“Why Not Period Glue?”
Total Page:16
File Type:pdf, Size:1020Kb
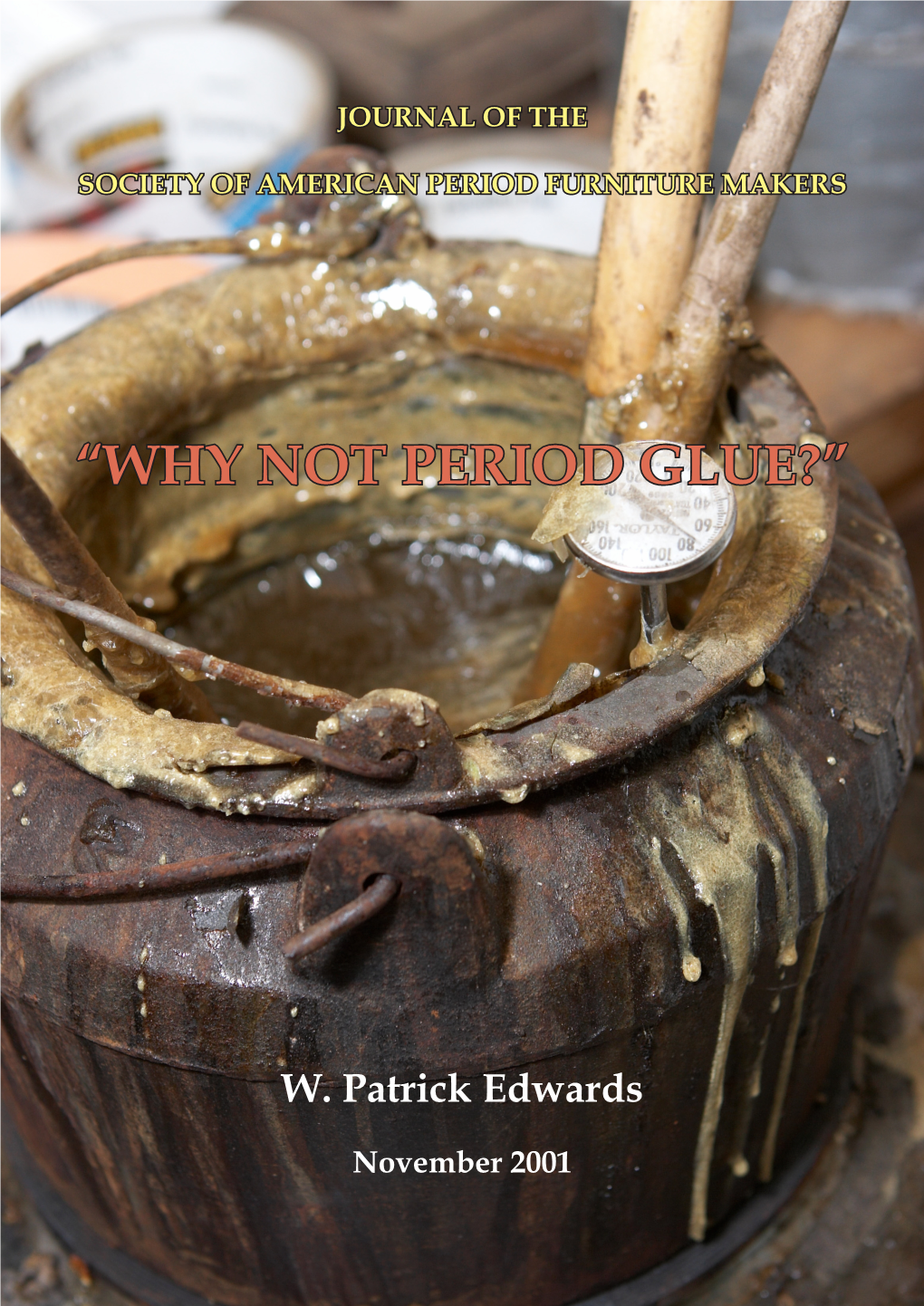
Load more
Recommended publications
-
Medieval Glues Upto 1600 CE Class Notes - SCA Estrella 23 Collegium, Feb 18, 2007 C
Medieval Glues Upto 1600 CE Class Notes - SCA Estrella 23 Collegium, Feb 18, 2007 C. M. Helm-Clark, Ph.D. Overview of Medieval Glues There are many glues which were used in period. Several glues and glue ingredients are as follows: Cheese glue wood natural must be made up and polymer made used immediately, sets up of globular permanently, subject to polypeptide attack by casein protein microorganisms in molecules damp conditions, stronger in thin coats, impervious when cured Hide Glue general all-around glue, natural rehydration undoes the sizing, vellum, paper, polymer made adhesive, stores forever wood, gilding mordant up of strands in the dried state, can ingredient of polypeptide make stronger bonds colloid protein than cheese glue but is molecules not impervious or permanent, brittle Wheatpaste vellum, paper, Natural Weak glue, edible, bookbinding polymer made subject to attack by up of gluten microorganisms or proteins water Gum Arabic Vellum, paper, pigment A true weak glue, edible binder, food binder, vegetable gum medicine binder Gum Vellum, paper, universal An oleoresin Weak glue, can be Ammoniac gilding mordant rehydrated to a tacky state, dries hard, is flexible Turpentine Vellum, paper, pigment An oleoresin Moderate glue, dries (real period binder, gilding mordant, hard, flexible when turpentine, not wood, wood filler young, may yellow or the modern cloud with age spirit turpentine) Plasters Stone, brick, tile, Calcined Moderate to strong ceramics, masonry filler, gypsum adhesive qualities, sets mordant ingredient compounds permanently Sugar, honey mordant ingredient, food hygroscopic Weak glue, can be and medicine binder sugars rehydrated to a tacky state, subject to mold Medieval Glues class notes, copyright 2007 by Catherine Helm-Clark. -
Adhesives and Sizes
MATERIALS INFORMATION and TECHNICAL RESOURCES for ARTISTS - Adhesives and Sizes A “size” is a material that is applied to a support (wood, fabric, etc.) to effectively seal the surface and serve as a barrier layer between the support and the paint and ground layers. Certain materials used as size will help to prevent Support Induced Discoloration (SID), a phenomenon that occurs when water-soluble impurities in the support migrate up through the ground and paint layers. A layer of size reduces the absorbency of the support, but size should not be applied too thickly. Too thick an application can lead to problems of delamination. It is best to use either a sponge or a brush and apply an even, thin solution that effectively penetrates the surface of the support. Sizing both the back and front of wooden supports will help mitigate warping of the panel. It is generally best to also size the sides of the panel. This is even more important if the support will remain unframed or is of lesser quality wood. Fabric supports, whether adhered to a rigid panel or mounted onto a stretcher, tend to shrink once properly sized. This is especially true when an animal glue size is used. Sizing reduces the absorbency of the fibers (preventing “strikethrough” or mediums/solvents from seeping through to the back of the support), protects the canvas from the acidity of certain materials (e.g. drying oils, alkyds), and creates a taut, planar surface suitable for painting. Table (courtesy of Golden Artist Colors, Inc.) summarizing results obtained using various sizes in combination with linseed oil grounds and canvas supports. -
