Paperboard Grades
Total Page:16
File Type:pdf, Size:1020Kb
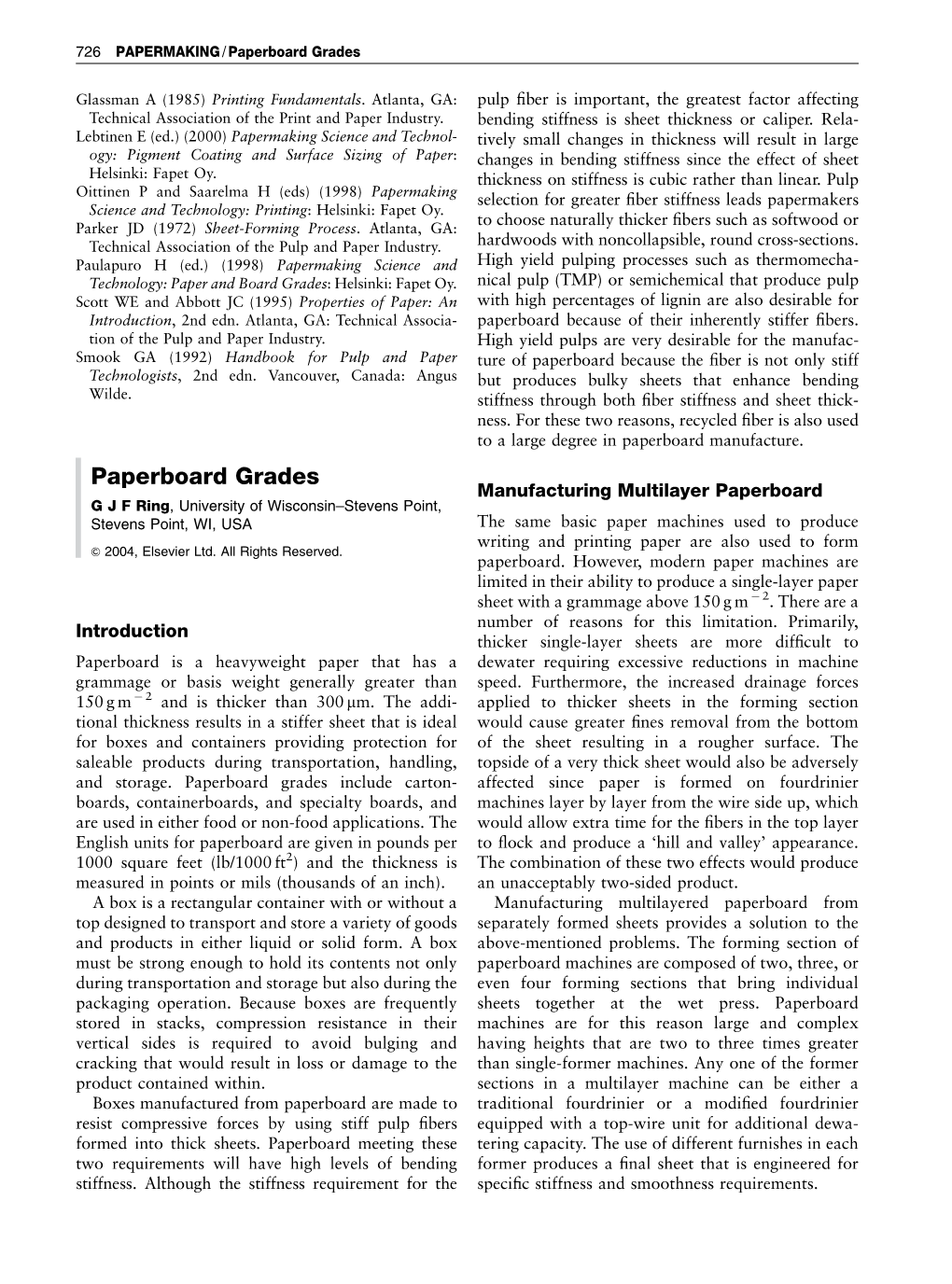
Load more
Recommended publications
-
Understanding Matboard
FRAMING FUNDAMENTALS by Jared Davis, MCPF, GCF Understanding Matboard Being the best frame shop in your area starts with the best products. atboard is a fundamental compo- Mnent of almost every framed pic- ture. However, understanding the vast range of information and choices avail- able in matboards can be daunting. In this article, I aim to provide some useful insights about matboard to help you to dispel some of the myths and decipher some of the facts about this vital aspect of our profession. The two primary purposes for matboard that the introduction of a matboard can in- Different grades of matboard are are to provide protection for the artwork and crease both the size and level of value in the designed for to enhance the framing design. sale of a frame. different appli- cations. Under- 1) Protect. The last consumer survey con- standing which choice to make is ducted by the Professional Picture Fram- How Matboard is Made important to both ers Association found that the num- Matboards are comprised of layers of pa- your customer and your business. ber-one reason why a consumer chose to per of various thickness, laminated together. custom frame an artwork was to protect The papers and core of a matboard are made the item. Preservation, clearly, is of prima- from either unpurified wood pulp, purified al- ry importance to your customer. pha-cellulose wood pulp, or in the case of mu- 2) Enhance. A matboard can help the view- seum-grade board, cotton linter pulp. er to focus correctly on the image. -
Decreased Wet Strength in Retorted Liquid Packaging Board Master of Science Thesis in the Master Degree Programme Materials and Nanotechnology
Decreased Wet Strength in Retorted Liquid Packaging Board Master of Science thesis in the Master Degree Programme Materials and Nanotechnology MARIA GUNNARSSON Department of Chemical and Biological Engineering Division of Organic chemistry CHALMERS UNIVERSITY OF TECHNOLOGY Göteborg, Sweden 2012 Report No. 2012:001 Decreased wet strength in retorted liquid packaging board Master of Science Thesis MARIA GUNNARSSON SUPERVISOR: Gunnar Westman EXAMINER: Gunnar Westman Department of Chemical and Biological engineering CHALMERS UNIVERSITY OF TECHNOLOGY Göteborg, Sweden, 2012 Decreased wet strength in retorted liquid packaging board MARIA GUNNARSSON ©MARIA GUNNARSSON, 2012 Report no 2012:001 Department of Chemical and Biological Engineering Chalmers University of Technology SE-412 96 Göteborg Sweden Telephone +46 (0)31-7721000 Cover: The Tetra Recart packaging. Department of Chemical and Biological Engineering Göteborg, Sweden 2012 Decreased wet strength in retorted liquid packaging board Maria Gunnarsson Department of Chemical and Biological Engineering Division of Organic Chemistry CHALMERS UNIVERSITY OF TECHNOLOGY ABSTRACT The Tetra Recart is a retortable food packaging, suitable for high viscous products, making it able to replace most food cans used for storage of food today. The packaging is built up by a paperboard, consisting of an unbleached bottom layer and a bleached top layer. Polymers and aluminium further cover the paperboard in order to protect the food against moisture and light, causing degradation. During the retorting process, the packaging develops a certain wet strength making it hard to disintegrate the pulp fibres in the board. The phenomenon of the developed wet strength is of high interest when inventing and developing new packaging materials. To investigate why and how the phenomenon occurs, a series of trials were made through production of laboratory sheets with subsequent disintegration. -
