Preparation of Papers for AIAA Technical Conferences
Total Page:16
File Type:pdf, Size:1020Kb
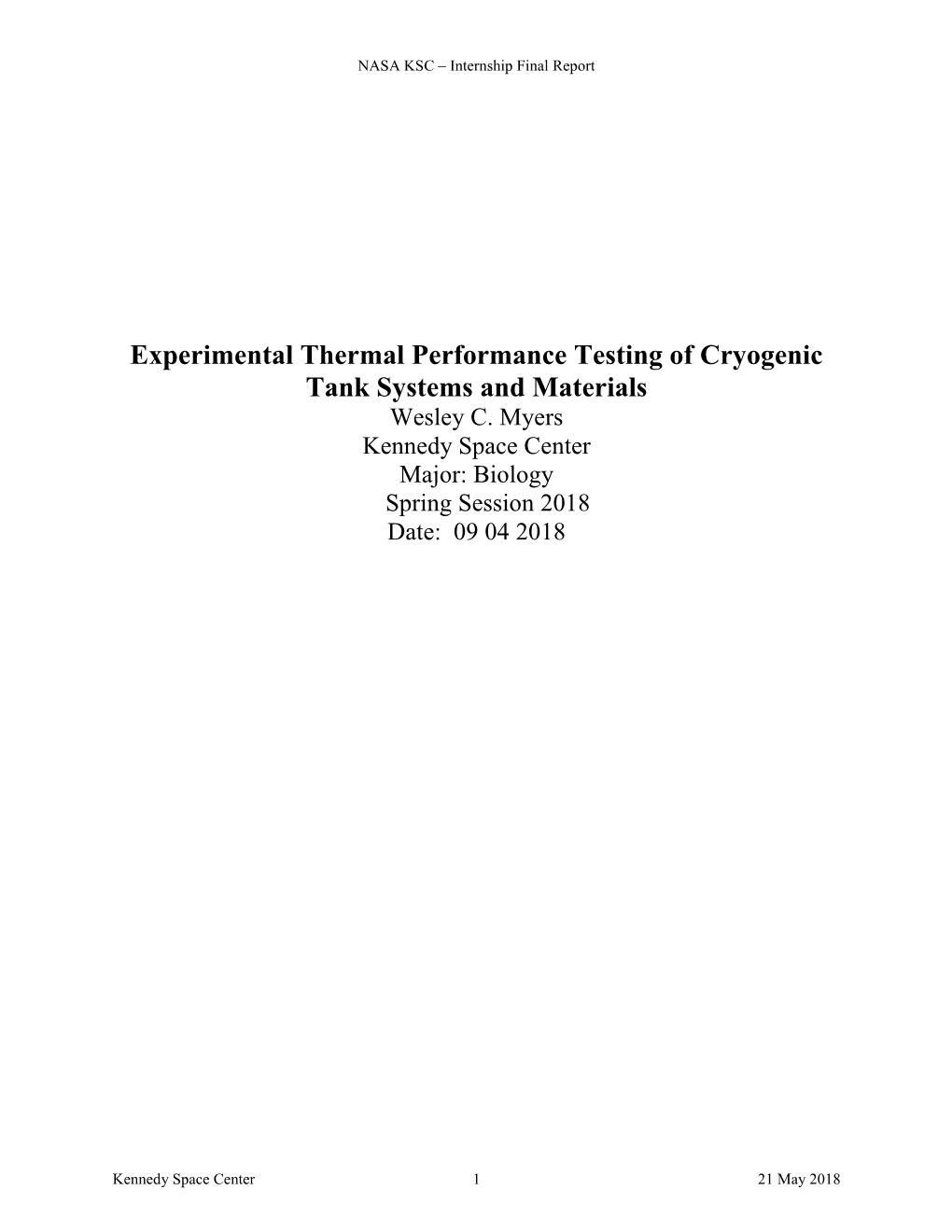
Load more
Recommended publications
-
V L Scientific Udyog
+91-8049592713 V L Scientific Udyog https://www.indiamart.com/vlscientificudyog/ We “V L Scientific Udyog” are a leading Manufacturer and Trader of a wide range of Laboratory Thermometer, Laboratory Burette, Laboratory Condenser, Laboratory Flask, Laboratory Tubes, Glass Beakers, Imhoff Cones, etc. About Us Established as a Sole Proprietorship firm in the year 2010, we “V L Scientific Udyog” are a leading Manufacturer and Trader of a wide range of Laboratory Thermometer, Laboratory Burette, Laboratory Condenser, Laboratory Flask, Laboratory Tubes, Glass Beakers, Imhoff Cones, Measuring Cylinder, etc. Situated in Ambala (Haryana, India), we have constructed a wide and well functional infrastructural unit that plays an important role in the growth of our company. We offer these products at reasonable rates and deliver these within the promised time-frame. Under the headship of our mentor “Mr. Sachin Lamba”, we have gained a huge clientele across the nation. For more information, please visit https://www.indiamart.com/vlscientificudyog/profile.html LABORATORY FLASK O u r P r o d u c t R a n g e Conical Flask School Lab Flask 2000 ML Conical Flask Iodine Flask BOD INCUBATOR O u r P r o d u c t R a n g e Laboratory BOD Incubator BOD Incubator 2 Shelves BOD Incubator BOD Incubator LABORATORY MICROSCOPE O u r P r o d u c t R a n g e Olympus Biological Labomed LX300 Microscope Microscope Physiotherapy Medical Comparison Microscope Laboratory Microscope LABORATORY TUBES O u r P r o d u c t R a n g e Laboratory Culture Tubes Glass Testing Tubes -
AP Galaxy Enterprises
+91-8068442236,295 A. P. Galaxy Enterprises https://www.indiamart.com/ap-galaxy-enterprises/ We “A. P. Galaxy Enterprises” are a Partnership firm that is an affluent manufacturer of a wide array of Glass Cylinder, Laboratory Flask, Laboratory Beaker, Laboratory Microscope, Glass Test Tubes, etc. About Us Incepted in the year 2002 at Ambala (Haryana, India), we “A. P. Galaxy Enterprises” are a Partnership firm that is an affluent manufacturer of a wide array of Glass Cylinder, Laboratory Flask, Laboratory Beaker, Laboratory Microscope, Glass Test Tubes, etc. We provide these products as per the latest market trends and deliver these at client's premises within the scheduled time frame. We have also selected a team of devoted and capable professionals who helped us to run the operation in a systematic and planned manner. Apart from this, we also export these products to Sirlanka, Gulf Country, African Country and Nepal. Under the supervision of “Mr. Iqbal" (Partner), we have gained huge success in this field. For more information, please visit https://www.indiamart.com/ap-galaxy-enterprises/profile.html O u r P r o d u c t R K a S n A L g F e Y R O T A R O B A L Lab Glass Beaker Conical Flask Laboratory Conical Flask Lab Conical Flask O u r P r o d u c t R a n R g E e D N I L Y C S S A L G Laboratory Glass Scale Measuring Cylinder Cylinder Glass Measuring Cylinder Lab Measuring Cylinder E R O A W u S r S P A L r o G d D u N c A t E R L T a T n O g B e Y R O T A R O B A L Laboratory Reagent Bottle Lab Reagent Bottle Reagent Bottles Laboratory -
Practical Manual Engineering Chemistry
