a MMM/C. Eazzam?E N LT T- 'Y
Total Page:16
File Type:pdf, Size:1020Kb
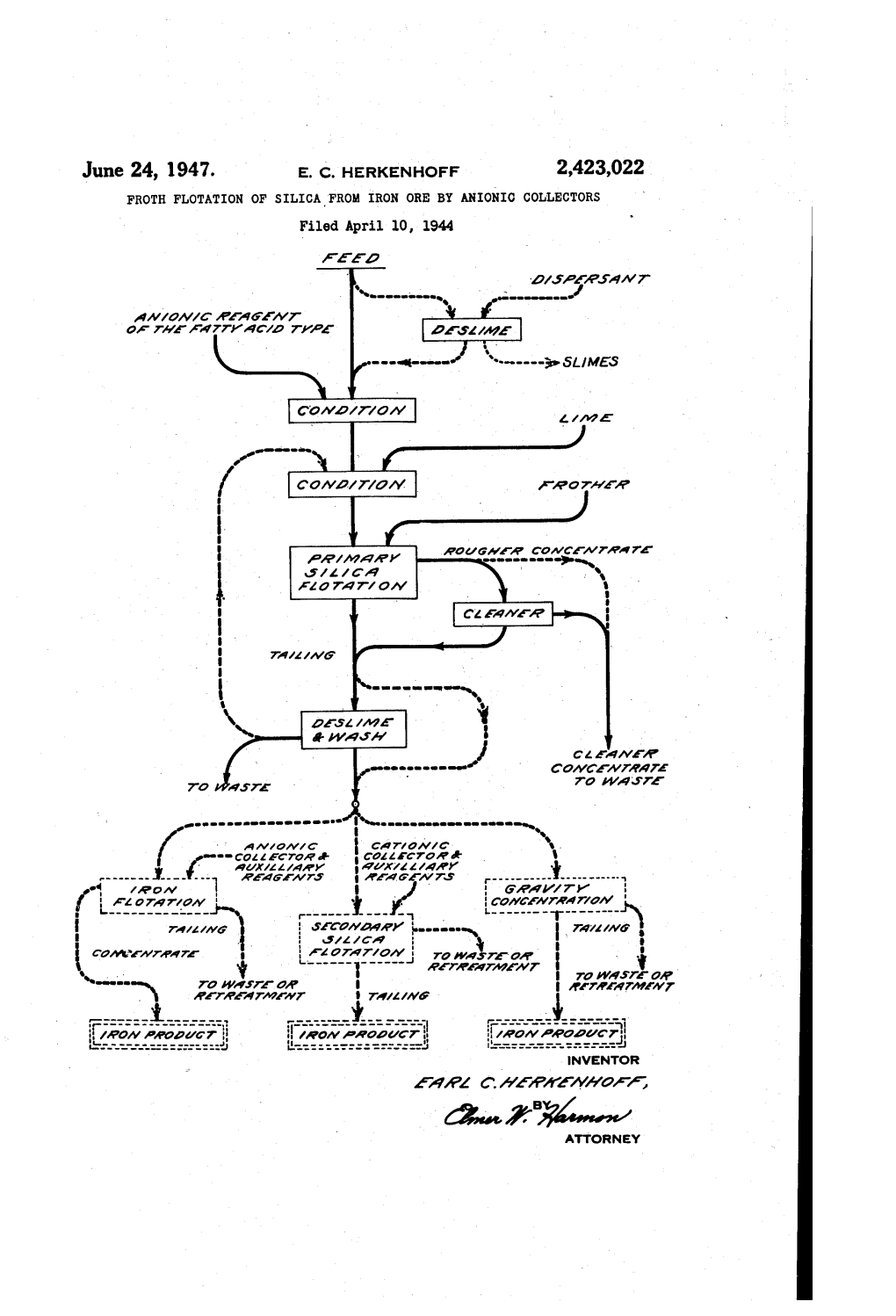
Load more
Recommended publications
-
A Study of a Carbonaceous Gold Ore James S
Montana Tech Library Digital Commons @ Montana Tech Bachelors Theses and Reports, 1928 - 1970 Student Scholarship 1941 A Study of a Carbonaceous Gold Ore James S. Huckaba Follow this and additional works at: http://digitalcommons.mtech.edu/bach_theses Part of the Ceramic Materials Commons, Environmental Engineering Commons, Geology Commons, Geophysics and Seismology Commons, Metallurgy Commons, Other Engineering Commons, and the Other Materials Science and Engineering Commons Recommended Citation Huckaba, James S., "A Study of a Carbonaceous Gold Ore" (1941). Bachelors Theses and Reports, 1928 - 1970. 147. http://digitalcommons.mtech.edu/bach_theses/147 This Bachelors Thesis is brought to you for free and open access by the Student Scholarship at Digital Commons @ Montana Tech. It has been accepted for inclusion in Bachelors Theses and Reports, 1928 - 1970 by an authorized administrator of Digital Commons @ Montana Tech. For more information, please contact [email protected]. ! -.. '_ _. r' ...: ,.... ,/'" f • . A STUJ.)Y C.u.RBON.u.CiiOUS GOLD By James S. Huckaba A Thesis ubmitted to the Departmen~ of etallurgy in }artial Fulf11~ent of the Requirouents fer the Degree of 2cchelor of ~cience in Jetallurgical ~n0ineering MONTAI~ SCI! OL OF r.mreB LIBRARY BUTTE " A S'J]UDY OF CARB ADEOUS GOLD ORE By ~mnes S. Huckaba I -4 D 70 s: Thesis Submi tted to the Dep artment of etallurgy in Partial Fulfillment of the Requirements for the Degree of Bachelor of Science in ~etallurgical Engineering MONTANA SCHOOL OF MINES LIBRARY, I - TABLE OF CONrENI'S -
The Separation of Galena and Blende from Their Gangue As Practised at the Mines of Sentein, Ariege, France
3% LUEIS ON THE SEPARATION OF GALENA AND BLENDE. [Selected (Paper No. 1942.) The Separation of Galena and Blende fiom their gangue as practised at the Mines of Sentein, Arihge, France.” By ERNESTDU BOISLUKIS, Assoc. M. Inst. C.E. THISis a record of detailed observations made whilst preparing formarket galena and blende, at the mines of Sentein in the Pyrenees. The oreswere intimately mixed in the proportion of 8 to 10 per cent. of galena, 15 to 20 percent. of blende, and gangue consisting of hard quartz, quartzose rock, schist, &c. The market lead-ore obtained included from 16 to 20 oz. of silver per ton.The blende did not contain sufficient silver for valuation. By experiments in the laboratory, it was found that the galena lost very little silver byfine crushing and washing. The machinery, supplied by Mr. George Green, of Aberystwyth, was erected in existing buildings; but these were so scattered that it is not thoughtnecessary to givea plan of them. Instead of this, a method of arranging the whole of the required plant under one roof, with slight modifications, that would render such proposed dressing-floors more efficient, is given in Plate 7, Figs. 1, the sub- stantialstructure indicated being necessary on account of the climate of the Pyrenees, where protection from frost and snow is indispensable. Water-power was used, being abundant, but the motors are not shown in Figs. 1, for, depending on the position of such proposed floors, steamor water wouldbe used asmight be found most advantageous. Mention is, however, made later on of the power required. -
FIG. 1 I Crush And/Or Grind to Free the Iron Oxide
