Program and System Evaluation Syncom
Total Page:16
File Type:pdf, Size:1020Kb
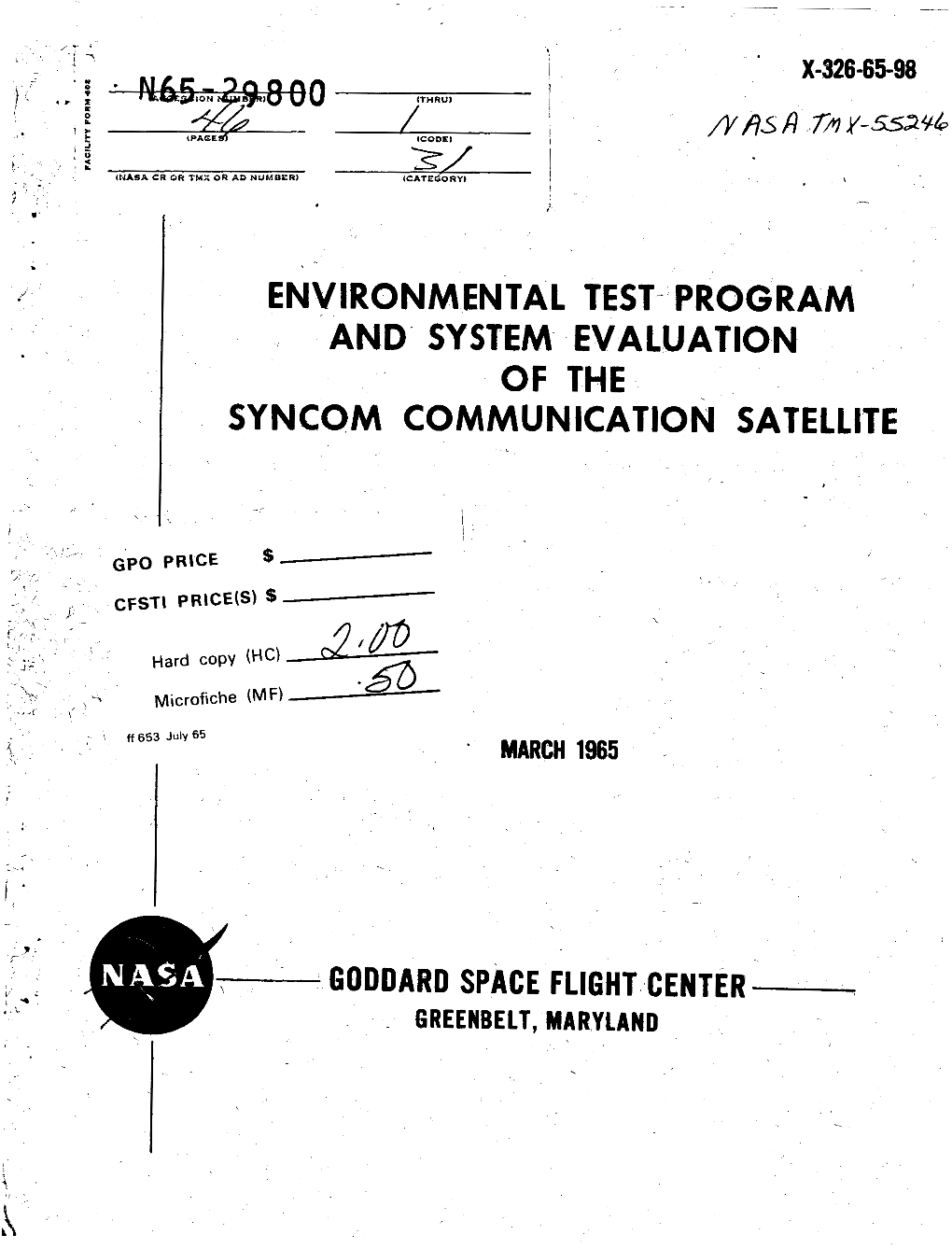
Load more
Recommended publications
-
Rendezvous and Proximity Operations of the Space Shuttle Source of Acquisition John L
FROM :UNITED SfffCE RLL I FINE 281 212 6326 2005s 08-11 09: 34 #127 P. 05/21 Rendezvous and Proximity Operations of the Space Shuttle Source of Acquisition John L. Gooban' NASA JO~~SO~Space Center Uniied Space Albance, LLC, Hou.Wm. Texas: 77058 Spnce Shuttle rendmous missinns presented unique chalfengcs Clint were not fully recogni;ccd altea the Shutde WH~:deslgned. Rendezvous hrgcte could be passive (Le., no lights or Wnnrponders), and not designad 10 BcllIfate Shuttro rendezvous, praxlntlty operfirttlons and rclricval. Shuttls rendon control system ]ct plume lmplngetnent nn target spacccmfl prewnrcd Induced dynnmlcs, structoral loading and conhmlndon concerns. These Issues, along with fliiilfed forWard raction control system prupcllxnf drove II change from the GcmlniiApollo cuuillptlc profile heritage to a stnbte orbit proflle. and the development of new prorlmlly opcrntlons techniqucs. Multiple xckiitlfic and an-orbit servicing. tlssions; and crew exchanp, nsocmbly and rcplenlshment nigh& to Mir and io the InlernnBonnf Space S(Bfi0n dmve further pmfflc and pilnfing technique change%,lrcluding new rciative naviptlon senran gnd new ciwputcr generated piloting CPCS. Nomenclature the issucs with Shuffle rmdczvous md proximity operatiom had been f1.111~identified and resolved, which in N~Ircsultcd in complcx H Bar = unit vector along &e =get orbital angular illomcntum opmntionnl work-wounds. koposds for \chicle cepabiiitia vector competed for funding based on available budget, Bvaihbk schcduk, and criticality to Safety and mission success. Technical challenges in ix = LVLH +X axis vcctor $ = LTL~*Wrnk~CIOT ---b-uilding-~wsable~~~'~prt~.c~~-s~c~as propubion, &txid -tr- Lv&--i.Z-xiwe~oT---- _-- . protwtion. -
The Legal Ordering of Satellite Telecommunication: Problems and Alternatives
Indiana Law Journal Volume 44 Issue 3 Article 1 Spring 1969 The Legal Ordering of Satellite Telecommunication: Problems and Alternatives Delbert D. Smith University of Wisconsin Follow this and additional works at: https://www.repository.law.indiana.edu/ilj Part of the Air and Space Law Commons, and the Communications Law Commons Recommended Citation Smith, Delbert D. (1969) "The Legal Ordering of Satellite Telecommunication: Problems and Alternatives," Indiana Law Journal: Vol. 44 : Iss. 3 , Article 1. Available at: https://www.repository.law.indiana.edu/ilj/vol44/iss3/1 This Article is brought to you for free and open access by the Law School Journals at Digital Repository @ Maurer Law. It has been accepted for inclusion in Indiana Law Journal by an authorized editor of Digital Repository @ Maurer Law. For more information, please contact [email protected]. INDIANA LAW JOURNAL Volume 44 Spring 1969 Number 3 THE LEGAL ORDERING OF SATELLITE TELECOMMUNICATION: PROBLEMS AND ALTERNATIVES DELBERT D. SMITHt The use of satellites in outer space to provide a means of transmission for international telecommunication could be viewed as simply a tech- nological advancement neither necessitating basic structural changes in the international control institutions nor requiring alteration of the control theories designed to regulate unauthorized transmissions. How- ever, the magnitude of the changes involved, coupled with increased governmental concern, has resulted in a number of politico-legal problems. It is the purpose of this article to examine on several levels of analysis the implications of utilizing satellites as a means of telecom- munication transmission. Introductory material on the development of communications satellite technology stresses the need for international organization and co-operation to oversee the launching and maintenance of a global communications system and indicates the pressures for the implementation of control measures over transmissions originating in outer space. -
