AERODYNAMICS and STATIC STABILITY INVESTIGATION of a V-TAIL LAYOUT USING CFD METHODS and VARIOUS TURBULENCE MODELS Georgios N
Total Page:16
File Type:pdf, Size:1020Kb
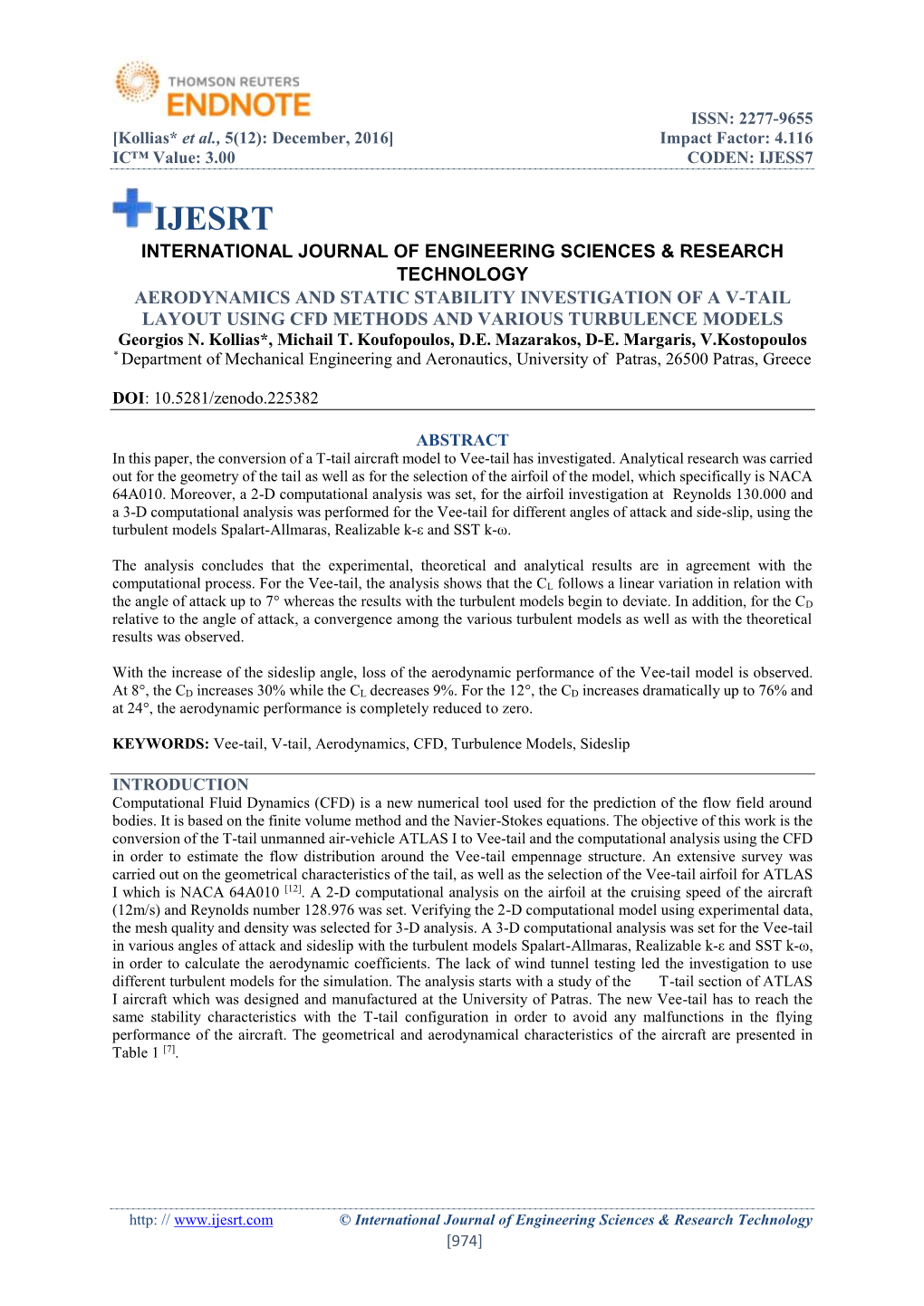
Load more
Recommended publications
-
Glider Handbook, Chapter 2: Components and Systems
Chapter 2 Components and Systems Introduction Although gliders come in an array of shapes and sizes, the basic design features of most gliders are fundamentally the same. All gliders conform to the aerodynamic principles that make flight possible. When air flows over the wings of a glider, the wings produce a force called lift that allows the aircraft to stay aloft. Glider wings are designed to produce maximum lift with minimum drag. 2-1 Glider Design With each generation of new materials and development and improvements in aerodynamics, the performance of gliders The earlier gliders were made mainly of wood with metal has increased. One measure of performance is glide ratio. A fastenings, stays, and control cables. Subsequent designs glide ratio of 30:1 means that in smooth air a glider can travel led to a fuselage made of fabric-covered steel tubing forward 30 feet while only losing 1 foot of altitude. Glide glued to wood and fabric wings for lightness and strength. ratio is discussed further in Chapter 5, Glider Performance. New materials, such as carbon fiber, fiberglass, glass reinforced plastic (GRP), and Kevlar® are now being used Due to the critical role that aerodynamic efficiency plays in to developed stronger and lighter gliders. Modern gliders the performance of a glider, gliders often have aerodynamic are usually designed by computer-aided software to increase features seldom found in other aircraft. The wings of a modern performance. The first glider to use fiberglass extensively racing glider have a specially designed low-drag laminar flow was the Akaflieg Stuttgart FS-24 Phönix, which first flew airfoil. -
ICE PROTECTION Incomplete
ICE PROTECTION GENERAL The Ice and Rain Protection Systems allow the aircraft to operate in icing conditions or heavy rain. Aircraft Ice Protection is provided by heating in critical areas using either: Hot Air from the Pneumatic System o Wing Leading Edges o Stabilizer Leading Edges o Engine Air Inlets Electrical power o Windshields o Probe Heat . Pitot Tubes . Pitot Static Tube . AOA Sensors . TAT Probes o Static Ports . ADC . Pressurization o Service Nipples . Lavatory Water Drain . Potable Water Rain removal from the Windshields is provided by two fully independent Wiper Systems. LEADING EDGE THERMAL ANTI ICE SYSTEM Ice protection for the wing and horizontal stabilizer leading edges and the engine air inlet lips is ensured by heating these surfaces. Hot air supplied by the Pneumatic System is ducted through perforated tubes, called Piccolo tubes. Each Piccolo tube is routed along the surface, so that hot air jets flowing through the perforations heat the surface. Dedicated slots are provided for exhausting the hot air after the surface has been heated. Each subsystem has a pressure regulating/shutoff valve (PRSOV) type of Anti-icing valve. An airflow restrictor limits the airflow rate supplied by the Pneumatic System. The systems are regulated for proper pressure and airflow rate. Differential pressure switches and low pressure switches monitor for leakage and low pressures. Each Wing's Anti Ice System is supplied by its respective side of the Pneumatic System. The Stabilizer Anti Ice System is supplied by the LEFT side of the Pneumatic System. The APU cannot provide sufficient hot air for Pneumatic Anti Ice functions. -
