The Behaviour of Polytetrafluoroethylene at High Pressure
Total Page:16
File Type:pdf, Size:1020Kb
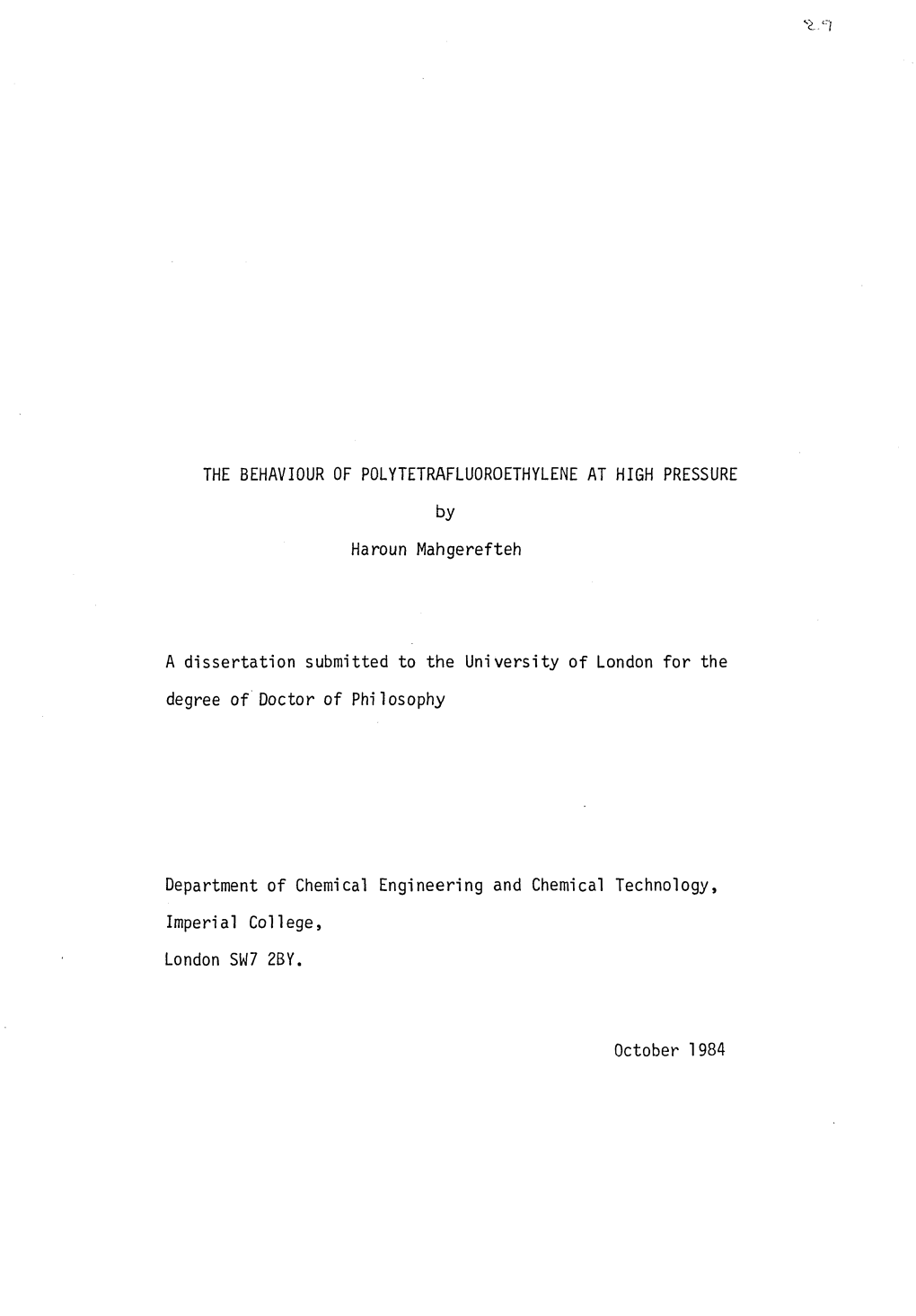
Load more
Recommended publications
-
Laser Isotope Separation (LIS), Technical and Economic
NASA TECHNICAL MEMORANDUM A STATUS OF PROGRESS FOR THL LASER lsofopE SEPARATION (11 SI PROCESS +tear 1976 NASA George C. Mdr~bdlSpace Flight Center Marshdl Space Fb$t Center, Alabama lLSFC - Form 3190 (Rev June 1971) REPORT STANDARD TITLE PACE I nEPMTn0. 3. RECIPIENT*$ CATILOC NO. NASA TM X-73345 10 TITLE UO SUTlTLt IS. REPORT DATE I September A st.tUaof for Iaser isotOpe ¶tian lS76 I Progress the (LIS) 6 PERFWYIIIG WGUIZATIO* CQOE George C. M8ralmll!3gam Flight Center I 1. COUTRUT OR am yo. I MarW Flight Center, Alabama 35812 Tecbnid Memormdum National Aemutics and Space Administration Washingtan, D.C. 20546 I I Prepared by Systems Aaalysis and Integration Iaboratory, Science and Engineering An overview of the various categories of the LE3 methodology is given together with illustrations showing a simplified version of the LIS tecbnique, an example of the two-phoiin photoionization category, and a diagram depicting how the energy levels of various isdope influence the LIS process. A&icatlons have been proposed for the LIS system which, in addition to the use to enrich uranium, could in themselves develop into programs of tremendous scope and breadth. Such applications as treatment of radioac '--ewastes from light-water nKzlear reactors, enriching the deuterlum isotope to make heavv-water, and enrlchhg tik light isotopes of such 17 KEt WORDS 18. DISTRIBUTION STATEMENT 5ECUQlTY CLASSIF. Ff thh PI*) 21 NO. OF PAbFS 22 PRICE Unclassified Unclassified I 20 NTIS PREFACE Since the publication of t& first Techid hiemomxitun (TM X-64947) on the Laser hotope Separation (LE)process in May 1975 [l], there bbeen a virtual explosion of available information on this process. -
Economic Perspective for Uranium Enrichment
SIDEBAR 1: Economic Perspective for Uranium Enrichment he future demand for enriched are the customary measure of the effort uranium to fuel nuclear power required to produce, from a feed material plants is uncertain, Estimates of with a fried concentration of the desired T this demand depend on assump- isotope, a specified amount of product en- tions concerning projections of total electric riched to a specified concentration and tails, power demand, financial considerations, and or wastes, depleted to a specified concentra- government policies. The U.S. Department tion. For example, from feed material with a of Energy recently estimated that between uranium-235 concentration of 0.7 per cent now and the end of this century the gener- (the naturally occurring concentration), ation of nuclear power, and hence the need production of a kilogram of uranium enrich- for enriched uranium, will increase by a ed to about 3 per cent (the concentration factor of 2 to 3 both here and abroad. Sale of suitable for light-water reactor fuel) with tails enriched uranium to satisfy this increased depleted to 0.2 per cent requires about 4.3 demand can represent an important source SWU. of revenue for the United States, Through Gaseous diffusion is based on the greater fiscal year 1980 our cumulative revenues rate of diffusion through a porous barrier of from such sales amounted to over 7 billion the lighter component of a compressed dollars, and until recently foreign sales ac- gaseous mixture. For uranium enrichment counted for a major portion of this revenue. the gaseous mixture consists of uranium The sole source of enriched uranium until hexafluoride molecules containing 23$ 1974, the United States now supplies only uranium-235 ( UF6) or uranium-238 238 about 30 per cent of foreign demand, New ( UF6). -
