Lvl) Having Different Patterns of Assembly
Total Page:16
File Type:pdf, Size:1020Kb
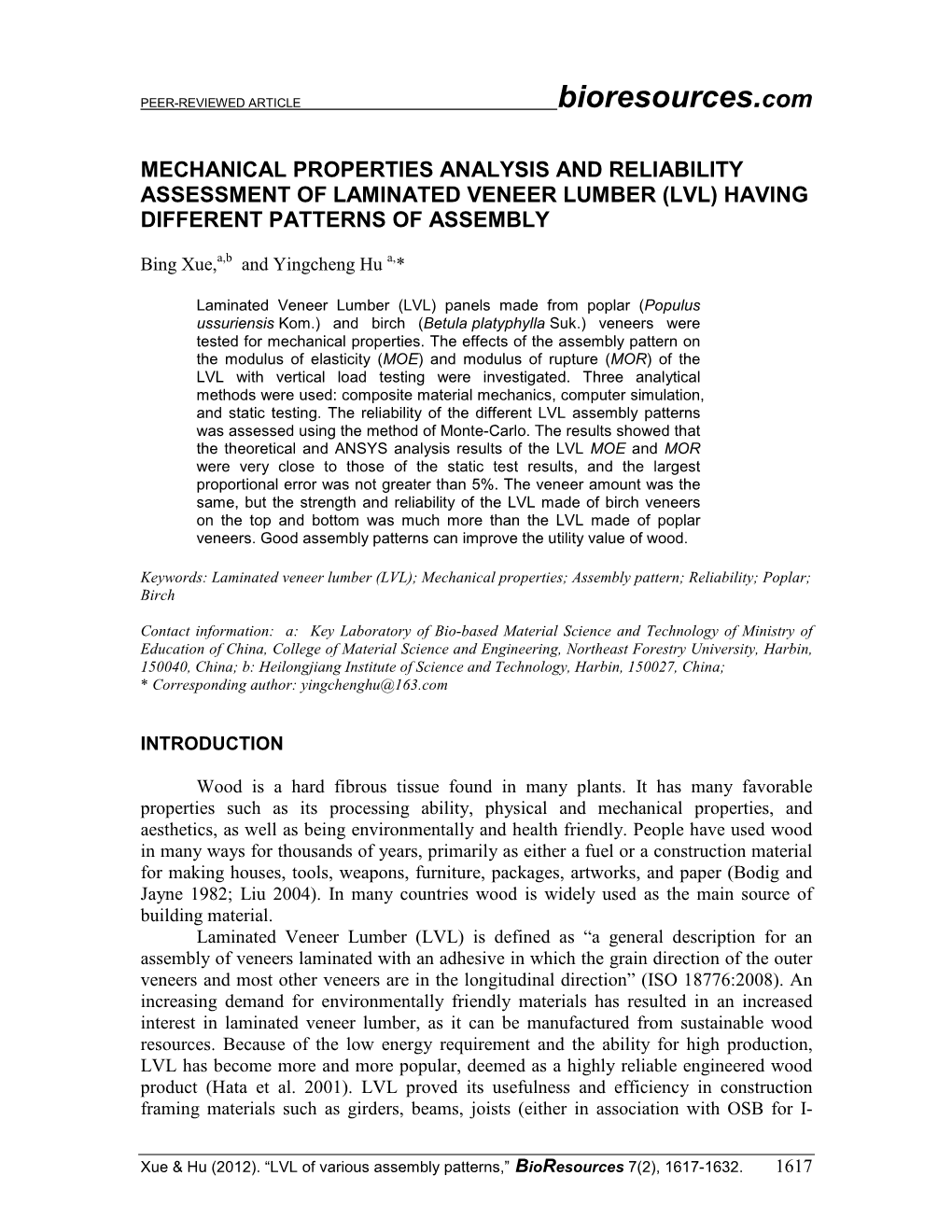
Load more
Recommended publications
-
Big Trees in the Southern Forest Inventory
United States Department of Big Trees in the Southern Agriculture Forest Inventory Forest Service Southern Christopher M. Oswalt, Sonja N. Oswalt, Research Station and Thomas J. Brandeis Research Note SRS–19 March 2010 Abstract or multiple years. Listings of big trees encountered during the most recent forest inventory activities in the South Big trees fascinate people worldwide, inspiring respect, awe, and oftentimes, even controversy. This paper uses a modified version of are reported in this research note and should supplement American Forests’ Big Trees Measuring Guide point system (May 1990) existing lists and registers. to rank trees sampled between January of 1998 and September of 2007 on over 89,000 plots by the Forest Service, U.S. Department of Agriculture, For more than 75 years, the FIA Program has been charged Forest Inventory and Analysis Program in the Southern United States. Trees were ranked across all States and for each State. There were 1,354,965 by Congress to “make and keep current a comprehensive trees from 12 continental States, Puerto Rico, and the U.S. Virgin Islands inventory and analysis of the present and prospective sampled. A bald cypress (Taxodium distichum) in Arkansas was the biggest conditions of and requirements for the renewable resources tree (according to the point system) recorded in the South, with a diameter of the forest and rangelands of the United States” of 78.5 inches and a height of 93 feet (total points = 339.615). The tallest tree recorded in the South was a 152-foot tall pecan (Carya illinoinensis) in (McSweeney-McNary Act of May 22, 1928. -
This File Was Created by Scanning the Printed
Eur. J. Wood Prod. (2012) 70:37-43 DOl 1O.1007/s00107 -0 10-0494-y OSB as substrate for engineered wood flooring Costel Barbuta . Pierre Blanchet· Alain Cloutier· Vikram Yadama . Eini Lowell Received: 26 August 2009 / Published online: 13 November 2010 © Springer-Verlag 2010 Abstract Oriented strand board (OSB) is a commodity sheathing, OSB web stock and ponderosa pine OSB sub product subject to market fluctuation.Development of a spe strates showed higher distortion. The PYA type I adhesive cialty OSB could lead to a better, and more stable, market led to weak bonding with high-density OSB surface.The re segment for OSB. It was demonstrated in a previous study sults of this study demonstrate the potential of OSB panels (Barbuta et al. in Eur. 1. Wood Prod. 2010), that OSB may to be used as substrate for EWF. be designed to obtain a high bending modulus of elasticity in the parallel direction, close to Baltic Birch Plywood (BBP) OSB als Tragerplatte ffir Doppelboden in its strongest direction. This study focused on the use of such specialty OSB in the manufacturing of engineered Zusammenfassung OSB ist ein Massenprodukt, das wood flooring (EWF) prototypes,a product that widely uses Marktschwankungen unterliegt. Die Entwicklung spezieller BBP as substrate in Canada. The performance of these two OSB-Platten konnte zu besseren und stabileren Absatzmog prototypes (aspen/birch and ponderosa pine) was studied. lichkeiten flir OSB flihren. In einer frliherenStudie (Barbuta Five types of substrates: BBP, sheathing OSB, web stock et al. Eur. J. Wood Prod. 20 I 0) wurde die Moglichkeit auf OSB and the two specialty OSB prototypes were used to gezeigt, OSB herzustellen, dessen Biege-Elastizitatsmodul manufacture EWF. -
Mid-Rise Engineering Considerations for Engineered Wood Products
