Cqmcogw MOQIQE
Total Page:16
File Type:pdf, Size:1020Kb
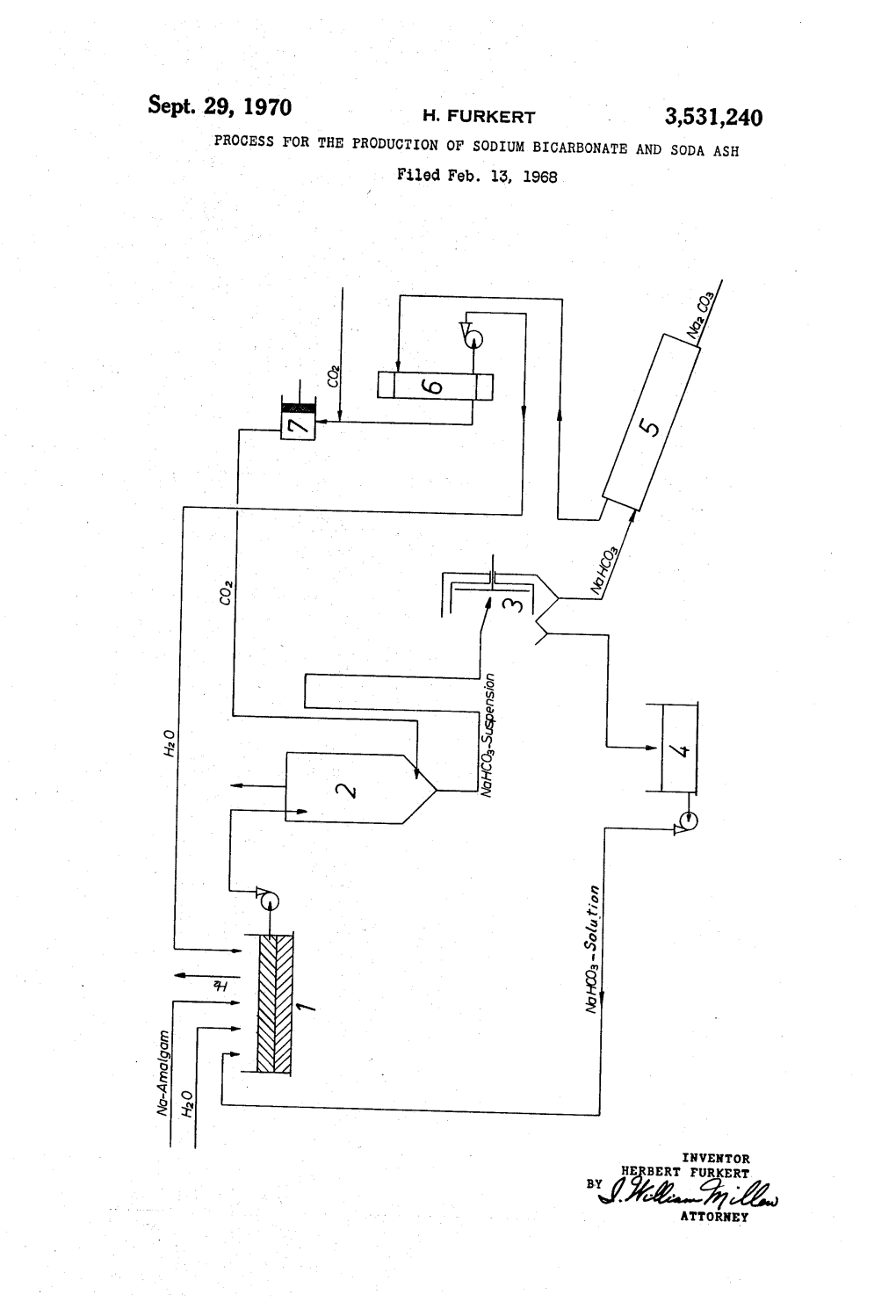
Load more
Recommended publications
-
Evaluation of Scale-Up Model for Flotation with Kristineberg Ore
Evaluation of Scale-up Model for Flotation with Kristineberg Ore Adam Isaksson Chemical Engineering, master's level 2018 Luleå University of Technology Department of Civil, Environmental and Natural Resources Engineering Evaluation of Scale-up Model for Flotation with Kristineberg Ore Adam Isaksson 2018 For degree of MASTER OF SCIENCE Luleå University of Technology Department of Civil, Environmental and Natural Resources Engineering Division of Minerals and Metallurgical Engineering Printed by Luleå University of Technology, Graphic Production 2018 Luleå 2018 www.ltu.se Preface As you may have figured out by now, this thesis is all about mineral processing and the extraction of metals. It was written as part of my studies at Luleå University of Technology, for a master’s degree in Chemical Engineering with specialisation Mineral and Metal Winning. There are many people I would like to thank for helping me out during all these years. First of all, my thanks go to supervisors Bertil Pålsson and Lisa Malm for the guidance in this project. Iris Wunderlich had a paramount role during sampling and has kindly delivered me data to this report, which would not have been finished without her support. I would also like to thank Boliden Mineral AB as a company. Partly for giving me the chance to write this thesis in the first place, but also for supporting us students during our years at LTU. Speaking of which, thanks to Olle Bertilsson for reading the report and giving me feedback. The people at the TMP laboratory deserves another mention. I am also very grateful for the financial support and generous scholarships from Jernkontoret these five years. -
Mercury and Mercury Compounds
United States Office of Air Quality EPA-454/R-97-012 Environmental Protection Planning And Standards Agency Research Triangle Park, NC 27711 December 1997 AIR EPA LOCATING AND ESTIMATING AIR EMISSIONS FROM SOURCES OF MERCURY AND MERCURY COMPOUNDS L & E EPA-454/R-97-012 Locating And Estimating Air Emissions From Sources of Mercury and Mercury Compounds Office of Air Quality Planning and Standards Office of Air and Radiation U.S. Environmental Protection Agency Research Triangle Park, NC 27711 December 1997 This report has been reviewed by the Office of Air Quality Planning and Standards, U.S. Environmental Protection Agency, and has been approved for publication. Mention of trade names and commercial products does not constitute endorsement or recommendation for use. EPA-454/R-97-012 TABLE OF CONTENTS Section Page EXECUTIVE SUMMARY ................................................ xi 1.0 PURPOSE OF DOCUMENT .............................................. 1-1 2.0 OVERVIEW OF DOCUMENT CONTENTS ................................. 2-1 3.0 BACKGROUND ........................................................ 3-1 3.1 NATURE OF THE POLLUTANT ..................................... 3-1 3.2 OVERVIEW OF PRODUCTION, USE, AND EMISSIONS ................. 3-1 3.2.1 Production .................................................. 3-1 3.2.2 End-Use .................................................... 3-3 3.2.3 Emissions ................................................... 3-6 4.0 EMISSIONS FROM MERCURY PRODUCTION ............................. 4-1 4.1 PRIMARY MERCURY -
Corrosion and Mercury Release from Dental Amalgam
