Analytical Study on Compound Planetary Gear Dynamics
Total Page:16
File Type:pdf, Size:1020Kb
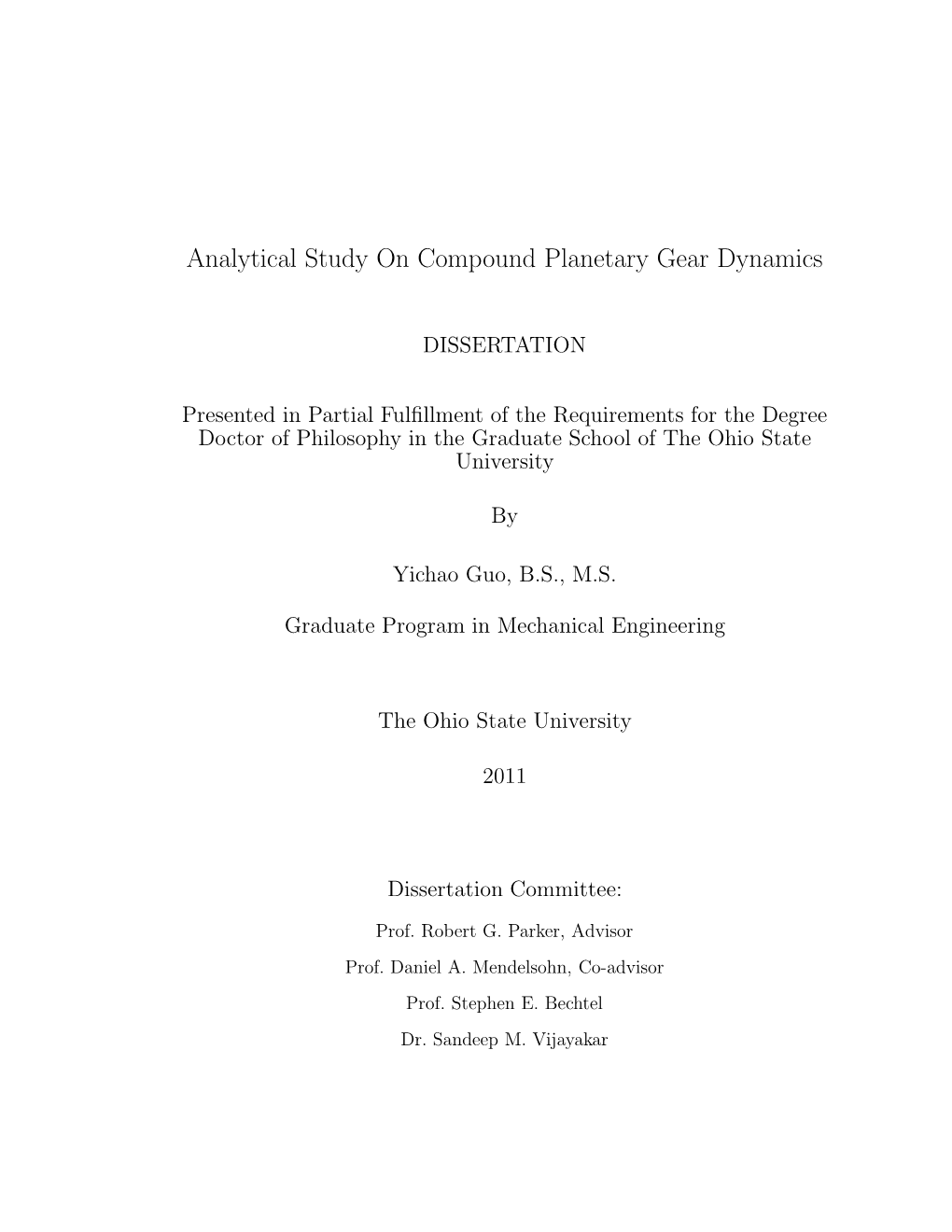
Load more
Recommended publications
-
Unit for a Power Split Continuously Variable Transmission
(19) & (11) EP 2 322 823 A1 (12) EUROPEAN PATENT APPLICATION (43) Date of publication: (51) Int Cl.: 18.05.2011 Bulletin 2011/20 F16H 37/08 (2006.01) (21) Application number: 11155260.0 (22) Date of filing: 03.09.2008 (84) Designated Contracting States: • Winter, Philip Duncan AT BE BG CH CY CZ DE DK EE ES FI FR GB GR Blackburn, Lancashire BB2 7FA (GB) HR HU IE IS IT LI LT LU LV MC MT NL NO PL PT • Burt, David RO SE SI SK TR Chorley, Lancashire PR7 5UJ (GB) (30) Priority: 04.09.2007 GB 0717143 (74) Representative: Bartle, Robin Jonathan W.P. Thompson & Co. (62) Document number(s) of the earlier application(s) in Coopers Building accordance with Art. 76 EPC: Church Street 08788747.7 / 2 195 556 Liverpool L1 3AB (GB) (71) Applicant: TOROTRAK (DEVELOPMENT) LTD. Leyland, Lancashire PR26 7UX (GB) Remarks: This application was filed on 21-02-2011 as a (72) Inventors: divisional application to the application mentioned • Greenwood, Christopher John under INID code 62. Preston, Lancashire PR5 3WS (GB) (54) Unit for a power split continuously variable transmission (57) The invention is concerned with a continuously output member. An arrangement of clutches is provided variable transmission incorporating a variator of the type for selectively engaging any of at least three regimes. In having at least two co- axial races (D1- D4) between which one regime the recirculater output member drives the drive is transferred at a continuously variable variator ra- transmission output. In another the layshaft drives the tio. The variator races are mounted for rotation about a transmission output. -
Download Full-Text
Journal of Mechanical Engineering and Automation 2020, 9(1): 1-8 DOI: 10.5923/j.jmea.20200901.01 Verification of the Dynamic Characteristics of an Epicyclic Gear Train Using Epicyclic Gear Train and Torque Apparatus Mauton Gbededo1,2,*, Chukwuemeke Onyenefa2, Matthew Arowolo1 1Department of Mechatronics Engineering, Federal University, Oye-Ekiti, Nigeria 2Department of Mechanical & Biomedical Engineering, Bells University of Technology, Ota, Nigeria Abstract An epicyclic gear train consists of two gears, mounted so that the center of one gear revolved around the center of the other. A carrier connects the centers of the two gears and it rotates to carry one gear, called the planet gear or planet pinion, around the other, called the sun gear or sun wheel. The planet and sun gears were meshed so that their pitch circles rolled without slipping. A point on the pitch circle of the planet gear traced an epicycloid curve. This paper deals with analysis and verification of dynamic characteristics of an epicyclic gear train using the gear train and torque apparatus. The apparatus was installed in the Engineering lab while taking adequate safety precautions to ensure accurate collection of data. A record of the input, holding and output at various speed of the gear system were taken. At the end of the experiment, gear ratio, speed ratio and torque relationship of the epicyclic gear train were obtained. The experimental results were compared to the analytical data from various calculations using respective governing equations. It was observed that the experimental results were similar to the analytical data obtained for the speed ratio and torque relationship with a maximum 1.11% deviation between the two methods for torque relationship and 1.6% for the speed ratios, which were due to some frictional and mechanical losses in the belt and gear system. -