Mid-Rise Engineering Considerations for Engineered Wood Products PresentedPresented by [ byPresenter’s Jeff Olson, Name ]P.E. Please add relevant logo here Disclaimer: This presentation was developed by a third party and is not funded by WoodWorks or the Softwood Lumber Board. “The Wood Products Council” is a This course is registered with AIA CES Registered Provider with The for continuing professional education. American Institute of Architects As such, it does not include content Continuing Education Systems that may be deemed or construed to (AIA/CES), Provider #G516. be an approval or endorsement by the AIA of any material of Credit(s) earned on completion of this construction or any method or course will be reported to AIA CES for manner of handling, using, AIA members. Certificates of distributing, or dealing in any Completion for both AIA members material or product. and non-AIA members are available upon request. ______________________________ Questions related to specific materials, methods, and services will be addressed at the conclusion of this presentation. Course Description Wood products take on a seemingly infinite variety of shapes and forms. While many designers are familiar with engineered wood products such as I-joists, wood sheathing and structural composite lumber, it is important to understand the structural requirements associated with each in order to achieve proper performance—especially in mid-rise applications. With an emphasis on products used in commercial and multi-family buildings, this presentation will cover fastening requirements, load capacity and proper detailing. Learning Objectives 1. Dimension stability in regards to moisture content changes and the differences between solid wood products. -
Veneer Guidelines 1
V T INDUSTRIES VENEER GUIDELINES 1 VTWO O D VENEERS PLAN I SLICED NATURAL MAPLE N ATURAL VARIATIONS The word natural brings to mind certain connotations like “beauty”, “warmth” and “purity”. Merriam-Webster defines natural as “occurring in conformity with the ordinary course of nature (the genetically controlled qualities of an organism): not marvelous or supernatural”. Wood is a product of nature, and in some cases, will accentuate and enhance a project design when used in its purest, or natural, state. However, as a product of nature, each wood species has certain intrinsic and industry-acceptable characteristics, which can vary from tree to tree and flitch (half log) to flitch. It is precisely these naturally occurring variations that provide such richness and uniqueness to each project design. Certain wood species such as natural maple and birch can vary widely in color range, which is why in many cases select white is specified so that the sapwood can be accumulated and spliced together to create a consistent color. The photos and information in this brochure are designed to assist you in specifying and receiving the product you envision. When specifying "natural" maple and birch, the veneer will contain unlimited amounts of Sapwood (the light portion of the log) and/or Heartwood (the dark portion of the log) unselected for color. If a light colored veneer is preferred, specify Select White (all Sapwood) maple or birch. If a dark colored veneer is preferred, specify Select Red/Brown (all Heartwood) Note, availability may be limited. 2 VTWO O D VENEERS PLAN I SLICED SELECT WHITE MAPLE HO W TO SPECIFY Natural veneers, such as maple and birch, may contain sapwood/ heartwood combinations, color streaks, spots and color variation from almost white to very dark. -
External Timber Quality of Birch in Birch-Spruce Mixtures
External timber quality of birch in birch-spruce mixtures Fredrik Hörnsten Supervisor: Emma Holmström, SLU Southern Swedish Forest Research Centre Swedish University of Agricultural Sciences Master Thesis no. 300 Southern Swedish Forest Research Centre Alnarp 2018 External timber quality of birch in birch-spruce mixtures Fredrik Hörnsten Supervisor: Emma Holmström, SLU Southern Swedish Forest Research Centre Examiner: Eric Agestam, SLU Southern Swedish Forest Research Centre Swedish University of Agricultural Sciences Master Thesis no. 300 Southern Swedish Forest Research Centre Alnarp 2018 MSc Thesis in Forest Science – Jägmästarprogrammet SY001 Advanced level (A2E), SLU course code EX0838, 30ECTS Abstract The Swedish forest management model, largely based on monocultures of conifer species, has increasingly come under scrutiny. Its disadvantages to biodiversity, recreation and climate change susceptibility incentivize alternative ways of forest production. Mixtures with a secondary species is one such alternative. Birch and spruce, two species native to Sweden, are well-known to function together. Mixtures of the two exist today already, although the species are usually