New Challenges Based on Bmw Hydrogen 7
Total Page:16
File Type:pdf, Size:1020Kb
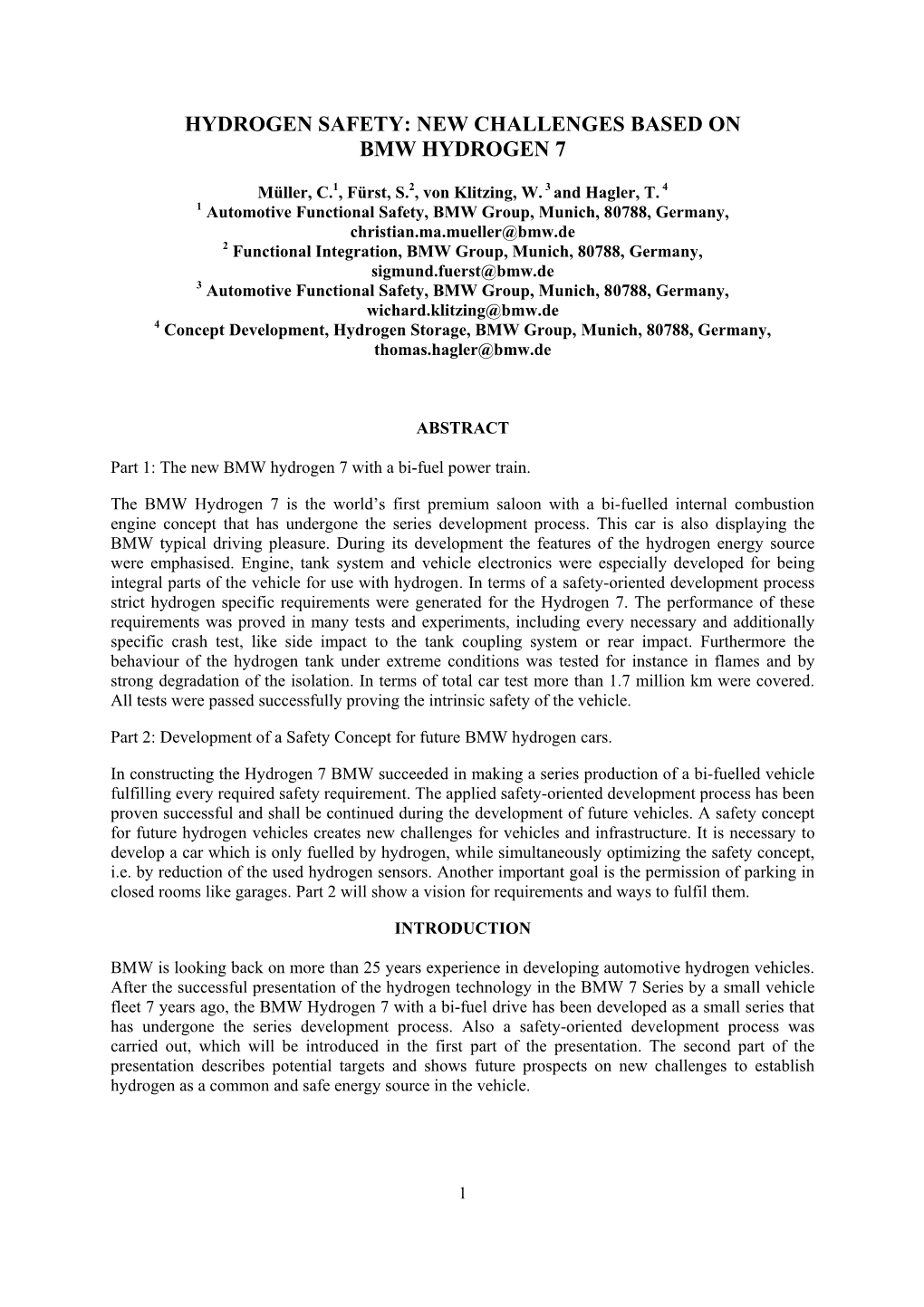
Load more
Recommended publications
-
1 Introduction Agata Godula-Jopek
1 1 Introduction Agata Godula-Jopek We find ourselves on the cusp of a new epoch in history, where every pos- sibility is still an option. Hydrogen, the very stuff of the stars and our own sun, is now being seized by human ingenuity and harnessed for human ends. Charting the right course at the very beginning of the journey is essential if we are to make the great promise of a hydrogen age a viable reality for our children and a worthy legacy for the generations that will come after us. Jeremy Rifkin [1]. Hydrogen is being considered as an important future energy carrier, which means it can store and deliver energy in a usable form. At standard temperature and pressure (0 ∘C and 1013 hPa), hydrogen exists in a gaseous form. It is odourless, colourless, tasteless, non-toxic and lighter than air. The stoichiometric fraction of hydrogen in air is 29.53 vol%. Abundant on earth as an element, hydrogen is present everywhere, being the simplest element in the universe representing 75 wt% or 90 vol% of all matter. As an energy carrier, hydrogen is not an energy source itself; it can only be produced from other sources of energy, such as fossil fuels, renewable sources or nuclear power by different energy conversion processes. Exothermic combustion reaction with oxygen forms water (heat of combustion 1.4 × 108 Jkg−1) and no greenhouse gases containing carbon are emitted to the atmosphere. Selected physical properties of hydrogen based on Van Nostrand are presented in Table 1.1 [2]. The energy content of hydrogen is 33.3 kWh kg−1, corresponding to 120 MJ kg−1 (lower heating value, LHV), and 39.4 kWh kg−1, corresponding to 142 MJ kg−1 (upper heating value, UHV). -
Vehicle Applicatons, Future of IC Engines
Part 10: Vehicle Applications, Future of IC Engines Reciprocating Internal Combustion Engines Prof. Rolf D. Reitz Engine Research Center University of Wisconsin-Madison 2014 Princeton-CEFRC Summer School on Combustion Course Length: 15 hrs (Mon.- Fri., June 23 – 27, 2014) Copyright ©2014 by Rolf D. Reitz. This material is not to be sold, reproduced or distributed without prior written permission of the owner, Rolf D. Reitz. 1 1 CEFRC9 CEFRC5 June-10, 29, 2014 2012 Part 10: Vehicle Applications, Future of IC Engines Short course outine: Engine fundamentals and performance metrics, computer modeling supported by in-depth understanding of fundamental engine processes and detailed experiments in engine design optimization. Day 1 (Engine fundamentals) Part 1: IC Engine Review, 0, 1 and 3-D modeling Part 2: Turbochargers, Engine Performance Metrics Day 2 (Combustion Modeling) Part 3: Chemical Kinetics, HCCI & SI Combustion Part 4: Heat transfer, NOx and Soot Emissions Day 3 (Spray Modeling) Part 5: Atomization, Drop Breakup/Coalescence Part 6: Drop Drag/Wall Impinge/Vaporization/Sprays Day 4 (Engine Optimization) Part 7: Diesel combustion and SI knock modeling Part 8: Optimization and Low Temperature Combustion Day 5 (Applications and the Future) Part 9: Fuels, After-treatment and Controls Part 10: Vehicle Applications, Future of IC Engines 2 CEFRC5-10, 2014 Part 10: Vehicle Applications, Future of IC Engines Kokjohn, IJER 2011, SAE 2011, SAE 2009 Light- & heavy-duty engine RCCI Heavy Light Duty Duty HD and LD engines compared over Engine CAT GM 1.9 L IMEP (bar) 9 gasoline/diesel fuel ratio sweep at 9 Engine speed (rev/min) 1300 1900 bar IMEP Mean piston speed (m/s) 7.2 5.7 LD engine intake temperature and Total fuel mass (mg) 94 20.2 pressure adjusted in to match HD EGR (%) 41 compression stroke Premixed gasoline (%) 82 to 89 81 to 84 Diesel SOI 1 (°ATDC) -58 -56 Engine size scaling laws do not provide Diesel SOI 2 (°ATDC) -37 -35 a scaling parameter for engine speed Diesel inj. -
