April 20, 1971 L. R. MZELL 3,575,751. by 4.6% F 44
Total Page:16
File Type:pdf, Size:1020Kb
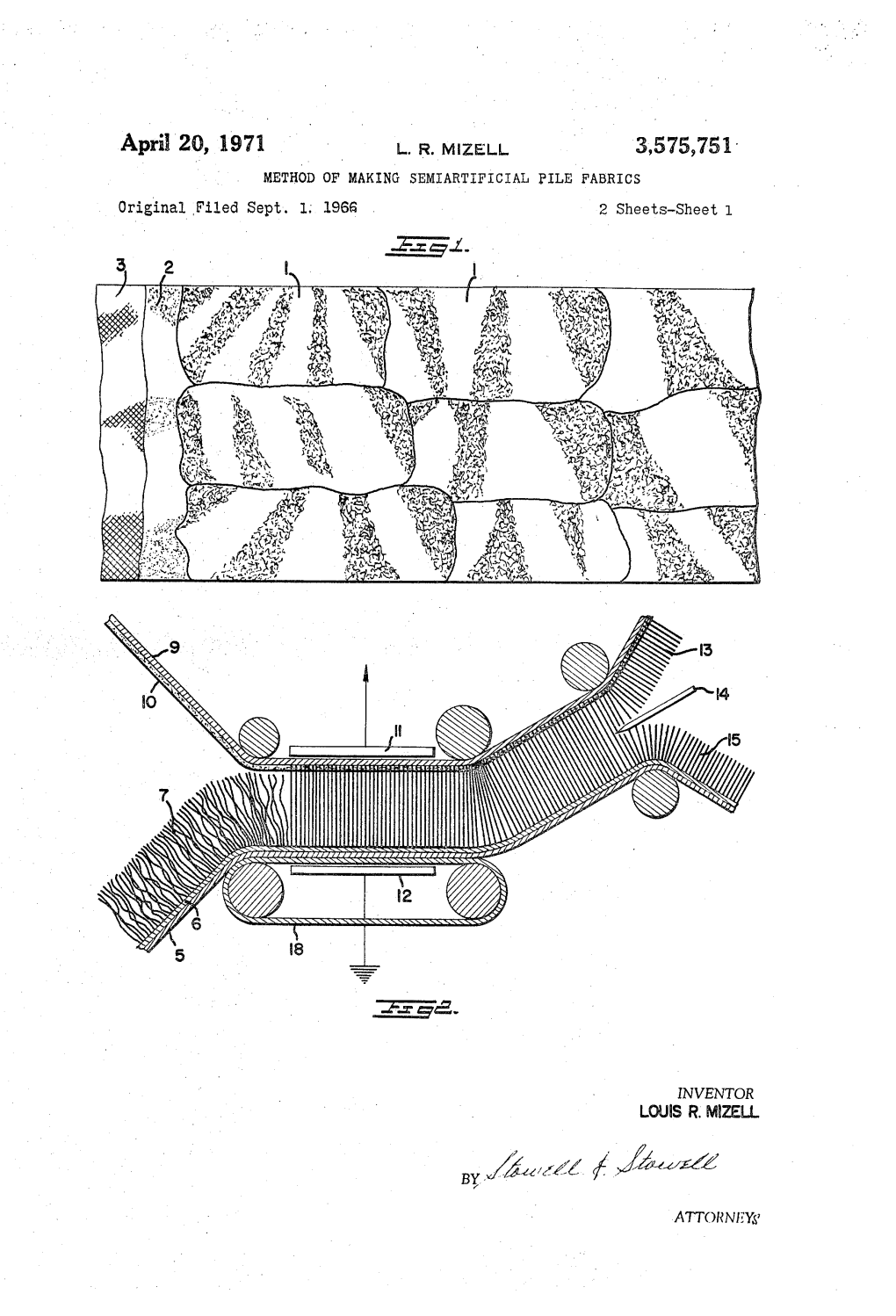
Load more
Recommended publications
-
Analysis of Artificial Leather with Textile Fabric on the Backside
Volume 6, Issue 2, Fall2009 ANALYSIS OF ARTIFICIAL LEATHER WITH TEXTILE FABRIC ON THE BACKSIDE Darko Ujević, Stana Kovačević, *Larry C. Wadsworth, Ivana Schwarz, and Blaženka Brlobašić Šajatović University of Zagreb, Faculty of Textile Technology, Zagreb, Croatia *The University of Tennessee, Department of Materials Science and Engineering ABSTRACT The fundamental characteristics of a textile fabric intended for the vehicle interior is presented. Chemical and physical-mechanical properties of artificial leather with bonded textile fabric on the back side are analyzed. The most important parameters for leather durability are: breaking force and elongation-at-break, and these properties will be tested in different circular directions. Likewise, chemical properties of artificial leather and basic construction parameters of the textile fabric are investigated. When using artificial leather, physical-mechanical properties of artificial leather as well as the quality of the seams are most important. In addition to the results obtained, physical-mechanical properties and aesthetic evaluation of the joined places will be compared. Keywords: Artificial leather, Textile fabric on the back side, Joined place strength, Seam strength, Physical-mechanical properties Introduction pleather (plastic leather) is a slang term for synthetic leather made out of plastic, a In addition to ergonomically designed car portmanteau of plastic and leather, the term seats for keeping the body in a correct sitting can be either descriptive, or derogatory, position, it is important that the passenger depending upon the user (the derogatory use feels no bodily fatigue due to sitting implies use as a substitute for genuine discomfort. Pleasant contact between the animal hide leather to cut costs). -
Ethical Consumers' Awareness of Vegan Materials
sustainability Article Ethical Consumers’ Awareness of Vegan Materials: Focused on Fake Fur and Fake Leather Yeong-Hyeon Choi 1 and Kyu-Hye Lee 2,* 1 Department of Clothing and Textiles, Hanyang University, Seoul 04763, Korea; [email protected]figure 2 Human-Tech Convergence Program, Department of Clothing and Textiles, Hanyang University, Seoul 04763, Korea * Correspondence: [email protected]; Tel.: +82-2-2220-1191 Abstract: With an increase in ethical awareness, people have begun to criticize the unethical issues associated with the use of animal materials. This study focused on the transition of global consumers’ awareness toward vegan materials and the relationship between the interest in ethical subjects such as animals, the environment, and vegan materials. For this purpose, consumers’ posts about fur/fake fur and leather/fake leather uploaded on Google and Twitter from 2008 to 2019 were utilized, and the Term Frequency-Inverse Document Frequency (Tf-idf ) value was extracted using Python 3.7. Furthermore, the worldwide Google keyword search volume of each word was analyzed using Smart PLS 3.0 to investigate global consumers’ awareness. First, with time, consumers began relating animal materials such as fur and leather to topics such as animal rights, animal abuse, and animal protection. Second, as interest in “animal welfare” increased, interest in “fake fur” also rose, and as interest in “cruelty free” increased, interest in “fake fur”, “vegan fur”, and “vegan leather” also increased. Third, as consumers’ interest in the “environment” increased, interest in vegan materials such as “fake fur” and “fake leather” decreased. However, as interest in “eco” increased, interest in “vegan leather” also augmented. -
