PATENT OFFICE 2,632,026 OXDATION OFAROMATIC HYDROCARBONS Joshua C
Total Page:16
File Type:pdf, Size:1020Kb
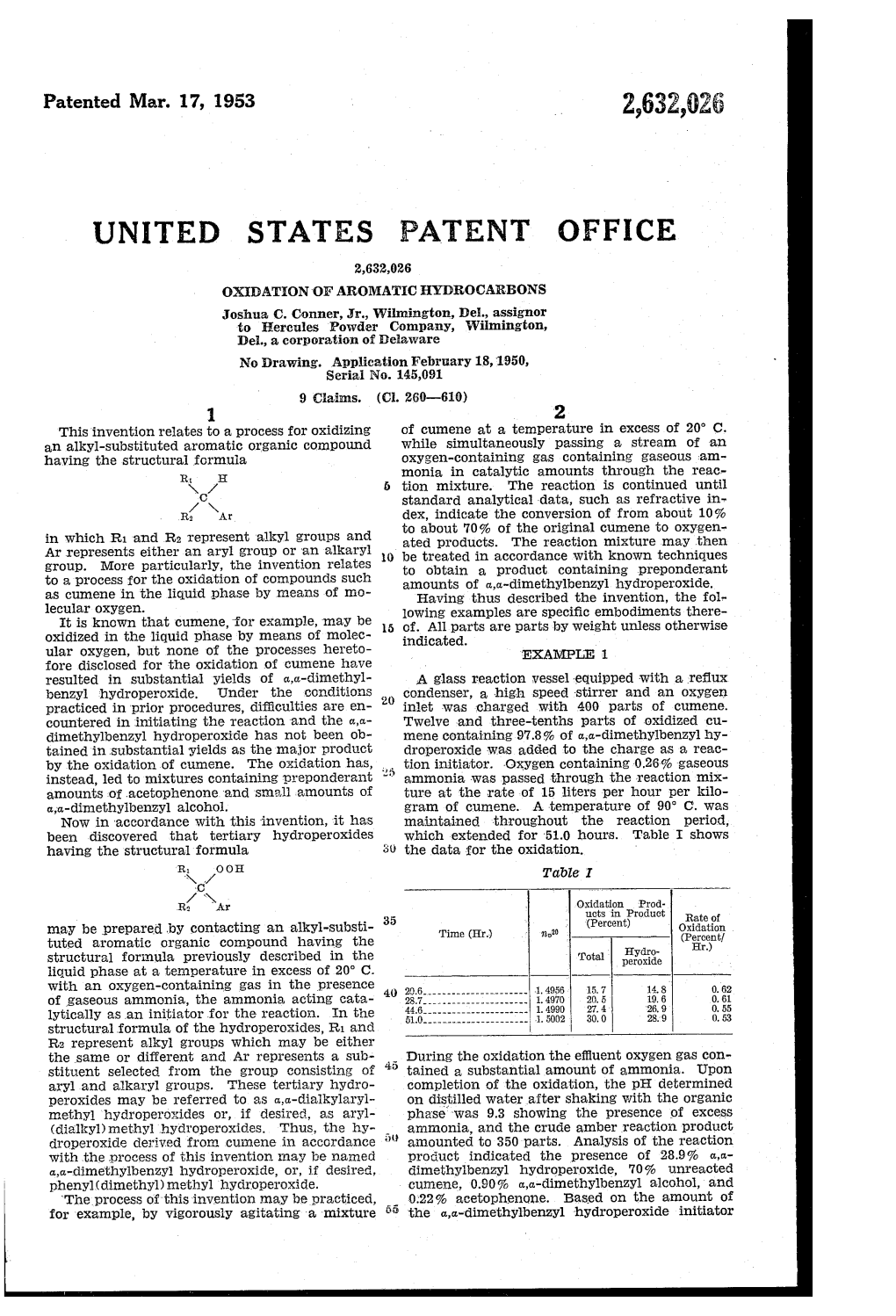
Load more
Recommended publications
-
The Evolutionary Story Ahead of Biochemistry
Downloaded from http://cshperspectives.cshlp.org/ on September 24, 2021 - Published by Cold Spring Harbor Laboratory Press The Organic Composition of Carbonaceous Meteorites: The Evolutionary Story Ahead of Biochemistry Sandra Pizzarello1 and Everett Shock1,2 1Department of Chemistry and Biochemistry, Arizona State University, Tempe, Arizona 85287-1604 2School of Earth and Space Exploration, Arizona State University, Tempe, Arizona 85287-1404 Correspondence: [email protected] Carbon-containing meteorites provide a natural sample of the extraterrestrial organic chemistry that occurred in the solar system ahead of life’s origin on the Earth. Analyses of 40 years have shown the organic content of these meteorites to be materials as diverse as kerogen-like macromolecules and simpler soluble compounds such as amino acids and polyols. Many meteoritic molecules have identical counterpart in the biosphere and, in a primitive group of meteorites, represent the majority of their carbon. Most of the compounds in meteorites have isotopic compositions that date their formation to presolar environments and reveal a long and active cosmochemical evolution of the biogenic elements. Whether this evolution resumed on the Earth to foster biogenesis after exogenous deliveryof meteoritic and cometary materials is not known, yet, the selective abundance of biomolecule precur- sors evident in some cosmic environments and the unique L-asymmetry of some meteoritic amino acids are suggestive of their possible contribution to terrestrial molecular evolution. INTRODUCTION that fostered biogenesis. These conditions are entirely unknown because geological and Why Meteorites are Part of the Discourse biological processes of over four billion years about the Origin of Life have long eradicated any traces of early Earth’s he studies of meteorites have long been part chemistry. -
Volatile Organic Compounds, Polycyclic Aromatic Hydrocarbons and Elements in the Air of Ten Urban Homes
AIVC #13,657 J11<loor Air 2001; 11: 49-64 Copyrigfil © Mi111ksg11nl'd 2001 /itlp;//jo11mnls.1111111ksgnard.dlr/i11doornir L'IDOOR AIR Pd1lied in De1111111rk. All rights reserved ISSN 0905-6947 Volatile Organic Compounds, Polycyclic Aromatic Hydrocarbons and Elements in the Air of Ten Urban Homes MICHAEL R. VAN WINKLE1 AND PETER A. SCHEFF2* istics or occupant activities. The data indicate that several pre Abstract Ten homes were monitored at regular intervals from dietor variables, including mothball storage, air freshener use, June 1994 through April 1995 as part of a Public Health Assess and cooking activities, are reasonable predictors for emission ment in Southeast Chicago for exposure to volatile organic com rates of specific pollutants in the homes. pounds (VOCs), polycyclic aromatic hydrocarbons (PAHs), and elements. Simultaneous 24-h indoor and outdoor samples were Received for review 24 March 1999. Accepted for publication 11 March 2000. collected. VOCs were and analyzed using USEPA Method T0-14 © Indoor Air (2001) with Selected Ion Monitoring Mass Spectrometry (GC/MS). PAHs were analyzed using USEPA Method T0-13 with GC/MS. Elements were collected on quartz fiber filters and analyzed by Inductively Coupled Argon Plasma (ICP) spectroscopy or Graph ite Furnace Atomic Absorption (GFA A). Continuous measure Introduction ments of C02 and temperature were recorded for each indoor Exposure to indoor airborne pollutants is a function of sample. Twenty-four h total C02 emissions were determined from occupancy and estimated gas stove usage and were moder many variables, including pollutant infiltration, exfil 2 ately correlated (R =0.19) with 24 h average indoor C02 concen tration, deposition, resuspension, filtration, and gener trations. -
