(12) Patent Application Publication (10) Pub. No.: US 2009/0137191A1 3
Total Page:16
File Type:pdf, Size:1020Kb
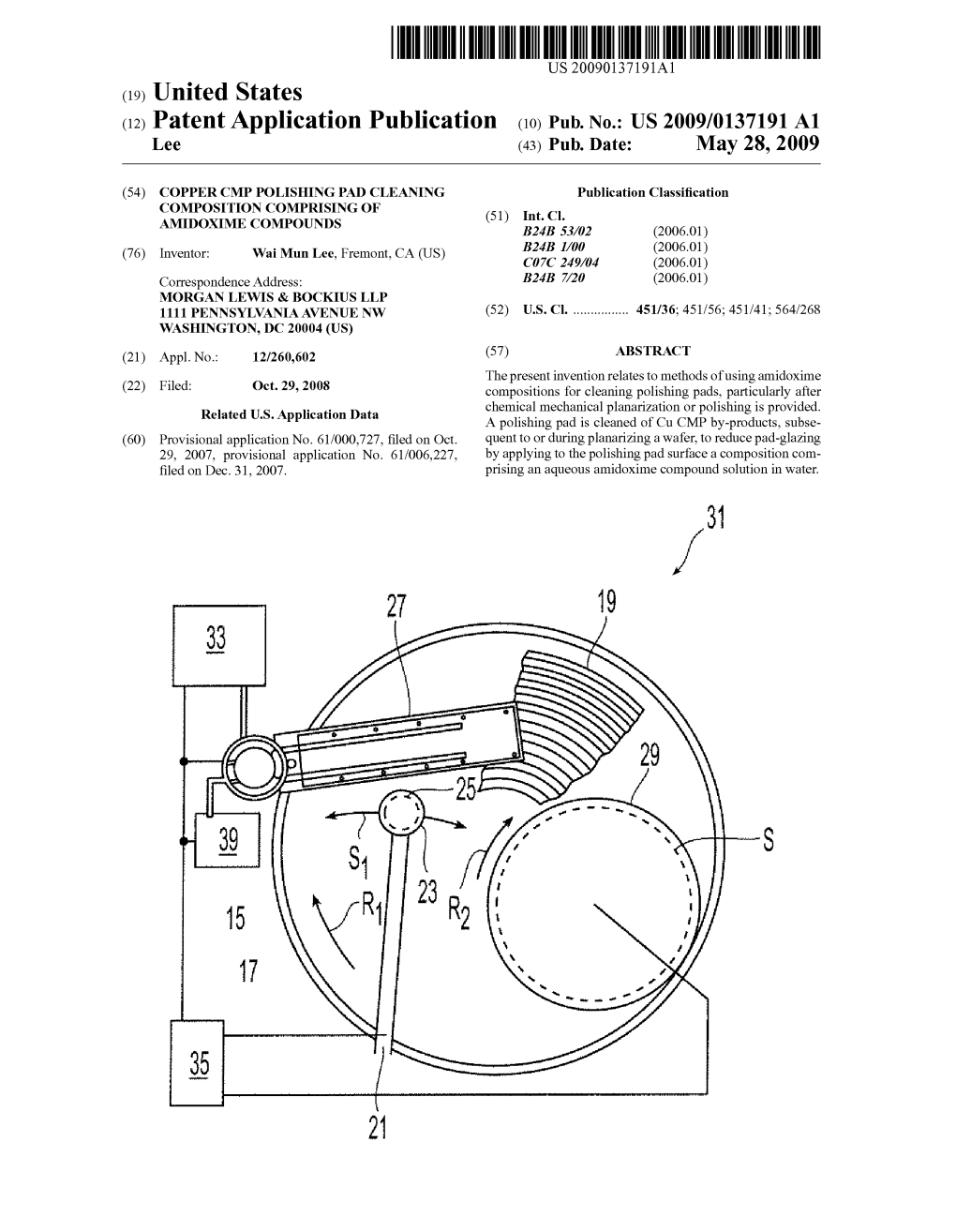
Load more
Recommended publications
-
United States Patent ‘ Patented Mar
r 2,786,869 United States Patent ‘ Patented Mar. 26, 1957 l 2 tically, mixtures of tert-alkylamine such as are available on the market. Typical mixtures are those containing ‘ 2,786,869 C12H25NH2 to C15H31NH2 or C18H3'INH2 to C24H49NH2 N-TRIALKYLCARBINYL-N-(HYDROXYETHYL or C15H31- to C24H49NH2. These may be represented by POLYOXYETHYL) GLYCINES the formula Peter L. de Benneville and Homer J. Sims, Philadelphia, 31 Pa., assignors to Rohrn & Haas Company, Philadelphia, R’-—-C—NH2 Pa., a corporation of Delaware Rs No Drawing. Application June 16, 1954, 10 As catalysts in the ?rst step of the process of this Serial No. 437,273 invention, wherein the hydroxyethyl group is introduced, 9 Claims.‘ (or. 260-534) there may be used any of the strong acids, such as hy drochloric, hydrobromic, sulfuric, arylsulfonic, alkanesul fonic, or phosphoric. The preferred amount of this cat This invention relatesto-compounds of the structure 15 alyst is 10 to 30 mole percent of the amine. With R1 '(CH2CH2O),.H ‘ , amines from 12 carbon atoms upward it is exceedingly di?icult to introduce more than one hydroxyethyl group in a tert-alkylamine molecule. Such amines‘yicld ?nal 3 \CHrCOOH products which have the desired balance of properties. ' wherein R1, R2, and R3 are alkyl groups containing a 20 The ?rst reaction with ethylene oxide is effected by total of 11 to 23 carbon atoms and n is an integer having bringing together ethylene oxide and tert-alkylamine, a value from 5 to about 50 or more, preferably 5 to 25. usually by passing ethylene oxide into amine and catalyst, These compounds may be called N-(trialkylcarbinyl)-N at temperatures from 0° to 180° C. -
Hydroxyacetonitrile (HOCH2CN) As a Precursor for Formylcyanide (CHOCN), Ketenimine (CH2CNH), and Cyanogen (NCCN) in Astrophysical Conditions
A&A 549, A93 (2013) Astronomy DOI: 10.1051/0004-6361/201219779 & c ESO 2013 Astrophysics Hydroxyacetonitrile (HOCH2CN) as a precursor for formylcyanide (CHOCN), ketenimine (CH2CNH), and cyanogen (NCCN) in astrophysical conditions G. Danger1, F. Duvernay1, P. Theulé1, F. Borget1, J.-C. Guillemin2, and T. Chiavassa1 1 Aix-Marseille Univ, CNRS, PIIM UMR 7345, 13397 Marseille, France e-mail: [email protected] 2 Institut des Sciences Chimiques de Rennes, École Nationale Supérieure de Chimie de Rennes, CNRS, UMR 6226, Avenue du Général Leclerc, CS 50837, 35708 Rennes Cedex 7, France Received 8 June 2012 / Accepted 19 November 2012 ABSTRACT Context. The reactivity in astrophysical environments can be investigated in the laboratory through experimental simulations, which provide understanding of the formation of specific molecules detected in the solid phase or in the gas phase of these environments. In this context, the most complex molecules are generally suggested to form at the surface of interstellar grains and to be released into the gas phase through thermal or non-thermal desorption, where they can be detected through rotational