Naval Applications of Elastomers
Total Page:16
File Type:pdf, Size:1020Kb
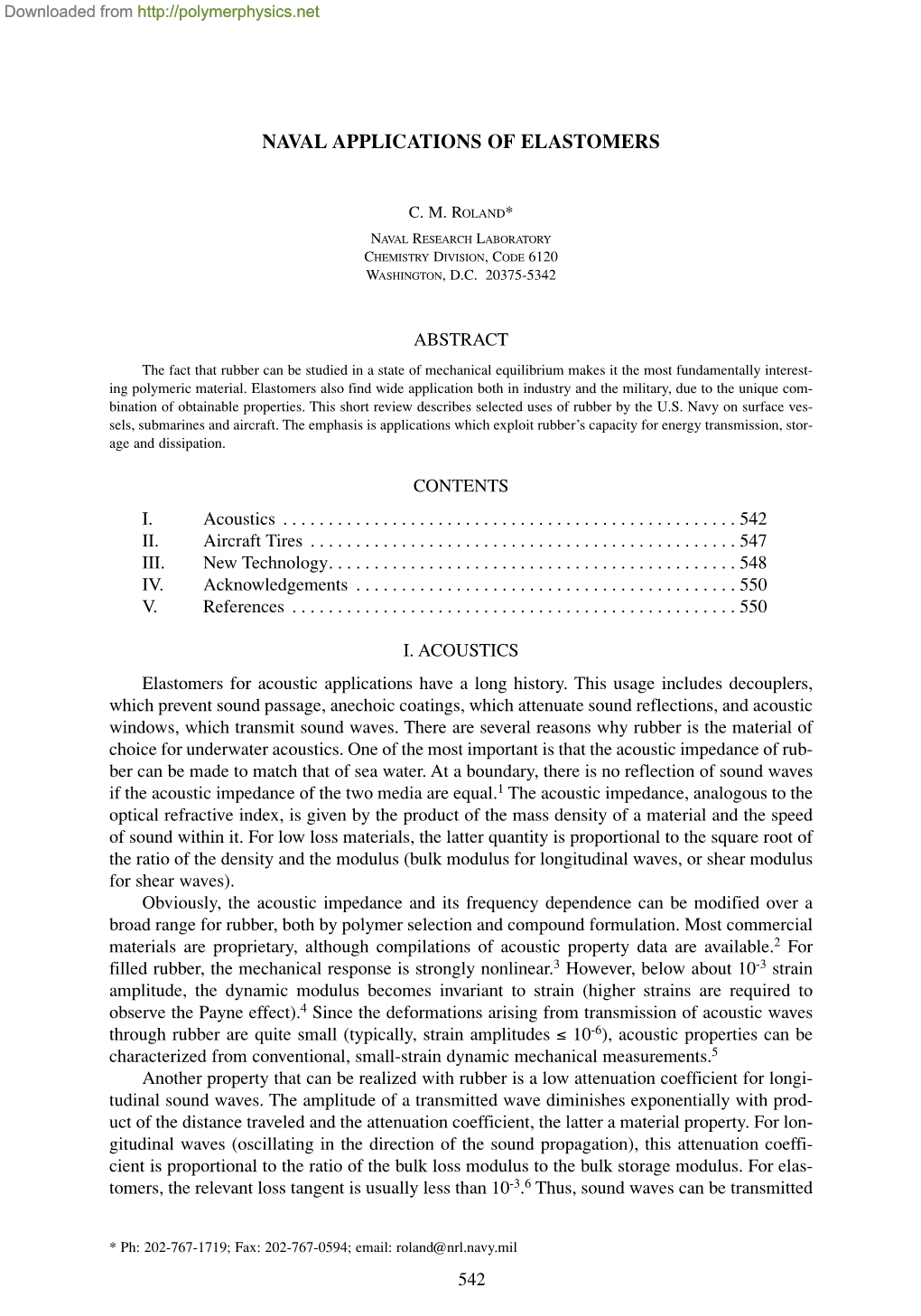
Load more
Recommended publications
-
Latex Free Claims: a White Paper on the Risks Associated with Latex Allergies and Latex in Healthcare
Latex Free Claims: A White Paper on the Risks Associated with Latex Allergies and Latex in Healthcare Brought to you by: Allergy and Asthma Network: Sue Lockwood and Robert Hamilton, M.S., Ph.D. Avella Specialty Pharmacy: Eric Sredzinski, Pharm.D., AAHIVP and Jenna Vaughn, Pharm.D., PGY1 Executive Summary There is significant confusion as to the meaning of “latex free” in healthcare. The FDA has urged manufacturers to drop the term “latex free” or a ”does not contain latex” claim from labels because of the challenge to ensure a product is completely devoid of natural rubber latex proteins which cause the allergic reactions. While there are no regulations requiring the On December 2, labeling of a medical product to state natural rubber latex was not used as a material in the manufacturing process, the terms “latex free” or 2014, the FDA “does not contain latex” are used too broadly. According to the FDA, these labeling techniques are not sufficiently specific, not necessarily scientifically released the accurate, and may be misunderstood and applied too widely. final latex guidance On December 2, 2014, the FDA released the final latex guidance document document advising [https://www.fda.gov/downloads/MedicalDevices/DeviceRegulationandGuidance/ GuidanceDocuments/UCM342872.pdf] advising firms to use “not made with firms to use natural rubber latex” if no natural (Hevea brasiliensis) rubber latex was used in the "not made manufacturing process. Not all types of latex are from natural rubber latex; for example, products that contain nitrile and polyvinyl chloride, will not cause a with natural natural rubber latex allergy because these are synthetic formulations. -
CORALITE MUSCLE JOINT- Camphor Menthol Menthyl Salicylate Patch United Exchange Corp
CORALITE MUSCLE JOINT- camphor menthol menthyl salicylate patch United Exchange Corp. Disclaimer: Most OTC drugs are not reviewed and approved by FDA, however they may be marketed if they comply with applicable regulations and policies. FDA has not evaluated whether this product complies. ---------- Active ingredients Purpose Camphor 1.2%...........................................Topical analgesic Menthol 5.7%.............................................Topical analgesic Methyl Salicylate 6.3%.................................Topical analgesic Uses For temporary relief of minor aches and pains of muscles and joints associated with: arthritis simple backache strains bruises sprains Warnings For external use only Allergy alert: If prone to allergic reaction from aspirin or salicylates, consult a doctor before use. Do not use on wounds or damaged skin with a heating pad if you are allergic to any ingredients of this product When using this product do not use other than directed avoid contact with the eyes, mucous membranes or rashes do not bandage tightly Stop use and ask a doctor if: rash, itching, or excessive skin irritation develops conditions worsen symptoms persist for more than 7 days symptoms clear up and occur again within a few days If pregnant or breast-feeding, ask a health professional before use. Keep out of reach of children. If swallowed, get medical help or contact a Poision Control Center right away. Directions Adults and children 12 years of age and over: clean and dry affected area remove patch from film apply to affected area not more than 3 to 4 times daily remove patch from skin after at most 8 hours of application Children under 12 years of age: consult with a doctor Other information avoid storing product in direct sunlight protect from excessive moisture Inactive ingredients butylated hydroxytoluene, glyceryl rosinate, natural rubber, polybutene, polyisobutylene, precipitated calcium carbonate, quinton, sorbitan stearate, tocopherol acetate, YS resin, zinc oxide DISTRIBUTED BY: UNITED EXCHAGE CORP. -