Phosphorus and Sulfur Cosmochemistry: Implications for the Origins of Life
Phosphorus and Sulfur Cosmochemistry: Implications for the Origins of Life Item Type text; Electronic Dissertation Authors Pasek, Matthew Adam Publisher The University of Arizona. Rights Copyright © is held by the author. Digital access to this material is made possible by the University Libraries, University of Arizona. Further transmission, reproduction or presentation (such as public display or performance) of protected items is prohibited except with permission of the author. Download date 07/10/2021 06:16:37 Link to Item http://hdl.handle.net/10150/194288 PHOSPHORUS AND SULFUR COSMOCHEMISTRY: IMPLICATIONS FOR THE ORIGINS OF LIFE by Matthew Adam Pasek ________________________ A Dissertation Submitted to the Faculty of the DEPARTMENT OF PLANETARY SCIENCE In Partial Fulfillment of the Requirements For the Degree of DOCTOR OF PHILOSOPHY In the Graduate College UNIVERSITY OF ARIZONA 2 0 0 6 2 THE UNIVERSITY OF ARIZONA GRADUATE COLLEGE As members of the Dissertation Committee, we certify that we have read the dissertation prepared by Matthew Adam Pasek entitled Phosphorus and Sulfur Cosmochemistry: Implications for the Origins of Life and recommend that it be accepted as fulfilling the dissertation requirement for the Degree of Doctor of Philosophy _______________________________________________________________________ Date: 04/11/2006 Dante Lauretta _______________________________________________________________________ Date: 04/11/2006 Timothy Swindle _______________________________________________________________________ Date: 04/11/2006 -
Experimental Analysis and Modeling Aspects of the Removal of Polycyclic Aromatic Hydrocarbons in Soil Slurry Bioreactors Douglas Pino Herrera
Experimental analysis and modeling aspects of the removal of polycyclic aromatic hydrocarbons in soil slurry bioreactors Douglas Pino Herrera To cite this version: Douglas Pino Herrera. Experimental analysis and modeling aspects of the removal of polycyclic aromatic hydrocarbons in soil slurry bioreactors. Earth Sciences. Université Paris-Est, 2018. English. NNT : 2018PESC2190. tel-03012451 HAL Id: tel-03012451 https://tel.archives-ouvertes.fr/tel-03012451 Submitted on 18 Nov 2020 HAL is a multi-disciplinary open access L’archive ouverte pluridisciplinaire HAL, est archive for the deposit and dissemination of sci- destinée au dépôt et à la diffusion de documents entific research documents, whether they are pub- scientifiques de niveau recherche, publiés ou non, lished or not. The documents may come from émanant des établissements d’enseignement et de teaching and research institutions in France or recherche français ou étrangers, des laboratoires abroad, or from public or private research centers. publics ou privés. Experimental analysis and modeling aspects of the removal of PAHs in soil slurry bioreactor Douglas Oswaldo Pino Herrera Thesis committee Thesis Promotor Reviewers Prof. Mehmet A. Oturan Prof. Marie-Odile Simonnot Université Paris-Est Université de Lorraine Marne-la-Vallée, France Nancy, France Thesis Co-Promotors Prof. Francesca Beolchini Dr. Hab. Eric D. van Hullebusch, Università Politecnica delle Marche Université Paris-Est Ancona, Italy Marne-la-Vallée, France Examiners Dr. Giovanni Esposito, Prof. Piet Lens University of Cassino and Southern Lazio UNESCO-IHE Delft Cassino, Italy Delft, The Netherlands Thesis Supervisor Dr. Yannick Fayolle Dr. Yoan Pechaud Irstea Université Paris-Est Antony, France Marne-la-Vallée, France Dr. -
