CEMNTAION DEPH,Mm
Total Page:16
File Type:pdf, Size:1020Kb
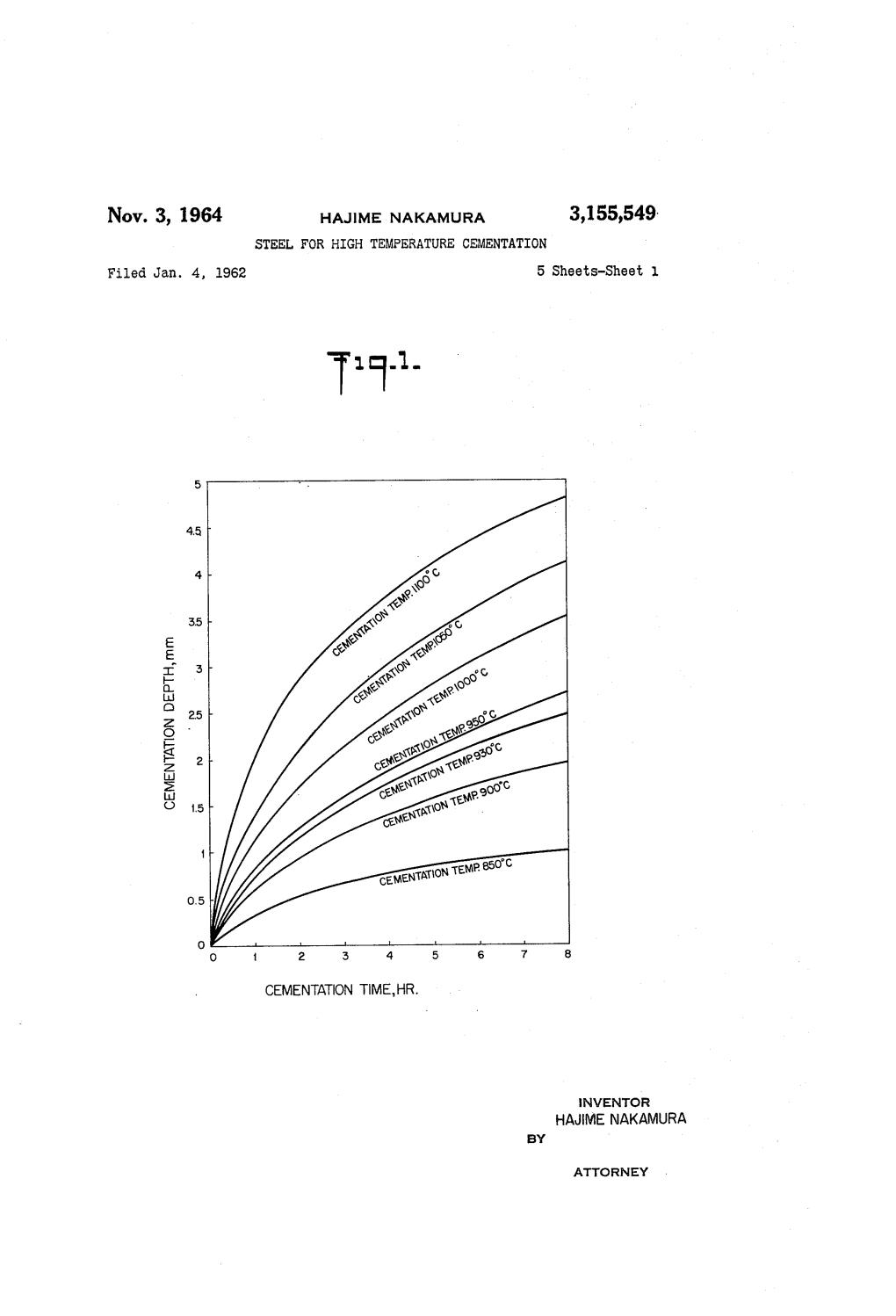
Load more
Recommended publications
-
Monitoring of Silicon Nitride Films Grown by PLD Using Real
Beryllium nitride thin film grown by reactive laser ablation G. Soto, J. A. Díaz, R. Machorro, A. Reyes-Serrato* Centro de Ciencias de la Materia Condensada, UNAM, A. Postal 2681, 22800 Ensenada B.C., México. W. de la Cruz Centro de Investigación Científica y de Educación Superior de Ensenada, Km. 107 carretera Tijuana-Ensenada, 22800 Ensenada B.C., México. Beryllium nitride thin films were grown on silicon substrates by laser ablating a beryllium foil in molecular nitrogen ambient. The composition and chemical state were determined with Auger (AES), X-Ray photoelectron (XPS) and energy loss (EELS) spectroscopies. A low absorption coefficient in the visible region, and an optical bandgap of 3.8 eV, determined by reflectance ellipsometry, were obtained for films grown at nitrogen pressures higher than 25 mTorr. The results show that the reaction of beryllium with nitrogen is very effective using this preparation method, producing high quality films. keywords: Beryllium nitride, laser ablation, thin films, wide bandgap, optical properties. PACS numbers: 81.05.Je, 81.15.Fg, 81.40.Tv *Corresponding author. Centro de Ciencias de la Materia Condensada UNAM, P.O. Box 439036, San Ysidro CA 92143. Tel. ++52-6-174 4602. Fax. ++52-6-174 4603. E-mail address: [email protected] 1 The production and characterization of nitrides materials are subject of many publications due to technological importance. An important example is the research done to obtain a material suitable for laser diodes emitting in the blue/ultraviolet region. A very important feature is the quantum efficiency, therefore the material must own a direct band-gap. -
WO 2016/074683 Al 19 May 2016 (19.05.2016) W P O P C T
(12) INTERNATIONAL APPLICATION PUBLISHED UNDER THE PATENT COOPERATION TREATY (PCT) (19) World Intellectual Property Organization International Bureau (10) International Publication Number (43) International Publication Date WO 2016/074683 Al 19 May 2016 (19.05.2016) W P O P C T (51) International Patent Classification: (81) Designated States (unless otherwise indicated, for every C12N 15/10 (2006.01) kind of national protection available): AE, AG, AL, AM, AO, AT, AU, AZ, BA, BB, BG, BH, BN, BR, BW, BY, (21) International Application Number: BZ, CA, CH, CL, CN, CO, CR, CU, CZ, DE, DK, DM, PCT/DK20 15/050343 DO, DZ, EC, EE, EG, ES, FI, GB, GD, GE, GH, GM, GT, (22) International Filing Date: HN, HR, HU, ID, IL, IN, IR, IS, JP, KE, KG, KN, KP, KR, 11 November 2015 ( 11. 1 1.2015) KZ, LA, LC, LK, LR, LS, LU, LY, MA, MD, ME, MG, MK, MN, MW, MX, MY, MZ, NA, NG, NI, NO, NZ, OM, (25) Filing Language: English PA, PE, PG, PH, PL, PT, QA, RO, RS, RU, RW, SA, SC, (26) Publication Language: English SD, SE, SG, SK, SL, SM, ST, SV, SY, TH, TJ, TM, TN, TR, TT, TZ, UA, UG, US, UZ, VC, VN, ZA, ZM, ZW. (30) Priority Data: PA 2014 00655 11 November 2014 ( 11. 