A HISTORY of the DEVORE TEXTILE 1880 to 1940. a Thesis
Total Page:16
File Type:pdf, Size:1020Kb
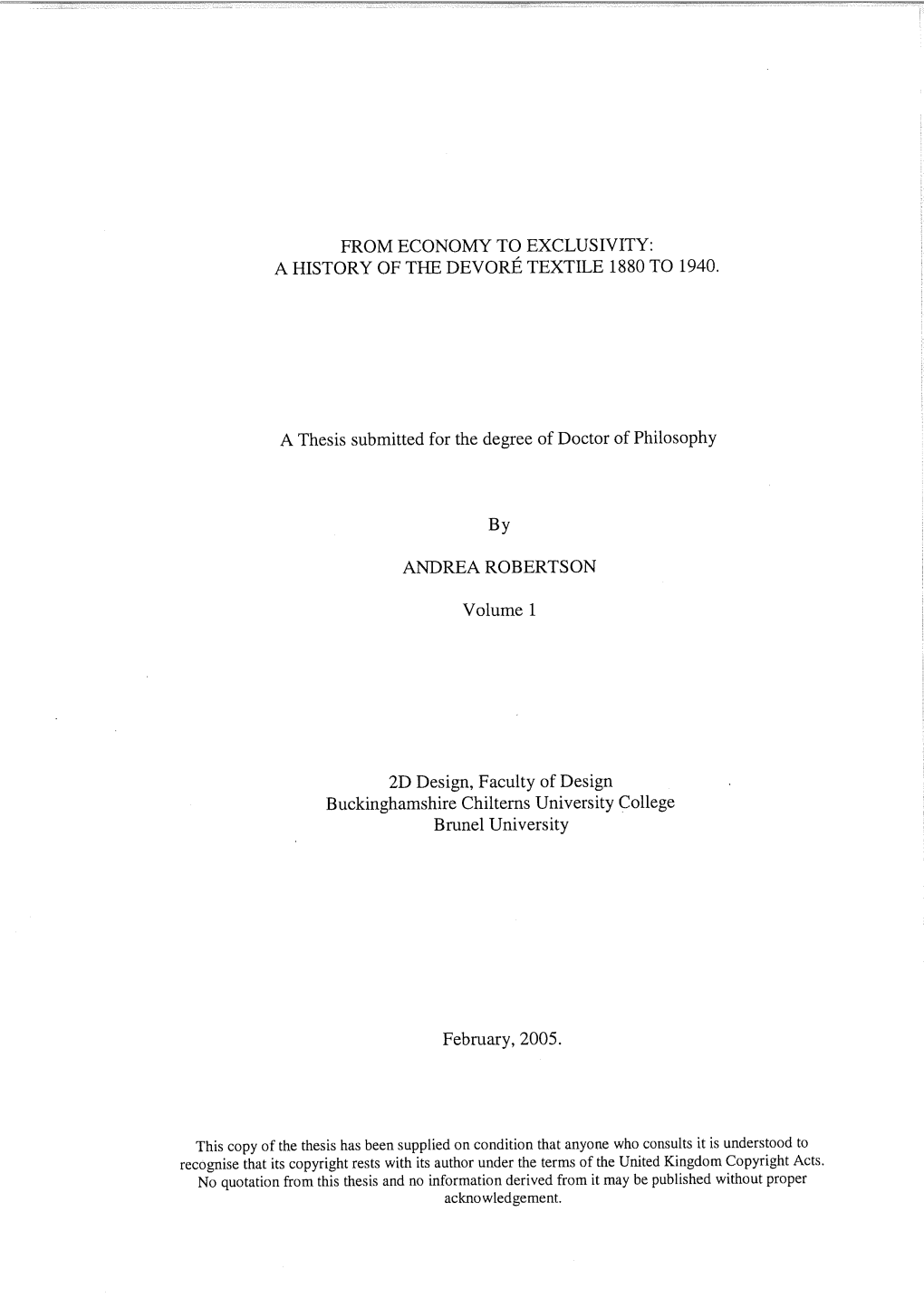
Load more
Recommended publications
-
', :':':;"Texa's- Agricultural , Ex-Ten '
4> ~ -,' , :':':;"TEXA'S- AGRICULTURAL , EX-TEN ' . ... -:>-.~ -~•• ,....,~ hi.t~.' ~ ___ '>::"'" - 'J. E .. 'Hutchison, 'Director, College:.shlt~QP" Texas GRAHAM HARD NENA ROBERSON RHEBA MERLE BOYLES FANNIE BROWN EATON EXTENSION CLOTHING SPECIALISTS The A. and M. College of Texas THE CHARACTERISTICS OF FABRICS which . give 3. Fabrics made of chemically treated cotton, them the virtues of quick drying, crease re linen and rayon. The resin finishes are the most sistance, little or no ironing, keeping their orig commonly used. These finishes should last the inal shape and size during use and care, retaining normal life of a garment. a look of newness and fresh crispness after being worn and cleaned continuously also create sewing FABRIC SELECTION difficulties. The surface often is smoother and The best guides in the selection of quality harder which makes the fabric less pliable and fabrics are informative labels of reputable manu more difficult to handle. These qualities can facturers. Good quality finishes add to the cost cause seams to pucker. Even in the softest blends of fabrics, but compensate for the extra cost in there is a springiness which requires more care in durability and appearance. handling ease, as in the sleeve cap. Each fabric presents different problems. Look Wash-and-wear fabrics may be divided into at the fabric and feel it. Is it closely or loosely three groups: woven? Is it soft and firm, or stiff and wiry? 1. Fabrics woven or knitted from yarns of Will it fray? What style pattern do you have in 100 percent man-made fibers. These fabrics, if mind? properly finished, are highly crease resistant and The correctness of fabric grain is important keep their original shape and size during use and in sewing. -
Liniment a Close Two-Cent Stamp for Repb- Form of Construction Insures the Best Can Have in the House
Effective Costumes home “Two bottles the American Cured My Wm A.RADFORD rngmSKm Rheumatism’’ EDITOR Mr. William A. Radford will answer way on the outside may be considered questions and give advice FREE OF practically fireproof. COST on all subjects pertaining to the There is no combination of subject of building for the readers of mate- this paper. On account of his wide expe- irals more pleasing to the eye than rience as Editor. Author and Manufac- this high grade face brick and the turer, he Is, without doubt, the highest cement plaster In a harmonizing col- authority on all these subjects. Address or. As far as warmth and freedom foundrelief at all Inquiries to William A. Radford. No. person IS4 Fifth Ave.. Chicago, 111., and only en- from dampness are concerned this got two bottles and they cured me. I think it is the best Liniment a close two-cent stamp for repb- form of construction Insures the best can have In the house. Ishall always keep a bottle in my house as long as I possible results, and the expense Is can get it”—Mrs. E. R. Wallace, Morrisons, Va. The well-to-do suburban builder Is getting rather particular about the Another Letter. kind of a house he puts up. It Is not Mrs. James McGraw, of 1216 Mandeville St., New Orleans, La., writes: — enough to simply provide comfortable “ I take pleasure in writing to you that I had a pain in my arm for five years, shelter for his family and have room and I used enough for all; but the general style and appearance of the house has to be given due thought so that it will work In well with Its surroundings and con- form In size and style to what his friends and neighbors consider neces- sary for his home. -