VPCOE CHEMISTRY LAB MANUAL VPCOE VIDYA PRATHISHTHAN’S COLLEGE OF ENGINEERING PRACTICAL MANUAL ENGINEERING CHEMISTRY (Academic year 20152015----16)16) FOR FIRST YEAR ENGINEERING DEGREE COURSES ACCORDING TO THE REVISED SYLLABUS OF S.P.PUNE UNIVERSITY (W.E.F. 2012) Head PrinPrinPrincipalPrin cipal Gen. Sc. & Engg. Dept VPCoE PREPARED BY Dr. APARNA G. SAJJAN Assistant Professor of Chemistry VPCOE (2014 -15) Page 1 of 46 VPCOE CHEMISTRY LAB MANUAL CONTENTS Common Laboratory Glassware I Titration Assembly II Glassware and Their Use III - V Safety Rules & Acknowledgement by Student V - VII I) Determination of Alkalinity of Water Sample 1−4 II) Determination of Hardness of Water by EDTA Method 5−8 III) Determination of Dissociation Constant of Weak Acid (Acetic Acid) using 9−13 PH - Meter IV) To Determine Maximum Wavelength of Absorption of FeSO 4, to Verify Beer’s Law and to Find Unknown Concentration of Ferrous ions (Fe 2+ ) in 14−17 Given Sample by Spectrophotomety / colorimetry V) Titration of Mixture of Weak Acid and Strong Acid with Strong Base 18−20 Using Conductometer VI) Preparation of Polystyrene and Phenol - Formaldehyde or Urea - 21−24 Formaldehyde Resin and their Characterization VII) To Determine Molecular Weight of a Polymer using Ostwald’s Viscometer 25−27 VIII) Proximate Analysis of Coal 28−30 Appendix 31–34 References 35 Development of Intellectual and Motor Skills 35 Grid Table 36 Page 2 of 46 VPCOE CHEMISTRY LAB MANUAL COMMON LABORATORY GLASSWARES Burette Pipette Test-tube Measuring cylinder Conical flask Separating funnel Volumetric flask Beaker Filter funnel I Page 3 of 46 VPCOE CHEMISTRY LAB MANUAL TITRATION ASSEMBLY White tile (To observe sharp colour changes) Correct method to note down the readings Graduated Cylinder Burette The reading is 36.5 ml. -
Desiccator Glassware
· WUBO® Laboratory Glassware PRODUCT CATALOG CONSTENTS Burning Glassware.........................目..录........................................................P1 LOW WALL BEAKER........................................................................................................................................................................ 1 HIGH WALL BEAKER....................................................................................................................................................................... 1 CONICAL BEAKER............................................................................................................................................................................2 NARROW NECK CONICAL FLASK................................................................................................................................................2 WIDE NECK CONICAL FLASK....................................................................................................................................................... 3 IODINE FLASK................................................................................................................................................................................... 3 AMBER CONICAL FLASK................................................................................................................................................................4 CONICAL FLASK WITH CAP...........................................................................................................................................................4 -
Yamato LM100, LM110, LM200, LM210 Laboratory Flask Mixer
