FIG. 1 I Crush And/Or Grind to Free the Iron Oxide
Total Page:16
File Type:pdf, Size:1020Kb
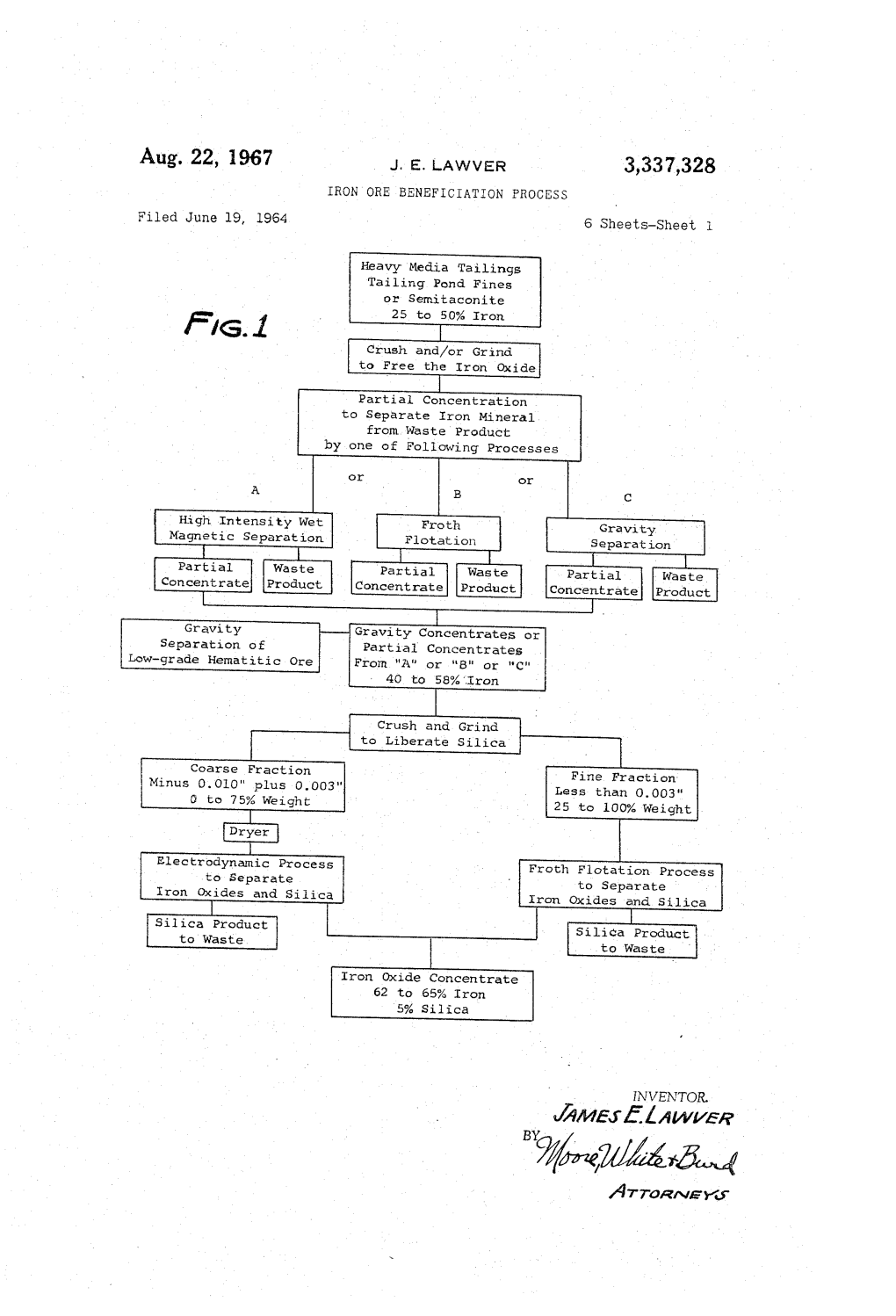
Load more
Recommended publications
-
Positive PFS Results for Razorback High Grade Iron Ore Concentrate Project
ASX Announcement 5 July 2021 Positive PFS Results for Razorback High Grade Iron Ore Concentrate Project Highlights: • Pre Feasibility Study completed and scope defined for Definitive Feasibility Study • PFS supports declaration of a maiden ore reserve of 473mt based on a 12.8Mtpa plant throughput, backed by PFS level or AACE Class 4 capital cost estimates and/or third-party service proposals1 • Optimisation of the processing plant configuration with a nominal 15.5Mtpa feed plant utilising three grinding stages, three stage magnetic separation and flotation to generate a premium grade magnetite concentrate with 67.5 - 68.5% Fe content • Non-process infrastructure and transport studies confirm preferred scope for operating inputs and initial route selection to load annual production of between 2 and 3 Mtpa of high grade concentrate on to Cape size vessels • Initial capital investment of US$429-$506M (A$572-$675M) resulting in optimised case results of NPV of A$669M and 20% IRR for selected go-forward case at long run average prices (post tax, ungeared) • Preparation for a prompt commencement of Definitive Feasibility Study is well advanced with further drilling, testwork, metallurgical investigation and engineering workplans in progress Magnetite Mines Limited (Magnetite Mines or the Company) today announced the results of the Pre Feasibility Study (PFS) for development of its 100% owned Razorback High Grade Iron Ore Concentrate Project (the Project or Razorback) and is now proceeding with the Definitive Feasibility Study (DFS). The PFS has confirmed the opportunity for a high return, long life, initial development of the large scale Razorback resource which leverages the advantages of resource scale, low stripping ratio, available infrastructure, low cost sustainable power and leading product quality. -
Recovery of Magnetite-Hematite Concentrate from Iron Ore Tailings
E3S Web of Conferences 247, 01042 (2021) https://doi.org/10.1051/e3sconf/202124701042 ICEPP-2021 Recovery of magnetite-hematite concentrate from iron ore tailings Mikhail Khokhulya1,*, Alexander Fomin1, and Svetlana Alekseeva1 1Mining Institute of Kola Science Center of Russian Academy of Sciences, Apatity, 184209, Russia Abstract. The research is aimed at study of the probable recovery of iron from the tailings of the Olcon mining company located in the north-western Arctic zone of Russia. Material composition of a sample from a tailings dump was analysed. The authors have developed a separation production technology to recover magnetite-hematite concentrate from the tailings. A processing flowsheet includes magnetic separation, milling and gravity concentration methods. The separation technology provides for production of iron ore concentrate with total iron content of 65.9% and recovers 91.0% of magnetite and 80.5% of hematite from the tailings containing 20.4% of total iron. The proposed technology will increase production of the concentrate at a dressing plant and reduce environmental impact. 1 Introduction The mineral processing plant of the Olcon JSC, located at the Murmansk region, produces magnetite- At present, there is an important problem worldwide in hematite concentrate. The processing technology the disposal of waste generated during the mineral includes several magnetic separation stages to produce production and processing. Tailings dumps occupy huge magnetite concentrate and two jigging stages to produce areas and pollute the environment. However, waste hematite concentrate from a non-magnetic fraction of material contains some valuable components that can be magnetic separation [13]. used in various industries. In the initial period of plant operation (since 1955) In Russia, mining-induced waste occupies more than iron ore tailings were stored in the Southern Bay of 300 thousand hectares of lands. -