Rubber Tapping Machine
International Research Journal of Engineering and Technology (IRJET) e-ISSN: 2395-0056 Volume: 07 Issue: 06 | June 2020 www.irjet.net p-ISSN: 2395-0072 Rubber Tapping Machine Mr. Raghavendra Prasad S.A Assistant Professor, Dept. of Mechanical Engineering, St. Joseph Engineering College, Mangalore, Karnataka, India ----------------------------------------------------------------------***--------------------------------------------------------------------- Abstract - A labour has to apply force many times on each 89% of area and 92% of production came from small holding tree to get the desired path for the harvesting of rubber so, this with an average size of 0.50 ha. The total area of natural makes the labour tired and they to do this job for so many rubber cultivation is sub-grouped into traditional (0.53 Mha) trees in a short duration at early morning on every day. This and nontraditional regions, where the traditional regions leads shortage in labour for rubber tapping in India. Hence a have the lion share. The state of Kerala and Kanyakumari motorized concept of tapping knife is needed to reduce their district of Tamil Nadu are the traditional NR cultivating effort. Our proposed machine will satisfy and full fill the above regions, whereas the non-traditional region are in the states problem. The main aim of this project is to rubber tapping in of Maharashtra, Karnataka, Goa , Andhra Pradesh and rubber trees. This equipment is having rack and pinion, Odisha, as classified by RBI [3]. battery, motor arrangement, in the rubber tapping machine. In this project the components are modeled by CREO Software 1.1 Uses & Importance of Rubber and animation also done by CREO software. -
(AMEO) As a Coupling Agent on Curing and Mechanical Properties of Natural Rubber/Palm Kernel Shell Powder Composites
Available online at www.sciencedirect.com ScienceDirect Procedia Chemistry 19 ( 2016 ) 327 – 334 5th International Conference on Recent Advances in Materials, Minerals and Environment (RAMM) & 2nd International Postgraduate Conference on Materials, Mineral and Polymer (MAMIP), 4-6 August 2015 The Effect of 3-aminopropyltrimethyoxysilane (AMEO) as a Coupling Agent on Curing and Mechanical Properties of Natural Rubber/Palm Kernel Shell Powder Composites Shuhairiah Daud, Hanafi Ismail*, Azhar Abu Bakar aSchool of Materials and Mineral Resources Engineering, Engineering Campus, Universiti Sains Malaysia, 14300 Nibong Tebal, Pulau Pinang, Malaysia *Corresponding author:[email protected] Abstract This research is conducted using palm kernel shell powder (PKS) as filler in natural rubber. The effect of 3- aminopropyltrimethoxysilane as coupling agent on composites were studied at different palm kernel shell loading i.e, 0. 5, 10, 15 and 20 phr. The palm kernel shell was crushed and sieved to an average particle size of 5.53 µm. The palm kernel shell filled natural rubber composites were prepared using laboratory size two roll mill. The curing characteristics such as scorch time, cure time and maximum torque were obtained from rheometer. The palm kernel shell powder filled natural rubber composites were cured at 150oC using hot press according to their cure time. Curing characteristics, tensile properties, rubber-filler interaction and morphological properties of palm kernel shell powder filled natural rubber were studied. Scorch time and cure time show reduction but tensile strength, elongation at break, modulus at 100% (M100) and modulus at 300% (M300) increased with the presence of 3-aminopropyltrimethyloxysilane. Rubber-filler interaction studies showed that rubber filler interaction in natural rubber filled with palm kernel shell powder improved with incorporation of 3-aminopropyltrimethyoxysilane. -
