Raks). ATTORNEYS June 30, 1964 E
Total Page:16
File Type:pdf, Size:1020Kb
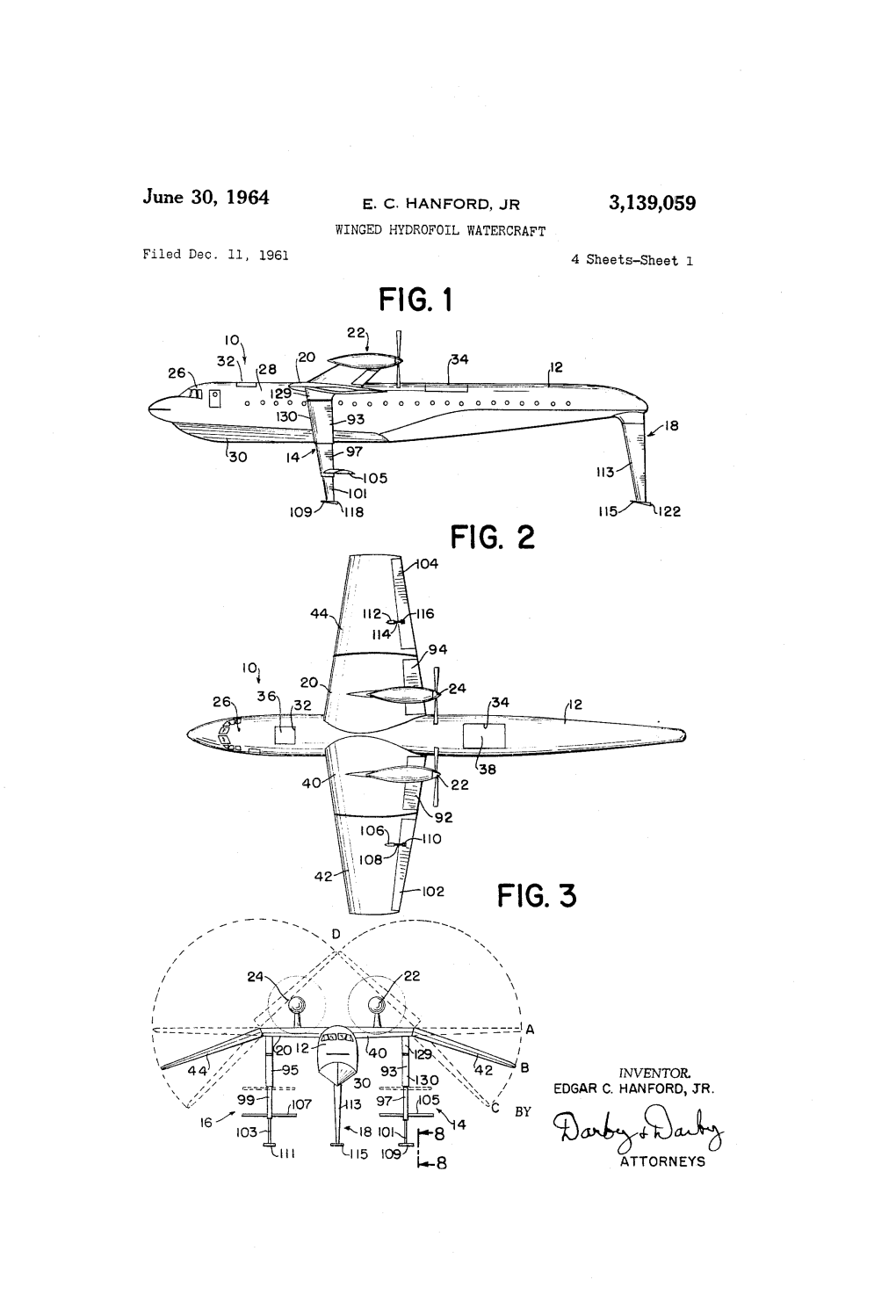
Load more
Recommended publications
-
The Stepped Hull Hybrid Hydrofoil
The Stepped Hull Hybrid Hydrofoil Christopher D. Barry, Bryan Duffty Planing @brid hydrofoils or partially hydrofoil supported planing boat are hydrofoils that intentionally operate in what would be the takeoff condition for a norma[ hydrofoil. They ofler a compromise ofperformance and cost that might be appropriate for ferq missions. The stepped hybrid configuration has made appearances in the high speed boat scene as early as 1938. It is a solution to the problems of instability and inefficiency that has limited other type of hybrids. It can be configured to have good seakeeping as well, but the concept has not been used as widely as would be justified by its merits. The purpose of this paper is to reintroduce this concept to the marine community, particularly for small, fast ferries. We have performed analytic studies, simple model experiments and manned experiments, andfiom them have determined some specljic problems and issues for the practical implementation of this concept. This paper presents background information, discusses key concepts including resistance, stability, seakeeping, and propulsion and suggests solutions to what we believe are the problems that have limited the widespread acceptance of this concept. Finally we propose a “strawman” design for a ferry in a particular service using this technology. BACKGROUND Partially hydrofoil supported planing hulls mix hydrofoil support and planing lift. The most obvious A hybrid hydrofoil is a vehicle combining the version of this concept is a planing hull with a dynamic lift of hydrofoils with a significant amount of hydrofoil more or less under the center of gravity. lit? tiom some other source, generally either buoyancy Karafiath (1974) studied this concept and ran model or planing lift. -
Human Powered Hydrofoil Design & Analytic Wing Optimization
Human Powered Hydrofoil Design & Analytic Wing Optimization Andy Gunkler and Dr. C. Mark Archibald Grove City College Grove City, PA 16127 Email: [email protected] Abstract – Human powered hydrofoil watercraft can have marked performance advantages over displacement-hull craft, but pose significant engineering challenges. The focus of this hydrofoil independent research project was two-fold. First of all, a general vehicle configuration was developed. Secondly, a thorough optimization process was developed for designing lifting foils that are highly efficient over a wide range of speeds. Given a well-defined set of design specifications, such as vehicle weight and desired top speed, an optimal horizontal, non-surface- piercing wing can be engineered. Design variables include foil span, area, planform shape, and airfoil cross section. The optimization begins with analytical expressions of hydrodynamic characteristics such as lift, profile drag, induced drag, surface wave drag, and interference drag. Research of optimization processes developed in the past illuminated instances in which coefficients of lift and drag were assumed to be constant. These shortcuts, made presumably for the sake of simplicity, lead to grossly erroneous regions of calculated drag. The optimization process developed for this study more accurately computes profile drag forces by making use of a variable coefficient of drag which, was found to be a function of the characteristic Reynolds number, required coefficient of lift, and airfoil section. At the desired cruising speed, total drag is minimized while lift is maximized. Next, a strength and rigidity analysis of the foil eliminates designs for which the hydrodynamic parameters produce structurally unsound wings. Incorporating constraints on minimum takeoff speed and power required to stay foil-borne isolates a set of optimized design parameters. -
