Airdata Measurement and Calibration
Total Page:16
File Type:pdf, Size:1020Kb
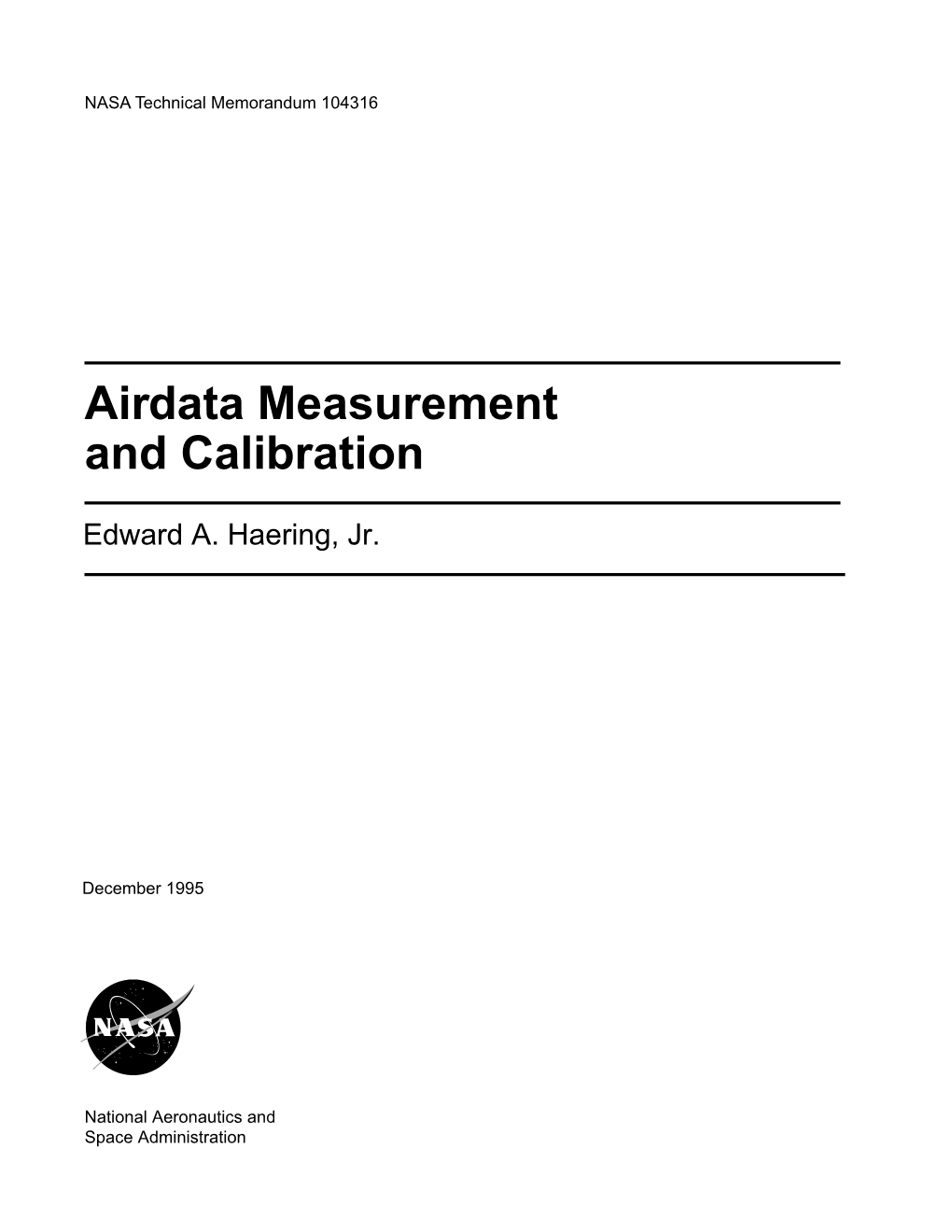
Load more
Recommended publications
-
Pitot-Static System Blockage Effects on Airspeed Indicator
The Dramatic Effects of Pitot-Static System Blockages and Failures by Luiz Roberto Monteiro de Oliveira . Table of Contents I ‐ Introduction…………………………………………………………………………………………………………….1 II ‐ Pitot‐Static Instruments…………………………………………………………………………………………..3 III ‐ Blockage Scenarios – Description……………………………..…………………………………….…..…11 IV ‐ Examples of the Blockage Scenarios…………………..……………………………………………….…15 V ‐ Disclaimer………………………………………………………………………………………………………………50 VI ‐ References…………………………………………………………………………………………….…..……..……51 Please also review and understand the disclaimer found at the end of the article before applying the information contained herein. I - Introduction This article takes a comprehensive look into Pitot-static system blockages and failures. These typically affect the airspeed indicator (ASI), vertical speed indicator (VSI) and altimeter. They can also affect the autopilot auto-throttle and other equipment that relies on airspeed and altitude information. There have been several commercial flights, more recently Air France's flight 447, whose crash could have been due, in part, to Pitot-static system issues and pilot reaction. It is plausible that the pilot at the controls could have become confused with the erroneous instrument readings of the airspeed and have unknowingly flown the aircraft out of control resulting in the crash. The goal of this article is to help remove or reduce, through knowledge, the likelihood of at least this one link in the chain of problems that can lead to accidents. Table 1 below is provided to summarize -
Airspeed Indicator Calibration
TECHNICAL GUIDANCE MATERIAL AIRSPEED INDICATOR CALIBRATION This document explains the process of calibration of the airspeed indicator to generate curves to convert indicated airspeed (IAS) to calibrated airspeed (CAS) and has been compiled as reference material only. i Technical Guidance Material BushCat NOSE-WHEEL AND TAIL-DRAGGER FITTED WITH ROTAX 912UL/ULS ENGINE APPROVED QRH PART NUMBER: BCTG-NT-001-000 AIRCRAFT TYPE: CHEETAH – BUSHCAT* DATE OF ISSUE: 18th JUNE 2018 *Refer to the POH for more information on aircraft type. ii For BushCat Nose Wheel and Tail Dragger LSA Issue Number: Date Published: Notable Changes: -001 18/09/2018 Original Section intentionally left blank. iii Table of Contents 1. BACKGROUND ..................................................................................................................... 1 2. DETERMINATION OF INSTRUMENT ERROR FOR YOUR ASI ................................................ 2 3. GENERATING THE IAS-CAS RELATIONSHIP FOR YOUR AIRCRAFT....................................... 5 4. CORRECT ALIGNMENT OF THE PITOT TUBE ....................................................................... 9 APPENDIX A – ASI INSTRUMENT ERROR SHEET ....................................................................... 11 Table of Figures Figure 1 Arrangement of instrument calibration system .......................................................... 3 Figure 2 IAS instrument error sample ........................................................................................ 7 Figure 3 Sample relationship between -
Sept. 12, 1950 W