Laboratory Flask Mixer LM100/110/200/210 Series Max. Speed Range 50 ~1000rpm Max. Torque 0.1N•m LM Series compact design flask mixer features integrated drive and stirring seal allowing direct installation of flask and stirring in a vacuum and sealed state. No time-consuming shaft alignment required. Its strong stirring power is perfect for samples of high volume and high viscosity. LM100/110 is designed with manual type rotation speed while LM200/210 is equipped with digital indicator. • Wide range rotation speed of 50-1000 rpm • Capable of vacuuming up to 399.9Pa without impairing rotation efficiency • Directly attachable to a three-neck flask 24/40, 29/42 optional • Maintenance free and superior DC brushless motor • Belt drive transmission minimizes noise and vibration • Variety of stirring shafts and blades available to handle small to large volume samples • Fluorine rubber seal as standard for shaft seal, superior chemical resistant Teflon® rubber seal available as option • At the flask joint, FKM o-ring is used as standard, superior chemical resistant Kalrez® o-ring available as option • Equipped with 24/40 rotary joint, 29/42 optional • Capable of AC100-240 by changing power cord LM100/110 LM200/210 with Digital Display Specifications Model LM100 LM110 LM200 LM210 Operating temp. range 5°C~35°C Operating speed range *1 50~1000rpm Max. torque 0.1N•m Max. ultimate vacuum ≤399.9Pa Exterior PBT /ADC12 (Surface treatment: Baking finish) Motor DC brushless motor 30W Power switch Speed control dial with switch (stepless adjustment) Rotation -
Manual for SPARK
Instructions for Use – Reference Guide SPARK Document Part No.: 30124664 2017-11 Document Version: 1.2 WARNING: Carefully read and follow the instructions provided in this document before operating the instrument. Notice Every effort has been made to avoid errors in text and diagrams; however, Tecan Austria GmbH assumes no responsibility for any errors, which may appear in this publication. It is the policy of Tecan Austria GmbH to improve products as new techniques and components become available. Tecan Austria GmbH therefore reserves the right to change specifications at any time with appropriate validation, verification, and approvals. We would appreciate any comments on this publication. Manufacturer Tecan Austria GmbH Untersbergstr. 1A A-5082 Grödig, Austria T +43 62 46 89 330 F +43 62 46 72 770 E-mail: [email protected] www.tecan.com Copyright Information The contents of this document are the property of Tecan Austria GmbH and are not to be copied, reproduced or transferred to another person or persons without prior written permission. Copyright Tecan Austria GmbH All rights reserved. Printed in Austria CE Declaration of Conformity See the last page of these Instructions for Use. Area of Application – Intended Use See chapter 2.2 Intended Use (Hardware and Software). 2 Instructions for Use – Reference Guide SPARK Part No. 30124664 Version 1.2 2017-11 About the Instructions for Use Original Instructions. This document describes the SPARK multifunctional microplate reader. It is intended as reference and instructions for use. This document describes how to: • Install the instrument • Operate the instrument • Clean and maintain the instrument Remarks on Screenshots The version number displayed in screenshots may not always be the one of the currently released version. -
Federal Register/Vol. 80, No. 14/Thursday, January 22, 2015