2008 Fact Book
2008 PUBLIC TRANSPORTATION FACT BOOK 59th Edition June 2008 PUBLISHED BY American Public Transportation Association American Public Transportation Association 1666 K Street, N.W., Suite 1100 Washington, DC 20006 TELEPHONE: (202) 496-4800 EMAIL: [email protected] WEBSITE: www.apta.com APTA’s Vision Statement Be the leading force in advancing public transportation. APTA’s Mission Statement APTA serves and leads its diverse membership through advocacy, innovation, and information sharing to strengthen and expand public transportation. APTA’s Policy on Diversity APTA recognizes the importance of diversity for conference topics and speakers and is committed to increasing the awareness of its membership on diversity issues. APTA welcomes ideas and suggestions on how to strengthen its efforts to meet these important diversity objectives. Prepared by John Neff, Senior Policy Researcher [email protected] (202) 496-4812 PUBLIC TRANSPORTATION FACT BOOK American Public Transportation Association Washington, DC June 2008 Material from 2008 Public Transportation Fact Book may be quoted or reproduced without obtaining the permission of the American Public Transportation Association. Suggested Identification: American Public Transportation Association: Public Transportation Fact Book, Washington, DC, June, 2008. TABLE OF CONTENTS Table of Contents 28. Fossil Fuel Consumption by Mode…………….. 31 29. Non-diesel Fossil Fuel Consumption by Fuel… 31 INTRODUCTION 30. Bus Power Sources…....................................... 31 31. Bus Fossil Fuel Consumption…………………... 32 PUBLIC TRANSPORTATION OVERVIEW…………… 7 32. Paratransit Fuel Consumption………………….. 32 33. Rail Vehicle Fuel and Power Consumption….… 32 NATIONAL SUMMARY………………………….....…… 15 SAFETY………………………...............………..........… 33 1. Number of Public Transportation Service Providers by Mode……………………………… 15 34. Fatality Rates by Mode of Travel, 2001-2003… 33 2. -
Getting to Orsa Maggiore Hotel Orsa Maggiore Is Located in Anacapri, the Highest and Most Peaceful Area of the Island of Capri
How to get to Hotel Orsa Maggiore Getting to Orsa Maggiore Hotel Orsa Maggiore is located in Anacapri, the highest and most peaceful area of the island of Capri. We provide a free shuttle service on arrival and departure , from the port to the hotel and vice versa. Navigational companies: Call us a couple of hours before you are scheduled to arrive on the island, letting us know which ferry or Roma Aliscafi SNAV +39 081 8377577 hydrofoil you are going to take: you’ll find our driver waiting for you at the port. ORSA MAGGIORE Caremar Spa +39 081 8370700 NLG Navigazione Libera del Golfo +39 081 8370819 Phone: +39 081 8373351 Port Authority +39 081 8370226 Capri’s port is a small one and it's not always possible to park vehicles near to the landing docks. When Tourist Information Offices the port is busy, we ask guests to wait for the driver next to the Funicular railway ticket office. +39 081 8370686 Our shuttle service is available from 09.00 until 20.30. Should you decide to arrive or leave early in the Napoli morning or late in the evening, you will need to take a taxi or the bus (Marina Grande-Anacapri). Sorrento Positano Capri Hydrofoils and ferries to Capri depart from Naples and Sorrento. How long will the journey take? In the summer months, sea crossings are also From Rome airport: minimum 3 hours available from Positano, Amalfi, Salerno and (traveling by fast train and without missing a the island of Ischia. single connection) Times of crossings are subject to variation and From Naples airport: 90mins it’s always a good idea to check the hydrofoil From Sorrento: 30mins and ferry schedule before you travel to the port. -
