The Falcon 1 Launch Vehicle: Demonstration Flights, Status, Manifest, and Upgrade Path
Total Page:16
File Type:pdf, Size:1020Kb
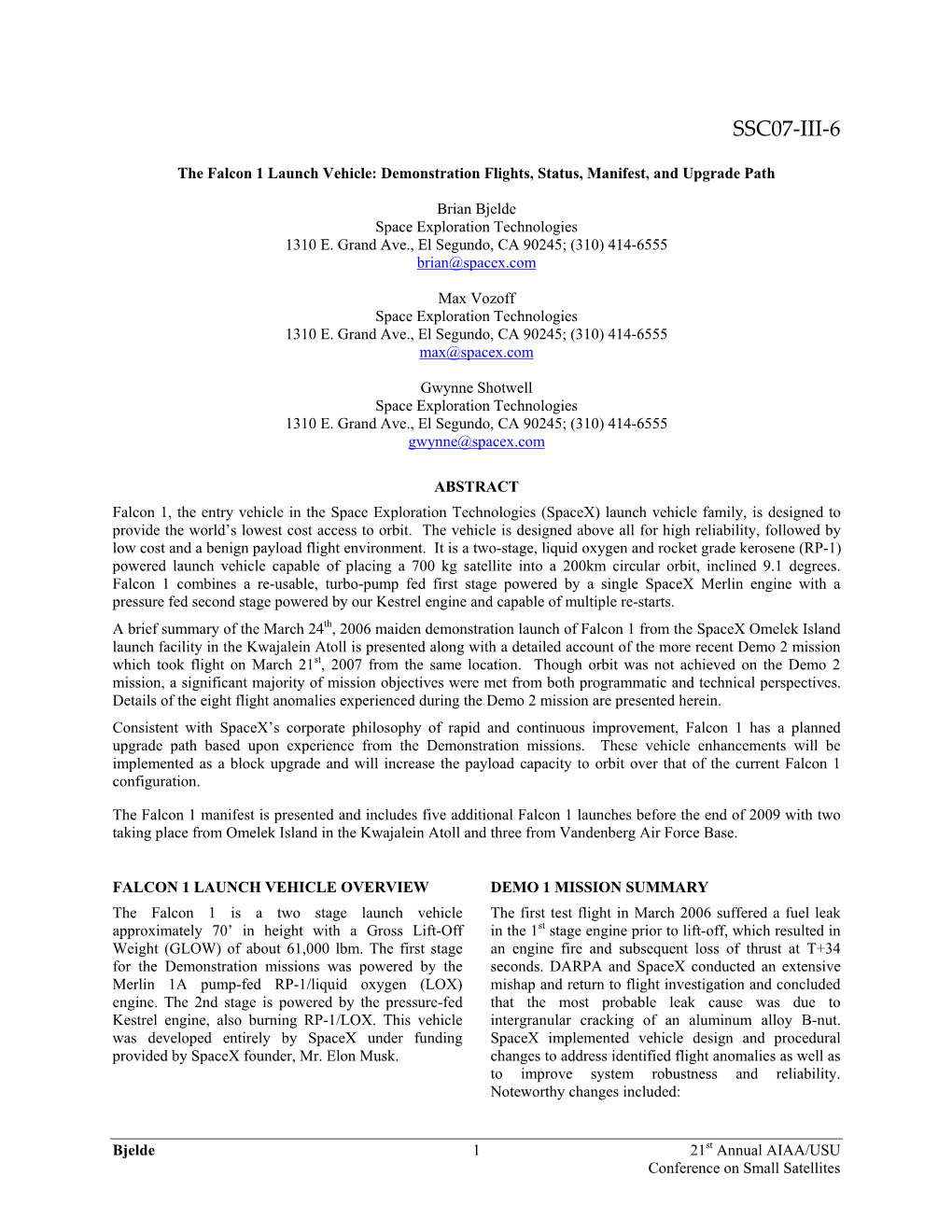
Load more
Recommended publications
-
Validation of Wind Tunnel Test and Cfd Techniques for Retro-Propulsion (Retpro): Overview on a Project Within the Future Launchers Preparatory Programme (Flpp)
VALIDATION OF WIND TUNNEL TEST AND CFD TECHNIQUES FOR RETRO-PROPULSION (RETPRO): OVERVIEW ON A PROJECT WITHIN THE FUTURE LAUNCHERS PREPARATORY PROGRAMME (FLPP) D. Kirchheck, A. Marwege, J. Klevanski, J. Riehmer, A. Gulhan¨ German Aerospace Center (DLR) Supersonic and Hypersonic Technologies Department Cologne, Germany S. Karl O. Gloth German Aerospace Center (DLR) enGits GmbH Spacecraft Department Todtnau, Germany Gottingen,¨ Germany ABSTRACT and landing (VTVL) spacecraft, assisted by retro-propulsion. Up to now, in Europe, knowledge and expertise in that field, The RETPRO project is a 2-years activity, led by the Ger- though constantly growing, is still limited. Systematic stud- man Aerospace Center (DLR) in the frame of ESA’s Future ies were conducted to compare concepts for possible future Launchers Preparatory Program (FLPP), to close the gap of European launchers [2, 3], and activities on detailed inves- knowledge on aerodynamics and aero-thermodynamics of tigations of system components of VTVL re-usable launch retro-propulsion assisted landings for future concepts in Eu- vehicles (RLV) recently started in the RETALT project [4, 5]. rope. The paper gives an overview on the goals, strategy, and Nevertheless, validated knowledge on the aerodynamic current status of the project, aiming for the validation of inno- and aerothermal characteristics of such vehicles is still lim- vative WTT and CFD tools for retro-propulsion applications. ited to a small amount of experimental and numerical inves- Index Terms— RETPRO, retro-propulsion, launcher tigations mostly on lower altitude VTVL trajectories, e. g. aero-thermodynamics, wind tunnel testing, CFD validation within the CALLISTO project [6, 7, 8]. Other studies were conducted to analyze the aerothermodynamics of a simplified generic Falcon 9 geometry during its re-entry and landing 1. -
Spacex Launch Manifest - a List of Upcoming Missions 25 Spacex Facilities 27 Dragon Overview 29 Falcon 9 Overview 31 45Th Space Wing Fact Sheet
COTS 2 Mission Press Kit SpaceX/NASA Launch and Mission to Space Station CONTENTS 3 Mission Highlights 4 Mission Overview 6 Dragon Recovery Operations 7 Mission Objectives 9 Mission Timeline 11 Dragon Cargo Manifest 13 NASA Slides – Mission Profile, Rendezvous, Maneuvers, Re-Entry and Recovery 15 Overview of the International Space Station 17 Overview of NASA’s COTS Program 19 SpaceX Company Overview 21 SpaceX Leadership – Musk & Shotwell Bios 23 SpaceX Launch Manifest - A list of upcoming missions 25 SpaceX Facilities 27 Dragon Overview 29 Falcon 9 Overview 31 45th Space Wing Fact Sheet HIGH-RESOLUTION PHOTOS AND VIDEO SpaceX will post photos and video throughout the mission. High-Resolution photographs can be downloaded from: http://spacexlaunch.zenfolio.com Broadcast quality video can be downloaded from: https://vimeo.com/spacexlaunch/videos MORE RESOURCES ON THE WEB Mission updates will be posted to: For NASA coverage, visit: www.SpaceX.com http://www.nasa.gov/spacex www.twitter.com/elonmusk http://www.nasa.gov/nasatv www.twitter.com/spacex http://www.nasa.gov/station www.facebook.com/spacex www.youtube.com/spacex 1 WEBCAST INFORMATION The launch will be webcast live, with commentary from SpaceX corporate headquarters in Hawthorne, CA, at www.spacex.com. The webcast will begin approximately 40 minutes before launch. SpaceX hosts will provide information specific to the flight, an overview of the Falcon 9 rocket and Dragon spacecraft, and commentary on the launch and flight sequences. It will end when the Dragon spacecraft separates -
