Methods for Synthesizing Diethyl Carbonate from Ethanol and Supercritical Carbon Dioxide by One- Pot Or Two-Step Reactions in the Presence of Potassium Carbonate
Total Page:16
File Type:pdf, Size:1020Kb
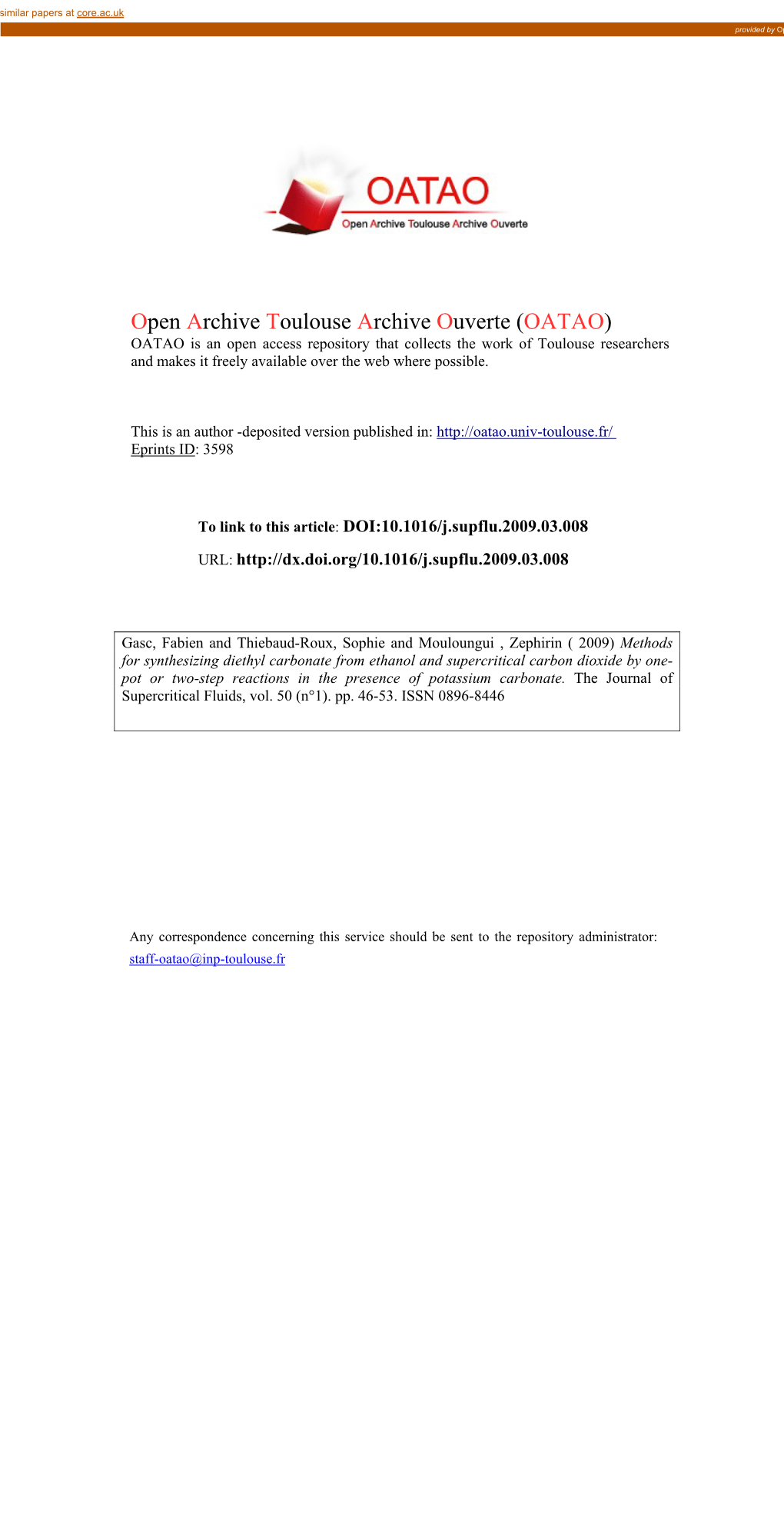
Load more
Recommended publications
-
Inventory Size (Ml Or G) 103220 Dimethyl Sulfate 77-78-1 500 Ml
Inventory Bottle Size Number Name CAS# (mL or g) Room # Location 103220 Dimethyl sulfate 77-78-1 500 ml 3222 A-1 Benzonitrile 100-47-0 100ml 3222 A-1 Tin(IV)chloride 1.0 M in DCM 7676-78-8 100ml 3222 A-1 103713 Acetic Anhydride 108-24-7 500ml 3222 A2 103714 Sulfuric acid, fuming 9014-95-7 500g 3222 A2 103723 Phosphorus tribromide 7789-60-8 100g 3222 A2 103724 Trifluoroacetic acid 76-05-1 100g 3222 A2 101342 Succinyl chloride 543-20-4 3222 A2 100069 Chloroacetyl chloride 79-04-9 100ml 3222 A2 10002 Chloroacetyl chloride 79-04-9 100ml 3222 A2 101134 Acetyl chloride 75-36-5 500g 3222 A2 103721 Ethyl chlorooxoacetate 4755-77-5 100g 3222 A2 100423 Titanium(IV) chloride solution 7550-45-0 100ml 3222 A2 103877 Acetic Anhydride 108-24-7 1L 3222 A3 103874 Polyphosphoric acid 8017-16-1 1kg 3222 A3 103695 Chlorosulfonic acid 7790-94-5 100g 3222 A3 103694 Chlorosulfonic acid 7790-94-5 100g 3222 A3 103880 Methanesulfonic acid 75-75-2 500ml 3222 A3 103883 Oxalyl chloride 79-37-8 100ml 3222 A3 103889 Thiodiglycolic acid 123-93-3 500g 3222 A3 103888 Tetrafluoroboric acid 50% 16872-11-0 1L 3222 A3 103886 Tetrafluoroboric acid 50% 16872-11-0 1L 3222 A3 102969 sulfuric acid 7664-93-9 500 mL 2428 A7 102970 hydrochloric acid (37%) 7647-01-0 500 mL 2428 A7 102971 hydrochloric acid (37%) 7647-01-0 500 mL 2428 A7 102973 formic acid (88%) 64-18-6 500 mL 2428 A7 102974 hydrofloric acid (49%) 7664-39-3 500 mL 2428 A7 103320 Ammonium Hydroxide conc. -
Evaluating the Acute and Chronic Toxicity of Potassium Carbonate and the Interactive Effects Between Sodium and Potassium on Rainbow Trout (Oncorhynchus Mykiss)
University of New Hampshire University of New Hampshire Scholars' Repository Master's Theses and Capstones Student Scholarship Fall 2020 Evaluating the acute and chronic toxicity of potassium carbonate and the interactive effects between sodium and potassium on rainbow trout (Oncorhynchus mykiss) Ashutosh Rao University of New Hampshire, Durham Follow this and additional works at: https://scholars.unh.edu/thesis Recommended Citation Rao, Ashutosh, "Evaluating the acute and chronic toxicity of potassium carbonate and the interactive effects between sodium and potassium on rainbow trout (Oncorhynchus mykiss)" (2020). Master's Theses and Capstones. 1395. https://scholars.unh.edu/thesis/1395 This Thesis is brought to you for free and open access by the Student Scholarship at University of New Hampshire Scholars' Repository. It has been accepted for inclusion in Master's Theses and Capstones by an authorized administrator of University of New Hampshire Scholars' Repository. For more information, please contact [email protected]. Evaluating the acute and chronic toxicity of potassium carbonate and the interactive