spectroscopy. Here, we focus our experiments on the photochemistry of hydroxyacetonitrile (HOCH2CN), whose formation has been shown to compete with aminomethanol (NH2CH2OH), a glycine precursor, through the Strecker synthesis. Aims. We present the first experimental investigation of the ultraviolet (UV) photochemistry of hydroxyacetonitrile (HOCH2CN) as a pure solid or diluted in water ice. Methods. We used Fourier transform infrared (FT-IR) spectroscopy to characterize photoproducts of hydroxyacetonitrile (HOCH2CN) and to determine the different photodegradation pathways of this compound. To improve the photoproduct identifications, irradiations of hydroxyacetonitrile 14N and 15N isotopologues were performed, coupled with theoretical calculations. -
United States Patent Office Patented Jan
2,700,668 United States Patent Office Patented Jan. 25, 1955 1. 2 Glycolonitrile, as is known, is readily prepared by re acting formaldehyde and hydrogen cyanide. Cf. Prepa 2,700,668 ration of Formaldehyde Cyanohydrin, p. 168 in "Prepara PREPARATION OF KETOPPERAZINES tion of Organic Intermediates' by Shirley, John Wiley & 5 Sons, New York, 1951. See also, p. 176 of "Chemistry James S. Strong and W. E. Craig, Philadelphia, and Vin of Organic Cyanogen Compounds,” Migridichian, 1947 cent T. Elkind, Roslyn, Pa., assignors to Rohm & Haas ed. Glycolonitrile may also be prepared in the reaction Company, Philadelphia, Pa., a corporation of Delaware mixture as described in the next example wherein form No Drawing. Application February 8, 1952, aldehyde and hydrogen cyanide are reacted in the pres Serial No. 270,761 O ence of an amine catalyst. 7 Claims. (C. 260-268) Example 2 To 83 parts of a 36.3% aqueous formaldehyde solution there were added a trace of piperidine to serve as catalyst This invention concerns a method for preparing keto 5 and 27 parts of hydrogen cyanide. During addition of piperazines having the formula the hydrogen cyanide the temperature was kept between N. R. 27 and 30° C. by cooling. After the cyanide had been added, the temperature of the mixture was allowed to, cá, Yo4R, rise to 50° C. The mixture was allowed to stand for bH, d-o 20 3.5 hours. This solution was then slowly added to 78 N parts of 76.7% ethylenediamine in water, which was stirred and held at 100° C. -
Lllllllllliillilllllllllllliihiillllllllllllllllllllllllll
llllllllllIIllIllllllllllllIIHIIllllllllllllllllllllllllllllllllllllllllll . US005208363A United States Patent [19] [11] Patent Number: 5,208,363 Crump et al. [45] Date of Patent: May 4, 1993 [54] PREPARATION OF AMINONITRILES 3,907,858 9/1975 Davis et a1. ....................... .. 558/346 3,925,448 12/1975 Tanier ................... .. 558/346 [75] Inv9nt9r$= B11199 K- Crumm Lake Jackson; 3,959,342 5/1976 Homberg et a1. ......... .. 558/346 Band A. W1lson, R1chwood, both of 3,988,360 10/1976 Gaudette et a1. .. 558/346 Tex. 4,022,815 5/1977 Schlecht 61 a1. 558/346 . 4,478,759 10/1984 Diatler C181. .. .558/346 [73] Asslgnee‘ “F D" @e'mcal Cmnpmy, 4,560,516 12/1985 Singer .......... ..' 558/346 M1d1and,M1¢h- 4,661,614 4/1987 M08161 61. .. 558/346 . 4,704,465 11/1987 Tannet et 111. ........ .. 558/346 [21] Appl' N°" 878’572 4,980,471 12/1990 Christiansen e181 ............ .. 544/384 [ 221 Fil e d: M “y 5’ 1992 OTHER PUBLICATIONS Related US. Application Data Stewart, et 81., J. Chem. Soc., pp. 3281-3285, (1940), [ 63 1 553333,?". _.Ma" _ “S” _ N° _ 597 , 625 , 0°‘ _ 15 , 199°’ V01.ChOh-HQO 62. Li, et aL, J. Chem. Soc., pp. 2596-2599, (1937), V01. 59. Céi5 .......................................... .. C07C5§33é2 Stewart, et 31“ J_ chem Soc” pp_ 27824737, (1933), n a O - . 6 . 6 3 . 6 . 0. vol. 60' I [58] Field of Search ....................................... .. 558/ 346 [56]‘ R f Cit‘ d Primary Examiner-Joseph Paul Brust e erences e U.s. PATENT DOCUMENTS :2] _ ‘ABS-“MCI f _ , e present 1nvent1on 1s a process or preparing 2,205,995 6/1940 Ulnch e181. -
(2) Appl. No. 97.27 OTHER PUBLICATIONS 22) Filed: Oct
III US005187301A United States Patent 19) 11 Patent Number: 5,187,3019 9 Cullen et al. (45) Date of Patent: k Feb. 16, 1993 54 PREPARATION OF 3,412,137 11/1968 Stutts et al. ...................... 260/465.5 IMINODIACETONITRILE FROM 3,904,668 9/1975 Gaudette et al. ... 260/465.5. A GLYCOLONTRILE 3,988,360 10/1976 Gaudette et al. ............ 260/465.5. A 4,543,215 9/1985 Brunnmueller et al. ......... 260/465.5 75 Inventors: Barry A. Cullen, Lyndeboro; Brian 4,661,614 4/1987 Most et al. .......................... 558/346 A. Parker, Nashua, both of N.H. 4,895,971 1/1990 Su et al. .............................. 558/346 4,948,909 8/1990 K t al. ....................... 558/346 73) Assignee: W. R. Grace & Co.-Conn., New York, / oenge N.Y. FOREIGN PATENT DOCUMENTS * Notice: The portion of the term of this patent 3242.193 5/1984 Fed. Rep. of Germany . subsequent- - - to Jul. 16, 2009 has been o: 2. 3: Eleapan . disclaimed. 744675 2/1956 United Kingdom . (2) Appl. No. 97.27 OTHER PUBLICATIONS 22) Filed: Oct. 11, 1990 Eschweiler, Ann 278 (1894) pp. 232-243 (Translation of Related U.S. Application Data pp. 235-238 included). (63) continuation-in-partabandoned. of ser. No. 427,414, Oct. 26, 1989, Attorney,Primary ExaminerAgent, or Firm--KevinJoseph Paul S.Brust Lemack; William L. Baker 51) int. Cl. ............................................ C07C 253/30 52 U.S. C. ..................................... 558/.455; 558/346 (57) ABSTRACT 58) Field of Search ................................ 558/346,455 A process for producing iminodiacetonitrile (IDAN) 56) References Cited from glycolonitrile and ammonia or its salt is disclosed. -
United States Patent (19) 11) Patent Number: 4,634,789 Teller Et Al
United States Patent (19) 11) Patent Number: 4,634,789 Teller et al. 45 Date of Patent: "Jan. 6, 1987 54 CONVERSION OF ACETONTRILE TO 56) References Cited GLYCOLONTRILE AND/OR U.S. PATENT DOCUMENTS GLYCOLAMDE 3,516,789 6/1970 Sennewald et al. ......... 260/465.3 X (75) Inventors: Raymond G. Teller, Aurora; James F. 4,515,732 5/1985 Brazdil et al. .................... 260/465.6 Brazdil, Mayfield Village; Linda C. Glaeser, Middleburg Heights, all of OTHER PUBLICATIONS Ohio Deutsch et al.; J. Prabst. Chemie, 321 (1), (1979), pp. (73) Assignee: The Standard Oil Company, 137-40, Cleveland, Ohio Primary Examiner-Joseph Paul Brust * Notice: The portion of the term of this patent Attorney, Agent, or Firm-Charles S. Lynch; John E. subsequent to May 7, 2002 has been Miller; Larry W. Evans disclaimed. 