NASA Begins 5Th RS-25 Test Series
Volume 14 Issue 8 www.nasa.gov/centers/stennis August 2018 NASA begins 5th RS-25 test series NASA conducts a successful hot fire test of RS-25 developmental engine No. 0525 – featuring a new flight controller unit – on the A-1 Test Stand at Sten- nis Space Center on Aug. 14.The test was viewed by new NASA Administrator Jim Bridenstine and other guests. (See page 3 article) Page 2 LAGNIAPPE August 2018 It is estimated somewhere between 500 million to It was only fitting, then, that new NASA Administra- 600 million people around the world watched Neil tor Jim Bridenstine wasted little time in making his first Armstrong step onto the surface of the Moon in July visit to the site as agency leader. More fitting, he was 1969. It was the largest television audience at the time, able to view the Aug. 14 test and see firsthand the Sten- although they were not all in the same room. Ark! nis blended test team of NASA, Aerojet Rocketdyne and Syncom Space Services engineers and operators Probably nowhere near that many folk watched the at work. He also got a firsthand look at site facilities, NASA-TV and social media live broadcast of the RS- including the Aerojet Rocketdyne Engine Assembly 25 rocket engine test here Aug. 14 – but it is safe to say Facility, the E Test Complex and the B-2 Test Stand. an awful lot of attention is focused on Stennis Space Center these days. More importantly, the new NASA leader was able to visit with center and resident agency leaders, local Stennis is at the forefront of NASA’s work to build and media members, community representatives and site launch its new Space Launch System (SLS) rocket that employees. -
The Delta Launch Vehicle- Past, Present, and Future
The Space Congress® Proceedings 1981 (18th) The Year of the Shuttle Apr 1st, 8:00 AM The Delta Launch Vehicle- Past, Present, and Future J. K. Ganoung Manager Spacecraft Integration, McDonnell Douglas Astronautics Co. H. Eaton Delta Launch Program, McDonnell Douglas Astronautics Co. Follow this and additional works at: https://commons.erau.edu/space-congress-proceedings Scholarly Commons Citation Ganoung, J. K. and Eaton, H., "The Delta Launch Vehicle- Past, Present, and Future" (1981). The Space Congress® Proceedings. 7. https://commons.erau.edu/space-congress-proceedings/proceedings-1981-18th/session-6/7 This Event is brought to you for free and open access by the Conferences at Scholarly Commons. It has been accepted for inclusion in The Space Congress® Proceedings by an authorized administrator of Scholarly Commons. For more information, please contact [email protected]. THE DELTA LAUNCH VEHICLE - PAST, PRESENT AND FUTURE J. K. Ganoung, Manager H. Eaton, Jr., Director Spacecraft Integration Delta Launch Program McDonnell Douglas Astronautics Co. McDonnell Douglas Astronautics Co. INTRODUCTION an "interim space launch vehicle." The THOR was to be modified for use as the first stage, the The Delta launch vehicle is a medium class Vanguard second stage propulsion system, was used expendable booster managed by the NASA Goddard as the Delta second stage and the Vanguard solid Space Flight Center and used by the U.S. rocket motor became Delta's third stage. Government, private industry and foreign coun Following the eighteen month development program tries to launch scientific, meteorological, and failure to launch its first payload into or applications and communications satellites. -