V-Tails for Aeromodels
Please see the V-Tails for Aeromodels recommendations for Yet Another Attempt to Explain Them the browser settings Watching the RCSE forum during November 1998 I felt, that the discussion on V-tails is not always governed by facts and knowledge, but feelings and sometimes even by irritation. I think, some theory of V-tails should be compiled and written down for aeromodellers such that we can answer most of the questions by ourselves. V- tails are almost never used with full scale airplanes but not all of the reasons for this are also valid for aeromodels. As a consequence V-tails are not treated appropriately in standard literature. This article contains well known and also some not so well known facts on V-tails and theoretical explanations for them; I don't claim anything to be "new". I also list some occasionally to be heard statements, which are simply not true. If something is wrong or missing: Please let me know ([email protected]), or, if you think that this article is a valuable contribution to make V- tails clearer for aeromodellers. Introduction Almost always designing a V-tail means converting a standard tail into a V-tail; the reasons are clear: Calculations yield specifications of a standard tail or an existing model is really to be converted (the photo above documents the end of the 2nd life of this glider;-). The task is to find a V-tail, which behaves "exactly like its corresponding" standard- or T-tail - we will see, that this is not possible. We can design the V-tail to have the same behaviour in many respects, we might get some advantages, but we have to pay a price. -
Chapter 55 Stabilizers
EXTRA - FLUGZEUGBAU GmbH SERVICE MANUAL EXTRA 200 Chapter 55 Stabilizers PAGE DATE: 1. July 1996 CHAPTER 55 PAGE 1 EXTRA - FLUGZEUGBAU GmbH SERVICE MANUAL EXTRA 200 Table of Contents Chapter Title 55-00-00 GENERAL . 3 55-21-00 MAINTENANCE PRACTICES . 8 55-21-01 Horizontal Stabilizer . 8 55-21-02 Vertical Stabilizer . 10 PAGE DATE: 1. July 1996 CHAPTER 55 PAGE 2 EXTRA - FLUGZEUGBAU GmbH SERVICE MANUAL EXTRA 200 55-00-00 GENERAL The EXTRA 200 has a conventional empennage with stabilizers and moveable control surfaces. The spars con- sist of carbon roving caps, carbon fibre webs and PVC foam cores. The shells are built of honeycomb sandwich with glass fibre or optional carbon fibre laminate. Also buckling is prevented by plywood ribs. Deviating from this, the elevator is constructed in the same manner as the ailerons (refer to Chapter 57). On the R/H elevator half a trim tab is fitted with a piano hinge. The layer sequences of the stabilizers, the elevator and the rudder are shown in Figures 1-2. All composite parts, as protection against moisture and UV radiation, are coated with an unsaturated polyester gel- coat, an acrylic filler and finally with an acrylic paint. For repair of composite parts refer to Chapter 51. PAGE DATE: 1. July 1996 CHAPTER 55 PAGE 3 EXTRA - FLUGZEUGBAU GmbH GENERAL SERVICE MANUAL EXTRA 200 Layer Sequence Horizontal Tail Figure 1, Sheet 1 PAGE DATE: 1. July 1996 CHAPTER 55 PAGE 4 EXTRA - FLUGZEUGBAU GmbH GENERAL SERVICE MANUAL EXTRA 200 Layer Sequence Horizontal Tail Figure 1, Sheet 2 PAGE DATE: 1. -
Issue No. 1, Jan-Mar
