Why an Offshore Sailing Barge Might Be Worth Building
Total Page:16
File Type:pdf, Size:1020Kb
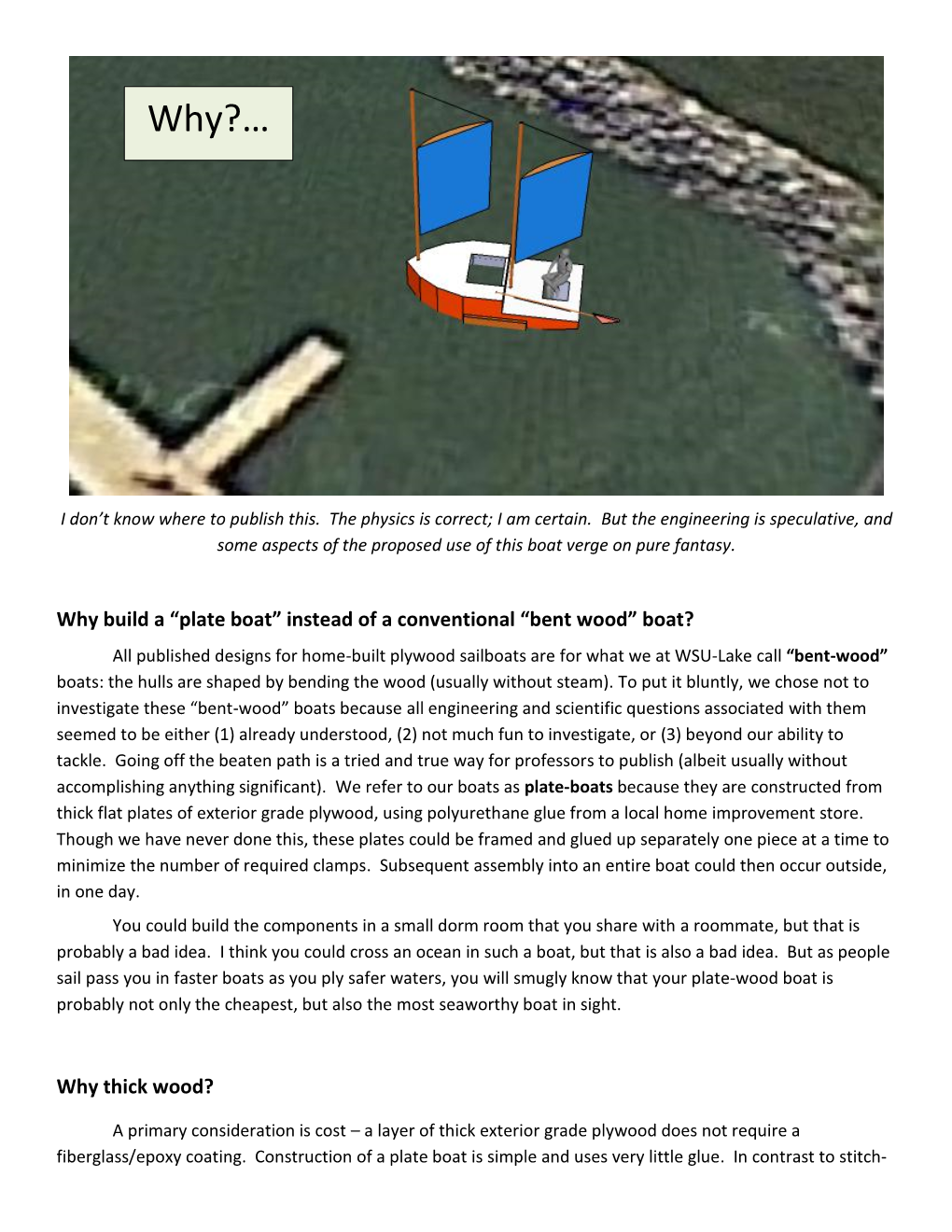
Load more
Recommended publications
-
'Sprats and Minnows'
‘SPRATS AND M INNOWS’ SOME S & S SMALL FRY BY PATRICK MATTHIESEN Last year I touched on the ‘pocket cruiser-racer’ of approximately 30ft LOA which many had considered to be the smallest practicable size for minimal comfort and safety, particularly with the vastly more Spartan early designs. Yet, as has often been pointed out in the past, there is an equation which simply does not work and it is this: Enjoyment + HCF 1 = LOA + Beam + SA x (£+$+E). In fact there are many able mathematicians who would argue the converse and that is that maximum enjoyment experienced when sailing is the LCD 2 of LOA ÷ Cost. Thus, wise sailors have long known that they are faster onto the water, spend less time commissioning and therefore enjoy more sailing closer to the water if their boats are small. The headaches are lessened, equipment costs a fraction of that for larger vessels and most jobs can be executed on a ‘do it yourself’ basis 3 Manhasset Bay O.D. Construction plan Copyright S&S Inc. The very first S & S design #1, The Manhasset Bay O.D. falls into this category. The contract was arranged by Drake Sparkman, Olin and Rod’s future broker partner (the partnership was not formed till the following year) at the Larchmont Y.C. The boat is a daysailor/racer rather than a cruiser, but she was the first of the breed and S & S never lost sight of the impecunious family man who, by buying a pedigree product, might later move on to bigger, and some would say better, things. -
Auction List 2019
Chesapeake Bay Maritime Museum Charity Boat Donation Program 2019 Charity Auction August 31, 2019 See Photos and more info:bitly.com/buyaboat From luxury boats to dinghies, CBMM accepts and sells donated boats all year-round. 213 N. Talbot St., St. Michaels, MD 21663 410-745-4942 [email protected] Inv. # ***BOATS IN THE WATER ARE LISTED SEPARATELY AT THE END*** Trailer TREAD LIGHTLY YAWL. The ultimate pocket cruiser from the design board of John Welsford, similar to the more well known Scamp. Custom built to very nice 5213 Y/U standards and fully rigged and ready. Very good untitled storage trailer included. Untitled, unregistered small craft not intended for motorization. 1978 Cobalt Bowrider 19 with a Replaced 5 litre GM V-8 sterndrive. 2017 USCG 6005 safety inspection sticker. Runs well, electric shift, new upper outdrive, new lower Y/T outdrive, new prop. 9.9 hp Evinrude kicker motor and transom mount. Beautiful Cedar Strip rowing dinghy with sail rig. Would be a fun rowing dinghy for 6016 an adult or sailing dinghy for a kid. N 1980 North American Spirit 21 with titled trailer. Boat is in good overall condition. 6018 Sails and rigging are in good shape. Titled galvanized trailer and Nissan 5 HP Y/T outboard included. Great trailer sailer. 1988 18' Ebbtide Campione Bow Rider. 150 HP Mercury Engine that runs. great 6030 Y/U boat for skiing, tubing or just cruising. Sitting on a nice trailer 1987 Foli Star boat. She is in good overall condition with the expected wear and 6039 Y/T tear for her age and comes with a nice trailer with storage lockers. -