Planning and Operational Analyses for a New Intercity Transit Service
Planning and Operational Analyses for A New Intercity Transit Service Item Type text; Electronic Dissertation Authors Ranjbari, Andisheh Publisher The University of Arizona. Rights Copyright © is held by the author. Digital access to this material is made possible by the University Libraries, University of Arizona. Further transmission, reproduction, presentation (such as public display or performance) of protected items is prohibited except with permission of the author. Download date 25/09/2021 07:58:17 Link to Item http://hdl.handle.net/10150/630234 PLANNING AND OPERATIONAL ANALYSES FOR A NEW INTERCITY TRANSIT SERVICE By ANDISHEH RANJBARI ________________________ Copyright © Andisheh Ranjbari 2018 A Dissertation Submitted to the Faculty of the DEPARTMENT OF CIVIL ENGINEERING AND ENGINEERING MECHANICS In Partial Fulfillment of the Requirements for the Degree of DOCTOR OF PHILOSOPHY In the Graduate College THE UNIVERSITY OF ARIZONA 2018 THE LTNIVERSITY OF ARIZONA GRADUATE COLLEGE As members of the Dissertation Commiuee, we certifu that we have read the dissertation prepared by Andisheh Ranjbari, titled Planning and Operation Analyses for A New Intercity Transit Service and recommend that it be accepted as fulfilling the dissertation requirement for the Degree of Doctor of Philosophy. Date: May 3,2418 Date: May 3,2018 Mark D. Hickman Date: May 3,2018 Neng Fan Date: May 3,2018 Final approval and acceptance of this dissertation is contingent upon the candidate's submission of the final copies of the dissertation to the Graduate College. I hereby certiff that I have read this dissertation prepared under my direction and recommend that it be accepted as fulfilling the dissertation requirement. -
Course Objectives Chapter 2 2. Hull Form and Geometry
COURSE OBJECTIVES CHAPTER 2 2. HULL FORM AND GEOMETRY 1. Be familiar with ship classifications 2. Explain the difference between aerostatic, hydrostatic, and hydrodynamic support 3. Be familiar with the following types of marine vehicles: displacement ships, catamarans, planing vessels, hydrofoil, hovercraft, SWATH, and submarines 4. Learn Archimedes’ Principle in qualitative and mathematical form 5. Calculate problems using Archimedes’ Principle 6. Read, interpret, and relate the Body Plan, Half-Breadth Plan, and Sheer Plan and identify the lines for each plan 7. Relate the information in a ship's lines plan to a Table of Offsets 8. Be familiar with the following hull form terminology: a. After Perpendicular (AP), Forward Perpendiculars (FP), and midships, b. Length Between Perpendiculars (LPP or LBP) and Length Overall (LOA) c. Keel (K), Depth (D), Draft (T), Mean Draft (Tm), Freeboard and Beam (B) d. Flare, Tumble home and Camber e. Centerline, Baseline and Offset 9. Define and compare the relationship between “centroid” and “center of mass” 10. State the significance and physical location of the center of buoyancy (B) and center of flotation (F); locate these points using LCB, VCB, TCB, TCF, and LCF st 11. Use Simpson’s 1 Rule to calculate the following (given a Table of Offsets): a. Waterplane Area (Awp or WPA) b. Sectional Area (Asect) c. Submerged Volume (∇S) d. Longitudinal Center of Flotation (LCF) 12. Read and use a ship's Curves of Form to find hydrostatic properties and be knowledgeable about each of the properties on the Curves of Form 13. Calculate trim given Taft and Tfwd and understand its physical meaning i 2.1 Introduction to Ships and Naval Engineering Ships are the single most expensive product a nation produces for defense, commerce, research, or nearly any other function. -