Safety Consideration on Liquid Hydrogen
Safety Considerations on Liquid Hydrogen Karl Verfondern Helmholtz-Gemeinschaft der 5/JULICH Mitglied FORSCHUNGSZENTRUM TABLE OF CONTENTS 1. INTRODUCTION....................................................................................................................................1 2. PROPERTIES OF LIQUID HYDROGEN..........................................................................................3 2.1. Physical and Chemical Characteristics..............................................................................................3 2.1.1. Physical Properties ......................................................................................................................3 2.1.2. Chemical Properties ....................................................................................................................7 2.2. Influence of Cryogenic Hydrogen on Materials..............................................................................9 2.3. Physiological Problems in Connection with Liquid Hydrogen ....................................................10 3. PRODUCTION OF LIQUID HYDROGEN AND SLUSH HYDROGEN................................... 13 3.1. Liquid Hydrogen Production Methods ............................................................................................ 13 3.1.1. Energy Requirement .................................................................................................................. 13 3.1.2. Linde Hampson Process ............................................................................................................15 -
Comparison of Hydrogen Powertrains with the Battery Powered Electric Vehicle and Investigation of Small-Scale Local Hydrogen Production Using Renewable Energy
Review Comparison of Hydrogen Powertrains with the Battery Powered Electric Vehicle and Investigation of Small-Scale Local Hydrogen Production Using Renewable Energy Michael Handwerker 1,2,*, Jörg Wellnitz 1,2 and Hormoz Marzbani 2 1 Faculty of Mechanical Engineering, University of Applied Sciences Ingolstadt, Esplanade 10, 85049 Ingolstadt, Germany; [email protected] 2 Royal Melbourne Institute of Technology, School of Engineering, Plenty Road, Bundoora, VIC 3083, Australia; [email protected] * Correspondence: [email protected] Abstract: Climate change is one of the major problems that people face in this century, with fossil fuel combustion engines being huge contributors. Currently, the battery powered electric vehicle is considered the predecessor, while hydrogen vehicles only have an insignificant market share. To evaluate if this is justified, different hydrogen power train technologies are analyzed and compared to the battery powered electric vehicle. Even though most research focuses on the hydrogen fuel cells, it is shown that, despite the lower efficiency, the often-neglected hydrogen combustion engine could be the right solution for transitioning away from fossil fuels. This is mainly due to the lower costs and possibility of the use of existing manufacturing infrastructure. To achieve a similar level of refueling comfort as with the battery powered electric vehicle, the economic and technological aspects of the local small-scale hydrogen production are being investigated. Due to the low efficiency Citation: Handwerker, M.; Wellnitz, and high prices for the required components, this domestically produced hydrogen cannot compete J.; Marzbani, H. Comparison of with hydrogen produced from fossil fuels on a larger scale. -
