United States (12) Patent Application Publication (10) Pub
Total Page:16
File Type:pdf, Size:1020Kb
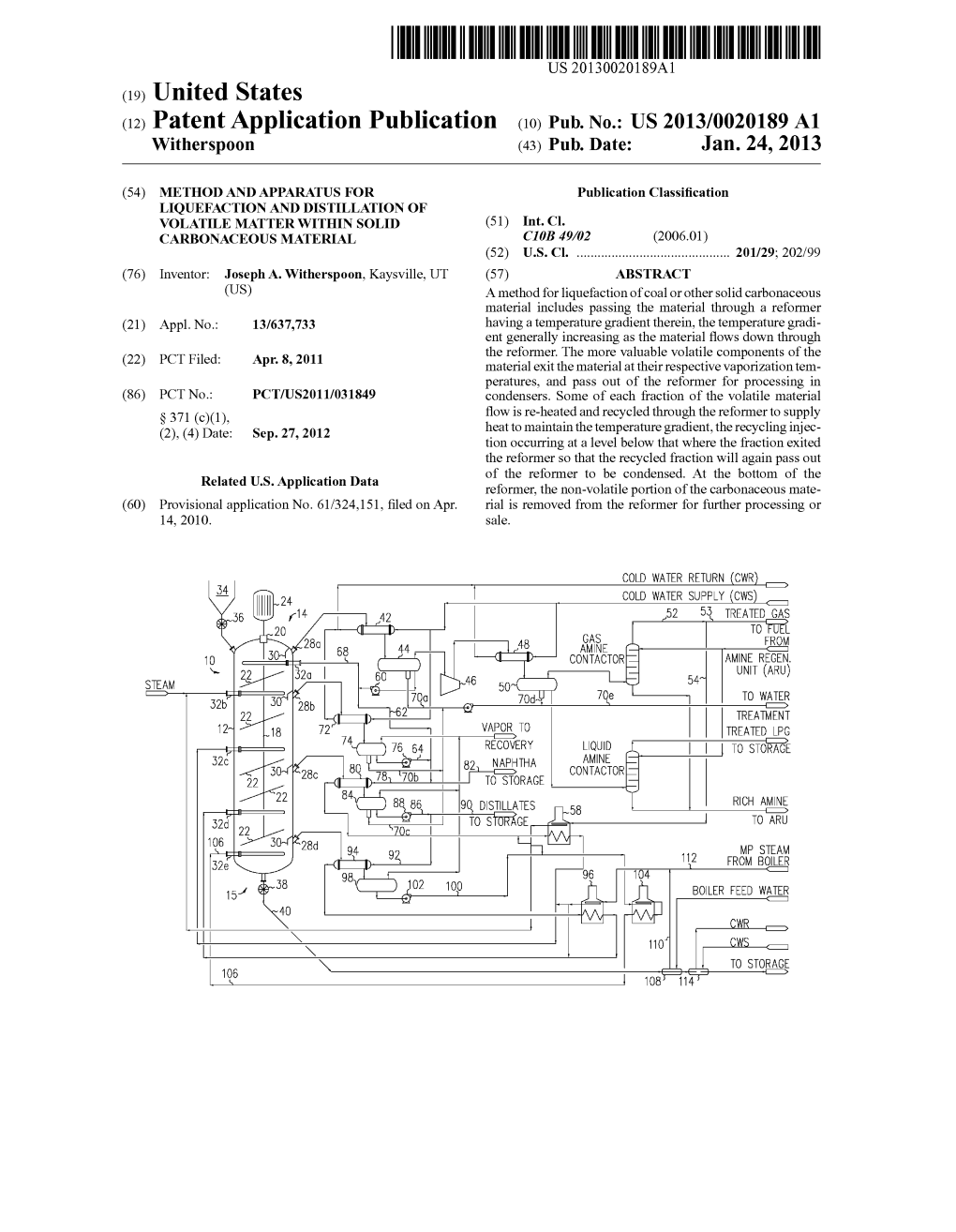
Load more
Recommended publications
-
Coal and Oil: the Dark Monarchs of Global Energy – Understanding Supply and Extraction Patterns and Their Importance for Futur
nam et ipsa scientia potestas est List of Papers This thesis is based on the following papers, which are referred to in the text by their Roman numerals. I Höök, M., Aleklett, K. (2008) A decline rate study of Norwe- gian oil production. Energy Policy, 36(11):4262–4271 II Höök, M., Söderbergh, B., Jakobsson, K., Aleklett, K. (2009) The evolution of giant oil field production behaviour. Natural Resources Research, 18(1):39–56 III Höök, M., Hirsch, R., Aleklett, K. (2009) Giant oil field decline rates and their influence on world oil production. Energy Pol- icy, 37(6):2262–2272 IV Jakobsson, K., Söderbergh, B., Höök, M., Aleklett, K. (2009) How reasonable are oil production scenarios from public agen- cies? Energy Policy, 37(11):4809–4818 V Höök M, Söderbergh, B., Aleklett, K. (2009) Future Danish oil and gas export. Energy, 34(11):1826–1834 VI Aleklett K., Höök, M., Jakobsson, K., Lardelli, M., Snowden, S., Söderbergh, B. (2010) The Peak of the Oil Age - analyzing the world oil production Reference Scenario in World Energy Outlook 2008. Energy Policy, 38(3):1398–1414 VII Höök M, Tang, X., Pang, X., Aleklett K. (2010) Development journey and outlook for the Chinese giant oilfields. Petroleum Development and Exploration, 37(2):237–249 VIII Höök, M., Aleklett, K. (2009) Historical trends in American coal production and a possible future outlook. International Journal of Coal Geology, 78(3):201–216 IX Höök, M., Aleklett, K. (2010) Trends in U.S. recoverable coal supply estimates and future production outlooks. Natural Re- sources Research, 19(3):189–208 X Höök, M., Zittel, W., Schindler, J., Aleklett, K. -
Shale Oil Combustion
INIS-mf—1 5509 University of Jordan J09600040 Faculty of Graduate Studies f’'r*dit.i(c Department of Engineering Mnthrm.'Ucs nncl Physical Science: SHALE OIL COMBUSTION 13 Y MOHAMMED AW WAD ALI AL-DABJJAS SUPERVISOR Dr. MOHAMMED II AMD AN AND Dr. V. II. KHRA1SIIA Submitted in partial fulfillment of Hie requirements for the degree of master of science in mechanical engineering. Faculty of Graduate Studies, University of Jordan. Amman , Jordan May , 1002 tr** POUR QUALITY I ORIGINAL 8 Ns OS u We regret that some of the pages in this report may not be up to the proper legibility standards, even though the best possible copy was used for scanning The Examining CommiU.ee considers this thesis satisfactory and acceptable for Ui award of the Degree of Master of Science in Mechanical Engineering in MAY, 1992. Dr. Mohammed Hamdan Chairman of Conrfhittee Mechanical Engineering Department University of Jordan Dr. Y. II. Khraisha Chemical Engineering Department University of Jordan Dr. S. A. Saved Member of Committee Chemical Engineering Department University of Jordan Dr. M. Ham mad Member of Committee Mechanical Engineering Department University of Jordan Dr. Ali Badran Member of Committee Mechanical Engineering Department University of Jordan To my mother and father I Acknowledgements H. is of my pleasure to express my gratitude to all people who helped me in completing the present work. Special thanks are indebted to my supervisors Dr. M. Hamdan and Dr. Y. Khraisha, whom without their support, encouragement and advice, my work could have been infinitely more difficult . Also special thanks are indebted to my family, especially my father and my mother for their advice and encouragement . -
