By 344-/7-2 6%
Total Page:16
File Type:pdf, Size:1020Kb
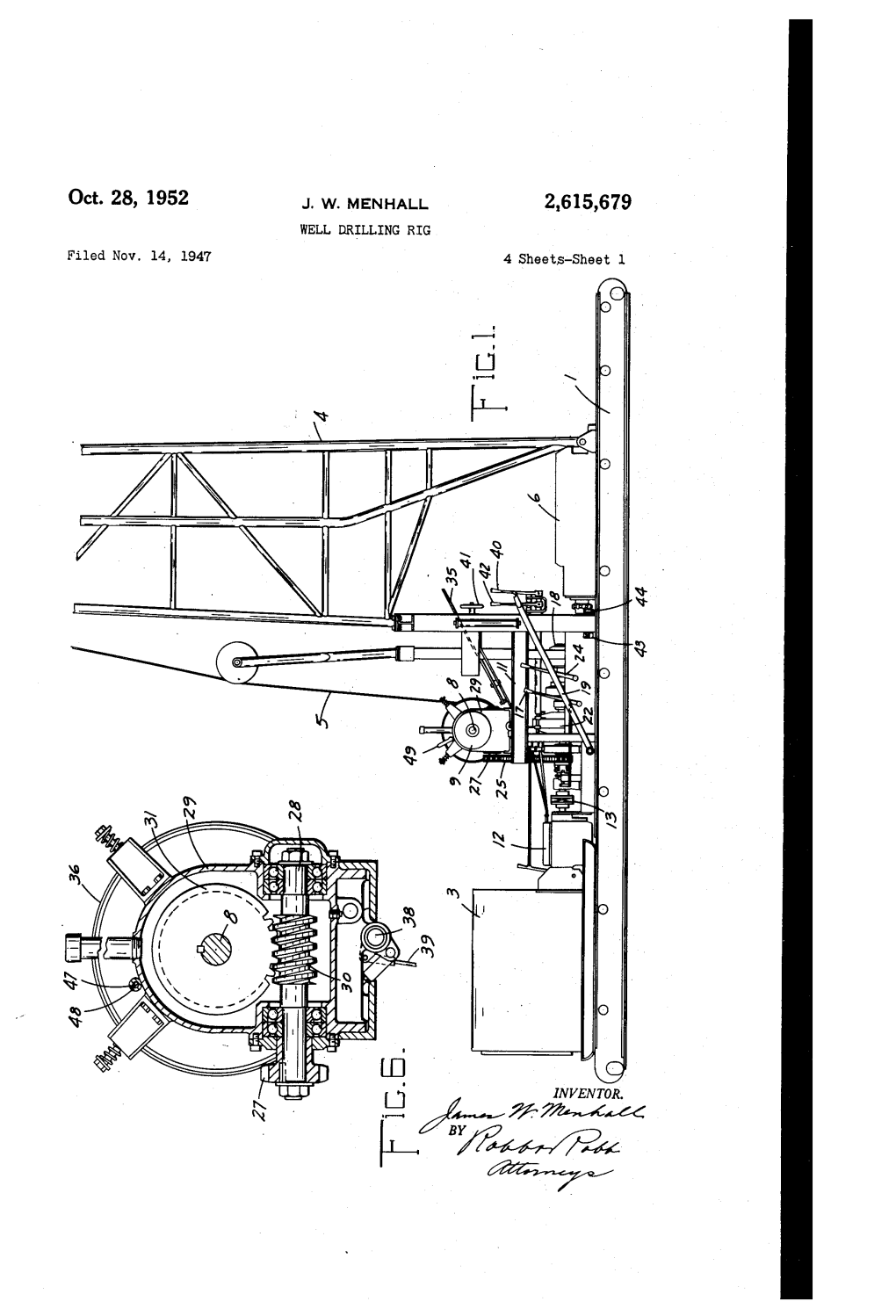
Load more
Recommended publications
-
Installation and Maintenance Manual Winch Performa 46.2 STP
Installation and Maintenance Manual MRPW-05 Performa™ Winch 46.2 STP 46.2 STQP Index Introduction 3 Technical characteristics 3 Performance data 3 Weight 3 Maximum working load 3 Technical characteristics - Winch Quattro Performa 4 Performance data 4 Weight 4 Maximum working load 4 Outline 3 Winch 46.2 STP 3 Outline - Winch Quattro Performa 4 Winch 46.2 STQP 4 Installation 5 Installation procedure 6 Positioning the self-tailing arm 9 Maintenance 9 Washing 9 Maintenance table 9 Disassembly procedure 9 Exploded view with maintenance products 13 Assembly 14 Harken® limited worldwide warranty 15 Ordering spare parts 15 Exploded view 16 Performa Winch 46.2 STP 16 Performa Winch 46.2 STQP 18 Parts list 20 Performa Winch 46.2 STP 20 Performa Winch 46.2 STQP 21 Performa™ Winch 46.2 STP 2 Installation and Maintenance Manual Introduction - Technical characteristics - Outline Introduction This manual gives technical information on winch installation and maintenance, including disassembling and reassembling. This information is DESTINED EXCLUSIVELY for specialised personnel or expert users. Installation, disassembling and reassembling of the winch by personnel who are not experts may cause serious damage to users and those in the vicinity of the winch. Harken® accepts no responsibility for defective installation or reassembly of its winches. In case of doubt the Harken® Tech Service is at your disposal at [email protected] This Manual is available only in English. If you do not fully understand the English language, do not carry out the operations described in this Manual. Technical characteristics Power ratio Gear ratio 1st speed 11,70 : 1 2,30 : 1 2nd speed 46,50 : 1 9,20 : 1 The theoretical power ratio does not take friction into account. -
82 Subpart 77.03—Marine Engineering Systems
§ 77.03±1 46 CFR Ch. I (10±1±98 Edition) 100 Barr Harbor Drive, West Conshohocken, PA Miscellaneous machinery alarms and con- 19428±2959 trols. ASTM F1014±1986, Standard Specification for General alarm systems. Flashlights on Vessels: 77.35±5(c) (b) Electrical equipment installed in [CGD 82±042, 53 FR 17704, May 18, 1988, as spaces ``specially suitable for vehicles'' amended by CGD 95±072, 60 FR 50463, Sept. 29, shall be in accordance with subchapter 1995; CGD 96-041, 61 FR 50729, Sept. 27, 1996; CGD 97±057, 62 FR 51045, Sept. 30, 1997] J (Electrical Engineering) of this chap- ter. Subpart 77.03ÐMarine [CGFR 65±50, 30 FR 16953, Dec. 30, 1965, as Engineering Systems amended by CGFR 66±33, 31 FR 15283, Dec. 6, 1966; CGFR 68±32, 33 FR 5716, Apr. 12, 1968; § 77.03±1 Installation and details. CGD 74±125A, 47 FR 15231, Apr. 8, 1982] (a) The installation of all systems of a marine engineering nature, together Subpart 77.06ÐLifesaving with the details of design, construc- Appliances and Arrangements tion, and installation, shall be in ac- cordance with the requirements of sub- § 77.06±1 Installation. chapter F (Marine Engineering) of this The installation of all lifesaving ap- chapter. Systems of this type include pliances and arrangements must be in the following: accordance with the requirements of subchapter W (Lifesaving Appliances Steering systems. Power for going astern. and Arrangements) of this chapter. Bilge and ballast systems. [CGD 84±069, 61 FR 25288, May 20, 1996] Tank vent and sounding systems. Overboard discharges and shell connections. -