Corrosion and Mercury Release from Dental Amalgam 1 Jaro Pleva, Ph.D. Abstract been presented, amalgam is still by far the most Corrosion attacks on twenty-two dental extensively used material for dental restorations.2 amalgam restorations after in vivo service have Since the investigations and warnings of the been studied by Scanning Electron Microscopy outstanding German chemist Alfred Stock, 1920- together with the Energy Dispersive X-Ray 19453 4 5 little epidemiological studies of mercury Technique, and by optical microscopy. From the release and its effects have been made. One of the measured depth and type of corrosion attack, possible reasons may be the very interdisciplinary estimates of released mercury amounts are made. character of the problem. For correct answer, The amalgam fillings have been obtained from specialist competence in the following fields is members of a group of 250 individuals, who required: materials science, suspected their health troubles potentially to be corrosion/electrochemistry, toxicology, chronic mercury poisoning from amalgam and medicine/diagnostics, physical biology, analytical were to have all amalgam fillings removed. Three chemistry. typical patient cases are presented. The common type of dental amalgam is an Model calculations of released mercury, based alloy containing typically in weight-%; 50 Hg, 35 on previously published measurements of Ag, 10 Sn, Cu, Zn. corrosion currents with and without abrasion are Reported types of amalgam degradation are also given. crevice corrosion,2 6 7 8 selective corrosion,9 The investigations show, that the long-term galvanic corrosion in contact with dissimilar release of mercury from a few amalgam fillings alloys10 11 and mechanical wear.12 33 Besides will often reach or exceed the recommended selective attack, stress corrosion has been limits for daily intake of mercury. -
NATURE MAY 6, 1944, Vol
562 NATURE MAY 6, 1944, VoL. 153 If the number of young people leaving school and nineteenth century led to the emancipation of the college is much larger in recent years than at the lower classes and of women, and to increasing de beginning of the century, it would seem that this is mands for improved social status and better educa less marked in Switzerland than in certain other tion. Dr. Erb considers that, in Switzerland, the countries. For example, it is pointed out that, in exaggerated importance imputed to academic learn 1930-31, per 100,000 of population, Germany had 63 ing of the more showy or superficial type was par Abiturienten (holders of school-leaving certificates or ticularly marked, and was closely associated with equivalent) whereas Switzerland had only 34. Japan the growing soci»l prejudice for black-coated respect and Rumania in 1934 had more than six times as ability. Those who had not themselves attained many with academic training as in 1913. In the to this status were anxious and determined that their same period those of Holland increased by 146 per children should do so; and this delusion, says Dr. cent, of France 112 per cent, of Great Britain 83 per Erb, will continue until it is more generally realized cent, and of Switzerland 59 per cent. According to that the harder one studies the more certainly will Dr. Erb, the most disturbing aspect of this increase he miss the road to wealth. This may be often true, in quantity is the serious decline in quality : he but scarcely attains the dignity of a general thinks the standard, however measured, is definitely proposition ; and in any event strikes a slightly dis lower. -
Silver City Santa Rita Hurley