1 1.2014) DK (84) Designated States (unless otherwise indicated, for every 62/077,933 11 November 2014 ( 11. 11.2014) US kind of regional protection available): ARIPO (BW, GH, 62/202,3 18 7 August 2015 (07.08.2015) US GM, KE, LR, LS, MW, MZ, NA, RW, SD, SL, ST, SZ, TZ, UG, ZM, ZW), Eurasian (AM, AZ, BY, KG, KZ, RU, (71) Applicant: LUNDORF PEDERSEN MATERIALS APS TJ, TM), European (AL, AT, BE, BG, CH, CY, CZ, DE, [DK/DK]; Nordvej 16 B, Himmelev, DK-4000 Roskilde DK, EE, ES, FI, FR, GB, GR, HR, HU, IE, IS, IT, LT, LU, (DK). -
Chemical Names and CAS Numbers Final
Chemical Abstract Chemical Formula Chemical Name Service (CAS) Number C3H8O 1‐propanol C4H7BrO2 2‐bromobutyric acid 80‐58‐0 GeH3COOH 2‐germaacetic acid C4H10 2‐methylpropane 75‐28‐5 C3H8O 2‐propanol 67‐63‐0 C6H10O3 4‐acetylbutyric acid 448671 C4H7BrO2 4‐bromobutyric acid 2623‐87‐2 CH3CHO acetaldehyde CH3CONH2 acetamide C8H9NO2 acetaminophen 103‐90‐2 − C2H3O2 acetate ion − CH3COO acetate ion C2H4O2 acetic acid 64‐19‐7 CH3COOH acetic acid (CH3)2CO acetone CH3COCl acetyl chloride C2H2 acetylene 74‐86‐2 HCCH acetylene C9H8O4 acetylsalicylic acid 50‐78‐2 H2C(CH)CN acrylonitrile C3H7NO2 Ala C3H7NO2 alanine 56‐41‐7 NaAlSi3O3 albite AlSb aluminium antimonide 25152‐52‐7 AlAs aluminium arsenide 22831‐42‐1 AlBO2 aluminium borate 61279‐70‐7 AlBO aluminium boron oxide 12041‐48‐4 AlBr3 aluminium bromide 7727‐15‐3 AlBr3•6H2O aluminium bromide hexahydrate 2149397 AlCl4Cs aluminium caesium tetrachloride 17992‐03‐9 AlCl3 aluminium chloride (anhydrous) 7446‐70‐0 AlCl3•6H2O aluminium chloride hexahydrate 7784‐13‐6 AlClO aluminium chloride oxide 13596‐11‐7 AlB2 aluminium diboride 12041‐50‐8 AlF2 aluminium difluoride 13569‐23‐8 AlF2O aluminium difluoride oxide 38344‐66‐0 AlB12 aluminium dodecaboride 12041‐54‐2 Al2F6 aluminium fluoride 17949‐86‐9 AlF3 aluminium fluoride 7784‐18‐1 Al(CHO2)3 aluminium formate 7360‐53‐4 1 of 75 Chemical Abstract Chemical Formula Chemical Name Service (CAS) Number Al(OH)3 aluminium hydroxide 21645‐51‐2 Al2I6 aluminium iodide 18898‐35‐6 AlI3 aluminium iodide 7784‐23‐8 AlBr aluminium monobromide 22359‐97‐3 AlCl aluminium monochloride -
Hydrogen Retention in Beryllium Nitride
Hydrogen retention in beryllium nitride. A. ALLOUCHE* Physique des Interactions Ioniques et Moléculaires, CNRS and Aix-Marseille Université (UMR7345), Campus Scientifique de Saint Jérôme, service 242, 13397 Marseille Cedex 20 - FRANCE M. OBERKOFLER Max-Planck-Institut für Plasmaphysik Boltzmannstr. 2, 85748 Garching, GERMANY M. KÖPPEN, CH. LINSMEIER Forschungszentrum Jülich GmbH, Institut für Energie- und Klimaforschung – Plasmaphysik, 52425 Jülich, Germany E-mail: [email protected] Abstract: The valence band density of states of bulk beryllium nitride (alpha-Be3N2) and the solvation energy of hydrogen atoms in this nitride is herein studied using the generalized gradient approximation density functional theory. The DOS is compared to photoelectron spectroscopy investigations of nitrogen-implanted beryllium. The presence of defects (atomic vacancies) was taken into consideration in the calculations on the trapping of deuterium. The barriers of activation for hydrogen atom diffusion in the bulk and from the defect were calculated and compared to their values in pure beryllium metal and in beryllium oxide. Some consequences regarding the effects of nitrogenation of beryllium as a plasma-facing material in nuclear fusion devices are eventually proposed. 