VOL. 25, NO. 1 JANUARY – MARCH 1998 ServiceService NewsNews A SERVICE PUBLICATION OF LOCKHEED MARTIN AERONAUTICAL SYSTEMS SUPPORT COMPANY Previous Page Table of Contents Next Page LOCKHEED MARTIN Service News HOC 1997 A SERVICE PUBLICATION OF uring the week of 13 - 17 October 1997, the ninth Hercules LOCKHEED MARTIN AERONAUTICAL Operators Conference (HOC) was held in Marietta. Judging from SYSTEMS SUPPORT COMPANY D the surveys of approximately 330 attendees, the conference was an overall success. Lockheed Martin is most pleased to Editor Charles E. Wright, II have hosted this event and trusts each participant ben- efitted greatly from the proceedings. Vol. 25, No. 1, January - March 1998 Lockheed Martin is committed to continuation of the CONTENTS conference on a regular basis. We see the conference 2 Focal Point as a valuable forum for sharing of technical informa- L. D. “Dave” Holcomb, Co-Chairman tion and in-service experiences of Hercules operators. Airlift Field Service We also see the importance of having a variety of atten- Alex Gibbs, Squadron Leader dees to Please turn to page 15, column 1 RAAF Technical Liaison Officer L. D. Holcomb 3 Troubleshooting Pressurization Problems HOC Co-Chairman Comments A guide to understanding and solving pressurization problems. or the last three years I have had the privilege of attending the HOC as the International Operator’s Co-Chairman. The increase in rep- 9 Cumulative Index 1974 - 1997 A complete, alphabetical listing of F resentation and presentations from operators each year confirms my Service News technical articles. strong belief in the need and value for operators and Lockheed Martin in the HOC. -
A Historical Overview of Flight Flutter Testing
tV - "J -_ r -.,..3 NASA Technical Memorandum 4720 /_ _<--> A Historical Overview of Flight Flutter Testing Michael W. Kehoe October 1995 (NASA-TN-4?20) A HISTORICAL N96-14084 OVEnVIEW OF FLIGHT FLUTTER TESTING (NASA. Oryden Flight Research Center) ZO Unclas H1/05 0075823 NASA Technical Memorandum 4720 A Historical Overview of Flight Flutter Testing Michael W. Kehoe Dryden Flight Research Center Edwards, California National Aeronautics and Space Administration Office of Management Scientific and Technical Information Program 1995 SUMMARY m i This paper reviews the test techniques developed over the last several decades for flight flutter testing of aircraft. Structural excitation systems, instrumentation systems, Maximum digital data preprocessing, and parameter identification response algorithms (for frequency and damping estimates from the amplltude response data) are described. Practical experiences and example test programs illustrate the combined, integrated effectiveness of the various approaches used. Finally, com- i ments regarding the direction of future developments and Ii needs are presented. 0 Vflutte r Airspeed _c_7_ INTRODUCTION Figure 1. Von Schlippe's flight flutter test method. Aeroelastic flutter involves the unfavorable interaction of aerodynamic, elastic, and inertia forces on structures to and response data analysis. Flutter testing, however, is still produce an unstable oscillation that often results in struc- a hazardous test for several reasons. First, one still must fly tural failure. High-speed aircraft are most susceptible to close to actual flutter speeds before imminent instabilities flutter although flutter has occurred at speeds of 55 mph on can be detected. Second, subcritical damping trends can- home-built aircraft. In fact, no speed regime is truly not be accurately extrapolated to predict stability at higher immune from flutter. -
Air Accident Investigation Unit Ireland