SCENIC TRIPS to the GEOLOGIC PAST SILVER CITY SANTA RITA HURLEY NEW MEXICO Scenic Trips to the Geologic Past Series: No. I - Santa Fe, New Mexico No. 2 - Taos-Red River - Eagle Nest, New Mexico, Circle Drive No. 3 - Roswell- Capitan - Ruidoso and Bottomless Lakes Park, New Mexico No. 4 - Southern Zuni Mountains, New Mexico No. 5 - Silver City-Santa Rita-Hurley, New Mexico Additional copies of these guidebooks are available, for 25 cents, from the New Mexico Bureau of Mines and Mineral Resources, Campus Station, Socorro, New Mexico. HO: FOR THE GOLD AND SILVER MINES OF NEW MEXICO Fortune hunters, capitalists, poor men, Sickly folks, all whose hearts are bowed down; And Ye who would live long, be rich, healthy, and Happy; Come to our sunny clime and see For Yourselves. Handbill -- 1883 Santa Rita Open Pit, 1959. Scenic Trips to the Geologic Past No. 5 SILVER CITY - SANTA RITA - HURLEY, NEW MEXICO by JOHN H. SCHILLING 1959 STATE BUREAU OF MINES AND MINERAL RESOURCES a division of NEW MEXICO INSTITUTE OF MINING AND TECHNOLOGY Socorro - New Mexico NEW MEXICO INSTITUTE OF MINING AND TECHNOLOGY E. J. Workman, President STATE BUREAU OF MINES AND MINERAL RESOURCES Alvin J. Thompson, Director THE REGENTS Members Ex Officio The Honorable John Burroughs ...............Governor of New Mexico Tom Wiley ……….…… ...........Superintendent of Public Instruction Appointed Members Holm 0. Bursum, Jr. ........................................................ Socorro Thomas M. Cramer.......................................................... Carlsbad Frank C. DiLuzio ...................................................... Albuquerque John N. Mathews, Jr. ....................................................... Socorro Richard A. Matuszeski .............................................. Albuquerque PREFACE Much of the work undertaken at the New Mexico Bureau of Mines and Mineral Resources is done to help the mineral industries -- the prospector, miner, geologist, oil man. -
Chemistry As a Tool for Historical Research: Identifying Paths of Historical Mercury Pollution in the Hispanic New World
Bull. Hist. Chem., VOLUME 37, Number 2 (2012) 61 CHEMISTRY AS A TOOL FOR HISTORICAL RESEARCH: IDENTIFYING PATHS OF HISTORICAL MERCURY POLLUTION IN THE HISPANIC NEW WORLD Saúl Guerrero, History Department, McGill University, Montreal, QC H3A 2T7, Canada, [email protected] Introduction silver ores to identify and quantify the different mercury loss vectors that resulted from the amalgamation process This article is the first of a series that explore the as practiced in the Hispanic New World. potential of chemistry as an efficient tool for historical research. Basic chemical principles such as the The Scale of Anthropogenic Emissions of stoichiometry of chemical reactions provide the historian Mercury in the New World with a powerful tool to judge the reliability of archival records and interpret better the historiography of events From 1521 to 1810 Spain produced nearly 69% of that relate directly to processes of production based the total world output of silver from its mines in New on chemical reactions. Chemical mass balances have Spain (present day Mexico) and in the Vice-Royalty of determined both revenue streams and environmental Peru (present day Peru and Bolivia). During this period consequences in the past. there was no other non-Hispanic major silver produc- A very appropriate case study to apply this ap- tion in the New World (2). The global economic impact proach is the first industrial scale chemical process to of these exports of silver to Europe and China during have caused a global economic impact. The application the Early Modern Era has received wide coverage in of mercury amalgamation to extract silver from the ores the historiography of this period (3). -