21) Appl. No.: 643,207 57 ABSTRACT 22 Filed: Aug. 22, 1984 The vapor phase oxidation of acetonitrile with molecu lar oxygen in the presence or absence of water vapor to 51) Int. Cl. .................. C07C 121/34; CO7C 121/36; produce glycolonitrile or glycolamide in the presence CO7C 102/08 of a vanadium oxide based catalyst. 52 U.S. Cl. ..................................... 558/451; 558/457 58 Field of Search ..................... 260/465.6; 564/130; 558/451 10 Claims, No Drawings 4,634,789 1. 2 port being 5-95, usually 10-90 weight percent of the CONVERSION OF ACETONTRLE TO catalyst composition. GLYCOLONTRILE AND/OR GLYCOLAM DE Especially useful catalysts are where A is K, a is 0.005-0.05, b is zero and c is 2; and where B is Fe, a is This invention relates to a novel catalytic method of 5 zero, b is 0.05-0.5 and c is 2. -
Chapter 5206 Department of Labor and Industry Employee Right-To-Know Standards
MINNESOTA RULES 1985 4485 EMPLOYEE RIGHT-TO-KNOW STANDARDS 5206.0100 CHAPTER 5206 DEPARTMENT OF LABOR AND INDUSTRY EMPLOYEE RIGHT-TO-KNOW STANDARDS 5206.0100 DEFINITIONS. 5206.0900 CRITERIA FOR TECHNICALLY 5206.0200 PURPOSE. QUALIFIED INDIVIDUALS. 5206.0300 SCOPE; EXCEPTIONS. LABELING 5206.0400 HAZARDOUS SUBSTANCES. 5206.1000 LABELING HAZARDOUS SUBSTANCES. 5206.0500 HARMFUL PHYSICAL AGENTS. 5206.0600 INFECTIOUS AGENTS: HOSPITALS 5206.1100 LABELING HARMFUL PHYSICAL AND CLINICS. AGENTS: LABEL CONTENT. 5206 0700 TRAINING 5206 1200 CERTIFICATION OF EXISTING 5206.0800 AVAILABILITY OF INFORMATION. LABELING PROGRAM. 5206.0100 DEFINITIONS. Subpart 1. Scope. For purposes of this chapter the following terms have the meanings given them. Subp. 2. Commissioner. "Commissioner" means the commissioner of the Department of Labor and Industry. Subp. 3. Data sheet. "Data sheet" means a document, such as a material safety data sheet, operation standard, placard or display device, used by an employer to communicate to an employee the information required under Minnesota Statutes, section 182.653, subdivisions 4b, 4c, and 4e. Subp. 4. Department. "Department" means the Department of Labor and Industry. Subp. 5. Display device. "Display device" means a video screen or video display terminal that is part of electronic data processing equipment. Subp. 6. Harmful physical agent. "Harmful physical agent" means a physical agent determined by the commissioner as part of the standard for that agent to present a significant risk to worker health or safety or imminent danger of death or serious physical harm to an employee. "Harmful physical agent" does not include an agent being developed or utilized by a technically qualified individual in a research, medical research, medical diagnostic, or medical educational laboratory, or in a health care facility or in a clinic associated with the laboratory or health care facility, or in a pharmacy registered and licensed under Minnesota Statutes, chapter 151. -
Discovery in Space of Ethanolamine, the Simplest Phospholipid Head Group