Treatment and Microscopy of Gold
TREATMENT AND MICROSCOPY OF GOLD AND BASE METAL ORES. (Script with Sketches & Tables) Short Course by R. W. Lehne April 2006 www.isogyre.com Geneva University, Department of Mineralogy CONTENTS (Script) page 1. Gold ores and their metallurgical treatment 2 1.1 Gravity processes 2 1.2 Amalgamation 2 1.3 Flotation and subsequent processes 2 1.4 Leaching processes 3 1.5 Gold extraction processes 4 1.6 Cyanide leaching vs. thio-compound leaching 5 2. Microscopy of gold ores and treatment products 5 2.1 Tasks and problems of microscopical investigations 5 2.2 Microscopy of selected gold ores and products 6 (practical exercises) 3. Base metal ores and their beneficiation 7 3.1 Flotation 7 3.2 Development of the flotation process 7 3.3 Principles and mechanisms of flotation 7 3.4 Column flotation 9 3.5 Hydrometallurgy 10 4. Microscopy of base metal ores and milling products 10 4.1 Specific tasks of microscopical investigations 11 4.2 Microscopy of selected base metal ores and milling products 13 (practical exercises) 5. Selected bibliography 14 (Sketches & Tables) Different ways of gold concentration 15 Gravity concentration of gold (Agricola) 16 Gravity concentration of gold (“Long Tom”) 17 Shaking table 18 Humphreys spiral concentrator 19 Amalgamating mills (Mexican “arrastra”, Chilean “trapiche”) 20 Pressure oxidation flowsheet 21 Chemical reactions of gold leaching and cementation 22 Cyanide solubilities of selected minerals 23 Heap leaching flowsheet 24 Carbon in pulp process 25 Complexing of gold by thio-compounds 26 Relation gold content / amount of particles in polished section 27 www.isogyre.com Economically important copper minerals 28 Common zinc minerals 29 Selection of flotation reagents 30 Design and function of a flotation cell 31 Column cell flotation 32 Flowsheet of a simple flotation process 33 Flowsheet of a selective Pb-Zn flotation 34 Locking textures 35 2 1. -
Addressing the Information Gaps on Prices of Minerals Sold in an Intermediate Form
The Platform for Cooperation on Tax DISCUSSION DRAFT: Addressing the Information Gaps on Prices of Minerals Sold in an Intermediate Form Feedback Period 24 January 2017 – 21 February 2017 Organisation for Economic Co-operation and Development (OECD) World Bank Group (WBG) International Monetary Fund (IMF) United Nations (UN) 1 This discussion draft has been prepared in the framework of the Platform for Collaboration on Tax by the OECD, under the responsibility of the Secretariats and Staff of the four mandated organisations. The draft reflects a broad consensus among these staff, but should not be regarded as the officially endorsed views of those organisations or of their member countries. 1 Table of Contents Introduction................................................................................................................................................................ 6 Domestic Resource Mobilisation from Mining......................................................................................... 