treated with different goals in mind. Further encouragement of forest owners is necessary for the practice to become more widespread. This thesis attempts to reflect upon whether naturally regenerated birch in birch-spruce mixtures have a high enough timber quality to make the birch valuable from an economic perspective. The aim of the study was therefore to assess external timber quality of naturally regenerated birch in birch-spruce mixtures in southern Sweden. The hypotheses to be addressed was a) that naturally regenerated birch trees in Norway spruce plantations fulfill the requirements for high quality saw timber and b) that the quality of the future crop trees of birch is lower when the surrounding competition is of Norway spruce instead of other birches. -
Walk with Larch Trails Upland Young Forest Trail 0.8 Mi
Walk With Larch Paths Through an Ever-Changing Forest Coram Experimental Forest Raymond C. Shearer E. Donald Kiehn Mushroom and larch needle, Upland Trail, Stop 2. Above: Upland Trail, Stop 5. Left: Upland Trail, Stop 4. U.S. Department of Agriculture Forest Service Rocky Mountain Research Station Above: Upland Trail, Stop 7. Walk With Larch, a Continuing Adventure As you return to the parking area, consider what you have seen. You may have unanswered questions—so do we. That is why research continues here and elsewhere on the Coram Experimental Forest. Answers will come in the future, but usually every answer raises more questions. Puzzler Clues—as you read this brochure, we hope you kept track of the underlined letters. One vital letter is still missing. Here are clues to its identity, as well as to the key concept of the mystery word itself: in forests Above: Upland Trail, Stop 6. there are no beginnings and no ends, all parts and Left: Riparian Trail, Stop 4. processes are interconnected, always in transition, forever cycling, a continuous circle of mysteries! The mystery word is: __ __ __ __ __ __ __ __ __ __ Photo Credits: R. Steven Wirt and Raymond C. Shearer Cover: Life cycle of larch. 200 year old larch. Insets: cone dispersing seeds; first year seedling; and 42-year-old pole-size trees. The U.S. Department of Agriculture (USDA) prohibits discrimination in all its programs and activities on the basis of race, color, national origin, sex, religion, age, disability, political beliefs, sexual orientation, or marital or family status. -
Metsä Wood Birch Plywood Products
METSÄ WOOD BIRCH PLYWOOD PRODUCTS CONTENTS Birch, Birch L ............................... .2-3 Birch XL ................................... .4-5 KingSize ................................... .6-7 Deck, Deck L .............................. .8-10 Deck XL .................................. 11-12 Floor, Floor L .............................. 13-14 Form, Form L .............................. 15-17 FormPLUS ............................... 18-20 Form XL ..................................21-23 Top, Top L ................................ 24-25 Integra .................................. 26-28 SP ...................................... 29-30 Granit, Granit L ........................... .31-32 Laser .................................... 33-34 Flex ..................................... 35-36 Flex L.................................... 37-38 Flex Smooth .............................39-40 Flex XL .................................. 41-42 Sonex Light .............................. 43-44 Phoenix.................................. 45-46 Metsä Wood Birch is a high-quality Finnish plywood product sanded on both sides. Birch plywood can be used for a wide range of applications. Metsä Wood Birch is available in various sizes: standard, L, XL and KingSize. Base plywood Metsä Wood Birch plywood is made of cross-bonded 1.4 mm thick birch veneers bonded with weather- and boil-resistant phenol formaldehyde Applications adhesive. Metsä Wood Birch is a multipurpose panel for different uses where Designed and tailor-made to serve in demanding applications, birch a strong -
Paper Birch and Fireweed Stand Establishment Decision Aids