Origin and Resources of World Oil Shale Deposits - John R
COAL, OIL SHALE, NATURAL BITUMEN, HEAVY OIL AND PEAT – Vol. II - Origin and Resources of World Oil Shale Deposits - John R. Dyni ORIGIN AND RESOURCES OF WORLD OIL SHALE DEPOSITS John R. Dyni US Geological Survey, Denver, USA Keywords: Algae, Alum Shale, Australia, bacteria, bitumen, bituminite, Botryococcus, Brazil, Canada, cannel coal, China, depositional environments, destructive distillation, Devonian oil shale, Estonia, Fischer assay, Fushun deposit, Green River Formation, hydroretorting, Iratí Formation, Israel, Jordan, kukersite, lamosite, Maoming deposit, marinite, metals, mineralogy, oil shale, origin of oil shale, types of oil shale, organic matter, retort, Russia, solid hydrocarbons, sulfate reduction, Sweden, tasmanite, Tasmanites, thermal maturity, torbanite, uranium, world resources. Contents 1. Introduction 2. Definition of Oil Shale 3. Origin of Organic Matter 4. Oil Shale Types 5. Thermal Maturity 6. Recoverable Resources 7. Determining the Grade of Oil Shale 8. Resource Evaluation 9. Descriptions of Selected Deposits 9.1 Australia 9.2 Brazil 9.2.1 Paraiba Valley 9.2.2 Irati Formation 9.3 Canada 9.4 China 9.4.1 Fushun 9.4.2 Maoming 9.5 Estonia 9.6 Israel 9.7 Jordan 9.8 Russia 9.9 SwedenUNESCO – EOLSS 9.10 United States 9.10.1 Green RiverSAMPLE Formation CHAPTERS 9.10.2 Eastern Devonian Oil Shale 10. World Resources 11. Future of Oil Shale Acknowledgments Glossary Bibliography Biographical Sketch Summary ©Encyclopedia of Life Support Systems (EOLSS) COAL, OIL SHALE, NATURAL BITUMEN, HEAVY OIL AND PEAT – Vol. II - Origin and Resources of World Oil Shale Deposits - John R. Dyni Oil shale is a fine-grained organic-rich sedimentary rock that can produce substantial amounts of oil and combustible gas upon destructive distillation. -
OIL SHALE, NATURAL BITUMEN, HEAVY OIL and PEAT – Vol
COAL, OIL SHALE, NATURAL BITUMEN, HEAVY OIL AND PEAT – Vol. II -Oil Shale - J.L.Qian and S.Y.Li OIL SHALE J.L.Qian and S.Y.Li School of Chemical Engineering, University of Petroleum, Beijing, China Keywords : Oil shale, Algal shale, Bituminous shale, Kukersite, Kerogen, Pyrolysis, Shale oil, Resources, Reserves, Combustion, Origin, Formation, Algae, Sapropel, Classification, Aboveground mining, Underground mining, Properties, Composition, Bitumen, Baltic, Green River, Irati, Fushun, Maoming, Stuart, Fischer Assay, Heating value, Retorting, Kiviter retort, Petrosix retort, Fushun retort, Union oil rock, pump type retort, Galoter retort, Tosco retort, Underground retorting , In-situ retorting , Shale oil upgrading, Shale oil processing, Shale ash, Cement, Soil improver, Retorted shale, Environmental problems, Waste water, Dust, Economic problem, Oil shale industry, Gasoline, Diesel, fuel, Wax, Liquid petroleum gas, Sulfur, Naphtha, Phenols, Australia, Brazil, China, Estonia, German, Israel, Russia, USA Contents 1. Introduction 2. Resources 3. Origin and Formation 3.1 Origin 3.2 Formation 3.3 Age of Formation 3.4 Environment of Formation 3.5 Classification of Kerogen 4. Mining 4.1 Aboveground Mining 4.2 Underground Mining 5. Properties and Composition 5.1 Physical Properties 5.2 Chemical Composition 5.3 Analysis and Evaluation of Oil Shale 6. Pyrolysis 6.1 Pyrolysis reaction and Mechanism 6.2 Pyrolysis Kinetics 6.3 ParticulateUNESCO and Lump Oil Shale Pyrolysis – EOLSS 7. Retorting Technology 7.1 AbovegroundSAMPLE Retorting CHAPTERS 7.2 Underground Retorting 7.3 Condensation and Recovery System 8. Shale Oil and Its Products 8.1 Shale Oil Characteristics 8.2 Shale Oil Processing and its products 9. Combustion 9.1 Pulverized Oil Shale Suspension Combustion 9.2 Particulate Oil Shale Fluidized Bed Combustion 10. -