Reusable Launch Vehicle Technology Program{
Acta Astronautica Vol. 41, No. 11, pp. 777±790, 1997 # 1998 Published by Elsevier Science Ltd. All rights reserved Printed in Great Britain PII: S0094-5765(97)00197-5 0094-5765/98 $19.00 + 0.00 REUSABLE LAUNCH VEHICLE TECHNOLOGY PROGRAM{ DELMA C. FREEMAN{ JR. and THEODORE A. TALAY} NASA Langley Research Center, Hampton, Virginia 23681-0001, USA R. EUGENE AUSTIN} NASA Marshall Space Flight Center, Marshall Space Flight Center, Alabama 35812-1000, USA (Received 25 April 1997) AbstractÐIndustry/NASA reusable launch vehicle (RLV) technology program eorts are underway to design, test, and develop technologies and concepts for viable commercial launch systems that also satisfy national needs at acceptable recurring costs. Signi®cant progress has been made in understanding the technical challenges of fully reusable launch systems and the accompanying management and oper- ational approaches for achieving a low-cost program. This paper reviews the current status of the RLV technology program including the DC-XA, X-33 and X-34 ¯ight systems and associated technology programs. It addresses the speci®c technologies being tested that address the technical and operability challenges of reusable launch systems including reusable cryogenic propellant tanks, composite structures, thermal protection systems, improved propul- sion, and subsystem operability enhancements. The recently concluded DC-XA test program demon- strated some of these technologies in ground and ¯ight tests. Contracts were awarded recently for both the X-33 and X-34 ¯ight demonstrator systems. The Orbital Sciences Corporation X-34 ¯ight test ve- hicle will demonstrate an air-launched reusable vehicle capable of ¯ight to speeds of Mach 8. -
IAC-17-D2.4.3 Page 1 of 18 IAC-17
68th International Astronautical Congress (IAC), Adelaide, Australia, 25-29 September 2017. Copyright ©2017 by DLR-SART. Published by the IAF, with permission and released to the IAF to publish in all forms. IAC-17- D2.4.3 Evaluation of Future Ariane Reusable VTOL Booster stages Etienne Dumonta*, Sven Stapperta, Tobias Eckerb, Jascha Wilkena, Sebastian Karlb, Sven Krummena, Martin Sippela a Department of Space Launcher Systems Analysis (SART), Institute of Space Systems, German Aerospace Center (DLR), Robert Hooke Straße 7, 28359 Bremen, Germany b Department of Spacecraft, Institute of Aerodynamics and Flow Technology, German Aerospace Center (DLR), Bunsenstraße 10, 37073 Gottingen, Germany *[email protected] Abstract Reusability is anticipated to strongly impact the launch service market if sufficient reliability and low refurbishment costs can be achieved. DLR is performing an extensive study on return methods for a reusable booster stage for a future launch vehicle. The present study focuses on the vertical take-off and vertical landing (VTOL) method. First, a restitution of a flight of Falcon 9 is presented in order to assess the accuracy of the tools used. Then, the preliminary designs of different variants of a future Ariane launch vehicle with a reusable VTOL booster stage are described. The proposed launch vehicle is capable of launching a seven ton satellite into a geostationary transfer orbit (GTO) from the European spaceport in Kourou. Different stagings and propellants (LOx/LH2, LOx/LCH4, LOx/LC3H8, subcooled LOx/LCH4) are considered, evaluated and compared. First sizing of a broad range of launcher versions are based on structural index derived from existing stages. -