Clean Energy Partnership
CLEAN ENERGY 2002–2016 PARTNERSHIP Clean Energy Partnership c/o be: public relations gmbh Phone: +49 (0)40 238 05 87 90 Fax: +49 (0)40 238 05 87 96 Email: [email protected] www.cleanenergypartnership.de/en www.facebook.com/cleanenergypartnership www.youtube.com/cleanenergypartner HYDROGEN – WHAT KEPT US MOVING 2002–2016 CONTENT Foreword............................................................................................................................................................ 04 Fourteen years of hydrogen mobility....................................................................................................... 06 Knowledge and project management...................................................................................................... 08 Developing.solutions.together..................................................................................................................... 08 The.focus.is.on.customer.friendliness......................................................................................................... 08 What.we.are.talking.about............................................................................................................................ 09 Production and storage..................................................................................................................................10 Crude.glycerol.pyrolysis...................................................................................................................................12 Reforming.process............................................................................................................................................12 -
The Case for Hydrogen Internal Combustion Engines Adam Campisi, Kyle Bartosik Stephen Poppa, Casey Rivera Advisor: Professor Brian Savilonis
Hydrogen Powered Vehicle The Case for Hydrogen Internal Combustion Engines Adam Campisi, Kyle Bartosik Stephen Poppa, Casey Rivera Advisor: Professor Brian Savilonis Abstract HICE vs. Fuel Cells Hydrogen Fuel Cell Hydrogen powered vehicles have been in development for the past decade. While hydrogen fuel cells HICE Vs. Current Fuel Cells have been receiving the majority of the attention, they will not be ready for mass production for fifteen to twenty-five years. Hydrogen internal combustion engines may prove to be the most Now Widespread Availability 15-25 Years effective solution for the immediate future. This project explores the feasibility of making hydrogen internal combustion engines in mass produced vehicles. We researched the different methods for $5000 to convert ICE to Cost >$100,000 producing hydrogen, storing it in vehicles and converting traditional internal combustion to burn HICE hydrogen instead of gasoline. Through this research we investigated the advantages of hydrogen BMW Hydrogen 7 HICE internal combustion engines over hydrogen fuel cells. 65% Efficiency 50% Power output compared to Up to 120% 80% gas None, runs effectively in all Difficulties running in Condition Limits conditions freezing temperatures Production Methods •Electrolysis is the separation of water into oxygen and hydrogen by running a direct electric current through the water. •It is the simplest and cleanest way of producing hydrogen, because the hydrogen that comes out of the process is 99.999% pure. •The total land area of Class 4 (medium purple color 50-100 thousand kg/sq. km year) and higher wind areas is approximately 568 944 square kilometers. If http://geothermal.marin.org/geopresentation/sld117.htm we assume the output of these areas to be 5 megawatts/sq kilometer (MW/km 2), the calculated potential for the United States becomes 2,845,000 MW. -