6 Report Structure ................................................................................................................................................... 9 Building An Understanding of the Mining Sector – A Methodology ................................................ 10 Introduction ........................................................................................................................................................ 10 Steps in the Methodology ........................................................................................................................... -
An Issue Dedicated to Solutions for the Modern Mining Industry
Metso’s customer magazine » ISSUE 1/2017 Mining minds An issue dedicated to solutions for the modern mining industry More efficiency Six-fold reduction Longer wear life and with less energy in moisture content fewer liner changes 06 and water 18 at Olenegorsky GOK 28 reduce costs “Metso has gone beyond combining and re-releasing technology based on prior designs. Its solution is more efficient, lasts longer and reduces operating costs.” mining Results mining is PUBLISHED BY EDITOR-IN-CHIEF © Copyright 2017 PRINTING Metso’s customer magazine Metso Corporation Inka Törmä, Metso Corporation. Hämeen Kirjapaino Oy, showcasing our work and [email protected] All rights reserved. February 2017 Töölönlahdenkatu 2, the success of our customers. P.O. Box 1220, DESIGN AND LAYOUT Reproduction permitted ISSN SUBSCRIPTIONS FI-00101 Helsinki, Brandkind, brandkind.fi quoting “Results mining” 2343-3590 To receive your personal Finland as source. ENGLISH LANGUAGE ADDRESSES 4041 0209 copy, please contact your Printed matter tel. +358 20 484 100 Kathleen Kuosmanen All product names used Metso customer data nearest Metso office or HÄMEEN KIRJAPAINO OY www.metso.com are trademarks of their the e-mail provided. respective owners. This magazine, including all claims regarding operational performance, is intended for sharing information on successful customer cases. Metso makes no warranty or representation whatsoever, either express or implied, that similar or any performance levels or improvements are achievable for all sites or for any particular site. Metso assumes no legal liability for any use of information contained in this presentation. If requested, Metso can execute a site specific survey to provide an estimate of performance or performance improvement for a specific site and operation. -
Charge Calculations in Pyrometallurgical Processes
Charge Calculations in Pyrometallurgical Processes Smelting It is a unit process similar to roasting, to heat a mixture of ore concentrate above the melting point The objective is to separate the gangue mineral from liquid metal or matte The state of the gangue mineral in case of smelting is liquid which is the main difference between roasting and smelting Inputs – Ore, flux, fuel, air Output – Metal or Matte, slag, off-gas When metal is separated as sulphide from smelting of ore, it is called Matte smelting e.g. Cu2S and FeS When metal is separated as liquid, it is called reduction smelting e.g. Ironmaking Density of liquid metal or matte is around 5-5.5 g/cm3 Density of slag is around 2.8-3 g/cm3 The additives and fluxes serve to convert the waste or gangue materials in the charge into a low melting point slag which also dissolves the coke ash and removes sulphur Matte Smelting Advantages of matte smelting • Low melting point of matte so that less amount of thermal energy is required by converting the metal of the ore in the form of sulphide and then extracting the metal e.g. melting point of Cu2S and