Telstar – a Philatelic History the Communication Revolution Began with This Satellite Series
Telstar – A Philatelic History The Communication Revolution Began with this Satellite Series Don Hillger SU5200, Garry Toth, and Sig Bette SU-1063 This Telstar article appeared in the October 2012 issue of American Philatelic Society’s “American Philatelist” magazine, and is reprinted with the permission of Editor Barbara Boal Telstar-1 made history for our interested Space Unit members. over fifty years ago on July 11, 1962, one day after its launch, when it transmitted the first television signals across the Atlantic Ocean,1 between the United States of America and France. Al- though not the first active communications satellite,2 it became a popular and recognizable name in the new world of artificial satellites. Telstar even spawned a musical composition titled “Telstar,” performed by The Tornados, an instrumental band A second set of common design stamps of the early 1960s. Their recording was was issued to commemorate the same the first single by a British band to event, but the event is noted as the “first reach number one in the United States, television transmission between Europe later becaming a number one hit in the and America,” versus “first television United Kingdom as well. Written and transmission by satellite” on the previous produced by Joel Meek, the spacey issue. On all of these stamps the cities of sounds of the recording were produced Andover (Maine) and Pleumeur-Bodou by a clavioline, a keyboard instrument (France) are identified, with Telstar shown with distinctive electronic sounds. The in orbit, relaying signals between the song was also recorded by other bands, two locations. -
Shuttle Missions 1981-99.Pdf
1 2 Table of Contents Flight Page Flight Page 1981 STS-49 .................................................................................... 24 STS-1 ...................................................................................... 5 STS-50 .................................................................................... 25 STS-2 ...................................................................................... 5 STS-46 .................................................................................... 25 STS-47 .................................................................................... 26 1982 STS-52 .................................................................................... 26 STS-3 ...................................................................................... 5 STS-53 .................................................................................... 27 STS-4 ...................................................................................... 6 STS-5 ...................................................................................... 6 1993 1983 STS-54 .................................................................................... 27 STS-6 ...................................................................................... 7 STS-56 .................................................................................... 28 STS-7 ...................................................................................... 7 STS-55 ................................................................................... -
China Dream, Space Dream: China's Progress in Space Technologies and Implications for the United States
