Zžezvere ZOZ 64227Zze Z2
Total Page:16
File Type:pdf, Size:1020Kb
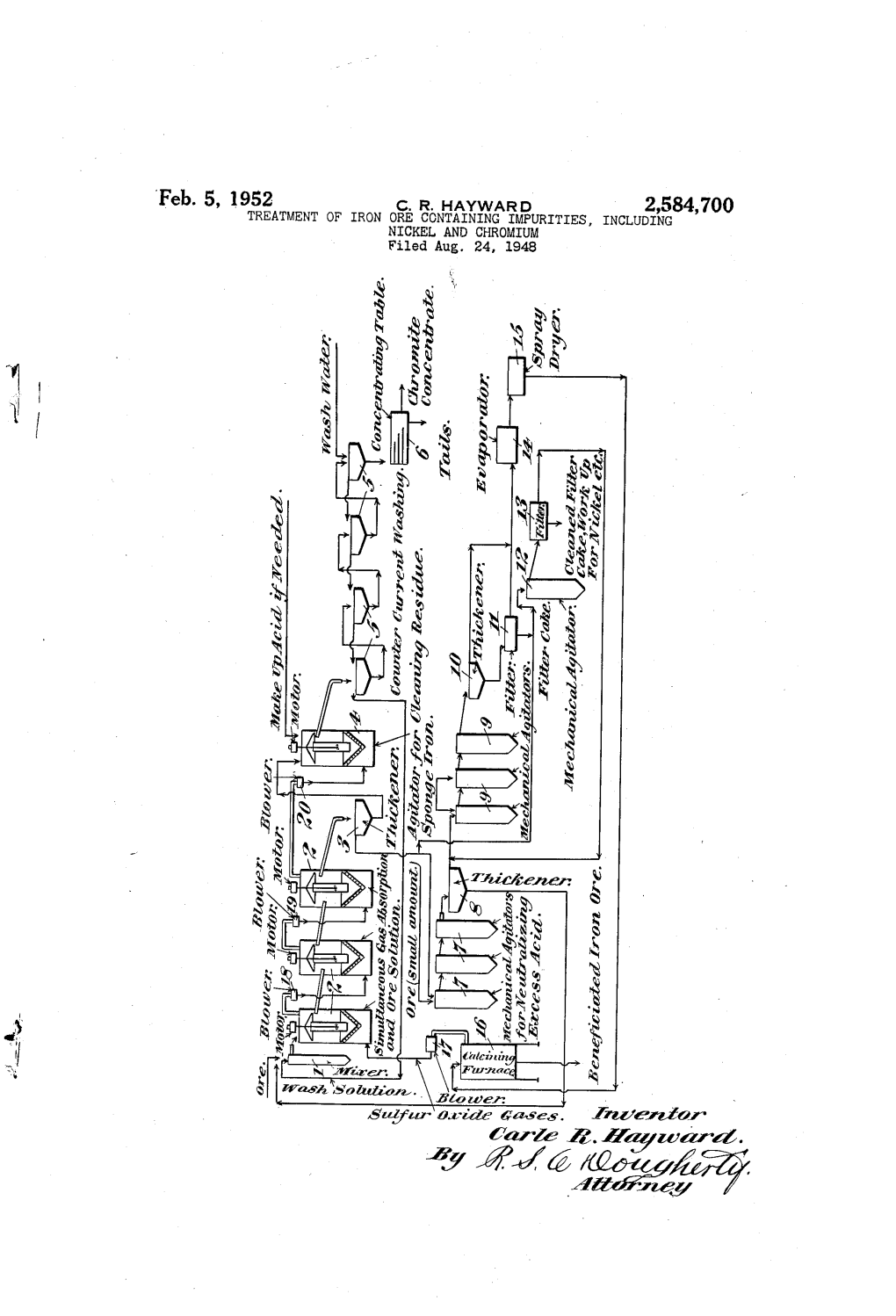
Load more
Recommended publications
-
The Efficient Improvement of Original Magnetite in Iron Ore Reduction
minerals Article The Efficient Improvement of Original Magnetite in Iron Ore Reduction Reaction in Magnetization Roasting Process and Mechanism Analysis by In Situ and Continuous Image Capture Bing Zhao 1,2, Peng Gao 1,2,*, Zhidong Tang 1,2 and Wuzhi Zhang 1,2 1 School of Resources and Civil Engineering, Northeastern University, Shenyang 110819, China; [email protected] (B.Z.); [email protected] (Z.T.); [email protected] (W.Z.) 2 National-Local Joint Engineering Research Center of High-Efficient Exploitation Technology for Refractory Iron Ore Resources, Shenyang 110819, China * Correspondence: [email protected]; Tel.: +86-024-8368-8920 Abstract: Magnetization roasting followed by magnetic separation is considered an effective method for recovering iron minerals. As hematite and magnetite are the main concomitant constituents in iron ores, the separation index after the magnetization roasting will be more optimized than with only hematite. In this research, the mechanism of the original magnetite improving iron ore reduction during the magnetization roasting process was explored using ore fines and lump ore samples. Under optimum roasting conditions, the iron grade increased from 62.17% to 65.22%, and iron recovery increased from 84.02% to 92.02% after separation, when Fe in the original magnetite content increased from 0.31% to 8.09%, although the Fe masses in each sample were equal. For lump ores with magnetite and hematite intergrowth, the method of in situ and continuous image capture Citation: Zhao, B.; Gao, P.; Tang, Z.; for microcrack generation and the evolution of the magnetization roasting process was innovatively Zhang, W. -
Recovery of Magnetite-Hematite Concentrate from Iron Ore Tailings
E3S Web of Conferences 247, 01042 (2021) https://doi.org/10.1051/e3sconf/202124701042 ICEPP-2021 Recovery of magnetite-hematite concentrate from iron ore tailings Mikhail Khokhulya1,*, Alexander Fomin1, and Svetlana Alekseeva1 1Mining Institute of Kola Science Center of Russian Academy of Sciences, Apatity, 184209, Russia Abstract. The research is aimed at study of the probable recovery of iron from the tailings of the Olcon mining company located in the north-western Arctic zone of Russia. Material composition of a sample from a tailings dump was analysed. The authors have developed a separation production technology to recover magnetite-hematite concentrate from the tailings. A processing flowsheet includes magnetic separation, milling and gravity concentration methods. The separation technology provides for production of iron ore concentrate with total iron content of 65.9% and recovers 91.0% of magnetite and 80.5% of hematite from the tailings containing 20.4% of total iron. The proposed technology will increase production of the concentrate at a dressing plant and reduce environmental impact. 