Simulation Technology for Railway Vehicle Dynamics
Total Page:16
File Type:pdf, Size:1020Kb
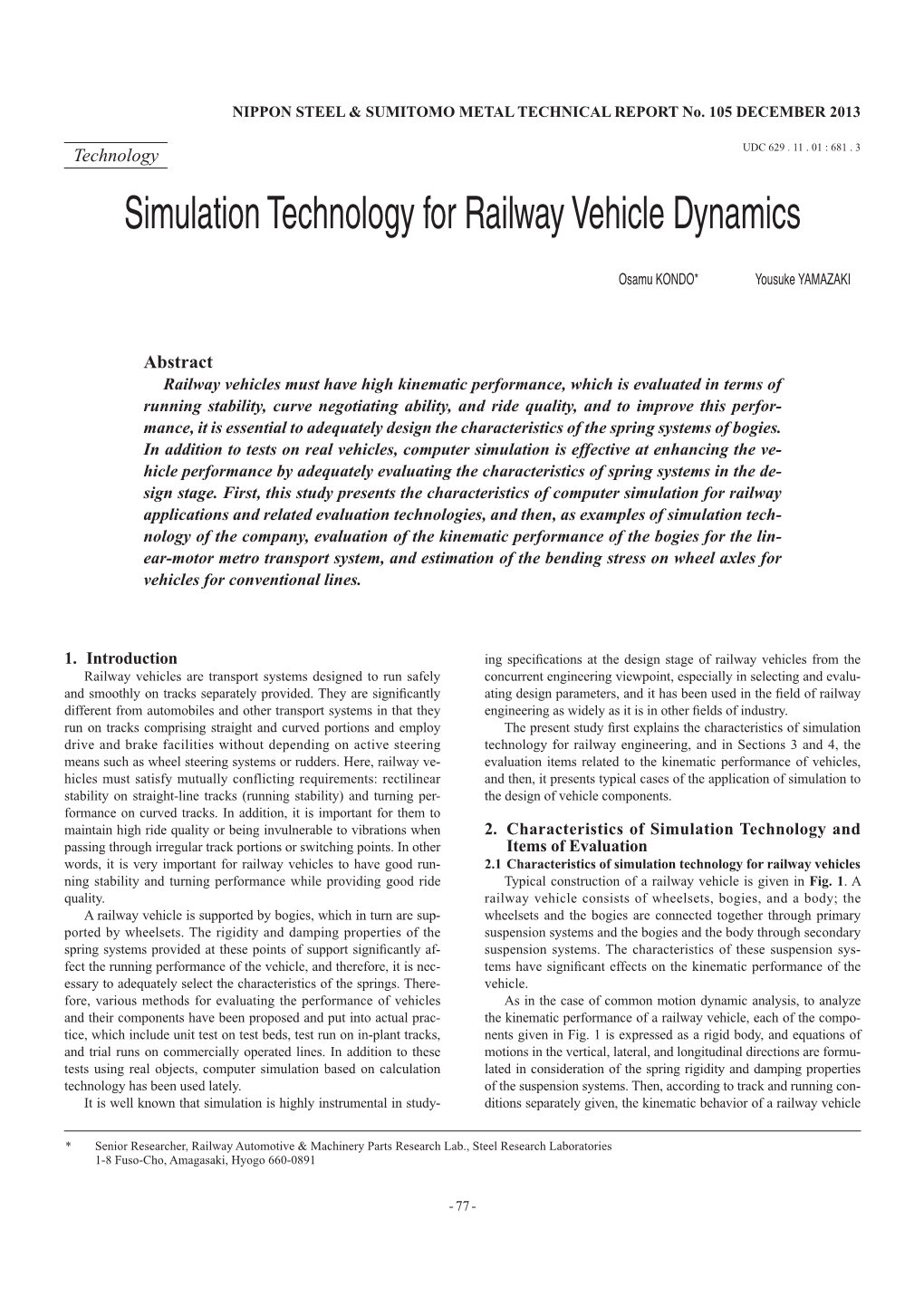
Load more
Recommended publications
-
Hyōgo Prefecture
Coor din ates: 3 4 °4 1 ′2 6 .9 4 ″N 1 3 5 °1 0′5 9 .08″E Hyōgo Prefecture Hyōgo Prefecture (兵庫県 Hyōgo-ken) is a prefecture of Japan located in the Kansai region on Hyōgo Prefecture Honshu island.[1] The capital is Kobe.[2] 兵庫県 Prefecture Contents Japanese transcription(s) • Japanese 兵庫県 History • Rōmaji Hyōgo-ken Geography Cities Towns Islands National parks Mergers Flag Future mergers Symbol Economy Culture National Treasures of Japan Important Preservation Districts for Groups of Historic Buildings in Japan Museums Education Universities Amagasaki Takarazuka Sanda Nishinomiya Ashiya Kobe Kato Akashi Kakogawa Country Japan Himeji Region Kansai Akō Island Honshu High schools Capital Kobe Sports Government Tourism • Governor Toshizō Ido Festival and events Area Transportation Rail • Total 8,396.13 km2 People movers (3,241.76 sq mi) Road Area rank 12th Expressways Population (November 1, 2011) National highways Ports • Total 5,582,978 Airport • Rank 7th • Density 660/km2 (1,700/sq mi) Notable people Sister regions ISO 3166 JP-28 code See also Notes Districts 8 References Municipalities 41 External links Flower Nojigiku (Chrysanthemum japonense) Tree Camphor tree History (Cinnamomum camphora) Bird Oriental white stork Present-day Hyōgo Prefecture includes the former provinces of Harima, Tajima, Awaji, and parts (Ciconia boyciana) of Tanba and Settsu.[3] Website web.pref.hyogo.lg.jp/fl /english/ (http://web.pre In 1180, near the end of the Heian period, Emperor Antoku, Taira no Kiyomori, and the Imperial f.hyogo.lg.jp/fl/english/) court moved briefly to Fukuhara, in what is now the city of Kobe. -
Concentration of Field Offices
Dear Customers: March, 2016 Shinyei Capacitor Co., Ltd. Masafumi Ogata President and Representative Director Concentration of Field Offices We would like to express our sincere gratitude for your loyal patronage. As part of our move to strengthen our business functions, we will be incorporating our Tokyo field office in our head office (Shinyei Kaisha head office). This move is designed to strengthen the operations of our staff, and we hope that it will assist you in our relationship. Please excuse the informality of this letter. 1. New address: M-int Kobe ● Ikuta Shrine ● JR Kobe Line Shinyei Bldg. 5F, 77-1 Kyomachi, Chuo-ku, Hankyu Kobe Line Port Liner Sannomiya Station Sannomiya Station JR Sannomiya Station Sannomiya Station Kobe, Hyogo 650-0034, Japan ● West entrance Prefectural Highway 30 Municipal Subway Seishin and Yamate Line Sogo Sannomiya Station ● ● Kobe Marui Kobe International House Tel: +81-78-392-6909 ● San Plaza Center Plaza ● Fax: +81-78-332-1621 West Kobe-kosoku Line Center Plaza Prefectural● Highway 21 Clefy Sannomiya Sannomiya-Hanadokeimae Station ● Shinyei Building ● Banshu ● Shinkin Bank Flower Road Sannomiya Social Insurance MunicipalKaigan Subway Line Hanshin Main Line Office ● MotomachiStation Senshu Ikeda Bank, Kyomachisuji ● Kobe Branch ● Kobe City Hall 2. Commencement of operations: ● Kyukyoryuchi-Kobe Asahi Building● Japan Asia Securities Boeki Center Daimarumae Station Station Sannomiya Higashi-yuenchi Park ● Panasonic ● April 1st, 2016 (Friday) Daimaru Kobe Store● Daiichi-seimei Building● ・8 minutes walk from JR Sannomiya Station Nearest ・8 minutes walk from Sannomiya Station on the Hankyu stations Kobe Line, Hanshin Main Line, and Kobe-kosoku Line ・8 minutes walk from Sannomiya Station on the Municipal Subway Seishin and Yamate Line. -
Hanshin Electric Railway's
Autumn & Winter 2021 Version Tic le. kets ailab best w av suited are no for sightseeing and business Go out with convenient and money-saving tickets! Notice: Measures to prevent the spread of COVID-19 may be in place at some facilities, including entry restrictions, changes to business hours, temporary closures, etc. Please inquire directly at the relevant facility before visiting. Also, please bear in mind the above when purchasing Economical Tickets. A convenient and money-saving one-way ticket This ticket is very economical and convenient for KIX Keihan- for those traveling from Hanshin Line stations shin those who visit Keihanshin not only for to Kansai International Airport. leisure but also for business. Kanku Access Ticket Hankyu-Hanshin (Hanshin version) One-Day Pass Sale period On Sale Now to March 31, 2022 (Thursday) Sale period On Sale Now to March 31, 2022 (Thursday) Valid period Any single day until April 30, 2022 (Saturday) Valid period Any single day during the sale period Price 1,150 yen (adult fare only) Price Adult: 1,300 yen Child: 650 yen ■Valid section ■Valid section Hanshin Electric Railway: All lines Hanshin Electric Railway: From any station (except Kobe Kosoku Line) to Osaka-Namba Station Hankyu Railway: All lines Nankai Electric Railway: From Namba Station to Kansai-Airport Station Kobe Kosoku Line: All lines (including Nishidai and Minatogawa stations) ■Sales locations ■Sales locations Stationmaster’s office in Osaka-Umeda, Amagasaki, Koshien, Stationmaster’s office in Osaka-Umeda, Amagasaki, Koshien, Mikage, Kobe-Sannomiya Mikage and Kobe-Sannomiya and Hanshin Electric Railway and Shinkaichi stations, ticket gates at each station, Service Center (Kobe-Sannomiya) Osaka-Namba Station (adult pass only; available at East Limited Express Ticket Counter), and Hanshin Electric Railway Service Center (Kobe-Sannomiya) *This ticket cannot be used for travel from Kansai International Airport to any station on *Except Nishidai and Minatogawa stations and during the absence of station clerks Hanshin Electric Railway Line. -
Activia Properties Inc. (Code: 3279/API)
(証券コード:3279/API) Activia Properties Inc. (Code: 3279/API) Financial Results Presentation for the 19th Fiscal Period Ended May 2021– July 2021 Section1 1. Executive Summary 2. Financial Results & Forecasts Section2 3. External Growth 4. Internal Growth 5. Financial Management & ESG Appendix Relaxing green courtyard (A-PLACE Shinagawa Higashi) 1. Executive Summary Executive Summary 3 Despite temporary rent reductions were offered to tenants due to the state of emergency