3380 Federal Register / Vol. 80, No. 14 / Thursday, January 22, 2015 / Proposed Rules ENVIRONMENTAL PROTECTION information to support agent information whose disclosure is AGENCY preauthorization or authorization of use restricted by statute. Certain other decisions. material, such as copyrighted material, 40 CFR Parts 110 and 300 DATES: Comments must be received on will be publicly available only in hard copy. Publicly available docket [EPA–HQ–OPA–2006–0090; FRL–9689–9– or before April 22, 2015. OSWER] ADDRESSES: Submit your comments, materials are available either identified by Docket ID No. EPA–HQ– electronically in http:// RIN 2050–AE87 OPA–2006–0090, by one of the www.regulations.gov or in hard copy at the EPA Docket, EPA/DC, EPA West, National Oil and Hazardous following methods: • Federal Rulemaking Portal: http:// Room 3334, 1301 Constitution Avenue Substances Pollution Contingency NW., Washington, DC. The Public Plan www.regulations.gov. Follow the on-line instructions for submitting comments. Reading Room is open from 8:30 a.m. to AGENCY: U.S. Environmental Protection • Mail: The mailing address of the 4:30 p.m., Monday through Friday, Agency (EPA). docket for this rulemaking is EPA excluding legal holidays. The telephone number for the Public Reading Room is ACTION: Proposed rule. Docket Center (EPA/DC), Docket ID No. EPA–HQ–OPA–2006–0090, 1200 202–566–1744 to make an appointment SUMMARY: The Environmental Protection Pennsylvania Avenue NW., Washington, to view the docket. Agency (EPA or the Agency) proposes to DC 20460. FOR FURTHER INFORMATION CONTACT: For amend the requirements in Subpart J of • Hand Delivery: Such deliveries are general information, contact the the National Oil and Hazardous only accepted during the Docket’s Superfund, TRI, EPCRA, RMP, and Oil Substances Pollution Contingency Plan normal hours of operation, and special Information Center at 800–424–9346 or (NCP) that govern the use of dispersants, arrangements should be made for TDD at 800–553–7672 (hearing other chemical and biological agents, deliveries of boxed information. -
Beaker : a Simple Container for Stirring, Mixing and Heating Liquids Commonly Used in Many Laboratories
Beaker : A simple container for stirring, mixing and heating liquids commonly used in many laboratories. It is generally cylindrical in shape, with a flat bottom. Erlenmeyer flask : The type of laboratory flask which features a flat bottom, a conical body, and a cylindrical neck.(The tapered sides and narrow neck of this flask allow the contents of the flask to be mixed by swirling, without risk of spillage, making them suitable for titrations.) Volumetric flask(measuring flask or graduated flask) : A piece of laboratory glassware, a type of laboratory flask, calibrated to contain a precise volume at a particular temperature. It is used for precise dilutions and preparation of standard solutions. These flasks are usually pear-shaped, with a flat bottom, and made of glass or plastic. The neck of the volumetric flasks is elongated and narrow with an etched ring graduation marking. Graduated cylinder(measuring cylinder or mixing cylinder) : A piece of laboratory equipment used to measure the volume of a liquid. Graduated cylinders are generally more accurate and precise than laboratory flasks and beakers. However, they are less accurate and precise than volumetric glassware, such as a volumetric flask or volumetric pipette. Pasteur Pipette(droppers or eye droppers) : Be used to transfer small quantities of liquids. They are usually glass tubes tapered to a narrow point, and fitted with a rubber bulb at the top. Burette(buret) : A device used in analytical chemistry for the dispensing of variable, measured amounts of a chemical solution. A volumetric burette delivers measured volumes of liquid. Petri dish : It is a shallow cylindrical glass or plastic lidded dish that biologists use to culture cells. -