Finish That Seam Barbara Short Iowa State College
Volume 30 Article 7 Number 5 The Iowa Homemaker vol.30, no.5 1950 Finish That Seam Barbara Short Iowa State College Follow this and additional works at: http://lib.dr.iastate.edu/homemaker Part of the Home Economics Commons Recommended Citation Short, Barbara (1950) "Finish That Seam," The Iowa Homemaker: Vol. 30 : No. 5 , Article 7. Available at: http://lib.dr.iastate.edu/homemaker/vol30/iss5/7 This Article is brought to you for free and open access by the Student Publications at Iowa State University Digital Repository. It has been accepted for inclusion in The oI wa Homemaker by an authorized editor of Iowa State University Digital Repository. For more information, please contact [email protected]. Finish That Seam - But fi rst be sure the finish is the proper one for you r material. Here are the recent 1 findings of two textiles and I clothing graduate students. I I j I I J I I J by Barbara Short I J Technical Journalism Junior I I I J I I I > HEN your mother was a little girl, often seam I > j W stresses stayed in the house for a week to outfit "'--- I the family each year. Then the inside of a dress was just as finished as the outside. Those seamstresses took 1. Double-stitch finish; 2. Pinked finish; 3. Q,·er-cast edges. pains to finish each seam so that they could be sure it wouldn't ravel. Recent graduate research at Iowa State has taken guesswork out of seam finishing. Find Hiltbold points out that the ridge produced when ings will mean no more unnecessary sewing or hope the edge is turned shows on certain fabrics. -
Women's Uniforms 1 Sept/Oct 2005 by Marie Robinette € in the Morris
By Marie Robinette € In the Morris and Company, Inc brochure from 1929 they ask, “Does a smile count? Can it cheer the patient and speed recovery? Then so does the costume of the nurse.” The uniforms of the Model A era reflected style and quality in every line. The nurses of the era who wore the newest styles in uniforms would not lose her personality by wearing a uniform that was unattractive. The styles were a mirror of trends in street dresses. Uniforms were available to the professional nurse, the business women and home service too. When we think of women’s uniforms during the Model A Era we tend to think of a nurse’s sterile white uniform. But, some nurse’s uniforms were offered in blue, pink, green and orchid fast color Chambray. Pin stripe prints were also available. Women’s Uniforms 1 Sept/Oct 2005 #2415 – Made of Ryster 5-Star #2412 – Made of fine weave #1889 – A new model at a low two-ply Poplin. Has Peter Pan 2-ply Dundalk Poplin. Has 8 price. Made of Linatex Nurses’ collar, French turnover cuffs inverted shoulder tucks, four Suiting with a high turn-over and two shaped patch pockets. on either side of long flat collar. scalloped collar. New form-fitting The four narrow inverted tucks Central from opening to waist sleeves.Dutch turned cuffs. Trimmed on either side of the yoke give line. Two bellows patch pockets. with detachable ocean pearl buttons a slight fullness over the bust. French cuffs. Detachable belt and sloped welt pockets Detachable ocean pearl buttons, and detachable ocean pearl and detachable belt. -