DF-629 Fastwinder Winch Owner's Manual
NABRICO DF-629 BARGE CONNECTING WINCH Owner’s Manual OM-DF629-001-A THIS PAGE IS INTENTIONALLY LEFT BLANK. NABRICO DF-629-40-HL-6 BARGE CONNECTING WINCH Owner’s Manual NABRICO DF-629-40-HL-6 BARGE CONNECTING MANUAL WINCH Owner’s Manual CONTENTS SAFETY INFORMATION ........................................................................................ 4 1.1 GENERAL INFORMATION ............................................................................. 5 1.2 INSTALLATION OF EQUIPMENT ................................................................... 6 1.3 INSTALLATION OF WIRE ROPE .................................................................... 8 2.1 OPERATING THE WINCH .............................................................................. 10 3.1 EQUIPMENT INSPECTION ........................................................................... 13 3.2 EQUIPMENT LUBRICATION ......................................................................... 15 3.3 CLEANING AND STORAGE .......................................................................... 16 A.1 DIMENSIONAL .............................................................................................. 18 A.2 EQUIPPED WIRE ROPE ................................................................................ 19 A.3 PARTS BREAKDOWN ................................................................................... 20 A.4 PARTS LIST ................................................................................................... 21 NOTES .................................................................................................................. -
Pulls up to 75,000 Lbs. PULSTAR P75 PULLS up to 75,000 LBS
P75 Pulls up to 75,000 lbs. PULSTAR P75 PULLS UP TO 75,000 LBS. STANDARD FEATURES & SPECIFICATIONS PULLING • 75,000 lbs. hook load accomplished by primary mainline and 6-part traveling block • Roller bearing sheaves • Inner stinger may be fully extended and locked mechanically • Mast is self-supporting and does not require guy cables in most operating conditions (additional tower heights, if selected, have individual load ratings and restrictions) • We provide highly compacted, high-performance wire rope and also provide a tapered roller bearing eye and hook swivel, Pulstar-engineered 6-part traveling block with roller bearing sheaves, and documented certification MAST & MAIN FRAME • Pulstar-engineered and fabricated • Load tested and proven • Documented certification DERRICK ASSEMBLY • Pulstar-engineered rectangular tubing • Alloy tubing incorporated into stinger • (8) elevating and holding hydraulic cylinders incorporated into elevation and holdback • Once in the layback position, we can maintain 475,000 lbs. of holdback automatically, making our derrick truly self-supporting • Documented certification WIRE ROPE • Highly compacted and rotation-resistant • High-performance configuration for state-of-the-art durability • Documented certification PRIMARY MAINLINE • Pulstar-engineered winch drum and drives • Planetary reduction • Failsafe hydraulic disc brakes • Lebus grooving sleeves installed • Heavy hoist option • 2-speed option • Electronic shift on the fly • 6-line traveling block reeved at all times • Eye and hook swivel and high-performance wire rope • Documented certification TAILOUT WINCH • Pulstar-engineered drum and drives • Planetary driven • Hydraulic failsafe brake • Lebus grooving sleeve • 140 FPM bare spool line speed • 8,500 lbs. bare spool pull • High-performance wire rope and swivel hook provided • Documented certification HYDRAULIC SYSTEM • Pressure-compensated, load-sensing pump • Independed stacker control valves • Remotes provided where noted 2 PULSTAR P75 PULLS UP TO 75,000 LBS. -