How to Get to Capri Town How to Get to Capri Town Upon Arrival at the Marina Grande Port, Take the Funicular to the Center of Capri (A Four Minute Ride)
How to get to Capri Town How to Get to Capri Town Upon arrival at the Marina Grande port, take the funicular to the center of Capri (a four minute ride). Once you have exited the funicular, instead of climbing the stairs to the scenic terrace, pass through the Navigational companies: gate on the left. You will find yourself in a narrow lane; walk down a few meters and Capri Town is on the Aliscafi SNAV +39 081 8377577 right. Caremar Spa +39 081 8370700 NLG Navigazione Libera del Golfo Roma +39 081 8370819 To transport baggage on the funicular, you must buy a supplementary ticket for €1.80 per piece. Port Authority +39 081 8370226 If you choose to take a taxi to get here, keep in mind that the car can't reach directly the door of Capri Town, since it is situated in a pedestrian area. Ask the driver to leave you in Piazzetta (and not at the beginning of Tourist Information Offices Via Acquaviva). From here follow the stairs that go down between Piccolo Bar and Bar Caso. In this way you +39 081 8370686 have to walk only a short downhill section. Napoli Sorrento Positano Capri Hydrofoils and ferries to Capri depart from Naples and Sorrento. In the summer months, How long will the journey take? sea crossings are also available from From Rome airport: minimum 3 hours Positano, Amalfi, Salerno and the island of (traveling by fast train and without missing a Ischia. Times of crossings are subject to variation and it’s always a good idea to check single connection) the hydrofoil and ferry schedule before you From Naples airport: 90mins travel to the port. -
2019 NTD Policy Manual for Reduced Reporters
Office of Budget and Policy National Transit Database 2019 Policy Manual REDUCED REPORTING 2019 NTD Reduced Reporter Policy Manual TABLE OF CONTENTS List of Exhibits .............................................................................................................. v Acronyms and Abbreviations .................................................................................... vii Report Year 2019 Policy Changes and Reporting Clarifications .............................. 1 Introduction ................................................................................................................... 6 The National Transit Database ................................................................................... 7 History .................................................................................................................... 7 NTD Data ................................................................................................................ 8 Data Use and Funding .......................................................................................... 11 Failure to Report ................................................................................................... 14 Inaccurate Data .................................................................................................... 15 Standardized Reporting Requirements ..................................................................... 15 Reporting Due Dates ........................................................................................... -
Transport Systems: European Examples and Decisions About Odessa
