Teaching the ARM Microcontroller to Keep up with the Embedded Industry Technology Change
Total Page:16
File Type:pdf, Size:1020Kb
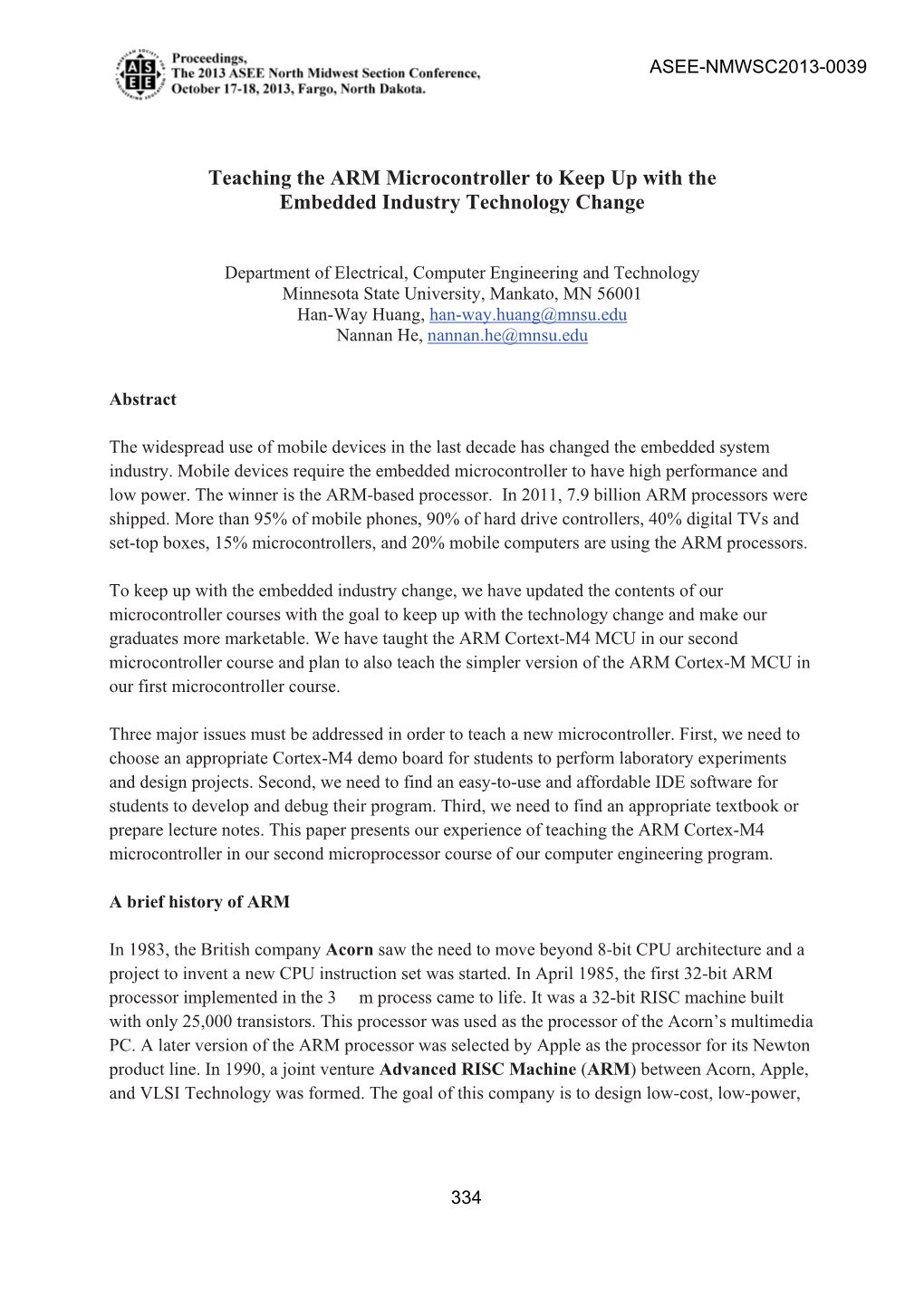
Load more
Recommended publications
-
Types and Programming Languages by Benjamin C
< Free Open Study > . .Types and Programming Languages by Benjamin C. Pierce ISBN:0262162091 The MIT Press © 2002 (623 pages) This thorough type-systems reference examines theory, pragmatics, implementation, and more Table of Contents Types and Programming Languages Preface Chapter 1 - Introduction Chapter 2 - Mathematical Preliminaries Part I - Untyped Systems Chapter 3 - Untyped Arithmetic Expressions Chapter 4 - An ML Implementation of Arithmetic Expressions Chapter 5 - The Untyped Lambda-Calculus Chapter 6 - Nameless Representation of Terms Chapter 7 - An ML Implementation of the Lambda-Calculus Part II - Simple Types Chapter 8 - Typed Arithmetic Expressions Chapter 9 - Simply Typed Lambda-Calculus Chapter 10 - An ML Implementation of Simple Types Chapter 11 - Simple Extensions Chapter 12 - Normalization Chapter 13 - References Chapter 14 - Exceptions Part III - Subtyping Chapter 15 - Subtyping Chapter 16 - Metatheory of Subtyping Chapter 17 - An ML Implementation of Subtyping Chapter 18 - Case Study: Imperative Objects Chapter 19 - Case Study: Featherweight Java Part IV - Recursive Types Chapter 20 - Recursive Types Chapter 21 - Metatheory of Recursive Types Part V - Polymorphism Chapter 22 - Type Reconstruction Chapter 23 - Universal Types Chapter 24 - Existential Types Chapter 25 - An ML Implementation of System F Chapter 26 - Bounded Quantification Chapter 27 - Case Study: Imperative Objects, Redux Chapter 28 - Metatheory of Bounded Quantification Part VI - Higher-Order Systems Chapter 29 - Type Operators and Kinding Chapter 30 - Higher-Order Polymorphism Chapter 31 - Higher-Order Subtyping Chapter 32 - Case Study: Purely Functional Objects Part VII - Appendices Appendix A - Solutions to Selected Exercises Appendix B - Notational Conventions References Index List of Figures < Free Open Study > < Free Open Study > Back Cover A type system is a syntactic method for automatically checking the absence of certain erroneous behaviors by classifying program phrases according to the kinds of values they compute. -
A High-Level Programming Language for Multimedia Streaming
Liquidsoap: a High-Level Programming Language for Multimedia Streaming David Baelde1, Romain Beauxis2, and Samuel Mimram3 1 University of Minnesota, USA 2 Department of Mathematics, Tulane University, USA 3 CEA LIST – LMeASI, France Abstract. Generating multimedia streams, such as in a netradio, is a task which is complex and difficult to adapt to every users’ needs. We introduce a novel approach in order to achieve it, based on a dedi- cated high-level functional programming language, called Liquidsoap, for generating, manipulating and broadcasting multimedia streams. Unlike traditional approaches, which are based on configuration files or static graphical interfaces, it also allows the user to build complex and highly customized systems. This language is based on a model for streams and contains operators and constructions, which make it adapted to the gen- eration of streams. The interpreter of the language also ensures many properties concerning the good execution of the stream generation. The widespread adoption of broadband internet in the last decades has changed a lot our way of producing and consuming information. Classical devices from the analog era, such as television