effects between sodium and potassium on rainbow trout (Oncorhynchus mykiss) By Ashutosh Rao BS in Marine, Freshwater, & Estuarine Biology, University of New Hampshire, 2017 THESIS Submitted to the University of New Hampshire in Partial Fulfillment of the Requirements for the Degree of Master of Science in Biological Sciences: Marine Biology September 2020 i This thesis was examined and approved in partial fulfillment of the requirements for the degree of Master’s in Biological Sciences: Marine Biology by: Thesis/Dissertation Director, Dr. Elizabeth Fairchild, Research Associate Professor in Biological Sciences, University of New Hampshire Dr. Todd Guerdat, Assistant Professor of Agricultural Engineering, University of New Hampshire Dr. -
Ryflor™ Chemical Compatibility List
Chemical Compatibility List The following information is based on known chemical compatibility data for RyFlor™, and should only be considered as reference. Further laboratory tests may be required to verify the compatibility of a particular chemical with expanded RyFlor™ products. Chemicals Compatible with RyFlor™ Acetaldehyde Barium Sulfide Cetane (Hexadecane) Acetamide Beer Chloric Acid Acetic Acid Benzaldehyde Chlorinated Water Acetic Anhydride Benzene Chlorine Acetone Benzoic Acid Chlorine Dioxide Acetophenone Benzonitrile Chloroacetic Acid Acetylene Benzyl Alcohol Chlorobenzene Acrylic Anhydride Benzyl Chloride Chloroethylene Adipic Acid Black Liquor (Sulfate Chloroform Allyl Acetate Liquor) Chlorosulfonic Acid Allyl Alcohol Borax Chromic Acid Allyl Chloride Boric Acid Chromic Anhydride Aluminum Chloride Brine Citric Acid Aluminum Flouride Bromine Copper Acetate Aluminum Hydroxide Butadiene Copper Chloride Aluminum Nitrate Butane Copper Fluoride Aluminum Potassium Butyl Acetate Copper Sulfate Sulfate (Alum) Butyl Alcohol (Butanol) Cottonseed Oil Aluminum Sulfate Butyl Amine Creosote Ammonia Butyl Chloride Cresols (Cresylic Acid) Ammonium Carbonate Butyl Ether Crude Oil Ammonium Chloride Butyl Phthalate Cyanic Acid Ammonium Fluoride Butyl Methacrylate Cyclohexane Ammonium Hydroxide Butylene Cyclohexanol Ammonium Nitrate Butyric Acid Cyclohexanone Ammonium Phosphate Calcium Bisulfite Dibutyl Phthalate Ammonium Sulfate Calcium Chloride Dichlorobenzen Amyl Acetate Calcium Hydroxide Dichloroethane Amyl Alcohol Calcium Hypochlorite Dichloroethylene -
Using Sodium and Potassium Bicarbonates in the Prevention and Treatment of All Sickness and Disease
International Journal of Complementary & Alternative Medicine Using Sodium and Potassium Bicarbonates in the Prevention and Treatment of all Sickness and Disease Abstract Mini Review This article suggests that the use sodium and potassium bicarbonates are non- Volume 9 Issue 6 - 2017 toxic primary alkalizing agents in the prevention and treatment of all cancers, kidney disease, liver disease, Type I & Type II diabetes, Lupus, heart disease, Pharmacological toxicosis, vascular surgery operation, tonsillar herniation due Universal Medical Imaging Group, USA to cerebral edema, lactic acid toxicosis, and