Natural Rubber Systems and Climate Change Proceedings and Extended Abstracts from the Online Workshop, 23–25 June 2020
May 2021 FTA WORKING PAPER • 9 Natural rubber systems and climate change Proceedings and extended abstracts from the online workshop, 23–25 June 2020 Salvatore Pinizzotto, Datuk Dr Abdul Aziz b S A Kadir, Vincent Gitz, Jérôme Sainte-Beuve, Lekshmi Nair, Eric Gohet, Eric Penot, Alexandre Meybeck Natural rubber systems and climate change Proceedings and extended abstracts from the online workshop, 23–25 June 2020 The CGIAR Research Program on Forests, Trees and Agroforestry (FTA) Working Paper 9 © 2021 The CGIAR Research Program on Forests, Trees and Agroforestry (FTA) Content in this publication is licensed under a Creative Commons Attribution 4.0 International (CC BY 4.0), http://creativecommons.org/licenses/by/4.0/ DOI: 10.17528/cifor/008029 Pinizzotto S, Aziz A, Gitz V, Sainte-Beuve J, Nair L, Gohet E, Penot E and Meybeck A. 2021. Natural rubber systems and climate change: Proceedings and extended abstracts from the online workshop, 23–25 June 2020. Working Paper 9. Bogor, Indonesia: The CGIAR Research Program on Forests, Trees and Agroforestry (FTA). CGIAR Research Program on Forests, Trees and Agroforestry CIFOR Headquarters Jalan CIFOR Situ Gede, Sindang Barang Bogor Barat 16115 Indonesia T +62-251-8622-622 E [email protected] foreststreesagroforestry.org We would like to thank all funding partners who supported this research through their contributions to the CGIAR Fund. For a full list of the ‘CGIAR Fund’ funding partners please see: http://www.cgiar.org/our-funders/ Any views expressed in this publication are those of the authors. They do not necessarily represent the views of The CGIAR Research Program on Forests, Trees and Agroforestry (FTA), the editors, the authors’ institutions, the financial sponsors or the reviewers. -
Effects of Coconut Coir Powders on the Properties of Natural Rubber Composites
International Jounal of Science and Innovative Technology Volume3 Issue1 January - June 2020 53 Effects of Coconut Coir Powders on the properties of Natural Rubber Composites Teerakorn Kongkaew1,Sureeporn Kumneadklang1, Jate Panichpakdee1 and Siriporn Larpkiattaworn1, * Received May 18, 2020; Revised, June 10, 2020; Accepted June 29 2020 Abstract In this work, the coconut coir powders (CCP)/natural rubber (NR) composites were successfully prepared. The CCP acts as a reinforcing filler with two different sizes of fine powders (39 um) and coarse powders (101 um). The coconut coir powders added to the natural rubber matrix at the filler content of 25, 50, 75, and 100 phr. The effect of CCP contents on physical and mechanical properties was studied. The result revealed that the increase in CCP content has decreased the tensile strength, elongation at break and toughness of composites but increased the modulus of elasticity. The CCP/NR composite at 25 phr of filler loading shows better mechanical properties. For different sizes of fillers, the F-CCP exhibit the better mechanical properties and hardness compare to C-CCP. These properties of composites indicate that it can develop and possible apply in rubber mats. Keywords: Coconut coir powders, Natural rubber, Mechanical properties, Composites Introduction al., 2002; Luz et al., 2007; Panthapulakkal et al., 2006). Polymer composites are a combination of a The natural fibers act as reinforcing natural fillers with polymer matrix with fillers. They have been attractive- biodegradable and renewable properties. The proba- ly applied in industrial and academic researches due bility of natural fibers such as kenaf, sisal, pineapple to the control of the material properties. -
