests. The goal of the research is to investigate the application of this new type of glued insulated rail joint where the fishplates are manufactured at high pressure, regulated temperature, glass-fiber reinforced polymer composite plastic material. The usage of this kind of glued insulated rail joints is able to eliminate the electric fishplate circuit and early fatigue deflection and it can ensure the isolation of rails’ ends from each other by aspect of electric conductivity. Keywords: Glued insulated rail joint, Fiber-glass reinforced fishplate, Polymer composite plastic material, Laboratory test 1. Introduction The role of the rail connections (rail joints) is to ensure the continuity of rails without vertical and horizontal ‘step’, as well as directional break. The opportunities to connect rails are the fishplate joints, welding, and dilatation structure (rail expansion device) [1]. -
Operating Manual for Indian Railways
OPERATING MANUAL FOR INDIAN RAILWAYS GOVERNMENT OF INDIA MINISTRY OF RAILWAYS (RAILWAY BOARD) INDEX S.No. Chapters Page No. 1 Working of Stations 1-12 2 Working of Trains 13-14 3 Marshalling 15-18 4 Freight Operation 19-27 5 Preferential Schedule & Rationalization Order 28 6 Movement of ODC and Other Bulky Consignment 29-32 7 Control Organisation 33-44 8 Command, Control & Coordination of Emergency Rescue Operations on the open line 45-54 9 Marshalling Yards and Freight Terminals 55-67 10 Container Train Operation 68-72 11 Customer Interface and Role of Commercial Staff 73-77 12 Inspections 78-83 13 Interlocking 84-92 14 Station Working Rules and Temporary Working Order 93-102 15 Non-Interlocked Working of Station 103-114 16 Operating Statistics 115-121 17 FOIS 122-146 I.C.M.S - Module in ICMS - System - Data Feeding 147-148 - - MIS Reports 18 C.O.A 149 19 ACD 150 20 Derailment Investigation 151-158 21 Concept of Electric Traction 159-164 Crew link, loco link & power plant 165-166 Electric Loco maintenance schedule Diesel Loco maintenance schedule 167-169 Features of Electric Locomotives Brake power certificate 170 Various machines used for track maintenance 171 WORKING OF STATIONS (Back to Index) Railway Stations, world wide, are located in prime city centres, as railways were started at a time when expansion of cities was yet to start. Railway station continues to be the focal point of central business district in all cities in the world. All description of rail business is transacted at the station, passengers start journey or complete it, outward parcels are booked and inward parcel consignments received and kept ready for delivery.