hyponatremia or low salt or loss of salts due to excessive or over-exercise! *Corresponding author: Robert O Young, Universal Medical Imaging Group, 16390 Dia Del Sol Valley Center, California Keywords: Cancer; Diabetes; Lupus; Heart disease; Vascular surgery; 92082, USA, Tel: 760 751 8321; Herniation; Cerebral edema; Lactic acid toxicosis; Liver disease; Kidney disease; Email: Hyponatremia; Pharmacological toxicosis Received: January 10, 2016 | Published: December 08, 2017 Introduction Sodium and potassium bicarbonate increases the hydroxyl ions or electron levels through increased alkalinity to the cells Sodium and potassium bicarbonate are excellent agents for buffering the metabolic acids that can cause cancer [20]. It is a natural alkaline approach in the treatment for all sickness and also one of the most basic medicines in allopathic and alternative disease, including cancer. Sodium bicarbonate is the universal medicine we have for the treatment of kidney disease. Research by mainstream treatment of acidosis. It is used every day by British scientists at the Royal London Hospital shows that sodium oncologists to neutralize the heavy acidic nature of their chemical bicarbonate can dramatically slow the progress of chronic kidney and chemotherapeutic agents which are often quite toxic. -
Food and Drug Administration, HHS § 184.1639
Food and Drug Administration, HHS § 184.1639 (2) The ingredient is used in food at Academy Press, 2101 Constitution Ave. levels not to exceed current good man- NW., Washington, DC 20418, or may be ufacturing practice. examined at the National Archives and (d) Prior sanctions for this ingredient Records Administration (NARA). For different from the uses established in information on the availability of this this section do not exist or have been material at NARA, call 202–741–6030, or waived. go to: http://www.archives.gov/ federallregister/ [48 FR 52444, Nov. 18, 1983] codeloflfederallregulations/ § 184.1634 Potassium iodide. ibrllocations.html. (c) The ingredient is used as a dough (a) Potassium iodide (KI, CAS Reg. strengthener as defined in § 170.3(o)(6) No. 7681–11–0) is the potassium salt of of this chapter. hydriodic acid. It occurs naturally in (d) The ingredient is used in the man- sea water and in salt deposits, but can ufacture of bread in accordance with be prepared by reacting hydriodic acid § 184.1(b)(2) of this chapter in an (HI) with potassium bicarbonate amount not to exceed 0.0075 percent (KHCO ). 3 based on the weight of the flour. (b) The ingredient meets the speci- (e) Prior sanctions for this ingredient fications of the ‘‘Food Chemicals different from the uses established in Codex,’’ 3d Ed. (1981), pp. 246–247, which this section do not exist or have been is incorporated by reference. Copies waived. may be obtained from the National Academy Press, 2101 Constitution Ave. [43 FR 11699, Mar. 21, 1978, as amended at 49 NW., Washington, DC 20418, or may be FR 5613, Feb. -
LIST of ANNEXURES SR. NO. NAME of ANNEXURE I List of Products