Family Agriculture and the Sustainable Development Issue: Possible Approaches from the African Oil Palm Sector. the Example of Ivory Coast and Cameroon
LES ACTEURS Family agriculture and the sustainable development issue: possible approaches from the African oil palm sector. The example of Ivory Coast and Cameroon 1 Emmanuelle CHEYNS Abstract: Based on the results of studies conducted in Ivory Coast and Cameroon, the article proposes Sylvain RAFFLEGEAU2 an analysis of the family agriculture situation in the oil palm commodity chain, repositioning it within a context of sustainable development issues. At a time when production standards are back on the agenda 1 CIRAD, UR Normes et régulation des marchés, with so-called ″voluntary commitment″ processes, through ″private standards″ to enable sustainable Montpellier, France agriculture, the authors examines the outcome of the previous phases of family agriculture standardi- 2 CIRAD, UR Performance des systèmes de zation by Estates and State-owned companies between 1960 and 1990, followed by privatization of the culture de plantes pérennes / IRAD, La Dibamba, sector. The article shows that family agriculture possesses its own rationality which needs to be taken Cameroon into consideration, if the stakes, over and above guaranteeing ″sustainable oil″, are indeed those of the impact that the palm oil sector has on ″sustainable development″. Starting from that point, the question is no longer: how can family agriculture take on board technical standards designed for other production models, but how can family agriculture take part in the compromises negotiated in the commodity chain in such a way that its logics and operating methods are considered -
“Automated Rubber Tapping Machine”
VISVESVARAYA TECHNOLOGICAL UNIVERSITY Jnana Sangama, Belgavi, Karnataka – 590 014 Project Report on “AUTOMATED RUBBER TAPPING MACHINE” Submitted in partial fulfillment of the requirement for the award of degree of BACHELOR OF ENGINEERING IN MECHANICAL ENGINEERING SUBMITTED BY SAGAR K 1NH14ME109 SREESH S KRISHNA 1NH14ME123 SUSHREETH PUTHRAN 1NH14ME128 SYED ANIES 1NH14ME130 Under the guidance of Mr. SUJEETH SWAMI Asst. Professor, Department of Mechanical Engineering, DEPARTMENT OF MECHANICAL ENGINEERING NEW HORIZON COLLEGE OF ENGINEERING BANGALORE-560 103 2017-18 DEPARTMENT OF MECHANICAL ENGINEERING CERTIFICATE It is certified that the project entitled “AUTOMATED RUBBER TAPPING MACHINE” is work carried out by Sagar K, Sreesh S Krishna,Sushreeth Puthran,Syed Anies, a bonafide student of New Horizon College of Engineering, Bangalore in partial fulfillment for the award of degree of Bachelor of Engineering in Mechanical Engineering of the Visvesvaraya Technological University, Belgaum during the year 2017-18. It is further certified that all corrections/suggestions indicated for internal assessment has been incorporated in the report deposited in the departmental library. The Project Report has been approved as it satisfies the academic requirements in respect of Project Work prescribed for the said degree. Signature of the guide Signature of the HOD Signature of the Principal Mr. SUJEETH SWAMI Dr. M S GANESHA PRASAD Dr. MANJUNATHA Asst. Professor Dean-Student Affairs & HOD-ME, Principal Dept. of Mechanical Engineering, Dept. of Mechanical Engineering, NHCE NHCE NHCE Name(s) of the student: University Seat Number(s): 1. SAGAR K 1NH14ME109 2. SREESH S KRISHNA 1NH14ME123 3. SUSHREETH PUTHRAN 1NH14ME128 4. SYED ANIES 1NH14ME130 External Examiner(s) Signature with Date 1. -
What Is Natural Rubber Latex?
