PROCEEDINGS of the 28Th ANNUAL MEETING FERTILIZER INDUSTRY ROUND TABLE 1978
Total Page:16
File Type:pdf, Size:1020Kb
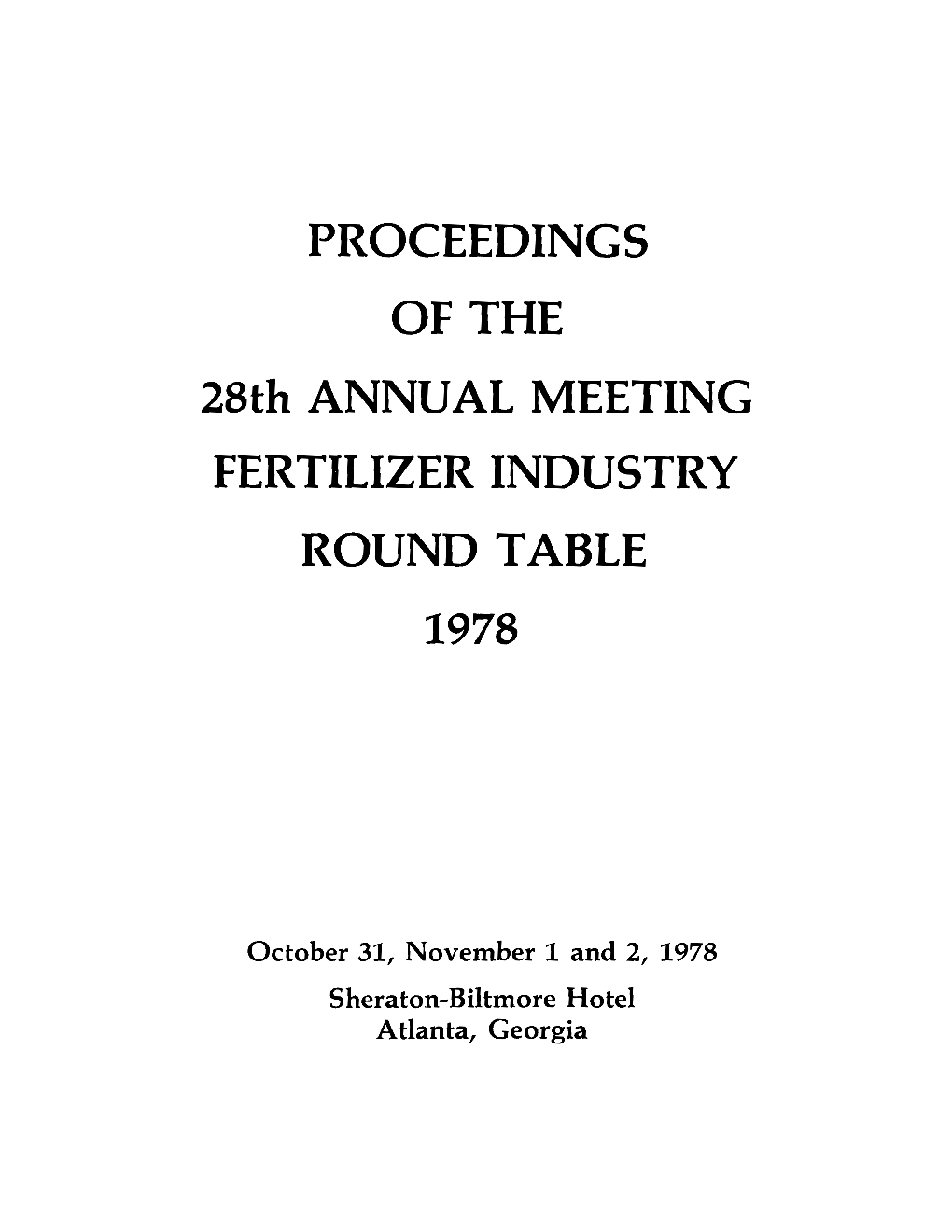
Load more
Recommended publications
-
2021 Salary Projection Survey Summary
2021 Salary Projection Survey Insights on compensation trends expected in 2021 - Summary report 38th edition | September 2020 Table of contents 1 Introduction 2 Compensation consulting 3 Participant profile 6 Survey highlights 8 Historical base salary increase trend 9 Base salary 11 Salary structure 13 Survey participants 22 Notice 22 For more information Introduction The results presented in this report are an analysis of responses collected between July and August 2020 to the 38th edition of Morneau Shepell’s 2021 Salary Projection Survey. The data represents a broad cross-section of industries representing 889 organizations across Canada and provides data on actual salary budget increase percentages for the past and current years, along with projected increases for next year. • The report contains segmented data and a detailed analysis by Morneau Shepell’s compensation consultants. • Survey participation jumped over 75% on a year over year basis from 506 organizations participating in 2019, to 889 in 2020. Many of these organizations also participated in our 2020 Canadian Salary Surveys. • Survey data includes actual 2020 and projected 2021 base salary increases and salary structure adjustments. • Survey data is reported excluding zeros and including zeros (freezes) but does not include temporary rollbacks due to COVID-19. • Findings are summarized for non-unionized employees. • Statistical requirements applied to the data analysis include a minimum of three organizations for average/mean reported results, and a minimum of five organizations -
Canwest Top 100 Saskatchewan Companies
Wednesday, September 30, 2009 Saskatoon, Saskatchewan TheStarPhoenix.com D1 New Top 100 list showcases Sask.’s diversification By Katie Boyce almost $3 billion since 2007. Viterra Inc., in its second year of his year’s Top 100 Saskatchewan operation, has also experienced significant Companies list is filled with sur- growth in revenue, jumping by almost T prises. $3 billion in the last year to claim third Besides a new company in the No. 1 spot, ranking. Long-standing leaders Canpotex 23 businesses are featured for the first time Limited and Cameco Corporation continue in the 2009 ranking, which is based on 2008 to make the top five, backed by the profit- gross revenues and sales. The additions able potash market. — headquartered in Carlyle, Davidson, Este- One major modification to this year’s list van, Lampman, Melfort, Regina, Rosetown, has been to exclude the province’s individual Saskatoon, Warman, and Yorkton — show retail co-operatives, instead allowing Feder- off the incredible economic growth that our ated Co-operatives Ltd. to represent these province has experienced during the last year. businesses. Another change has been in how 1 Covering a wide cross-section of industries SaskEnergy reports its revenue. Rather than in our province, newcomers to the list include providing gross revenue amounts, the crown PotashCorp Allan Construction, Kelsey Group of Compa- corporation started this fiscal year to report nies, Partner Technologies Incorporated and only net revenue, which accounts for the Reho Holding Ltd. (owner of several Warman significant drop in rankings. companies) in the manufacturing and con- The Top 100 Saskatchewan Companies is struction field, and Arch Transco Ltd. -