LIST OF ANNEXURES SR. NO. NAME OF ANNEXURE I List of Products and Raw materials along with their Production Capacity II Layout Map of the Plant III Brief Manufacturing Process Description IV Details of water consumption & waste water generation V Details of Effluent Treatment Scheme VI Details of Hazardous Waste Generation and Disposal VII Details of Stacks and Vents, Fuel & Energy Requirements VIII Details of Hazardous Chemicals Storage & Handling IX Socio-economic Impacts X Proposed Terms of Reference XI GIDC Plot Allotment Letter XII ETL Membership Letter (M/s. ETL) XIII TSDF & CHWIF Membership Letter (M/s BEIL) XIV Toposheet XV Copy of existing CCA ANNEXURE-I _____________________________________________ _________________________ LIST OF PRODUCTS ALONG WITH THEIR PRODUCTION CAPACITY WITH RAW MATERIALS PRODUCTION CAPACITY (MT/MONTH) SR. PRODUCTS CAS NO NO EXISTING ADDITIONAL TOTAL QUANTITY QUANTITY PROPOSED QUANTITY EXISITING PRODUCTS 1 Optical Brightening Agent 13001-39-3 1.0 0 1.0 2 Ortho Toluene Nitrite 88-72-2 4.0 0 4.0 TOTAL (EXISITING PRODUCTS) 5.0 0 5.0 PROPOSED PRODUCTS 1 Darunavir 206361-99-1 5 5 2 Levosulpiride 23672-07-3 10 10 3 Montelukast Sodium 151767-02-1 5.5 5.5 4 Tramadol hydrochloride 36282-47-0 7 7 5 Nifedipine 21829-25-4 4.5 4.5 6 Quetiapinehemifumarate 111974-72-2 3 3 7 Furosemide 54-31-9 3.5 3.5 8 Risedronate Sodium 105462-24-6 4.5 4.5 66108-95- 0/60166-93- 9 Iohexol/Iopamidol/Iodixanol 0/92339-11- 2 6 6 10 Lauryl Pyridinium chloride 104-74-5 10 10 11 Vildagliptin 274901-16-5 4 4 12 Ambroxol Hydrochloride 23828-92-4 -
Recent Progress in Phosgene-Free Methods for Synthesis of Dimethyl Carbonate*
Pure Appl. Chem., Vol. 84, No. 3, pp. 603–620, 2012. http://dx.doi.org/10.1351/PAC-CON-11-06-02 © 2011 IUPAC, Publication date (Web): 22 September 2011 Recent progress in phosgene-free methods for synthesis of dimethyl carbonate* Weicai Peng1, Ning Zhao1, Fukui Xiao1, Wei Wei1,‡, and Yuhan Sun1,2,‡ 1State Key Laboratory of Coal Conversion, Institute of Coal Chemistry, Chinese Academy of Sciences, Taiyuan 030001, China; 2Low Carbon Conversion Center, Shanghai Advanced Research Institute, Chinese Academy of Sciences, Shanghai 201203, China Abstract: Dimethyl carbonate (DMC) is considered as an environmentally benign chemical due to negligible ecotoxicity, low bioaccumulation, and low persistence. However, the tradi- tional process of DMC synthesis via phosgene and methanol is limited in industry owing to the toxic raw material involved. Thus, environmentally friendly phosgene-free processes for DMC production have been proposed and developed in the past decades. Until now, the alter- natives appear to be the oxidative carbonylation of methanol, the transesterification of pro - pylene or ethylene carbonate (PC or EC), the methanolysis of urea, and the direct synthesis of DMC from CO2 with methanol. In this review, we present some recent developments of these phosgene-free approaches and their prospects for industrialization. Keywords: carbon dioxide; dimethyl carbonate synthesis; oxidative carbonylation; phosgene- free; transesterification; urea. INTRODUCTION Along with the global spread of sustainable development strategy, the chemical synthesis processes and materials endangering humans and the environment would be gradually restricted. The “clean produc- tion process” and “green chemicals” will be the developmental direction for the modern chemical indus- try, and the production and chemical utilization of dimethyl carbonate (DMC) are closely concerted by this trend. -