1700 Animated Linkages
Nguyen Duc Thang 1700 ANIMATED MECHANICAL MECHANISMS With Images, Brief explanations and Youtube links. Part 1 Transmission of continuous rotation Renewed on 31 December 2014 1 This document is divided into 3 parts. Part 1: Transmission of continuous rotation Part 2: Other kinds of motion transmission Part 3: Mechanisms of specific purposes Autodesk Inventor is used to create all videos in this document. They are available on Youtube channel “thang010146”. To bring as many as possible existing mechanical mechanisms into this document is author’s desire. However it is obstructed by author’s ability and Inventor’s capacity. Therefore from this document may be absent such mechanisms that are of complicated structure or include flexible and fluid links. This document is periodically renewed because the video building is continuous as long as possible. The renewed time is shown on the first page. This document may be helpful for people, who - have to deal with mechanical mechanisms everyday - see mechanical mechanisms as a hobby Any criticism or suggestion is highly appreciated with the author’s hope to make this document more useful. Author’s information: Name: Nguyen Duc Thang Birth year: 1946 Birth place: Hue city, Vietnam Residence place: Hanoi, Vietnam Education: - Mechanical engineer, 1969, Hanoi University of Technology, Vietnam - Doctor of Engineering, 1984, Kosice University of Technology, Slovakia Job history: - Designer of small mechanical engineering enterprises in Hanoi. - Retirement in 2002. Contact Email: [email protected] 2 Table of Contents 1. Continuous rotation transmission .................................................................................4 1.1. Couplings ....................................................................................................................4 1.2. Clutches ....................................................................................................................13 1.2.1. Two way clutches...............................................................................................13 1.2.1. -
Novel Designs and Geometry for Mechanical Gearing
Novel Designs and Geometry for Mechanical Gearing by Erasmo Chiappetta School of Engineering, Computing and Mathematics Oxford Brookes University In collaboration with Norbar Torque Tools ltd., UK. A thesis submitted in partial fulfilment of the requirements of Oxford Brookes University for the degree of Doctor of Philosophy September 2018 Abstract This thesis presents quasi-static Finite Element Methods for the analysis of the stress state occurring in a pair of loaded spur gears and aims to further research the effect of tooth profile modifications on the mechanical performance of a mating gear pair. The investigation is then extended to epicyclic transmissions as they are considered the most viable solution when the transmission of high torque level within a compact volume is required. Since, for the current study, only low speed conditions are considered, dynamic loads do not play a crucial role. Vibrations and the resulting noise might be considered negligible and consequently the design process is dictated entirely by the stress state occurring on the mating components. Gear load carrying capacity is limited by maximum contact and bending stress and their correlated failure modes. Consequently, the occurring stress state is the main criteria to characterise the load carrying capacity of a gear system. Contact and bending stresses are evaluated for multiple positions over a mesh cycle of a contacting tooth pair in order to consider the stress fluctuation as consequence of the alternation of single and double pairs of teeth in contact. The influence of gear geometrical proportions on mechanical properties of gears in mesh is studied thoroughly by means of the definition of a domain of feasible combination of geometrical parameters in order to deconstruct the well-established gear design process based on rating standards and base the defined gear geometry on operational and manufacturing constraints only. -