1 Introduction The mineral processing plant of the Olcon JSC, located at the Murmansk region, produces magnetite- At present, there is an important problem worldwide in hematite concentrate. The processing technology the disposal of waste generated during the mineral includes several magnetic separation stages to produce production and processing. Tailings dumps occupy huge magnetite concentrate and two jigging stages to produce areas and pollute the environment. However, waste hematite concentrate from a non-magnetic fraction of material contains some valuable components that can be magnetic separation [13]. used in various industries. In the initial period of plant operation (since 1955) In Russia, mining-induced waste occupies more than iron ore tailings were stored in the Southern Bay of 300 thousand hectares of lands. -
Banded Iron Formations
Banded Iron Formations Cover Slide 1 What are Banded Iron Formations (BIFs)? • Large sedimentary structures Kalmina gorge banded iron (Gypsy Denise 2013, Creative Commons) BIFs were deposited in shallow marine troughs or basins. Deposits are tens of km long, several km wide and 150 – 600 m thick. Photo is of Kalmina gorge in the Pilbara (Karijini National Park, Hamersley Ranges) 2 What are Banded Iron Formations (BIFs)? • Large sedimentary structures • Bands of iron rich and iron poor rock Iron rich bands: hematite (Fe2O3), magnetite (Fe3O4), siderite (FeCO3) or pyrite (FeS2). Iron poor bands: chert (fine‐grained quartz) and low iron oxide levels Rock sample from a BIF (Woudloper 2009, Creative Commons 1.0) Iron rich bands are composed of hematitie (Fe2O3), magnetite (Fe3O4), siderite (FeCO3) or pyrite (FeS2). The iron poor bands contain chert (fine‐grained quartz) with lesser amounts of iron oxide. 3 What are Banded Iron Formations (BIFs)? • Large sedimentary structures • Bands of iron rich and iron poor rock • Archaean and Proterozoic in age BIF formation through time (KG Budge 2020, public domain) BIFs were deposited for 2 billion years during the Archaean and Proterozoic. There was another short time of deposition during a Snowball Earth event. 4 Why are BIFs important? • Iron ore exports are Australia’s top earner, worth $61 billion in 2017‐2018 • Iron ore comes from enriched BIF deposits Rio Tinto iron ore shiploader in the Pilbara (C Hargrave, CSIRO Science Image) Australia is consistently the leading iron ore exporter in the world. We have large deposits where the iron‐poor chert bands have been leached away, leaving 40%‐60% iron. -
Smelting Iron from Laterite: Technical Possibility Or Ethnographic Aberration?