Sept. 12, 1950 W. ANGST 2,522,337 MACH METER Filed Dec. 9, 1944 2 Sheets-Sheet. INVENTOR. M/2 2.7aar alwg,57. A77OAMA). Sept. 12, 1950 W. ANGST 2,522,337 MACH METER Filed Dec. 9, 1944 2. Sheets-Sheet 2 N 2 2 %/ NYSASSESSN S2,222,W N N22N \ As I, mtRumaIII-m- III It's EARAs i RNSITIE, 2 72/ INVENTOR, M247 aeawosz. "/m2.ATTORNEY. Patented Sept. 12, 1950 2,522,337 UNITED STATES ; :PATENT OFFICE 2,522,337 MACH METER Walter Angst, Manhasset, N. Y., assignor to Square D Company, Detroit, Mich., a corpora tion of Michigan Application December 9, 1944, Serial No. 567,431 3 Claims. (Cl. 73-182). is 2 This invention relates to a Mach meter for air plurality of posts 8. Upon one of the posts 8 are craft for indicating the ratio of the true airspeed mounted a pair of serially connected aneroid cap of the craft to the speed of sound in the medium sules 9 and upon another of the posts 8 is in which the aircraft is traveling and the object mounted a diaphragm capsuler it. The aneroid of the invention is the provision of an instrument s: capsules 9 are sealed and the interior of the cas-l of this type for indicating the Mach number of an . ing is placed in communication with the static aircraft in fight. opening of a Pitot static tube through an opening The maximum safe Mach number of any air in the casing, not shown. The interior of the dia craft is the value of the ratio of true airspeed to phragm capsule is connected through the tub the speed of sound at which the laminar flow of ing 2 to the Pitot or pressure opening of the Pitot air over the wings fails and shock Waves are en static tube through the opening 3 in the back countered. -
E6bmanual2016.Pdf
® Electronic Flight Computer SPORTY’S E6B ELECTRONIC FLIGHT COMPUTER Sporty’s E6B Flight Computer is designed to perform 24 aviation functions and 20 standard conversions, and includes timer and clock functions. We hope that you enjoy your E6B Flight Computer. Its use has been made easy through direct path menu selection and calculation prompting. As you will soon learn, Sporty’s E6B is one of the most useful and versatile of all aviation computers. Copyright © 2016 by Sportsman’s Market, Inc. Version 13.16A page: 1 CONTENTS BEFORE USING YOUR E6B ...................................................... 3 DISPLAY SCREEN .................................................................... 4 PROMPTS AND LABELS ........................................................... 5 SPECIAL FUNCTION KEYS ....................................................... 7 FUNCTION MENU KEYS ........................................................... 8 ARITHMETIC FUNCTIONS ........................................................ 9 AVIATION FUNCTIONS ............................................................. 9 CONVERSIONS ....................................................................... 10 CLOCK FUNCTION .................................................................. 12 ADDING AND SUBTRACTING TIME ....................................... 13 TIMER FUNCTION ................................................................... 14 HEADING AND GROUND SPEED ........................................... 15 PRESSURE AND DENSITY ALTITUDE ................................... -
Aviation Occurrence No 200403238