Commercial Space Transportation Developments and Concepts: Vehicles, Technologies and Spaceports
Commercial Space Transportation 2006 Commercial Space Transportation Developments and Concepts: Vehicles, Technologies and Spaceports January 2006 HQ003606.INDD 2006 U.S. Commercial Space Transportation Developments and Concepts About FAA/AST About the Office of Commercial Space Transportation The Federal Aviation Administration’s Office of Commercial Space Transportation (FAA/AST) licenses and regulates U.S. commercial space launch and reentry activity, as well as the operation of non-federal launch and reentry sites, as authorized by Executive Order 12465 and Title 49 United States Code, Subtitle IX, Chapter 701 (formerly the Commercial Space Launch Act). FAA/AST’s mission is to ensure public health and safety and the safety of property while protecting the national security and foreign policy interests of the United States during commercial launch and reentry operations. In addition, FAA/AST is directed to encour- age, facilitate, and promote commercial space launches and reentries. Additional information concerning commercial space transportation can be found on FAA/AST’s web site at http://ast.faa.gov. Federal Aviation Administration Office of Commercial Space Transportation i About FAA/AST 2006 U.S. Commercial Space Transportation Developments and Concepts NOTICE Use of trade names or names of manufacturers in this document does not constitute an official endorsement of such products or manufacturers, either expressed or implied, by the Federal Aviation Administration. ii Federal Aviation Administration Office of Commercial Space Transportation 2006 U.S. Commercial Space Transportation Developments and Concepts Contents Table of Contents Introduction . .1 Significant 2005 Events . .4 Space Competitions . .6 Expendable Launch Vehicles . .9 Current Expendable Launch Vehicle Systems . .9 Atlas 5 - Lockheed Martin Corporation . -
A Review of Current Research in Subscale Flight Testing and Analysis of Its Main Practical Challenges
aerospace Article A Review of Current Research in Subscale Flight Testing and Analysis of Its Main Practical Challenges Alejandro Sobron * , David Lundström and Petter Krus Department of Management and Engineering, Division of Fluid and Mechatronic Systems, Linköping University, SE-58183 Linköping, Sweden; [email protected] (D.L.); [email protected] (P.K.) * Correspondence: [email protected]; Tel.: +46-1328-1893 Abstract: Testing of untethered subscale models, often referred to as subscale flight testing, has traditionally had a relatively minor, yet relevant use in aeronautical research and development. As recent advances in electronics, rapid prototyping and unmanned-vehicle technologies expand its capabilities and lower its cost, this experimental method is seeing growing interest across academia and the industry. However, subscale models cannot meet all similarity conditions required for simulating full-scale flight. This leads to a variety of approaches to scaling and to other alternative applications. Through a literature review and analysis of different scaling strategies, this study presents an overall picture of how subscale flight testing has been used in recent years