A Guide to Packaging Material Flows and Terminology Pollution Is Nothing but the Resources We Are Not Harvesting
A Guide to PAckAGinG MAteriAl Flows And terMinoloGy Pollution is nothing but the resources we are not harvesting. We allow them to disperse because we’ve been ignorant of their value. R. Buckminster Fuller A Guide to Packaging Material Flows and Terminology The work upon which this publication is based was funded, in whole, through grants awarded by the California Department of Conservation and GreenBlue through its Sustainable Packaging Coalition®. The statements and conclusions of this report are those of GreenBlue and not necessarily those of the Department of Conservation or its employees. The Department makes no warranties, express or implied, and assumes no liability for the information contained in the succeeding text. The Guide to Packaging Material Flows and Terminology is issued “as is” and with all faults. We give no express warranties, guarantees or conditions. You may have additional rights under local laws which this disclaimer cannot change. However, to the extent permitted under applicable laws, the Green Blue Institute makes no warranty of any kind, either express or implied, including but not limited to, any implied warranties of merchantability, fitness for a particular purpose or non–infringement. The Scrap Specifications Circular 2008 is © 2008 Institute of Scrap Recycling Industries, Inc. (ISRI), 1615 L Street, N.W., Suite 600, Washington, DC 20036, and portions were used by permission. ISRI’s Scrap Specifications Circular is subject to change; therefore, readers should contact ISRI or go to http://www.isri. org/specs to make certain they are reading the most recent version of the Scrap Specifications Circular. Closing the Loop: A Guide to Packaging Material Flows and Terminology Closing the Loop: A Guide to Packaging Material Flows and Terminology was developed by GreenBlue®, a nonprofit institute that works with the private sector to enable the positive redesign of industrial systems. -
26 the Carton Packaging Fact File CARTONBOARD
26 The Carton Packaging Fact File CARTONBOARD 5 The Carton Packaging Fact File 27 KEY FACTS Cartonboard is a multilayered material. The main types of cartonboard are solid bleached board, solid unbleached board, folding boxboard and white lined chipboard. Cartonboard usually has a white, pigmented coating on one or both surfaces Cartonboard specifications Cartonboard can be vary with respect to the pulp combined with other composition of the various materials to vary the visual layers and by the grammage appearance and to extend (weight per sq. metre in the protective properties grammes) and thickness (microns or 0.001 millimetre) Laminations, coatings and impregnations can be added to extend the range of carton applications 28 The Carton Packaging Fact File CARTONBOARD COMMON ABBREVIATIONS SBB Solid Bleached Board SUB Solid Unbleached Board FBB Folding Box Board WLC White Lined Chipboard Different types and grades the range 200-600g/m 2 for grammage product aroma, flavour and hygiene are of cartonboard and their and 350-800µm for thickness. critical. Examples of cartons where abbreviations. The principles SBB is used are perfumes, cosmetics, of cartonboard manufacture, What are the main characteristics chocolates, pharmaceuticals, frozen developments and treatments of cartonboard? foods and cigarettes. Cartonboard is mechanically strong. What is cartonboard? Its stiffness, rigidity and toughness SBB is sometimes referred to as SBS Cartonboard is a multilayer material provide compression strength to protect or GZ. with, usually, three or more layers, or products in distribution and use. It can plies, of cellulose fibre (pulp) derived be cut, creased, folded and glued, giving What is Solid Unbleached Board? from wood. -