China Dream, Space Dream 中国梦,航天梦China’s Progress in Space Technologies and Implications for the United States A report prepared for the U.S.-China Economic and Security Review Commission Kevin Pollpeter Eric Anderson Jordan Wilson Fan Yang Acknowledgements: The authors would like to thank Dr. Patrick Besha and Dr. Scott Pace for reviewing a previous draft of this report. They would also like to thank Lynne Bush and Bret Silvis for their master editing skills. Of course, any errors or omissions are the fault of authors. Disclaimer: This research report was prepared at the request of the Commission to support its deliberations. Posting of the report to the Commission's website is intended to promote greater public understanding of the issues addressed by the Commission in its ongoing assessment of U.S.-China economic relations and their implications for U.S. security, as mandated by Public Law 106-398 and Public Law 108-7. However, it does not necessarily imply an endorsement by the Commission or any individual Commissioner of the views or conclusions expressed in this commissioned research report. CONTENTS Acronyms ......................................................................................................................................... i Executive Summary ....................................................................................................................... iii Introduction ................................................................................................................................... 1 -
Television Tests with the Syncom Ii Synchronous Communications Satellite
NASA TECHNICAL NOTE NASA TN D-2911I__ --- _I c:: c:: [ TELEVISION TESTS WITH THE SYNCOM I1 SYNCHRONOUS COMMUNICATIONS SATELLITE Goddard Space Flight Center Greenbelt, Md. NATIONAL AERONAUTICS AND SPACE ADMINISTRATION WASHINGTON, D. C. JULY 1965 TECH LIBRARY KAFB, NM I Illill lllll11111 Plll111lll Ill11 lllll RII 111 0079bLO NASA TN D-2911 TELEVISION TESTS WITH THE SYNCOM I1 SYNCHRONOUS COMMUNICATIONS SATELLITE By Varice F. Henry and Michael E. McDonald Goddard Space Flight Center Greenbelt, Md. NATIONAL AERONAUTICS AND SPACE ADMlN ISTRATION For sale by the Clearinghouse for Federal Scientific and Technical Information Springfield, Virginia 22151 - Price $1.00 TELEVISION TESTS WITH THE SYNCOM II SYNCHRONOUS COMMUNICATIONS SATELLITE by Varice F. Henry and Michael E. McDonald Goddard Space Flight Center SUMMARY The results of a series of experimental tests employing a reduced video bandwidth of 2.5 Mc with the restricted radio frequency bandwidth of 5 Mc in the Syncom I1 satellite are described. These tests were de- signed to explore the feasibility of television transmissions for demon- stration purposes only because the original system design parameters were based on a few channels of voice transmissions. Emphasis is placed on the microwave parameters of the transmitting and receiving ground terminals, located at Ft. Dix, New Jersey and Andover, Maine respectively. Quantitative and qualitative evaluations of the results are presented, as well as recorded samples of the received video signals which represent the first successful transmissions of standard mono- chrome television signals in real-time through a synchronous satellite. iii CONTENTS Summary ....................................... iii INTRODUCTION ................................... 1 GROUND TERMINALS .............................. 2 Transmission Terminal........................... 2 Receiving Terminal ............................ -
Space Shuttle Mission Sts-41D Press Kit August 1984