Chapter 7 on Energy Systems Gas (GHG) Emissions
7 Energy Systems Coordinating Lead Authors: Thomas Bruckner (Germany), Igor Alexeyevich Bashmakov (Russian Federation), Yacob Mulugetta (Ethiopia / UK) Lead Authors: Helena Chum (Brazil / USA), Angel De la Vega Navarro (Mexico), James Edmonds (USA), Andre Faaij (Netherlands), Bundit Fungtammasan (Thailand), Amit Garg (India), Edgar Hertwich (Austria / Norway), Damon Honnery (Australia), David Infield (UK), Mikiko Kainuma (Japan), Smail Khennas (Algeria / UK), Suduk Kim (Republic of Korea), Hassan Bashir Nimir (Sudan), Keywan Riahi (Austria), Neil Strachan (UK), Ryan Wiser (USA), Xiliang Zhang (China) Contributing Authors: Yumiko Asayama (Japan), Giovanni Baiocchi (UK / Italy), Francesco Cherubini (Italy / Norway), Anna Czajkowska (Poland / UK), Naim Darghouth (USA), James J. Dooley (USA), Thomas Gibon (France / Norway), Haruna Gujba (Ethiopia / Nigeria), Ben Hoen (USA), David de Jager (Netherlands), Jessica Jewell (IIASA / USA), Susanne Kadner (Germany), Son H. Kim (USA), Peter Larsen (USA), Axel Michaelowa (Germany / Switzerland), Andrew Mills (USA), Kanako Morita (Japan), Karsten Neuhoff (Germany), Ariel Macaspac Hernandez (Philippines / Germany), H-Holger Rogner (Germany), Joseph Salvatore (UK), Steffen Schlömer (Germany), Kristin Seyboth (USA), Christoph von Stechow (Germany), Jigeesha Upadhyay (India) Review Editors: Kirit Parikh (India), Jim Skea (UK) Chapter Science Assistant: Ariel Macaspac Hernandez (Philippines / Germany) 511 Energy Systems Chapter 7 This chapter should be cited as: Bruckner T., I. A. Bashmakov, Y. Mulugetta, H. Chum, A. de la Vega Navarro, J. Edmonds, A. Faaij, B. Fungtammasan, A. Garg, E. Hertwich, D. Honnery, D. Infield, M. Kainuma, S. Khennas, S. Kim, H. B. Nimir, K. Riahi, N. Strachan, R. Wiser, and X. Zhang, 2014: Energy Systems. In: Climate Change 2014: Mitigation of Climate Change. Contribution of Working Group III to the Fifth Assessment Report of the Intergovernmental Panel on Climate Change [Edenhofer, O., R. -
•LOW TEMEEBATUEB GAEBONIZATION of Cokl, A
•LOW TEMEEBATUEB GAEBONIZATION OF COkL, A SOLUTION TO THE SHOES NUISANCE PROBLEM AND A I.STHDD OP Lr0H3 FULLY UTILIZING THS COAL H3SOURCSS 05* THE BOCKY MOUNTAIN E3GI0N. By Biard 33. Anderson liyron W. Kellor Robert C. Woodhead A thesis submitted to the Faculty of the University of Utah in -oartial fulfillment of the requirements for the degree of Bachelor of Science. May 1 5 , 1935 Approved "by . „ ___________________- -_______ _ I v 5 Digital Image © 2006 Biard E.Anderson, Myron W.Mellor, Robert C.Woodhead. All rights reserved. •?GIVB INSTRUCTION TO A WISE MAN, AND HE WILL BE YET WISER; TEACH A JUST MAN, AND HE WILL- INCREASE IN LEARNING.M — Proverbs. Digital Image © 2006 Biard E.Anderson, Myron W.Mellor, Robert C.Woodhead. All rights reserved. FOH&lflOHD Abatement of the smoke nuisance in Salt Lake City, and all other communities as well, is unquestionably an economic and social problem of major importance. Smoke represents a vast economic loss and also a definite danger to the health and comfort of all individuals concerned. Since the •oroblem is so far reaching and is of interest to people from all walks of life, any thesis which discusses a solution should not be purely technical but of such a nature that it can be appreciated by anyone who reads it. It is the ob.ject of the authors to present their find ings in this manner. The subject matter discussed on the pages to follow is a continuation of very extensive research studies on low- temperature carbonization of Bocky ifountain cosls. -