FeS is around 1000 degrees Celsius • Cu2S which is contained in the matte, does not require any reducing agent It is converted to oxide by blowing oxygen • Matte smelting is beneficial for extraction of metal from sulphide ore, particularly when sulphide ore is associated with iron sulphide which forms eutectic point with Cu and Ni The grade of the matte is defined as the copper grade of matte A matte of 40 percent means, it has 40% copper, so matte is always given in terms of copper, because it is used to produce copper not iron Slag in matte smelting is mixture of oxides e.g. -
India's Contribution to the Mining, Extraction and Refining of Gold: Some Observations Related to the Pre-Christian Era
0 2001 NML Jamshedpur 831 007, India; Metallurgy in India: A Retrospective; (ISBN: 81-87053-56-7); Eds: P. Ramachandra Rao and N.G. Goswami; pp.163-181. 8 India's Contribution to the Mining, Extraction and Refining of Gold: Some Observations Related to the Pre-Christian Era ' R.K. Dube. • Department of Materials & Metallurgical Engineering, Indian Institute of Technology, Kanptir .208 016, India. ABSTRACT India has a very old and fascinating history of gold. Various aspects of the mining and metallurgy of gold were known to the Indians since time immemorial. In this paper, different types of the gold ore deposits', and the technique used in the extraction and refining of gold in ancient India as obtained from the literary sources 'composed in the pre-Christian era and some archaeological findings are discussed. The recovery of a novel variety of high purity gold powder, known as Pipilaka Gold, from the auriferous soil of ant-hills, as stated in the Maheibharata, has also been discussed. Key, words : Alluvial placer gold, Vein gold, Liquid ore of gold, Panning, Deep mining, Cupellation, Solid state refining of gold, Anks'r gold. INTRODUCTION Man and metal have an age-old relationship. Out of all metals known to man in ancient times, p-6i-haps gold was the first with which man became acquainted. Indians had, and still continue to have, great fascination for gold. Its special attributes, such as pleasing and untarnishing colour, excellent corrosion and . oxidation resistance, ease of forming, and limited availability made it an ideal metal for ornaments, decoration, currency, and store of wealth in ancient India. -
A Study of a Carbonaceous Gold Ore James S
Montana Tech Library Digital Commons @ Montana Tech Bachelors Theses and Reports, 1928 - 1970 Student Scholarship 1941 A Study of a Carbonaceous Gold Ore James S. Huckaba Follow this and additional works at: http://digitalcommons.mtech.edu/bach_theses Part of the Ceramic Materials Commons, Environmental Engineering Commons, Geology Commons, Geophysics and Seismology Commons, Metallurgy Commons, Other Engineering Commons, and the Other Materials Science and Engineering Commons Recommended Citation Huckaba, James S., "A Study of a Carbonaceous Gold Ore" (1941). Bachelors Theses and Reports, 1928 - 1970. 147. http://digitalcommons.mtech.edu/bach_theses/147 This Bachelors Thesis is brought to you for free and open access by the Student Scholarship at Digital Commons @ Montana Tech. It has been accepted for inclusion in Bachelors Theses and Reports, 1928 - 1970 by an authorized administrator of Digital Commons @ Montana Tech. For more information, please contact [email protected]. ! -.. '_ _. r' ...: ,.... ,/'" f • . A STUJ.)Y C.u.RBON.u.CiiOUS GOLD By James S. Huckaba A Thesis ubmitted to the Departmen~ of etallurgy in }artial Fulf11~ent of the Requirouents fer the Degree of 2cchelor of ~cience in Jetallurgical ~n0ineering MONTAI~ SCI! OL OF r.mreB LIBRARY BUTTE " A S'J]UDY OF CARB ADEOUS GOLD ORE By ~mnes S. Huckaba I -4 D 70 s: Thesis Submi tted to the Dep artment of etallurgy in Partial Fulfillment of the Requirements for the Degree of Bachelor of Science in ~etallurgical Engineering MONTANA SCHOOL OF MINES LIBRARY, I - TABLE OF CONrENI'S -