declarations, which happened twice during the period, FP19 results came in better than the management guidance Forecasts for FP20 and FP21 are calculated with an assumption that the COVID-19 impact will prolong We aim to enhance our unitholder value through external growth in preparation for the post COVID-19 and extra internal growth fully utilizing the unique & competitive characteristics of our properties Results Market Outlook • • DPU for the FP19 ended May 2021 • Uncertainty still prevails despite Forecast DPUs for the next FPs Results & resulted to be ¥9,401, up from the vaccination progresses assume COVID-19 impact prolongs Forecasts previous forecast as we could minimize • The entire facility closure would • ¥9,350 for FP20, Nov. 2021 the pandemic-related adverse impacts negatively affect our earnings • ¥9,100 for FP21, May 2022 • Focus on rent increase at tenant • Rent increase achieved at tenant • Rent increase slows as vacancy rate replacements leveraging upon replacements and lease renewals remains high strong demand for prime location backed by solid demand -
Available Area MAP SAGA TAKARAGAIKE Available Area MAP ANO-O SHUGAKUIN SHIGASATO KITANO LINE ICHIJOJI NISHIOJI-OIKE MINAMI-SHIGA LAKE BIWA
IWAKURA KYOTO SEIKADAI-MAE KURAMA 比叡山坂本ケーブル KINO HIEIZAN SAKAMOTO CABLE EIZAN ELECTRIC RAILWAY KIBUNEGUCHI OMURO- NINNAJI NINOSE MYOSHINJI KITANO-HAKUBAICHO KURUMAZAKI-JINJA CABLE-ENRYAKUJI RYOANJI ICHIHARA HIEIZAN TOJI-IN HIEIZAN UTANO KURAMA LINE MOTATEYAMA NIKENCHAYA 二軒茶屋 EIZAN MAIN LINE SAKAMOTO HORAIOKA YASE HIEIZANGUCHI YASE RANDEN (KEIFUKU RAILWAY) HACHIMAN-MAE CABLE SAKAMOTO KOKUSAI KAIKAN RANDEN- MIYAKEHACHIMAN ARISUGAWA MATSUNOBAMBA MATSUGASAKI ARASHIYAMA ROKUOIN Available Area MAP SAGA TAKARAGAIKE Available Area MAP ANO-O SHUGAKUIN SHIGASATO KITANO LINE ICHIJOJI NISHIOJI-OIKE MINAMI-SHIGA LAKE BIWA UZUMASA-TENJINGAWA KITAYAMA CHAYAMA OMIJINGU-MAE The convenient can be used on trains and buses in Kansai. NARUTAKI OJIYAMA TOKIWA MOTOTANAKA Available at KITAOJI Ishiyama-Sakamoto Line NIJO KARASUMA LINE BESSHO KATABIRANOTSUJI NIJOJO-MAE KURAMAGUCHI ARASHIYAMA MAIN LINE UZUMASA-KORYUJI DEMACHIYANAGI by presenting the PASS. MIIDERA NISSEI LINE MYOKENGUCHI KYOTO- DEMACHIYANAGI LEGEND WOODY TOWN CHUO ARASHIYAMAARASHIYAMA LINE SHIYAKUSYO-MAE HAMAOTSU KOENTOSHI LINE TOKIWADAI SAITO LINE KAIKONOYASHIRO IMADEGAWA ISHIYAMASAKAMOTO LINE MIKIUENOMARU OTSU ■ MINAMI-WOODY TOWN KOFUDAI MATSUO JINGU-MARUTAMACHI SANJO KEIHAN OTSU RAILROAD AREA EBISU NISSEI-CHUO SAITONISHI RANDEN-TENJINGAWA MARUTAMACHI KAMISAKAEMACHI 叡山電車 AO HATA ONO ICHIBA KASHIYAMA OMURA MIKI SASABE YAMANOUCHI EIZAN ELECTORIC RAILWAY SHIJIMI FLOWER TOWN YAMASHITA HIRONO GOLFJO-MAE MYOKEN LINE NOSE ELECTRIC RAILWAY TOZAI LINE OTANI AO LINE KAMI-KATSURA OMIYA SHIMANOSEKI KINTETSU -
Activia Properties Inc. (Code: 3279/API)
