Primary Calibration of Accelerometers at NIST Using a Dual Coil Shaker
Total Page:16
File Type:pdf, Size:1020Kb
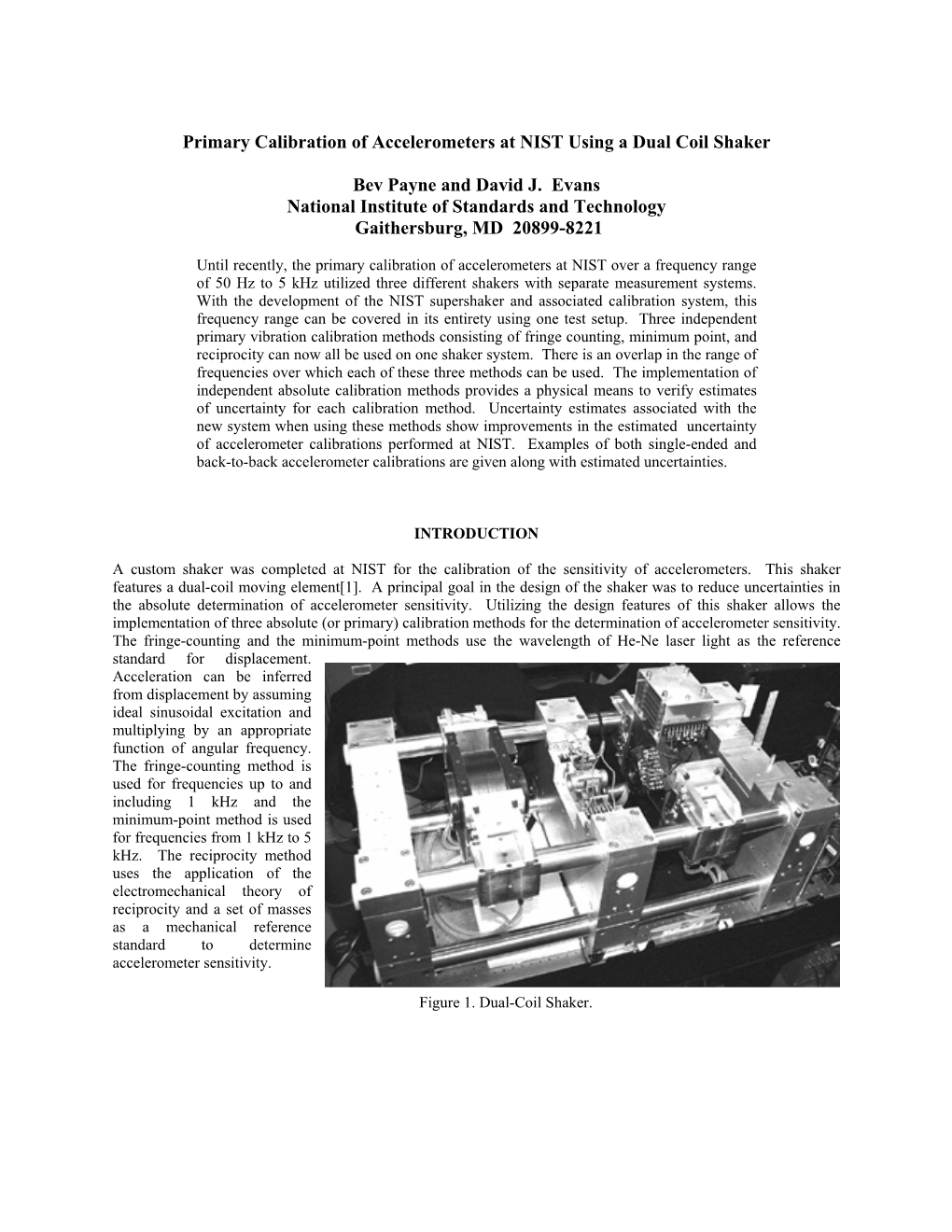
Load more
Recommended publications
-
2020-22 GRADUATE CATALOG | Eastern New Mexico University
2020-22 TABLE OF CONTENTS University Notices..................................................................................................................2 About Eastern New Mexico University ...........................................................................3 About the Graduate School of ENMU ...............................................................................4 ENMU Academic Regulations And Procedures ........................................................... 5 Program Admission .............................................................................................................7 International Student Admission ...............................................................................8 Degree and Non-Degree Classification ......................................................................9 FERPA ................................................................................................................................. 10 Graduate Catalog Graduate Program Academic Regulations and Procedures ......................................................11 Thesis and Non-Thesis Plan of Study ......................................................................11 Graduation ..........................................................................................................................17 Graduate Assistantships ...............................................................................................17 Tuition and Fees ................................................................................................................... -
Homo Reciprocans: Survey Evidence on Behavioural Outcomes*
The Economic Journal, 119 (March), 592–612. Ó The Author(s). Journal compilation Ó Royal Economic Society 2009. Published by Blackwell Publishing, 9600 Garsington Road, Oxford OX4 2DQ, UK and 350 Main Street, Malden, MA 02148, USA. HOMO RECIPROCANS: SURVEY EVIDENCE ON BEHAVIOURAL OUTCOMES* Thomas Dohmen, Armin Falk, David Huffman and Uwe Sunde This article complements the experimental literature that has shown the importance of reciprocity for behaviour in stylised labour markets or other decision settings. We use individual measures of reciprocal inclinations in a large, representative survey and relate reciprocity to real world labour market behaviour and life outcomes. We find that reciprocity matters and that the way in which it matters is very much in line with the experimental evidence. In particular, positive reciprocity is associated with receiving higher wages and working harder. Negatively reciprocal inclinations tend to reduce effort. Negative reciprocity increases the likelihood of being unemployed. Reciprocity is an in-kind response to friendly or hostile acts. Homo economicus would never engage in reciprocal behaviour, where it does not advance material self-interest. An alternative model is homo reciprocans, for whom reciprocal behaviour is driven by reciprocal motivations: direct utility value is placed on rewarding or punishing (Rabin, 1993; Falk and Fischbacher, 2006). Conceptually, one can distinguish between positive reciprocity, the degree to which an individual rewards kind actions, and negative reci- procity, the extent to which the individual punishes unkind actions. Positive reciprocity has been demonstrated in experimental settings where contracts are incomplete and workers reciprocate generous wages with high effort, even though there is no way to enforce contracts (Fehr et al., 1993; Brown et al., 2004). -