The Separation of Galena and Blende from Their Gangue As Practised at the Mines of Sentein, Ariege, France
3% LUEIS ON THE SEPARATION OF GALENA AND BLENDE. [Selected (Paper No. 1942.) The Separation of Galena and Blende fiom their gangue as practised at the Mines of Sentein, Arihge, France.” By ERNESTDU BOISLUKIS, Assoc. M. Inst. C.E. THISis a record of detailed observations made whilst preparing formarket galena and blende, at the mines of Sentein in the Pyrenees. The oreswere intimately mixed in the proportion of 8 to 10 per cent. of galena, 15 to 20 percent. of blende, and gangue consisting of hard quartz, quartzose rock, schist, &c. The market lead-ore obtained included from 16 to 20 oz. of silver per ton.The blende did not contain sufficient silver for valuation. By experiments in the laboratory, it was found that the galena lost very little silver byfine crushing and washing. The machinery, supplied by Mr. George Green, of Aberystwyth, was erected in existing buildings; but these were so scattered that it is not thoughtnecessary to givea plan of them. Instead of this, a method of arranging the whole of the required plant under one roof, with slight modifications, that would render such proposed dressing-floors more efficient, is given in Plate 7, Figs. 1, the sub- stantialstructure indicated being necessary on account of the climate of the Pyrenees, where protection from frost and snow is indispensable. Water-power was used, being abundant, but the motors are not shown in Figs. 1, for, depending on the position of such proposed floors, steamor water wouldbe used asmight be found most advantageous. Mention is, however, made later on of the power required. -
World Bank Document
ReportNo. 1351-BA Burma Appraisalof the Tin and TungstenExpansion Project Public Disclosure Authorized February8, 1977 Industrial ProjectsDepartment FOR OFFICIAL USEONLY Public Disclosure Authorized Public Disclosure Authorized Public Disclosure Authorized Document of the World Bank Thisdocument hasa restricteddistribution and may be usedby recipients only in the performanceof their officialduties. Its contents may not otherwise be disclosedwithout World Bankauthorization. CURRENCYEQUIVALENTS Except where otherwise indicated, all figures are quoted in Kyats (K) and US Dollars (US$). K 1.00 = US$0.15 K 6.65 = US$1.00 ABBRIVIATIONSAND ACRONYMS CIDA Canadian InternationalDevelopment Association DGSE Directorateof Geological Survey and Mineral Exploration Government Government of the SocialistRepublic of the Union of Burma KfW Kreditanstaltfur Wiederaufbau ITC InternationalTin Council LMB London Metal Bulletin LME London Metal Exchange LTPY Long tons per year MC2, the Corporation No. 2 Mining Corporation (formerlyMyanma Tin Tungsten Corporation - MTTC) MDC Mineral Development Corporation MEB Myanma Economic Bank IMEIC Myanma Export Import Corporation MMDC Myanma Mineral Development Corporation HOC Myanma Oil Corporation 1'PY Metric tons per year PTA Primary Tungsten Association UBB Union Bank of Burma UGCF Union Government ConsolidatedFund UNCTAD United Nations Conference on Trade and Development UNDP United Nations Development Program USBM US Bureau of Mines WBMS World Bureau of Metal Statistics WEIGHTSAND MEASURES 1 Hectare = 2.47 acres 1 Kilometer (km) = 0.62 miles 1 Long Ton (LT) = 2,240 pounds 1 Long Ton Unit (LTU) = 1% of a long ton or 22.4 pounds 1 Meter (m) = 39.3 inches 1 Metric Ton (MT) = 2,205 pounds 1 Metric Ton Unit (MTU)= 1% of a metric ton, or 22.05 pounds 1 Picul (Pikul) = 133.33 pounds FISCAL YEAR April 1 - March 31 Industrial Projects Department February 1977 FOR OFFICIAL USE ONLY BURMA APPRAISAL OF THE TIN AND TUNGSTEN EXPANSION PROJECT TABLE OF CONTENTS Page No. -