The in Uence of Animal Glue on Mechanical Properties of Painting Canvases
The Inuence of Animal Glue on Mechanical Properties of Painting Canvases Hannah Duggan University College London Matija Strlic University College London Josep Grau-Bove ( [email protected] ) University College London https://orcid.org/0000-0003-0444-3194 Research article Keywords: glue, canvas, tensile test, accelerated ageing Posted Date: May 28th, 2020 DOI: https://doi.org/10.21203/rs.3.rs-30788/v1 License: This work is licensed under a Creative Commons Attribution 4.0 International License. Read Full License Page 1/19 Abstract Glues derived from animal products have been used in the preparation and conservation of painting canvas for hundreds of years. However, it is not clear how exactly these adhesives contribute to the mechanical strength of a canvas and how this contribution changes with time. This comparative study looks at the effect of age, thickness, and type of animal glue on the mechanical reinforcement the glues provide to canvas. Isinglass, rabbit skin, bovine hide and bone glue are compared. The mechanical strength of the canvas and glue system have been measured with a tensile test. The inuence of glue on the tensile response of canvas has been observed in the slope of the initial region of the stress-strain curve for these samples. This region has been identied as the initial load-bearing region which corresponds to the glue coating. The major contributing factor to change mechanical reinforcement of canvas is found to be the degradation of the glue, however the type of glue used plays a small role as does the thickness of the glue applied. -
English Edition, with the Addition of an Index, Was Prepared by ICCROM, Which Is Responsible for the Scientific Quality of the Translation
ANCIENT BINDING MEDIA, VARNISHES AND ADHESIVES Liliane Masschelein-Kleiner Translated by Janet Bridgland Sue Walston A.E. Werner ICCROM Rome, 1995 Editor's note: The place names included in this volume are not necessarily a reflec- tion of current geopolitical reality, but are based on the historical trade names under which various products and substances have come to be known. This second edition of Ancient Binding Media, Varnishes and Adhesives is based on the third French edition of Liants, vernis et aditesifs anciens, published in 1992 by the Institut Royal du Patrimoine Artistique, Brussels — ISBN 20930054-01-8. The English edition, with the addition of an index, was prepared by ICCROM, which is responsible for the scientific quality of the translation. ISBN 92-9077-119-4 © 1995 ICCROM ICCROM — International Centre for the Study of the Preservation and Restoration of Cultural Property Via di San Michele 13 1-00153 Rome RM, Italy Printed in Italy by A & J Servizi Grafici Editoriali Cover design: Studio PAGE Layout: Cynthia Rockwell Technical editing, indexing: Thorgeir Lawrence CONTENTS INTRODUCTION vii Chapter 1. PHYSICAL AND CHEMICAL PROPERTIES OF FILM-FORMING MATERIALS I. LIQUID STATE 1 Definitions: solution, dispersion, emulsion 1 I. 1 Surface phenomena and wetting 2 I. 2 Stabilization of pigments 5 I. 3 Rheological properties 6 I. 4 Oil index and critical concentration 10 II. SOLID STATE 12 II. 1 Film formation 12 II. 1. 1 Film formation by physical change 12 II. 1. 2 Film formation by chemical reaction 15 II. 2 Optical properties 17 II. 2. 1 Gloss 17 II. 2. -
Animal Glues