Highly Enriched Uranium (HEU) Is Defined As Uranium That Has Been Enriched to 20 Percent Or Greater in the Uranium-235 Isotope
- DRAFT U.S. DEPARTMENTOF ENERGY NATIONALNUCLEAR SECURITY ADMINISTRATION OFFICEOF THE DEPUTYADMINISTRATOR FOR DEFENSEPROGRAMS OFFICIAL USE ONLY - DRAFT - DRAFT U.S. DEPARTMENTOF ENERGY NATIONALNUCLEAR SECURITY ADMINISTRATION OFFICEOF THE DEPUTYADMINISTRATOR FOR DEFENSEPROGRAMS JANUARY200 1 - DRAFT - DRAFT Highly enriched uranium (HEU) is defined as uranium that has been enriched to 20 percent or greater in the uranium-235 isotope. All HEU is considered to be weapons-usable. HEU comes in different forms, including metals, oxides, solutions, reactor fuel, and irradiated spent nuclear fuel. Pictured above is a metal disk or "button" of HEU. - DRAFT - DRAFT .TABLE OF CONTENTS YL..*--~-*..~~.. -- - &*. +"-. w-~P~zF~zr~--~-"?wa~..=-&..m~w-=..L " EXECUTIVESUMMARY ...................................................................................... 1 BACKGROUND.................................................................................................................. 1 U.S. HEU INVENTORY...................................................................................................... 2 MATERIALBALANCE .......................................................................................................... 3 NEWLYDECLASSIFIED INFORMATION ........................................................................................ 3 CORRECTIONSTO PREVIOUSLY RELEASED DATA ........................................................................ 3 SECTION2 = URANIUMPRODUCTION AND UTILIZATION........................................... 21 OVERVIEWOF -
An Access-Dictionary of Internationalist High Tech Latinate English
An Access-Dictionary of Internationalist High Tech Latinate English Excerpted from Word Power, Public Speaking Confidence, and Dictionary-Based Learning, Copyright © 2007 by Robert Oliphant, columnist, Education News Author of The Latin-Old English Glossary in British Museum MS 3376 (Mouton, 1966) and A Piano for Mrs. Cimino (Prentice Hall, 1980) INTRODUCTION Strictly speaking, this is simply a list of technical terms: 30,680 of them presented in an alphabetical sequence of 52 professional subject fields ranging from Aeronautics to Zoology. Practically considered, though, every item on the list can be quickly accessed in the Random House Webster’s Unabridged Dictionary (RHU), updated second edition of 2007, or in its CD – ROM WordGenius® version. So what’s here is actually an in-depth learning tool for mastering the basic vocabularies of what today can fairly be called American-Pronunciation Internationalist High Tech Latinate English. Dictionary authority. This list, by virtue of its dictionary link, has far more authority than a conventional professional-subject glossary, even the one offered online by the University of Maryland Medical Center. American dictionaries, after all, have always assigned their technical terms to professional experts in specific fields, identified those experts in print, and in effect held them responsible for the accuracy and comprehensiveness of each entry. Even more important, the entries themselves offer learners a complete sketch of each target word (headword). Memorization. For professionals, memorization is a basic career requirement. Any physician will tell you how much of it is called for in medical school and how hard it is, thanks to thousands of strange, exotic shapes like <myocardium> that have to be taken apart in the mind and reassembled like pieces of an unpronounceable jigsaw puzzle. -
