US 2001/0013826A1 AHMED Et Al
Total Page:16
File Type:pdf, Size:1020Kb
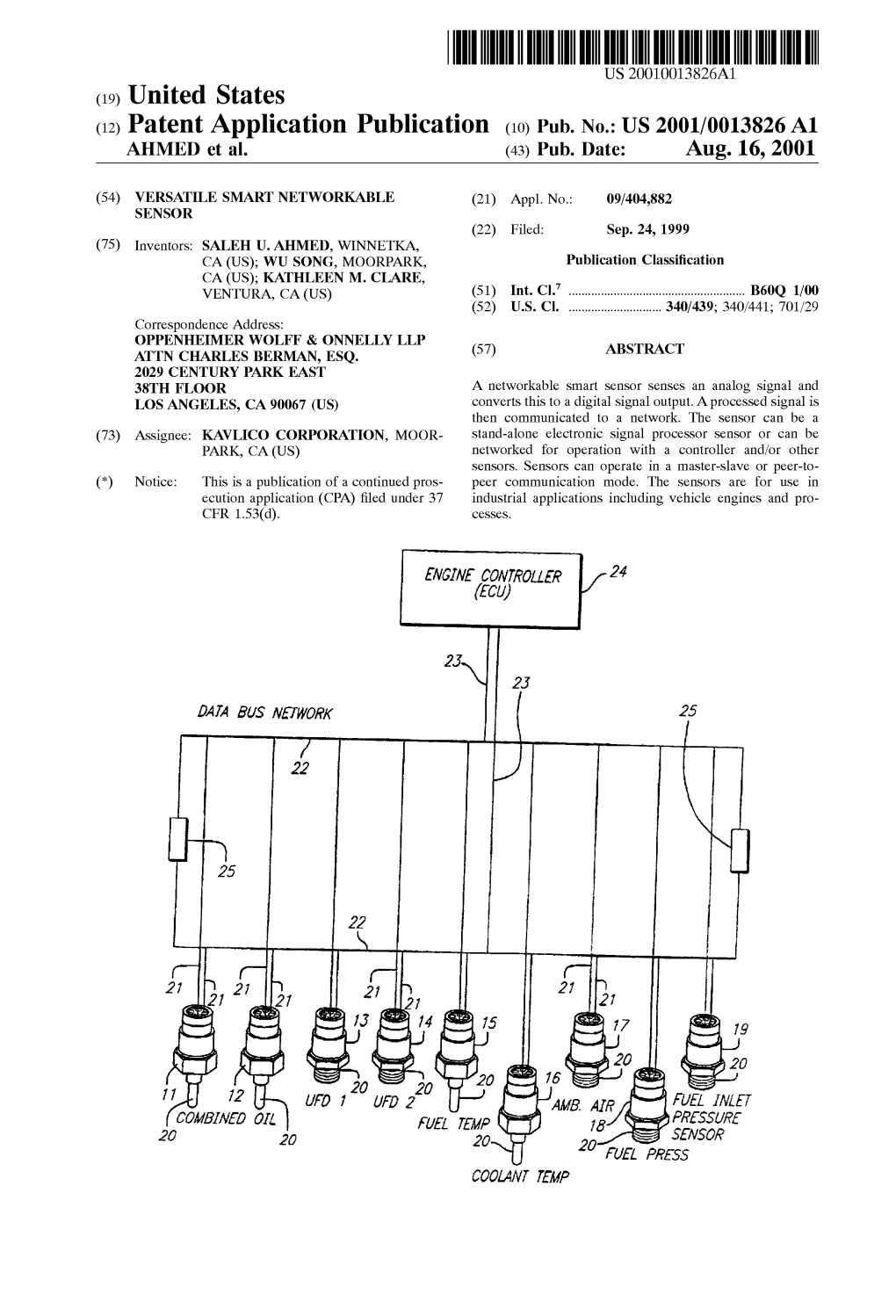
Load more
Recommended publications
-
SAE J1587 (2002 Standard).Pdf
SURFACE REV. VEHICLE J1587 FEB2002 RECOMMENDED Issued 1988-01 400 Commonwealth Drive, Warrendale, PA 15096-0001 PRACTICE Revised 2002-02 Superseding J1587 JUL1998 Electronic Data Interchange Between Microcomputer Systems in Heavy-Duty Vehicle Applications 1. Scope—This SAE Recommended Practice defines a document for the format of messages and data that is of general value to modules on the data communications link. Included are field descriptions, size, scale, internal data representation, and position within a message. This document also describes guidelines for the frequency of and circumstances in which messages are transmitted. In order to promote compatibility among all aspects of electronic data used in heavy-duty applications, it is the intention of the SAE Truck and Bus Low Speed Communications Network Subcommittee (formerly Data Format Subcommittee) (in conjunction with other industry groups) to develop recommended message formats for: a. Vehicle and Component Information—This includes all information that pertains to the operation of the vehicle and its components (such as performance, maintenance, and diagnostic data). b. Routing and Scheduling Information—Information related to the planned or actual route of the vehicle. It includes current vehicle location (for example, geographical coordinates) and estimated time of arrival. c. Driver Information—Information related to driver activity. Includes driver identification, logs, (for example, DOT), driver expenses, performance, status, and payroll data. d. Freight Information—Provides data associated with cargo being shipped, picked up, or delivered. Includes freight status, overage, shortage and damage reporting, billing and invoice information as well as customer and consignee data. This document represents the recommended formats for basic vehicle and component identification and performance data. -
SAE International® PROGRESS in TECHNOLOGY SERIES Downloaded from SAE International by Eric Anderson, Thursday, September 10, 2015
Downloaded from SAE International by Eric Anderson, Thursday, September 10, 2015 Connectivity and the Mobility Industry Edited by Dr. Andrew Brown, Jr. SAE International® PROGRESS IN TECHNOLOGY SERIES Downloaded from SAE International by Eric Anderson, Thursday, September 10, 2015 Connectivity and the Mobility Industry Downloaded from SAE International by Eric Anderson, Thursday, September 10, 2015 Other SAE books of interest: Green Technologies and the Mobility Industry By Dr. Andrew Brown, Jr. (Product Code: PT-146) Active Safety and the Mobility Industry By Dr. Andrew Brown, Jr. (Product Code: PT-147) Automotive 2030 – North America By Bruce Morey (Product Code: T-127) Multiplexed Networks for Embedded Systems By Dominique Paret (Product Code: R-385) For more information or to order a book, contact SAE International at 400 Commonwealth Drive, Warrendale, PA 15096-0001, USA phone 877-606-7323 (U.S. and Canada) or 724-776-4970 (outside U.S. and Canada); fax 724-776-0790; e-mail [email protected]; website http://store.sae.org. Downloaded from SAE International by Eric Anderson, Thursday, September 10, 2015 Connectivity and the Mobility Industry By Dr. Andrew Brown, Jr. Warrendale, Pennsylvania, USA Copyright © 2011 SAE International. eISBN: 978-0-7680-7461-1 Downloaded from SAE International by Eric Anderson, Thursday, September 10, 2015 400 Commonwealth Drive Warrendale, PA 15096-0001 USA E-mail: [email protected] Phone: 877-606-7323 (inside USA and Canada) 724-776-4970 (outside USA) Fax: 724-776-0790 Copyright © 2011 SAE International. All rights reserved. No part of this publication may be reproduced, stored in a retrieval system, distributed, or transmitted, in any form or by any means without the prior written permission of SAE. -