Aug. 22, 1967 J‘ E. LAWVER 3,337,328 IRON ORE BENEFICIATION PROCESS Filed June 19, 1964 6 Sheets-Sheet l Heavy Media Tailings Tailing Pond Fines or Semitaconite 25 to 50% Iron FIG. 1 I Crush and/or Grind to Free the Iron Oxide Partial Concentration to Separate Iron Mineral from Waste Product by one of Following Processes or or A B C High Intensity Wet Froth Gravity Magnetic Separation Flotation Separation l l I I Partial Waste Partial Waste Partial Waste Concentrate Product Concentrate Product Concentrate Product L I I . Gravity Gravity Concentrates or Separation of Partial‘ Concentrates Low-grade Hematitic Ore From "An or “all or "ch 40 to 58%‘.Iron Crush and Grind to Liberate Silica Coarse Fraction Minus O. 010" plus 0.003" Fine Fraction‘ Less than 0.003" G to 75% Weight @ 25 to 100% Weight Electrodynamic Process to Separate Froth Flotation Process to Separate Iron Oxides and Silica Iron Oxides and Silica Silica Product to Waste Silica Product to Waste Iron Oxide Concentrate 62 to 65% Iron 5% Silica ' INVENTOR J9me; E. L’ AWl/ER 14 T TORNE Y! Aug. 22, 1967 J. e. LAWVER 3,337,328 IRON ORE BENEFICIATION PROCESS Filed ‘June 19, 1964 6 Sheets-Sheet 2 Crude Ore %Wt. 100. O0 FIG.' 2 %Fe%Insol.4l.l9 39 . 35 4" Screen -4" Ore +4" Ore %wt.84.45 %Wt. 15.39 %E‘e 4O. 19 %E'e 34. 75 %Inso]l . 48. 57 Crush 8 Screen %Fe Rec.l3.59 _ -___.______ +14 Mesh ~~14 Mesh Heavy Media Sands Slimes Separation '7‘Wt- 9-58 Spirals %E‘e 11.78 Sinks Floats ' Concentrate r(‘ailing %Wt. -
Control of Comminution Circuit for Efficient Froth Flotation D
FROTH FLOTATION : RECENT TRENDS @IIME, JAMSHEDPUR, 1998; pp. 10-17 Control of Comminution Circuit for Efficient Froth Flotation D. D. IVIIISRA ilndian School of Mines, :Marked] - 626004 ABSTRACT Efficiency of separation in the froth flotation circuit is rely much dependant on the efficiency of size reduction and size separation in the preceeding comminution and classification circuit. A coarser grinding product than desired causes loss of grade or recovery due to inadequate liberation where as with over grinding there is an increase in slime loss. This paper ennumerates the factors that affect the performance of the grinding circuit and the steps that should be taken for its efficient operation. Once the grinding circuit is commisioned its performance is dependant mainly on the operation and control of the classifier. In case of the mechanical classifiers very effective control can be obtained by suitably varying the wash water flow rate and the weir height. In case of the cyclone classifiers the control is some what difficult. Key Words : Comminution circuit, Control froth flotation, Operating parameters, Efficiency. INTRODUCTION The froth flotation process is extremely sensitive to the particle size. Ideally the particles should be just small enough to ensure liberation of the ore from the gangue and no smaller. In some rare cases of relatively high grade ore deposits some what acceptable liberation may take place at a size too large (+1 mm) to float in thd froth flotation, process. In such cases the ore should be ground to about -0.3 mm to ensure flotation as the flotation rate is observed to decrease rapidly with the increase in particle size. -
The Cornish Vanning Shovel Bryan Earl