ISSN: 2521-6384 (Online), ISSN: 2521-103X (Print) №4(10), 2019 Economic journal Odessa polytechnic university DOI: 10.5281/zenodo.3835708 UDC: 338.242.2:640.4 JEL: G18, L92 TRANSPORT SYSTEMS: EUROPEAN EXAMPLES AND DECISIONS ABOUT ODESSA МІСЬКІ ТРАНСПОРТНІ СИСТЕМИ: ЄВРОПЕЙСЬКІ ПРИКЛАДИ ТА РІШЕННЯ ЩОДО ОДЕСИ Olena А. Lypynska, Doctor of Economics, Professor Odessa National Polytechnic University, Odessa, Ukraine Oleksii М. Kotlubai, Doctor of Economics, Professor Institute of Market Problems and Economic& Ecological Research, Odessa, Ukraine ORCID: 0000-0002-6317-7511 Received 29.11.19 Липинська О.А., Котлубай О.М, Міські транспортні системи: європейські приклади та рішення щодо Одеси. Науково- методична стаття. У статті розглядаються основні форми та Концепції організації міського транспортного повідомлень. Виявлені стратегічні та практичні проблеми, пов'язані з організацією міського сполучення, виявлені основні проблеми, пов'язані з цим. Представлені принципи на основі яких має бути організованого рух міського транспорту приморського міста. Розглянуто варіанти організації міського сполучення, в різних містах світу, таких як Лондона, Ліона, Квінсленда, Сан Пауло, а так само Санкт-Петербурга. Наведені приклади організації взаємодії різних видів міського транспорту, а так само можливості застосування їх в Україні. Представлені, розроблені авторами напрямки і етапи організації міського транспортного руху в місті Одесі. Ключові слова: міські транспортні системи, принципи організації руху транспорту, міський транспорт, організація перевезень в місті Lypynska O.А., Kotlubai O.М. Urban transport systems: European examples and decisions about Odessa. Scientific and methodical article. The article deals with the main forms and Concepts of organization of urban transport systems. The identified strategic and practical problems associated with the organization of urban communication revealed the main problems associated with this. -
Hydrofoils and Chesapeake Bay Ferries
International Hydrofoil Society 11 March 2010 Mark Rice, P.E. & Jeanne Torstenson, P.E. Hydrofoils and Chesapeake Bay Ferries Graphic from Google Earth Graphic from Woods Hole Oceanographic Institution Chesapeake Bay Growth Since 1986 Outline Early Ferry Transportation & Transition to Bridges John Smith Historic Waterway Trail Transportation Changes? Hydrofoil Ferries for Chesapeake Bay Technology Options for Reducing Hydrofoil Energy Consumption BALTIMORE ROCK HALL ANNAPOLI KENT ISLAND S SHADY SIDE ST. MICHAELS CAMBRIDGE SOLOMONS/ LEXINGTON PARK CRISFIELD REEDVILLE ONANCOC K CAPE CHARLES WILLIAMSBUR YORKTOWN G HAMPTON VA BEACH NORFOLK Common 19th & 20th Century Ferry Routes 1640 - 1952 Slower pace No bridges Lots of Time No other choice Alternative routes were very long 19th Century Chesapeake Bay excursion steamboat the Emma Giles, circa 1890 1829: The Washington, Alexandria, and Baltimore Steam-packet Company was succeeded by the Washington, Alexandria and Georgetown Steam –packet Company 1840: Baltimore Steam Packet Company is founded. Early 20th Century Love Point Resort Steamer Westmoreland at Love Point - 1910 - two dollars for the car and driver - $0.50 per passenger Baltimore 1912 Early 20th Century Steamboat Louise Steamer Nellie White Early 20th Century Steamer Routes • Tolchester – Baltimore • Baltimore – Love Point • Annapolis – St Michaels • Annapolis – Matapeake - Claiborne Baltimore Harbor 1935 1930s Steamers Luxury Steamer President Warfield – Built for Chesapeake Bay Converted to a Troop Ship in WW II – Survived a torpedo attack Purchased as scrap – Renamed EXODUS Covertly Carried 4,554 Illegal Jewish Emigrants to Palestine in 1947 1928 - 1964 316’ M.V. North Hampton – 1948-1964 339’ S.S. Delmarva – 1933-1964 339’ S.S. Virginia Lee – 1928-1964 291’ S.S. -