Characteristics of Artificial Leather for Footwear - Heat and Moisture Transport Properties -
Technical Paper Characteristics of Artificial Leather for Footwear - Heat and Moisture Transport Properties - Won Young Jeong !1,Jung Woo Park !2,Masayoshi Kamijo !1,YoshioShimizu !1,andSeung Kook An !2 *1 Dept. of Kansei Engineering, Faculty of Textile Science and Technology, Shinshu University, Ueda, Nagano 386-8567, Japan *2 Dept. of Textile Engineering, Pusan National University, Busan 609-735, Korea Abstract :Artificial leather used in this study was prepared by wet coagulation method with polyurethane resin in a laboratory instrument. Various needle-punching nonwoven fabrics were used as substrate material, which are widely used in the shoe industry as the substrate ofinsole or artificial leather. To estimatecomfort properties with the finishing for artificial leather, we measured air, water vapor, and thermal transport properties ; and then we evaluated the changes of each property of finished nonwoven fabrics which were dipped and coated with polyurethane resin. The changes due to the dipping and coating processes for artificial leather may give rise to a feeling of discomfort. Water vapor permeability and heat keeping rate decreased, but thermal conductivity and a cool feeling increased with the finishing process. After dipping and coating processes, there was little significant difference in the transport properties of base materials. Therefore, the transport characteristics were more closely related to the finishing condition than the constructive characteristics of the base materials. (Received 14 December, 2006 ; Accepted 4 July, 2007) 1. Introduction some situations, the evaporation rate of perspiration from wet skin is less than that of perspiration secretion. So Artificial leathers have the advantage over natural accumulated water vapor may condense inside the inner products in uniformity of quality and availability in roll clothing of a wearer undertaking arduous exercise in a form, which facilitates production planning and cold and wet climate. -
A SURVEY of STANDARDS for the U.S. FIBER/TEXTILE/APPAREL INDUSTRY
A Survey of Standards for the U.S. Fiber/Textile/Apparel lndustr y Craig 6. Pawlak U.S. DEPARTMENT OF COMMERCE Technology Administration National Institute of Standards and Technology Manufacturing Systems Integration Division Gaithersburg, MD 20899 April 1996 U.S. DEPARTMENT OF COMMERCE Michael Kantor, Secretary TECHNOLOGY ADMl NlSTRATlON Mary L. Good, Under Secretary for Technology NATIONAL INSTITUTE OF STANDARDS AND TECHNOLOGY Arati Prabhakar, Director DISCLAIMER No approval or endorsement of any commercial product, organization, or company by the National Institute of Standards and Technology is intended or implied. Certain commercial equipment, instruments, or materials may be identified in this report in order to facilitate understanding. Such identification does not imply recommendation or endorsement by the National Institute of Standards and Technology, nor does it imply that the materials or equipment identified are necessarily the best available for the purpose. This publication was prepared by United States Government employees as part of their official duties and is, therefore, a work of the US. Government and not subject to