2 I. Introduction Beryllium is planned to be used as a plasma-facing material for the international nuclear fusion experiment ITER and hence will be subjected to hydrogen isotopes deuterium and tritium escaping from the magnetically confined plasma. Therefore, hydrogen atom implantation and release in beryllium are vital issues that have been the focus of many investigations [1]. On the other hand seeding of impurities in the plasma is often used in tokamak experiments for various purposes. In particular, the absence of carbon in modern divertor concepts makes radiative cooling by nitrogen seeding mandatory to reduce the power flux. -
Printed Copies for Reference Only
Supplier Environmental Health and Safety Number:CHI-EHS30-000 Revision:A Specification 1 APPROVERS INFORMATION PREPARED BY: Jennilyn Rivera Dinglasan Title: EHS DATE: 5/3/2017 2:35:30 AM APPROVED BY: Jennilyn DATE: 8/10/2017 7:00:05 Rivera Dinglasan Title: EHS PM DATE: 7/21/2017 2:43:17 APPROVED BY: Aline Zeng Title: Purchasing AM APPROVED BY: Bill Hemrich Title: Purchasing DATE: 6/1/2017 3:28:35 PM DATE: 6/11/2017 11:05:48 APPROVED BY: Jade Yuan Title: Purchasing PM APPROVED BY: Matthew DATE: 5/26/2017 6:54:14 Briggs Title: Purchasing AM DATE: 5/26/2017 3:56:07 APPROVED BY: Michael Ji Title: Purchasing AM DATE: 8/31/2017 4:24:35 APPROVED BY: Olga Chen Title: Purchasing AM APPROVED BY: Alfredo DATE: 6/2/2017 11:54:20 Heredia Title: Supplier Quality AM APPROVED BY: Audrius DATE: 5/31/2017 1:20:01 Sutkus Title: Supplier Quality AM DATE: 5/26/2017 2:03:53 APPROVED BY: Sam Peng Title: Supplier Quality AM APPROVED BY: Arsenio DATE: 6/28/2017 2:43:49 Mabao Cesista Jr. Title: EHS Manager AM Printed copies for reference only Printed copies for reference only Supplier Environmental Health and Safety Number:CHI-EHS30-000 Revision:A Specification 1 1.0 Purpose and Scope 1.1 This specification provides general requirements to suppliers regarding Littelfuse Inc’s EHS specification with regards to regulatory compliance, EHS management systems, banned and restricted substances, packaging, and product environmental content reporting. 1.2 This specification applies to all equipment, materials, parts, components, packaging, or products supplied to Littelfuse, Inc. -
Interaction Dynamics of Beryllium Surfaces with Nitrogen and Deuterium Projectiles