INVESTIGATION of POLYCYCLIC AROMATIC HYDROCARBONS (Pahs) on DRY FLUE GAS DESULFURIZATION (FGD) BY-PRODUCTS
INVESTIGATION OF POLYCYCLIC AROMATIC HYDROCARBONS (PAHs) ON DRY FLUE GAS DESULFURIZATION (FGD) BY-PRODUCTS DISSERTATION Presented in Partial Fulfillment of the Requirements for the Degree Doctor of Philosophy in the Graduate School of The Ohio State University By Ping Sun, M.S. ***** The Ohio State University 2004 Dissertation Committee: Approved by Professor Linda Weavers, Adviser Professor Harold Walker Professor Patrick Hatcher Adviser Professor Yu-Ping Chin Civil Engineering Graduate Program ABSTRACT The primary goal of this research was to examine polycyclic aromatic hydrocarbons (PAHs) on dry FGD by-products to determine environmentally safe reuse options of this material. Due to the lack of information on the analytical procedures for measuring PAHs on FGD by-products, our initial work focused on analytical method development. Comparison of the traditional Soxhlet extraction, automatic Soxhlet extraction, and ultrasonic extraction was conducted to optimize the extraction of PAHs from lime spray dryer (LSD) ash (a common dry FGD by-product). Due to the short extraction time, ultrasonic extraction was further optimized by testing different organic solvents. Ultrasonic extraction with toluene as the solvent turned out to be a fast and efficient method to extract PAHs from LSD ash. The possible reactions of PAHs under standard ultrasonic extraction conditions were then studied to address concern over the possible degradation of PAHs by ultrasound. By sonicating model PAHs including naphthalene, phenanthrene and pyrene in organic solutions, extraction parameters including solvent type, solute concentration, and sonication time on reactions of PAHs were examined. A hexane: acetone (1:1 V/V) ii mixture resulted in less PAH degradation than a dichloromethane (DCM): acetone (1:1 V/V) mixture. -
The Emergence of Nucleic Acids in an Iron-Sulphur World
Cardiff University School of Earth, Ocean and Planetary Sciences THE EMERGENCE OF NUCLEIC ACIDS IN AN IRON-SULPHUR WORLD By Bryan Hatton Thesis submitted for the Degree of Philosophiae Doctor September 2007 UMI Number: U585139 All rights reserved INFORMATION TO ALL USERS The quality of this reproduction is dependent upon the quality of the copy submitted. In the unlikely event that the author did not send a complete manuscript and there are missing pages, these will be noted. Also, if material had to be removed, a note will indicate the deletion. Dissertation Publishing UMI U585139 Published by ProQuest LLC 2013. Copyright in the Dissertation held by the Author. Microform Edition © ProQuest LLC. All rights reserved. This work is protected against unauthorized copying under Title 17, United States Code. ProQuest LLC 789 East Eisenhower Parkway P.O. Box 1346 Ann Arbor, Ml 48106-1346 DECLARATION This work has not previously been accepted in substance for any degree and is not concurrently submitted in candidature for any degree. Signed . { 3 3 ...................(candidate) Date STATEMENT 1 This U ^j^s^being submitted in partial fulfillment of the requirements for the degree of Signed (3. r. 3 3 3 ^ 3 ^ ..............(candidate) STATEMENT 2 This thesis is the result of my own independent work/investigation, except where otherwise stated. Other sources are acknowledged by explicit references. Signed 33. (candidate) D a te <3? STATEMENT 3 I hereby give consent for my thesis, if accepted, to be available for photocopying and for inter-library loan, and for the title and summary to be made available to outside organisations. -