Csa Winch Procedures
CSA WINCH PROCEDURES Cover photo courtesy Neil Van Lieu TABLE OF CONTENTS 1. SCOPE ............................................................................................................................................. 1 2. REFERENCES ................................................................................................................................. 1 3. WINCH DESCRIPTION ................................................................................................................... 1 4. CREW ROLES ................................................................................................................................. 2 4.1 WINCH CAPTAIN ...................................................................................................................... 3 4.2 WINCH OPERATOR ................................................................................................................. 3 4.3 WINCH OBSERVER/TRAINEE ................................................................................................. 3 4.4 SHAG DRIVER .......................................................................................................................... 4 4.5 WING RUNNER ........................................................................................................................ 4 4.6 FLAGGER.................................................................................................................................. 4 4.7 PILOT ....................................................................................................................................... -
DNVGL-CG-0170 Offshore Classification Projects
CLASS GUIDELINE DNVGL-CG-0170 Edition July 2015 Offshore classification projects - testing and commissioning The electronic pdf version of this document found through http://www.dnvgl.com is the officially binding version. The documents are available free of charge in PDF format. DNV GL AS FOREWORD DNV GL class guidelines contain methods, technical requirements, principles and acceptance criteria related to classed objects as referred to from the rules. © DNV GL AS July 2015 Any comments may be sent by e-mail to [email protected] This service document has been prepared based on available knowledge, technology and/or information at the time of issuance of this document. The use of this document by others than DNV GL is at the user's sole risk. DNV GL does not accept any liability or responsibility for loss or damages resulting from any use of this document. CHANGES – CURRENT General This document supersedes DNV-RP-A205, October 2013. Text affected by the main changes in this edition is highlighted in red colour. However, if the changes involve a whole chapter, section or sub-section, normally only the title will be in red colour. On 12 September 2013, DNV and GL merged to form DNV GL Group. On 25 November 2013 Det Norske Veritas AS became the 100% shareholder of Germanischer Lloyd SE, the parent company of the GL Group, and on 27 November 2013 Det Norske Veritas AS, company registration number 945 748 931, changed its name to DNV GL AS. For further information, see www.dnvgl.com. Any reference in this document to “Det Norske Veritas AS”, “Det Norske Veritas”, “DNV”, “GL”, “Germanischer Lloyd SE”, “GL Group” or any other legal entity name or trading name presently owned by the DNV GL Group shall therefore also be considered a reference to “DNV GL AS”. -