latex allergy latexallergy What is natural rubber latex? NATURAL RUBBER IS A HIGHLY PROCESSED PLANT PRODUCT FROM THE LATEX OF THE COMMERCIAL RUBBER TREE. ABOUT 90% IS PROCESSED FOR MANUFACTURE OF EXTRUDED RUBBER PRODUCTS, MOULDED GOODS OR PNEUMATIC TYRES. The remaining 10% is used for the manufacture of rubber gloves and other dipped products, such as condoms, swimming caps and balloons. Although there are traces of latex allergen in tyre dust, dipped rubber products are responsible for most allergic reactions. What is a latex allergy? A latex allergy is an allergy to products made from natural rubber latex. The allergy-causing particles become attached to the cornstarch powder in gloves, swimming caps and balloons. Moisture from the skin can enhance this process. The particles can become airborne and inhaled when products are used. Sensitized individuals react to these particles. Milk protein is sometimes mixed in with latex in surgical and household gloves and this can be the cause of reactions in milk allergic individuals. Who is at risk of a latex allergy? Adults and children most at risk are those with other allergies such as eczema, asthma and hayfever.Those who have regular contact with natural rubber latex such as powdered gloves or catheters are the most likely to become sensitized. What are the symptoms of a latex allergy? The reactions can be mild and cause rashes on the hands, itchy swollen eyes, runny nose and sneezing.An asthma attack can occur. latex allergy It is also possible to have a severe life threatening allergic reaction (anaphylactic shock).This is occurs when the latex particles come in contact with mucous membranes. -
Restoration & Reparations: Reforming the World's Largest Rubber Company
RESTORATION & REPARATIONS Reforming the world’s largest rubber company With the help of Appui pour la Protection de l’Environnement et le Développement AUGUST 2019 RESTORATION & REPARATIONS Reforming the world’s largest rubber company CONTRIBUTORS TO THIS REPORT Etelle Higonnet, Julian Oram, Patrice Kamkuimo-Piam, Heather Weiss, Margaret Kran-Annexstein Copy editor: Alex Armstrong; translator: Julie Grislain; graphic design: Cecily Anderson, anagramist.com Cover photo: Etelle Higonnet/Mighty Earth ACKNOWLEDGEMENTS The report authors would like to express their gratitude to the following individuals and institutions that provided input or comment on this report: Victorien Mba, Eric Parfait Essomba, Max Mbakop, Rose Armelle, Olinga Andela, Samuel Nguiffo, Alex Armstrong, Liviya James, Glenn Hurrowitz, Abdul Tejan-Cole, Kristin Urquiza, Laurence Gold, MapHubs, Greenpeace Africa, Corrie MacColl. Any errors or inaccuracies remain the responsibility of Mighty Earth. ABOUT MIGHTY EARTH Mighty Earth is a global campaign organization that works to protect lands, oceans, and the climate. We aspire to be the most effective envi- ronmental organization in the world. We have played a leading role in persuading the world’s largest food and agriculture companies to adopt policies to eliminate deforestation, land grabbing and human rights abuses from their supply chains, and driven adoption of multi-billion dollar shifts to clean energy. Mighty Earth is a fiscally sponsored project of the Center for International Policy, a 501(c)3 non-profit organization. -
Epoxidized Natural Rubber for Adhesive Applications