or radio broadcasting devices have been rapidly adapted to the digital world in order to benefit from the new technologies available. While analog devices were mostly based on hardware implementations, their digital counterparts often consist in software implementations, which po- tentially offers much more flexibility and modularity in their design. However, there is still much progress to be done to unleash this potential in many ar- eas where software implementations remain pretty much as hard-wired as their digital counterparts. -
Managing Files with Sterling Connect:Direct File Agent 1.4.0.1
Managing Files with Sterling Connect:Direct File Agent 1.4.0.1 IBM Contents Managing Files with Sterling Connect:Direct File Agent.......................................... 1 Sterling Connect:Direct File Agent Overview.............................................................................................. 1 How to Run Sterling Connect:Direct File Agent.......................................................................................... 2 Sterling Connect:Direct File Agent Logging.................................................................................................3 Sterling Connect:Direct File Agent Configuration Planning........................................................................ 3 Sterling Connect:Direct File Agent Worksheet ...........................................................................................4 Considerations for a Large Number of Watch Directories.......................................................................... 6 Modifying MaxFileSize............................................................................................................................ 6 Modifying MaxBackupIndex...................................................................................................................6 Considerations for a Large Number of Files in a Watch Directory..............................................................7 Sterling Connect:Direct File Agent Configuration Scenarios...................................................................... 7 Scenario:Detecting -
Soft Machines Targets Ipcbottleneck
SOFT MACHINES TARGETS IPC BOTTLENECK New CPU Approach Boosts Performance Using Virtual Cores By Linley Gwennap (October 27, 2014) ................................................................................................................... Coming out of stealth mode at last week’s Linley Pro- president/CTO Mohammad Abdallah. Investors include cessor Conference, Soft Machines disclosed a new CPU AMD, GlobalFoundries, and Samsung as well as govern- technology that greatly improves performance on single- ment investment funds from Abu Dhabi (Mubdala), Russia threaded applications. The new VISC technology can con- (Rusnano and RVC), and Saudi Arabia (KACST and vert a single software thread into multiple virtual threads, Taqnia). Its board of directors is chaired by Global Foun- which it can then divide across multiple physical cores. dries CEO Sanjay Jha and includes legendary entrepreneur This conversion happens inside the processor hardware Gordon Campbell. and is thus invisible to the application and the software Soft Machines hopes to license the VISC technology developer. Although this capability may seem impossible, to other CPU-design companies, which could add it to Soft Machines has demonstrated its performance advan- their existing CPU cores. Because its fundamental benefit tage using a test chip that implements a VISC design. is better IPC, VISC could aid a range of applications from Without VISC, the only practical way to improve single-thread performance is to increase the parallelism Application (sequential code) (instructions per cycle, or IPC) of the CPU microarchi- Single Thread tecture. Taken to the extreme, this approach results in massive designs such as Intel’s Haswell and IBM’s Power8 OS and Hypervisor that deliver industry-leading performance but waste power Standard ISA and die area. -