The Gaseous Diffusion Process
The Gaseous Diffusion Process The Portsmouth Gaseous Diffusion Plant, built in 1953-1954, produces enriched uranium hexafluoride (UF6) for commercial power reactors. In the past highly enriched uranium hexafluoride 235 was produced for the U.S. Navy. Enriched UF6 is material that contains the isotope U in assays (concentrations) greater than 0.711 weight percent. Commercial power plants currently use uranium enriched to the 3 to 5 percent range. The plant is capable of producing a range of U235 assays from 0.2% to over 97%. In late 1991, the equipment that produced high assay uranium was taken off line and placed in long term shutdown. High assay material that was declared excess by the US Navy and Department of Energy was fed into the cascade and blended down to the assays used by commercial power plants. This refeed project was completed in July 1998. It is possible that other high assay material will be declared excess in the future and would possibly be blended down at PORTS. It is also possible that high assay production could be resumed in the future. The plant's certification under the Nuclear Regulatory Commission (NRC) limits the maximum assay to 10%. Enrichment is accomplished using gaseous diffusion technology as the name implies. The gaseous diffusion cascade consists of many stages of equipment connected in series, i.e., in a cascade arrangement. Each stage consists of an electric motor, a compressor, and a converter which contains 235 a porous membrane through which the lighter U F6 diffuses at a slightly faster rate than the heavier 238 U F6. -
Actinide Series
20-Mar-20 Lecture 6-8 ACTINIDE SERIES (5f- elements) 4th year (Micro/Chem- Botany/Chem and Biochemistry) 18 Occurrence and Preparation of the Elements • Ac, Th, Pa, U are naturally occur • All known isotopes of all actinide metals are radioactive. • Thorium (Th) occurs in monazite sands, which are up to 20% ThO2. • Chemically it can be prepared from thermal decomposition of the iodide (de Boer process): ThI4 → Th + 2I2 • Uranium (U) occurs (at about 0.1%) in uraninite ores as U3O8, and carnotite as K2(UO2)2(VO4)2·3H2O. 19 1 20-Mar-20 Occurrence and Preparation of the Elements • The transuranic elements must all be prepared artificially. • About 1200 tonnes of plutonium (Pu) have been produced worldwide in reactors! 20 Actinide Metals Preparation • Reduction of AnF3 or AnF4 with vapors of Li, Mg, Ca or Ba at 1100 - 1400°C • Chlorides and oxides can be similarly reduced. Example: • Am can be Chemically prepared by reduction of AmF3 with Ba: 3Ba(g) + 2AmF3 → 3BaF2 + 2Am • Or by reduction of americium oxide with lanthanum (La) at 1200oC: Am2O3 + 2La → La2O3 + 2Am 21 2 20-Mar-20 Chemical reactivity of Actinides • Actinides are Highly reactive metals, especially when finely divided. • Typically react with: • air → tarnishing • boiling water or dilute acid → releasing Hydrogen • most non-metals in direct combination • Alkalies have no effect. 22 Oxides and hydroxides • Some actinides can exists in several oxide forms such as An2O3, AnO2, An2O5 and AnO3. • For all actinides, oxides AnO3 are amphoteric and An2O3, AnO2 and An2O5 are basic, they easily react with water, forming bases: An2O3 + 3 H2O → 2 An(OH)3. -
Portsmouth Gaseous Diffusion Plant Spill Report 9-1 Underground Storage Tanks (Usts) 9-1