Basic Concept Laboratory Tech M
Basic concept in Laboratory Techniques M. Sc. 2nd Semester Subject: Basic Concepts in Laboratory Techniques 1 Code: PGS – 504 (0 + 1) Chemical Use Guideline 1) Never use a product that doesn't have a label to reference. 2) Don't mix chemicals without specific authorization from the formulator. 3) Always use personal protective equipments. 4) When pouring chemicals, pour concentrates into the water and not vice-versa. 5) Never pour chemicals into an empty, unlabeled container. 6) Don't store flammable chemicals near a source of heat. 7) Pesticides, fungicides, etc. always must be stored in a safe and elevated position. Basically, there are four types of chemicals • Toxic chemicals : These are chemicals that are poisonous to you, and can act upon the body very rapidly. Hydrogen sulfide and cyanide are examples of toxic agents. • Corrosives : This type of chemical is usually an irritant. Corrosives can damage your body by burning, scalding or inflaming body tissues. Examples are chlorine and HCl acid. • Flammables : Flammables are the chemicals that burn readily. They may explode or burn if sparks, flames or other ignition sources are present. Examples are gasoline, benzene and ethyl ether. • Reactive : Reactive chemicals are those that require stability and careful handling. Some of them can explode or react violently if the container is dropped or hit. Nitroglycerine is an example. Basic Tips of Safe Chemical Handling 1. Read the label 2. Dress the part 3. Follow directions 4. Know emergency procedures 5. Be careful! 6. Report any suspected problems 7. Keep your work area neat, clean and organized 8. -
Gentix Plasticwares Vol II
1 CAT# Product Description Price( ) CAT# Product Description Price( ) Contents 02-03 Eco-Prep 04 05-29 PLASTICWARE (SPL) 30-57 58 59-61 62-63 64-67 BENCH TOP INSTRUMENTS 68-79 80-81 LAB SAFETY & HYGEINE 82 83 GENETIX BRAND GLOVES 84-85 2015-16 86-87 E-mail : [email protected] Call +91-11-45027000 ~ Fax: +91-11-25419631 2 CAT# Product Description Price( ) CAT# Product Description Price( ) Nucleopore brings you the best tools available for purification of nucleic acids (DNA and RNA) and NP-36172 Rapid Prep 96 Plasmid Kit (4 Plates) 54,180 proteins. These kits are user-friendly, reliable, effi- NP-36174 Rapid Prep 96 Plasmid Kit (24 Plates) 273,420 cient and versatile. NP-37192 SureSpin® Plasmid 96 Kit, 1 x 96 Preps POR NP-37193 SureSpin® Plasmid 96 Kit, 4 x 96 Preps POR NP-79182 DNA SureSpin 96 Plant Kit, 4 x 96 Preps POR NP-79183 DNA SureSpin 96 Plant Kit, 24 x 96 Preps POR NP-84182 RNA SureSpin 96 Kit, 2 x 96 Preps POR NP-84183 RNA SureSpin 96 Kit, 4 x 96 Preps POR Genomic DNA Purification Tissue NP-61305 DNASure® Tissue Mini Kit (50) 9,324 NP-61307 DNASure® Tissue Mini Kit (250) 39,690 Benefits: NP-66405 DNASure® PET Mini Kit (50) 10,710 l Reliable Analysis NP-1003D Nucleopore® MicroPET DNA Mini Kit (50) 27,996 l Reproducible Results l Increased Power to Compete Blood DNA Extraction Kits (Plasmid & Genomic) NP-61105 DNASure® Blood Mini Kit (50) 8,820 Plasmid DNA Purification NP-61107 DNASure® Blood Mini Kit (250) 37,800 NP-37105 SureSpin® Plasmid Mini Kit (50) 5,230 NP-61184 DNASure® Blood Midi Kit (20) 12,474 NP-37107 SureSpin® -