Extension Note CONDENSED TITLE BC Journal of Ecosystems and Management British Columbia’s Coastal Forests Paper Birch and Fireweed Stand Establishment Decision Aids Brian D’Anjou1 and Jennifer Turner2 Introduction The Coastal Western Hemlock submaritime biogeoclimatic subzones (cwhds1 and ds2) occur in the inland valleys of coastal British Columbia, where the climate is commonly transitional between the province’s coastal and interior regions. Vegetation management issues in these subzones include species such as fireweed (Epilobium angustifolium) and paper birch (Betula papyrifera). On wetter, rich sites of the cwh zone, management options for other vegetation (e.g., salmon- berry, devil’s club, and elderberry) are well documented; however, little research has focussed on the competing species found primarily in the submaritime British Columbia subzones. A field guide for the region (Green and Klinka 1994) lists a number of vegetation concerns for the cwh’s submaritime subzones. Practitioners, however, have identified a need for more information about paper birch and fireweed. The vegeta- tion management Stand Establishment Decision Aids (sedas) included in this extension note are designed to fill this gap. Although initially developed to address the needs of coastal managers, much of the information presented here can be ap- plied to other areas of the province experiencing similar issues related to successful conifer regeneration. Most of the con- tent was adapted from previously published information on paper birch and fireweed management in the former Cariboo Forest Region (Swift and Turner 2002). The majority of the information provided for paper birch emanates from research conducted in the province’s southern interior (Simard 1996; Simard and Henigman 1996), where birch is well distributed and can affect crop tree regeneration and survival. -
The Chestnut Oak Forests of the Anthracite Region
STATION PAPER Ne.9 SEPTEMBER 1947 . THE CHESTNUT OAK FORESTS OF THE ANTHRACITE REGION by C. Burnham M.J. Ferree E E. Cunningham t U.S. Depurtm ent of Ag r~culture Forest Service Northeastern Forest Experiment Station Bonkers Securities Building t Philadelphia 7, Pa. K L. Horper, Director This paper is a progress report of forest research in the Anthracite Region by personnel of the Station's branch at Kingston, Pa. It is the sixth in a series of seven reports dealing with the principal forest types of the Anth- racite Region. The previous reports are: \ 1. The Northern Hardwood Forests of the Anthracite Region. Station Paper 1, issued in March 1947. 2. The Red Oak - White Oak Forests of the Anthracite Region. Station Paper 2, issued in May 1947. 3. The Scrub Oak Forests of the Anthracite Region. Station Paper 4, issued in June 1947. 4. The Aspen - Gray Birch Forests of the Anthracite Region. % Station Paper 7, issued in August 1947. 5. The White Pine - Oak Forests of the Anthracite Region. Station Paper 8, issued in August 1947. The seventh in the series will deal with the white pine - hemlock forests. This paper presents data on the condition of the for- ests in the chestnut oak type, and recommendations for improving such forests. The recommendations are only tent- ative; but they should serve as a useful guide until more precise and refined information is available. The authors thank the many landowners on whose prop- erty the. sample plots were established; the personnel of the Industrial Forestry Division of the Wyoming Valley Chamber of Commtsrce, for their advice and assistance; and the many other individuals who have shown a desire to help solve the forest problems of the Anthracite Region. -
BIRCH RIDGE POND the Lower Pond in the Series Is Located on the Outlet 1/8 Mile T-A R11, Piscataquis Co
BIRCH RIDGE POND The lower pond in the series is located on the outlet 1/8 mile T-A R11, Piscataquis Co. below Birch Ridge Pond. It is an old beaver flowage. The water' U.S.G.S. Jo-Mary Mountain, Me. is quite shallow, and emergent aquatic vegetation is present throughout the pond. Fishes Birch Ridge Pond is accessible only by foot trail. A hike of Brook trout (squaretail) Minnows more than 112 mile through an old burn, now forested by birch Lake ch ub and poplar, is required to reach it. The pond will be managed Finescale dace for its wild brook trout population. The existing fly fishing only, five-fish daily bag limit restrictions should maintain ~he Physical