Don Boyko's Bio
Don Boyko's Bio Here is a little bit about myself. I‘ve been involved in sailing for a good portion my adult life, but have always been interested in sailing for as long as I can remember. I remember being fascinated watching the sailboats passing by my Grandparents home on the river north of Detroit, and I guess the seed was planted. Growing up I spent most of me weekends, and all of my summer vacations with my Grandparents. I had an older cousin that bought a 14’ dinghy, and he would take me sailing, then someone gave a buddy of mine an old wooden Lightning and we soon learned to always sail upstream so when the wind died, we wouldn’t have to paddle against the current to get home. Once my wife, and I, got our careers established and we had a few extra bucks, we purchased our first sailboat, a 13’ Chrysler Pirateer. The family had a lot of good times learning how to sail, but soon out grew the Pirateer, and slowly traded our way up to our first C-22. Our first C-22 was a 1980 model, and it opened new adventures for the family. One year I was working in St Louis while the family was back in Kansas City. I discovered the Alton Pool of the Mississippi River north of St Louis and after finding a slip at one of the yacht clubs, I decided to move the boat to St Louis and live on the boat during the week while I was on my assignment. -
From the Masthead
April 2009 Issue 2 Sailorgram Commodore Eric Vasquez 978-521-9017 FROM THE MASTHEAD Vice Commodore Bob Chadwick April 2009 • Eric Vasquez, Commodore 978-373-6106 lthough there are no boats in the water, the Club is very busy behind the scenes.This time Rear Commodore of the year is full of planning, organizing, thinking and re-thinking. In a phrase, we are David W. Hewey A 978-373-6038 “flat-out-busy”. Here, take a look: Secretary To start, I want to thank R/C David Hewey for joining Angela and I to the April 8th.“Mayor’s Gary Gastman 978-462-6533 Social”, held at the North End Boat Club.Attendees were the Harbor Commission, representa- tives of the Coast Guard, our harbormasters, marina owners, and the host club.This is the annu- Treasurer Douglas Cornell al “meet and greet”, and Mayor and AYC Member John Moak led the meeting to talk about cur- 978-474-4323 rent events and to gather feedback from our various community partners. These are the meet- Collector ing minutes: Pamela Mertinooke 978-388-4515 The city would like to have the fireworks for Yankee Homecoming, and need some fundraising to support the event.The fireworks costs around $25k for a 37 minute show.You’ll remember Measurer William R. Gynan last year a fog bank moved in between the light show and us, but as you know, the show must 978-462-1157 go on and it’s slated again for this year. Continued on page 2 Membership Committee Daniel Streeter 978-462-4605 Mooring Committee Gene Piermattei 978-374-7940 House Committee Robert A. -
FJUNCISCO YIBIJU DB Flgljbillbdo, a PORTUGUESE MERCBANT