(証券コード:3279/API) Activia Properties Inc. (Code: 3279/API) Financial Results Presentation for the 19th Fiscal Period Ended May 2021– July 2021 Section1 1. Executive Summary 2. Financial Results & Forecasts Section2 3. External Growth 4. Internal Growth 5. Financial Management & ESG Appendix Relaxing green courtyard (A-PLACE Shinagawa Higashi) 1. Executive Summary Executive Summary 3 Despite temporary rent reductions were offered to tenants due to the state of emergency declarations, which happened twice during the period, FP19 results came in better than the management guidance Forecasts for FP20 and FP21 are calculated with an assumption that the COVID-19 impact will prolong We aim to enhance our unitholder value through external growth in preparation for the post COVID-19 and extra internal growth fully utilizing the unique & competitive characteristics of our properties Results Market Outlook • • DPU for the FP19 ended May 2021 • Uncertainty still prevails despite Forecast DPUs for the next FPs Results & resulted to be ¥9,401, up from the vaccination progresses assume COVID-19 impact prolongs Forecasts previous forecast as we could minimize • The entire facility closure would • ¥9,350 for FP20, Nov. 2021 the pandemic-related adverse impacts negatively affect our earnings • ¥9,100 for FP21, May 2022 • Focus on rent increase at tenant • Rent increase achieved at tenant • Rent increase slows as vacancy rate replacements leveraging upon replacements and lease renewals remains high strong demand for prime location backed by solid demand -
METROS/U-BAHN Worldwide
METROS DER WELT/METROS OF THE WORLD STAND:31.12.2020/STATUS:31.12.2020 ّ :جمهورية مرص العرب ّية/ÄGYPTEN/EGYPT/DSCHUMHŪRIYYAT MISR AL-ʿARABIYYA :القاهرة/CAIRO/AL QAHIRAH ( حلوان)HELWAN-( المرج الجديد)LINE 1:NEW EL-MARG 25.12.2020 https://www.youtube.com/watch?v=jmr5zRlqvHY DAR EL-SALAM-SAAD ZAGHLOUL 11:29 (RECHTES SEITENFENSTER/RIGHT WINDOW!) Altamas Mahmud 06.11.2020 https://www.youtube.com/watch?v=P6xG3hZccyg EL-DEMERDASH-SADAT (LINKES SEITENFENSTER/LEFT WINDOW!) 12:29 Mahmoud Bassam ( المنيب)EL MONIB-( ش ربا)LINE 2:SHUBRA 24.11.2017 https://www.youtube.com/watch?v=-UCJA6bVKQ8 GIZA-FAYSAL (LINKES SEITENFENSTER/LEFT WINDOW!) 02:05 Bassem Nagm ( عتابا)ATTABA-( عدىل منصور)LINE 3:ADLY MANSOUR 21.08.2020 https://www.youtube.com/watch?v=t7m5Z9g39ro EL NOZHA-ADLY MANSOUR (FENSTERBLICKE/WINDOW VIEWS!) 03:49 Hesham Mohamed ALGERIEN/ALGERIA/AL-DSCHUMHŪRĪYA AL-DSCHAZĀ'IRĪYA AD-DĪMŪGRĀTĪYA ASCH- َ /TAGDUDA TAZZAYRIT TAMAGDAYT TAỴERFANT/ الجمهورية الجزائرية الديمقراطيةالشعبية/SCHA'BĪYA ⵜⴰⴳⴷⵓⴷⴰ ⵜⴰⵣⵣⴰⵢⵔⵉⵜ ⵜⴰⵎⴰⴳⴷⴰⵢⵜ ⵜⴰⵖⴻⵔⴼⴰⵏⵜ : /DZAYER TAMANEỴT/ دزاير/DZAYER/مدينة الجزائر/ALGIER/ALGIERS/MADĪNAT AL DSCHAZĀ'IR ⴷⵣⴰⵢⴻⵔ ⵜⴰⵎⴰⵏⴻⵖⵜ PLACE DE MARTYRS-( ع ني نعجة)AÏN NAÂDJA/( مركز الحراش)LINE:EL HARRACH CENTRE ( مكان دي مارت بز) 1 ARGENTINIEN/ARGENTINA/REPÚBLICA ARGENTINA: BUENOS AIRES: LINE:LINEA A:PLACA DE MAYO-SAN PEDRITO(SUBTE) 20.02.2011 https://www.youtube.com/watch?v=jfUmJPEcBd4 PIEDRAS-PLAZA DE MAYO 02:47 Joselitonotion 13.05.2020 https://www.youtube.com/watch?v=4lJAhBo6YlY RIO DE JANEIRO-PUAN 07:27 Así es BUENOS AIRES 4K 04.12.2014 https://www.youtube.com/watch?v=PoUNwMT2DoI -
Tokyo Individualized Educational Institute Announces the Opening of Two New Schools in Kansai Area