Smelting Iron from Laterite: Technical Possibility or Ethnographic Aberration? T. O. PRYCE AND S. NATAPINTU introduction Laterites deposits (orlateriticsoilsastheyarealsocalled)arefrequently reported in Southeast Asia, and are ethnographically attested to have been used for the smelting of iron in the region (Abendanon 1917 in Bronson 1992:73; Bronson and Charoenwongsa 1986), as well as in Africa (Gordon and Killick 1993; Miller and Van Der Merwe 1994). The present authors do not dispute this evidence; we merely wish to counsel cautioninitsextrapolation.Modifyingour understanding of a population’s potential to locally produce their own iron has immediate ramifications for how we reconstruct ancient metal distribution net- works, and the social exchanges that have facilitated them since iron’s generally agreed appearance in Southeast Asian archaeological contexts during the mid-first millennium b.c. (e.g., Bellwood 2007:268; Higham 1989:190). We present this paper as a wholly constructive critique of what appears to be a prevailingperspectiveonpre-modernSoutheastAsianironmetallurgy.Wehave tried to avoid technical language and jargon wherever possible, as our aim is to motivate scholars working within the regiontogivefurtherconsiderationtoiron as a metal, as a technology, and as a socially significant medium (e.g., Appadurai 1998; Binsbergen 2005; Gosden and Marshall 1999). When writing a critique it is of course necessary to cite researchers with whom one disagrees, and we have done this with full acknowledgment that in modern archaeology no one person can encompass the entire knowledge spectrum of the discipline.1 The archaeome- tallurgy of iron is probably on the periphery of most of our colleagues’ interests, but sometimes, within the technical, lies the pivotal, and in sharing some of our insights we hope to illuminate issues of benefit to all researchers in Metal Age Southeast Asia. -
ITP Mining: Energy and Environmental Profile of the U.S. Mining Industry: Chapter 4: Iron
Energy and Environmental Profile of the U.S. Mining Industry 4 Iron The chemical element iron is the fourth most common element in the Earth's crust and the second most abundant metal. About five percent of the Earth's crust is composed of iron. The metal is chemically active and is found in nature combined with other elements in rocks and soils. In its natural state, iron is chemically bonded with oxygen, water, carbon dioxide, or sulfur in a variety of minerals. Forms of Iron Minerals, Ores, and Rocks Iron occurs mainly in iron-oxide ores. Some ores are a mixture of minerals rich in iron. Other iron ores are less rich and have a large number of impurities. The most important iron ore- forming minerals are: • Magnetite - Magnetite (Fe3O4) forms magnetic black iron ore. There are large deposits of magnetite in Russia and Sweden. • Hematite - Hematite (Fe2O3) is a red iron ore. Hematite occurs in almost all forms, from solid rock to loose earth. It is the most plentiful iron ore and occurs in large quantities throughout the world. • Goethite - Goethite (Fe2O3.H2O), a brown ore, contains iron. • Limonite - Limonite (Fe2O3.H2O) is a yellow-brown iron ore. Limonite is a collective term for impure goethite and a mixture of hydrated iron oxides. Iron 4-1 Energy and Environmental Profile of the U.S. Mining Industry Taconite contains low-grade iron in fine specks and bands. It is an extremely hard and flinty - containing about 25 - 30 percent iron. The iron in taconite occurs principally as magnetite and hematite and finely dispersed with silica in sedimentary deposits. -
Conservation and Systematic Development of Iron