Pdf 631.92 Kb
Separating Platinum from Gold During the Early Eighteenth Century THE METHODS USED IN SPANISH SOUTH AMERICA By Professor L. F. Capithn-Vallvey Department of Analytical Chemistry, University of Granada, Spain Following the discovery of platinum in the Viceroyalty of New Granada at the beginning of the 18th Century, its use to degrade gold forced the colonial authorities to improve their existing methods of separating and analysing the precious metals. Using information from the Royal Mint of Santa F6 de Bogota, the various ways of separating these metals are now considered, including the little-knuwn method of inquartation. Even before the discovery of the Americas by European explorers, elementary platinum metallurgy was apparently known to some of the indigenous population of the central region of New Granada; an area, shown alongside on a rare 18th century map, which was never fully integrated into the Inca world, and which now constitutes the southern part of Colombia and the northern part of Equador. Following the conquest of the New World by European in- vaders, however, this information appears to have been lost. The somewhat late discovery of platina in the Reproduced by courtesy of the Bibliotecn Nacional, Madrid Chocd area of the New Granada viceroyalty, during the 18th century, was due to several fac- ed. Its presence in the gold obtained from tors. This area had remained relatively isolated alluvial deposits would have been noted by the from Spanish penetration because of the moun- miners, by employees of the Novita and CitarA tainous terrain, high temperatures, heavy rain- foundries, and by officials of the Royal Mints at fall, numerous rivers and, above all, warlike the administrative centres of Popayan, Mari- inhabitants. -
Treating Gold Ores
Vol. VI, No.3 April I, 1935 Jlnintfsttp af Ari8nna iulltttn ARIZONA BUREAU OF MINES G. M. BUTLER, Director TREATING GOLD ORES (Second Edition) By T. G. CHAPMAN ARIZONA BUREAU OF MINES, METALLURGICAL SERIES NO. 4 BULLETIN No. 138 ptTBI.JSJID BY •••••lIIftIttv Iff ArtII1aa TUCSON,AlUZONA VoL VI, No.3 April 1, 1935 HOMERLERoy SHANTZ,PH.D., SC.D President of the University PUBLICATIONS COMMITTEE C. Z. LEsHER, Chairman; G. M. BUTLER;P. S. BURGESS;R. J. LEONARD; M. P. VOSSKUBLER;R. H. GJELSNESS;H. A. PRAEGER ARIZONA BUREAU OF MINES STAFF G. M. BUTLER,Director E. P. MATHEWSON,Metalll1l"gist T. G. CHAPMAN,Metallurgist ELDREDD. WILSON,Geologist M.uut Em.E, Mining Engineer R. E. S. lIJ:mEMAN, Mineralogist G. R. FANSE'rr, Mining Engineer STATEMENTOF MAn:.mGPRIvn.EGE The University of Arizona Bulletin is issued semi-quarterly. Entered as second-class matter June 18, 1921, at the post office at Tucson, Arizona, under the Act of August 24, 1912. Acceptance for mailing at special rate of postage provided for in Section 1103, Act of October 3, 1917, authorized June 29, 1921. Vol. VI, No.3 April 1, 1935 llnturrsitp of ~rt~ouu 1Bul1rtin ARIZONA BUREAU OF MINES G. M. BUTLER, Director TREATING GOLD ORES (Second Edition) By T. G. CHAf'MAN ARIZONA BUREAU OF MINES, METALLURGICAL SERIES NO.4 BULLETIN No. 138 PUBLISHED BY "niuusity of Arizona TUCSON, ARIZONA PREFACE As is stated by the author of this bulletin, it was prepared not to enable the owners of relatively small gold mines to decide what process should be used in extracting the gold from their ores, but rather, to acquaint them with the various processes available and the advantages and disadvantages of each of them. -