ATSB TRANSPORT SAFETY INVESTIGATION REPORT Aviation Occurrence Report – 200403238 / 200404436 Final Abnormal airspeed indications En route from/to Brisbane Qld 31 August 2004 / 9 November 2004 Bombardier Aerospace DHC8-315 VH-SBJ / VH-SBW ATSB TRANSPORT SAFETY INVESTIGATION REPORT Aviation Occurrence Report 200403238 / 200404436 Final Abnormal airspeed indications En route from/to Brisbane Qld 31 August 2004 / 9 November 2004 Bombardier Aerospace DHC8-315 VH-SBJ / VH-SBW Released in accordance with section 25 of the Transport Safety Investigation Act 2003 - i - Published by: Australian Transport Safety Bureau Postal address: PO Box 967, Civic Square ACT 2608 Office location: 15 Mort Street, Canberra City, Australian Capital Territory Telephone: 1800 621 372; from overseas + 61 2 6274 6590 Accident and serious incident notification: 1 800 011 034 (24 hours) Facsimile: 02 6274 6474; from overseas + 61 2 6274 6474 E-mail: [email protected] Internet: www.atsb.gov.au © Commonwealth of Australia 2007. This work is copyright. In the interests of enhancing the value of the information contained in this publication you may copy, download, display, print, reproduce and distribute this material in unaltered form (retaining this notice). However, copyright in the material obtained from non- Commonwealth agencies, private individuals or organisations, belongs to those agencies, individuals or organisations. Where you want to use their material you will need to contact them directly. Subject to the provisions of the Copyright Act 1968, you must not make any other use of the material in this publication unless you have the permission of the Australian Transport Safety Bureau. Please direct requests for further information or authorisation to: Commonwealth Copyright Administration, Copyright Law Branch Attorney-General’s Department, Robert Garran Offices, National Circuit, Barton ACT 2600 www.ag.gov.au/cca - ii - CONTENTS THE AUSTRALIAN TRANSPORT SAFETY BUREAU ................................. -
Air Data Computer 8EB3AAA1 DESCRIPTION AMETEK Has Designed a Compact, Solid State Air Data Computer for Military Applications
Air Data Computer 8EB3AAA1 DESCRIPTION AMETEK has designed a compact, solid state Air Data Computer for military applications. The Air Data Computer utilizes a digital signal processor for fast calculation and response of air data parameters. Silicon pressure transducers provide the static and Pitot pressure values and are easily replaced without calibration. The AMETEK Air Data Computer incorporates a unique power supply that allows the unit to operate through 5 second power interrupts when at any input voltage in its operating range. This ensures that critical air data parameters reach the cockpit and control systems under a FEATURES wide variety of conditions. 3 The MIL-STD-1553 interface 40 ms update rate Thirteen (13) different air data parameters are provided on the MIL-STD- 3 11-bit reported pressure 1553B interface and are calculated by the internal processor at a 40 ms rate. altitude interface 3 AOA and total temperature An 11-bit reported pressure altitude interface encoded per FAA order inputs 1010.51A is available for Identification Friend or Foe equipment. 3 Low weight: 2.29 lbs. 3 Small size: 6.81” x 6.0” x 2.5” 3 Low power: 1.5 watts 3 DO-178B level A software AEROSPACE & DEFENSE Air Data Computer 8EB3AAA1 SPECIFICATIONS PERFORMANCE CHARACTERISTICS Air Data Parameters Power: DO-160, Section 16 Cat Z or MIL-STD-704A-F • ADC Altitude Rate Output (Hpp or dHp/dt) 5 second power Interruption immunity at any • True Airspeed Output (Vt) input voltage • Calibrated Airspeed Output (Vc) Power Consumption: 1.5 watts • Indicated Airspeed Output (IAS) Operating Temperature: -55°C to +71°C; 1/2 hour at +90°C • Mach Number Output (Mt) Weight: 2.29 lbs. -