copyright. A SURVEY of STANDARDS for the U.S. FIBER/TEXTILE/APPAREL INDUSTRY Craig G. Pawlak Manufacturing Systems Integration Division Manufacturing Engineering Laboratory National Institute of Standards and Technology Gaithersburg, MD ABSTRACT This report documents a survey of standards relevant to the U.S. Fiber/Textile/Apparel (FTA) industry. The standards are discussed in four main groups-integration standards, test methods, quality standards, and standard reference data and materials. The Appendix of the report lists the titles of all standards found, grouped together by the organization responsible for them. Those organizations are also listed along with contact information for them. -
Artificial Leather Is Booming, but Its Production Is Currently Not Very
INNOVATION ARTIFICIAL LEATHER Better ven experts can hardly distinguish artificial leather from the than real thing at first glance. The look, structure, and feel of this Eproduct now comes very close to its natural model. As a result, artificial leather has become an integral part of our daily lives. It can be found in sofas and dentist’s chairs, luxury handbags and car seats, shoes and clothing. And sometimes it’s even better than the origi- nal—in surfaces that are exposed to intense mechanical stress, ultraviolet light or saltwater, or in medical equipment that needs to be frequently disinfected. High-quality material rather than a cheap imitation: The image Real of artificial leather is changing. It’s also benefiting from people’s heightened environmental awareness. Processors and consumers are increasingly attaching importance to production methods that harm neither people nor the environment—an expectation that is seldom fulfilled by genuine leather. “Vegan” leather is also popular with shoppers who reject animal products in general. This has resulted in the steadily growing use of imitation leather. In 2016 the annual worldwide production of artificial leather amount- ed to about 3.5 million tons. If all of it were to be rolled out in a TEXT CHRISTA FRIEDL single piece, it would cover an area equal to the German federal states of Berlin, Hamburg, and Saarland. Asia is the Number One produc- er of artificial leather, with 85 percent of the annual tonnage coming Artificial leather is booming, but its production is from China. currently not very sustainable. Researchers have A multilayered composite developed an additive that paves the way for envi Artificial leather is a multilayered composite material. -
Effect of Sewing Machine and Thread Type on the Quality of Leather Garments
Eman Rafat Saad Effect of sewing machine and thread type on the quality of leather garments Effect of sewing machine and thread type on the quality of leather garments Dr.Eman Rafat Saad Lecturer in Apparel Design & Technology Department, Faculty of Applied Arts, Helwan University, Cairo, Egypt Abstract: Sewing Machine is one of the most important factors affecting the quality of the Keywords: clothing industry. Also, leather garments require special care during sewn. The - Leather purpose of this paper is to study sewing leather fabrics Techniques to reach the - artificial leather highest degree of quality and efficiency of sewing leather and the efficiency of - natural leather functional and aesthetic appearance of clothing and age consumer. And by identifying some of the research variables ,there was two leather type (sheep natural - ordinary sewing leather – Pu artificial leather), the skin of sheep is the most commonly used types machine of leather in the field of