Surface Vehicle Standard
SURFACE J1939-01 VEHICLE Issued 2000-09 STANDARD Submitted for recognition as an American National Standard Recommended Practice for Control and Communications Network for On-Highway Equipment Foreword—This series of SAE Recommended Practices have been developed by the Truck and Bus Control and Communications Network Subcommittee of the Truck and Bus Electrical and Electronics Committee. The objectives of the subcommittee are to develop information reports, recommended practices and standards concerned with the requirements design and usage of devices which transmit electrical signals and control information among vehicle components. The usage of these recommended practices is not limited to truck and bus applications, other applications may utilize them as long as they adhere to the recommended practices listed herein. These SAE Recommended Practices are intended as a guide toward standard practice and are subject to change so as to keep pace with experience and technical advances. As described in the parent document, SAE J1939, there are a minimum of five documents required to fully define a complete version of this network. This particular document, SAE J1939-01, identifies one such complete network by specifying the particular set of SAE J1939 documents which define the Truck and Bus Control and Communications Vehicle Network as it applies to on-highway equipment. Table of Contents 1 Scope ......................................................................................................................................2 1.1 Degree -
Selection Guide for Automotive & Industrial Fanless Box-PC
1/127 PDF Online Selection Guide Stand vom 02.10.2021 - 23:17:17 Bitte laden Sie sich bei Bedarf hier eine aktualisierte Fassung dieses Dokuments herunter! 180 von 180 Artikel aus dem Bereich Automotive & Industrial Box-PC wurden für das PDF ausgewählt. Selection Guide Automotive & Industrial Fanless Box-PC 1. Automotive Box-PC / Car-PC 3 2. KI-Automotive Box-PC 31 3. Railway Box-PC 51 4. Industrial Box-PC / IoT Gateways 61 5. Factory Automation Box-PC 95 6. Digital Signage Box-PC 107 7. Video Surveillance 119 8. Zubehör für Box-PC 127 DELTA COMPONENTS ...we make the difference! 3/127 Automotive Box-PC PDF Online Selection Guide Stand vom 02.10.2021 - 23:17:17 Bitte laden Sie sich bei Bedarf hier eine aktualisierte Fassung dieses Dokuments herunter! 41 von 41 Artikel aus dem Bereich Automotive Box-PC wurden für das PDF ausgewählt. Advanced Telematics Computer Advanced Telematics Computer Advanced Telematics Computer 8010-7AF/7DF 8010-7A 8010-7B Cooling System Swappable fan kit (externally removable fans) Fanless Fanless Mounting System Wall Mount, DIN Rail Wall Mount, DIN Rail Wall Mount, DIN Rail CPU Intel® Core i7-8700T Coffee Lake-S, 6-core, Intel® Core i7-8700T Coffee Lake-S, 6-core, Intel® Core i7-8700T Coffee Lake-S, 6-core, 2.4GHz 2.4GHz 2.4GHz Chipset Intel® Q370 platform controller hub Intel® Q370 platform controller hub Intel® Q370 platform controller hub Watchdog Timer - - - Basic Equipment 8GB 8GB 8GB Maximum Equipment 64G (for two channels) 64G (for two channels) 64G (for two channels) DRAM - - - SDRAM - - - DIMM / MemorySocket -
Cybersecurity Research Considerations for Heavy Vehicles