Upwind Sail Aerodynamics : a RANS Numerical Investigation Validated with Wind Tunnel Pressure Measurements I.M Viola, Patrick Bot, M
Upwind sail aerodynamics : A RANS numerical investigation validated with wind tunnel pressure measurements I.M Viola, Patrick Bot, M. Riotte To cite this version: I.M Viola, Patrick Bot, M. Riotte. Upwind sail aerodynamics : A RANS numerical investigation validated with wind tunnel pressure measurements. International Journal of Heat and Fluid Flow, Elsevier, 2012, 39, pp.90-101. 10.1016/j.ijheatfluidflow.2012.10.004. hal-01071323 HAL Id: hal-01071323 https://hal.archives-ouvertes.fr/hal-01071323 Submitted on 8 Oct 2014 HAL is a multi-disciplinary open access L’archive ouverte pluridisciplinaire HAL, est archive for the deposit and dissemination of sci- destinée au dépôt et à la diffusion de documents entific research documents, whether they are pub- scientifiques de niveau recherche, publiés ou non, lished or not. The documents may come from émanant des établissements d’enseignement et de teaching and research institutions in France or recherche français ou étrangers, des laboratoires abroad, or from public or private research centers. publics ou privés. I.M. Viola, P. Bot, M. Riotte Upwind Sail Aerodynamics: a RANS numerical investigation validated with wind tunnel pressure measurements International Journal of Heat and Fluid Flow 39 (2013) 90–101 http://dx.doi.org/10.1016/j.ijheatfluidflow.2012.10.004 Keywords: sail aerodynamics, CFD, RANS, yacht, laminar separation bubble, viscous drag. Abstract The aerodynamics of a sailing yacht with different sail trims are presented, derived from simulations performed using Computational Fluid Dynamics. A Reynolds-averaged Navier- Stokes approach was used to model sixteen sail trims first tested in a wind tunnel, where the pressure distributions on the sails were measured. -
WM@ 93,@ 2,807,165 United States Patent O Ice Patented Sept
Sept. 24, 1957 w, KUZYK :TAL 2,807,165 CRUISE CONTROL METER Filed NOV. 5. 1953 m razona ovnnnvc Henn »119m sfuma »no ,.4 ' mmmcrcg, VILA-IHM. KUZYK DONALD. C. WHITTl-CY PCQ,WM@ 93,@ 2,807,165 United States Patent O ice Patented Sept. 24, 1957 2 1 and the Machmeter is also connected by a pipe 14 to a Pitot head (not shown) which senses the dynamic air 2,307,165 pressure, the latter being dependent upon the airspeed of the aircraft. The term “altitude” as used herein refers CRUISE CoNTRoL METER to the “pressure altitude” of the aircraft rather than to William Kuzyk, Weston, Ontario, and Donald Charles the absolute altitude in vfeet or another linear unit. Whittley, Etobicoke, Ontario, Canada, assignors, by Mounted in front of the scale 10b of the altimeter 10 mesne assignments, to Avro Aircraft Limited, Malton, is a transparent disc 15 held by a rotatable bezel ring 16. Ontario, Canada, a corporation The bezel ring 16 is enclosed by an annular rim 17. Application November 3, 1953, Serial No. 390,014 Along its inner edge the rim 17 has a peripheral flange 17a which is secured to the panel 12 and surrounds the Claims priority, application Canada December 16, 1952 scale 10b, and along its outer edge the rim 17 has a periph 4 Claims. (Cl. 73-178) eral flange 17b. The bezel ring 16 is rotatably supported within the rim 17 on spaced apart idler pinions 18 and a drive pinion 19, rollers 20 being provided between the This invention relates to aircraft instruments and par bezel ring 16 and the outer flange 17b of the rim. -