Polycyclic Aromatic Hydrocarbon (PAH) Distributions Within Urban Estuarine Sediments
W&M ScholarWorks Dissertations, Theses, and Masters Projects Theses, Dissertations, & Master Projects 1997 Polycyclic aromatic hydrocarbon (PAH) distributions within urban estuarine sediments Siddhartha Mitra College of William and Mary - Virginia Institute of Marine Science Follow this and additional works at: https://scholarworks.wm.edu/etd Part of the Biogeochemistry Commons, Environmental Sciences Commons, and the Geochemistry Commons Recommended Citation Mitra, Siddhartha, "Polycyclic aromatic hydrocarbon (PAH) distributions within urban estuarine sediments" (1997). Dissertations, Theses, and Masters Projects. Paper 1539616779. https://dx.doi.org/doi:10.25773/v5-74km-4h38 This Dissertation is brought to you for free and open access by the Theses, Dissertations, & Master Projects at W&M ScholarWorks. It has been accepted for inclusion in Dissertations, Theses, and Masters Projects by an authorized administrator of W&M ScholarWorks. For more information, please contact [email protected]. INFORMATION TO USERS This manuscript has been reproduced from the microfilm master. UMI films the text directly from the original or copy submitted. Thus, some thesis and dissertation copies are in typewriter face, while others may be from any type o f computer printer. The quality of this reproduction is dependent upon the quality of the copy submitted. Broken or indistinct print, colored or poor quality illustrations and photographs, print bleedthrough, substandard margins, and improper alignment can adversely afreet reproduction. In the unlikely event that the author did not send UMI a complete manuscript and there are missing pages, these will be noted. Also, if unauthorized copyright material had to be removed, a note will indicate the deletion. Oversize materials (e.g., maps, drawings, charts) are reproduced by sectioning the original, beginning at the upper left-hand comer and continuing from left to right in equal sections with small overlaps. -
2-Properties of Organic Compnds
Experiment 2 – Properties of Organic Compounds Organic compounds are compounds based on carbon. They contain carbon and hydrogen, and can also contain other nonmetal elements such as oxygen, nitrogen, or halogen atoms. The properties of organic compounds are very different from the properties of inorganic compounds that you have been using up to this point. In this lab, you will explore some of the differences in the properties of organic vs. ionic substances. Most organic compounds are nonpolar and thus do not mix with polar molecules like water. Therefore organic substances, in general, are insoluble in water. However, they are soluble in nonpolar solvents. Most ionic substances, on the other hand, are soluble in water and insoluble in nonpolar solvents. Organic compounds can be gases, liquids, or solids at room temperature. Ionic compounds are all solids at room temperature with very high melting points. Organic compounds have relatively low melting points and boiling points. The reason for these differences lies in the type of attractive forces holding the particles next to each other in each case. Ionic compounds consist of a vast array of alternating positive and negatively charged ions. Ionic substances are held together by very strong electrostatic forces and there are no individual molecules present. In order to melt an ionic compound, the ions must be able to move around each other, so a huge amount of energy is needed to break these strong electrostatic forces and thus ionic compounds have very high melting points. Organic compounds, on the other hand, consist of individual molecules held together by covalent bonds. -