and synthesises its main issues and practical limitations. Results show that, while the estimation of full-scale characteristics is still an interesting application within certain flight conditions, subscale models are progressively taking a broader role as low-cost technology-testing platforms with relaxed similarity constraints. Different approaches to tackle the identified practical challenges, implemented both by the authors and by other organisations, are discussed and evaluated through flight experiments. Citation: Sobron, A.; Lundström, D.; Keywords: subscale flight testing; similarity; scale model; remotely piloted aircraft; demonstration; Krus, P. -
+ Part 10: Test and Evaluation
10. Test and Evaluation 10.1 Approach Architecture Design, Development, Test, and Evaluation (DDT&E) schedule, costs, and risk are highly dependent on the integrated test and evaluation approach for each of the major elements. As a part of the Exploration Systems Architecture Study (ESAS), a top-level test and evaluation plan, including individual flight test objectives, was developed and is summarized in this section. The test and evaluation plan described here is derived from the Apollo Flight Test Program of the 1960s. A more detailed test and evaluation plan will be based on detailed verification requirements and objectives documented in specifications and verification plans. In order to support schedule, cost, and risk assessments for the reference ESAS architecture, an integrated test and evaluation plan was developed to identify the number and type of major test articles (flight and ground) and the timing and objectives of each major flight test, including facilities and equipment required to support those tests. This initial plan is based on the Apollo Program and the ESAS Ground Rules and Assumptions (GR&As)—including the human- rating requirements from NASA Procedural Requirements (NPR) 8705.2A, Human-Rating Requirements for Space Systems. 10. Test and Evaluation 645 10.2 Ground Rules and Assumptions ESAS GR&As establish the initial set of key constraints to testing. Although all ESAS GR&As are considered, the specific ones listed below are particularly significant, as they deal with schedule and testing/qualification assumptions. • The crew launch system shall facilitate crew survival using abort and escape. There will be three all-up tests of the Launch Abort System (LAS). -
6. Chemical-Nuclear Propulsion MAE 342 2016
2/12/20 Chemical/Nuclear Propulsion Space System Design, MAE 342, Princeton University Robert Stengel • Thermal rockets • Performance parameters • Propellants and propellant storage Copyright 2016 by Robert Stengel. All rights reserved. For educational use only. http://www.princeton.edu/~stengel/MAE342.html 1 1 Chemical (Thermal) Rockets • Liquid/Gas Propellant –Monopropellant • Cold gas • Catalytic decomposition –Bipropellant • Separate oxidizer and fuel • Hypergolic (spontaneous) • Solid Propellant ignition –Mixed oxidizer and fuel • External ignition –External ignition • Storage –Burn to completion – Ambient temperature and pressure • Hybrid Propellant – Cryogenic –Liquid oxidizer, solid fuel – Pressurized tank –Throttlable –Throttlable –Start/stop cycling –Start/stop cycling 2 2 1 2/12/20 Cold Gas Thruster (used with inert gas) Moog Divert/Attitude Thruster and Valve 3 3 Monopropellant Hydrazine Thruster Aerojet Rocketdyne • Catalytic decomposition produces thrust • Reliable • Low performance • Toxic 4 4 2 2/12/20 Bi-Propellant Rocket Motor Thrust / Motor Weight ~ 70:1 5 5 Hypergolic, Storable Liquid- Propellant Thruster Titan 2 • Spontaneous combustion • Reliable • Corrosive, toxic 6 6 3 2/12/20 Pressure-Fed and Turbopump Engine Cycles Pressure-Fed Gas-Generator Rocket Rocket Cycle Cycle, with Nozzle Cooling 7 7 Staged Combustion Engine Cycles Staged Combustion Full-Flow Staged Rocket Cycle Combustion Rocket Cycle 8 8 4 2/12/20 German V-2 Rocket Motor, Fuel Injectors, and Turbopump 9 9 Combustion Chamber Injectors 10 10 5 2/12/20 -