The Cornish Vanning Shovel Bryan Earl First published in Tools & Trades Volume 10, 1997 A Shovel big enough to be a collier's banjo,I but made of light, 16-gauge, mild steel: here is something special, the Cornish Vanning Shovel. Its Function was to "try" or assay ores. On Vanning, and Assaying Generally Of entrancing simplicity, when properly used the shovel becomes a refined and pre cise instrument. In skilled hands it can reveal not only the presence of a whole range of valuable ores, but also their con centration. Its greatest use was by miners in the West of England for examining tin ores: rocks holding the mineral cassiterite (Sn02). Such ores are considered rich if they hold 5% are more of metal, valuable down to I % and workable, by the legendary "tinstreamers", down to 0.1%. The tin streamers were "tinners" who chiefly made their living by extracting the values left in stream and river beds, originating either from the natural breakdown of lodes, or discharged as waste "tailings" from a mine. Tinners also frequently bought orestuff from workers who had small mines or who picked over old mine dumps but did not have the resources to treat the "stuff' to reach a grade of tin con Wilfred Bray making a vanning assay in the South centrate that could be sold to a "blower" or Crofty assay laboratory. Apart from assaying he was a . talented musician and composed for his harmonium, are smelter. The are matenal Itself, the including a rousing "South Crofty" - unfortunately the cassiterite, is usually of a drab brown score for this appears to have been lost The la~e Frank colour entrapped in waste "gangue" rock Hutchm, chief assayer of the mme, considered him to be .' . -
A Partial Glossary of Spanish Geological Terms Exclusive of Most Cognates
U.S. DEPARTMENT OF THE INTERIOR U.S. GEOLOGICAL SURVEY A Partial Glossary of Spanish Geological Terms Exclusive of Most Cognates by Keith R. Long Open-File Report 91-0579 This report is preliminary and has not been reviewed for conformity with U.S. Geological Survey editorial standards or with the North American Stratigraphic Code. Any use of trade, firm, or product names is for descriptive purposes only and does not imply endorsement by the U.S. Government. 1991 Preface In recent years, almost all countries in Latin America have adopted democratic political systems and liberal economic policies. The resulting favorable investment climate has spurred a new wave of North American investment in Latin American mineral resources and has improved cooperation between geoscience organizations on both continents. The U.S. Geological Survey (USGS) has responded to the new situation through cooperative mineral resource investigations with a number of countries in Latin America. These activities are now being coordinated by the USGS's Center for Inter-American Mineral Resource Investigations (CIMRI), recently established in Tucson, Arizona. In the course of CIMRI's work, we have found a need for a compilation of Spanish geological and mining terminology that goes beyond the few Spanish-English geological dictionaries available. Even geologists who are fluent in Spanish often encounter local terminology oijerga that is unfamiliar. These terms, which have grown out of five centuries of mining tradition in Latin America, and frequently draw on native languages, usually cannot be found in standard dictionaries. There are, of course, many geological terms which can be recognized even by geologists who speak little or no Spanish. -
Morenci) Mining District, Greenlee County, Arizona David F