Chapter 3: the Chemical Basis for Life Lesson 2: Organic Compounds
Chapter 3: The Chemical Basis for Life Lesson 2: Organic Compounds We have already learned that water is the primary substance for life on Earth, but we will now explore the element found in most of the molecules from which living organisms are made. That element is carbon and it is found in all organic compounds. The picture above is a graphic depiction of the organic compounds: carbohydrates, proteins, lipids, and nucleic acids. These are all large complex molecules that have contributed to the great diversity of life on Earth. Lesson Objectives • Define and explain elements and compounds; the relationships from atom to molecule to macromolecule. • Explain why carbon is essential to life on Earth and uniquely suited to form biological macromolecules. • Describe and compare the structure and function of the four major types of organic compounds. Vocabulary • atom biochemical conversion biological macromolecule carbohydrate DNA (deoxyribonucleic acid) isomers lipids macromolecules molecule monomer nucleic acid organic molecule polymer protein 63 INTRODUCTION If you look at your hand, what do you see? Of course, you see skin, which consists of cells. But what are skin cells made of? Like all living cells, they are made of matter. In fact, all things are made of matter. Matter is anything that takes up space and has mass. Matter, in turn, is made up of chemical substances. In this lesson you will learn about the chemical substances that make up living things. CHEMICAL SUBSTANCES A chemical substance is matter that has a definite composition. It also has the same composition throughout. A chemical substance may be either an element or a compound. -
4 Organic Compounds
Name Class Date CHAPTER 3 Chemical Compounds SECTION 4 Organic Compounds National Science BEFORE YOU READ Education Standards After you read this section, you should be able to answer PS 1a, 1b, 1c these questions: • Why are there so many organic compounds? • What are the names and the properties of organic compounds? • What organic compounds are found in living things? How Does Carbon Form Compounds? Most of the chemical compounds that exist contain STUDY TIP carbon. These compounds are called organic compounds. Brainstorm With a partner, Organic compounds are compounds made of molecules write down the names of several of your favorite foods. in which carbon atoms are covalently bonded to other After you have read about atoms. the carbohydrates, lipids, and Every organic compound contains carbon. Carbon proteins, identify which of atoms have four outer electrons. This means that each these groups are in the foods. carbon atom can make four covalent bonds with other atoms. Most organic molecules have two or more carbon atoms linked to one another. READING CHECK The illustrations in the figure below are models of 1. Identify What do most organic molecules. These models are called structural organic molecules have in formulas. They show the order in which atoms in a mol- them? ecule are connected to one another. A line between two element symbols represents a covalent bond, or one pair of shared electrons. Models of Organic Molecules H H H C H H C H H H H C H H H H C H H C H C H H C C H H C C H H C H H C C H H C H H C H C H H H TAKE A LOOK H C H H H H C H H 2. -