FJUNCISCO YIBIJU DB FlGlJBIllBDO, A PORTUGUESE MERCBANT·ADVENTURER IN SOUTB EAST ASlA, 1624-1667 VERHANDELINGEN VAN HET KONINKLIJK INSTITUUT VOOR TAAL-, LAND- EN VOLKENKUNDE DEEL 52 C.R.BOXER FRANCISCO VIEIRA DE FIGUEIREDO I A PORTUGUESE MERCHANT-ADVENTURER IN SOUTH EAST ASlA, 1624.-1667 'S·GRA. VEN H AG E - MAR TIN U S NU HOF F - 1967 FOREWORD Twenty-seven years ago, I published in the Boletim Eclesiástico de M acau a short article about Francisco Vieira de Figueiredo and the role of the Portuguese in Macassar and Timor during the period 1640--1668.1 Three years ago, Dr. J. Noorduyn suggested that the article, long since out of print, might be brought to the attention of a wider public through the medium of an English translation in the Bijdragen, the Portuguese text of the supporting documents being added as an appendix. I was naturally flattered by this suggestion; though other commitments have prevented me from carrying out the detailed researches in the archives of Lisbon, Goa, The Hague and Jakarta, which a definitive work on this intriguing character would necessarily involve. Nevertheless, the references to Vieira de Figueiredo which I have been able to gather from published and unpublished sources since 1940, will, I hope, justify the appearance of the present study on the 300th aniversary of the death of its subject. lts publication mayalso, perhaps, stimulate someone with more time at his disposal to write the definitive biography of this Portuguese merchant-adventurer which he undoubtedly deserves. Meanwhile, my special thanks are due to the Board of Directors of the Koninklijk Instituut voor Taal-, Land- en Volkenkunde for affording me the hospitality of the series of the Verhandelingen and to Dr. -
INSANE’ RORC CARIBBEAN 600 See Regatta News on Page 12 TIM WRIGHT / APRIL 2017 CARIBBEAN COMPASS PAGE 2 INGA BEITZ
C A R I B B E A N On-line C MPASS APRIL 2017 NO. 259 The Caribbean’s Monthly Look at Sea & Shore ‘INSANE’ RORC CARIBBEAN 600 See Regatta News on page 12 TIM WRIGHT / WWW.PHOTOACTION.COM APRIL 2017 CARIBBEAN COMPASS PAGE 2 INGA BEITZ ’ The Caribbean’s Monthly Look at Sea & Shore www.caribbeancompass.com APRIL 2017 • NUMBER 259 OFFSHORE PASSAGE OPPORTUNITIES Coral Group Bay Better in Barbuda ................. 30 ANNA LANDRY DEPARTMENTS Info & Updates ......................4 Readers’ Forum .....................38 Business Briefs .......................10 Meridian Passage .................40 Regatta News........................ 12 What’s On My Mind ..............40 Y2A ......................................... 18 Caribbean Market Place .....41 Appreciation! Look Out For… ......................33 Calendar of Events ...............44 Dominica’s Yacht Week ........... 8 The Caribbean Sky ...............34 Classified Ads ....................... 45 Cooking with Cruisers ..........36 Advertisers Index ..................46 Cuba, at Last Getting there ........................ 20 Caribbean Compass is published monthly by Compass Publishing Ltd., The Valley, P.O. Box 727, APRIL 2017 CARIBBEAN COMPASS PAGE 3 SUZANNE WENTLEY Anguilla, British West Indies. Tel: (784) 457-3409, Fax: (784) 457-3410, [email protected], www.caribbeancompass.com Publisher..................................Tom Hopman Art, Design & Production.........Wilfred Dederer [email protected] [email protected] Editor...........................................Sally -