NATIONAL AERONAUTICS AND SPACE ADMINISTRATION SPACE SHUTTLE MISSION STS-41D PRESS KIT AUGUST 1984 FIRST FLIGHT OF DISCOVERY SBS-4, LEASAT-2, TELSTAR-3 DEPLOYMENT; OAST-1 Edited by Richard W. Orloff, 01/2001/Page 1 STS-41D INSIGNIA S84-26391 -- The insignia for the STS-41D mission features the Discovery, NASA's third orbital vehicle, as it makes its maiden voyage. The ghost ship represents the orbiter's namesakes which have figured prominently in the history of exploration. The space shuttle Discovery heads for new horizons to extend that proud tradition. The NASA insignia design for space shuttle flights is reserved for use by the astronauts and for other official use as the NASA Administrator may authorize. Public availability has been approved only in the form of illustrations by the various news media. When and if there is any change in this policy, which we do not anticipate, it will be publicly announced. PHOTO CREDIT: NASA or National Aeronautics and Space Administration. Edited by Richard W. Orloff, 01/2001/Page 2 RELEASE NO: 8 4 - 117 August 1984 CONTACTS Charles Redmond/Debra Rahn Headquarters, Washington, D.C. (Phone: 202/453-8590) Dick Young Kennedy Space Center, Fla. (Phone: 305/867-2468) Dave Alter Johnson Space Center, Houston, Texas (Phone: 713/483-5111) Bob Ruhl Marshall Space Flight Center, Huntsville, Ala. (Phone: 205/453-0034) Ralph Jackson Dryden Flight Research Facility, Edwards, Calif. (Phone: 805/258-8381) Edited by Richard W. Orloff, 01/2001/Page 3 RELEASE NO: 8 4 - 117 August 1984 CONTENTS GENERAL RELEASE 5 41-D BRIEFING SCHEDULE 7 GENERAL INFORMATION 8 MISSION 41-D REMANIFEST -- QUICK LOOK FACTS 9 SUMMARY OF MAJOR ACTIVITIES 10 41-D REMANIFEST SEQUENCE OF EVENTS 12 CONFIGURATION AND WEIGHTS 13 SBS-4 15 LEASAT 2 (Syncom IV-2) 16 TELSTAR 3 18 OAST-1 19 Solar Array Experiment 22 Dynamic Augmentation Experiment 23 Solar Cell Calibration Facility 23 OAST-1 Team 23 CONTINUOS FLOW ELECTROPHORESIS SYSTEM 25 VEHICLE GLOW EXPERIMENT 27 CLOUDS 27 IMAX 27 SHUTTLE STUDENT INVOLVEMENT PROJECT 28 41-D FLIGHT CREW DATA 29 Edited by Richard W. -
Assessing the Impact of US Air Force National Security Space Launch Acquisition Decisions
C O R P O R A T I O N BONNIE L. TRIEZENBERG, COLBY PEYTON STEINER, GRANT JOHNSON, JONATHAN CHAM, EDER SOUSA, MOON KIM, MARY KATE ADGIE Assessing the Impact of U.S. Air Force National Security Space Launch Acquisition Decisions An Independent Analysis of the Global Heavy Lift Launch Market For more information on this publication, visit www.rand.org/t/RR4251 Library of Congress Cataloging-in-Publication Data is available for this publication. ISBN: 978-1-9774-0399-5 Published by the RAND Corporation, Santa Monica, Calif. © Copyright 2020 RAND Corporation R® is a registered trademark. Cover: Courtesy photo by United Launch Alliance. Limited Print and Electronic Distribution Rights This document and trademark(s) contained herein are protected by law. This representation of RAND intellectual property is provided for noncommercial use only. Unauthorized posting of this publication online is prohibited. Permission is given to duplicate this document for personal use only, as long as it is unaltered and complete. Permission is required from RAND to reproduce, or reuse in another form, any of its research documents for commercial use. For information on reprint and linking permissions, please visit www.rand.org/pubs/permissions. The RAND Corporation is a research organization that develops solutions to public policy challenges to help make communities throughout the world safer and more secure, healthier and more prosperous. RAND is nonprofit, nonpartisan, and committed to the public interest. RAND’s publications do not necessarily reflect the opinions of its research clients and sponsors. Support RAND Make a tax-deductible charitable contribution at www.rand.org/giving/contribute www.rand.org Preface The U.S. -
I- Marshall Space Flight Center 1990 Annual Chronology of Events