Characteristics quality of the wild brook trout fishery in this remote pond. Area - 14 acres Temperatures Surface - 72° F. Maximum depth - 18 feet 17 feet-50°F. Principal Fishery - Brook trout Birch Ridge Pond is the middle and largest of a series of three ponds that drain into Big Pleasant Pond. It is located on the south side of a forested ridge that rises 200 feet above the pond. Spruce, fir, and white pine now dominate the forested slopes of this ridge, not birch, as the name of the pond implies. Large rocks are common both along the shore of the pond and submerged on the botto·IT!. A. very limited are:l of shallo"!.' water occurs along the shore and near the outlet. Around most of the pond the bottom drops off steeply very close to the shore. -
How to Grow and Maintain a Healthy Birch Tree
How to Grow and Maintain a Healthy Birch Tree HOW to Grow and Maintain a Healthy Birch Tree USDA Uni w S atos PriparlKI by INo.rt:hoastem An~ == ID@ p.ar1rn!1 f1l of Forest SBrvicti Sta :ij & Pnvato Agr1icu tture IForesu-y NA-FR -02-97 Contents • Introduction • Step 1 - Selecting the Proper Site • Step 2 - Selecting the Right Birch Tree for Your Landscape • Table 1 - Birch Tree Characteristics • Step 3- Maintaining Your Tree • Step 4 - Monitoring and Controlling Insect Problems • Suggested Reading • Authors • Northeastern Area State and Private Forestry Offices Cover Photo Courtesy of Edward Gilman, Associate professor, University of Florida This publication is targeted for the upper Midwestern states. However, much of the material discussed is relevant anywhere birch is grown as a landscape tree. https://www.na.fs.fed.us/spfo/pubs/howtos/ht_birch/ht_birch.htm#offices[10/10/2017 2:35:45 PM] How to Grow and Maintain a Healthy Birch Tree Introduction Birch trees are prized for their outstanding bark characteristics and their graceful delicate foliage. Numerous species and cultivars are used in landscapes, and almost all are distinctive in bark coloration, growth form, and susceptibility to certain insect pests. Though homeowners often desire birch as an ornamental tree, they soon discover that birch can be very difficult to maintain as a healthy, long-lived specimen. In many landscapes, birch trees begin to decline within a few years, and many trees die well before reaching maturity. A healthy birch tree should be able to survive and thrive for 40-50 years. In many yards, however, it is not unusual for birch trees, especially the white-barked birches, to die well before reaching 20 years of age. -
SWB – Spruce-Willow-Birch Zone
SWB – Spruce-Willow-Birch zone By: Derek Marcoux R.P.Bio., Selkirk College Introduction The Spruce-Willow-Birch (SWB) zone occupies subalpine environments in northern British Columbia. It is situated above the Boreal-White and Black Spruce Zone. This zone replaces the Engelmann-Spruce Subalpine fir zone in northern latitudes. Elevational ranges are between 1000-1600m in the southern part of its range and 600-1400m in the northern part of the range (Banner at. al. 1993). Generally the climate consists of dry, very cold winters and cool summers. Mean annual precipitation is between 460 and 700mm with a mean annual precipitation of about –0.7 to-0.3oC (Meidinger and Pojar 1991). There have been no formal subzones described for the SWB. However, Banner et. al (1993) has tentatively identified a very wet, cold (SWBvk) subzone in the Tatshenshini- Alsek region. This region is reported to have very snowy winters and is primarily non- forested. Banner et. al. (1993) reports that soils in this zone are generally young and weakly developed Regosols because of relative recent glaciation. In addition, they are subject to a wide range of geologic process such as solifluction and cryoturbation, which constantly disturbs the soil. Podzols, brunisols and Luvisols are fairly common soils on zonal forested ecosystems. In addition, cryosols can occur in valleys subject to extensive cold air drainage. Ecosystems Forested ecosystems occur in the lower elevation areas and are dominated by white spruce, subalpine-fir and lodgepole pine. Trembling aspen and black spruce occur less frequently on these sites. With increasing elevation, subalpine-fir becomes the dominant tree species.