leather garments. There was a comparison between two - leather sewing types of sewing machines (Ordinary sewing machine – leather sewing machine) machine and using two types of thread (polyester – nylon). Then we examined leather using - sewing thread a number of test methods like thickness, tensile strength, abrasion and seam pucker - seam. according to standards. Tests took place into conditioned atmosphere of 21ºC and 65% RH. Comparisons have been made between the two different types of sewing machines and also between the two different thread types this was done with reference to seamed lines’ durability, efficiency and appearance. In conclusion we was able to determine the best quality to sew leather garments in terms of identifying the type of sewing machine-the type of sewing thread To suit every type of leather in this test. -
OCCASION This Publication Has Been Made Available to the Public
OCCASION This publication has been made available to the public on the occasion of the 50th anniversary of the United Nations Industrial Development Organisation. DISCLAIMER This document has been produced without formal United Nations editing. The designations employed and the presentation of the material in this document do not imply the expression of any opinion whatsoever on the part of the Secretariat of the United Nations Industrial Development Organization (UNIDO) concerning the legal status of any country, territory, city or area or of its authorities, or concerning the delimitation of its frontiers or boundaries, or its economic system or degree of development. Designations such as “developed”, “industrialized” and “developing” are intended for statistical convenience and do not necessarily express a judgment about the stage reached by a particular country or area in the development process. Mention of firm names or commercial products does not constitute an endorsement by UNIDO. FAIR USE POLICY Any part of this publication may be quoted and referenced for educational and research purposes without additional permission from UNIDO. However, those who make use of quoting and referencing this publication are requested to follow the Fair Use Policy of giving due credit to UNIDO. CONTACT Please contact [email protected] for further information concerning UNIDO publications. For more information about UNIDO, please visit us at www.unido.org UNITED NATIONS INDUSTRIAL DEVELOPMENT ORGANIZATION Vienna International Centre, P.O. Box -
Resource-Saving Technologies for the Production of Elastic Leather Materials: Collective Monograph
University of Tennessee, Knoxville TRACE: Tennessee Research and Creative Exchange Chemistry Publications and Other Works Chemistry Fall 10-2020 Resource-saving technologies for the production of elastic leather materials: Collective monograph Olena Korotych University of Tennessee, Knoxville, [email protected] Anatolii Danylkovych Kyiv National University of Technologies and Design, [email protected] Serhii Bilinskyi Kyiv National University of Technologies and Design Serhii Bondarenko [email protected] Slava Branovitska See next page for additional authors Follow this and additional works at: https://trace.tennessee.edu/utk_chempubs Part of the Design of Experiments and Sample Surveys Commons, Materials Chemistry Commons, Multivariate Analysis Commons, Other Chemical Engineering Commons, Other Chemistry Commons, Other Engineering Science and Materials Commons, Other Materials Science and Engineering Commons, and the Other Statistics and Probability Commons Recommended Citation Resource-saving