The Sitcom | Arts & Entertainment in Spokane Valley, WA | Mainvest
3/18/2021 Invest in Selling Seattle- The Sitcom | Arts & Entertainment in Spokane Valley, WA | Mainvest ls dashboard | Print to text | View investment opportunities on Mainvest Edit Profile Watch this investment opportunity Share Selling Seattle- The Sitcom Arts & Entertainment 17220 E Mansfield Ave Spokane Valley, WA 99016 Get directions Coming Soon View Website Profile Data Room Discussion This is a preview. It will become public when you start accepting investment. THE PITCH Selling Seattle- The Sitcom is seeking investment to produce one or two episodes. Generating Revenue This is a preview. It will become public when you start accepting investment. Early Investor Bonus: The investment multiple is increased to 20 for the next $200,000 invested. This is a preview. It will become public when you start accepting investment. SELLING SEATTLE IS? Play 0000 0107 Mute Settings Enter fullscreen Play Who or What is Michael? This is a preview. It will become public when you start accepting investment. OUR STORY "Selling Seattle" is a smart broad comedy in the vein of "Seinfeld" and "Arrested Development". We are working with the video production company North by Northwest to produce the pilot and the second episode in Spokane, Washington this spring. We plan to stream episodes on the internet with commercials in a thirty-minute format. With cash flow from the pilot and second episode we will produce four to six episodes this fall and at least twelve episodes next year. The money raised through Mainvest will be used to produce the first one or two episodes of Selling Seattle and for advertising costs, office expenses and an income for Jim McGuffin not to exceed $15,000 per episode. -
Ugp-20G Of1 Classic Gas Range Installation and Owner's
CLASSIC GAS RANGE (LPG & NG convertible) INSTALLATION UGP-20G OF1 AND OWNER’S MANUAL 20” (50.8 cm) SERIAL NUMBER: READ AND SAVE THESE INSTRUCTIONS AUG17V2 UNIQUE 20G CLASSIC MODEL OFF GRID GAS RANGE – LPG & NG CONVERTIBLE Installation and Owner’s Manual This manual contains information for: • Important Safeguards • Installation • Use and Care Certain ranges come equipped with special features. Determine from a study of your range which of the instructions given in this booklet pertain to your range. This booklet gives valuable instructions covering the installation, adjustment and use of your range. How to Obtain Service and/or Parts When your range does not operate in accordance with the instructions in the manual, you should contact the dealer in your immediate vicinity for service. Or, the purchaser may contact the service organization noted on the warranty. Important TO THE OWNER OF THE RANGE: Retain this owner’s manual for future reference. TO THE INSTALLER: Leave this owner’s manual with the range. Read and Save These Instructions The installation of the appliance must conform with local codes ANSI Z21.1b-2012, in the absence of local national Fuel Gas Code, ANSI Z233.1, and in Canada B149.2 Propane Storage and Handling Code MANUFACTURED AND CERTIFIED BY Unique Gas Products Ltd A child or adult can tip WARNING the range and be killed. Install the anti-tip device to the structure and/or the range. Verify the anti-tip device has been properly installed and engaged. Engage the range to the anti-tip device by ensuring the anti-tip device is re-engaged when the range is moved. -