Air Accident Investigation Unit Ireland SYNOPTIC REPORT ACCIDENT Boeing, 737-8AS, EI-EMH/EI-EKK LINK 2, Dublin Airport, Ireland 7 October 2014 Boeing 737-8AS, EI-EMH/EI-EKK Dublin Airport 7 October 2014 FINAL REPORT Foreword This safety investigation is exclusively of a technical nature and the Final Report reflects the determination of the AAIU regarding the circumstances of this occurrence and its probable causes. In accordance with the provisions of Annex 131 to the Convention on International Civil Aviation, Regulation (EU) No 996/20102 and Statutory Instrument No. 460 of 20093, safety investigations are in no case concerned with apportioning blame or liability. They are independent of, separate from and without prejudice to any judicial or administrative proceedings to apportion blame or liability. The sole objective of this safety investigation and Final Report is the prevention of accidents and incidents. Accordingly, it is inappropriate that AAIU Reports should be used to assign fault or blame or determine liability, since neither the safety investigation nor the reporting process has 1 been undertaken for that purpose. Extracts from this Report may be published providing that the source is acknowledged, the material is accurately reproduced and that it is not used in a derogatory or misleading context. 1 Annex 13: International Civil Aviation Organization (ICAO), Annex 13, Aircraft Accident and Incident Investigation. 2 Regulation (EU) No 996/2010 of the European Parliament and of the Council of 20 October 2010 on the investigation and prevention of accidents and incidents in civil aviation. 3 Statutory Instrument (SI) No. 460 of 2009: Air Navigation (Notification and Investigation of Accidents, Serious Incidents and Incidents) Regulations 2009. -
Wing, Fuselage and Tail • Mainplane: Airfoil Cross-Section Shape, Taper Ratio Selection, Sweep Angle Selection, Wing Drag Estimation
Design Of Structural Components - Wing, Fuselage and Tail • Mainplane: Airfoil cross-section shape, taper ratio selection, sweep angle selection, wing drag estimation. Spread sheet for wing design. • Fuselage: Volume consideration, quantitative shapes, air inlets, wing attachments; Aerodynamic considerations and drag estimation. Spread sheets. • Tail arrangements: Horizontal and vertical tail sizing. Tail planform shapes. Airfoil selection type. Tail placement. Spread sheets for tail design Main Wing Design 1. Introduction: Airfoil Geometry: • Wing is the main lifting surface of the aircraft. • Wing design is the next logical step in the conceptual design of the aircraft, after selecting the weight and the wing-loading that match the mission requirements. • The design of the wing consists of selecting: i) the airfoil cross-section, ii) the average (mean) chord length, iii) the maximum thickness-to-chord ratio, iv) the aspect ratio, v) the taper ratio, and Wing Geometry: vi) the sweep angle which is defined for the leading edge (LE) as well as the trailing edge (TE) • Another part of the wing design involves enhanced lift devices such as leading and trailing edge flaps. • Experimental data is used for the selection of the airfoil cross-section shape. • The ultimate “goals” for the wing design are based on the mission requirements. • In some cases, these goals are in conflict and will require some compromise. Main Wing Design (contd) 2. Airfoil Cross-Section Shape: • Effect of ( t c ) max on C • The shape of the wing cross-section determines lmax for a variety of the pressure distribution on the upper and lower 2-D airfoil sections is surfaces of the wing. -
Approaches to Assure Safety in Fly-By-Wire Systems: Airbus Vs