Limited Indoor Air Quality Assessment Report Stamford Public Schools
Limited Indoor Air Quality Assessment Report February 24, 2020 Toquam Elementary School – Room 34 123 Ridgewood Avenue Stamford, Connecticut Stamford Public Schools Stamford, Connecticut February 27, 2020 Fuss & O’Neill, Inc. 56 Quarry Road Trumbull, CT 06611 Project No. 20140748.A10 February 27, 2020 Mr. Kevin McCarthy Facilities Manager Stamford Public Schools 888 Washington Blvd Stamford, CT 06901 RE: Limited Indoor Air Quality Assessment Toquam Elementary School – Room 34 123 Ridgewood Ave, Stamford, CT Fuss & O’Neill Project No. 20140748.A10 Dear Mr. McCarthy: Enclosed please find the report for the limited indoor air quality assessment conducted within Room 34 (Area of Concern) and surrounding non-affected areas at the Toquam Elementary School located at 123 Ridgewood Avenue, Stamford, Connecticut (the “Site”). The work was conducted for Stamford Public Schools (the “Client”). The services were performed on February 24, 2020 by a Fuss & O’Neill, Inc. in accordance with our email task authorization dated February 24, 2020. If you have any questions regarding the enclosed report, please do not hesitate to contact me at (203) 374-3748, extension 5574. Thank you for this opportunity to have served your environmental needs. Sincerely, 56 Quarry Road Trumbull, CT 06611 t 203.374.3748 Eduardo Miguel Marques 800.286.2469 Senior Environmental Analyst f 203.374.4391 www.fando.com EMM/kr California Enclosure Connecticut Maine Massachusetts New Hampshire Rhode Island Vermont F:\P2014\0748\A10\Deliverables\Report\JBB_LimitedIndoorAirQualityAssessment_20200227.docx Table of Contents Limited Indoor Air Quality Assessment Toquam Elementary School – Room 34 Stamford Public Schools 1 Introduction and Background .................................................................... 1 2 Building Description .................................................................................... -
One-Year Study of Polycyclic Aromatic Compounds at an Urban
One-year study of polycyclic aromatic compounds at an urban site in Grenoble (France): Seasonal variations, gas/particle partitioning and cancer risk estimation Sophie Tomaz, Pourya Shahpoury, Jean-Luc Jaffrezo, Gerhard Lammel, Emilie Perraudin, Eric Villenave, Alexandre Albinet To cite this version: Sophie Tomaz, Pourya Shahpoury, Jean-Luc Jaffrezo, Gerhard Lammel, Emilie Perraudin, et al.. One-year study of polycyclic aromatic compounds at an urban site in Grenoble (France): Seasonal variations, gas/particle partitioning and cancer risk estimation. Science of the Total Environment, Elsevier, 2016, 565, pp.1071-1083. 10.1016/j.scitotenv.2016.05.137. insu-01387781 HAL Id: insu-01387781 https://hal-insu.archives-ouvertes.fr/insu-01387781 Submitted on 25 Sep 2018 HAL is a multi-disciplinary open access L’archive ouverte pluridisciplinaire HAL, est archive for the deposit and dissemination of sci- destinée au dépôt et à la diffusion de documents entific research documents, whether they are pub- scientifiques de niveau recherche, publiés ou non, lished or not. The documents may come from émanant des établissements d’enseignement et de teaching and research institutions in France or recherche français ou étrangers, des laboratoires abroad, or from public or private research centers. publics ou privés. One-year study of polycyclic aromatic compounds at an urban site in Grenoble (France): seasonal variations, gas/particle partitioning and cancer risk estimation Sophie Tomaz a,b,c, Pourya Shahpoury d, Jean-Luc Jaffrezo f, Gerhard Lammel d,e,