AIRSPEED INDICATORS - ALTIMETERS WINTER 3-INCH ALTIMETERS WINTER 2-1/4 INCH Standard Precision Altimeters 4 FGH 10
AIRSPEED INDICATORS - ALTIMETERS WINTER 3-INCH ALTIMETERS WINTER 2-1/4 INCH Standard Precision Altimeters 4 FGH 10. AIRSPEED INDICATORS Airtight, black plastic housing. Connection This precision instrument is enclosed in a via hose from static pressure sensor to hose CM compact housing and operates by means of a connector on rear. Kollsman window with measuring tube. This ensures high accuracy millibar scale, reading from 940 to 1050 even at very low speeds. EBF-series airspeed millibars. See scale drawing for installation indicators are available with a pitot tube and dimensions. static pressure connection. Weight 0.330 kg. Linear scale The 4 FGH 10 altimeter can be fitted with a Description Part No. Price WP scale ring. Winter 2-1/4 ASI 8020 EBF Various 10-05625 $374.00 Range 360 Degree Dial Description Part No. Price Winter 2-1/4 ASI 8022 EBF Various 10-05627 $374.00 Winter 3 Altimeter 4 FGH 10 1000-20000 FT MB 10-05621 $1,202.00 Range 360 Degree Dial Winter 3 Altimeter 4 FGH 10 1000-20000 FT INHG 10-05622 $1,198.00 ME Winter 2-1/4 ASI 8026 EBF Various 10-05629 $455.00 Range 510 Degree Dial Winter 2-1/4” ASI 7 FMS 213 10-05908 $603.00 Range 0 To 100 Knot 360 Dial WINTER 2-1/4 INCH ALTIMETERS The pressure-sensitive measuring element is HA WINTER 3 INCH a diaphragm capsule (aneroid capsule) which AIRSPEED INDICATORS reacts to the effect of changing air pressure This precision instrument is enclosed in a com- as the aircraft changes altitude. -
Joint Aviation Requirements JAR–FCL 1 ЛИЦЕНЗИРОВАНИЕ ЛЕТНЫХ ЭКИПАЖЕЙ (САМОЛЕТЫ)
Joint Aviation Requirements JAR–FCL 1 ЛИЦЕНЗИРОВАНИЕ ЛЕТНЫХ ЭКИПАЖЕЙ (САМОЛЕТЫ) Joint Aviation Authorities 1 JAR-FCL 1 ЛИЦЕНЗИРОВАНИЕ ЛЕТНЫХ ЭКИПАЖЕЙ (САМОЛЕТЫ) Издано 14 февраля 1997 года ПРЕДИСЛОВИЕ ПРЕАМБУЛА ЧАСТЬ 1 - ТРЕБОВАНИЯ ПОДЧАСТЬ A – ОБЩИЕ ТРЕБОВАНИЯ JAR-FCL 1.001 Определения и Сокращения JAR-FCL 1.005 Применимость JAR-FCL 1.010 Основные полномочия членов летного экипажа JAR-FCL 1.015 Признание свидетельств, допусков, разрешений, одобрений или сер- тификатов JAR-FCL 1.016 Кредит, предоставляемый владельцу свидетельства, полученного в государстве не члене JAA JAR-FCL 1.017 Разрешения/квалификационные допуски для специальных целей JAR-FCL 1.020 Учет военной службы JAR-FCL 1.025 Действительность свидетельств и квалификационных допусков JAR-FCL 1.026 Свежий опыт для пилотов, не выполняющих полеты в соответствии с JAR-OPS 1 JAR-FCL 1.030 Порядок тестирования JAR-FCL 1.035 Годность по состоянию здоровья JAR-FCL 1.040 Ухудшение состояния здоровья JAR-FCL 1.045 Особые обстоятельства JAR-FCL 1.050 Кредитование летного времени и теоретических знаний JAR-FCL 1.055 Организации и зарегистрированные предприятия JAR-FCL 1.060 Ограничение прав владельцев свидетельств, достигших 60-летнего возраста и более JAR-FCL 1.065 Государство выдачи свидетельства 2 JAR-FCL 1.070 Место обычного проживания JAR-FCL 1.075 Формат и спецификации свидетельств членов летных экипажей JAR-FCL 1.080 Учет летного времени Приложение 1 к JAR-FCL 1.005 Минимальные требования для выдачи свиде- тельства/разрешения JAR-FCL на основе нацио- нального свидетельства/разрешения, выданного в государстве-члене JAA. Приложение 1 к JAR-FCL 1.015 Минимальные требования для признания дейст- вительности свидетельств пилотов, выданных государствами не членами JAA. -
Investigation of Sailing Yacht Aerodynamics Using Real Time Pressure and Sail Shape Measurements at Full Scale