EUROFUSION WPPFC-PR(14) 12681 K. Dobes et al. Interaction Dynamics of Beryllium Surfaces with Nitrogen and Deuterium Projectiles Preprint of Paper to be submitted for publication in New Journal of Physics This work has been carried out within the framework of the EUROfusion Con- sortium and has received funding from the Euratom research and training pro- gramme 2014-2018 under grant agreement No 633053. The views and opinions expressed herein do not necessarily reflect those of the European Commission. This document is intended for publication in the open literature. It is made available on the clear under- standing that it may not be further circulated and extracts or references may not be published prior to publication of the original when applicable, or without the consent of the Publications Officer, EUROfu- sion Programme Management Unit, Culham Science Centre, Abingdon, Oxon, OX14 3DB, UK or e-mail Publications.Offi[email protected] Enquiries about Copyright and reproduction should be addressed to the Publications Officer, EUROfu- sion Programme Management Unit, Culham Science Centre, Abingdon, Oxon, OX14 3DB, UK or e-mail Publications.Offi[email protected] The contents of this preprint and all other EUROfusion Preprints, Reports and Conference Papers are available to view online free at http://www.euro-fusionscipub.org. This site has full search facilities and e-mail alert options. In the JET specific papers the diagrams contained within the PDFs on this site are hyperlinked Interaction Dynamics of Beryllium Surfaces with Nitrogen -
Li Na K Be Mg Ca B Al Ni Au Ag
LAST NAME____________________ FIRST NAME____________________________ DATE ___________ 6.1 NAMING IONIC COMPOUNDS = Use the notes to write the correct names of the IONIC COMPOUNDS created by the Cations and Anions. SIMPLE EXAMPLES Anions Cations ↓ F Cl Br I Li Lithium Fluoride Lithium Chloride Lithium Bromide Lithium Iodide Na Sodium Fluoride Sodium Chloride Sodium Bromide Sodium Iodide K Potassium Fluoride Potassium Chloride Potassium Bromide Potassium Iodide Be Beryllium Fluoride Beryllium Chloride Beryllium Bromide Beryllium Iodide Mg Magnesium Fluoride Magnesium Chloride Magnesium Bromide Magnesium Iodide Ca Calcium Fluoride Calcium Chloride Calcium Bromide Calcium Iodide B Boron Fluoride Boron Chloride Boron Bromide Boron Iodide Al Aluminum Fluoride Aluminum Chloride Aluminum Bromide Aluminum Iodide Ni Nickel Fluoride Nickel Chloride Nickel Bromide Nickel Iodide Au Gold Fluoride Gold Chloride Gold Bromide Gold Iodide Ag Silver Fluoride Silver Chloride Silver Bromide Silver Iodide And some more Anions Cations ↓ O S N Li Lithium Oxide Lithium Sulfide Lithium Nitride Na Sodium Oxide Sodium Sulfide Sodium Nitride K Potassium Oxide Potassium Sulfide Potassium Nitride Be Beryllium Oxide Beryllium Sulfide Beryllium Nitride Mg Magnesium Oxide Magnesium Sulfide Magnesium Nitride Ca Calcium Oxide Calcium Sulfide Calcium Nitride B Boron Oxide Boron Sulfide Boron Nitride Al Aluminum Oxide Aluminum Sulfide Aluminum Nitride Ni Nickel Oxide Nickel Sulfide Nickel Nitride Au Gold Oxide Gold Sulfide Gold Nitride Ag Silver Oxide Silver Sulfide Silver -
Beryllium Nitride Thin Film Grown by Reactive Laser Ablation G