27.10.2017 Notice Under Section 6 (2) of the Competition Act, 2002 Given by Agrium Inc. and Potash Corporation of Saskatchewan
Fair Competition For Greater Good COMPETITION COMMISSION OF INDIA (Combination Registration No. C-2016/10/443) 27.10.2017 Notice under Section 6 (2) of the Competition Act, 2002 given by Agrium Inc. and Potash Corporation of Saskatchewan, Inc. CORAM: Mr. Devender Kumar Sikri Chairperson Mr. Sudhir Mital Member Mr. Augustine Peter Member Mr. U. C. Nahta Member Mr. G. P. Mittal Member Legal Representatives of the parties: M/s Shardul Amarchand Mangaldas & Co. Order under Section 31 (7) of the Competition Act, 2002 (“Order”) 1. On 10.10.2016, the Competition Commission of India (“Commission”) received a notice (“Notice”) under Section 6(2) of the Competition Act, 2002 (“Act”) given by Agrium Inc. (“Agrium”) and Potash Corporation of Saskatchewan, Inc. (“PotashCorp”) (hereinafter, Agrium and PotashCorp are collectively referred to as the “Parties”). 2. The Notice was filed with the Commission pursuant to a Plan of Arrangement entered into by and between the Parties on 11.09.2016 (“Plan of Arrangement”). Page 1 of 21 Fair Competition COMPETITION COMMISSION OF INDIA For Greater Good (Combination Registration No. C-2016/10/443) 3. In terms of Regulation 14 of Competition Commission of India (Procedure in regard to the transaction of business relating to combinations) Regulations, 2011 (“Combination Regulations”), vide letter dated 24.10.2016, the Parties were required to provide certain information / document(s) latest by 31.10.2016. The Parties filed their reply on 04.11.2016, after seeking extension of time. Letter under Regulation 14 in continuation to Parties’ reply was issued on 06.12.2016 and the Parties were directed to provide information / documents by 09.12.2016. -
August 3, 1989 Hansard Evening
LEGISLATIVE ASSEMBLY OF SASKATCHEWAN August 3, 1989 EVENING SITTING (a) the privatization of the Potash Corporation of ADJOURNED DEBATES Saskatchewan to foreign interests and other outside investors is not in the best interests of Saskatchewan people; SECOND READINGS (b) the privatization of the Potash Corporation of The Assembly resumed the adjourned debate on the proposed Saskatchewan will result in increased taxes and cut-backs motion by the Hon. Mr. Lane that Bill No. 20 — An Act in services for Saskatchewan people; and respecting the Reorganization of the Potash Corporation of Saskatchewan be now read a second time. (c) the privatization of the Potash Corporation of Saskatchewan has been overwhelmingly rejected by the Ms. Simard: — Thank you very much, Mr. Speaker. Just before people of Saskatchewan. we adjourned for supper, I had indicated that what I had wanted to do this evening was to deal with the events leading up to 1975, So I will be moving that motion at the conclusion of my remarks, and my interpretation of those events, and why the potash Mr. Speaker. corporation was established, and therefore why the potash corporation should be retained. And so where I left off at just before supper was the point that if these deposits were properly managed, Mr. Speaker, properly I also wanted to talk about some of the accomplishments of the managed and properly developed, that we have, the Potash potash corporation, and why I felt these created a very strong Corporation of Saskatchewan has the potential to supply an argument for maintaining the public Crown corporation and not increasing proportion of world demand as the ore bodies in other for privatizing it. -