Itanium-Based Solutions by Hp
Itanium-based solutions by hp an overview of the Itanium™-based hp rx4610 server a white paper from hewlett-packard june 2001 table of contents table of contents 2 executive summary 3 why Itanium is the future of computing 3 rx4610 at a glance 3 rx4610 product specifications 4 rx4610 physical and environmental specifications 4 the rx4610 and the hp server lineup 5 rx4610 architecture 6 64-bit address space and memory capacity 6 I/O subsystem design 7 special features of the rx4610 server 8 multiple upgrade and migration paths for investment protection 8 high availability and manageability 8 advanced error detection, correction, and containment 8 baseboard management controller (BMC) 8 redundant, hot-swap power supplies 9 redundant, hot-swap cooling 9 hot-plug disk drives 9 hot-plug PCI I/O slots 9 internal removable media 10 system control panel 10 ASCII console for hp-ux 10 space-saving rack density 10 complementary design and packaging 10 how hp makes the Itanium transition easy 11 binary compatibility 11 hp-ux operating system 11 seamless transition—even for home-grown applications 12 transition help from hp 12 Itanium quick start service 12 partner technology access centers 12 upgrades and financial incentives 12 conclusion 13 for more information 13 appendix: Itanium advantages in your computing future 14 hp’s CPU roadmap 14 Itanium processor architecture 15 predication enhances parallelism 15 speculation minimizes the effect of memory latency 15 inherent scalability delivers easy expansion 16 what this means in a server 16 2 executive The Itanium™ Processor Family is the next great stride in computing--and it’s here today. -
Computer Architecture Out-Of-Order Execution
Computer Architecture Out-of-order Execution By Yoav Etsion With acknowledgement to Dan Tsafrir, Avi Mendelson, Lihu Rappoport, and Adi Yoaz 1 Computer Architecture 2013– Out-of-Order Execution The need for speed: Superscalar • Remember our goal: minimize CPU Time CPU Time = duration of clock cycle × CPI × IC • So far we have learned that in order to Minimize clock cycle ⇒ add more pipe stages Minimize CPI ⇒ utilize pipeline Minimize IC ⇒ change/improve the architecture • Why not make the pipeline deeper and deeper? Beyond some point, adding more pipe stages doesn’t help, because Control/data hazards increase, and become costlier • (Recall that in a pipelined CPU, CPI=1 only w/o hazards) • So what can we do next? Reduce the CPI by utilizing ILP (instruction level parallelism) We will need to duplicate HW for this purpose… 2 Computer Architecture 2013– Out-of-Order Execution A simple superscalar CPU • Duplicates the pipeline to accommodate ILP (IPC > 1) ILP=instruction-level parallelism • Note that duplicating HW in just one pipe stage doesn’t help e.g., when having 2 ALUs, the bottleneck moves to other stages IF ID EXE MEM WB • Conclusion: Getting IPC > 1 requires to fetch/decode/exe/retire >1 instruction per clock: IF ID EXE MEM WB 3 Computer Architecture 2013– Out-of-Order Execution Example: Pentium Processor • Pentium fetches & decodes 2 instructions per cycle • Before register file read, decide on pairing Can the two instructions be executed in parallel? (yes/no) u-pipe IF ID v-pipe • Pairing decision is based… On data -