History of the Copper Mountain (Morenci) Mining District, Greenlee County, Arizona David F. Briggs Freeport-McMoRan’s Morenci operation November 2016 CONTRIBUTED REPORT CR-16-C Arizona Geological Survey www.azgs.az.gov | repository.azgs.az.gov Arizona Geological Survey Phil A. Pearthree, Interim Director Manuscript approved for publication in November 2016 Printed by the Arizona Geological Survey All rights reserved For an electronic copy of this publication: www.repository.azgs.az.gov For information on the mission, objectives or geologic products of the Arizona Geological Survey visit www.azgs.az.gov. This publication was prepared by a department of the University of Arizona. The Univer- sity of Arizona, or any department thereof, or any of their employees, makes no warranty, expressed or implied, or assumes any legal liability or responsibility for the accuracy, completeness, or usefulness of any information, apparatus, product, or process disclosed in this report. Any use of trade, product, or firm names in this publication is for descriptive purposes only and does not imply endorsement by the University of Arizona Arizona Geological Survey Contributed Report series provides non-AZGS authors with a forum for publishing documents concerning Arizona geology. While review comments may have been incorpo- rated, this document does not necessarily conform to AZGS technical, editorial, or policy standards. The Arizona Geological Survey issues no warranty, expressed or implied, regarding the suitability of this product for a particular use. Moreover, the Arizona Geological Survey shall not be liable un- der any circumstances for any direct, indirect, special, incidental, or consequential damages with respect to claims by users of this product. -
British Geological Survey
BRITISH GEOLOGICAL SURVEY Mineralogy and Petrology Short Report Series Short Report No. MPSR/99/24 RECOVERING THE LOST GOLD OF THE DEVELOPING WORLD: BIBLIOGRAPHIC DATABASE E J Evans & C J Mitchell Date 31/03/99 Classification Open Geographical Index World-wide Subject index Gold, mercury, mineral processing, gravity, sluice, Bibliographic reference E J Evans & C J Mitchell Recovering the lost gold of the developing world: bibliographic database Mineralogy and Petrology Group Short Report MPSR/99/24 ©NERC 1999 British Geological Survey, Keyworth, Nottingham. NG12 5GG. UK. MPSR/99/24 31103/99 BRITISH GEOLOGICAL SURVEY Mineralogy and Petrology Group Short Report No. MPSR/99/24 Recovering the lost gold of the developing world: bibliographic database E J Evans & C J Mitchell INTRODUCTION This report contains a library of 181 references, including abstracts, prepared for Project R 7120 "Recovering the lost gold of the developing world" funded by the UK' s Department for International Development (DFID) under the Knowledge and Research (KAR) programme. As part of an initial desk study, a literature review of gold processing methods used by small-scale miners was carried out using the following sources; the lSI Science Citation Index accessed via Bath Information and Data Services (BIDS), a licensed GEOREF CD-ROM database held at the BGS's Library in Keyworth and IMMage a CD-ROM database produced by the Institution of Mining and Metallurgy held by the Minerals group ofBGS. Information on the search terms used is available from the author. Results of this literature review were compiled in digital form as an Endnote® bibliographic library containing 181 individual references. -
Tin and Silver Recovery from Coal Creek, AK