Staff Paper Series Number 206 : United States Wood-Based Industry: a Review of Structure and Organization
UNITED STATES WOOD-BASED INDUSTRY: A REVIEW OF STRUCTURE AND ORGANIZATION by Paul V. Ellefson and Michael A. Kilgore January 2010 STAFF PAPER SERIES NUMBER 206 Department of Forest Resources College of Food, Agricultural and Natural Resources Sciences University of Minnesota St. Paul, MN 55108 For more information about the Department of Forest Resources and its teaching, research, and outreach programs, contact the Department at: Department of Forest Resources University of Minnesota 115 Green Hall 1530 N. Cleveland Avenue North St. Paul, MN 55108-6112 Ph: 612-624-3400 Fax: 612-625-5212 Email: [email protected] http://forestry.umn.edu/publications/staffpapers/index.html The University of Minnesota is committed to the policy that all persons shall have equal access to its programs, facilities, and employment without regard to race, color, creed, religion, national origin, sex, age, martial status, disability, public assistance status, veteran status, or sexual orientation UNITED STATES WOOD-BASED INDUSTRY: A REVIEW OF STRUCTURE AND ORGANIZATION by Paul V. Ellefson and Michael A. Kilgorea January 2010 a Professors, Department of Forest Resources, University of Minnesota, St. Paul, MN. Research supported by Minnesota Agricultural Experim ent Station; Research and Developm ent-RPA Assessment Program, Forest Service, U.S. Departm ent of Agriculture, Washington, DC; and the Southern Research Station, Forest Service, U.S. Department of Agricultural, New Orleans, LA. Contents Page INTRODUCTION 1 TIMBER GROWING INDUSTRY 1 General Character -
Clarification Announcement
The Stock Exchange of Hong Kong Limited takes no responsibility for the contents of this announcement, makes no representation as to its accuracy or completeness and expressly disclaims any liability whatsoever for any loss howsoever arising from or in reliance upon the whole or any part of the contents of this announcement. * (Incorporated in Bermuda with limited liability) (Stock Code: 2689) CLARIFICATION ANNOUNCEMENT This announcement intends to clarify certain matters following the recent meetings of the Directors with investors and analysts of international research institutions regarding the Company’s progress in new products development and upstream expansion plan. In the recent meetings of the directors of the Company (the “Directors”) with investors and analysts of international research institutions, the Directors noted keen interests from the investors and analysts on the Company’s progress in new products development and upstream expansion plan. In this connection, the Directors wish to clarify the progress made by the Company in its development of new products and upstream expansion. Sichuan Factories In December 2007, the Company entered into agreements with three independent third parties (the “Vendors”) in Sichuan Province pursuant to which the Company agreed to acquire (the “Acquisition”) from the Vendors (i) Sichuan Qian Wei Baiya Paper Co. Ltd. (“Qian Wei”) and (ii) Sichuan Rui Song Paper Co. Ltd. (“Rui Song”). Qian Wei Pursuant to the sale and purchase agreements (the “Qian Wei Agreements”) for the acquisition of Qian Wei, the Vendors transferred their entire equity interests in Qian Wei to the Group free of consideration. Except for those items which the Group has expressly agreed to be responsible, the Vendors will be responsible for all debts and liabilities of Qian Wei prior to completion of the acquisition. -