Curtains and Draperies
Extension Bulletin 264 June 1951 BULLErJN HU()fvt liBRARY, Uf\WERC:ITY Fi>.P.M Selecting and Making CURTAINS AND DRAPERIES planning ideas buying guides construction aids Jfelen Jf. )Uatfteis WitcH Vou Select eurtnifiS and Vraperies ODAY'S homemaker has a world of new ideas and new prod T ucts to choose from when she plans window treatments for her home. She finds tremendous stress placed on the number, size, shape, and placement of windows in rooms in order that they may serve a number of purposes. Among these are, of course, the basic functions of windows-light, air, and vision. In addition windows often are the focal point, or gathering place for people in a room. All these points must be considered when planning windows and window decor. Whatever your light, air, vision, or by the store display of suggested room activity problems, remember that good settings. window treatment will be restful, it In addition, successful shopping calls will harmonize with the room, and lend for accurate information about your ·distinction to the furnishings used room requirements. You supply this by there. This means that good window carrying with you a sketch of your treatment will take its place as a sat room, preferably with wall and floor isfying part of the room furnishings and space indicated in %-inch scale. will also allow flowers, books,' works Salespeople count on this when they of art, and hobby interests of the family prepare merchandise for your selec to accent the character of furnishings tion. They must know about the archi in the room. -
Cora Ginsburg Catalogue 2015
CORA GINSBURG LLC TITI HALLE OWNER A Catalogue of exquisite & rare works of art including 17th to 20th century costume textiles & needlework 2015 by appointment 19 East 74th Street tel 212-744-1352 New York, NY 10021 fax 212-879-1601 www.coraginsburg.com [email protected] NEEDLEWORK SWEET BAG OR SACHET English, third quarter of the 17th century For residents of seventeenth-century England, life was pungent. In order to combat the unpleasant odors emanating from open sewers, insufficiently bathed neighbors, and, from time to time, the bodies of plague victims, a variety of perfumed goods such as fans, handkerchiefs, gloves, and “sweet bags” were available for purchase. The tradition of offering embroidered sweet bags containing gifts of small scented objects, herbs, or money began in the mid-sixteenth century. Typically, they are about five inches square with a drawstring closure at the top and two to three covered drops at the bottom. Economical housewives could even create their own perfumed mixtures to put inside. A 1621 recipe “to make sweete bags with little cost” reads: Take the buttons of Roses dryed and watered with Rosewater three or foure times put them Muske powder of cloves Sinamon and a little mace mingle the roses and them together and putt them in little bags of Linnen with Powder. The present object has recently been identified as a rare surviving example of a large-format sweet bag, sometimes referred to as a “sachet.” Lined with blue silk taffeta, the verso of the central canvas section contains two flat slit pockets, opening on the long side, into which sprigs of herbs or sachets filled with perfumed powders could be slipped to scent a wardrobe or chest. -