/,/ ._J i- National Aeronautics and Space Administration MHR-20 IllU George C. Marshall Space Flight Center Marshall Space Flight Center, Alabama 35812 Marshall Space Flight Center 1990 Annual Chronology of Events -_ ,j ? C r ;_. _' 1._,? J ,,,_!';_1;,| Cii#_J_}.J( _,','r ,. '-V:':T ":"; ':_r_, ) J 'i-,o - -",,:,r- . '_.r_(_r-_ ( :_, ) '- ::eL Compiled by Management Operations Office MSFC - Form 454 (Rev. October 1976) 5-026-2 Form Approved REPORT DOCUMENTATION PAGE o_8 _o o7o_-ola8 i Public re/:_Orllng burOen for thfs collection of information is e_tlmate_l to average 1 hour Der resoonse, including the tii_e for reviewing Instructions searchrng ex_stlng data _ource_, gathering anti f_alntalnlng the data nee¢led, and completing and revlew=ng the colted_on Of Information send comments regarding this burden es_qma_e o_"any other asoect Of this COlleCtiOn Of i_forlff_atlon, rncluding suggestions for reducing this burden, to Wash,ngton HeaclQuarters Servtces, Directorate for Information Ol_et'3_l@n_ and Re!_orts, 1215 Jefferson Oaws Highway. Suite ! 204, A¢/ingtOn, VA 22202-4302. and to the Office O_ V_anagemen_ anO Budget, Pa_cwork Reduction Proleqt (0704-O t88), Washington. [)C 2050_ 1. AGENCY USE ONLY (Leave blank) J '2. REPORT DATE 3. REPORT TYPE AND DATES COVERED I October 1991 Jan _Q - _e: 90 4. TITLE AND SUBTITLE S. FUNDING NUMBERS Marshall Space Flight Center 1990 Annual Chronology of Events 6. AUTHOR(S) Michael Wright 7. PERFORMING ORGANIZATION NAME(S) AND ADDRESS(ES) 8. PERFORMING ORGANIZATION REPORT NUMBER George C. Marshall Space Flight Center Marshall Space Flight Center, Alabama 35812 MHR-20 9. -
Hubble Space Telescope Specifications
This document is from the collections at the Dole Archives, University of Kansas http://dolearchives.ku.edu SPACE SHUTTLE MISSION STS-31 PRESS KIT APRIL 1990 Page 1 of 24 This document is from the collections at the Dole Archives, University of Kansas http://dolearchives.ku.edu PUBLIC AFFAIRS CONTACTS Ed Campion Office of Space Flight Kyle Herring Johnson NASA Headquarters, Washington, D.C. Space Center, Houston, Texas (Phone: 202/453-8536) (Phone: 713/483-5111) Paula Cleggett-Haleim Dave Drachlis/Jerry Berg Marshall Office of Space Science and Applications Space Flight Center, Huntsville, Ala. NASA Headquarters, Washington, D.C. (Phone: 205/544-0034) (Phone: 202/453-1548) Myron Webb Barbara Selby Stennis Space Center, Bay St. Louis, Miss. Office of Commercial Programs (Phone: 601/688-3341) NASA Headquarters, Washington, D.C. (Phone: 202/453-2927) Nancy Lovato Ames-Dryden Flight Research Facility, Edwards, Calif. Dwayne Brown (Phone: 805/258-8381) Office of Space Operations NASA Headquaters, Washington, D.C. Robert J. MacMillin Jet Propulsion (Phone: 202/453-8956) Laboratory, Pasadena, Calif. (Phone: 818/354-5011) Lisa Malone Kennedy Space Center, Fla. Jim Elliott (Phone: 407/867-2468) Goddard Space Flight Center, Greenbelt, Md. (Phone: 301/286-6256) Page 2 of 24 CONTENTS GENERAL RELEASE ............................................................ 1 SPACE TELESCOPE OPERATIONS CONTROL ............... 18 GENERAL INFORMATION .................................................... 2 SPACE TELESCOPE SCIENCE INSTITUTE ...................... 18 STS-31 QUICK LOOK ...........................................................3 EUROPEAN COORDINATING FACILITY ........................... 20 SUMMARY OF MAJOR ACTIVITIES .................................... 3 HUBBLE SPACE TELESCOPE SPECIFICATIONS ............ 20 TRAJECTORY SEQUENCE OF EVENTS ........................... .4 FUNCTIONAL DESCRIPTION OF HST OPERATIONS ...... 21 SPACE SHUTTLE ABORT MODES ...................................... 4 SCIENCE QUESTIONS HST WILL HELP ANSWER .........