APPROACHES TO ASSURE SAFETY IN FLY-BY-WIRE SYSTEMS: AIRBUS VS. BOEING Andrew J. Kornecki, Kimberley Hall Embry Riddle Aeronautical University Daytona Beach, FL USA <[email protected]> ABSTRACT The aircraft manufacturers examined for this paper are Fly-by-wire (FBW) is a flight control system using Airbus Industries and The Boeing Company. The entire computers and relatively light electrical wires to replace Airbus production line starting with A320 and the Boeing conventional direct mechanical linkage between a pilot’s 777 utilize fly-by-wire technology. cockpit controls and moving surfaces. FBW systems have been in use in guided missiles and subsequently in The first section of the paper presents an overview of military aircraft. The delay in commercial aircraft FBW technology highlighting the issues associated with implementation was due to the time required to develop its use. The second and third sections address the appropriate failure survival technologies providing an approaches used by Airbus and Boeing, respectively. In adequate level of safety, reliability and availability. each section, the nature of the FBW implementation and Software generation contributes significantly to the total the human-computer interaction issues that result from engineering development cost of the high integrity digital these implementations for specific aircraft are addressed. FBW systems. Issues related to software and redundancy Specific examples of software-related safety features, techniques are discussed. The leading commercial aircraft such as flight envelope limits, are discussed. The final manufacturers, such as Airbus and Boeing, exploit FBW section compares the approaches and general conclusions controls in their civil airliners. The paper presents their regarding the use of FBW technology. -
C-130J Super Hercules Whatever the Situation, We'll Be There
C-130J Super Hercules Whatever the Situation, We’ll Be There Table of Contents Introduction INTRODUCTION 1 Note: In general this document and its contents refer RECENT CAPABILITY/PERFORMANCE UPGRADES 4 to the C-130J-30, the stretched/advanced version of the Hercules. SURVIVABILITY OPTIONS 5 GENERAL ARRANGEMENT 6 GENERAL CHARACTERISTICS 7 TECHNOLOGY IMPROVEMENTS 8 COMPETITIVE COMPARISON 9 CARGO COMPARTMENT 10 CROSS SECTIONS 11 CARGO ARRANGEMENT 12 CAPACITY AND LOADS 13 ENHANCED CARGO HANDLING SYSTEM 15 COMBAT TROOP SEATING 17 Paratroop Seating 18 Litters 19 GROUND SERVICING POINTS 20 GROUND OPERATIONS 21 The C-130 Hercules is the standard against which FLIGHT STATION LAYOUTS 22 military transport aircraft are measured. Versatility, Instrument Panel 22 reliability, and ruggedness make it the military Overhead Panel 23 transport of choice for more than 60 nations on six Center Console 24 continents. More than 2,300 of these aircraft have USAF AVIONICS CONFIGURATION 25 been delivered by Lockheed Martin Aeronautics MAJOR SYSTEMS 26 Company since it entered production in 1956. Electrical 26 During the past five decades, Lockheed Martin and its subcontractors have upgraded virtually every Environmental Control System 27 system, component, and structural part of the Fuel System 27 aircraft to make it more durable, easier to maintain, Hydraulic Systems 28 and less expensive to operate. In addition to the Enhanced Cargo Handling System 29 tactical airlift mission, versions of the C-130 serve Defensive Systems 29 as aerial tanker and ground refuelers, weather PERFORMANCE 30 reconnaissance, command and control, gunships, Maximum Effort Takeoff Roll 30 firefighters, electronic recon, search and rescue, Normal Takeoff Distance (Over 50 Feet) 30 and flying hospitals. -
Design of Canard Aircraft