Catalogue of the Famous Blackborne Museum Collection of Laces
'hladchorvS' The Famous Blackbome Collection The American Art Galleries Madison Square South New York j J ( o # I -legislation. BLACKB ORNE LA CE SALE. Metropolitan Museum Anxious to Acquire Rare Collection. ' The sale of laces by order of Vitail Benguiat at the American Art Galleries began j-esterday afternoon with low prices ranging from .$2 up. The sale will be continued to-day and to-morrow, when the famous Blackborne collection mil be sold, the entire 600 odd pieces In one lot. This collection, which was be- gun by the father of Arthur Blackborne In IS-W and ^ contmued by the son, shows the course of lace making for over 4(Xi ye^rs. It is valued at from .?40,fX)0 to $oO,0()0. It is a museum collection, and the Metropolitan Art Museum of this city would like to acciuire it, but hasnt the funds available. ' " With the addition of these laces the Metropolitan would probably have the finest collection of laces in the world," said the museum's lace authority, who has been studying the Blackborne laces since the collection opened, yesterday. " and there would be enough of much of it for the Washington and" Boston Mu- seums as well as our own. We have now a collection of lace that is probablv pqual to that of any in the world, "though other museums have better examples of some pieces than we have." Yesterday's sale brought SI. .350. ' ""• « mmov ON FREE VIEW AT THE AMERICAN ART GALLERIES MADISON SQUARE SOUTH, NEW YORK FROM SATURDAY, DECEMBER FIFTH UNTIL THE DATE OF SALE, INCLUSIVE THE FAMOUS ARTHUR BLACKBORNE COLLECTION TO BE SOLD ON THURSDAY, FRIDAY AND SATURDAY AFTERNOONS December 10th, 11th and 12th BEGINNING EACH AFTERNOON AT 2.30 o'CLOCK CATALOGUE OF THE FAMOUS BLACKBORNE Museum Collection of Laces BEAUTIFUL OLD TEXTILES HISTORICAL COSTUMES ANTIQUE JEWELRY AND FANS EXTRAORDINARY REGAL LACES RICH EMBROIDERIES ECCLESIASTICAL VESTMENTS AND OTHER INTERESTING OBJECTS OWNED BY AND TO BE SOLD BY ORDER OF MR. -
The Manufacture of Paper
/°* '^^^n^ //i,- '^r. c.^" ^'IM^"* *»^ A^ -h^" .0^ V ,<- ^.. A^^ /^-^ " THE MANUFACTURE OF PAPER BY R. W. SINDALL, F.C.S. CHEMIST CONSULTING TO THE WOOD PULP AND PAPER TRADES ; LECTURER ON PAPER-MAKING FOR THE HERTFORDSHIRE COUNTY COUNCIL, THE BUCKS COUNTY COUNCIL, THE PRINTING AND STATIONERY TRADES AT EXETER HALL, 1903-4, THE INSTITUTE OF PRINTERS ; TECHNICAL ADVISER TO THE GOVERNMENT OF INDIA, 1905 AUTHOR OF "paper TECHNOLOGY," " THE SAMPLING OF WOOD PULP " JOINT AUTHOR OF " THE C.B.S. UNITS, OR STANDARDS OF PAPER TESTING," " THE APPLICATIONS OF WOOD PULP," ETC. WITH ILLUSTRATIONS, AND A BIBLIOGRAPHY OF WORKS RELATING TO CELLULOSE AND PAPER-MAKING ^^RlFFeo^ ^^ ^, 11^ OCT 3 11910 ^^f-40 ^\^c> A BU\ lo\' NEW YORK D. VAN NOSTRAND COMPANY 23 MURRAY AND 27 WARREN STREETS 1908 By trassf»r trom U. S. Tariff Boarri 1012 /(o'?'<Q / PREFACE •Papee-making, in common with many other industries, is one in which both engineering and chemistry play important parts. Unfortunately the functions of the engineer and chemist are generally regai^dedi •a&n.inelepejident of one another, so that the chemist ife^o^ify e^llfeS-iii-hy the engineer when efforts along the lines of nlecTianical improvement have failed, and vice versa. It is impossible, however, to draw a hard and fast line, and the best results in the art of paper-making are only possible when the manufacturer appreciates the fact that the skill of both is essential to progress and commercial success. In the present elementary text-book it is only proposed to give an outline of the various stages of manufacture and to indicate some of the improvements made during recent years. -