News Release :Tokyo Individualized Educational Institute, Inc. (4745 TSE 1) February 17, 2014 Tokyo Individualized Educational Institute Announces the Opening of Two New Schools In Kansai Area Tokyo Individualized Educational Institute, Inc. (TIEI) announces that the Company will open two new schools - “Kansai Individualized Educational Institute Sannomiya School (Kobe-shi, Hyogo)” and “Kansai Individualized Educational Institute Uehonmachi School (Osaka-shi, Osaka)”- on March 13, 2014 as follows. The opening of both schools is based on the “Shining☆2015” medium-term management plan announced in October 2013. TIEI will operate schools in full-scale in Kansa by opening three schools including the “Kansai Individualized Educational Institute Tennoji School” to be opened on March 7 in populated areas near railway stations. Including two new schools, the total number of schools directly operated by TIEI will be 211. Seven new schools are scheduled to open during the fiscal year ending February 2015. 1. Kansai Individualized Educational Institute Sannomiya School 1) Date of opening: March 13, 2014 (Thursday) 2) Address: 4F Neoffice Sannomiya, 4-2-12 Nunobiki-cho, Chuo-ku, Kobe-shi, Hyogo 651-0097 (1 or 2 minutes’ walk from JR Kobe Line “Sannomiya” Station, Hankyu Kobe Line “Kobe Sannomiya” Station, Hanshin Kobe Line “Sannomiya” Station, Kobe Subway Nishijin/Yamate Line “Sannomiya” Station, Port Island Line “Sannomiya” Station; 5 minutes’ walk from Kobe Subway Kaigan Line “Sannomiya/Hanadokei” Station) 2. Kansai Individualized Educational Institute -
Inside • the Cheapskate's Guide to Japanese Travel • Language of Love
1.16 ht Inside • The Cheapskate’s Guide to Japanese Travel • Language of Love • Plight of the Penguins: Should I Stay or Should I Go Letter from the Editor Hello! Happy New Year, everybody! Wakayama. As far as first visits go, it was pretty jam-packed and educational. It also served to January is in many ways a false start. Besides the nurture the seed of my wanting to live here. I year, one of the few things to begin again are anticipated only one year. school terms. And those aren’t even the start of a new school year! At my university, the month To start your year off right, we have many articles was dedicated to intensive month-long classes, for you to peruse. Newcomer Jappy shares ht and I partook all three Januarys during which I her experience of volunteering with the deaf was enrolled. Chemistry was a review and thus and blind and how language impacts our lives. dull, Buddhism and Yoga at the same time was Rackle advises us on inexpensive transportation enlightening, but by far, my favorite class was options for traveling around and there is also a January Features Cultural Psychology in Japan. It was my first visit review of Nagasaki, just in time to plan before to this fascinating country we live in. the Lantern Festival next month. Scott returns 5 The Cheapskate’s Guide to Japanese Travel with an entertaining take on onsen. Sometime Of the fourteen students in the class, I was the Last Week also returns with its fifth chapter and 7 Language of Love only one that could say anything beyond あり is joined by the first part of a story about one がとうand こんにちは, which proved to make thespian’s darkest deed. -