Running Rigging Plans Sheet 1 of 12 Dh-04-17 View Looking Fwd Under Sheet Winch Pedestal
MAINTAMER BOOM ILLUSTRATED, SELDEN BOOM SIMILAR BAILS BY SELDEN GOOSENECK BY SELDEN HARKEN 6058 FAIRLEADS ON MAINTAMER BLOCKS (5) OR SELDEN BOOM TURNING BLOCK SHACKLES TO GOOSENECK BAIL MAINSHEET USES 115' (35M) 1/2" (12mm) BRAID, EYE SPLICE ONE END HARKEN CARS & TRACK ASSY. SEE DH-04-18, HARDTOP FITOUT SHEET DESCENDS THROUGH UP TO SHEET STARBOARD FAIRLEAD IN MAST CLUTCH & WINCH MOUNTING PLATE TO MAST BASE ORGANIZERS, SEE DH-04-15 FROM MAST BASE ORGANIZERS MAIN SHEET TACKLE HARKEN 6058 75MM ANTARES 44 DECK HARDWARE BLOCK AT SHEET PEDESTAL TURNING BRACKET RUNNING RIGGING PLANS SHEET 1 OF 12 DH-04-17 VIEW LOOKING FWD UNDER SHEET WINCH PEDESTAL FIRST ISSUE NOV.6 2003 T. C. FIRST USED VESSEL 4408 HARKEN 6058 BLOCK AT JIB CLEW HARKEN OVER THE TOP BLOCK 3002, MOUNTS ON MAST PLATE SELF-TACKING JIB SHEET IS 108' (33M) X 3/8" (10mm) DYNEMA HARKEN 6058 BLOCKS ON CARS AND PORT PADEYE HARKEN PADEYE 688, P&S HARKEN 1617 3m TRACK, COMPOUND BEND AS PER DH-04-20 HARKEN CAR ASSEMBLY 2 OF 1624 CAR 1 OF 1614 COUPLER 2 OF 1561 TOGGLE SHEET DESCENDS THROUGH HARKEN PIN STOPS STARBOARD FAIRLEAD IN MAST 1624, P&S MOUNTING PLATE TO MAST BASE HARKEN END STOPS ORGANIZERS, SEE DH-04-15 1522 P&S UP TO SHEET CLUTCH & WINCH SELF TACKING JIB SHEET TACKLE FROM MAST BASE ORGANIZERS ANTARES 44 DECK HARDWARE RUNNING RIGGING PLANS HARKEN 6058 75MM BLOCK AT SHEET PEDESTAL TURNING SHEET 2 OF 12 BRACKET DH-04-17 VIEW LOOKING FWD T. C. UNDER SHEET WINCH PEDESTAL LINE ENTERS AND EXITS FURLING LINE IS AS CHAIN LOCKER THROUGH TWO HARKEN 134NP BULLET ORIGINAL SUPPLIED WITH FURLEX. -
Manual for Furling Mast TYPE RB Mk 4
595-065-E 2020-03-23 Manual for Furling mast TYPE RB Mk 4 Contents: Page: Contents: Page: Product description 2 Fitting and hoisting the sail 8 Checks and adjustments before Stepping 4 Before sailing 9 Line routing 6 Maintenance 10 Operation 7 2 Product description • Seldén furling mast allow for convenient setting and reefing of the mainsail. • The unique design of the halyard swivel bearing distributes the load over the whole ball race to give smoother furling and the lowest possible friction, even under high loads. • The new Mk 4 compact gear mechanism offers improved gear efficiency, allows a smaller mast cutout and is prepared for easy retro fit of electric furling drive unit. • This Instruction Manual has been compiled to give you information on the furling mast reefing system. Study it and follow the instructions carefully, and we guarantee you pleasurable use from your Seldén furling mast. Follow the relevant rigging instructions in our booklet ”HINTS AND ADVICE” for tuning the rig. Fig. 2:1 Sail compartment with luff extrusion 3 Top swivel Halyard swivel Access to sail feeder and Sail feeder halyard swivel Tensioning screw Tack hook Access to tack hook and tensioning screw Outhaul car Rachet lever Winch handle socket Line driver Fig 3:1 4 Checking luff extrusion tension prior to stepping the mast The luff extrusion is correctly tensioned before leaving the factory, but tension can be re-checked before stepping the mast in the following manner. Lay the mast horizontally on the side and keep it straight. The luff extrusion should now be just clear off the mast wall at its midpoint. -