ES/ESH-50 POEF-3050 PORTSMOUTH GASEOUS DIFFUSION PLANT ANNUAL SITE ENVIRONMENTAL REPORT FOR 1993 Project director F. C. Kornegay Project coordinator D. C. West Technical coordinator S. C. Newman Coordinating editor C. M. Horak Date Published: November 1994 Prepared by Environmental, Safety, and Health Compliance and Environmental Management staffs MARTIN MARIETTA ENERGY SYSTEMS, INC. P.O. Box 2008 Oak Ridge, Tennessee 37831-6285 and the Environmental Control Department Portsmouth Gaseous Diffusion Plant MARTIN MARIETTA ENERGY SYSTEMS, INC. P.O. Box 628 P^OMo 45661 |„ftT, U.S. DEPARTMENT OF ENERGY If i§ Ofm under contract No. DE-AC05-84OR21400 «t?3ff" & %M M ^ ^ and MARTIN MARIETTA UTILITY SERVICES, INC. for the UNITED STATES ENRICHMENT CORPORATION under contract No. DE-AC05-76OR00001 ^-^a*11^-'^ DISCLAIMER This report was prepared as an account of work sponsored by an agency of the United States Government. Neither the United States Government nor any agency thereof, nor any of their employees, make any warranty, express or implied, or assumes any legal liability or responsibility for the accuracy, completeness, or usefulness of any information, apparatus, product, or process disclosed, or represents that its use would not infringe privately owned rights. Reference herein to any specific commercial product, process, or service by trade name, trademark, manufacturer, or otherwise does not necessarily constitute or imply its endorsement, recommendation, or favoring by the United States Government or any agency thereof. The views and opinions of authors expressed herein do not necessarily state or reflect those of the United States Government or any agency thereof. DISCLAIMER Portions of this document may be illegible in electronic image products. -
Mining, Milling, Conversion, and Enrichment of Uranium Ores
MINING, MILLING, CONVERSION, AND ENRICHMENT OF URANIUM ORES Presented by Lisa Loden Export Control Implementation Global Nuclear Security Technology Division Oak Ridge National Laboratory Oak Ridge, TN 37830 Based on the slides of the late Dr. Clarence J. Hardy Past President Pacific Nuclear Council Secretary, Australian Nuclear Association Managing Director, Nuclear Fuel Australia Ltd July 19, 2011 Uranium Background Key points over 150 years •1789 – Uranium was discovered by Klaproth in Germany and named after the planet Uranus recently discovered by Herschel. •1896 – Professor Becquerel in Paris discovered radioactivity in uranium minerals; radium was then discovered by Mme. Curie in Paris. •1910 – Dr. Soddy in Cambridge, UK, proposed “isotopes” for atoms with different atomic weights but identical chemical properties. •1913 – Professor Thomson at Cambridge showed neon had “isotopes,” and, therefore, other elements were likely to have them, too. •1932 – Dr. Chadwick at Cambridge discovered the neutron. •1935 – Dr. Dempster in Chicago showed uranium contained 0.7% of uranium-235 and the rest was uranium-238. Uranium structure was shown to be 92 p and 146 n in U-238; 92 p and 143 n in U-235. Background to the Nuclear Fuel Cycle •1939 – Discovery of fission of uranium by Hahn and Strassman in Germany with extra neutrons released gave rise to the possibility of a chain reaction. •1939–1942 – Concept of an atomic bomb was developed in UK, U.S., and Germany. •1942 – Start of the Manhattan Project and the need for the nuclear fuel cycle with uranium ore processing, uranium enrichment, plutonium production, etc. •1942 – Chemical and physical separation processes became very important for the production of large amounts of uranium-235 and plutonium. -
