JUMPSUIT Size Scissor Pattern
Total Page:16
File Type:pdf, Size:1020Kb
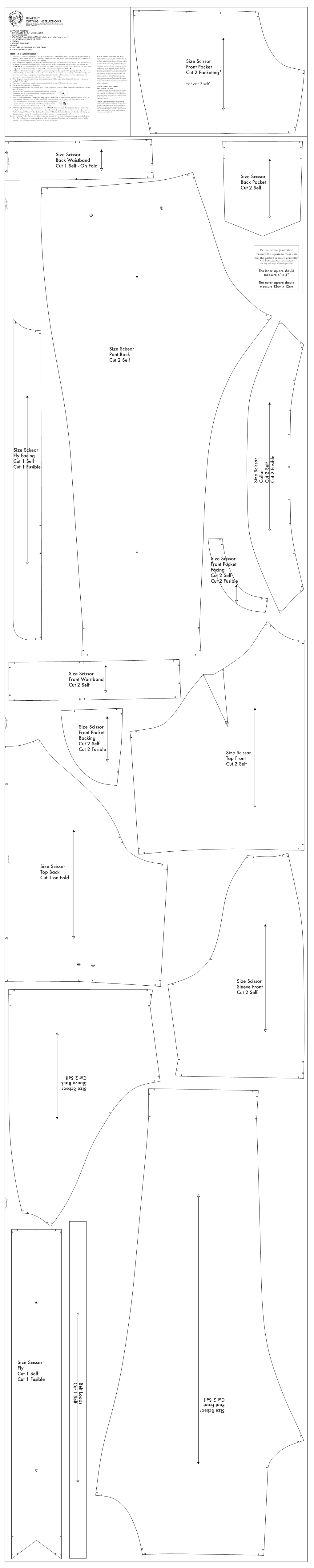
Load more
Recommended publications
-
Tailoring Series TECHNIQUES for TAILORING UNDERLINING a TAILORED GARMENT—Underlining Is a Second Layer of Fabric. It Is Cut By
tailoring series TECHNIQUES FOR TAILORING UNDERLINING A TAILORED GARMENT—Underlining is a second layer of fabric. It is cut by the garment pattern pieces and staystitched to the wrong side of the corresponding outer sections before any seams are joined. The two layers are then handled as one. As a general guide, most suit jackets and coats look more pro- fessional when underlined. Underlining is especially recommended for lightweight wool materials, loosely woven materials and light- colored materials. For additional information on selecting fabrics for underlining and applying the underlining, see Lining a Shirt 01' Dress HE 72, N. C. Agricultural Extension Service. STAYSTITCHING—Staystitch all outer garment pieces before construction begins. If garment is underlined, stays-titching is done when the two layers of fabric are sewn together. Staystitch 1/3 in. outside seamline (on the seam allowance). Stay- stitch “ with matching cotton thread on all curved *areas that may stretch during construction such as necklines, side seams, shoulder seams, armholes, and side seams of skirt. Use directional stitching always to prevent stretching of fabric and to prevent one layer of fabric from riding. The direction to stitch is indicated by small arrows on the pattern on the seamlines. INTERFACINGS—Select a high quality hair canvas for the front and collar of coats and jackets. The percentage of wool indicates the quality—the higher the wool content of the canvas the better the quality. Since a high percentage of wool makes the hair canvas fairly dark in color, it cannot be used successfully under light-colored fabrics. In these cases use an interfacing lighter in color and lower in wool content. -
Instructions
Lekala 4932 Dress With Straps Dress With Straps - Sewing Pattern #4932 Recommendations on fabric: natural/mixed fabric suitable for dresses. You will also need: fusible interfacing; 11 buttons. Seam allowances: Seam allowance for hem of garment – 2 cm; other seams – 1 cm. Note on seam allowances: - If the pattern has double contour the seam allowances are included. They are 1 cm unless specified otherwise. - If the pattern has single contour, the seam allowances are NOT included and need to be added when laying out the pattern. Note on length of fabric: Attention! The amount of fabric needed for your pattern is not included. It will depend on the selected pattern size, the width, and design of the fabric you plan to use. First, print all the paper patterns and lay them out at the width of fabric you plan to use (usually from 90 to 150 cm). Measure how much fabric you will need. Don't forget to account for pieces that need to be cut multiple times and pieces that are cut on the fold. CUTTING: Note on cutting: On the pattern pieces, “beam” means straight of grain. Lay out your pieces accordingly. Some pieces will be cut on the fold. This is noted on the pattern piece. Mark all notches and other design features such as pleats etc. from the pattern onto your fabric. When sewing the garment, pay attention to notches, they must match up. Main fabric: 1. Upper center back - cut 2 2. Upper side back - cut 2 3. Lower back – cut 1 on fold 4. -
Fabrication and Analysis of Dielectric-Elastomer Minimum-Energy Structures for Highly-Deformable Soft Robotic Systems