Research Module: Scheme 2A. N-Benzylation Using Benzyl Bromide 63
Research Module: Scheme 2A. N-Benzylation Using Benzyl Bromide 63 O Scheme 2 Option O Methanol Solvent NH N-Benzylation + Br NH2 N via Alkyl Halide 1 K2CO3 Workup NH 8 R1 R1 (0.139g/mmol) 6a-e Synthesis of 3a-e Benzyl Bromide N-Benzyl 171 g/mol N-Benzyl 1.438 g/ml Pyrazolidinone Pyrazolidinones 119 ml/mol Scheme 2 Part A: Redissolve in Methanol 1. Turn hot plate to 5. 2. To the flask with your product 3 from Scheme 1, attach a condener with gentle water flow. 3. Add 15 mL of methanol. • For 4-methoxy compoud 3c, you may need to add 20 mL of methanol, since the 4-methoxy substrates is probably less soluble. 4. Heat the mixture on the hot plate with the stirrer at 6 until the material dissolves and becomes completely homogeneous. Once it’s dissolved, reduce the hot plate setting to 4. • If the stir bar isn’t coming free even after several minutes, you may wish to detach the condenser and poke the stir-bar free with a spatula • Make sure that there aren’t chunks or blobs of undissolved material on the outside. Everything needs to be dissolved. 5. Calculate 0.9 equivalents of benzyl bromide. Calculate how many mL of benzyl bromide (119 mL/mol) you need to add 0.90 mmol benzyl bromide per mmol of 3. In other words, if you have 20.0 mmol of 3c, how many mL of benzaldehyde will it take to provide 18.0 mmol? • You need to know how many mmol of reactant 3 you are working with. -
CAS No.) Screening Justification Is Public Comment Now Open? CAS No
EGLE Air Quality Division (AQD) Air Toxics Screening Level Justifications (Numerically by CAS No.) Screening Justification Is Public Comment Now Open? CAS No. Chemical Name Level & Responses Info E-Mail AQD Deadline None ad acid View View Not Open for Public Comment None amyl acetate (mixture) View View Not Open for Public Comment None atlox 848 View View Not Open for Public Comment None biosam tp-1.5 View View Not Open for Public Comment None calcium chloride View View Not Open for Public Comment None epoxy resin solution View View Not Open for Public Comment None heptamethyl-1-vinyl-1,7-dichlorotetrasilazane View View Not Open for Public Comment None n-butylglucamine View View Not Open for Public Comment None n-chloro-2,6-difluorobenzamide View View Not Open for Public Comment None trichloroethylene View View Not Open for Public Comment None triethylammonium suleptanate View View Not Open for Public Comment 50-00-0 formaldehyde View View Not Open for Public Comment 50-03-3 hydrocortisone acetate View View Not Open for Public Comment 50-21-5 lactic acid View View Not Open for Public Comment 