Basic Fundamentals of Gear Drives
Basic Fundamentals of Gear Drives Course No: M06-031 Credit: 6 PDH A. Bhatia Continuing Education and Development, Inc. 22 Stonewall Court Woodcliff Lake, NJ 07677 P: (877) 322-5800 [email protected] BASIC FUNDAMENTALS OF GEAR DRIVES A gear is a toothed wheel that engages another toothed mechanism to change speed or the direction of transmitted motion. Gears are generally used for one of four different reasons: 1. To increase or decrease the speed of rotation; 2. To change the amount of force or torque; 3. To move rotational motion to a different axis (i.e. parallel, right angles, rotating, linear etc.); and 4. To reverse the direction of rotation. Gears are compact, positive-engagement, power transmission elements capable of changing the amount of force or torque. Sports cars go fast (have speed) but cannot pull any weight. Big trucks can pull heavy loads (have power) but cannot go fast. Gears cause this. Gears are generally selected and manufactured using standards established by American Gear Manufacturers Association (AGMA) and American National Standards Institute (ANSI). This course provides an outline of gear fundamentals and is beneficial to readers who want to acquire knowledge about mechanics of gears. The course is divided into 6 sections: Section -1 Gear Types, Characteristics and Applications Section -2 Gears Fundamentals Section -3 Power Transmission Fundamentals Section -4 Gear Trains Section -5 Gear Failure and Reliability Analysis Section -6 How to Specify and Select Gear Drives SECTION -1 GEAR TYPES, CHARACTERISTICS & APPLICATIONS The gears can be classified according to: 1. the position of shaft axes 2. -
EPICYCLIC GEARING and the ANTIKYTHERA MECHANISM PART II by M.T
EPICYCLIC GEARING AND THE ANTIKYTHERA MECHANISM PART II by M.T. Wright ART I of this article appeared in March scheme is familiar to students of complicated 2003.26 I withdrew the concluding part dial-work as one adopted where a ratio is desired Pbecause more refi ned data became available. that cannot conveniently be achieved by a I apologize to readers for the long-delayed fi xed-axis train alone, and I suggest that this is completion of the consequent revision. the reason for its introduction here. It is a little The Antikythera Mechanism, dateable startling to fi nd the application in so early an to the first century BC, is by far the oldest instrument, but arguably it is no more so than geared mechanism in the world. I began by the diff erential gear that it ‘supplants’. showing that all earlier attempts to understand We know that one revolution of the input to it were vitiated by the acceptance of mistaken this train represented one tropical month, but arrangements described by Professor Derek Price, the poor state of preservation of the instrument on whose writing most readers’ understanding makes it hard to be sure what output period of the Mechanism is (directly or indirectly) was intended. Th e numbers of teeth in several based. I described how, working from new of the train wheels are uncertain and we cannot observations of the original artefact made by even be sure of the number of arbors on the the late Professor A.G. Bromley and myself, I epicyclic platform, while the remaining part of was able to correct one of Price’s errors and so the lower back dial off ers few direct clues as to to develop a new reconstruction of the dial on the function displayed on it. -