Appendix 1 Sources
APPENDIX 1 SOURCES UMIST: DEPARTMENT OF TEXTILES Most of the work described in this book comes from research in the Department of Textiles, UMIST, under the direction of Professor John Hearle. It started with the purchase of a scanning electron microscope with a grant from the Science Research Council in 1967, together with five-year funding for an experimental officer and a technician. Since 1972, the staff have been supported by general UMIST funds; a second grant from SERC enabled a replacement SEM to be bought in 1979; industrial sponsors, listed below, have contributed through membership of the Fibre Fracture Research Group; special research grants have been made by the Ministry of Defence (SCRDE, Colchester, and RAE, Farnborough) and jointly by the Wool Research Organization of New Zealand (WRONZ) and the Wool Foundation (IWS); and other research programmes and contract services have contributed indirectly to our knowledge. Pat Cross was the first SEM experimental officer and she was followed in 1969 by Brenda Lomas, who retired in 1990. Trevor Jones then took on responsibility for microscopy in the Department of Textiles in addition to photography. Over the years, many staff and students have contributed to the research. Their names are given below. Some have worked wholly on fibre fracture problems. Others have used fracture studies as an incidental element in their work. PERSONNEL The following people at UMIST have contributed to the research. Academic staff J.D. Berry Aspects of fibre breakage CP. Buckley Mechanics of tensile fracture, general direction C. Carr Fabric studies W.D. Cooke Pilling in knitwear, conservation studies G.E. -
California and the Fiber Art Revolution
View metadata, citation and similar papers at core.ac.uk brought to you by CORE provided by UNL | Libraries University of Nebraska - Lincoln DigitalCommons@University of Nebraska - Lincoln Textile Society of America Symposium Proceedings Textile Society of America 2004 California and the Fiber Art Revolution Suzanne Baizerman Oakland Museum of California, [email protected] Follow this and additional works at: https://digitalcommons.unl.edu/tsaconf Part of the Art and Design Commons Baizerman, Suzanne, "California and the Fiber Art Revolution" (2004). Textile Society of America Symposium Proceedings. 449. https://digitalcommons.unl.edu/tsaconf/449 This Article is brought to you for free and open access by the Textile Society of America at DigitalCommons@University of Nebraska - Lincoln. It has been accepted for inclusion in Textile Society of America Symposium Proceedings by an authorized administrator of DigitalCommons@University of Nebraska - Lincoln. California and the Fiber Art Revolution Suzanne Baizerman Imogene Gieling Curator of Crafts and Decorative Arts Oakland Museum of California Oakland, CA 510-238-3005 [email protected] In the 1960s and ‘70s, California artists participated in and influenced an international revolution in fiber art. The California Design (CD) exhibitions, a series held at the Pasadena Art Museum from 1955 to 1971 (and at another venue in 1976) captured the form and spirit of the transition from handwoven, designer textiles to two dimensional fiber art and sculpture.1 Initially, the California Design exhibits brought together manufactured and one-of-a kind hand-crafted objects, akin to the Good Design exhibitions at the Museum of Modern Art in New York City. -