Fabrication and analysis of dielectric-elastomer minimum-energy structures for highly-deformable soft robotic systems Michael T. Petralia and Robert J. Wood Abstract— Dielectric-elastomer minimum-energy structures (DEMES) form an emerging class of soft robotic system. The ap- propriate materials and method for rapidly fabricating DEMES prototypes are described. A DEMES component suitable for use in highly-deformable soft robots is presented and analyzed. Combinations of this component into snake-like robots are also presented. A calculation for determining a DEMES’s maximum mechanical work, electromechanical efficiency, and energy density is described. The scope of the DEMES design- space and future research paths are discussed. I. INTRODUCTION It is well-known that a dielectric elastomer film with stretchable surface electrodes—a dielectric elastomer actu- ator (DEA)—experiences an electrostatic pressure on its surfaces when an appropriate voltage (typically on the order of kV’s) is applied across the film’s thickness [1]. This pressure causes the film to contract in the thickness di- rection and expand its area. When stretched across a rigid frame, simple dielectric elastomer actuators (DEAs) have demonstrated areal strains greater than 380% [2], energy densities as high as 3.4 MJ/m3 [3], and maximum efficiencies up to 90% [4]. DEAs are of particular interest as elec- tromechanical transducers because the transduction element is extremely pliant and highly extensible when compared to most other transducer technologies [5], [6]. As a result, DEAs are able to operate in systems that are entirely soft; moreover, DEAs have the ability to function as actively and Fig. 1: Various inextensible, pliant planar frames adhered to 500% passively deformable systems capable of large-scale changes isotropically stretched elastomer films. -
To Complete the Pattern Join Bodice #1 to #2 at Circle Front Bodice #1
To complete the pattern join bodice #1 to #2 at circle Chapter 2 Chapter 4 Chapter 6 Chapter 19 Front Bodice #1 1/2” FACING N CUT 1 FABRIC ON FOLD CUT 2 WITH FACING CUT 2 EXTENSIO INTERFACING USE FOR: GRAINLINE LAYOUT CUTTING FABRIC PATTERN MARKINGS DARTS SEAMS COLLARS CLOSURES CENTER FRONT FOLD To completeTo the pattern join bodice #1 to #2 at circle TO COMPLETE THE PATTERN JOIN BODICE #1 TO #2 AT CIRCLE STITCH TO MATCHPOINTS FOR DART TUCK FRONT BODICE #2 Front Bodice #2 Chapter 2 Chapter 4 Chapter 6 Chapter 19 STITCH TO MATCHPOINTS FOR DART TUCKS To complete the pattern join bodice #3 to #4 at circle Chapter 2 Chapter 4 Chapter 6 Back Bodice #3 CUT 2 FABRIC USE FOR: CK SEAM GRAINLINE LAYOUT CUTTING FABRIC CK FOLD PATTERN MARKINGS DARTS SEAMS COLLARS CENTER BA CUT HERE FOR CENTER BA To completeTo the pattern join bodice #3 to #4 at circle STITCH TO MATCHPOINTS FOR DART TUCKS Back Bodice #4 Chapter 2 Chapter 4 Chapter 6 Chapter 4 Chapter 11 Chapter 14 Chapter 17 MATCHPOINT Front Skirt #5 CUT 1 FABRIC USE FOR: V SHAPED SEAM WAISTBAND WAIST FACING BIAS WAIST FINISH CURVED/ALINE HEM BIAS FALSE HEM CENTER FRONT FOLD Chapter 4 Chapter 11 Chapter 14 Front Yoke #6 CUT 1 FABRIC CUT 1 INTERFACING USE FOR: V SHAPE SEAM WAISTBAND WAIST FACING BIAS WAIST FINISH C. F. FOLD C. F. MATCHPOINT Chapter 4 Chapter 6 Chapter 10 Chapter 11 Chapter 14 Chapter 17 MARK DART POINT HERE Back Skirt #7 CUT 2 FABRIC USE FOR: SEAMS ZIPPERS WAISTBAND WAIST FACING BIAS WAIST FINISH CURVED ALINE HEM BIAS FALSE HEM Chapter 4 CUT ON FOLD Chapter 12 Chapter 17 H TC NO WHEN -
Surprise Humbug Tutorial You Will Need: 1 Rectangle of Stitched Linen Some 5Mm Ribbon Some Interfacing Some Matching Beads (Optional) Some Felt
Surprise Humbug Tutorial You will need: 1 rectangle of stitched linen some 5mm ribbon some interfacing some matching beads (optional) some felt Step 1 : getting ready. Iron your stitched linen (on the back of the work). Allow an extra 1cm around all the sides of the stitched design to allow for the seams. Cut a rectangle of interfacing to the same dimensions as the design, and iron it onto the back of it. Then fold back the hems and iron them down into position. Step 2 : putting it together. Place the felt rectangle over the back of the design, and stitch it in place, so that you hide the back of the design as well as the hems. Stitch the ribbons in place (on the felt side), on both sides of the rectangle, making sure that they are aligned with the design. Page 1/3 Copyright © 2012 Faby Reilly (www.fabyreilly.com) All rights reserved Surprise Humbug Tutorial Roll up your rectangle so that the “ribbon” sides are touching. Start stitching them together, taking care to leave a large enough opening (roughly 2/3 up from the bottom of the design). Whip-stitch** your way up towards the top, around the corner and down until you can stitch no more. You can (if you so wish) add beads to your seam as you go. Then work on the opposite side, shaping it so that you get a humbug. Step 3 : adding the finishing touches. The ribbons should be facing each other, ready to be tied into a pretty bow. Your surprise humbug is now to be filled with a “surprise” of your choice. -