Subject-Index-1-157.Pdf
SUBJECT INDEX ISSUES 1 – 157 Abma, Albert, author: “A Study in Slender,” A B C D E F G H I J K L M N 147:18, O P Q R S T U V W X Y Z Abramson, Tim: on displaying hull A&S Building Systems, Inc.: pre-engineered identification numbers, 61:5 metal buildings, 17:34, 26:18 abrasive discs. See abrasives, diamond; Abaris Training: advanced-composite grinders/polishers, discs for; sandpaper workshops, 47:57, 52:67, 69:125; abrasive pads: Micro-Mesh, 12:60 ultrasonic inspection/survey techniques, abrasives, diamond: Mister Blister, 12:60; 35:42; vocational training program, 20:26 Tech-Lok diamond discs, 25:59 Abbass, D.K. (Kathy): on surveyor Paul Abrasive Technology Inc.: Tech-Lok Coble and development of his Marine diamond discs, 25:59 Survey Seminars, 93:4 ABS. See American Bureau of Shipping Abbey, Howard: profile of, 104:100; Wyn-Mill (ABS) racer/Jim Wynne/Walt Walters, 132:36 ABS Construct: parts generation software, Abbott, Daniela T.H., author: “Olin 8:35 Stephens’s Last Project,” 119:20 ABS plastic: ABS/acrylic coextrusions, ABBRA. See American Boat Builders and 10:34, 11:20; ABS/Rovel coextrusions, Repairers Association 34:59; performance, 10:34. See also Abeking & Rasmussen: Concordia yawl, Royalex 50:32; Michael Peters Yacht Design 44m ABYC. See American Boat and Yacht motoryacht, 66:52; waterjet-powered fast Council (ABYC); ABYC safety standards motoryacht/Michael Peters Yacht Design, ABYC safety standards: battery chargers, 126:38; Vamarie, steel ketch, 68:11 61:128; bilge pumps, 44:26, 57:48; boat Abely Wheeler, aluminum constructed -
Final Sept 09 Soundings
Soundings Newsletter of South Port Sailing Club October 2009 From the Harbourmaster October Work party Month !! HAUL OUT Saturday Calling all Weed Whackers October 24th & Limb trimmers !! Winter Storage Request and Saturday October 3rd. we need volunteers to release forms are enclosed with this month’s assist with cleaning up the weeds along the driveway Soundings. To those members who receive our & fence, as well as around the shed. The balance of newsletter by email only, you will receive the the work party is a general clean up of the grounds, forms via Canada Post. As in the past, the system including some tree trimming in the area of the picnic for paying winter storage and haul out will tables before haul out. As noted in the last issue, we continue in this manner to streamline the billing are attempting to identify several trailers in the area. process. Please calculate your own storage fees If they are not claimed, we will move to them to a place on the property for eventual disposal. Lunch and submit your cheque with the form by October will be provided. If you can assist, please contact 11 to the attention of the Harbourmaster , Wesley Tim Aseltine at [email protected] Arthur. Cheques can be post dated to Oct. 11th. Your boat will not be hauled out if the harbour- master does not receive your form and cheque. CRADLE MOVING DAY The paper work must be completed by ‘all’ boat owners regardless of whether the rental crane is Saturday October 17th. required. 9:00 am. -