An Atomic History Chapter 2
An Atomic History 0-3 8/11/02 7:31 AM Page 18 Chapter Two 19 THE FERMI-SZILARD PILE AND URANIUM RESEARCH The first government funding for nuclear research was allocated to purchase graphite and uranium oxide for the chain reaction experiments being organized by Fermi and World War II and the Manhattan Project Szilard at Columbia University in February 1940.2 This work, which began in New York 2 City, soon spread to Princeton, the University of Chicago, and research institutions in California.3 Even at this stage, the scientists knew that a chain reaction would need three major components in the right combination: fuel, moderator, and coolant. The fuel would contain the fissile material needed to support the fission process. The neutrons generated by the fission process had to be slowed by the moderator so that they could initiate addi- tional fission reactions. The heat that resulted from this process had to be removed by the coolant. Fermi’s initial research explored the possibility of a chain reaction with natural urani- The 1930s were a time of rapid progress in the development of nuclear physics. um. It was quickly determined that high-purity graphite served as the best neutron moder- Research accelerated in the early years of the Second World War, when new developments ator out of the materials then available.4 After extensive tests throughout 1940 and early were conceived and implemented in the midst of increasing wartime urgency. American 1941, Fermi and Szilard set up the first blocks of graphite at Columbia University in government interest in these developments was limited at first, but increased as the war September 1941. -
Agenda November 14, 2012 Page 2 Dr
ORANGE WATER AND SEWER AUTHORITY A public, non-profit agency providing water, sewer and reclaimed water services to the Carrboro-Chapel Hill community. MEMORANDUM TO: Natural Resources/Technical Systems Committee Terri Buckner (Chair) Dana Stidham Stephen Dear Michael Hughes Will Raymond Amy Witsil Alan Rimer (ex officio) THROUGH: Ed Kerwin FROM: Mason Crum DATE: November 14, 2012 SUBJECT: December 4, 2012 Natural Resources/Technical Systems (NRTS) Committee Meeting The NRTS Committee will meet December 4, 2012 at 4:00 PM in the OWASA Community Room. The Committee will discuss the two petitions received from the public on August 23rd and September 27th requesting that OWASA discontinue its current practice of adding fluoride to drinking water as part of the treatment process at the Jones Ferry Road Water Treatment Plant. The Committee Chair, Ms. Terri Buckner, and the OWASA staff have contacted Dr. Rebecca King, Section Chief of the NC Oral Health Section and Mr. Allen Spalt, co-founder of Toxic Free North Carolina and previous Carrboro Alderman, and they will participate in the Committee’s discussions. We will invite to the meeting the two petitioners and all OWASA customers (approximately 25) that have asked questions about our fluoridation practices since 1998. Please note that the NRTS Committee will not receive comments from the public at this Committee meeting. However, the public is welcome to present comments or petition the OWASA Board at any of its regularly scheduled Board meetings. Attached are statements from the following individuals/organizations stating their support for fluoridation of drinking water: Dr. L. Herald, State Health Director Dr. -
Uranium Enrichment Processes Directed Self-Study Course! This Is the Fifth of Seven Modules Available in This Self-Study Course