Since Our Last SIA Member News Summary, Press Releases and Posts
SIA PRESIDENT’S REPORT – MEMBER NEWS FOR OCT 2020 Since our last SIA Member News Summary, press releases and posts from many SIA Members including AGI, Blue Origin, Hawkeye 360, Inmarsat, Integrasys, Iridium, Kymeta, Lockheed Martin, OneWeb, Planet, SES, SpaceX, Spire, Telesat and XTAR have released news. Please see the summary of stories and postings below and click on the COMPANY LINK for more details. PLANET (above) On Oct 28th, Planet announced the successful launch of nine Flock 4e latest-generation SuperDove satellites onboard a Rocket Lab Electron rocket from New Zealand. The Flock 4e’ SuperDoves were deployed into an approximately 500 km, morning-crossing Sun Synchronous Orbit (SSO), joining the rest of the constellation providing medium-resolution Earth imagery with unprecedented coverage and frequency of update. The nine SuperDoves are equipped with 8 spectral bands that provide high image quality and accurate surface reflectance values for advanced algorithms and time-series analysis. Planet’s SuperDoves are also interoperable with publicly available imagery, like Copernicus’ Sentinel-2, enabling innovative applications and use cases. (Photo credit: Image courtesy of Planet and Rocket Lab) AGI On Oct 26th, Analytical Graphics Inc., (AGI) announced that AGI and Ansys, a leading innovator of engineering software, had entered into a definitive acquisition agreement. According to the terms of the agreement, Ansys would acquire AGI. The purchase price for the transaction, which is expected to close in Q4 of 2020 pending regulatory clearance, is $700 million. SPACEX On Oct 24th, SpaceX announced that a Falcon 9 rocket had launched 60 Starlink satellites to orbit from Space Launch Complex 40 (SLC-40) at Cape Canaveral Air Force Station in Florida. -
Forecast of Upcoming Anniversaries -- September 2018
FORECAST OF UPCOMING ANNIVERSARIES -- SEPTEMBER 2018 60 Years Ago - 1958 September 17: NASA-ARPA Manned Satellite Panel established. The NASA/Advanced Research Projects Agency Manned Satellite Panel was formed to draft plans for future manned spaceflight. Langley Research Center and Glenn (then Lewis) Research Center were the primary NASA centers involved. September 30: Last day of NACA operations, Washington, D.C. 55 Years Ago - 1963 September 18: Asset 1 launched to an altitude of 39 miles aboard a Thor rocket from Cape Canaveral, Fla. The first successful suborbital lifting body flight, the Asset vehicle served as a proof-of-concept for the idea of a reusable winged spacecraft. September 28: Transit V-B launched by Thor Ablestar at 12:09 p.m. PDT, from Vandenberg AFB. This Transit satellite was the first US satellite to be powered entirely by nuclear electric power (RTGs). 50 Years Ago - 1968 September 5: Zond 5 launched from Baikonur by Proton K, at 21:36 UTC. An unmanned precursor for Soviet circumlunar cosmonaut program, it was the first Soviet circumlunar flight to successfully reenter Earth’s atmosphere. 45 Years Ago – 1973 September 25: Skylab 2, with astronauts Bean, Garriott, and Lousma, splashes down in Pacific Ocean. Crew was retrieved by recovery ship USS New Orleans, 6:20 p.m., EDT. September 26: Concorde 02 flew from Orly Field, Paris France, to Dulles International Airport, Washington, DC, in 3 hours and 33 minutes. The flight was a new speed record for the route. September 27: Soyuz 12 launched aboard a Soyuz rocket from Baikonur at 12:18 UTC. -