Latitude 38 June 2015
VOLUME 456 June 2015 WE GO WHERE THE WIND BLOWS THE YIN AND YANG A lthough Bay Area racers enjoyed ALL PHOTOS LATITUDE / CHRIS a sunny, delightful and quick but mod- EXCEPT AS NOTED erate race to Vallejo on May 2, the race back on May 3 tuned into an ordeal that outside in a tent. The club awarded just had to be endured. Saturday's starts special Great Vallejo Race hats to all the on the Berkeley Circle went off like clock- fi rst-place fi nishers on Saturday. work. After a short leg to a windward After the band quit at midnight, mark, 133 boats were off on a pleasant the ominous shuddering of wind gusts race to Vallejo Yacht Club. dominated the soundtrack of the night, Spinnakers slowly began appearing, a prelude to Sunday's race to San Rafael. and once they blossomed most stayed up all the way to the Mare Island Strait entrance, where a jibe around a mark Forecasts called for 15 knots of was quickly preceded or followed by a breeze all afternoon on Sunday. The douse to 'white' sails. Playing the big, reality was more than twice that, with shifty puffs up the river to the fi nish a persistent overcast, resulting in hypo- thermic crew, busted gear, and even a dismasting. Playing the puffs in Mare Island Strait "Imagine six hours of again required vigilant main and jib riding a bucking bronco trimming. Boats that carried #1 genoas to San Pablo Bay soon changed down to through a car wash." smaller #3 jibs. -
Good Sailing; Good Trailing Day Before in Mainly Light Winds
Kite Just Flies! With clients’ needs taking priority, it took a while before andrew Wolstenholme and Colin Henwood’s shared pocket cruiser was on the water. But making her debut at the English raid, she proved the long wait was worthwhile, writes Kathy Mansfield. With photographs by the author. ometimes there's a Eureka moment, when you realise of Henwood & Dean, decide to build a boat for themselves and something has really worked. For me, it was at the end their families. Such projects tend to fall to the bottom of the Sof July in the Solent, when I was waiting near Newtown list. Andrew had started by thinking about a pocket cruiser, Creek for boats of the first English Raid boats to arrive. I cat ketch rigged, in which they could enjoy family outings suspect that what I saw was the result of good tactics but and also participate in Raids but as he considered the options I was expecting the longer waterline boats to arrive early and the compromises that would have to be made, he ended on and at first couldn't identify the boat that was pounding up with a different set of parameters which seemed to work down towards us, flying along, pushing the spray outwards. It better for what they had in mind. sparkled. I wanted one. Then I realized it had to be Kite , the boat I’d sailed the Good sailinG; Good trailinG day before in mainly light winds. An elegant little day cruiser, The basic concept was a daysailer with a small cabin for she’d proved comfortable and easy to handle and I liked her occasional nights aboard, able to be towed by an ordinary very much. -
Compact Cruisers for Quick Getaways | Cruising World