18th Australasian Fluid Mechanics Conference Auckland, New Zealand 3-7 December 2012 Investigation of sailing yacht aerodynamics using real time pressure and sail shape measurements at full scale F. Bergsma1,D. Motta2, D.J. Le Pelley2, P.J. Richards2, R.G.J. Flay2 1Engineering Fluid Dynamics,University of Twente, Twente, Netherlands 2Yacht Research Unit, University of Auckland, Auckland, New Zealand Abstract VSPARS for sail shape measurement The steady and unsteady aerodynamic behaviour of a sailing yacht Visual Sail Position and Rig Shape (VSPARS) is a system that is investigated in this work by using full-scale testing on a Stewart was developed at the YRU by Le Pelley and Modral [7]; it is 34. The aerodynamic forces developed by the yacht in real time designed to measure sail shape and can handle large perspective are derived from knowledge of the differential pressures across the effects and sails with large curvatures using off-the-shelf cameras. sails and the sail shape. Experimental results are compared with The shape is recorded using several coloured horizontal stripes on numerical computation and good agreement was found. the sails. A certain number of user defined point locations are defined by the system, together with several section characteristics Introduction such as camber, draft, twist angle, entry and exit angles, bend, sag, Sail aerodynamics is an open field of research in the scientific etc. All these outputs are then imported into the FEPV system and community. Some of the topics of interest are knowledge of the appropriately post-processed. The number of coloured stripes used flying sail shape, determination of the pressure distribution across is arbitrary, but it is common practice to use 3-4 stripes per sail. -
Introduction
CHAPTER 1 Introduction "For some years I have been afflicted with the belief that flight is possible to man." Wilbur Wright, May 13, 1900 1.1 ATMOSPHERIC FLIGHT MECHANICS Atmospheric flight mechanics is a broad heading that encompasses three major disciplines; namely, performance, flight dynamics, and aeroelasticity. In the past each of these subjects was treated independently of the others. However, because of the structural flexibility of modern airplanes, the interplay among the disciplines no longer can be ignored. For example, if the flight loads cause significant structural deformation of the aircraft, one can expect changes in the airplane's aerodynamic and stability characteristics that will influence its performance and dynamic behavior. Airplane performance deals with the determination of performance character- istics such as range, endurance, rate of climb, and takeoff and landing distance as well as flight path optimization. To evaluate these performance characteristics, one normally treats the airplane as a point mass acted on by gravity, lift, drag, and thrust. The accuracy of the performance calculations depends on how accurately the lift, drag, and thrust can be determined. Flight dynamics is concerned with the motion of an airplane due to internally or externally generated disturbances. We particularly are interested in the vehicle's stability and control capabilities. To describe adequately the rigid-body motion of an airplane one needs to consider the complete equations of motion with six degrees of freedom. Again, this will require accurate estimates of the aerodynamic forces and moments acting on the airplane. The final subject included under the heading of atmospheric flight mechanics is aeroelasticity.