Comparison of Hydrocarbon Compositions in a Sequence of Humic Coals, Cannel Coals and Oil Shales from the Pictou Coalfield, Nova Scotia
ATLANTIC GEOLOGY 93 Comparison of hydrocarbon compositions in a sequence of humic coals, cannel coals and oil shales from the Pictou Coalfield, Nova Scotia W. Puttmann Lehrstuhl fur Geologie, Geochemie und Lagerstdtten des Erddls und der Kohle, RWTH Aachen, Lochnerstr. 4-20,51 Aachen, FRG. and W. Kalkreuth Institute of Sedimentary and Petroleum Geology, Geological Survey of Canada 3303-33rd Street N. W., Calgary, Alberta T2L 2A 7, Canada Date Received May 25,1988 Date Accepted August 15,1988 Thirty oil shale, cannel coal and humic coal samples from the Pennsylvanian Stellarton Group, Nova Scotia, Canada have been investigated in this study by means of organic geochemical methods including gas chromatography (GC) and gas chromatography/mass spectrometry (GC/MS). Hydrocarbon compositions o f the solvent extracts were found to vary significantly with lithology and facies. Analysis of the saturated hydrocarbon fractions revealed that the relative amounts o f long-chain alkanes (>C20) compared to those o f short-chain alkanes (<C20) are higher in the humic coal than in the cannel coal and oil shale samples. Moreover, the humic coal is characterized by the presence of homodrimane as the dominant bicyclic alkane. In the oil shale and cannel coal samples, on the other hand, C ,5-bicyclanes are present as major sesquiterpenoid hydrocarbons. Compounds such as biphenyl, dibenzofuran, fluorene and their mono-methylated and di-methylated homologues were shown to occur almost exclusively in the aromatic hydrocarbon fractions o f the humic coal samples. Presumably, these compounds are products of the degradation of lignin during diagenesis. The bitumen compositions of cannel coal and oil shale samples are quite similar. -
Oil Shale: History, Incentives, and Policy
Order Code RL33359 CRS Report for Congress Received through the CRS Web Oil Shale: History, Incentives, and Policy April 13, 2006 Anthony Andrews Specialist, Industrial Engineering and Infrastructure Policy Resources, Science, and Industry Division Congressional Research Service ˜ The Library of Congress Oil Shale: History, Incentives, and Policy Summary Oil shale is prevalent in the western states of Colorado, Utah, and Wyoming. The resource potential of these shales is estimated to be the equivalent of 1.8 trillion barrels of oil in place. Retorted oil shale yields liquid hydrocarbons in the range of middle-distillate fuels, such as jet and diesel fuel. However, because oil shales have not proved to be economically recoverable, they are considered a contingent resource and not true reserves. It remains to be demonstrated whether an economically significant oil volume can be extracted under existing operating conditions. In comparison, Saudi Arabia reportedly holds proved reserves of 267 billion barrels. Federal interest in oil shale dates back to the early 20th Century, when the Naval Petroleum and Oil Shale Reserves were set aside. Out of World War II concerns for a secure oil supply, a Bureau of Mines program began research into exploiting the resource. Commercial interest followed during the 1960s. After a second oil embargo in the 1970s, Congress created a synthetic fuels program to stimulate large- scale commercial development of oil shale and other unconventional resources. The federal program proved short-lived, and commercially backed oil shale projects ended in the early 1980s when oil prices began declining. The current high oil prices have revived the interest in oil shale. -