Making Paper from Trees
Making Paper from Trees Forest Service U.S. Department of Agriculture FS-2 MAKING PAPER FROM TREES Paper has been a key factor in the progress of civilization, especially during the past 100 years. Paper is indispensable in our daily life for many purposes. It conveys a fantastic variety and volume of messages and information of all kinds via its use in printing and writing-personal and business letters, newspapers, pamphlets, posters, magazines, mail order catalogs, telephone directories, comic books, school books, novels, etc. It is difficult to imagine the modern world without paper. Paper is used to wrap packages. It is also used to make containers for shipping goods ranging from food and drugs to clothing and machinery. We use it as wrappers or containers for milk, ice cream, bread, butter, meat, fruits, cereals, vegetables, potato chips, and candy; to carry our food and department store purchases home in; for paper towels, cellophane, paper handkerchiefs and sanitary tissues; for our notebooks, coloring books, blotting paper, memo pads, holiday greeting and other “special occasion’’ cards, playing cards, library index cards; for the toy hats, crepe paper decorations, paper napkins, paper cups, plates, spoons, and forks for our parties. Paper is used in building our homes and schools-in the form of roofing paper, and as paperboard- heavy, compressed product made from wood pulp-which is used for walls and partitions, and in such products as furniture. Paper is also used in linerboard, “cardboard,” and similar containers. Wood pulp is the principal fibrous raw material from which paper is made, and over half of the wood cut in this country winds up in some form of paper products. -
The Renaissance Spreads Outside of Italy
5/9/2019 Big Idea The Renaissance Spreads Outside of Italy Essential Question How did the Renaissance spread to the rest of Europe? 1 5/9/2019 Words To Know Renaissance - “rebirth” in French, the Renaissance was a cultural movement in the 14th-17th centuries during which European artists, scientists, and scholars, were inspired by the achievements of the Greeks and Romans. Let’s Set The Stage… As the Renaissance began to grow in Italy, northern Europe was still recovering from the ravages of the Black Death. But by the 1400s, the cities of the north began to enjoy the economic growth—and the wealth—needed to develop their own Renaissance. 2 5/9/2019 The Spread of Wealth Through Trade Trade routes that existed since the Roman Empire were infused by new wealth and products when trade between the Italian city-states and the Ottoman Empire increased. The Spread of Wealth Through Trade As a result, cities like Cologne, Bruges, Paris, London, and Lisbon became centers of trade and banking. Like in Italian cities, trade led to the establishment of a wealthy class of traders and bankers who supported architects and paid for work from artists. 3 5/9/2019 Papermaking By 1300, papermaking and printing technology reached Europe from China and the Middle East. Papermaking Paper making had contributed to golden ages in China and the Middle East, and to the preservation (saving) of Greek and Roman learning that had been “lost” in Europe and preserved (saved) by scholars (students) in the Ottoman Empire. 4 5/9/2019 The Earliest Books The earliest books were written on scrolls. -