January 2002 Materials Letters 52Ž. 2002 29–33 www.elsevier.comrlocatermatlet Beryllium nitride thin film grown by reactive laser ablation G. Soto a, J.A. Dıaz´ a, R. Machorro a, A. Reyes-Serrato a,), W. de la Cruz b a Centro de Ciencias de la Materia Condensada, UNAM, A. Postal 2681, 22800 Ensenada B.C., Mexico b Centro de InÕestigacion´´ Cientıfica y de Educacion ´ Superior de Ensenada, Km. 107 carretera Tijuana-Ensenada, 22800 Ensenada B.C., Mexico Received 28 January 2001; accepted 20 March 2001 Abstract Beryllium nitride thin films were grown on silicon substrates by laser ablating a beryllium foil in molecular nitrogen ambient. The composition and chemical state were determined with AugerŽ. AES , X-ray photoelectron Ž. XPS and energy lossŽ. EELS spectroscopies. A low absorption coefficient in the visible region and an optical bandgap of 3.8 eV, determined by reflectance ellipsometry, were obtained for films grown at nitrogen pressures higher than 25 mTorr. The results show that the reaction of beryllium with nitrogen is very effective using this preparation method in producing high quality films. q 2002 Elsevier Science B.V. All rights reserved. PACS: 81.05.Je; 81.15.Fg; 81.40.Tv Keywords: Beryllium nitride; Laser ablation; Thin films; Wide bandgap; Optical properties The production and characterization of nitrides nitride are possible at the berylliumrliquid nitrogen materials are subject of many publications due to interfacewx 3 . In this work, we demonstrate that nitro- technological importance. An important example is gen can be incorporated into beryllium films by the research done to obtain a material suitable for ablating a beryllium target in a background N2 gas laser diodes emitting in the bluerultraviolet region. -
Preliminary Report on the Thermodynamic Properties of Selected Light -Element and Some Related Compounds, NBS Report 7587, 1 July 1962
AFOSR Scientific Report AFOSR 68-1625 NATIONAL BUREAU OF STANDARDS REPORT 9803 PRELIMINARY REPORT ON THE THERMODYNAMIC PROPERTIES OF SELECTED LIGHT-ELEMENT AND SOME RELATED COMPOUNDS (The previous semiannual reports in this series have the NBS Report Nos. 6297, 6484, 6645, 6928, 7093, 7192, 7437, 7587, 7796, 8033, 8186, 8504, 8628, 8919, 9028, 9389, 9500, and 9601.) <NB^> U.S. DEPARTMENT OF COMMERCE NATIONAL BUREAU OF STANDARDS This document is subject to special export controls and each transmittal to foreign governments or to foreign nationals may be made only with prior approval of the AFOSR (SRGL). : Qualified requestors may obtain additional copies from the Defense Documentation Center. NATIONAL BUREAU OF STANDARDS The National Bureau of Standards 1 was established by an act of Congress March 3, 1901. Today, in addition to serving as the Nation’s central measurement laboratory, the Bureau is a principal focal point in the Federal Government for assuring maxi- mum application of the physical and engineering sciences to the advancement of tech- nology in industry and commerce. To this end the Bureau conducts research and provides central national services in three broad program areas and provides cen- tral national services