Arduino and AVR
Arduino and AVR Ke vin J Dola n a nd Eric Te ve lson Agenda • History of Arduino • Comparison to Other Platforms • Arduino Uno - Hardware • ATmega328P Peripherals • Instruction Set • Processor Components • Pipe lining • Programming • Applica tions • Future of Arduino History of Arduino • Fa mily of Microcontrolle rs cre a te d a s a ma ste rs the sis proje ct • intended for use by a non-technical audience of artists, designers, etc. • Made for accessibility and ease of use. • Programming made easy for the audience • Ability to program board via USB • Inexpensive price point • Expanded for other types and configurations • Example: Arduino Lilypad for wearable technologies • Popularity has expanded functionality including “shields” and Bluetooth. Comparison to Other Platforms • Raspberry Pi • Raspberry Pi is a full computer that can run and support an OS, and has built in graphics. • Porta bility is a n issue , since a n e xte rna l supply is ne e de d. • Network needs more setup on an Arduino • Raspberry Pi does not support analog sensors as well • Teensy • Less expensive • Compatible with Arduino “sketches” and “shields” • Be tte r ADC sa mpling, sa me functiona lity, be tte r re solution • Sma lle r physica l boa rd size Arduino Uno - Hardware • ATmega328P Microcontroller • 3 2 KB Fla s h Me m o ry (2 KB S RAM, 1 KB EEP RO M) • 16 MH z C lo c k • 14 Digita l I/O Pins • 6 PWM Digita l I/O Pins • 6 Analog Input Pins • Up to 20mA DC Current per I/O Pin up to 300mA total across all pins • 50mA DC Current on 3.3V Pin Arduino Uno - Hardware ATmega328P Peripherals • Total of 6 accessible A/D Pins on Port C • 14 GPIO (7 Pins each from PORT B & D) • UART (Se ria l) • SPI Support • Watchdog timer to reset CPU Instruction Set • Harvard Architecture, which is non-von Neumann memory, but still a von Neumann architecture. -
Performance of a Computer (Chapter 4) Vishwani D
ELEC 5200-001/6200-001 Computer Architecture and Design Fall 2013 Performance of a Computer (Chapter 4) Vishwani D. Agrawal & Victor P. Nelson epartment of Electrical and Computer Engineering Auburn University, Auburn, AL 36849 ELEC 5200-001/6200-001 Performance Fall 2013 . Lecture 1 What is Performance? Response time: the time between the start and completion of a task. Throughput: the total amount of work done in a given time. Some performance measures: MIPS (million instructions per second). MFLOPS (million floating point operations per second), also GFLOPS, TFLOPS (1012), etc. SPEC (System Performance Evaluation Corporation) benchmarks. LINPACK benchmarks, floating point computing, used for supercomputers. Synthetic benchmarks. ELEC 5200-001/6200-001 Performance Fall 2013 . Lecture 2 Small and Large Numbers Small Large 10-3 milli m 103 kilo k 10-6 micro μ 106 mega M 10-9 nano n 109 giga G 10-12 pico p 1012 tera T 10-15 femto f 1015 peta P 10-18 atto 1018 exa 10-21 zepto 1021 zetta 10-24 yocto 1024 yotta ELEC 5200-001/6200-001 Performance Fall 2013 . Lecture 3 Computer Memory Size Number bits bytes 210 1,024 K Kb KB 220 1,048,576 M Mb MB 230 1,073,741,824 G Gb GB 240 1,099,511,627,776 T Tb TB ELEC 5200-001/6200-001 Performance Fall 2013 . Lecture 4 Units for Measuring Performance Time in seconds (s), microseconds (μs), nanoseconds (ns), or picoseconds (ps). Clock cycle Period of the hardware clock Example: one clock cycle means 1 nanosecond for a 1GHz clock frequency (or 1GHz clock rate) CPU time = (CPU clock cycles)/(clock rate) Cycles per instruction (CPI): average number of clock cycles used to execute a computer instruction. -