technologies for the production of elastic leather materials: collective monograph / edited by A. Danylkovych and O. Коrotych. – Riga, Latvia: “Baltija Publishing”, 2020. – 418 p. This Book is brought to you for free and open access by the Chemistry at TRACE: Tennessee Research and Creative Exchange. It has been accepted for inclusion in Chemistry Publications and Other Works by an authorized administrator of TRACE: Tennessee Research and Creative Exchange. For more information, please contact [email protected]. Authors Olena Korotych, Anatolii Danylkovych, -
US5134178.Pdf
||||||||| USOO513478A United States Patent (19) 11 Patent Number: 5,134,178 Nishibori (45) Date of Patent: Jul. 28, 1992 (54) ANIMAL PROTEIN RESIN-PLASTIC 2,257,726 10/1941 Emmitt ..............................., 264/40 COMPOSTIONS AND MANUFACTURES 2,433,727 12/1947 Arnold ..... ... 428/291 NCORPORATING ANEMAL SKINS AND/OR 3,157,524 A1964 Artandi .... ... 106/122 3,663,472 5/1972 Raymond .............................. 524/11 LEATHER AND/OR GELATIN POWDER 3,665,061 5/1972 Eberly, Jr. ............................ 264/49 THEREIN, THE POWDER THEREIN, AND 3,756,518 9/1973 Bailey .................................... 24/65 METHOD OF PRODUCING THE SAME 4,057,607 11/1977 Soehngen et al. .................... 264/28 75) Inventor: Sadao Nishibori, Tokyo, Japan FOREIGN PATENT DOCUMENTS 73) Assignee: EIN (America) Inc., New York, N.Y. 50-149768 12/1975 Japan. (21) Appl. No.: 515,318 586232 3/1947 United Kingdom .................. 524/11 22 Filed: Apr. 23, 1990 Primary Examiner-Allan M. Lieberman Attorney, Agent, or Firm-Shlesinger, Arkwright & Related U.S. Application Data Garvey 60 Continuation of Ser. No. 221,904, Jul. 20, 1981, aban (57) ABSTRACT doned, which is a division of Ser. No. 68,347, Jul. , The present invention relates to methods, compositions, 1987, Pat. No. 4,834,762. and articles manufactured from scrap treated skin and 30) Foreign Application Priority Data /or leather which has been finely pulverized and mixed Aug. 7, 1986 JP Japan ................................ 61-185896 with synthetic resin. It further includes a method for the Aug. 7, 1986 JP Japan ................................ 6-185900 manufacture of improved leather products made from Mar. 14, 1987 JP Japan .................................. 62-59832 animal skin and/or leather and/or animal gelatin includ ing the products derived therefrom and the method of 51 Int, Cl. -
Sewing and Clothing ID Skill-A-Thon Booklet
4-H FCS Skill-a-thon Sewing and Clothing ID The photos shown here are only one option of what an item may look like. Other options are available. Revised January 2020 1 Fabrics Batik is an Indone- sian technique of wax- resist dyeing applied to whole cloth. This tech- nique originated from Java, Indonesia. Batik Broadcloth is a very is made either by lightweight, smooth, flat drawing dots and lines looking fabric, with no of the resist with a pattern in the weave of the spouted tool called a tjanting, or by printing the threads. It is similar in resist with a copper stamp called a cap. quality to pinpoint fabric, but has less texture. This usually means it is slightly more transparent and not as shiny as the pinpoint Chambray is a plain weave fabric woven with a colored yarn in the warp and a white yarn in the weft. Like chambray, denim is made with a colored yarn in the warp and white in the weft, but is woven in a twill con- Corduroy is a textile with a dis- struction. tinct pattern, a "cord" or wale. Mod- ern corduroy is most commonly composed of tufted cords, sometimes exhibiting a channel (bare to the base fabric) between the tufts. Both velvet Cotton — Good material for first time Eyelet fabric is a type of lace sewers to use. Has a good hand and little made by creating holes in a fabric elasticity. Considered a heavy weight medium. Each hole is edged using a buttonhole stitch. The holes are pre- material. -