KIER's 5-BARREL STILL 'A Venerable Industrial Relic" W
KIER'S 5-BARREL STILL 'A Venerable Industrial Relic" W. K. Cadman okof toclax,today, completely 5Ulroun6e<1surrounded byox petroleum and2n6 en- joying the many services derived from it, may look upon this „„ ~ People ~*~^*.-.~n rt « n *..~ natural«*#>4-«««.r*1 mineral~~.^«-..rw~.r>1 resource as something4.U.'«» new. However,TLT^ the4-i*A record shows that petroleum, in its various forms, belongs to a group of minerals that have excited the curiosity and the interest of mankind from a time even before the dawn of written human history. In this group are found gold and copper, whose first use antedates the earliest records of civilization; the more common metals, such as iron, tin, and bronze, all known to man prior to 3500 B.C. Petroleum has been found in many widely separated places throughout the globe. It has appeared in the form of heavy tar or pitch deposited in sedimentary formations or on the surface of the earth, or found flowing from cracks or crevices in rocks, as oil springs or seeps. Ithas attracted mankind by its smell, its strange oiliness, and by the ease with which it burns. On the basis of use, the long history of petroleum can be logi- cally and conveniently divided into two main periods, namely: the Crude Petroleum Era, and the Refined Petroleum Era. The Crude Petroleum Era includes a segment of time perhaps as long as 8000 years, and is constantly being projected further into the past by research, especially in the field of archeology. On the other hand, the Refined Era, in comparison, is just an infant, whose present age is but five years past the century mark. -
Investigation of Byproduct Application to Jet Fuel
October 2001 • NREL/SR-510-30611 Investigation of Byproduct Application to Jet Fuel Final Report J.E. Sinor Consultants Inc. Niwot, Colorado National Renewable Energy Laboratory 1617 Cole Boulevard Golden, Colorado 80401-3393 NREL is a U.S. Department of Energy Laboratory Operated by Midwest Research Institute ••• Battelle ••• Bechtel Contract No. DE-AC36-99-GO10337 October 2001 • NREL/SR-510-30611 Investigation of Byproduct Application to Jet Fuel Final Report J.E. Sinor Consultants Inc. Niwot, Colorado NREL Technical Monitor: Kelly Ibsen Prepared under Subcontract No. TXE-0-29113-01 National Renewable Energy Laboratory 1617 Cole Boulevard Golden, Colorado 80401-3393 NREL is a U.S. Department of Energy Laboratory Operated by Midwest Research Institute ••• Battelle ••• Bechtel Contract No. DE-AC36-99-GO10337 NOTICE This report was prepared as an account of work sponsored by an agency of the United States government. Neither the United States government nor any agency thereof, nor any of their employees, makes any warranty, express or implied, or assumes any legal liability or responsibility for the accuracy, completeness, or usefulness of any information, apparatus, product, or process disclosed, or represents that its use would not infringe privately owned rights. Reference herein to any specific commercial product, process, or service by trade name, trademark, manufacturer, or otherwise does not necessarily constitute or imply its endorsement, recommendation, or favoring by the United States government or any agency thereof. The views and opinions of authors expressed herein do not necessarily state or reflect those of the United States government or any agency thereof. Available electronically at http://www.osti.gov/bridge Available for a processing fee to U.S. -