Design Validation of High Speed Ratio Epicyclic Gear Technology in Compression Systems
DESIGN VALIDATION OF HIGH SPEED RATIO EPICYCLIC GEAR TECHNOLOGY IN COMPRESSION SYSTEMS Gaspare Maragioglio Shawn Buckley Engineering Manager Engineering Director Advanced Train Integration Allen Gears GE Oil & Gas Pershore, UK Florence, Italy Shawn Buckley is currently the Engineering Gaspare Maragioglio is currently Engineering Director at Allen Gears (part of GE Oil & Gas) Manager of the Advanced Train Integration based in Pershore, UK joining early 1990. Team for GE Oil & Gas, in Florence, Italy. He Shawn is responsible for leading both the is responsible for technical selection and design verification of flexible original equipment and services engineering design teams producing and rigid couplings, load gears and auxiliary equipment, with bespoke gearboxes for a wide range of applications from power particular focus on the train rotor-dynamic behaviour, torsional and generation to naval marine main propulsion drives, employing lateral. He has a degree in Mechanical Engineering and before parallel shaft, epicyclic and compound epicyclic gearing solutions. joining GE he had a research assignment at University College He is engineering apprentice trained and studied through the open London. He is currently member of API613 Task Force and the ATPS university and is currently a member of the API 677 Task Force. Advisor Committee. Giuseppe Vannini Paul Bradley Principal Engineer Engineering Technical Director Rotor-dynamics Allen Gears GE Oil&Gas Pershore, UK Florence, Italy Paul Bradley is Technical Director at Allen Giuseppe Vannini is Principal Engineer in the Gears and has over 20 years experience Advanced Technology Organization of GE working within the power transmission and Oil&Gas, which he joined in early 2001. -
DNA-Assembled Nanoarchitectures with Multiple Components In
DNA-assembled nanoarchitectures with multiple components in regulated and coordinated motion Pengfei Zhan1#, Maximilian J. Urban1,2#, Steffen Both3, Xiaoyang Duan1,2, Anton Kuzyk4, Thomas Weiss3, and Na Liu1,2,* 1Max Planck Institute for Intelligent Systems, Heisenbergstrasse 3, D-70569 Stuttgart, Germany 2Kirchhoff Institute for Physics, Heidelberg University, Im Neuenheimer Feld 227, D-69120 Heidelberg, Germany 34th Physics Institute and Stuttgart Research Center of Photonic Engineering, University of Stuttgart, 70569 Stuttgart, Germany 4Department of Neuroscience and Biomedical Engineering, Aalto University, School of Science, P.O. Box 12200, FI-00076 Aalto, Finland e-mail: [email protected] Coordinating functional parts to operate in concert is essential for machinery. In gear trains, meshed gears are compactly interlocked, working together to impose rotation or translation. In photosynthetic systems, a variety of biological entities in the thylakoid membrane interact with each other, converting light energy into chemical energy. However, coordinating individual parts to carry out regulated and coordinated motion within an artificial nanoarchitecture poses great challenges, owing to the requisite control on the nanoscale. Here, we demonstrate DNA-directed nanosystems, which comprise hierarchically-assembled DNA origami filaments, fluorophores, and gold nanocrystals. These individual building blocks can execute independent, synchronous, or joint motion upon external inputs. The dynamic processes are in situ optically monitored using fluorescence spectroscopy, taking advantage of the sensitive distance-dependent interactions between the gold nanocrystals and fluorophores positioned on the DNA origami. Our work leverages the complexity of DNA-based artificial nanosystems with tailored dynamic functionality, representing a viable route towards technomimetic nanomachinery. 1 Machines are built with multiple parts, which can work together for a particular function. -