DOT HS 812 636 December 2018 Cybersecurity Research Considerations for Heavy Vehicles Disclaimer This publication is distributed by the U.S. Department of Transportation, National Highway Traffic Safety Administration, in the interest of information exchange. The opinions, findings, and conclusions expressed in this publication are those of the authors and not necessarily those of the Department of Transportation or the National Highway Traffic Safety Administration. The United States Government assumes no liability for its contents or use thereof. If trade or manufacturers’ names are mentioned, it is only because they are considered essential to the object of the publication and should not be construed as an endorsement. The United States Gov- ernment does not endorse products or manufacturers. Suggested APA Format Citation: Stachowski, S., Bielawski, R., & Weimerskirch, A. (2018, December). Cybersecurity research considerations for heavy vehicles (Report No. DOT HS 812 636). Washington, DC: National Highway Traffic Safety Administration. 1. Report No. 2. Government Accession No. 3. Recipient's Catalog No. DOT HS 812 636 4. Title and Subtitle 5. Report Date Cybersecurity Research Considerations for Heavy Vehicles December 2018 6. Performing Organization Code 7. Authors 8. Performing Organization Report No. Stephen Stachowski, P.E. (UMTRI), Russ Bielawski (UMTRI), André Weimerskirch 9. Performing Organization Name and Address 10. Work Unit No. (TRAIS) University of Michigan Transportation Research Institute 2901 Baxter Rd Ann Arbor, MI 48109 11. Contract or Grant No. DTNH22-15-R-00101, a Vehicle Electronics Systems Safety IDIQ 12. Sponsoring Agency Name and Address 13. Type of Report and Period Covered National Highway Traffic Safety Administration Final Report 1200 New Jersey Avenue SE. -
SAMTEC Automotive Software & Electronics
SAMTEC Automotive Software & Electronics PRODUCT CATALOG 2016 AUTOMOTIVE www.samtec.de PUBLICATION DETAILS 2 CONTACT samtec automotive software & electronics gmbh Einhornstr. 10, D-72138 Kirchentellinsfurt - Germany Phone +49-7121-9937-0 Telefax +49-7121-9937-177 Internet www.samtec.de E-mail [email protected] DISCLAIMER The information contained in this catalog corresponds to the technical status at the time of printing and is passed on with the best of our knowledge. The information in this catalog is in no event a basis for warranty claims or contractual agreements concerning the described products and may especially not be deemed as warranty concerning the quality and durability pursuant to Sec. 443 German Civil Code. samtec automotive software & electronics gmbh reserves the right to make any alterations to this catalog without prior notice. The actual design of products may deviate from the information contained in the catalog if technical alterations and product improvements so require. In any cases, only the proposal made by samtec automotive software & electronics gmbh for a concrete application or product will be binding. All mentioned product names are either registered or unregistered trademarks of their respective owners. Errors and omissions excepted. This catalog has been made available to our customers and interested parties free of charge. It may not, in part or in its entirety, be reproduced in any form without our prior consent. All rights reserved. LEGAL NOTICE samtec automotive software & electronics gmbh Managing directors: René von Stillfried, Dr. Wolfgang Trier Registered office: Kirchentellinsfurt Date: March 2016 Commercial register: Stuttgart, HRB 224968 PREFACE Dear readers, 3 Many of you already know us! You deploy electronic control units, we provide you with the diagnostic solutions. -