Fundamental Aspects of Alloy Smelting in a DC Arc Furnace
F U N D A M E N T A L A S P E C T S O F A L L O Y S M E L T I N G I N A D C A R C F U R N A C E ------------ Rodney Trevor Jones PhD 2015 F U N D A M E N T A L A S P E C T S O F A L L O Y S M E L T I N G I N A D C A R C F U R N A C E Rodney Trevor Jones A thesis submitted to the Faculty of Engineering and the Built Environment, University of the Witwatersrand, Johannesburg, in fulfilment of the requirements for the degree of Doctor of Philosophy Johannesburg, 2015 DECLARATION I declare that this thesis is my own unaided work. It is being submitted to the Degree of Doctor of Philosophy to the University of the Witwatersrand, Johannesburg. It has not been submitted before for any degree or examination to any other university. Much of the information presented in this thesis was obtained during the course of my employment in the Pyrometallurgy Division at Mintek in Randburg. 17 June 2015 DECLARATION I declare that this thesis is my own unaided work. It is being submitted to the Degree of Doctor of Philosophy to the University of the Witwatersrand, Johannesburg. It has not been submitted before for any degree or examination to any other university. Much of the information presented in this thesis was obtained during the course of my employment in the Pyrometallurgy Division at Mintek in Randburg. -
Control of Comminution Circuit for Efficient Froth Flotation D
FROTH FLOTATION : RECENT TRENDS @IIME, JAMSHEDPUR, 1998; pp. 10-17 Control of Comminution Circuit for Efficient Froth Flotation D. D. IVIIISRA ilndian School of Mines, :Marked] - 626004 ABSTRACT Efficiency of separation in the froth flotation circuit is rely much dependant on the efficiency of size reduction and size separation in the preceeding comminution and classification circuit. A coarser grinding product than desired causes loss of grade or recovery due to inadequate liberation where as with over grinding there is an increase in slime loss. This paper ennumerates the factors that affect the performance of the grinding circuit and the steps that should be taken for its efficient operation. Once the grinding circuit is commisioned its performance is dependant mainly on the operation and control of the classifier. In case of the mechanical classifiers very effective control can be obtained by suitably varying the wash water flow rate and the weir height. In case of the cyclone classifiers the control is some what difficult. Key Words : Comminution circuit, Control froth flotation, Operating parameters, Efficiency. INTRODUCTION The froth flotation process is extremely sensitive to the particle size. Ideally the particles should be just small enough to ensure liberation of the ore from the gangue and no smaller. In some rare cases of relatively high grade ore deposits some what acceptable liberation may take place at a size too large (+1 mm) to float in thd froth flotation, process. In such cases the ore should be ground to about -0.3 mm to ensure flotation as the flotation rate is observed to decrease rapidly with the increase in particle size.