When Reciprocity Becomes Back-Scratching: an Economic Inquiry
When reciprocity becomes back-scratching: An economic inquiry Cameron K Murray M.Sci. (Business), B.Sci. (Property Economics) A thesis submitted for the degree of Doctor of Philosophy at The University of Queensland in 2015 School of Economics Abstract This thesis reports four studies of a particular type of cooperation where the formation of coor- dinated groups through favour exchanges benefits the connected few at the expense of the many. This process is labelled back-scratching, and is a common feature of political decision-making where institutional powers allow for a large amount of discretion and the imposition of external- ities in situations where property rights are not well-defined. Chapter 1 introduces the concept of back-scratching in as a coordination game with negative externalities, providing a common framework within which to incorporate the studies that follow. The first study in Chapter 2 uses a natural experiment to quantify the gains from back-scratching in political decisions about value-enhancing land zoning. The effectiveness of a variety meth- ods used to support implicit favouritism are examined, including political donations, employing professional lobbyists, and investing in relationships. Using micro-level relationship data from multiple sources, characteristics of landowners of comparable sites inside and outside rezoned areas are compared. `Connected' landowners owned 75% of land inside rezoned areas, and only 12% outside, and captured $410 million in value gains, indicating a trade in favours amongst con- nected insiders. Marginal gains to all landowners of connections in our sample were $190 million. Engaging a professional lobbyist appears to be a substitute for having one's own connections. -
Paul Mitchell the School Jacksonville 4624 Town Crossing Drive, Suite 155 Jacksonville, FL 32246 (877) 298-1854 / (904) 713-2700
Paul Mitchell The School Jacksonville 4624 Town Crossing Drive, Suite 155 Jacksonville, FL 32246 (877) 298-1854 / (904) 713-2700 E-mail: [email protected] A copy of this catalog is provided to students at least one week prior to enrollment. Volume No. 105 Institution ID No. 1132 April 14, 2014 Melissa Jenkins PAUL MITCHELL THE SCHOOL JACKSONVILLE CATALOG 1 Table of Contents MISSION STATEMENT . 4 SCHOOL FACILITIES . 4 SCHOOL FACULTY . 4 ADMINISTRATION/OWNERSHIP . 4 COURSE DESCRIPTION (All courses are taught in English) ............................................... 4 PARKING . 5 NONDISCRIMINATION . 5 ANTI-HAZING POLICY . 5 ADMISSION REQUIREMENTS . 6 ADMISSION PROCEDURE . 6 ACCEPTANCE . 7 STATE LICENSING DISCLAIMER . 7 ENROLLMENT INFORMATION . 7 EDUCATION GOALS . 8 COST OF TUITION AND SUPPLIES . 9 SCHOLARSHIPS . 9 2014 CLASS START DATES . 10 CONSTITUTION DAY . 10 VOTER REGISTRATION . 10 DEFINITION OF CLOCK HOUR . 10 STUDENTS WHO WITHDRAW . 10 REENTRY STUDENTS . .. 11 TRANSFER STUDENTS . 11 TERMINATION POLICY . 11 DETERMINATION POLICY . 12 COSMETOLOGY COURSE OVERVIEW . 12 COSMETOLOGY COURSE OUTLINE . .. 12 BARBERING COURSE OVERVIEW . 13 COSMETOLOGY COURSE OUTLINE . .. 13 STATE OF FLORIDA REQUIREMENTS . 14 COURSE DESCRIPTION – COSMETOLOGY . 15 COURSE DESCRIPTION – BARBERING . 