Research and Development Concerning Superconducting Maglev and Research on Applying Superconducting Maglev Technology to the Conventional Railway System
PERSPECTIVE Research and Development Concerning Superconducting Maglev and Research on Applying Superconducting Maglev Technology to the Conventional Railway System Ken NAGASHIMA Maglev Systems Technology Division RTRI is advancing the fundamental research and development concerning supercon- ducting maglev. The topics of this issue are characteristics of maglev vehicle dynamics, ex- perimental production and evaluation of REBCO high-temperature superconducting coils. RTRI is also promoting the applied research based on maglev technology to the conventional railway system. The topics of this issue are the LIM-type eddy-current rail brakes and the fly- wheel energy storage system. Keywords: levitation railway, superconducting linear, conventional railway, superconduct- ing magnet, ground coil 1. Introduction The groundbreaking idea of levitating and guiding ve- hicles using onboard superconducting magnets, the basic Superconducting coil principles for the current superconducting magnetically levitated transportation system, was originally proposed Vehicle cross section by Dr. J. R. Powell and Dr. G. R. Danby of Brookhaven Na- Levitation force Levitation force tional Laboratory in the U.S. This idea was officially jointly X ・ X ・ presented by Dr. Powell and Dr. Danby in 1966 at a gath- Levitation height (15 cm or more) ering of the American Society of Mechanical Engineers, ・ X ・ X Guidance coil in their presentation“ High-Speed Transport by Magneti- Ground surface cally Suspended Trains”[1]. The year 2016 is therefore a Levitation coil 2.4 m 0.6 m special year because it marks the 50th anniversary of this announcement. This paper discusses the original proposal Fig. 1 Basic concepts for Powell-Danby proposal by Dr. Powell and Dr. Danby, recent developments and the current status of maglev train development with a view to tion (EDS = Electro Dynamic Suspension System); and (3) using the technology in practice. -
Presentation of Strategies for Railway Systems Business
Presentation of Strategies for Railway Systems Business Stra teg ies for RRilailway Sys tems BiBusiness -- Accelerate Globalization with Technologies Developed in Japan -- Gaku Suzuki President & CEO, Industrial & Social Infrastructure Systems Company Vice President and Executive Officer, Hitachi, Ltd. March 29, 2010 © Hitachi, Ltd. 2010. All rights reserved. Strategies for Railway Systems Business Accelerate Globalization with Technologies Developed in Japan 1O1. Overvi ew 2.. Strategies 3. Domestic Business 4. Overseas Business 5. Conclusion © Hitachi, Ltd. 2010. All rights reserved. 