1 PART : II INTRODUCTION CONSERVATION (PRESERVATION) AND SYSTEMATIC DEVELOPMENT OF IRON ORE One of the species of National Wealth is iron ore. Conservation of this mineral is of prime importance for industrial development. Indian legislature has recognized it in Section: 18 of the Mines & Minerals (Development & Regulation) Act, 1957. Section : 18, inter-alia, directs the Central Government to take all such steps as may be necessary for: (a) the conservation (Preservation) (b) and systematic development of minerals in India Systematic development of minerals in India would require: (a) exact estimate of reserves available (b) reasonable estimate of resources from where probable reserves can be estimated. This, inter–alia, would require opening of new mines. For that purpose, exploration is necessary. 2 For this, it would be worthwhile to refer to: A (REPORTS FOR EXPLORATION) (i) DOCUMENT ON STRATEGY FOR EXPLORATION, EXPLOITATION AND DEVELOPMENT FOR IRON ORE IN INDIA, PUBLISHED BY THE SUB–GROUP ON IRON ORE in India (January, 2006) (ii) MINERAL POLICY ISSUES IN THE CONTEXT OF EXPORT AND DOMESTIC USE OF IRON ORE IN INDIA - REPORT - FEBRUARY 2008 (INDIAN COUNCIL FOR RESEARCH ON INTERNATIONAL ECONOMIC RELATIONS) (iii) ECONOMICS OF SPONGE IRON AND STEEL PRODUCTION (SEPTEMBER, 2008) BY STEEL AND NATURAL RESOURCES STRATEGY RESEARCH, VASANT KUNJ, NEW DELHI (iv) IRON ORE – STATUS AND FUTURE PROSPECTS” by M. S. Jairam, Director, Geological Survey of India (v) IBM REPORT, 2009, AND PROVISIONAL FIGURES, AS ON 1-4-2010, SUPPLIED BY IBM, FOR IRON ORE 3 B (ILLEGAL MINING) (vi) 19TH REPORT OF STANDING COMMITTEE ON COAL & STEEL which highlights menace of illegal mining. -
Sustainable Underground Iron Ore Mining in Ukraine with Backfilling Worked-Out Area
sustainability Review Sustainable Underground Iron Ore Mining in Ukraine with Backfilling Worked-Out Area Oleg Bazaluk 1,* , Mykhailo Petlovanyi 2 , Vasyl Lozynskyi 2,* , Serhii Zubko 3, Kateryna Sai 2 and Pavlo Saik 2 1 Belt and Road Initiative Centre for Chinese-European Studies, Guangdong University of Petrochemical Technology, Maoming 525000, China 2 Department of Mining Engineering and Education, Dnipro University of Technology, 49005 Dnipro, Ukraine; [email protected] (M.P.); [email protected] (K.S.); [email protected] (P.S.) 3 PJSC Zaporizhzhia Iron-ore Plant, 69061 Zaporizhzhia, Ukraine; [email protected] * Correspondence: [email protected] (O.B.); [email protected] (V.L.) Abstract: The present paper considers aspects of underground iron ore mining in Ukraine, in par- ticular the level of mine production and reserves of basic ore fields. It analyzes and generalizes the practice of using cemented rockfill under difficult mining and hydrogeological conditions of the Pivdenno-Bilozerske high-grade iron ore field. The Belozersky iron ore district is the only one in Ukraine that, without any technological cycle of beneficiation, can provide both domestic and foreign consumers with high-quality raw iron ore as required by world markets. The PJSC Zaporizhzhia iron ore plant extracts iron ore from the Pivdenno-Bilozerske field with an iron content of more than 60% using the low-waste, environmentally friendly technology of backfilling the mined-out area with a hardening mixture. The peculiarities of the technology for steep deposit mining and the main processes of backfilling operations in terms of preparation, transportation, and construction of the backfill mass with its stability assessment are explained in detail in this paper. -
The Iron-Ore Resources of Europe
DEPARTMENT OF THE INTERIOR ALBERT B. FALL, Secretary UNITED STATES GEOLOGICAL SURVEY GEORGE OTIS SMITH, Director Bulletin 706 THE IRON-ORE RESOURCES OF EUROPE BY MAX ROESLER WASHINGTON GOVERNMENT PRINTING OFFICE 1921 CONTENTS. Page. Preface, by J. B. Umpleby................................................. 9 Introduction.............................................................. 11 Object and scope of report............................................. 11 Limitations of the work............................................... 11 Definitions.........................:................................. 12 Geology of iron-ore deposits............................................ 