ELM325 J1708 Interpreter
ELM325 J1708 Interpreter Description Features With the advent of electronic engine controls, • Supports both SAE J1587 and J1922 many vehicles also adopted some form of diagnostic • High speed RS232 interface tools to help monitor their operation. As more modules began to be used in vehicles, there was • Works with standard RS485 transceivers also a need for the devices to share information • Fully configurable with AT commands rather than each independently obtain this from separate sensors. • Wide operating voltage range (1.8 to 5.5V) In the 1980’s, the SAE J1708 standard was • Low power CMOS design created to provide a specification for a common data bus to be used in heavy duty vehicles. It used RS485 wiring (already proven to be reliable in noisy environments), and a UART-based low speed data Connection Diagram format. The SAE J1587 standard followed a few PDIP and SOIC years later to describe the mechanism by which (top view) messages and data should be sent between vehicle modules. The ELM325 allows a PC or similar device to be VDD 1 14 VSS used to monitor and query devices on a J1708 data XT1 2 13 RO bus, using simple commands that can be sent from almost any terminal program. It is able to work with XT2 3 12 RE either the J1587 or the J1922 data formats. InvDE 4 11 DE RS232 Rx 5 10 J Tx LED Applications RS232 Tx 6 9 J Rx LED • Diagnostic trouble code readers RS Rx LED 7 8 RS Tx LED • Heavy duty vehicle scan tools • Teaching aids • ECU Simulators Block Diagram 3.58 MHz InvDE XT12 3 XT2 4 Timing and Control 13 RO RS232 Rx 5 RS232 J1708 11 DE Interface Interface RS232 Tx 6 J1587/1922 Interpreter 12 RE RS Rx LED 7 10 J Tx LED RS Tx LED 8 9 J Rx LED ELM325DSA Elm Electronics – Circuits for the Hobbyist 1 of 31 www.elmelectronics.com ELM325 Contents Electrical Information Copyright and Disclaimer.............................................................2 Pin Descriptions.......................................................................... -
APPLICATION NOTE ANI13 RS-485 and RS-422 Physical Topologies
Solved by APPLICATION NOTE ANI13 TM RS-485 and RS-422 Physical Topologies RS-485 and RS-422 are in wide use as an interface for telecommunications, industrial, medical, security and networking applications. The reasons for their popularity are low cost, flexibility and very desirable feature set. The published TIA/EIA 485 and RS-422 standards define only the electrical characteristics of the drivers and receivers. They did not standardize such things such as cables and connectors, pinouts, bus arbitration, signaling protocols, or physical wiring topology. Many different implementations have come into use and they are often incompatible with each other. This document includes descriptions and examples of some of popular physical topologies. Point to Point RS-422 or RS-485 This is the simplest configuration, just one driver and one receiver. If termination is used, it is only required at the receiver. Most RS-422 cables used to connect telecom or data-com equipment are point to point links. Generally twisted pair cable is preferred due to its noise canceling ability. Cables may include a single channel over one pair of wires or there may be multiple channels routed through a multi-pin connector and bundled cable. Serial ports ranging from AppleTalk™ to telecom ports such as V.36, EIA-530 and X.21 carry high speed signals on RS-422 or V.11 type drivers and receivers in a point to point configuration. D R Any Sipex RS-485 or RS-422 device can be used in a point to point connection. Sipex has a full portfolio of transceivers with 5V or 3V supplies, half or full duplex, all in industry standard footprints. -