APPENDIX C2: Design of Canard Aircraft This appendix is a part of the book General Aviation Aircraft Design: Applied Methods and Procedures by Snorri Gudmundsson, published by Elsevier, Inc. The book is available through various bookstores and online retailers, such as www.elsevier.com, www.amazon.com, and many others. The purpose of the appendices denoted by C1 through C5 is to provide additional information on the design of selected aircraft configurations, beyond what is possible in the main part of Chapter 4, Aircraft Conceptual Layout. Some of the information is intended for the novice engineer, but other is advanced and well beyond what is possible to present in undergraduate design classes. This way, the appendices can serve as a refresher material for the experienced aircraft designer, while introducing new material to the student. Additionally, many helpful design philosophies are presented in the text. Since this appendix is offered online rather than in the actual book, it is possible to revise it regularly and both add to the information and new types of aircraft. The following appendices are offered: C1 – Design of Conventional Aircraft C2 – Design of Canard Aircraft (this appendix) C3 – Design of Seaplanes C4 – Design of Sailplanes C5 – Design of Unusual Configurations Figure C2-1: A single engine, four-seat Velocity 173 SE just before touch-down. (Photo by Phil Rademacher) GUDMUNDSSON – GENERAL AVIATION AIRCRAFT DESIGN APPENDIX C2 – DESIGN OF CANARD AIRCRAFT 1 ©2013 Elsevier, Inc. This material may not be copied or distributed without permission from the Publisher. C2.1 Design of Canard Configurations It has already been stated that preference explains why some aircraft designers (and manufacturers) choose to develop a particular configuration. -
Fly-By-Wire Augmented Manual Control - Basic Design Considerations
FLY-BY-WIRE AUGMENTED MANUAL CONTROL - BASIC DESIGN CONSIDERATIONS Dominik Niedermeier∗ , Anthony A. Lambregts∗∗ ∗Deutsches Zentrum für Luft- und Raumfahrt e.V., ∗∗Federal Aviation Administration [email protected]; [email protected] Keywords: Fly-by-Wire, Manual augmented control, C∗ control algorithm, C∗U control algorithm Abstract manufacturer allowing reduced training re- quirements After the introduction of Fly-by-Wire (FBW) flight control in the late eighties, several thousands of com- • Weight and maintenance effort reduction by re- mercial FBW aircraft are in service today. Look- placing mechanical components (e.g. pulleys, ing back, it can be concluded that FBW has brought cables) an impressive improvement to handling qualities and • Introduction of flight envelope protection func- flight safety. However, after the long time of experi- tions for enhanced safety ence with the first generations of FBW aircraft, open questions and issues with respect to the design and • Introduction of maneuver/gust load alleviation the operation of FBW have been revealed. The main functions objective of this paper is to discuss those issues and to • Optimization of aerodynamic performance (e.g. point out further research needs in this field. The char- drag reduction by aft-shifted center of gravity) acteristics of manual augmented pitch control algo- rithms implemented in commercial FBW aircraft are Manufacturer Current Models No. of deliveries discussed in detail. Subsequently the paper describes Boeing B777 1003 particular features of Airbus and Boeing FBW control B787 8 systems that are not directly related to the chosen con- Airbus A318/319/320/321 5022 trol algorithm. Open questions and resulting research A330/340 1225 needs with special focus on recent incidents and acci- A380 71 Embraer E-170/190 802 dents are discussed.