Flotation of Sulphide Ores - HZL Experience
FROTH FLOTATION : RECENT TRENDS @IIME, JAMSHEDPUR, 1998; pp. 18-41 Flotation of Sulphide Ores - HZL Experience V.P. KOHAD Hindustan Zinc Ltd., Zawar Mines, Udaipur - 313 901 ABSTRACT Flotation process, patented in the year 1906, was originally developed for mineral industry to recover values from high grade tailings of gravity separation plants. This technology has acclaimed importance as a versatile process for the beneficiation of vast variety of sulphide minerals. Due to flexibility of the process and remarkable development taken place in flotation technology and its ancillary systems, it has now become possible to recover fine grained sulphide minerals from complex ore deposits, whose processing was earlier considered un- economical. Today, about 400 million tonnes of sulphide ore is treated annually by flotation process worldwide. M/s Hindustan Zinc Ltd. (HZL), a leading lead-zinc mining and smelting company in India has experienced a spectacular growth from the time of its inception. Starting from a single 500 MT per day lead-zinc mine at Zawar, HZL has expanded its mining capacity to about 13,000 MT per day with matching ore beneficiation plants, all adopting froth flotation technology. The phenomenal progress is a result of HZL's emphasis on research and development with an objective to improve the efficiency and to optimize performance, and to seek innovative modern technology and control systems in their flotation plant and processes. This has not only solved metallurgical problems but improved overall plant economics. High grade concentrates produced with reduced deleterious impurities have further enhanced smelting efficiency. The paper covers general principles and aspects of industrial sulphide ore flotation practices in brief and processes adopted in HZL's plants. -
Unit4metallurgy.Pdf
TYBSc CHEMISTRY C303 UNIT IV THE PRINCIPLES OF METALLURGY AND CHEMISTRY OF Fe, Cu, Ni, U, Ag & Pb Minerals: Metals occur in nature, sometimes free but mostly in combined state. Those found in free or in native state are Cu, Hg, Ag, Au and Pb. The metals are found in the combined state with other elements and are obtained by mining from the earth are known as minerals i.e. Cu minerals are oxide ores – Cu2O, CuCO3.Cu(OH)2, Sulphide minerals are Cu2S , CuFeS2 etc. Ore: when a mineral contains sufficient quantity of a metal combined with other element from which it can be readily separated so as to render the extraction of metal of good quality probable. It is said to be an ore of metal. All ores are minerals but all minerals are not ores. i.e. Fe – Fe2O3.3H2O Haematite Al – Al2O3.3H2O Bauxite U – U3O8 Pitchblende Gangue or Matrix: The ores usually contains a large number of impurities like earth matters, rock stones, sand, lime stones, mica and other silicates. These impurities are known as gangue or matrix. The ores are divided into four groups. Native ores or Free State: The less reactive metals like Cu, Ag, Au, Pt, Hg and Pb occur in Free State. These metals are known as native ores. Oxides ores: These ores are classified as: Oxides and Hydroxides: The metals like Cu, Zn, Pb, Al, Sn, Cr, Mn, V, Fe,Ti, Mg, Be, Bi, etc occur as oxide and hydroxides. i.e. Fe2O3.3H2O – Haematite CuCO3.Cu(OH)2 —Malachite Carbonate : The metals like Fe, Cu, Zn, Pb, Mn, Ca, Sr, Ba, Mg etc occur as Carbonate ore. -
Lead Poisoning in the Smelting and Refining of Lead