in a fourth. These are: (1) basic measurements and standards, (2) materials measurements and standards, (3) technological measurements and standards, and (4) transfer of technology. The Bureau comprises the Institute for Basic Standards, the Institute for Materials Research, the Institute for Applied Technology, and the Center for Radiation Research. THE INSTITUTE FOR BASIC STANDARDS provides the central basis within the United States of a complete and consistent system of physical measurement, coor- dinates that system with the measurement systems of other nations, and furnishes essential services leading to accurate and uniform physical measurements throughout the Nation’s scientific community, industry, and commerce. -
9241571063-Eng.Pdf (551.3Kb)
Environmental Health Criteria 106 Beryllium Please note that the layout and pagination of this web version are not identical with the printed version. Beryllium (EHC 106, 1990) INTERNATIONAL PROGRAMME ON CHEMICAL SAFETY ENVIRONMENTAL HEALTH CRITERIA 106 BERYLLIUM This report contains the collective views of an international group of experts and does not necessarily represent the decisions or the stated policy of the United Nations Environment Programme, the International Labour Organisation, or the World Health Organization. Published under the joint sponsorship of the United Nations Environment Programme, the International Labour Organisation, and the World Health Organization World Health Orgnization Geneva, 1990 The International Programme on Chemical Safety (IPCS) is a joint venture of the United Nations Environment Programme, the International Labour Organisation, and the World Health Organization. The main objective of the IPCS is to carry out and disseminate evaluations of the effects of chemicals on human health and the quality of the environment. Supporting activities include the development of epidemiological, experimental laboratory, and risk-assessment methods that could produce internationally comparable results, and the development of manpower in the field of toxicology. Other activities carried out by the IPCS include the development of know-how for coping with chemical accidents, coordination of laboratory testing and epidemiological studies, and promotion of research on the mechanisms of the biological action of chemicals. WHO Library Cataloguing in Publication Data Beryllium. (Environmental health criteria ; 106) 1.Beryllium I.Series ISBN 92 4 157106 3 (NLM Classification: QV 275) ISSN 0250-863X Page 1 of 136 Beryllium (EHC 106, 1990) The World Health Organization welcomes requests for permission to reproduce or translate its publications, in part or in full. -
Chemistry of Ammonothermal Synthesis