17 COSMETOLOGY AND BARBERING PROGRAM TESTING AND GRADING PROCEDURE . 18 PROGRAM MEASURABLE PERFORMANCE OBJECTIVES . .. 18 SAFETY PRECAUTIONS FOR THE BEAUTY INDUSTRY . 19 INDUSTRY REQUIREMENTS . 19 STUDENT SERVICES . 19 GRADUATION REQUIREMENTS IN COURSES . 20 GRADUATION, PLACEMENT, AND JOB OPPORTUNITIES . 20 STUDENT KIT DISCLAIMER . 20 PAUL MITCHELL THE SCHOOL JACKSONVILLE CATALOG 2 STUDENT KIT – Cosmetology 1200 hours . 21 STUDENT KIT – Barbering 1200 hours . 22 FINANCIAL AID – CONSUMER INFORMATION . 23 FEDERAL RETURN OF TITLE IV FUNDS POLICY . 30 TREATMENT OF TITLE IV FUNDS WHEN A STUDENT WITHDRAWS FROM A CLOCK-HOUR PROGRAM . -
Iron Workers Reciprocating Local Unions
Iron Workers Reciprocating Local Unions Local Union Health and Welfare Pension Annuity 1 A & B A & B Structural Iron Workers Local 1 Structural Iron Workers Local 1 Structural Iron Workers Local 1 Welfare Fund Pension Fund Pension and Annuity Fund 7700 Industrial Drive 7700 Industrial Drive 7700 Industrial Drive Forest Park, IL 60130 Forest Park, IL 60130 Forest Park, IL 60130 John Gardiner, Administrator John Gardiner, Administrator John Gardiner, Administrator Email: [email protected] Email: [email protected] Email: [email protected] Tel: 708-366-1188 Tel: 708-366-1188 Tel: 708-366-1188 Fax: 708-366-4809 Fax: 708-366-4809 Fax: 708-366-4809 1/1/83 1/1/83 05/01/01 Also signatory to: Iron Workers Mid-America Pension Fund 2350 East 170th Street Lansing, IL 60438 Joseph J. Burke, Administrator Email: [email protected] Tel: 708-474-9902 or 800-232-8029 Fax: 708-474-9982 1/1/1985 3 A & B A & B Iron Workers of Western Pennsylvania Benefit Iron Workers of Western Pennsylvania Benefit Iron Workers of Western Pennsylvania Benefit Plans Local 3 and 772 Plans Local 3 and 772 Plans Local 3 and 772 2201 Liberty Avenue, Room 203 2201 Liberty Avenue, Room 203 2201 Liberty Avenue, Room 203 Pittsburgh, PA 15222-4598 Pittsburgh, PA 15222-4598 Pittsburgh, PA 15222-4598 Jessica Schneider, Plan Manager Jessica Schneider, Plan Manager Jessica Schneider, Plan Manager Email: [email protected] Email: [email protected] Email: [email protected] Tel: 412-227-6740 Tel: 412-227-6740 Tel: 412-227-6740 Fax: 412-261-3816 Fax: 412-261-3816 Fax: 412-261-3816 1/1/83 1/1/83 10/10/91 6/3/2016 Page 1 of 59 Iron Workers Reciprocating Local Unions Local Union Health and Welfare Pension Annuity 5 A & B A & B Iron Workers Local 5 Welfare Iron Workers Local 5 Pension Mid-Atlantic States District Council Participating Fund Fund Locals Annuity Fund GEM Group GEM Group Lawrence C. -
Laser Interferometer and Reciprocity Calibration of Accelerometers Using the NIST Super Shaker
Submitted to: Third Inter. Conference on Vibration Measurements by Laser Techniques: Advances and Applications, June 16-19, Ancona, Italy. Laser Interferometer and Reciprocity Calibration of Accelerometers Using the NIST Super Shaker Bev Payne National Institute of Standards and Technology Automated Production Technology Division Gaithersburg, Maryland 20899 Abstract The development of the NIST Super Shaker permits calibration of accelerometers by two independent and absolute methods on the same shaker. Minimizing the uncertainty of reciprocity calibrations imposes strin- gent requirements for distortion and cross-axis motion. Laser interferometer calibrations require very low coupling between the shaker and the interferometer components. The design of the Super Shaker provides for very low distortion and cross-motion with very low mechanical coupling between the