Discovery in space of ethanolamine, the simplest phospholipid head group V´ıctor M. Rivillaa,b,1 , Izaskun Jimenez-Serra´ a, Jesus´ Mart´ın-Pintadoa, Carlos Brionesa, Lucas F. Rodr´ıguez-Almeidaa, Fernando Rico-Villasa, Belen´ Terceroc , Shaoshan Zengd, Laura Colzia,b, Pablo de Vicentec, Sergio Mart´ıne,f , and Miguel A. Requena-Torresg,h aCentro de Astrobiolog´ıa, Consejo Superior de Investigaciones Cient´ıficas–Instituto Nacional de Tecnica´ Aeroespacial “Esteban Terradas”, 28850 Madrid, Spain; bOsservatorio Astrofisico di Arcetri, Istituto Nazionale de Astrofisica, 50125 Florence, Italy; cObservatorio Astronomico´ Nacional, Instituto Geografico´ Nacional, 28014 Madrid, Spain; dStar and Planet Formation Laboratory, Cluster for Pioneering Research, RIKEN, Wako 351-0198, Japan; eALMA Department of Science, European Southern Observatory, Santiago 763-0355, Chile; fDepartment of Science Operations, Joint Atacama Large Millimeter/Submillimeter Array Observatory, Santiago 763-0355, Chile; gDepartment of Astronomy, University of Maryland, College Park, MD 20742; and hDepartment of Physics, Astronomy and Geosciences, Towson University, Towson, MD 21252 Edited by Neta A. Bahcall, Princeton University, Princeton, NJ, and approved April 9, 2021 (received for review January 27, 2021) Cell membranes are a key element of life because they keep the iments of interstellar ice analogs (15, 16), which supports the genetic material and metabolic machinery together. All present idea that they can form in space. Regarding the different head cell membranes are made of phospholipids, yet the nature of the groups of phospholipids, EtA (also known as glycinol or 2- first membranes and the origin of phospholipids are still under aminoethanol, NH2CH2CH2OH; Fig. 1D) is the simplest one, debate. We report here the presence of ethanolamine in space, and it forms the second-most-abundant phospholipid in biolog- NH2CH2CH2OH, which forms the hydrophilic head of the sim- ical membranes: phosphatidylethanolamine (PE) (see Fig. -
Cyanite Waste Treatment Technology-The Old, the New, And
tl.ridation Oxidatioii most accepll past 30 yeii ’THE OLD, THE NEW, AND THE PRACTICAL illustrated tt By Walter Zabban and Robert Helwil CN- f CNCl- Chlorination is the most popular treatment for cyanide waste in plating plants. Other treatments such as ozonation. electroly( oxidation. and biooxidation deserve considerationfor at least some types of wastes. These and several other treatments are review1 2 CNC in this paper. .4 total 0)1 i heoreticallj) The technology of treating cyanide wastes, as is known today, recognized as the main commercially available method 6 83 Ib of CI1 was developed primarily between 1945 and 1955. An excellent treatment, the term “cyanide amenable to chlorination” w the chlorincc review of the early literature was published in 1949 by Dodge coined’’ and suitable methods of analysis7 were develop hypochlorit(( and Reams.’ That review, prepared during a project sponsored Since “cyanide amenable to chlorination” typifies those thata \aOCl or I by the American Electroplaters’ Society, presented the various easily decomposable in water and more toxic than others, SOI methods of treatment and described the toxicity of cyanide to of the regulatory agencies have adopted this terminology r The actu., aquatic life, bacteria, and other microorganisms in sewage practical way of differentiating between commercially treatat theoretical ii treatment plants. (amenable to chlorination) and total cyanide. cyanide-was; Supplemental detailed studies by a handful of researchers CN(A) may be determined by two procedures. One adap mmonia, a. during this period included those by Dobson,’ Pettet,3 and the distillation procedure for an aliquot that has k slows the 0) Dodge and Zabban.4 Since 1955 numerous commercial chlorinated and another that has not. -
Bioproduction of Glycolic Acid from Glycolonitrile with a New Bacterial Isolate of Alcaligenes Sp
Appl Biochem Biotechnol (2010) 160:1428–1440 DOI 10.1007/s12010-009-8607-y Bioproduction of Glycolic Acid from Glycolonitrile with a New Bacterial Isolate of Alcaligenes sp. ECU0401 Yu-Cai He & Jian-He Xu & Jin-Huan Su & Li Zhou Received: 13 January 2009 /Accepted: 9 March 2009 / Published online: 31 March 2009 # Humana Press 2009 Abstract Alcaligenes sp. ECU0401 has been isolated from soil samples with high nitrilase activity against glycolonitrile using the enrichment culture technique. The preferred carbon/ nitrogen sources and metal ions were sodium acetate, a composite of peptone and yeast extract, and Cu2+, respectively. Glycolic acid was obtained in a yield of 96.5% after 14 h of biotransformation from a total of 200 mM glycolonitrile in the mode of sequential addition during the cultivation of Alcaligenes sp. ECU0401 in a 5-L jar fermenter. Fifty micromolars of glycolonitrile could be hydrolyzed in a yield of 94.1% by resting cells after 36 h. The microbial nitrilase system could hydrolyze various nitriles with high activity, and no amidase activity and glycolic acid were observed in hydrolyzing glycolamide. It significantly exhibited high enantioselectivity in the hydrolysis of mandelonitrile and 2- chloromandelonitrile (>99.9% e.e.p). Efficient biocatalyst recycling was achieved as a result of immobilization in glutaraldehyde/polyethylenimine cross-linked carrageenan with immobilized cells exhibiting a biocatalyst productivity of 1,042.2 g glycolic acid per gram dry cell weight after 29 batch recycles. Keywords Nitrilase . Alcaligenes sp. ECU0401 . Glycolic acid . Glycolonitrile . Immobilization Introduction Nitriles are convenient and synthetically important chemical building blocks because they are widely used in the organic synthesis of compounds such as amides, carboxylic acids, Y.-C. -
Synthesis of Aldehydic Ribonucleotide and Amino Acid Precursors by Photoredox Chemistry** Dougal J