Soft Electronic Platforms Combining Elastomeric Stretchability and Biodegradability
RESEARCH ARTICLE www.advsustainsys.com Soft Electronic Platforms Combining Elastomeric Stretchability and Biodegradability Martin Held, Alexander Pichler, Joshua Chabeda, Natalie Lam, Philip Hindenberg, Carlos Romero-Nieto, and Gerardo Hernandez-Sosa* of these devices would, on the one hand, Soft and stretchable electronic devices are expected to offer technological help to reduce the high amount of global advances in the field of robotics, human–machine interfacing, and healthcare. electronic and plastic waste.[8] On the other Employing biodegradable elastomers, hydrogels, and nontoxic conductors hand, it would enable implantable tempo- would add significant value to and minimize the ecological impact of such rary sensors or prosthetics, which would not have to be removed after the therapy, disposable and transient electronic applications. Here, the biodegradable and making a second surgery redundant.[9,10] photo-crosslinkable elastomer poly(glycerol sebacic) acrylate (PGSA) is charac- An increasing number of biodegradable terized for its use in soft and stretchable electronics. Its mechanical proper- electronic elements,[11–13] such as transis- ties are investigated in terms of their chemical composition and compared to tors,[14] capacitors,[15] or light-emitting elec- [16–18] commonly used gelatin hydrogels. Furthermore, these materials are combined trochemical cells (LECs) have been reported in recent years. However, they with interconnects made of liquid Galinstan in order to create functional sub- have been commonly fabricated on rigid or strates with certified biodegradability under ISO standards. The combination foil substrates,[19] which lack stretchability. of these materials produces elastic circuit boards that act as soft platforms for Materials exhibiting evident biodegrada- body-mounted sensors or biodegradable stretchable light-emitting devices. -
FRONT PLACKET for BABY HENLEY SHIRT OTTOBRE Design® OTTOBRE Design 1/2020, Design 1 1/2020
FRONT PLACKET FOR BABY HENLEY SHIRT OTTOBRE design® OTTOBRE design 1/2020, design 1 1/2020 Fuse interfacing to placket piece, and also fuse a narrow strip of interfacing 6. Fold placket piece on left-hand side of placket wrong sides together to wrong side of shirt front panel over pattern marking for placket along marked foldline to form placket underlap. Overlap placket edges, opening. See areas shaded in grey on small-scale patterns. then stitch horizontal row of straight-stitching through all layers at bottom placket from right side, catching placket underlap in stitching. 1. Serge or zigzag raw straight side edge and raw bottom edge of placket piece. Slash placket opening on placket piece as marked on pattern. 7. Attach snap fasteners to placket or, alternatively, stitch buttonholes and sew buttons on it. 2. Pin placket piece to front panel right sides together (place slashed placket opening to the left of center-front line on front panel). Straight- stitch side edges and bottom of placket with 3 mm seam allowance. Slash placket opening on front panel between stitching lines. © OTTOBRE design® | STUDIO TUUMAT OY The designs, instructions and patterns are only intended for personal 3. and 4. Understitch seam allowances at each side edge of placket use by sewing hobbyists. All commercial or industrial use is prohibited. opening to placket piece close to seamline. The designs, instructions, patterns, drawings and photos are protected by copyright laws and the right of reproducing them by any means or 5. Turn placket piece to wrong side of front panel. Topstitch curved in any form is exclusively reserved for the copyright holder. -