T H E P R O F E S S I O N
THE prOFESSIONal EDGEISSUE 161 marCH/aprIl 2016 ETHICS achieving a Safe and prosperous Editorial provided by: martin Charlton Communications Future through Engineering and #300 - 1914 Hamilton Street, regina, Saskatchewan S4p 3N6 Geoscience T: 306.584-1000, F: 306. 584-5111, E: [email protected] Editor: lyle Hewitt, managing Director, martin Charlton Communications E: [email protected] Design and Layout: Jo anne lauder publishing & Design, T: 306.522-8461, E :[email protected] Opinions expressed in signed contributions are those of the individual authors only, and the association accepts no responsibility for them. The association reserves the right to make the usual editorial changes in manuscripts accepted for publication, including such revisions as are necessary to ensure correctness of grammar and spelling. The association also reserves the right to refuse or withdraw acceptance from or delay publication of Professional Edge Committee any manuscript. SSN 0841-6427 robert Schultz, p.Eng. - Chair Submissions to: Deb rolfes - Vice-Chair The Professional Edge Editorial Committee rob Stables, p.Eng. - liaison Councillor 300 - 4581 parliament avenue, regina SK S4W 0G3 T: 306.525.9547 F: 306.525.0851 Toll Free: 800.500.9547 Zahra Darzi, p.Eng., FEC E: [email protected] marcia Fortier, p.Geo. brett laroche, p.Eng. material is Copyright. articles appearing in The Professional Edge may be reprinted, provided the following credit Ken linnen, p.Eng., FEC is given: reprinted from The Professional Edge - association of professional Engineers and Geoscientists of brent marjerison, p.Eng., FEC Saskatchewan, (issue no.), (year). John masich, p.Eng. POSTMASTER John Styles, p.Eng., FEC return undeliverable copies to: The Professional Edge, apEGS, #300 - 4581 parliament avenue, regina SK S4W 0G3 Staff Advisor Chris Wimmer, p.Eng., FEC Advertising in The Professional Edge It pays to advertise in The Professional Edge. -
45 Years & 5 Divisions Strong
2015 WILLISTON BASIN CANPOTEX & THE BIG BUSINESS PETROLEUM CONFERENCE SASKATCHEWAN POTASH OF HOSTING EVENTS SPRING 2015 VOLUME 4 ISSUE 1 Saskatchewan 45 YEARS & 5 THE DIVISIONS STRONG MINING NORTHERN STRANDS IS GROWING WITH SASKATCHEWAN EDITION CANADA’S PREMIER INLAND PORT We are the Global Transportation Hub — western Canada’s newest, fastest-growing inland port authority. We are both independent and self-governing. Doing business with us is fast and easy. Located in the heart of western Canada, we’re home to a million sq. ft. Loblaw Distribution Centre and CP Rail’s massive new intermodal facility. Right now we have over 300 acres of prime, service-ready land for sale. Come grow with us. Already $485 million in private sector investment You’ll be in good company. — and we’re just getting started. THEGTH.COM | 306.798.4762 | REGINA, SASKATCHEWAN GTHA-0216A_BandI_Mag_Spring_Ad_8.25x10.75_031115.indd 1 2015-03-17 9:20 AM Travelling between Regina & Saskatoon? LET US GET YOU THERE ExpressAir offers frequent Monday-Friday flights between the two cities. Quick check-ins, stress-free travel and friendly service. flyexpressair.ca 1.877.392.2582 WITH BUSINESS & INDUSTRY ASSOCIATE PUBLISHER, PAUL HUBER Saskatchewan am Prairie proud! VOLUME 4 ISSUE 1 And I am especially Editors Erin Legg [email protected] proud to showcase Sherry Lee [email protected] a bunnyhug sent to Art Direction Ime by Cole Thorpe, founder Lisa Redden, Senior of Prairie Proud. Please find Design their great story inside about Candace Haiko bringing pride to this province Ghislaine Moffitt and charitably giving back at Staff Writers the same time. -