MODULE 5.0: ELECTROMAGNETIC SEPARATION (CALUTRON) AND THERMAL DIFFUSION Introduction Welcome to Module 5.0 of the Uranium Enrichment Processes Directed Self-Study Course! This is the fifth of seven modules available in this self-study course. The purpose of this module is to assist the trainee in describing the general principles of the electromagnetic separation (calutron) and thermal diffusion technologies and general facility and component layouts, identifying the uses of the calutron and thermal diffusion processes in industry and the production amounts of enriched uranium, and identifying the hazards and safety concerns for each process, including major incidents. This self-study module is designed to assist you in accomplishing the learning objectives listed at the beginning of the module. There are eight sections in this module. The module has self-check questions to help you assess your understanding of the concepts presented in the module. Before you Begin It is recommended that you have access to the following materials: 9 Trainee Guide Complete the following prerequisite: 9 Module 1.0 Introduction to Uranium Enrichment 1. Review the learning objectives. 2. Read each section within the module in sequential order. How to Complete 3. Complete the self-check questions and activities within this This Module module. 4. Check off the tracking form as you complete the self-check questions and/or activity within the module. 5. Contact your administrator as prompted for a progress review meeting. 6. Contact your administrator as prompted for any additional materials and/or specific assignments. 7. Complete all assignments related to this module. If no other materials or assignments are given to you by your administrator, you have completed this module. -
Designing the Bomb
designing the bomb The world’s first man-made atomic explosion take place efficiently and at the right time. A verit- took place only 28 months after the arrival of the able mountain of difficulties stood in the way. first scientific contingent at Los Alamos. Few greater No one knew how much fissionable material had tributes to human ingenuity have ever been written. to be put together to support an explosive chain The theoretical basis for nuclear weapons was reaction, but it was known that the reaction could already understood, in its outlines, when the Lab- not occur if the amount were insufficient. The oratory was established. Many of the engineering burning of conventional explosives is a chain reac- problems were foreseen in a general way, but much tion of a different kind; a tiny quantity of TNT remained to be done. The following summary of burns as readily as a larger amount. Fission chains weapon theory (all of it known in early 1943) will serve to suggest the enormous difficulty of the task cannot occur in the saline way, because the neutrons that lay ahead. on which they depend must remain within the fuel The nucleus of an atom of uranium-235 contains until they encounter fissionable nuclei. If the sur- 92 protons and 143 neutrons. When this nucleus face area of the fuel mass is large compared to the absorbs an additional neutron, it becomes unstable volume (i.e., if the fuel mass is too small or too and usually divides approximately in half. The two much flattened out), then the neutron escape area fragments become nuclei of two lighter elements, is too large compared to the neutron source volume, having a total mass somewhat less than the mass of and too many neutrons will find their way out with- the original uranium nucleus plus the additional out causing fission.