shaker and opti- cal components. The shaker is equipped with dual coils and two retractable magnets to provide for reci- procity measurements without attaching a driving shaker. These features enhance the convenience with which the Super Shaker can be used to perform both reciprocity and laser interferometer calibrations. This paper describes the shaker and calibration system and gives a comparison of calibration results from the two methods. Keywords: accelerometers, calibration, reciprocity, laser interferometer, uncertainty, shakers, exciters. 1. Introduction A new Super Shaker system for calibration of accelerometers at NIST was designed in 1993, and its initial testing was finished in 19951. A principal goal of this design is to reduce the uncertainties of accelerometer calibrations. This paper gives the results of additional testing and the implementation of two absolute calibration methods on the Super Shaker. The fringe-counting method uses the wavelength of a He-Ne laser light as a reference standard and the reciprocity method uses a set of standard masses as a reference standard. -
Acts of Reciprocity: Analyzing Social Exchange in a University Theater for Social Change Project
W&M ScholarWorks Dissertations, Theses, and Masters Projects Theses, Dissertations, & Master Projects 2010 Acts of reciprocity: Analyzing social exchange in a university theater for social change project Nicole Birgit Cloeren William & Mary - School of Education Follow this and additional works at: https://scholarworks.wm.edu/etd Part of the Educational Methods Commons, Educational Sociology Commons, and the Higher Education Commons Recommended Citation Cloeren, Nicole Birgit, "Acts of reciprocity: Analyzing social exchange in a university theater for social change project" (2010). Dissertations, Theses, and Masters Projects. Paper 1550154040. https://dx.doi.org/doi:10.25774/w4-s4nc-j548 This Dissertation is brought to you for free and open access by the Theses, Dissertations, & Master Projects at W&M ScholarWorks. It has been accepted for inclusion in Dissertations, Theses, and Masters Projects by an authorized administrator of W&M ScholarWorks. For more information, please contact [email protected]. ACTS OF RECIPROCITY: ANALYZING SOCIAL EXCHANGE IN A UNIVERSITY THEATER FOR SOCIAL CHANGE PROJECT A Dissertation Presented to The Faculty of the School ofEducation The College of William and Mary in Virginia In Partial Fulfillment Of the Requirements for the Degree Doctor of Philosophy by Nicole Birgit Cloeren May 2010 ACTS OF RECIPROCITY: ANALYZING SOCIAL EXCHANGE IN A UNIVERSITY THEATER FOR SOCIAL CHANGE PROJECT by Nicole Birgit Cloeren Approved May 201 0 by Chairperson of Doctoral Committee du__~~k,.~ Monica D. Griffin, Ph.D. Pamela -
Reciprocity, Revenge and Religious Imperatives
RECIPROCITY, REVENGE AND RELIGIOUS IMPERATIVES: FIGHTING IN THE HIGHLANDS OF PAPUA NEW GUINEA Louise Chiragakis Thesis submitted in partial fulfilment for the requirements of the Degree of Master of Arts in the Department of Archaeology and Anthropology, Faculty of Arts, Australian National University, Canberra, January 1995 Acknowledgments I wish to thank Dr Don Gardner for his encouragement and patience in giving me guidance during the writing of this thesis, particularly as his time has been so valuable. Thanks also to Dr Nick Peterson for motivation during Don’s absence, and for the original encouragement from the late Prof. Anthony Forge who thought that it was a good idea to pursue the