CUTS Comments on Form IV Submitted by The
SUBMISSION OF COMMENTS ON PROPOSED COMBINATION OF AGRIUM INC AND POTASH CORPORATION OF SASKATCHEWAN INC CUTS International (www.cuts-international.org) is an independent, non-profit economic policy research and outreach organisation. It works towards improvement in quality of regulation, competition and governance across sectors with the objective of enhancing consumer welfare. I. SETTING THE CONTEXT - INDIA’S DEPENDENCY ON POTASH IMPORTS The backbone of India‟s economy is agriculture, which contributes to over 22 percent of the gross domestic product (GDP) and provides livelihood to two-thirds of the population.1 With rapidly increasing population, achieving food security is a constant challenge and dependence on agricultural inputs such as fertilisers has continuously seen an upward trend. The global average demand for total fertilizer nutrients is estimated to grow at 1.8 percent per annum from 2014 to 2018, and the demand for potash is expected to grow at a rate of 2.6 percent per annum.2 Moreover, the regional demand growth for potash in South Asia is expected to be 4.9 percent (2014-2018), only second to the African region.3 In the coming months of 2017-18, market experts predict that consumption of fertilisers in India will increase, raising the demand by 5 percent in FY18.4 Notably, one of the major crop nutrients utilised entirely for the fertiliser industry in India is Potash. However, Indian reserves of Potash are not commercially exploitable and the entire demand for the mineral is met from other counties making India 100% dependent on imports in case of Potash.5 Globally, India is the 4th largest importer of potash (See Table 1). -
Economic Action Plan 2012
JOBS GROWTH AND LONG-TERM PROSPERITY ECONOMIC ACTION PLAN 2012 Tabled in the House of Commons By the Honourable James M. Flaherty, P.C., M.P. Minister of Finance March 29, 2012 Budget2012_BW_TitlePage_EN.indd 1 12-03-26 2:50 PM ©Her Majesty the Queen in Right of Canada (2012) All rights reserved All requests for permission to reproduce this document or any part thereof shall be addressed to Public Works and Government Services Canada. Available through your local bookseller or by mail from Publishing and Depository Services Public Works and Government Services Canada Ottawa, Ontario K1A 0S5 Telephone: 613-941-5995 Orders only: 1-800-635-7943 (Canada and U.S.A.) Fax: 613-954-5779 or 1-800-565-7757 (Canada and U.S.A.) Internet: http//publications.gc.ca Cat. No.: F1-23/3-2012E ISBN: 978-0-660-20189-4 This document is also available n the Internet at www.fin.gc.ca Cette publication est aussi disponible en français. Chapter 1 – Introduction ................................................................. 11 Chapter 2 –Economic Developments and Prospects .......... 23 Highlights ....................................................................................................... 25 Introduction ................................................................................................... 26 Global Economic Developments and Outlook .................................................. 26 Canada’s Recent Economic Performance ........................................................ 32 Financial Market Developments ..................................................................... -