Wind Resource Assessment Handbook Was Developed Under National Renewable Energy Laboratory (NREL) Subcontract No
WWIINNDD RREESSOOUURRCCEE AASSSSEESSSSMMEENNTT HHAANNDDBBOOOOKK Fundamentals for Conducting a Successful Monitoring Program Prepared By: AWS Scientific, Inc. CESTM, 251 Fuller Road Albany, NY 12203 www.awsscientific.com April 1997 NREL Subcontract No. TAT-5-15283-01 Prepared for: National Renewable Energy Laboratory 1617 Cole Boulevard Golden, CO 80401 NOTICE: This document was prepared as an account of work sponsored by an agency of the United States government. Neither the United States government nor any agency thereof, nor any of their employees, makes any warranty, express or implied, or assumes any legal liability or responsibility for the accuracy, completeness, or usefulness of any information, apparatus, product, or process disclosed, or represents that its use would not infringe privately owned rights. Reference herein to any specific commercial product, process, or service by trade name, trademark, manufacturer, or otherwise does not necessarily constitute or imply its endorsement, recommendation, or favoring by the United States government or any agency thereof. The views and opinions of authors expressed herein do not necessarily state or reflect those of the United States government or any agency thereof. FOREWORD The Wind Resource Assessment Handbook was developed under National Renewable Energy Laboratory (NREL) Subcontract No. TAT-5-15283-01. NREL is a national laboratory of the U.S. Department of Energy managed by Midwest Research Institute under contract No. DE-AC36- 83CH10093. Much of the material presented in the handbook was originally compiled for the preparation of the U*WRAP Handbook. This publication was written by AWS Scientific, Inc., in support of the Utility Wind Resource Assessment Program (U*WRAP), and was distributed to interested utilities. -
Glossary of Nautical Terms the Maritime World Has a Language of Its Own
Glossary of Nautical Terms The maritime world has a language of its own. It may seem silly to use special terms instead of simply using one that we use for the same thing shore side, but it actually serves a practical purpose. For example, why not just call a galley a kitchen; it’s just a place where you cook food, right? Not exactly, in a kitchen you can leave pot of hot soup on the counter and, barring some geological event, it will still be there when you get back. In a galley, it is more likely to be all over the deck upon return. Using the proper terminology aboard a vessel helps to enforce the mindset that the maritime environment is different from that on shore and therefore, demands a different code of conduct. Objects: Bit: Two adjacent posts used for mooring or making a line fast to Bollard: A single post used for mooring or making a line fast to Boom: (1) Horizontal spar attached to the foot of a sail; (2) A spar used for lifting such as on a crane or davit Bow: The forward end of the vessel *Bowsprit: Spar protruding from the bow of a sailing vessel used for the attachment of the headsails Bulkhead: A vertical partition inside a vessel Bulwark: A partition extending above the weather deck of a vessel used to prevent seas from washing over and keep objects and personnel from going overboard Capstan: Deck winch, usually configured vertically, used for hauling in lines See Windlass. Ceiling: Planking on the interior sides the hull used for separating internal space from the frame bays; in some cases used to increase hull stiffness to prevent hogging particularly in wood vessels (Hogging is the sagging of the vessel towards the bow and stern due to lack of floatation from the narrowing of the hull. -