Flight Engineer Knowledge Test Guide
AC 63-1 FLIGHT ENGINEER KNOWLEDGE TEST GUIDE U.S. Department of Transportation Federal Aviation Administration 1 FLIGHT ENGINEER KNOWLEDGE TEST GUIDE 1995 U.S. DEPARTMENT OF TRANSPORTATION FEDERAL AVIATION ADMINISTRATION Flight Standards Service 2 PREFACE The Flight Standards Service of the Federal Aviation Administration (FAA) has developed this guide to help applicants meet the knowledge requirements for the computer administered tests for flight engineer turbojet, turboprop, and reciprocating class certification. This guide contains information about the knowledge test eligibility requirements, test descriptions, testing and retesting procedures, and sample test questions with answers. As a convenience to the applicant, the eligibility requirements for the oral and flight tests are included. Appendix 1 provides a list of reference materials and subject matter knowledge codes, and computer testing designees. Changes to the subject matter knowledge code list will be published as a separate advisory circular. The sample questions and answers in this guide are predicated on Federal Aviation Regulations (FAR's) and references that were current at the time of publication. Questions and answers in the computer administered knowledge tests are updated when changes are made to these reference materials. The flight engineer test question bank and subject matter knowledge code list for all airmen certificates and ratings, with changes, may be obtained by computer access from FedWorld at (703) 321-3339. This bulletin board service is provided by the U.S. Department of Commerce, 24 hours a day, 7 days per week. For technical assistance regarding computer requirements for this service, contact the FedWorld help desk at (703) 487-4608 from 7:30 a.m. -
Falcon 1 User's Guide
Falcon 1 Launch Vehicle Payload User’s Guide Rev 7 TABLE OF CONTENTS 1. Introduction 4 1.1. Revision History 4 1.2. Purpose 6 1.3. Company Description 6 1.4. Falcon Program Overview 6 1.5. Mission Management 7 2. Falcon 1 Launch Vehicles 8 2.1. Overview 8 2.1.1. Falcon 1 9 2.1.2. Falcon 1e 11 2.2. Availability 12 2.3. Reliability 13 2.4. Performance 15 2.5. Pricing 16 2.6. Standard Services 16 2.7. Non‐standard Services 16 2.8. Vehicle Axes/Attitude Definitions 17 3. Requirements & Environments 18 3.1. Mass Properties 18 3.2. Payload Interfaces 19 3.2.1. Falcon Payload Attach Fittings 19 3.2.2. Test Fittings and Fitcheck Policy 19 3.2.3. Electrical Design Criteria 19 3.3. Documentation Requirements 21 3.4. Payload Environments 23 3.4.1. Transportation Environments 23 3.4.2. Humidity, Cleanliness and Thermal Control 23 3.4.3. Payload Air Conditioning 24 3.4.4. Launch and Flight Environments 24 4. Facilities 32 4.1. Headquarters – Hawthorne, California 32 4.2. Washington, DC 32 4.3. Test Facility ‐ Central Texas 32 4.4. Launch Site – Kwajalein Atoll 33 4.4.1. Processing Services and Equipment 33 5. Launch Operations 36 5.1. Launch Control Organization 36 5.2. Mission Integration 37 5.2.1. Payload Transport to Launch Site 38 5.2.2. Payload Integration 38 5.2.3. Example Flight Profiles 41 D000973 Rev Falcon 1 User’s Guide ‐ D000973 Rev. 7 Page | 3 6.