Issue 4 2014 Edinburgh Postgraduate Law Conference Edition
Edinburgh Student Law Review 2015 Volume II | Issue 4 2014 Edinburgh Postgraduate Law Conference Edition i BLANK ii Acknowledgement The Edinburgh Postgraduate Law Conference Committee 2014 wishes to thank the University of Edinburgh Law School and the Institute for Academic Development for their financial assistance. iii Blank iv Sponsors v vi Edinburgh Postgraduate Law Conference 2014 Organising Committee Humberto Carrasco Tom Gerald Daly Laura Downey David Komuves Ekrem Solak Leslie Stevens LL.M. Liaison to the Organising Committee Ognjenka Manojlovic LL.M. Assistants Basant Abdel-Ghany Abdel-Meguid Emiel de Buijne Thomas Godener Fabian Michl Neža Šubic Ellen Heyd David Retzmann Ciaran Donohue vii Blank viii Edinburgh Student Law Review 2014-15 Honorary President Lord Hope of Craighead Honorary Secretary Dr Andrew Steven Editor-in-Chief Lorna MacFarlane Content Editors Jiahong Chen Darin Clearwater María Paz Gatica Rodríguez Ilya A. Kotlyar Alexander Latham Alisdair MacPherson Alasdair Peterson Grant Stirling Marko John Supronyuk Griff Williams Amanda Wyper Chief Copy Editors Jann-Michael Greenburg Alisha Malik Terence Merck Finance Officers Publications Officer Joseph Stephen Liptrap Danielle McAlonan Shannon Russell Copy Editors Paul Alcorn, Natalia Bell, Rowena D. Carlton, John Callender, Daria Janus, Caitlin Jenkins, Maria Kelepeshi, Joseph Stephen Liptrap, Paloma Martyniuk, David Murphy, Emily O’Sullivan, Joanne Smith, Wai-Yee Tsang, Annie Valentine ix Blank x Foreword by Professor Richard Sparks It gives me great pleasure to welcome the publication of this special conference edition of the Edinburgh Student Law Review, containing a range of pieces written by speakers at the second Edinburgh Postgraduate Law Conference, held in December 2014. Having had the great pleasure of formally opening the conference, I have had the opportunity to see first-hand how much work went into the two-day event. -
This Is Us – the Blais Family 1919 – 2017
Thisthe Blais family is 1919 –us 2017 In early 2015, I began the task of scanning Mom I decided to dig a little deeper and recorded and Dad’s photo albums. We wanted them a conversation with Grandma. I told her I all digitized so our family could easilyForeword access had some questions to ask and rolled tape. them. As I was opening each book, I was While I got a few great answers out of her, the reminded of so many fantastic memories with information just wasn't enough. Enter Aunt Rita! the Blais family. Then, I found a photo from Through tireless research, and with the help 1982 when we all got together for a reunion. of all the Blais brothers and sisters (especially It was of Grandma Rosalie reading a card in Mary Ann), she built the beautiful history of her front of all her grandchildren with tears in her mother and my grandmother. eyes. This photograph planted the seed. Seeing We also needed to tell Grandpa Emile’s story. her reading This was a difficult task as, sadly, his personal something each narrative couldn’t come directly from him. of us wrote Again, with Rita’s organizational skills and to her and the help of her brothers and sisters, his story the emotional was told. I have to say, I knew very little about response it Grandpa Emile other than the usual lore we evoked meant grandkids have all heard. But now I can look it was time. into his eyes in the photographs on his pages We needed and truly feel like I know my grandfather. -