Aerospace Micro-Lesson
AIAA AEROSPACE M ICRO-LESSON Easily digestible Aerospace Principles revealed for K-12 Students and Educators. These lessons will be sent on a bi-weekly basis and allow grade-level focused learning. - AIAA STEM K-12 Committee. HOVERCRAFT, HYDROFOILS, AND ORNITHOPTERS When one thinks of flying vehicles, one thinks usually of airplanes, helicopters, and balloons. But there are other types of vehicle that fly. A hovercraft flies on a cushion of higher-pressure air underneath it. A hydrofoil does fly on wings, but the wings are embedded in water rather than in air. A third type of flying machine, an ornithopter, is more like a conventional airplane but its wings flap, providing propulsion as well as lift. This lesson explores these unusual flying machines. Next Generation Science Standards (NGSS): ● Discipline: Engineering Design ● Crosscutting Concept: Structure and Function ● Science & Engineering Practice: Asking Questions and Defining Problems GRADES K-2 K-2-ETS1-2. Develop a simple sketch, drawing, or physical model to illustrate how the shape of an object helps it function as needed to solve a given problem. A hovercraft is an unusual type of flying machine. It is a type of amphibious vehicle, meaning that it can travel on both land and water, but it is actually a flying machine because it travels on a cushion of air above the land or water. The idea for an air-cushion vehicle was first thought of by Sir Christopher Cockerell in 1955. He built a working model, improved upon it, and by 1959 the machine worked well enough that it could cross the English Channel between England and France. -
Last Mile Package Delivery Via Rural Transit: Project Summary and Pilot Outcomes
TTI: 0-6891 Last Mile Package Delivery via Rural Transit: Project Summary and Pilot Outcomes Technical Report 0-6891-R1 Cooperative Research Program TEXAS A&M TRANSPORTATION INSTITUTE COLLEGE STATION, TEXAS in cooperation with the Federal Highway Administration and the Texas Department of Transportation http://tti.tamu.edu/documents/0-6891-R1.pdf Technical Report Documentation Page 1. Report No. 2. Government Accession No. 3. Recipient's Catalog No. FHWA/TX-17/0-6891-R1 4. Title and Subtitle 5. Report Date LAST MILE PACKAGE DELIVERY VIA RURAL TRANSIT: Published: January 2019 PROJECT SUMMARY AND PILOT OUTCOMES 6. Performing Organization Code 7. Author(s) 8. Performing Organization Report No. Zachary Elgart, Kristi Miller, and Shuman Tan Report 0-6891-R1 9. Performing Organization Name and Address 10. Work Unit No. (TRAIS) Texas A&M Transportation Institute The Texas A&M University System 11. Contract or Grant No. College Station, Texas 77843-3135 Project 0-6891 12. Sponsoring Agency Name and Address 13. Type of Report and Period Covered Texas Department of Transportation Technical Report: Research and Technology Implementation Office September 2015–August 2017 125 E. 11th Street 14. Sponsoring Agency Code Austin, Texas 78701-2483 15. Supplementary Notes Project performed in cooperation with the Texas Department of Transportation and the Federal Highway Administration. Project Title: Using Public Transportation to Facilitate Last Mile Package Delivery URL: http://tti.tamu.edu/documents/0-6891-R1.pdf 16. Abstract Rural transit districts and intercity bus carriers are an important link within Texas’ multimodal transportation system. Without such service providers, many rural residents that are transit dependent would be forced to either relocate or find other means of transportation.