Kasetsart J. (Nat. Sci.) 42 : 325 - 332 (2008) Epoxidized Natural Rubber for Adhesive Applications Rangrong Yoksan ABSTRACT ENR-based adhesives were prepared under the concepts of (i) crosslinking at epoxirane rings and/or (ii) curing at α-carbon positions along the rubber chain. The crosslinking at epoxirane rings was accomplished when two crosslinking agent/catalyst systems, i.e., diamine/bisphenol A and anhydride/ imidazole were used. However, the crosslinking efficiency of the anhydride/imidazole crosslink system was higher than that of the diamine/bisphenol A crosslink system. The curing of ENR at the α-carbon positions was carried out by conventional vulcanization (CV). The mechanical testing of three formulations of ENR-toluene based adhesives, i.e., (i) ENR-PA adhesive, (ii) ENR-S adhesive, and (iii) sulfur cured ENR-PA adhesive showed that ENR-S adhesive gave the highest tensile strength. The fourth formulation of adhesive was, hence, prepared by adding tackifier (resin PX1150) to the ENR-S adhesive (ENR-S-resin PX1150 adhesive). The effect of resin PX1150 on the mechanical properties of ENR-S-resin PX1150 adhesives was studied to find that when the amount of tackifier increased the tensile strength and tensile modulus of the adhesive also increased, while the %elongation at break decreased. Key words: natural rubber, epoxidized natural rubber, phthalic anhydride, adhesive, tackifier INTRODUCTION structure (cis 1,4-polyisoprene), which contains double bonds and hydrocarbon atoms (Figure 1). Natural rubber (NR) is one of the most The chemical modification at double important economic commodities in Thailand bonds and introduction of hydrophilic groups produced from Para rubber tree, Hevea along NR backbone are alternative strategies to brasiliensis. -
Bete~~~~C~~Pe Sdn Bh4 ~~~(120426-A Omd Lot 3342, Jalan Keretapi Lama, 7/2 Mile, Off Jalan Kapar, 42200 Kapar, Selangor Darul Ehsan, West Malaysia
__ !Bete~~~~c~~pe Sdn Bh4 ~~~(120426-A OMd Lot 3342, Jalan Keretapi Lama, 7/2 Mile, OfF Jalan Kapar, 42200 Kapar, Selangor Darul Ehsan, West Malaysia Tel: (603) 3290 3301, (6(3) 3290 3302 Fax: (603) 3290 3303 510K Summary for BETELCARE SDN BHD-Latex Exam gloves Blue Pov lF~Seia~'dciiarinQ' mv it hilel Coln my 1. Submission Applicant: ~0o75t9 9 Name: Betelcare Sdn Bhd Address : Lot 3342,Jalan Keretapi Lama UAR - 5 2008 7.5 Miles Off Jalan Kapar,Kapar Selangor Darul Ehsan West Malaysia Telephone No: 603 3290 3301 Fax No: 603 3290 3303 Email address : kbsiah~betel.com.my Contact Person: K.B .Siah Registration Form 2891 number: 8040910 Device Listing Number : A 653345 Activity : Manufacturer Applicant 510k number: K893166,C047750 2. Device Particulars: Device Name : Powder Free Latex Exam gloves Blue Common Name : Chlorinated Blue Powder Free Latex Exam Gloves Classification: Patient Examination Gloves 3. Device Classification Device Class: Class II Product code: LYY 4. Device Classification Device Class: Class II Product code: LYY 5. Summary of Intended Use A medical gloves is worn on the hand of healthcare and or similar personnel to prevent contamination between healthcare personnel and the patient. ,AAhfI1lAI ANTIl 01pfP(ZfARI P PRflflICTT MANIJFACTTIRFR r~~3 Bteclcre Sin Bhcj (120426-A)[O Lot 3342, Jalan Keretapi Lama. 7½/ Mile, Ofl Jalan Kapar, qE~~Lj 42200 Kapar, Selangor Darul Ehsar, West Malaysia. Tel: (603) 3290 3301, (603) 3290 3302 Fax: (603) 32%0 3303 Email be,!el p.tdiart"gLm 6. Comparison Characteristic: irii betel Characteristic Reference Doc Betel Device performance Water Leak ASTM D 5151-06 Meets or Exceeds Residue Powder ASTM D6124-06 Meets or Exceeds Unaged ASTM D 3578-05 Meets or Exceeds Tensile :-Aged ASTM D 3578 -05 Meets or Exceeds Unaged ASTM D 3578-05 Meets or Exceeds Elongationobreak Unaged ASTM D 3578-05 Meets or Exceeds Aged ASTM D 3578 -05 Meets or Exceeds Extractable Protein Test ASTM D 5712-05el Meets or Excceds The above device does NOT include "hypoallergenic'labelling in packing.