BANASCH's INC. 603 Brooklyn Ave
Banasch’s Inc. www.banaschs.com FAMILY OWNED AND OPERATED SINCE 1910 Sewing Supplies, Notions, Sewing Equipment, Irons, Pressing Equipment, Hangers, Poly, Garment Rack, Heat Seal/Mending Tapes and much more! We specialize in providing our customers with quality products and quality service. We strive to be your single source vendor. 603 BROOKLYN AVE. STE. B MILFORD, OH 45150 www.banaschs.com Phone: 513-731-2040 Toll free phone: 800-543-0355 Fax: 513-731-2090 Toll free fax: 866-417-2090 www.banaschs.com Phone: 513-731-2040 Toll free phone: 800-543-0355 Fax: 513-731-2090 Toll free fax: 866-417-2090 Banasch’s is located at 603 Brooklyn Avenue, Suite B, Milford, Ohio 45150. We have been in business since 1910 providing quality products with competitive prices. We strive to be your single source sewing supply and sewing equipment vendor. We proudly staff knowledgeable people with many years of product knowledge and know how in the garment industry. Please don’t hesitate to contact us with any questions on supplies or equipment. How to place an order: Our sales staff and customer service are available Monday thru Friday from 8:30am to 5:30pm EST. We are always happy to take your order over the phone. We can accept your order also via mail, fax, e-mail, e-commerce from our website. Our website address is: www.banaschs.com Please use our order form in our catalog to prepare your order before calling or sending it to us. Our phone numbers are: 513-731-2040 or toll free 800-543-0355 Our fax phone numbers are: 513-731-2090 or toll free fax 866-417-2090 You can e-mail your order to: [email protected] Please be sure to specify the sizes, colors, quantities, style numbers and name or description of item. -
Lesson Guide Jacket Interfacing & Lining Draping: Advanced
Lesson Guide Jacket Interfacing & Lining Draping: Advanced Module 1 - Jacket Interfacing Step 1 For this lesson we will use the jacket created in our Jacket Draft & Drape lesson. We will begin this lesson by planning the jacket’s interfacing pieces. Consider these 5 points when choosing an interfacing: 1 Module 1 - Jacket Interfacing Step 1 Softly Tailored/Structured Decide on the overall look of your jacket. You may wish to create a softly tailored jacket or a more structured jacket. Here we will plan for a softly tailored jacket. 2 Module 1 - Jacket Interfacing Step 2 Woven fusible hair canvas or woven non-fusible mid-weight interfacing. Select the interfacing that best suits the look and the type of fashion fabric that you have chosen. For example, if you are going for a tailored, more structured look you may wish to choose a woven fusible hair canvas. If you are going for a softer look then you might choose a woven non-fusible mid-weight interfacing. 3 Module 1 - Jacket Interfacing Step 3 Interfacing - compatible with fashion fabric Always test various types of interfacing before you make your final selection, to be sure that the final choice is compatible with your choice of fashion fabric. You wouldn’t choose an interfacing that is heavier than your fashion fabric since it might be too overpowering for the overall look of the jacket. 4 Module 1 - Jacket Interfacing Step 4 Measure/Pre-Shrink Interfacing Once you have chosen the appropriate interfacing for your jacket design, whether it be a woven, non-woven or stretch or whether it is fusible or non-fusible, you must test it for shrink- age. -
Please Come with All of Your Pieces Pre-Cut with Interfacing Fused on and Labeled