The Design and Fabrication of an Omni-Directional Vehicle Platform
THE DESIGN AND FABRICATION OF AN OMNI-DIRECTIONAL VEHICLE PLATFORM By CHRISTOPHER ROBERT FULMER A THESIS PRESENTED TO THE GRADUATE SCHOOL OF THE UNIVERSITY OF FLORIDA IN PARTIAL FULFILLMENT OF THE REQUIREMENTS FOR THE DEGREE OF MASTER OF SCIENCE UNIVERSITY OF FLORIDA 2003 Copyright 2003 by Christopher Robert Fulmer ACKNOWLEDGMENTS The author would like to thank all of those who made his years at the University of Florida a memorable and interesting experience. In particular the author would like to express his deepest gratitude to Dr. Carl Crane for the dedication he has for his students and the engineering program as a whole. The author would also like to thank Dr. John Zigert and Shannon Ridgway for their guidance and many suggestions throughout the development of this project. Thanks go to all the people of the Center for Intelligent Machines and Robotics for their help and friendship. The author would like to thank his parents, Craig and Patty Fulmer, for their support and encouragement throughout the years. To his fiancee, Cindy, he wishes to extend his most heartfelt love and gratitude for inspiring him to make the most out of this opportunity. iii TABLE OF CONTENTS page ACKNOWLEDGMENTS ................................................................................................. iii LIST OF TABLES............................................................................................................. vi LIST OF FIGURES ......................................................................................................... -
Design Manual for Enclosed Epicyclic Gear Drives
This is a preview of "ANSI/AGMA 6123-B06". Click here to purchase the full version from the ANSI store. ANSI/AGMA 6123-B06 AMERICAN NATIONAL STANDARD Design Manual for Enclosed Epicyclic Gear Drives ANSI/AGMA 6123-B06 This is a preview of "ANSI/AGMA 6123-B06". Click here to purchase the full version from the ANSI store. Design Manual for Enclosed Epicyclic Gear Drives American AGMA 6123--B06 National [Revision of ANSI/AGMA 6023--A88 and ANSI/AGMA 6123--A88] Standard Approval of an American National Standard requires verification by ANSI that the require- ments for due process, consensus, and other criteria for approval have been met by the standards developer. Consensus is established when, in the judgment of the ANSI Board of Standards Review, substantial agreement has been reached by directly and materially affected interests. Substantial agreement means much more than a simple majority, but not necessarily una- nimity. Consensus requires that all views and objections be considered, and that a concerted effort be made toward their resolution. The use of American National Standards is completely voluntary; their existence does not in any respect preclude anyone, whether he has approved the standards or not, from manufacturing, marketing, purchasing, or using products, processes, or procedures not conforming to the standards. The American National Standards Institute does not develop standards and will in no circumstances give an interpretation of any American National Standard. Moreover, no person shall have the right or authority to issue an interpretation of an American National Standard in the name of the American National Standards Institute. -