From “Outsider” to Insider: the Case of Reliance
View metadata, citation and similar papers at core.ac.uk brought to you by CORE provided by Munich Personal RePEc Archive MPRA Munich Personal RePEc Archive From \Outsider" to Insider: The Case of Reliance Surajit Mazumdar 2016 Online at https://mpra.ub.uni-muenchen.de/93162/ MPRA Paper No. 93162, posted 9 April 2019 16:13 UTC From ‘Outsider’ to Insider: the Case of Reliance Surajit Mazumdar CESP/SSS. Jawaharlal Nehru University Revised Version of Paper presented at the Conference on the Sociology of the Indian Elites, Jawaharlal Nehru University, 4th and 5th January 2016 Abstract: At the time that India’s liberalization, the Reliance group was already one of India’s leading business groups and in subsequent years has only cemented its place at the top of India’s corporate hierarchy. Reliance was not, however, among the ‘traditional’ large groups that emerged during the colonial era and were found to be still dominant in the mid-1960s. This paper traces the story of the Reliance phenomenon and discusses briefly the process (method) by which that story was constructed. In addition to demystifying the phenomenon, the paper seeks to demonstrate that there is sufficient evidence available to establish the proposition that the basis for the success of Reliance was fundamentally no different from that which other groups used to perpetuate their dominant position, the roots of which lay in the nature of Indian capitalism. 1 Introduction A fundamental premise of this paper is that the capitalist or business class in any society is a product of its particular historical development. -
Dr.PRICE's 1 Day
win t Him ! iiuufeawimiafciaMit ii m - i iii ;n v."11"- - 1 IWkYV amm TV.S , "49&rmf-- - l. :, . y mj it, pj w jiid . i vj J Yti f I f - VOLUME XXXII. RED CLOUD, NEJill ASK A. APRIL 8, 1901, NUMBER 15 Lincoln Letter. prosecutod. Tho stato law give tho Lincoln. Nkh., April 0. board a groat deal of discretion iu inside a Governor Mickey has commuted tho donliug with such companies nud man's head is no WHAT'S ? Miner Bros. Bros. sontonco of throo years imposed upon thoro appeal from its decision, if Miner John Patterson of Hall county to 2 Its officers correctly understand tho shows by what's years, i months nnd 0 days, nnd Pat- stntuto. outside. terson has been roloased. Tho Gover- i 1 nor took this action bocauso tho wlfo Commissioner of Labor Hush is LADIES' OXFORDS. of tho prisoner was in feeble honlth mniling out lottors of inquiry to To wear a Gordon Hat is not a and dostltuto circumstances and Pat- county nssessors requesting statistics Dainty, stylish, designed on porfoct linos, which gives a slender, terson, who has boon a model prisoner aud 'information coucoruimr tho guarantee of cleverness, but it indi- pretty look to tho foot, without nuy mcrlflco of comfort. and ono of tho best workers in tho amount of land sold iu thoir respec- to penitentiary, promisod solemnly to tive counties nnd tho total value of cates that the mind inside the hat Fits Perfection at the Hollow of the root. care for his family nnd keep oat of land sold with the nvorago prico por trouble He was sent up for a small aero.