13 The utilization of iron ores............................................ 15 Acknowledgments...................................................... 16 Summary................................................................ 17 Geographic distribution of iron-ore deposits within the countries of new E urope............................................................. 17 Geologic distribution................................................... 22 Production and consumption.......................................... 25 Comparison of continents.............................................. 29 Spain..................................................................... 31 Distribution, character, and extent of the deposits....................... 31 Cantabrian Cordillera............................................. 31 The Pyrenees.................................................... -
1 Review and New Data from Wadi Kareim 2
1 Petrological and Geochemical Characteristics of Egyptian Banded Iron Formations: 2 Review and New Data from Wadi Kareim 3 4 K. I. Khalil1, and A. K. El-Shazly2* 5 6 1 Geology Department, Faculty of Science, University of Alexandria, Moharram Bey, Alexandria, 7 Egypt 8 2 Geology Department, Marshall University, 1 John Marshall Dr., Huntington, WV 25755 9 10 *Corresponding Author (e-mail: [email protected]). 11 12 # of words in text: 8307 13 # of words in references: 2144 14 15 Abbreviated title: Egyptian BIFs 16 17 Abstract 18 19 The banded iron formations in the eastern desert of Egypt are small, deformed, bodies 20 intercalated with metamorphosed Neoproterozoic volcaniclastic rocks. Although the 13 21 banded iron deposits have their own mineralogical, chemical, and textural characteristics, 22 they have many similarities, the most notable of which are the lack of sulfide and paucity of 23 carbonate facies minerals, a higher abundance of magnetite over hematite in the oxide 24 facies, and a well-developed banding/ lamination. Compared to Algoma, Superior, and 25 Rapitan type banded iron ores, the Egyptian deposits have very high Fe/Si ratios, high Al2O3 26 content, and HREE-enriched patterns. The absence of wave-generated structures in most of 27 the Egyptian deposits indicates sub-aqueous precipitation below wave base, whereas their 28 intercalation with poorly sorted volcaniclastic rocks with angular clasts suggests a 29 depositional environment proximal to epiclastic influx. The Egyptian deposits likely formed in 30 small fore-arc and back-arc basins through the precipitation of Fe silicate gels under slightly 31 euxinic conditions. -
It's Mine! Odisha Auction in Focus
It’s mine! Odisha auction in focus Iron ore cost set to rise 30-40% for non-integrated players after the auction – in a Karnataka redux January 2020 The steel sector, which had seen its fortunes revive in the last two fiscals, appears to be headed for a sturm und drang phase again. Disruptions in mines, elevated inventory levels and high bid premiums in the recent auctions in Karnataka pose hiccups on the supply side even as dampeners abound on the demand side, too. In the context, even the upcoming mine auctions in Odisha are expected to see high bid premiums. The fallout – a mighty blow to non-integrated steelmakers. Indeed, around 76% of domestic crude steel capacity, which procures from the merchant iron ore market, is expected to be impacted directly. In a possible scenario of downward rally of global iron ore prices, steelmakers (especially port-based) can potentially consider imports. However, given that domestic prices are typically at a 55-60% discount to imported prices, profitability of non-integrated steelmakers is expected be under pressure in the two fiscals following the Odisha auctions. That said, improving realisations and declining coal prices should provide some relief. Leases for 30% of India’s, and half of Odisha’s production to expire soon After the amendment of the Mines and Minerals (Development and Regulation) Act (MMDR Act), 24 iron ore blocks/mines with estimated reserves of ~640 million tonne of iron ore have been auctioned in the past three years (up to November 19). Of these, 18 in Karnataka with reserves of more than 330 million tonne of iron ore have already been auctioned. -