Method for Propelling a Vehicle As Well As Drive Unit
(19) & (11) EP 1 456 050 B1 (12) EUROPEAN PATENT SPECIFICATION (45) Date of publication and mention (51) Int Cl.: of the grant of the patent: B60K 6/10 (2006.01) F16H 3/72 (2006.01) 08.07.2009 Bulletin 2009/28 B60K 6/365 (2007.10) (21) Application number: 02783858.0 (86) International application number: PCT/NL2002/000803 (22) Date of filing: 06.12.2002 (87) International publication number: WO 2003/047898 (12.06.2003 Gazette 2003/24) (54) Method for propelling a vehicle as well as drive unit Verfahren zum betreiben eines Fahrzeugs und Antriebseinheit Procédé de propulsion de véhicule et unité d’entraînement (84) Designated Contracting States: (74) Representative: Verhees, Godefridus Josephus AT BE BG CH CY CZ DE DK EE ES FI FR GB GR Maria IE IT LI LU MC NL PT SE SI SK TR Brabants Octrooibureau, De Pinckart 54 (30) Priority: 06.12.2001 NL 1019503 5674 CC Nuenen (NL) 09.08.2002 NL 1021241 18.09.2002 NL 1021482 (56) References cited: 29.10.2002 NL 1021776 EP-A- 0 845 618 EP-A- 1 209 017 EP-A2- 1 209 017 WO-A-00/20242 (43) Date of publication of application: DE-A- 10 116 989 FR-A- 2 824 509 15.09.2004 Bulletin 2004/38 US-A- 4 471 668 US-A- 5 577 973 US-A- 5 730 675 (73) Proprietors: • van Druten, Roell Marie • TENBERGE P: "E-AUTOMAT 5612 CR Eindhoven (NL) AUTOMATIKGETRIEBE MIT ESPRIT" VDI • Vroemen, Bas G. BERICHTE, DUESSELDORF, DE, no. 1610, 2001, 5553 BG Valkenswaard (NL) pages 455-479, XP008010754 ISSN: 0083-5560 • Serrarens, Alexander Franciscus Maria • PATENT ABSTRACTS OF JAPAN vol. -
Introduction to Transmission System
INTRODUCTION TO TRANSMISSION SYSTEM :- . TYPES OF TRANSMISSION SYSTEM . CLUTCH . GEAR BOX . PROPEELER SHAFT . UNIVERSAL JOINTS . Final drive and differential . REAR AXLE Definition Of Transmission System :- The mechanism that transmits the power developed by the engine of automobile to the engine to the driving wheels is called the TRANSMISSION SYSTEM (or POWER TRAIN).It is composed of – Clutch The gear box Propeller shaft Universal joints Rear axle Wheel Tyres Requirements Of Transmission System :- Provide means of connection and disconnection of engine with rest of power train without shock and smoothly. Provide a varied leverage between the engine and the drive wheels Provide means to transfer power in opposite direction. Enable power transmission at varied angles and varied lengths. Enable speed reduction between engine and the drive wheels in the ratio of 5:1. Enable diversion of power flow at right angles. Provide means to drive the driving wheels at different speeds when required. Bear the effect of torque reaction , driving thrust and braking effort effectively. The above requirements are fulfilled by the following main units of transmission system :- Clutch Gear Box Transfer Case Propeller Shaft and Universal Joints. Final Drive Differential Torque Tube Road Wheel Difference between tyre and wheel :- Wheel Tyre A wheel is a device that allows While tyre is the outer part of heavy objects to be moved easily the wheel made up with rubber through rotating on an axle and mostly use in vehicles for through its centre, facilitating smooth movement movement or transportation while supporting a load (mass),or performing labor in machine. Types Of Transmission System -: Hydraulic transmission system:- Fluid coupling -: A fluid coupling is a hydrodynamic device used to transmit rotating mechanical power.It has been used in automobile transmissions as an alternative to a mechanical clutch.