Goddard Unveils New Antenna Network in White Sands
National Aeronautics and Space Administration www.nasa.gov Volume 3 Issue 16 November 2007 View Goddard Unveils New Antenna Network in White Sands Pg 2 Employees Participate in Tree Planting as Part of the GSFC Sustainability Program Pg 6 The BMW Hydrogen 7 Visits Goddard Pg 8 Goddard 02 Goddard Unveils New Antenna Table of Contents Network in White Sands GoddardUpdates By Rob Garner Goddard Unveils New Antenna Network in White Sands - 2 SDO Instrument to Peer Inside the Sun Arrives at Goddard - 4 NESC Honors Goddard Employees and Partners for Technical Excellence - 5 Updates Daniel Glavin Wins Center’s First IRAD Innovator of the Year Award - 5 Employees Participate in Tree Planting as Part of the GSFC Sustainability Program - 6 The BMW Hydrogen 7 Visits Goddard - 8 GSFC Replaces Standard Government Sedan With a Neighborhood Electric Vehicle - 9 NASA Warms Up to Maryland’s Trash - 10 Employee Spotlight Fred Pierce - 12 Goddard Cover: White Sands Test Facility Team posing in front of one of the Ka-band antenna’s. Photo credit: Bill Gardner Photo credit: Bill Gardner Caption: Dr. Weiler gives remarks before cutting the ribbon to dedicate NASA’s new Ka-band antennas at the White Sands facility in New Mexico. GoddardView Info Goddard engineers showcased the new 18-meter Ka-band An- tenna Network, the first such system in Agency history, during a Goddard View is an official publication of the Goddard Space ribbon-cutting ceremony at the White Sands Test Facility in New Flight Center. It is published biweekly by the Office of Public Mexico on November 8. -
Liquid Organic Hydrogen Carriers (LOHC): an Auspicious Al- Ternative to Conventional Hydrogen Storage Technologies
Liquid Organic Hydrogen Carriers (LOHC): An auspicious al- ternative to conventional hydrogen storage technologies J. von Wild, T. Friedrich, A. Cooper, B. Toseland, G. Muraro, W. TeGrotenhuis, Y. Wang, P. Humble, A. Karim This document appeared in Detlef Stolten, Thomas Grube (Eds.): 18th World Hydrogen Energy Conference 2010 - WHEC 2010 Parallel Sessions Book 4: Storage Systems / Policy Perspectives, Initiatives and Co- operations Proceedings of the WHEC, May 16.-21. 2010, Essen Schriften des Forschungszentrums Jülich / Energy & Environment, Vol. 78-4 Institute of Energy Research - Fuel Cells (IEF-3) Forschungszentrum Jülich GmbH, Zentralbibliothek, Verlag, 2010 ISBN: 978-3-89336-654-5 Proceedings WHEC2010 189 Liquid Organic Hydrogen Carriers (LOHC): An auspicious alternative to conventional hydrogen storage technologies J. von Wild, T. Friedrich, BMW Group Research and Technology, Germany A. Cooper, B. Toseland, G. Muraro, Air Products & Chemicals Ward TeGrotenhuis, Yong Wang, Paul Humble, Ayman Karim, Pacific Northwest National Laboratory, USA 1 Introduction Due to the limited availability of fossil fuels – the finite nature and instability of fossil fuel sup- ply and limited production rate – mankind is facing increasing pressure to establish a sus- tainable alternative energy economy. At least since the so-called “oil crises” in the 1970’s, the automotive industry has started to strive towards a possible substitution of an oil-based energy carrier. As the optimum long-term solution, hydrogen has been identified as an en- ergy carrier, produced on the basis of renewable energy sources (water, sun, wind, biomass) and distributed and stored within adapted infrastructure with new or modified facilities for car refueling. The realistic implementation of this vision, among others, has been pursued at BMW for more than 30 years in the framework of the “CleanEnergy” program [1]. -
Zero Emissions Trucks