Chap01: Computer Abstractions and Technology
CHAPTER 1 Computer Abstractions and Technology 1.1 Introduction 3 1.2 Eight Great Ideas in Computer Architecture 11 1.3 Below Your Program 13 1.4 Under the Covers 16 1.5 Technologies for Building Processors and Memory 24 1.6 Performance 28 1.7 The Power Wall 40 1.8 The Sea Change: The Switch from Uniprocessors to Multiprocessors 43 1.9 Real Stuff: Benchmarking the Intel Core i7 46 1.10 Fallacies and Pitfalls 49 1.11 Concluding Remarks 52 1.12 Historical Perspective and Further Reading 54 1.13 Exercises 54 CMPS290 Class Notes (Chap01) Page 1 / 24 by Kuo-pao Yang 1.1 Introduction 3 Modern computer technology requires professionals of every computing specialty to understand both hardware and software. Classes of Computing Applications and Their Characteristics Personal computers o A computer designed for use by an individual, usually incorporating a graphics display, a keyboard, and a mouse. o Personal computers emphasize delivery of good performance to single users at low cost and usually execute third-party software. o This class of computing drove the evolution of many computing technologies, which is only about 35 years old! Server computers o A computer used for running larger programs for multiple users, often simultaneously, and typically accessed only via a network. o Servers are built from the same basic technology as desktop computers, but provide for greater computing, storage, and input/output capacity. Supercomputers o A class of computers with the highest performance and cost o Supercomputers consist of tens of thousands of processors and many terabytes of memory, and cost tens to hundreds of millions of dollars. -
CPU) the CPU Is the Brains of the Computer, and Is Also Known As the Processor (A Single Chip Also Known As Microprocessor)
Central processing unit (CPU) The CPU is the brains of the computer, and is also known as the processor (a single chip also known as microprocessor). This electronic component interprets and carries out the basic instructions that operate the computer. Cache as a rule holds data waiting to be processed and instructions waiting to be executed. The main parts of the CPU are: control unit arithmetic logic unit (ALU), and registers – also referred as Cache registers The CPU is connected to a circuit board called the motherboard also known as the system board. Click here to see more information on the CPU Let’s look inside the CPU and see what the different components actually do and how they interact Control unit The control unit directs and co-ordinates most of the operations in the computer. It is a bit similar to a traffic officer controlling traffic! It translates instructions received from a program/application and then begins the appropriate action to carry out the instruction. Specifically the control unit: controls how and when input devices send data stores and retrieves data to and from specific locations in memory decodes and executes instructions sends data to other parts of the CPU during operations sends data to output devices on request Arithmetic Logic Unit (ALU): The ALU is the computer’s calculator. It handles all math operations such as: add subtract multiply divide logical decisions - true or false, and/or, greater then, equal to, or less than Registers Registers are special temporary storage areas on the CPU. They are: used to store items during arithmetic, logic or transfer operations.