lrl C~ RI 9356 REPORT OF INVESTIGATIONS/1991 Tin and Silver Recovery From Coal Creek, AK By J. L. Johnson and T. Parker UNITED STATES DEPARTMENT OF THE INTERIOR BUREAU OF MINES ..., \LS p."r!'::ll( of Mines $, :.'s~2r:::h Center t, .. ' i ~·:t:::iO:i1ery Ave. \.c,' I ,t-',!fI ~ 11 C:9207v L~ ~ l{f:~f{Y Mission: Asthe Nation's principal conservation agency, the Department of the Interior has respon sibility for most of our nationally-owned public lands and natural and cultural resources. This includes fostering wise use of our land and water resources, protecting our fish and wildlife, pre serving the environmental and cultural values of our national parks and historical places, and pro viding for the enjoyment of life through outdoor recreation. The Department assesses our energy and mineral resources and works to assure that their development is in the best interests of all our people. The Department also promotes the goals of the Take Pride in America campaign by encouraging stewardship and citizen respohsibil ity for the public lands and promoting citizen par ticipation in their care. The Department also has a major responsibility for American Indian reser vation communities and for people who live in Island Territories under U.S. Administration. Report of Investigations 9356 Tin and Silver Recovery From Coal Creek, AK By J. L Johnson and T. Parker UNITED STATES DEPARTMENT OF THE INTERIOR Manuel Lujan, Jr., Secretary BUREAU OF MINES T S Ary, Director Library of Congress Cataloging in Publication Data: Johnson, J. L. Tin and silver recovery from Coal Creek, AK / by J.L. -
TIN SMELTING at the ORIENTAL INSTITUTE by Bryan Earl, Metals Specialist, and K
oi.uchicago.edu THE ORIENTAL INSTITUTE NEWS & NOTES NO. 146 SUMMER 1995 @THE ORIENTAL INSTITUTE OF THE UNIVERSITY OF CHICAGO TIN SMELTING AT THE ORIENTAL INSTITUTE By Bryan Earl, Metals Specialist, and K. Aslzhan Yener, Assistant Professor, The Oriental Institute and the Department of Near Eastern Languages and Civilizations Several experimental smelting procedures were tested both in Because of the problems associated with the finding, min the field in Turkey and at the Oriental Institute by our metals ing, and smelting of tin, any assessment of tin work at an an specialist, Bryan Earl from Cornwall, with additional analysis cient site should be based on a highly practical examination. by Dr. Hadi Ozbal of Istanbul. A video camera documented It is necessary to apply a wide range of very refmed techniques both experiments, while photographs and slides were also to gain an understanding of the details of the operation, any taken for future publication. The courtyard of the Oriental In significant conditions that controlled what had happened, and stitute served as the setting for the smelting experiment, which the character of the materials resulting from the work. The trial was widely witnessed by faculty, at the Oriental Institute demon staff, and students from the Ori strated the methods that had been ental Institute. Scientists from adopted for the initial assessment other departments of the Univer of the Kestel and Goltepe sites in sity of Chicago such as Turkey. Using material from chemistry, geophysics, Enrico Goltepe, it was shown that tin Fermi Institute, as well as re mining and smelting, using meth searchers from the Field Museum ods that had been deduced by ex and the Illinois Institute of Tech amination of the archaeological nology also joined the evidence, were entirely practical. -
Laboratory and Pilot Size Materials Testing and Handling Equipment for the Process Industries