Zero emissions trucks An overview of state-of-the-art technologies and their potential Report Delft, July 2013 Author(s): Eelco den Boer (CE Delft) Sanne Aarnink (CE Delft) Florian Kleiner (DLR) Johannes Pagenkopf (DLR) Publication Data Bibliographical data: Eelco den Boer (CE Delft), Sanne Aarnink (CE Delft), Florian Kleiner (DLR), Johannes Pagenkopf (DLR) Zero emissions trucks An overview of state-of-the-art technologies and their potential Delft, CE Delft, July 2013 Publication code: 13.4841.21 CE publications are available from www.cedelft.eu Commissioned by: The International Council for Clean Transportation (ICCT). Further information on this study can be obtained from the contact person, Eelco den Boer. © copyright, CE Delft, Delft CE Delft Committed to the Environment CE Delft is an independent research and consultancy organisation specialised in developing structural and innovative solutions to environmental problems. CE Delft’s solutions are characterised in being politically feasible, technologically sound, economically prudent and socially equitable. Subcontractor information German Aerospace Center Institute of Vehicle Concepts Prof. Dr. Ing. H.E. Friedrich Pfaffenwaldring 38-40 D-70569 Stuttgart, Germany http://www.dlr.de 2 July 2013 4.841.1 – Zero emissions trucks Preface This report has been developed to contribute to the discussion on future road freight transport and the role on non-conventional drivetrains. The primary objective of the report is to assess zero emission drivetrain technologies for on-road heavy-duty freight vehicles. More specifically, their CO2 reduction potential, the state of these technologies, their expected costs in case of a technology shift, the role of policies to promote these technologies, and greenhouse reduction scenarios for the European Union have been studied. -
Analysis of Published Hydrogen Vehicle Safety Research
DOT HS 811 267 February 2010 Analysis of Published Hydrogen Vehicle Safety Research DISCLAIMER This publication is distributed by the U.S. Department of Transportation, National Highway Traffic Safety Administration, in the interest of information exchange. The opinions, findings, and conclusions expressed in this publication are those of the authors and not necessarily those of the Department of Transportation or the National Highway Traffic Safety Administration. The United States Government assumes no liability for its contents or use thereof. If trade names, manufacturers’ names, or specific products are mentioned, it is because they are considered essential to the object of the publication and should not be construed as an endorsement. The United States Government does not endorse products or manufacturers. TECHNICAL REPORT DOCUMENTATION PAGE 1. Report No. 2. Government Accession No. 3. Recipient's Catalog No. DOT HS 811 267 4. Title and Subtitle 5. Report Date Analysis of Published Hydrogen Vehicle Safety Research February 2010 6. Performing Organization Code NHTSA/NVS-312 7. Author(s) 8. Performing Organization Report Stephanie Flamberg, Susan Rose, Denny Stephens – Battelle Memorial Institute No. 9. Performing Organization Name and Address 10. Work Unit No. (TRAIS) Battelle Memorial Institute 11. Contract or Grant No. 505 King Avenue DTNH22-08-D-00080 Columbus, Ohio 43201 12. Sponsoring Agency Name and Address 13. Type of Report and Period National Highway Traffic Safety Administration Covered 1200 New Jersey Avenue SE. Final Washington, DC 20590 14. Sponsoring Agency Code 15. Supplementary Notes 16. Abstract Hydrogen-fueled vehicles (HFVs) offer the promise of providing safe, clean, and efficient transportation in a setting of rising fuel prices and tightening environmental regulations. -