PROJECTS & TECHNIQUES Gluescience ng PHOTOGRAPHS BY YANNICK CHASTANG PHOTOGRAPHS YANNICK BY PHOTOGRAPHS BY YANNICK CHASTAPHOTOGRAPHS YANNICK BY Animal glues History of animal glue Yannick Chastang looks at the range of animal & woodworking glues available to the furniture maker and how The earliest making of animal glue is recorded in ancient Egypt. Stone these can be used to their best advantage carvings depict glue preparation and use as early as 1500BC want to start this article by looking at any minute human error in mixing where it was used for wood hide, bone and skin glues. An animal will result in bad curing and fast furnishings, mural painting and Iglue is created by prolonged boiling degradation. Even though most for the furniture in the Pharaoh’s of animal tissue. All animal glues are manufacturers say their adhesives tomb. Although used by the collagen based which is a protein will last forever, their claims are as Greeks and Romans, knowledge contained in animal bones and skins. yet unproven. In my experience, I have of the usefulness of animal glue The production of hide glue has always come across PVA from the 1970s died out in Europe until the been linked to the tanning industries that has already degraded. All too 1400s when woodworking and and is principally, in Europe, of cattle often the glue no longer has any furniture re-emerged as a craft. origin. Bone and skin glues are cohesion or strength and has become The first commercial glue factory prepared from fresh or extracted bones a rubbery mess stuck to the wood, began in Holland around 1700, and connective tissues from cattle and which has to be laboriously removed manufacturing animal glue from pigs. -
A Brief Survey of Wood Adhesives
Brief Survey of Wood Adhesives By Carl A. Eckelman Introduction Adhesives may be defined as any substance capable of attaching materials together by means of surface attachment. This property is not necessarily an intrinsic characteristic of the substance itself since the adhesive may be much weaker than the materials joined together, but it is developed as the adhesive interacts with the adherends under certain conditions of temperature and pressure. Knowledge and use of adhesives is not new. The ancient Egyptians knew well the art of veneering and used adhesives to attach decorations to wood some 3500 years before Christ. Mud, dung, and clay, along with mixtures of these substances, must also be regarded as adhesives and have been used for centuries to build huts in many parts of the world. Thatched huts plastered with a mixture of camel's dung and mud are still regularly used in southwestern Saudi Arabia, for example. Many types of glue have been used to bond wood together, but until the time of the Second World War, essentially all of the glues were of natural origin. Adhesives based on synthetic polymers were introduced just before WWII and now surpass most of the older natural glues in importance for wood bonding. These synthetic adhesives are used in situations which are far too demanding for adhesives of natural origin and satisfy moisture, durability, and strength requirements that were unthinkable a few years ago. At one time, adhesives belonged exclusively in the realm of the craftsmen; today, they have become indispensable to the engineer as well. Classification and Description For the most part, adhesives used to bond wood together may be separated into two distinct groups--those adhesives such as animal, vegetable, casein, and blood glues which are formulated from materials of natural origin, and those adhesives which are based on synthetic resins derived from petroleum, natural gas, and coal, i.e., products of the petrochemical and related industries. -
ANIMAL GLUES: Tt1elr MANUFACTURE, TESTING, and PREPARATIO N Revised June 195 5