50-28-2 estradiol View View Not Open for Public Comment 50-29-3 ddt View View Not Open for Public Comment 50-32-8 benzo(a)pyrene View View Not Open for Public Comment 51-28-5 2,4-dinitrophenol View View Not Open for Public Comment 53-36-1 methyl predisolone acetate View View Not Open for Public Comment 53-70-3 dibenz(a,h)anthracene View View Not Open for Public Comment 56-23-5 carbon tetrachloride View View Not Open for Public Comment 56-49-5 3-methylcholanthrene View View Not Open for Public Comment 56-55-3 benz(a)anthracene View View Not Open for Public Comment 56-81-5 glycerol View View Not Open for Public Comment 57-11-4 stearic acid View View Not Open for Public Comment Revised Monday, September 27, 2021 Page 1 of 51 EGLE Air Quality Division (AQD) Air Toxics Screening Level Justifications (Numerically by CAS No.) Screening Justification Is Public Comment Now Open? CAS No. -
Safety Data Sheet - Patina Gel Revision 11/14/2016
Safety Data Sheet - Patina Gel Revision 11/14/2016 1. PRODUCT AND COMPANY IDENTIFICATION Product name: Patina Gel / Sulfurated Potash 39365-88-3 CAS #: 39365-88-3 Manufacturer: Cool Tools 945 N. Parkway St Jefferson, WI 53549 Telephone: 888-478-5060 Fax: 262-546-5275 Emergency Phone #: Chemtrec USA & Canada 800-424-9300 International 703-527-38 2. HAZARDS IDENTIFICATION GHSClassification Acute Toxicity, Oral (Category 3) Skin Irritation (Category 2) Serious Eye Irritation (Category 2) GH3 Label elements, including precautionary statements Signal Word: Warning Hazard statement(s) H303 May be harmful if swallowed. H315 Causes skin irritation. H320 Causes eye irritation. Precautionary statement(s) P264 Wash hands, face and clothing after handling. P270 Do not eat, drink or smoke when using this product. P271 Use only outdoors or in a well ventilated area. P280 Wear protective gloves/clothing/eye protection P305 & P351 If in eyes, rinse cautiously with water for several minutes. P338 Remove contact lenses, if present and easy to do. Continue rinsing. P312 Call a poison center/doctor if you feel unwell. HMIS Classification NFPA Classification Health hazard: 2 Health hazard: 2 Contact: 1 Reactivity: 0 Flammability 0 Flammability: 0 Physical hazards: 2 Personal B Distributed by: Cool Tools 945 N Parkway St Jefferson, WI 53549 3. COMPOSITION/INFORMATION ON INGREDIENTS Synonyms: Liver of Sulfur, Sulfurated potassa, hepar sulfuris Potassium Trisulfide CAS No. 37488-75-8: 6.25% Potassium Thiosulfate Hydrated CAS No. 10294-66-3: 18.75% Glycerin CAS No. 56-81-5: 75% 4. FIRST AID MEASURES Inhalation: Not likely to occur except as a mist. -
Spe-128 the Catalysis of Potassium Carbonate Solutions in Carbon Dioxide Absorption