LABORATORY AND PILOT SIZE MATERIALS TESTING AND HANDLING EQUIPMENT FOR THE PROCESS INDUSTRIES www.sepor.com • [email protected] 718 N Fries Ave., Wilmington, CA 90744 • Phone: 310-830-6601 Fax: 310-830-9336 Sepor, Inc has re-designed our website sepor.com. This reference will give you an abbreviated list of our complete range of mineral process and pilot scale equipment. Sepor has provided equipment to the mining and process industries for more than 55 years. Sepor has made many enhancements to our internet site. Some of these enhancements include: search capability, a "quick search" function, and downloadable product information sheets. We encourage you to check out our revised information. Sepor does not intend to publish our 128 page catalog of products and will rely on giving our customers the most current and useful information via our internet location. As always, Sepor has people with experience in the process industries to assist with your particular application. Sepor has incorporated an optional one-time login information entry. By entering your personal login name and password, your contact information will only need to be entered once. This is optional and is not required to visit our site or to view product information. Visit us today!! www.sepor.com Phone: 310-830-6601 Fax: 310-830-9336 Sepor now accepts VISA and MASTERCARD Table of Contents Product Code Page Crushing & Grinding ......................................... 010 1-2 Solids Handling ................................................. 020 3 Pumps, Air Compressors and Dust Control ....... 030 4 Screening and Sampling Equipment ................. 040 5-7 Gravity Separation / Concentration ................... 050 8-9 Magnetic / Electro Separation .......................... -
Hardcoverisbn-0-393-20788-0). PUB TYPE Books (010) -- Reports - Research/Technical (143)
DOCUMENT RESUME ED 323 088 SE 051 538 AUTHOR Brown, Lester R.; And Others TITLE Stai-p of +110 WorlA 1990. A WorlAwatch Institute Report on Progress toward a Sustainable Society. INSTITUTION Worldwatch Inst., Washington, D.C. REPORT NO ISBN-0-393-30614-3 PUB DATE 90 NOTE 268p. AVAILABLE FROMW. W. Norton and Company, Inc., 500 Fifth Avenue, New York, NY 10110 ($9.95; hardcoverISBN-0-393-20788-0). PUB TYPE Books (010) -- Reports - Research/Technical (143) EDRS PRICE MF01/PC11 Plus Postage. DESCRIPTORS Air Pollution; *Conservation (Environment); Energy Conservation; *Environmental Education; *Global Approach; Higher Education; *International Cooperation; *Natural Resources; Postsecondary EducaLion; Productivity; Water IDENTIFIERS *Global Climate Change ABSTRACT As the world enters the last decade of the 20th century, tLe environmental problems facing human societies have been given increased emphasis in world policy debates. The goal of the Worldwatch Institute is to help raise the level of public understanding of global environmental threats to the point where the public will support policies needed to reverse these trends. This document focuses on major policy initiatives needed to stabilize the global environment for human civilization. In this seventh annual issue of the description of the status of global environmental problems, 10 issues are presented and discussed. These issues include:(1) progress and productivity; (2) global climate change; (3) global water supplies;(4) global food supplies;(5) sea level changes;(6) air quality;(7) global bicycle use;(8) poverty; (9) the proliferation of peace; and (10) efforts to sustain world resources. (CW) *********************************************************************** Reproductions supplied by EDRS are the best that can be made from the original document.