4/ ANIMAL GLUES: Tt1ElR MANUFACTURE, TESTING, AND PREPARATIO N Revised June 195 5 (Te_?o v-+ No. 492 UNITED STATES ID.EPARTMENT OF AGRICULTURE FOREST SERVICE FOREST PRODUCTS LABORATOR Y Madison 5, Wisconsi n In Cooperation with the University of Wiaconain ANIMAL GLUES : iHhIR MANUFACTURE, TESTING, AND PREPARATION By Forest Products Laboratory,l Forest Servic e U. S . Department of Agricultur e Classes and Grades of Animal Glu e The term "animal glu e" refers broadly to all gelatin-type glues derive d from by-products of the meat-processing and tanning industries . The most common raw materials used are the hides, bones, and tendons of cat - tle . Other by-products of cattle and certain parts of other animals ar e also utilized. Glue made from hides is generally of higher grade, according to accepte d standards, than glue derived from bones and tendons . However, there is considerable variation in the grades of glue from hides as well as fro m the other sources . Glues for most uses, including woodworking, are com- monly blends of two or more batches from the same stock or from differen t classes of stock . Source is important only insofar as it affects grade . Each class of glue is sold in cake, flake, ground, pearl, shredded, an d other forms, but the form of the glue is no reliable indication of qual - ity . The chief difference between thevarious forms is in the quicknes s and convenience with which they can be put in solution . The finely di - vided forms absorb water more rapidly and can be dissolved more easil y than the cake and flake forms . -
Animal Glue and Inedible Gelatin from Yugoslavia, Sweden, the Netherlands, and West Germany
UNITED STATES INTERNATIONAL TRADE COMMISSION ANIMAL GLUE AND INEDIBLE GELATIN FROM YUGOSLAVIA, SWEDEN, THE NETHERLANDS, AND WEST GERMANY Determinations of Injury or Likelihood Thereof in Investigations Nos. AA1921-169, 170, 171 and 172 Under the Antidumping Act, 1921, as Amended, Together With the Information Obtained in the Investigations USITC Publication 840 Washington, D. C. October 1977 UNITED STATES INTERNATIONAL TRADE COMMISSION COMMISSIONERS Daniel Minchew, Chairman Joseph O. Parker, Vice Chairman George M. Moore Catherine Bedell Italo H. Ablondi Bill Alberger Kenneth R. Mason, Secretary to the Commission ~ This report was principally prepared by Thomas F. St. Maxens,. Investigator John M. MacHatton, Supervisory Investigator Address all communications to United States International Trade Commission Washington, D. C. 20436 C 0 N T E N T S Determinations--------------------------------------------------- 1 S tatement of reasons of Commissioners George M. Moore and Catherine Bedell------------------------------------------- 3 S tatement of reasons of Vice Chairman Joseph O. Parker---------- 9 Statement of reasons of Commissioner Italo H. Ablondi----------- 15 Statement of reasons of Chairman Daniel Hinchew---------------- 21 Information obtained in the investigations: Summary----------------------------------------------------- A-1 Overview of competitive conditions in the animal glue industry------------------------------------------------- A-4 Introduction------------------------------------------------ A-6 Description and -
Australian Adhesives for Paper, 1870-1920 for Paper, Adhesives Australian a and in Newspapers