Inorganics 2014, 2, 29-78; doi:10.3390/inorganics2010029 OPEN ACCESS inorganics ISSN 2304-6740 www.mdpi.com/journal/inorganics Review Chemistry of Ammonothermal Synthesis Theresia M. M. Richter and Rainer Niewa * Institut fur¨ Anorganische Chemie, Universitat¨ Stuttgart, Pfaffenwaldring 55, Stuttgart 70569, Germany; E-Mail: [email protected] * Author to whom correspondence should be addressed; E-Mail: [email protected]; Tel.: +49-711-685-64217; Fax: +49-711-685-64241. Received: 10 December 2013; in revised form: 21 January 2014 / Accepted: 27 January 2014 / Published: 28 February 2014 Abstract: Ammonothermal synthesis is a method for synthesis and crystal growth suitable for a large range of chemically different materials, such as nitrides (e.g., GaN, AlN), amides (e.g., LiNH2, Zn(NH2)2), imides (e.g., Th(NH)2), ammoniates (e.g., Ga(NH3)3F3, [Al(NH3)6]I3 · NH3) and non-nitrogen compounds like hydroxides, hydrogen sulfides and polychalcogenides (e.g., NaOH, LiHS, CaS, Cs2Te5). In particular, large scale production of high quality crystals is possible, due to comparatively simple scalability of the experimental set-up. The ammonothermal method is defined as employing a heterogeneous reaction in ammonia as one homogenous fluid close to or in supercritical state. Three types of milieus may be applied during ammonothermal synthesis: ammonobasic, ammononeutral or ammonoacidic, evoked by the used starting materials and mineralizers, strongly influencing the obtained products. There is little known about the dissolution and materials transport processes or the deposition mechanisms during ammonothermal crystal growth. However, the initial results indicate the possible nature of different intermediate species present in the respective milieus. -
Separation of Zirconium--Hafnium by Nitride Precipitation
United States Patent [19] [li] 4,036,637 Anderson et al. BEST AVAILABLE COPY [45] July 19,1977 [54] SEPARATION OF ZIRCONIUM-HAFNIUM 3,857,919 12/1974 Hazen et al 423/73 BY NITRIDE PRECIPITATION Primary Examiner—Leland A. Sebastian [75] Inventors: Robert N. Anderson, Palo Alto; Assistant Examiner—Josephine Lloyd Norman A. Parlee, Los Altos Hills, Attorney, Agent, or Firm—Flehr, Hohbach, Test, both of Calif. Albritton & Herbert [73] Assignee: Parlee-Anderson Corporation, Menlo [57] ABSTRACT Park, Calif. A method for the separation of a light reactive metal [21] Appl. No.: 517,581 (e.g., zirconium) from a heavy reactive metal (e.g., hafnium) by forming insoluble nitrides of the metals in a [22] Filed: Oct. 24, 1974 molten metal solvent (e.g., copper) inert to nitrogen and [51] Int. C1.2 .. C22B 34/00; C01G 23/00; having a suitable density for the light metal nitride to C01G 56/00 form a separate phase in the upper portion of the solvent [52] u.s. a 75/84; 423/3; and for the heavy metal nitride to form a separate phase 423/69; 423/73 in the lower portion of the solvent. Nitriding is per- [58] Field of Search 423/3, 69, 73; 75/84 formed by maintaining a nitrogen-containing atmo- sphere over the bath. The light and heavy metals may [56] References Cited be an oxide mixture and carbothermically reduced to U.S. PATENT DOCUMENTS metal form in the same bath used for nitriding. The nitrides are then separately removed and decomposed 1,580,650 4/1926 Coster 423/73 2,793,107 5/1957 Jazwinski 75/84 to form the desired separate metals.