Lenz® – the Specialist for Ground Joints
Lenz Laborglas GmbH & Co. KG Am Ried 8 | 97877 Wertheim | Germany Telefon +49 (0) 93 42-96 09-0 Fax +49 (0) 93 42-96 09-30 [email protected] www.lenz-laborglas.de Lenz® – The Specialist for Ground Joints The Lenz® range of laboratory glassware • Ground joints • Stopcocks • Flasks • Separating/dropping funnels, chromatography • Components and condensers • Extractors • General laboratory accessories • Water stills • Reaction vessels and accessories GENERAL CATALOGUE EDITION 17 6. Distillation, Separation, Filtration Distillation/Connectors, Stillheads 1 Distillation adapters (plain bends), ground glass joint 1 Made of DURAN® tubing. Lenz With socket and outlet tube angled at 105°, 12mm diameter. Length* Socket PK Cat. No. NS 65 29/32 1 9.012 603 200 29/32 1 9.012 606 * Outlet tube length (mm) 2 3 Receiver adapters 2 3 Made of DURAN® tubing. With vent/vacuum connection. Straight or angled (105°),with Lenz nozzle. Socket Cone Form PK Cat. No. NS NS 14/23 14/23 straight 1 9.012 611 14/23 14/23 angled 1 9.012 613 29/32 29/32 straight 1 9.012 621 29/32 29/32 angled 1 9.012 623 4 Splash head adapter, ground glass joint NEW! 4 Borosilicate glass 3.3 which is resistant to heat and almost all chemicals. Suitable to be Isolab used in distillation assemblies to prevent raw liquid step over from flask to condenser. Socket Cone Description PK Cat. No. NS NS 14/23 14/23 straight 1 4.008 373 29/32 29/32 straight 1 4.008 374 We can supply this manufactorer’s whole product range ! E & OE. -
Isotopic Signatures of Production and Uptake of H2 by Soil
"! Isotopic signatures of production and uptake of H2 by soil #! $! Qianjie Chen1, 2, Maria E Popa1, Anneke M Batenburg1, 3, and Thomas Röckmann1 %! &! 1 Institute for Marine and Atmospheric research Utrecht, Utrecht University, The Netherlands '! 2 Department of Atmospheric Sciences, University of Washington, Seattle, Washington, USA (! 3 Department of Applied Physics, University of Eastern Finland, Kuopio, Finland )! *! "+! ""! "#! "$! "%! "&! "'! "(! ")! "*! #+! #"! ##! ! ! "! #$! Abstract: Molecular hydrogen (H2) is the second most abundant reduced trace #%! gas (after methane) in the atmosphere, but its biogeochemical cycle is not well #&! understood. Our study focuses on the soil production and uptake of H2 and the #'! associated isotope effects. Air samples from a grass field and a forest site in the #(! Netherlands were collected using soil chambers. The results show that uptake #)! and emission of H2 occurred simultaneously at all sampling sites, with strongest #*! emission at the grassland sites where clover (N2 fixing legume) was present. $+! The H2 mole fraction and deuterium content were measured in the laboratory to $"! determine the isotopic fractionation factor during H2 soil uptake (!soil) and the $#! isotopic signature of H2 that is simultaneously emitted from the soil ("Dsoil). By $$! considering all net-uptake experiments, an overall fractionation factor for $%! deposition of !soil = kHD / kHH = 0.945±0.004 (95% CI) was obtained. The $&! difference in mean !soil between the forest soil 0.937±0.008 and the grassland $'! 0.951±0.025 is not statistically significant. For two experiments, the removal of $(! soil cover increased the deposition velocity (vd) and !soil simultaneously, but a $)! general positive correlation between vd and !soil was not found in this study.