Australian adhesives for paper, 1870-1920 Alice Cannon ABSTRACT From 1870–1920 adhesives for use with paper were either commercial preparations or made by hand in homes, studios and offices. For this research, recipes and commercial products in use in Australia during 1870–1920 were identified. However, the limited number of recipes discovered precludes any firm conclusions regarding the likely composition of unknown adhesives from this period. There is also little available information about Australian commercial products, such as Clag or Angus & Co Mucilage. It is likely that Australian usage trends mirrored those of England and America quite closely, as recipes published in international trade and amateur journals were available in Australia within months of publication. Additionally, commercial adhesives were shipped to Australia and sold by local businesses, such as those produced by the Russia Cement Company, the Leadenhall Press, the Gloy Manufacturing Company and Chas. M Higgins & Co. This paper presents the formulations and products known to be in use and the implications of these findings for the practicing paper conservator. KEYWORDS !"#$%&'(&!)%&*+&,-./&0-,,-1&"223/34%.5&%60$72318ĸ%9.5&31&)3./-930&9%03:%.& ';<+='>*+5&31/%91"/3-1"$&"12&?7./9"$3"1&31&-93831@ adhesive, Australia, conservation, glue, history, paper, starch Number/percentage of Ingredient recipes in which Probable uses INTRODUCTION ingredient occurs Old adhesives are an integral part of a paper conservator’s Water 621 (89.4%) Solvent/diluent work, as they are often disfiguring and damaging to paper- Alcohol 109 (15.7%) Solvent/diluent based collections. Conservators may remove old animal glue, Carbolic acid 100 (14.4%) Preservative starch paste and rubber cement from art works, documents and Glycerine 73 (10.5%) Plasticiser ephemera in order to release collection items from old mounts, to Alum (aluminium flatten cockling or in order to attempt stain reduction treatment. -
Protein Adhesives Chapter 5
5 Protein Adhesives Charles R. Frihart* and Linda F. Lorenz CONTENTS 5.1 Introduction .........................................................................,................................................ 145 5 2 Protein Structure................................................................,.................................................. 149 5 3 Soybean................................................................................................................................. 154 5.3.I High-pH Soy Flour Adhesives.................................................................................. 156 5.3.2 Moderate-pH Soy Flour Adhesives .......................................................................... 157 5.4 Other Plant Proteins (Wheat Gluten, Rapeseed/Canola, Lupine, Cottonseed).................... 157 5.4.1 Wheat Gluten............................................................................................................ 158 5.4.2 Rapeseed and Canola................................................................................................ 159 5.4.3 Lupine...................................................................,................................................... 160 5.4.4 Cottonseed ................................................................................................................ 161 5.5 Milk (Casein And Whey)................................................................................................... 162 5.5.1 Casein ...................................................................................................................... -
GC/MS Characterization of Beeswax, Protein, Gum, Resin, and Oil in Romano-Egyptian Paintings