topic. Preface In 1990, the Department of Anthropology at the A.N.U. offered The Anthropology of New Guinea and Melanesia, a course that looked interesting in its own right and was virtually guaranteed to be so because it was to be conducted by Prof. Anthony Forge. The focus of the course turned out to be the Highlands of Papua New Guinea, and thus began my interest in the area. A number of lectures and tutorials - as well as the essay topics that they generated - involved theories as to why Highlanders fought. These were interesting questions to contemplate but not so easy to answer because the question of tense was problematic. The literature to which I turned for evidence was written in an ethnographic present of anywhere between the early 1950's and the late 1980's. The early ethnographers wrote of fighting in the past tense and took it for granted that the Highlands had been 'pacified' yet later writers reported fighting in the present tense. -
Principles of Community Engagement (Second Edition) Iv
PRINCIPLES OF COMMUNITY ENGAGEMENT SECOND EDITION Clinical and Translational Science Awards Consortium Community Engagement Key Function Committee Task Force on the Principles of Community Engagement PRINCIPLES OF COMMUNITY ENGAGEMENT SECOND EDITION Clinical and Translational Science Awards Consortium Community Engagement Key Function Committee Task Force on the Principles of Community Engagement NIH Publication No. 11-7782 Printed June 2011 TABLE OF CONTENTS CTSA Community Engagement Key Function Committee Task Force on the Principles of Community Engagement (Second Edition) iv Publication Development ����������������������������������������������������������������������������������������������������������������� vi Foreword ix Executive Summary xiii Chapter 1: C ommunity Engagement: Definitions and Organizing Concepts from the Literature 1 Chapter 2: Principles of Community Engagement ���������������������������������������������������������������������������� 43 Chapter 3: Successful Examples in the Field 55 Chapter 4: Managing Organizational Support for Community Engagement ���������������������������������������91 Chapter 5: Challenges in Improving Community Engagement in Research 107 Chapter 6: The Value of Social Networking in Community Engagement 9 14 Chapter -
Select Board Town Meeting
TOWN OF ARLINGTON MASSACHUSETTS REPORT OF THE SELECT BOARD TO THE TOWN MEETING MONDAY APRIL 26, 2021 8:00 P.M. INTRODUCTION The Select Board is pleased to present its report to Town Meeting of its main motions under the following articles. These votes are the result of hearings the Board conducted between February 22nd and April 5th, during which time the Board heard from proponents and opponents of the various articles. The Board has also included its votes of support for two warrant articles (Articles 38 and 43) that will be presented through the main motions of the Arlington Redevelopment Board. The objective of Select Board Warrant Article Hearings is to develop the Board’s recommendations on each article before it by majority vote, to be set forth with the comments in the Select Board Report in advance of Town Meeting. Where the Board supports taking some action contemplated by an article, regardless of how it appears before the Board, the Select Board, with assistance of Town Counsel, shall develop a motion for Town Meeting to take a specific action. Where the Board opposes an article, it will recommend a vote of “no action” to Town Meeting in its report. The Board would like to welcome back John V. Hurd to serve as Arlington’s newly re- elected member of the Board, and Eric D. Helmuth, our newly elected member. The Board thanks Town Meeting members for their service and for their willingness to give fair and serious consideration to all of the important issues raised by the various articles. -