DOI: 10.1002/ange.201300321 Prebiotic Systems Chemistry Synthesis of Aldehydic Ribonucleotide and Amino Acid Precursors by Photoredox Chemistry** Dougal J. Ritson and John D. Sutherland* In continuing studies aimed at understanding the prebiotic The concurrent hydrolysis of cyanogen 2 produces cyanate 9, origin of RNA, we recently demonstrated a Kiliani–Fischer- which irreversibly traps the sugars 6 and 8 as cyclic adducts. type synthesis of simple sugars from hydrogen cyanide 1 using We wondered if the free sugars could be obtained by a variant photoredox cycling of cyanocuprates (Scheme 1).[1] of the process in which something other than 1 served as the ultimate reductant in the system, and report herein our findings with hydrogen sulfide (H2S, 10) fulfilling that role. Although our previous Kiliani–Fischer-type synthesis started with hydrogen cyanide 1 and proceeded through glycolonitrile 5, compound 5 itself is probably a more plausible starting point for the synthesis. This is because 1 produced in the atmosphere, (for example through impact shock[3]), would have been rained into bodies of ground water along with formaldehyde 4 (produced in the upper atmos- [4] phere by photoreduction of CO2 ) with which it would have reacted to give 5. Accordingly, in this work we initially explored the copper-catalyzed photoreduction of 5 with 10 in aqueous solution (containing 10% D2O to allow direct analysis by NMR spectroscopy). As phosphate is a reagent in a later stage of our ribonucleotide synthesis,[2] we incorpo- rated it into the system from the outset wherein it functioned Scheme 1. Photoredox systems chemistry of hydrogen cyanide 1, with as a pH buffer. -
Process for the Preparation of Iminodiacetonitrile and Iminodiacetic Acid
Europaisches Patentamt 3 European Patent Office © Publication number: 0 413 673 A2 Office europeen des brevets © EUROPEAN PATENT APPLICATION © Application number: 90870125.3125.3 © int. ci A C07C 255/25, C07C 229/16 © Date of filing: 13.08.90 © Priority: 14.08.89 US 394039 © Applicant: MONSANTO COMPANY Patent Department 800 North Lindbergh @ Date of publication of application: Boulevard 20.02.91 Bulletin 91/08 St. Louis, Missouri 63167(US) © Designated Contracting States: @ Inventor: Koenig, Karl Eric AT BE CH DE DK ES FR GB GR IT LI LU NL SE 1912 Gastorf Pointe Court Ballwin, Missouri 63011 (US) Inventor: Morrison, Paul Arthur 852 Hyde Park Drive Arnold, Missouri 6301 0(US) Inventor: Lanser, Gary Allen 1704 Falcon Ridge Blvd. Friendswood, Texas 77456(US) Inventor: Weisenfeid, Robert Beller 915 La Cherie Drive Manchester, Missouri 63021 (US) © Representative: Bosch, Henry A G et al Monsanto Services International S.A. Patent Department, Avenue de Tervuren 270/272, Letter Box No. 21 B-1150 Brussels(BE) © Process for the preparation of iminodiacetonitrile and iminodiacetic acid. © An improved process is provided for producing iminodiacetonitrile by contacting ammonia, formal- dehyde and hydrogen cyanide, or hex- amethylenetetramine, formaldehyde and hydrogen <^ cyanide in a reaction medium, the improvement ^ which comprises the further steps of thereafter ad- justing the pH of the reaction medium to a pH ^ between about 5.5 and about pH 10 and heating the CO reaction medium to an elevated temperature for a (Y) sufficient time to convert by-products in the reaction ^ medium to iminodiacetonitrile. <fr O Q. LU Xerox Copy Centre 1 EP0 413 673 A2 2 PROCESS FOR THE PREPARATION OF IMINODIACETONITRILE AND IMINODIACETIC ACID BACKGROUND OF THE INVENTION nide at a temperature between about 20° and ° 90 C and at a pH between 5.5 and 6.5.