Chapter 10 'SYNTHETIC' FUELS, OIL SHALE and TAR SANDS
Chapter 10 ‘SYNTHETIC’ FUELS, OIL SHALE AND TAR SANDS New clean coal technologies can substantially improve efficiency and reduce emissions from powerplants. Until they are proven at commercial scale, however, their use entails more risk for utilities than conventional technologies. This additional risk could make it difficult for these new technologies to enter the marketplace quickly, especially given the tight deadlines of the Clean Air Act Amendments of 1990. The Clean Coal Technology Program, the single largest technology development program in the Department of Energy, is designed to help overcome this risk by offering the Federal Government as a financial partner in demonstrating worthy projects. (National Energy Strategy, Executive Summary, 1991/1992) The long-term risk of investing in new technologies that have not been demonstrated in multiple commercial applications inhibits the new technology market to such an extent that Federal resources have been needed to help fund commercial demonstration efforts. The Department of Energy's cost-shared Clean Coal Technology Demonstration Program, to which industry has contributed $2 for every $1 of Federal money invested, has evolved from an early focus on emission control systems to an emphasis in its later rounds on highly efficient, environmentally superior advanced power systems. (Sustainable Energy Strategy, 1995) 182 CHAPTER 10 Coal, petroleum and natural gas are the traditional fossil fuels whose direct use today accounts for most of the world's energy consumption. These fuels are rich in carbon and hydrogen. A relatively large amount of energy is stored in them and they have a high calorific value. However, these are not the only fossil fuels found on our planet. -
From Oil to Lithium
From Oil to Lithium Authors: Executive Summary: Benoit Gervais MSc, CFA Climate change is forcing leading economies to make big decisions that could have Senior Vice President, Portfolio a historic impact on resource sectors. Many forces are at work. Human ingenuity, Manager, Head of Team innovation, and society’s desire to advance are creating demand from all nations Mackenzie Resource Team for a cleaner and more convenient world. These changing social and economic tides Onno Rutten MSc, MBA will likely influence profound changes in consumption patterns. We examine the roles Vice President, of Electric Vehicles (EV) and renewable energy and the likely outcome for consumption Investment Management over the next decade. The probability of a rapid petroleum obsolescence remains Mackenzie Resource Team low. However, a step change in transport convenience (autonomy, or speed) would substantially increase the odds of that obsolescence, but also lead to an accelerating Scott Prieur MBA, CFA Associate Portfolio Manager global energy demand. Mackenzie Resource Team In any case, resource investors can benefit from society’s shift away from the inefficient, Asmaa Marrat MSc, CFA polluting, and unsustainable to the clean, electrical and efficient. We suggest a valuation Senior Investment Analyst framework that can be applied by flexible resource investors. The framework works Mackenzie Resource Team through the lens of sustainability–from which all stakeholders and shareholders stand to benefit for the decades to come. Eric Glover CFA Investment Director Equities One hundred and fifty years ago, apart from coal and firewood, the energy business substantially consisted of harvesting waxy SIDEBAR 1 oil from the heads of whales.