heritage Article GC/MS Characterization of Beeswax, Protein, Gum, Resin, and Oil in Romano-Egyptian Paintings Joy Mazurek * , Marie Svoboda and Michael Schilling Getty Conservation Institute, Los Angeles, CA 90049, USA * Correspondence: [email protected]; Tel.: +1-310-440-6850 Received: 31 May 2019; Accepted: 13 July 2019; Published: 17 July 2019 Abstract: This article presents results from a binding media survey of 61 Romano-Egyptian paintings. Most of the paintings (51) are the better-known funerary mummy portraits created using either encaustic or tempera paint medium. Samples from all the paintings (on wooden panels or linen shrouds) were analyzed with gas chromatography/mass spectrometry (GC/MS) to identify waxes, fatty acids, resins, oils, and proteins in one sample. Analytical protocols that utilized three separate derivatization techniques were developed. The first analysis identified free fatty acids, waxes, and fatty acid soaps, the second characterized oils and plant resins, and the third identified proteins. The identification of plant gums required a separate sample. Results showed that fatty acids in beeswax were present as lead soaps and dicarboxylic fatty acids in some samples was consistent with an oxidized oil. The tempera portraits were found to contain predominantly animal glue, revising the belief that egg was the primary binder used for ancient paintings. Degraded egg coatings were found on several portraits, as well as consolidation treatments using paraffin wax and animal glue. The unknown restoration history of the portraits caused uncertainty during interpretation of the findings and made the identification of ancient paint binders problematic. Also, deterioration of the wooden support, residues from mummification, biodegradation, beeswax alteration, metal soap formation, and environmental conditions before and after burial further complicated the analysis. -
Ancient Egyptian Blackpatinated Copper
Archaeometry 54, 1 (2012) 175–192 doi: 10.1111/j.1475-4754.2011.00602.x ANCIENT EGYPTIAN BLACK-PATINATED COPPER ALLOYS* W. MOHAMED† and S. DARWEESH University of Cairo, Faculty of Archaeology, Conservation, El-Gamea Street, Giza, Egypt 12613 This analytical study aims to investigate ancient Egyptian black-patinated copper alloys. The study group was selected from the collections of the Egyptian Museum in Cairo and from the Faculty of Archaeology Museum in Cairo University. Examination and analysis were under- taken using optical microscopy (OM), scanning electron microscopy (SEM), energy-dispersive spectroscopy (EDX), X-ray diffractometry (XRD), X-ray fluorescence analysis (XRF) and Fourier transform infrared spectroscopy (FTIR). The analysis results indicated that the black patina contained mainly tenorite (CuO). The study presents evidence of thermal patination and animal glue coating. KEYWORDS: ANCIENT EGYPT, COPPER ALLOYS, BLACK PATINATION, THERMAL TREATMENT INTRODUCTION The colour black has been used as a pigment from prehistoric times. In dynastic times, it was considered to be the colour of the fertile soil of kmt (the Black Land), one of the names for Egypt; it therefore carried connotations of fertility and regeneration. It was also the colour of the underworld. The deity Osiris, ruler of the underworld, was referred to in texts as kmjj (the black one). During some periods, coffins were given a black ground as a reference to the underworld, to Osiris, and to the renewal of the deceased. Black skin was given to some royal images, to signify the king’s renewal and transformation. The association of black with the underworld and its transformatory powers explains the black statues of the king that were buried in the royal tomb of Tutankhamun and in other New Kingdom royal tombs (Redford 2000).