September 00, 2004
12800 Whitewater Drive Tel 800-918-8270 Minnetonka, Minnesota 55343 Fax 952-984-0032 www.mosaicco.com Press Release www.mosaicco.com MEDIA CONTACT: Linda Thrasher, 952-984-0350 INVESTOR CONTACT: Douglas Hoadley, 952.984.0234 THE MOSAIC COMPANY ANNOUNCES CANPOTEX SINOCHEM AGREEMENT MINNETONKA, MN, November 5, 2004 – The Mosaic Company (NYSE: MOS) announced today that Canpotex Limited (Canpotex), the offshore sales association for Saskatchewan potash producers, has entered into an agreement to sell 2.1 million tonnes of potash to Sinochem Corporation (Sinochem) for 2005. The agreement includes 1.5 million metric tonnes of red standard grade potash, 0.3 million metric tonnes of granular grade potash, and 0.3 million metric tonnes of white standard grade potash covering the 2005 calendar year. The agreement provides for FOB Vancouver price increases of US$40.00 and US$43.00 per metric tonne, respectively, for red standard potash and white standard potash over 2004 contract prices. The granular grade potash will be priced at a $10 per tonne premium over the red standard potash. The 2005 agreement covers the second year of the three-year “Memorandum of Understanding” between Canpotex and Sinochem signed by the parties in August, 2003. “This new agreement will create an excellent base for the 2005 year and gives us confidence that the potash market is likely to continue to be strong during this period,” said Fritz Corrigan, CEO and President of The Mosaic Company. Canpotex member companies are: Agrium Inc. (Agrium) (TSX and NYSE: AGU), The Mosaic Company (Mosaic) (NYSE: MOS) and Potash Corporation of Saskatchewan Inc. -
K+S Compendium January 2021
K+S Group Compendium January 2021 K+S Group K+S at a Glance K+S Group financials 2019 Revenues EBITDA EBITDA-Margin Earnings after taxes, adj. € 4.07 billion € 640 million 16% € 78 million OU Europe+: Revenues: € 2.54 billion; EBITDA: € 437 million; Margin: 17% OU Americas: € 1.53 billion; EBITDA: € 230 million; Margin: 15% Customer Segments Agriculture Industry Consumers Communities 18% 42% Revenues Revenues 12% Revenues Revenues € 1.72 billion 28% € 1.15 billion € 0.48 billion € 0.72 billion EBITDA EBITDA EBITDA 15% EBITDA 46% 9% € 295 million € 218 million € 60 million € 94 million Margin 17% 34% Margin 19% Margin 12% Margin 13% 3 Global Presence¹ 1 Revenues by regions 2019 40 % 36 % 3% 9 % 13 % Employees by region 2019 69% 22 % 5 % 3 % 1% Germany North South Rest of Asia America America Europe 4 Customer Segments - Overview 2019 EBITDA Revenue share margin • Potassium chloride (MOP) • Fertilizer specialities ~42% 17% Agriculture • Chemical • Oil and Gas • Pharma • Water Softening ~28% 19% • Food • other Industrial Industry • Animal Nutrition products • Culinary • Water and Pool ~12% 12% • Ice Melt Consumers • De-icing bulk • De-icing packaged ~18% 13% Communities Adding value along our entire supply chain Exploration Our potash and salt deposits came into being millions of years ago. They are either our property or we have corresponding rights or approvals that allow the extraction or solution mining of the raw material reserves. Mining We extract raw materials in conventional mining above and below ground as well as through solution mining. We also use the power of the sun and extract salt by evaporating sea water or saline water.