Hydrogen Powered Vehicle the Case for Hydrogen Internal Combustion Engines Adam Campisi, Kyle Bartosik Stephen Poppa, Casey Rivera Advisor: Professor Brian Savilonis
Hydrogen Powered Vehicle The Case for Hydrogen Internal Combustion Engines Adam Campisi, Kyle Bartosik Stephen Poppa, Casey Rivera Advisor: Professor Brian Savilonis Abstract HICE vs. Fuel Cells Hydrogen Fuel Cell Hydrogen powered vehicles have been in development for the past decade. While hydrogen fuel cells HICE Vs. Current Fuel Cells have been receiving the majority of the attention, they will not be ready for mass production for fifteen to twenty-five years. Hydrogen internal combustion engines may prove to be the most Now Widespread Availability 15-25 Years effective solution for the immediate future. This project explores the feasibility of making hydrogen internal combustion engines in mass produced vehicles. We researched the different methods for $5000 to convert ICE to Cost >$100,000 producing hydrogen, storing it in vehicles and converting traditional internal combustion to burn HICE hydrogen instead of gasoline. Through this research we investigated the advantages of hydrogen BMW Hydrogen 7 HICE internal combustion engines over hydrogen fuel cells. 65% Efficiency 50% Power output compared to Up to 120% 80% gas None, runs effectively in all Difficulties running in Condition Limits conditions freezing temperatures Production Methods •Electrolysis is the separation of water into oxygen and hydrogen by running a direct electric current through the water. •It is the simplest and cleanest way of producing hydrogen, because the hydrogen that comes out of the process is 99.999% pure. •The total land area of Class 4 (medium purple color 50-100 thousand kg/sq. km year) and higher wind areas is approximately 568 944 square kilometers. If http://geothermal.marin.org/geopresentation/sld117.htm we assume the output of these areas to be 5 megawatts/sq kilometer (MW/km 2), the calculated potential for the United States becomes 2,845,000 MW. -
Hydrogen – Join the Movement!
HYDROGEN – JOIN THE MOVEMENT! CEP Phase III April 2011 A lighthouse project within the National Hydrogen and Fuell Cell Technology Innovation Program km 1.000.000 Content Strong partners jointly developing the fuel of the future 4 The CEP: A lighthouse project 5 CEP Phase I–III – Phase I: How it all began 6 Phase II: Putting the technology to the test 6 Phase III: Quantities 7 Why hydrogen? 8 Hydrogen production 8 Hydrogen storage 9 Fuel cell mobility 10 Conventional but different – hydrogen internal combustion engine vehicle (HICEV) 12 The CEP’s hydrogen filling stations 14 Expectations and social aspects 17 Overview vehicles 18 Overview filling stations 20 Contact 24 2 | April 2011 April 2011 | 3 The Clean Energy Partnership is Europe’s largest demons- tration project for hydrogen mobility. Strong partners jointly developing the fuel of The CEP: A lighthouse the future project The Clean Energy Partnership (CEP) focuses on clean, quiet, low-emission mobility Lighthouse projects build a bridge between R&D for the future. Thirteen partners – Berliner Verkehrsbetriebe, BMW, Daimler, Ford, (research and development) and the markets, GM/Opel, Hamburger Hochbahn, Linde, Shell, Statoil, Total, Toyota, Vattenfall and and create platforms for subsequent marketing. Volkswagen – are testing the system compatibility of hydrogen (H2)n i everyday use. The s CEP i the lighthouse project of Germany’s National Innovation Programme for Hydrogen Itsn i a ambitious project, as both the technical and economic solutions will have and Fuel Cell Technology (NIP) in the traffic and to prove themselves under real-life conditions. This not only includes being able to transport sector.