The Evolution of Decorative Work on English Men-Of-War from the 16
THE EVOLUTION OF DECORATIVE WORK ON ENGLISH MEN-OF-WAR FROM THE 16th TO THE 19th CENTURIES A Thesis by ALISA MICHELE STEERE Submitted to the Office of Graduate Studies of Texas A&M University in partial fulfillment of the requirements for the degree of MASTER OF ARTS May 2005 Major Subject: Anthropology THE EVOLUTION OF DECORATIVE WORK ON ENGLISH MEN-OF-WAR FROM THE 16th TO THE 19th CENTURIES A Thesis by ALISA MICHELE STEERE Submitted to the Office of Graduate Studies of Texas A&M University in partial fulfillment of the requirements for the degree of MASTER OF ARTS Approved as to style and content by: C. Wayne Smith James M. Rosenheim (Chair of Committee) (Member) Luis Filipe Vieira de Castro David L. Carlson (Member) (Head of Department) May 2005 Major Subject: Anthropology iii ABSTRACT The Evolution of Decorative Work on English Men-of-War from the 16th to the 19th Centuries. (May 2005) Alisa Michele Steere, B.A., Texas A&M University Chair of Advisory Committee: Dr. C. Wayne Smith A mixture of shipbuilding, architecture, and art went into producing the wooden decorative work aboard ships of all nations from around the late 1500s until the advent of steam and the steel ship in the late 19th century. The leading humanists and artists in each country were called upon to draw up the iconographic plan for a ship’s ornamentation and to ensure that the work was done according to the ruler’s instructions. By looking through previous research, admiralty records, archaeological examples, and contemporary ship models, the progression of this maritime art form can be followed. -
Marine Investigation Report M11w0091
MARINE INVESTIGATION REPORT M11W0091 STRIKING OF A BRIDGE TUG F.W. WRIGHT AND BARGE EMPIRE 40 FRASER RIVER QUEENSBOROUGH RAILWAY BRIDGE, BRITISH COLUMBIA 28 JUNE 2011 The Transportation Safety Board of Canada (TSB) investigated this occurrence for the purpose of advancing transportation safety. It is not the function of the Board to assign fault or determine civil or criminal liability. Marine Investigation Report Striking of a Bridge Tug F.W. Wright and Barge Empire 40 Fraser River Queensborough Railway Bridge, British Columbia 28 June 2011 Report Number M11W0091 Summary On 28 June 2011 at 0410 Pacific Daylight Time, while under tow of the tug F.W. Wright, the loaded gravel barge Empire 40 struck the Queensborough Railway Bridge in the Fraser River, British Columbia. The bridge centre swing span and protection pier sustained extensive damage. This resulted in the bridge being inoperable for a period of 2 months after the striking, causing major disruptions to railway and river traffic. No one was injured and there was no pollution as a result of this occurrence. Ce rapport est également disponible en français. -2- Factual Information Particulars of the Vessels Names of vessels F.W. Wright Empire 40 Official number 807707 372638 Port of registry Victoria, British Columbia Vancouver, British Columbia Flag Canada Canada Type Tug Barge Gross Tonnage 8.17 1674 Length 1 12.59 m 61.57 m Breadth 5.49 m 17.71 m Draught 3.0 m 4.23 m Built 1987 1977 Propulsion Twin diesel engines Non–propelled (328 kilowatts each), twin fixed-pitch propellers Cargo N/A 3600 tons paving aggregate Crew 3 Unmanned Registered owners Mercury Launch & Tug Ltd.