SAILBOATS HOW TO DESTINATIONS SAILBOATSSite Search HOW TO DESTINATIONS CHARTER GEAR PHOTOS VIDEOS SUBSCRIBE SAILBOATSCHARTER BLOGS PEOPLE CONTESTS NEWS MARKETPLACE CHARTER DIRECTORY 2015GEAR Pocket Cruisers: Compact Cruisers For Quick Getaways PHOTOS ACCORDING TO BOAT OF THE YEAR JUDGE ED SHERMAN, THE JEANNEAU SUN ODYSSEY 349 "HAS COME IN AT SUCH AN EXCEPTIONAL PRICE FOR WHAT YOU GET THAT IT’S REALLY THE BEST VALUE IN THE ENTIRE CONTEST." MEET THE POCKET CRUISER NOMINEES IN VIDEOSCRUISING WORLD'S 2015 BOAT OF THE YEAR COMPETITION. BY Herb McCormick POSTED December 8, 2014 Subscribe 1 Privacy Policy Terms of Use PREVIOUS NEXT Abuse Contact Us FOLLOW US Billy Black EnlargeBilly BlackImage Jeanneau's Sun Odyssey 349 ghosted along well even in light air. Our judges enjoyed plenty of great sails during sea trials, but none better than a screaming reach on the Dragonfly 3200. This year’s group of pocket cruisers, the Salona 33, Dragonfly 3200 and Jeanneau Sun Odyssey 349, while all under 35 feet, delivered big-time thrills under sail. But before launching into the attributes of one of the more enjoyable and spritely classes of BOTY boats in recent memory, let’s briefly examine one of the major trends for 2015: the proliferation of truly interesting yachts under 40 feet that are now available to sailors. Along with this class, another trio of boats from 35 to 37 feet comprised the Midsize Cruiser division. Taken together, they account for almost a third of the year’s 19 new models. It’s been a good while since new-boat buyers had this many solid smaller cruisers from which to choose. -
How to Maintain an F-Boat
How to Maintain An F-Boat Notes taken from the F-Boat Listserver David Paule Editor August, 2004 1 Table of Contents Introduction 15 A note on the organization of this book..... 17 Thanks.... 18 A word of warning! 19 Brief Description of Major Differences 20 Book 2 - Options, Hardware, and Maintenance 22 5200 and Similar Products 22 Anchor Locker Hinge Fasteners 22 Anodized Aluminum Parts 23 Anodized Aluminum Parts – Removing Old Anodizing 24 Antennas 24 Antennas 25 Anti-Seize 25 Art Work 27 Attachments to the Hulls 27 Autopilot 27 Autopilots 30 Awnings 31 Backing Plates 31 Barbeques 32 Barber Haulers 32 2 Barnacles 32 Beam Bolts 32 Beam Core 33 Beam Cracks 33 Beam Hardware 35 Beer Holders 44 Binoculars 45 Birds 45 Blisters 46 Boom Height 46 Bottom Paint 47 Bottom paint - Copper Epoxy 50 Bottom paint - Interlux Micron 66 55 Bow Reinforcements and Bowsprits 58 Bulkhead Damage - F-31 64 Bungees 66 Buying Advice 66 Cap Shroud Adjusters 71 Carpets 72 Centerboard Gaskets - F-24-1 72 Chairs and Cushions 72 Cleaning and Polishing - Gelcoat 74 3 Cleaning and Polishing - Non-Skid 77 Clothing 78 Clutches 79 Cockpit Seat Crazing 80 Collision Damage 80 Coolers 81 Core, Hull 82 Core - Balsa or Other Wood 83 Core – Water Removal 86 Corrosion Control 87 Covering the Boat 88 Daggerboard, Case and Slot 90 Daggerboard Cheek Blocks 97 Deck Hardware to Beams 97 Diagonal Lines Under the Nets and Aft Cabin Hatch Brace 98 Dinghies 99 Docks 100 Documenting Your Boat 101 Dogs 101 Drogues, Series 105 Electrical - AA Battery Chargers 105 Electrical - Batteries