Integration Into the World Economy: Companies in Transition in the Czech Republic, Slovakia, and Hungary
INTEGRATION INTO THE WORLD ECONOMY: COMPANIES IN TRANSITION IN THE CZECH REPUBLIC, SLOVAKIA, AND HUNGARY Leslie E. Grayson The Isidore Horween Research Professor of International Business Samuel E. Bodily John Tyler Professor of Business Administration Darden Graduate School of Business Administration University of Virginia Charlottesville, Virginia, USA RR–96–19 December 1996 INTERNATIONAL INSTITUTE FOR APPLIED SYSTEMS ANALYSIS Laxenburg, Austria International Standard Book Number 3-7045-0130-1 Research Reports, which record research conducted at IIASA, are independently reviewed before publication. Views and opinions expressed herein do not necessarily represent those of the Institute, its National Member Organizations, or other organizations supporting the work. Copyright c 1996 International Institute for Applied Systems Analysis. All rights reserved. No part of this publication may be reproduced or transmitted in any form or by any means, electronic or mechanical, including photocopy, recording, or any information storage or retrieval system, without permission in writing from the publisher. Cover design by Anka James. Printed by Novographic, Vienna, Austria. Contents Acknowledgments v PART I: DISCUSSION Introduction 3 The Macroeconomic and Political Environment in Mid-1995 4 Financial Sectors 6 Marketing 9 Operations Management 11 Financial Management 13 Strategy 14 Managerial Behavior 15 Summary and Conclusions 21 PART II: CASE STUDIES Biotika, A.S., Slovakia 27 Botana, A.S., Czech Republic 32 Elektromontaˇzn´ıZ´avody, A.S., Czech -
Starpro Catalogue.Cdr
1 61105.CHN - TRAINING BOXING GLOVE wide Pu/velcro wrap around strap closing. Pre-curved High compression IMF foam padding. leather and perforated palm panel in middle with moisture wicking hydraflow palm. 8cm In "CH2" genuine cowhide leather with palm in 3G nubuck-II HL 100% PU hi-tec artificial Size: 8oz, 10oz, 12oz, 14oz, 16oz, 18oz, 20oz 61294.CHN - BOXING GLOVE (ONE PIECE MOULD) Hitting area in CH2 genuine cowhide leather with rest of the glove in 3G 100% pu hi-tech artifical leather. Palm lined with soft polyester fabric foam. Mesh palm panel in middle. 8cm wide velcro wrap around strap closing. Newly developed pre-curved high compression one piece IMF foam padding. Size: 8oz, 10oz, 12oz, 14oz, 16oz, 61218.HL3 - COACH SPARRING GLOVE In nubuck-II 100% Pu hi-tec artificial leather with finger area in MB lining Peforated palm pannel in middle with mesh moisture wicking palm linned inside. Palm padded with F-86 EVA. Pre-curved High compression 'IMF' foam padding. 6.5cm Rigid pu/velcro strap closing. Contrast stitching. Size: 10oz, 12oz, 14oz, 16oz, 2 61180.HL3 - TRAINING BAG GLOVE In nubuck-II 'HL' 100% Pu hi-tec artificial leather with "Hydra flow" mesh moisture wicking palm. 'IMF' foam padding. 6.5cm pu/velcro wrap around strap. Size: S/M , L/XL 61303.CHN - MMA Open Hand Sparring Glove “Leather/PU” Hitting area/fingers in CH2 genuine cowhide leather with rest In 3G HL' 100% Pu hi-tech artificial leather. Inner palm with Z-Tech quick drying / anti slip fabric. F85R1 EVA Ultra light foam padding .