U. S. DEPARTMENT OF LABOR BUREAU OF LABOR STATISTICS ROYAL MEEKER, Commissioner BULLETIN OF THE UNITED STATES ) (WHOLE 1 A 1 BUREAU OF LABOR STATISTICS) ' * * (NUMBER lTL 1 INDUSTRIAL ACCIDENTS AND HYGIENE SERIES: No. 4 LEAD POISONING IN THE SMELTING AND REFINING OF LEAD f FEBRUARY 17, 1914 WASHINGTON GOVERNMENT PRINTING OFFICE 1914 Digitized for FRASER http://fraser.stlouisfed.org/ Federal Reserve Bank of St. Louis Digitized for FRASER http://fraser.stlouisfed.org/ Federal Reserve Bank of St. Louis CONTENTS. Lead poisoning in the smelting and refining of lead: Page. Introduction............................................................................................................... 5-17 Dangerous processes in the smelting and refining of lead....... ............... 6-8 Dust and fumes.................................................................................................. 9-11 Sanitary equipment.......................................................................................... 11 Medical care....................................................................................................... 11 Disadvantages of a shifting force................................................................. 11,12 Prevalence of lead poisoning in the industry............................................. 12-14 Prevention of lead poisoning in the smelting industry............................ 14-17 Construction............................................................................................... 15 Sanitary equipment................................................................................. -
ALLOYS of GALLIUM with POWDERED METALS AS POSSIBLE REPLACEMENT for DENTAL AMALGAM By
NATIONAL BUREAU OF STANDARDS REPORT ^313 Progress Report on ALLOYS OF GALLIUM WITH POWDERED METALS AS POSSIBLE REPLACEMENT FOR DENTAL AMALGAM by Denton L. Smith Harold J. Caul U. S. DEPARTMENT OF COMMERCE NATIONAL BUREAU OF STANDARDS U. S. DEPARTMENT OF COMMERCE Sinclair Weeks, Secretary NATIONAL BUREAU OF STANDARDS A. V. Astin, Director THE NATIONAL BUREAU OF STANDARDS The scope of activities of the National Bureau of Standards is suggested in the following listing of the divisions and sections engaged in technical work. In general, each section is engaged in specialized research, development, and engineering in the field indicated by its title. A brief description of the activities, and of the resultant reports and publications, appears on the inside of the back cover of this report. Electricity and Electronics. Resistance and Reactance. Electron Tubes. Electrical Instru- ments. Magnetic Measurements. Process Technology. Engineering Electronics. Electronic Instrumentation. Electrochemistry. Optics and Metrology. Photometry and Colorimetry. Optical Instruments. Photographic Technology. Length. Engineering Metrology. Heat and Power. Temperature Measurements. Thermodynamics. Cryogenic Physics. Engines and Lubrication. Engine Fuels. Atomic and Radiation Physics. Spectroscopy. Radiometry. Mass Spectrometry. Solid State Physics. Electron Physics. Atomic Physics. Nuclear Physics. Radioactivity. X-rays. Betatron. Nucleonic Instrumentation. Radiological Equipment. AEC Radiation Instruments. Chemistry. Organic Coatings. Surface Chemistry. Organic Chemistry. Analytical Chemistry. Inorganic Chemistry. Electrodeposition. Gas Chemistry. Physical Chemistry. Thermo- chemistry. Spectrochemistry. Pure Substances. Mechanics. Sound. Mechanical Instruments. Fluid Mechanics. Engineering Mechanics. Mass and Scale. Capacity, Density, and Fluid Meters. Combustion Controls. Organic and Fibrous Materials. Rubber. Textiles. Paper. Leather. Testing and Specifica- tions. Polymer Structure. Organic Plastics. Dental Research. Metallurgy. Thermal Metallurgy.