Dokument Herunterladen
Reno De Medici Paris European Midcap Event 27 June 2018 Agenda 1 Overview 2 RDM Features and Strategic Guidelines 3 Delivering on Strategy 4 RDM Shares and Final Remarks 2 Some numbers… 2017 net Milan and Madrid revenues of Stock Exchange €569 million 1,487 Annual capacity of employees 1,050,000 tons (2017YE) 6 mills Commercial 2 sheeting network in 70 centers Countries 3 A PanEuropean asset base Three assets with capacity well above 200k tons/p.a. Ovaro mill focused on high-margin specialties. WLC White Lined Chipboard FBB Folding Boxboard GER, Arnsberg 220k tons LINER/GD WLC FRA, Blendecques ITA, S.Giustina 110k tons 240k tons WLC WLC ITA, Ovaro 95k tons OG-GK RDM La Rochette FRA, La Rochette (FBB business) 165k tons ITA, Villa S.Lucia included in the P&L GC-FBB 220k tons LINER WLC consolidation perimeter of RDM starting from H2 2016. 4 Our virtuous circle Consumers Recycled paper collectors Carton board producers Distributors Converters End users 5 With our cartonboard… Our cartonboard is used to produce a huge quantity of product we use every day. Any examples? 6 Market segmentation Packaging applications and, to a lesser extent, graphic purposes drive cartonboard production. SBB - Solid Bleached Sulphate Board (GZ/UZ) Based on virgin fiber FBB - Folding Boxboard (GC/UC); WLC - White Lined Chipboard (GD/UD) and Based on recycled fiber Triplex Board (GT/UT). European cartonboard demand (2016) SBS 8 % In the last few years, until H1 2016, RDM production was focused on one business FBB segment: White Lined Chipboard, “WLC”. WLC 32 % 52 % Following to the acquisition of La Rochette mill (30 June 2016), RDM is also involved in the “FBB” business. -
Folding Boxboards, White-Top Kraftliners and Fully Bleached Linerboards
Metsä Board Analyst day and site visit in Husum, Sweden 29 August 2016 Contents Growth with high-performance paperboards Seppo Puotinen, SVP, Marketing and Sales Production update and Husum investment programme Ari Kiviranta, SVP, Production and technology Financial performance Markus Holm, CFO Husum integrate Pertti Hietaniemi, Mill manager Growth with high-performance paperboards Seppo Puotinen, SVP Marketing and Sales Focus on premium fresh fibre paperboards Folding boxboards, white-top kraftliners and fully bleached linerboards Consumer goods Retail-ready Food service 4 Husum 08/2016 Metsä Board’s broad spectrum of customers BRAND OWNERS CONVERTERS CORRUGATED BOX folding cartons MANUFACTURERS and food service MERCHANTS Graphics and packaging FOLDING BOXBOARD WHITE LINERBOARDS fresh forest fibre-based 5 Husum 08/2016 Average annual growth target of 13% (2015–18) is based on new paperboard volumes from Husum Incremental volume of A total of 400,000 tonnes linerboard after the ceased of new FBB capacity paper production 2 000 150 150 1 500 250 tonnes 1 000 1,000 500 0 Deliveries in 2015 Folding boxboard to Food service board Linerboard to Targeted deliveries Americas globally Europe and in 2018 Americas 6 Husum 08/2016 Geographical growth focus is in Americas Targeted FBB deliveries in 2018 mainly from Husum Deliveries to Americas, 1,000 tonnes 300 300 250 250 200 tonnes 150 1,000 100 50 0 2011 2012 2013 2014 2015 2018 target FBB and FSB Linerboard 7 Husum 08/2016 Global folding boxboard market is about 9Mt/a Total cartonboard market*) is about 36 Mt/a North America 6 Mt/a EMEA 8 Mt/a APAC 20 Mt/a Folding boxboard Other fresh forest fibre grades Recycled grades Lat. -