SPE-128 THE CATALYSIS OF POTASSIUM CARBONATE SOLUTIONS IN CARBON DIOXIDE ABSORPTION By A. G. Eickmeyer, Chemical Engineering Consultant Prairie Village, Kansas ABS~:RACT bing. The activity o£ hot potassium car THEORY AND DEPINITIONS Downloaded from http://onepetro.org/speatce/proceedings-pdf/61fm/all-61fm/spe-128-ms/2087284/spe-128-ms.pdf by guest on 01 October 2021 bonate solutions has been £ound to be a function of contaminants, having a de The absorption of an acid gas in leterious effect, and catalysts, which any alkaline solution is classed as activate the solution. A small amount chemi-sorption, that is, absorption ll of "Catacarb catalyst cancels the e£ accompanied by chemical reaction. The £ect o£ contamination and larger amounts rate o£ chemical reaction determines give a much more active solution than the size of the towers required by the pure potassium carbonate. In commercial process. plant tests in existing carbonate Unlike caustic, a carbonate solu plants, the Catacarb Process resulted tion has very few hydroxyl ions to re in increased capacity, reduced steam act directly with CO , Therefore, it usaze, and less residual CO , In 2 2 is believed that CO2 must £irst become new plant construction, ~ ss equipment ·hydrated, or react with water to £orm and utility requirements o£ the Catacarb carbonic acid, which in turn reacts Process permit savings in capital in with a carbonate ion to form two bi vestment and operating costs. carbonate ions. INTRODUC '1'1 ON (1) CO2 • H2 0 = H2 CO 3 The hot potassium carbonate £r~cess, developed by the Bureau o£ Mines, ,-, has been applied extensively in recent years to CO 2 removal in the puri£ica Con£irmation o£ the reaction with tion of hydrogen and natural Gas. -
Gas Phase Chemistry and Removal of CH3I During a Severe Accident
DK0100070 Nordisk kernesikkerhedsforskning Norraenar kjarnoryggisrannsoknir Pohjoismainenydinturvallisuustutkimus Nordiskkjernesikkerhetsforskning Nordisk karnsakerhetsforskning Nordic nuclear safety research NKS-25 ISBN 87-7893-076-6 Gas Phase Chemistry and Removal of CH I during a Severe Accident Anna Karhu VTT Energy, Finland 2/42 January 2001 Abstract The purpose of this literature review was to gather valuable information on the behavior of methyl iodide on the gas phase during a severe accident. The po- tential of transition metals, especially silver and copper, to remove organic io- dides from the gas streams was also studied. Transition metals are one of the most interesting groups in the contex of iodine mitigation. For example silver is known to react intensively with iodine compounds. Silver is also relatively inert material and it is thermally stable. Copper is known to react with some radioio- dine species. However, it is not reactive toward methyl iodide. In addition, it is oxidized to copper oxide under atmospheric conditions. This may limit the in- dustrial use of copper. Key words Methyl iodide, gas phase, severe accident mitigation NKS-25 ISBN 87-7893-076-6 Danka Services International, DSI, 2001 The report can be obtained from NKS Secretariat P.O. Box 30 DK-4000RoskiIde Denmark Phone +45 4677 4045 Fax +45 4677 4046 http://www.nks.org e-mail: [email protected] Gas Phase Chemistry and Removal of CH3I during a Severe Accident VTT Energy, Finland Anna Karhu Abstract The purpose of this literature review was to gather valuable information on the behavior of methyl iodide on the gas phase during a severe accident.