Uniform Guidance Report 2020
The Trustees of Columbia University in the City of New York Report on Federal Awards in Accordance with OMB Uniform Guidance June 30, 2020 Employer Identification Number 13-5598093 The Trustees of Columbia University in the City of New York Index June 30, 2020 Page(s) Report of Independent Auditors .................................................................................................................. 1 Consolidated Financial Statements Balance Sheets ............................................................................................................................................... 2 Statements of Activities ................................................................................................................................... 3 Statements of Cash Flows .............................................................................................................................. 4 Notes to Financial Statements .................................................................................................................. 5–47 Supplemental Schedules Schedule of Expenditures of Federal Awards.......................................................................................48–540 Notes to Schedule of Expenditures of Federal Awards ..................................................................... 541–542 Schedule of Financial Responsibility Data……………………………………………………………………. 543 Report of Independent Auditors on Internal Control Over Financial Reporting and on Compliance and Other Matters Based on an -
General Index
P PACIFIC ISLANDERS PACKAGES COFA Premium Assistance Program, 735.601, See CONTAINERS AND PACKAGES, generally 735.604, 735.608, 735.611, 735.617 Commercial driving privileges, 807.040, 807.285 PAGEANTS Commission on Asian and Pacific Islander Champoeg Historical Pageant, 186.130 Affairs, see ASIAN AND PACIFIC ISLANDER AFFAIRS, COMMISSION ON, generally Public safety officer eligibility, 181A.055, PAIN 181A.490, 181A.520, 181A.530 Damages, pain and suffering, see DAMAGES Medical care, see MEDICAL CARE AND TREAT- MENT; PAIN MANAGEMENT COMMISSION, PACIFIC NORTHWEST ELECTRIC generally POWER AND CONSERVATION Willful infliction of physical pain, abuse, 124.005, PLANNING COUNCIL 124.050 (Generally), 469.802 et seq. Definitions, 469.802, 469.810 PAIN MANAGEMENT COMMISSION Members (Generally), 413.570 et seq. Appointment, 469.805, 469.820 Chairperson and vice chairperson, 413.576 Conflicts of interest, 469.810 Contributions, acceptance, 413.582 Duties; status as state officials, 469.815 Duties, 413.570, 413.572 Prohibited activities, 469.825 Education programs, health professionals, Public meetings, attendance, 469.815 413.572, 413.590 Removal, 469.830 Meetings, 413.576 413.574 Residence, 469.805 Members, Pain Management Fund, 413.580, 413.582 Salary, 469.835 Rules, 413.599 Term, 469.820 Staffing, 413.570 Northwest Regional Power and Conservation Account, 469.840 Oregon participation, 469.803 PAINE, THOMAS Report, annual, 469.845 Thomas Paine Day, 187.225 PACIFIC NORTHWEST EMERGENCY PAINT MANAGEMENT ARRANGEMENT Architectural paint stewardship program