Four Great Inventions of China Many of the Greatest Inventions in Human History Were First Made in China
History Topic of the Month Four Great Inventions of China Many of the greatest inventions in human history were first made in China. By the 13th century, China was an innovative and exciting place to live. Travellers from Europe discovered things there that were beyond imagination in Europe. When the explorer Marco Polo arrived in China, he encountered a Contributer: © Patrick Guenette / 123rf country vastly different from his home of Venice. In his book, The Travels of Marco Polo, Polo describes cities Cai Lun (AD c.57 – 121), was a Chinese courtier official. He is believed to with broad, straight and clean streets (very different from his be the inventor of paper and the home in Venice) where even the poorest people could wash papermaking process, discovering in great bath houses at least three time a week (again very techniques that created paper as we different from hygiene in Europe). would recognise it today. China celebrates four particular innovations as “the Four Great Inventions” — they were even featured as a part of the opening ceremony for the 2008 Beijing Olympic Games. So, what were these four great inventions? Writing it all down: Paper The first of the great inventions was something we all use almost every day: paper. Many different materials had been used for writing things down, like bamboo, wood (both hard to store and write on) or silk and cloth (much more expensive). Types of paper have been found in archaeological records dating back thousands of years, but it was very difficult to make. It wasn’t until AD c.105 that a quick and easy way of making paper was invented. -
Japanese Papermaking
A Guide To Japanese Papermaking Making Japanese Paper in the Western World Donald Farnsworth 3rd Edition A Guide To Japanese Papermaking Making Japanese Paper in the Western World Donald Farnsworth 3rd edition ISBN: 978-0-9799164-8-9 © 1989, 1997, 2018 Donald S. Farnsworth English translations © 1948 Charles E. Hamilton MAGNOLIA EDITIONS 2527 Magnolia St, Oakland CA 94607 Published by Magnolia Editions, Inc. www.magnoliapaper.com Table of Contents Author’s Preface 1 (Kunisaki Jihei, 1798; trans. Charles E. Hamilton, 1948) Introduction 3 Equipment (contemporary) 8 Cooking 23 ACKNOWLEDGMENTS Bleaching 27 I. Sunlight Bleaching (ultraviolet light) 28 Japanese text by Kunisaki Jihei and woodcut illustrations by Seich- II. Hydrogen Peroxide Bleaching 29 uan Tōkei are reproduced from a 1925 edition of Kamisuki chōhōki III. Chlorine Bleaching 30 (A Handy Guide to Papermaking), first published in 1798. Beating 31 Charles E. Hamilton's translations are reproduced from the 1948 Pigmenting 37 English language edition of A Handy Guide to Papermaking pub- Dyeing 39 lished by the Book Arts Club, University of California, Berkeley. Formation Aid 45 With the 1948 edition now out of print and increasingly difficult Mixing Formation aid powder PMP 46 to find, I hope to honor Mr. Hamilton's efforts by bringing his thoughtful and savvy translations to a broader audience. His trans- Contemporary vat, wooden stirring comb... 48 lations appear italicized and circumscribed in the following text. Sheet Formation 51 I. Japanese: Su and Keta 54 I would like to acknowledge Mr. Fujimori-san of Awagami Paper II. Pouring Method 59 and his employees, Mr. Yoshida-san and his employees, for fur- thering my understanding of Japanese papermaking.