Revisión Documental Del Protocolo CAN Como Herramienta De Comunicación Y Aplicación En Vehículos
ISSN 0188-7297 Certificación ISO 9001:2015 Revisión documental del protocolo CAN como herramienta de comunicación y aplicación en vehículos Luis Gerardo Sánchez Vela Martín Jonathan Molano Clemente Manuel de Jesús Fabela Gallegos Miguel Martínez Madrid José Ricardo Hernández Jiménez David Vázquez Vega Oscar Flores Centeno Publicación Técnica No. 474 Sanfandila, Qro, 2016 SECRETARÍA DE COMUNICACIONES Y TRANSPORTES INSTITUTO MEXICANO DEL TRANSPORTE Revisión documental del protocolo CAN como herramienta de comunicación y aplicación en vehículos Publicación Técnica No. 474 Sanfandila, Qro, 2016 Esta investigación fue realizada en la Coordinación Ingeniería Vehicular e Integridad Estructural del Instituto Mexicano del Transporte, por el Ing. Luis Gerardo Sánchez Vela, el M. C. Martín Jonathan Molano Clemente, el Dr. Manuel de Jesús Fabla Gallegos, el Dr. Miguel Martínez Madrid, el M. C. José Ricardo Hernández Jiménez y el M. C. Oscar Flores Centeno. Agradecemos la colaboración del Ing. Eduardo Malagon Paredes y la C. Ivonne Alejandra Flores Ángeles, como becarios del Instituto Mexicano del Transporte. Contenido Resumen v Abstract vii Resumen ejecutivo ix Introducción 1 Capítulo 1 Protocolos de comunicación en vehículos 3 1.1 Redes de comunicación en vehículos 3 1.2 Interfaces y protocolos de comunicación 4 1.3 Velocidad y seguridad en la transmisión de información 8 1.4 Unidades de control electrónicos 9 1.5 Evolución de protocolos de comunicación en vehículos 10 1.6 Protocolos de última generación 12 1.6.1 Protocolo de comunicación MOST 12 1.6.2 Protocolo de comunicación FLEXRAY 13 1.6.3 Protocolo de comunicación VAN 15 1.6.4 Protocolo de comunicación LIN 15 1.7 Conectores para diagnóstico de vehículos 17 1.7.1 Conector de diagnóstico para vehículos ligeros 17 1.7.2 Conector de diagnóstico para vehículos de 22 autotransporte 1.8 Objetivo del estudio 24 El bus CAN Capítulo 2. -
Analysis of the SAE J1708 Protocol Raine Saastamoinen
Volvo Construction Equipment AB Component Division Analysis of the SAE J1708 protocol Raine Saastamoinen Bachelor thesis report May - Juli 2008 School of Innovation Design and Engineering Mälardalen University, Västerås, Sweden Supervisor and Examiner: Johan Stärner Supervisors at company: Nils-Erik Bånkestad and Jarmo Talvén “ Engineers does’nt buy solutions they create them” LeCroy comersial 2 Abstract Component Division at Volvo Construction Equipment, develops electronic control units (ECU) to be used in entrepreneur machines. In an operating vehicle there are several ECU’s communicating with each other to make everything work as a complete. There are two main network protocols in use to solve different communication needs. One of them is using the SAE J1708 physical layer protocol in transmitting of the actual bits when exchanging information. Manufacturing of the units are made by external suppliers.Up to date, there is a lack of good tools, to verify that delivered components conforms to the J1708 specifications. WaveRunner 104 MXi, is an advanced digital oscilloscope with scripting possibilities. It has been used in this thesis work to find out, whether suitable or not to solve this problem. This thesis shows that analysis is possible and most important of all, in future potential of being a great tool for verification. 3 Acknowledgements Thanks to my supervisors Nils-Erik Bånkestad and Jarmo Talvén at VCE Component Division for professional guidance. Pushing me in the right direction when stumbeling into difficulties (especially after that important meeting the very first week). My supervisor at Mälardalen University, Johan Stärner, a friendly professional for support and important advices. -