1. Overview Railway Systems Business in Hitachi SEGMENT INFORMATION Financial Service (millions of yen) Revenues ¥412,040 Operating Income ¥10,210 Information & Telecommunication Systems Logistics, Services & Others Revenues ¥2,594,450 Revenues ¥1, 089, 971 Operating Income ¥176,629 Operating Income ¥23,063 Year ended March 31, 2009 High Functional Materials Consolidated Revenues Electronic Devices & Components ¥10,000.3 billion Revenues ¥1,151,066 Revenues ¥1,556,886 Operating Income ¥27,322 Operating Income ¥27, 777 Digital Media & Consumer Products Power & Industrial Systems Revenues ¥1,261,501 Revenues ¥3,310,544 Operating Loss ¥(105,563) Operating Income ¥24,245 Industrial & Social Infrastructure Systems Company Information & Control Systems Company (Transportation Systems Div.) (Transportation Information Systems Div.) Rolling Stock Systems: rolling stock, electrical component, Transport Management & Control Systems: overseas rolling stock maintenance services Seat reservation system Transport Management & Control Systems: Signali ng /Tra in con tro l sys tem, tra ffic /power management sys tem Railway operation information system power supply system 鉄道システムRailway systems: 1,459億円 ¥149.0 billion* IC card ticketing system *:Unconsolidated: ¥145.9 B Railway systems: ¥27.7 billion Total Railway Sy ystems Integrator Total railway systems revenue: ¥176.7 billion (Year ended March 31, 2009) © Hitachi, Ltd. -
Venues Port Island Campus, Kobe Gakuin University Hyogo University of Health Sciences Design and Creative Center
Guide for the Venue 1. Staff Room and Registration Desk C: Hyogo University of Health Sciences Area Hyogo University of Health Sciences (see page 7) (1) Staff Room 1-3-6 Minatojima, Chuo-ku, Kobe A: Kobe Gakuin University Area <General Assembly, Special Lectures, Symposia, Kobe Gakuin University Building B 2F B205, International Symposium for Medicinal Sciences> 206 (see page 6) Room Q: P Wing 2F Octa Hall (2) Registration Desk <Symposia, Oral Presentations, Luncheon Seminars> A: Kobe Gakuin University Area Room R–U: Mt.-Wing 2F M201–204 Registration Desk 1 (see page 6) Room V–X: Mt.-Wing 1F M112–114 Kobe Gakuin University Building B 2F Lounge B: Kobe Sambo Hall Area D: Design and Creative Center Kobe Area Registration Desk 2 (see page 8) Design and Creative Center Kobe (see page 8) Kobe Sambo Hall 1F Exhibition Hall 1-4 Onohama-cho, Chuo-ku, Kobe (3) Information Desk Tel: 078-325-2201 C: Hyogo University of Health Sciences Area <Poster> Information Desk 1 (see page 7) Room PB: 1F KIITO Hall Hyogo University of Health Sciences Mt.-Wing 1F Entrance 3. Area Map D: Design and Creative Center Kobe Area Information Desk 2 (see page 8) See pages 2 - 4 Design and Creative Center Kobe 1F KIITO Hall 4. Opening time 2. Venue Opening time of each area is as follows. Please note A: Kobe Gakuin University Area that the buildings will not be open until the time Kobe Gakuin University (see page 6) indicated below. 1-1-3 Minatojima, Chuo-ku, Kobe <Plenary Lecture, Special Lectures, Award Lectures, A: Kobe Gakuin University Area Symposia, Oral Presentations, Luncheon Seminars> 8:00 AM Room A–B: Building B 3F B301–302 B: Kobe Sambo Hall Area Room C–I: Building B 2F B211–217 8:00 AM Room J–L: Building B 2F B201–203 C: Hyogo University of Health Sciences Area Room M–P: Building B 1F B103–106 8:00 AM D: Design and Creative Center Kobe Area B: Kobe Sambo Hall Area 8:00 AM Kobe Sambo Hall (see page 8) 5-1-32 Hamabe-dori, Chuo-ku, Kobe 5.