SUPPLY LIST AND CLASS POLICIES Prima Diva Clutch Wallet Wednesday, April 21,2016, 10am-2pm Jenny Yannone Required Pattern: Prima Diva Clutch Wallet $10.00 Diva Wallet Frame (your choice of color) $12.00 1/2 yd Main Fabric (Outside of wallet, Outside of pockets, optional strap.) 5/8 yd Accent Fabric (Lining of wallet, lining of pockets) Fat Eighth or scrap of fabric (5” X 12”) for outer band Two 14” zippers Wonder tape 1/3 yard Décor-bond fusible interfacing Coordinated Isacord thread with matching bobbin Sewing Machine in good working order, power cord, slide-on table Zipper foot (#4 or #4D for Bernina) 1/4" Patchwork foot (#37, #57 or #97 for Bernina) Walking Foot or 37D foot Wonder Clips Fray Block E6000 glue Optional: 2 jump rings or D-rings and Chain for purse option Optional: Renaissance Ribbon for trim Basic supplies, ie: scissors, seam ripper, thread to match project, etc. Please come with all of your pieces pre-cut with interfacing fused on and labeled. Sewing supplies: Machine in cleaned and oiled working order, brush to clean your machine, machine oil, bobbins, foot pedal, cord, slide on table, thread, 80/12 needles, pins, small scissors to trim threads, seam ripper. 124 E. Lyndale Avenue, Helena, Mt. 59601 406-443-5724 www.thesewingpalacebernina.com Email: [email protected] The Sewing Palace 124 E Lyndale Helena, MT 59601 (406)443-5724 www.thesewingpalacebernina.com CLASS POLICIES 1. Registration can be made in person, online, by mail or telephone. 2. Phone reservations accepted with credit card payment. 3. -
Class Offerings
Class Offerings September 15 - 18 at the Ashton Gardens CLASSES Preregistration required for classes. Visit thanksgivingpoint.org/quilt for more information and to register. Attendees should come prepared with basic sewing supplies (straight pins and pin cushion, scissors, seam ripper, fabric marking pen or pencil, small cutting mat (no larger than 12x18), rotary cutter) in addition to any supplies noted in class descriptions. Shared ironing and cutting areas will be available in each room. Thanksgiving Point members recieve 10% discount on class registration. Member discount does not apply to kit fee. Wednesday, 9 am - Noon, Virtual Hand pieced Liberty Manx Log Cabin With Jenni Smith | Virtually & In Classroom Technique: Hand piecing Skill level: Beginner Manx Log Cabin - We are not going to sit in the dark with no tools for this workshop as was the case on the Isle of Man in the early 19th century– but I love how this technique was born from a necessity to use scraps and keep warm, with very basic equipment. A Manx Log Cabin block is very portable and involves tearing strips and embracing the slight imperfections to create a block so personal - in fact it is based entirely on the shape and size of your own hands! Jenni Smith (Author of Quilting with Liberty Fabrics) will teach you how to hand piece a Manx Log Cabin block, quilting it as you go and you can make 4 blocks to create a cushion top, table-runner or the start of a quilt. Log Cabins are brilliant scrap busters so I would recommend using a collection of cotton prints to play with (a mix of Tana Lawn and Quilting Cotton is fine). -
Quilting Classroom 8.00 Am
Quilting Classroom Jennie Rayment 10th April 2015 8.00 am Tools & Equipment Transform your sewing machine mat to a tidy tote, change a portable baby changing mat to a neat carry case, turn an ironing pad into a easy to cart caddy - it’s all here in today’s Classroom. Remember to record the show! Sewing machine Thread to match Fabrics Rotary Cutter 28/45/60 mm Cutting Mat 17 x 23” Acrylic Ruler - 24.5 x 6.5” Eazy Heart Acrylic template Petal Pattern Acrylic Template Square in a Square Acrylic Template Hobbs batting (Crib size) regular Hobbs batting (Crib size) fusible Boxall Craf-tex - heavyweight fusible Notions Pins Hook and Loop Fastener 25 mm Sew Easy or Clover Bias maker Nursery Zoo Panel Clover mini iron Fabric Products Nursery Zoo Panel Funky Spot Flo Turquoise 1.5m Mini Bolt Mini Cupcake Turquoise 1.5m Mini Bolt Melodic Floral Fat Quarters Windy Daze Fat Quarters Sew-in interfacing Windy Daze Fat Quarters Melodic Floral Fat Quarters Sewing Machine Table Mat Tidy You need: Five Fat Quarters (Three are used for front and front of tidy, two are for Petal Pattern and pockets.) 1. Make front: Trim selvedge from Purple F/Q. Cut 4½ x 21” strip from Multi-patterned F/Q. Sew this strip to one side of Purple F/Q. Press seam open and flat. 2. Make back: Trim selvedge from White & Purple Floral F/Q. Cut 4½ x 21” strip from Multi-patterned F/Q. Sew this strip to one side. Press seam open and flat. 3.