AVT – 822 CAN (J1939) and J1708 Controller Board Hardware
ADVANCED VEHICLE TECHNOLOGIES, Inc. AVT – 822 CAN (J1939) and J1708 Controller Board Hardware Description Hardware revision “A3” 24 April 2018 1509 Manor View Road, Davidsonville, MD 21035 USA +1-410-798-4038 (voice) [email protected] www.AVT-HQ.com AVT-84x Multiple Interface Table of Contents 1. INTRODUCTION ....................................................................................................................................................4 2. GLOSSARY ..............................................................................................................................................................4 2.1 CONVENTIONS .........................................................................................................................................................4 3. BRIEF HISTORY.....................................................................................................................................................4 4. SOFTWARE / FIRMWARE DEVELOPMENT ...................................................................................................5 4.1 FIRMWARE SOURCE CODE ......................................................................................................................................5 4.1.1 Development Environment.................................................................................................................................5 4.1.2 PE Micro............................................................................................................................................................5 -
Heavy Duty Scan Tool
HEAVY DUTY SCAN TOOL Bosch HDS 200 Medium and heavy-duty diagnostics for heavy-duty and aftermarket shops Ideal for heavy-duty shops as a second diagnostic J1587/J1708 & J1939 Heavy-Duty Standard tool and mobile repair trucks What does it mean? Cost-effective solution for aftermarket shops in SAE J1587/J1708 need of heavy-duty coverage SAE J1587 is a diagnostic protocol standard developed by the Society of Automotive Engineers (SAE) for heavy-duty and most medium-duty Includes heavy-duty standard coverage for vehicles built after 1985. Up to 1995, individual OEMs used their own medium and heavy-duty trucks connectors. From 1996 to 2001, the 6-pin Deutsch was standard. Beginning in 2001, most OEMs converted to the 9-pin Deutsch. Some OEMs still use the 6-pin Deutsch. SAE J1708 is an SAE physical specification developed especially for heavy HDS 200 Features duty vehicles (trucks & busses). The protocol promoted a standard for f Brilliant Color Display serial communication between modules with microcontrollers. J1708 describes the physical and data link layer. Almost always used in f Rugged enclosure for durability conjunction with the application layer protocol SAE J1587. f Class 4 – Class 8 truck coverage featuring SAE J1939 “Automatic Protocol Search” In the early 90's, the SAE Truck and Bus Control and Communications Sub-committee started the development of a CAN-based application f HD J1587 / J1708 and J1939 CAN, Engine, profile for in-vehicle communication in trucks. In 1998 the SAE published Transmission/ABS coverage and more the J1939 set of specifications. A J1939 network connects electronic control units (ECU) within a truck and trailer system.