Western Australia's Emerging Magnetite Iron Ore Industry The
Western Australia’s Emerging Magnetite Iron Ore Industry The Case for Exemption of Magnetite from the MRRT Presentation to the Senate Select Committee 8 November 2010 Megan Anwyl, Director, Magnetite Network [email protected] Phone 08 9214 3836 1 Summary • Magnetite has minimal value as raw ore – requires massive beneficiation before it is saleable to the steel industry; •Similar beneficiation process to copper, gold, bauxite and nickel; • Taxation of fledgling industry is contrary to policy intent; •Hard to calculate value of raw ore; • Huge public/private compliance burden; and • Capital intensive downstream processing provides jobs, regional development and infrastructure. 2 Definition of Ore and Beneficiation • Main ores of iron - hematite ( Fe2O3 ) and magnetite ( Fe3O4 ) • Most magnetic of all naturally occurring minerals • Requires much more sophisticated and extensive processing – exported as concentrate or pellets • Magnetite is produced extensively in China, Canada, Brazil and the United States of America and has been for decades • Magnetite is an attractive blast furnace feedstock for many reasons including lower greenhouse gas emissions • Currently only Grange Resources at Savage River and OneSteel at Whyalla Direct Shipping Ores cf Concentrates • Most of the world’s large “direct shipping” iron ore deposits derive from the natural enrichment of banded iron formations – BIF comprises sediment bands rich in iron oxides (usually magnetite) alternating with bands high in silicates. • Natural enrichment processes remove silica and replace with iron oxides – supergene enrichment – burial metamorphism – hypogene enrichment – channel iron deposits • As mined “direct shipping ore” is high in iron and low in silica – Large DSO deposits are rare and uniquely valuable (e.g. -
Metal Smelting and Refining Sources of Cdd/Cdf
7. METAL SMELTING AND REFINING SOURCES OF CDD/CDF 7.1. PRIMARY NONFERROUS METAL SMELTING/REFINING Little information has been published on the potential for the formation and environmental release of CDD/CDFs from primary nonferrous metal manufacturing facilities. Norwegian investigators (Oehme et al., 1989) have reported the presence of CDD/CDFs in the wastewater of a magnesium refining facility and in the receiving water sediments downstream of a nickel refining facility in Norway. Insufficient information is available from this study for evaluating CDD/CDF emissions, if any, from the smelting/refining of magnesium and nickel in the United States. The potential for formation and release of CDD/CDFs by primary copper smelters in the United States has been reported by Environmental Risk Sciences (1995) to be negligible. Lexen et al. (1993) reported finding few or no CDD/CDFs in solid wastes from a primary aluminum smelter. Bramley (1998) indicated that the smelting/refining of titanium may be a source of CDD/CDFs. The findings of these studies are discussed in the following subsections. 7.1.1. Primary Copper Smelting and Refining Environmental Risk Sciences (1995) prepared an analysis for the National Mining Association on the potential for CDD/CDF emissions from the primary copper smelting industry. The analysis included reviewing the process chemistry and technology of primary copper smelting, identifying operating conditions, and comparing process stream compositions from seven of the eight U.S. primary copper smelters that are members of the National Mining Association. The analysis also included stack testing for CDD/CDFs at two facilities. The stack testing (Secor International Inc., 1995a and 1995b) involved the principal off-gas streams for copper smelters: main stack, plant tail gas stack, and the vent fume exhaust.