Robot Safety: Overview of Risk Assessment and Reduction
Total Page:16
File Type:pdf, Size:1020Kb
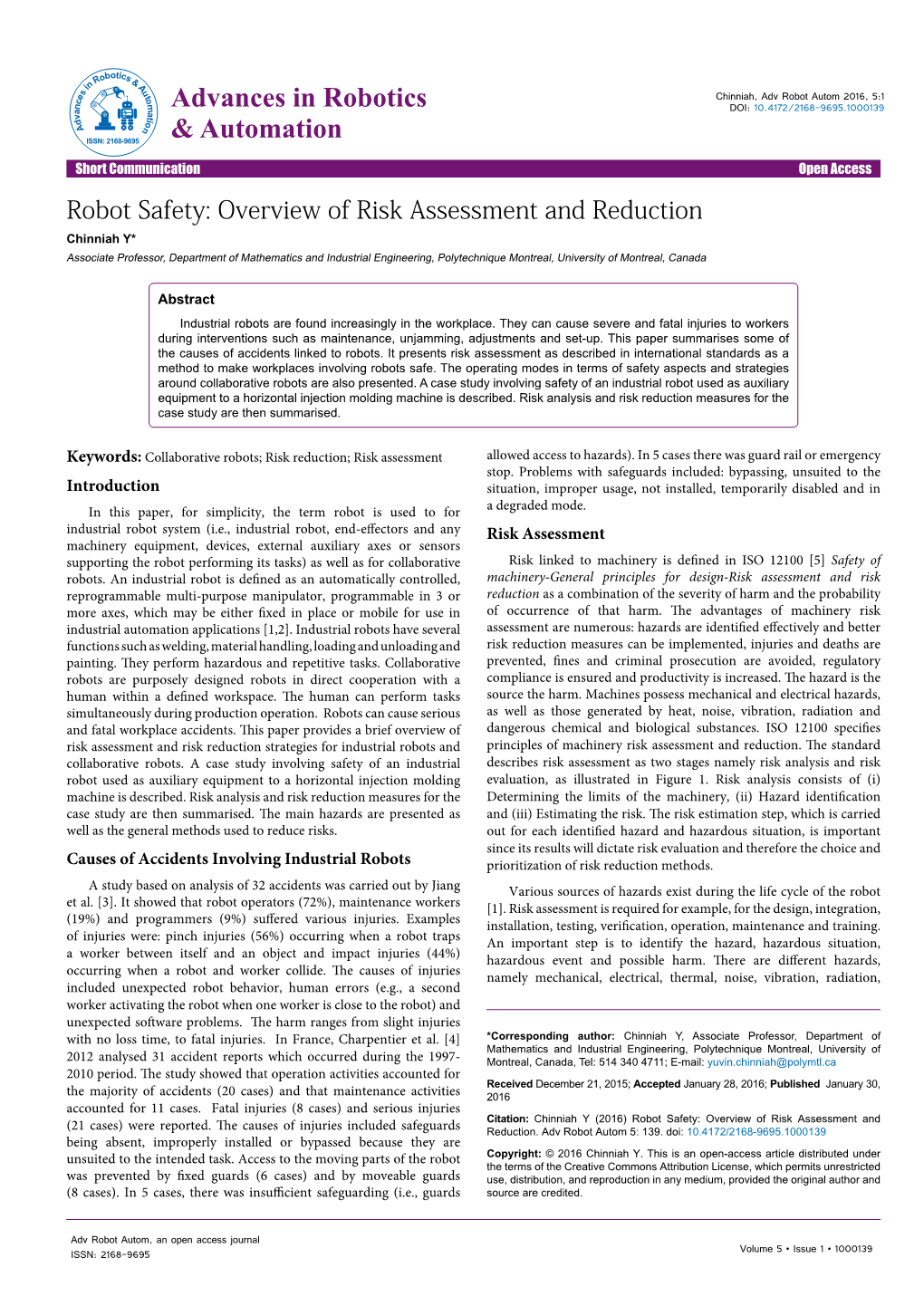
Load more
Recommended publications
-
Validating Safety in Human–Robot Collaboration: Standards and New Perspectives
robotics Article Validating Safety in Human–Robot Collaboration: Standards and New Perspectives Marcello Valori 1,* , Adriano Scibilia 1, Irene Fassi 1 , José Saenz 2 , Roland Behrens 2, Sebastian Herbster 2, Catherine Bidard 3 , Eric Lucet 3 , Alice Magisson 4 , Leendert Schaake 5, Jule Bessler 5,6 , Gerdienke B. Prange-Lasonder 5,7 , Morten Kühnrich 8, Aske B. Lassen 8 and Kurt Nielsen 8 1 Institute of Intelligent Industrial Technologies and Systems for Advanced Manufacturing, National Research Council of Italy, 20133 Milan, Italy; [email protected] (A.S.); [email protected] (I.F.) 2 Fraunhofer IFF, 39106 Magdeburg, Germany; [email protected] (J.S.); [email protected] (R.B.); [email protected] (S.H.) 3 Université Paris-Saclay, CEA List, F-91120 Palaiseau, France; [email protected] (C.B.); [email protected] (E.L.) 4 CEA, CEA Tech Grand Est, F-57075 Metz, France; [email protected] 5 Roessingh Research and Development, 7522 AH Enschede, The Netherlands; [email protected] (L.S.); [email protected] (J.B.); [email protected] (G.B.P.-L.) 6 Department of Biomedical Signals and Systems, University of Twente, 7522 NB Enschede, The Netherlands 7 Department of Biomechanical Engineering, University of Twente, 7522 NB Enschede, The Netherlands 8 Department of Robot Technology, Danish Technological Institute, 5230 Odense, Denmark; [email protected] (M.K.); [email protected] (A.B.L.); [email protected] (K.N.) * Correspondence: [email protected]; Tel.: +39-329-312-0837 Abstract: Human–robot collaboration is currently one of the frontiers of industrial robot implemen- Citation: Valori, M.; Scibilia, A.; tation. -
Chapter 3 – Values in Machine Age
Univ. Prof. Dr. Sarah Spiekermann; “The Human Use of Machine Beings”, Chatper 3, Taylor and Francis, New York, 2015 Chapter 3 – Values in Machine Age Chapter 3 – Values in Machine Age ...............................................................................................1 An Introduction to Values........................................................................................................2 What is a value?...............................................................................................................................2 Intrinsic versus extrinsic values......................................................................................................3 Intrinsic Values in Philosophy and Psychology..............................................................................3 Nonmoral Values versus Moral Values...........................................................................................4 Values versus Virtues.......................................................................................................................4 Necessary Values for Human Growth.............................................................................................5 Ethical Knowledge in Machine Age................................................................................................7 What is Knowledge?......................................................................................................................7 Structuring ethical challenges in IT driven knowledge creation.....................................................8 -
CPS Platform Approach to Industrial Robots
View metadata, citation and similar papers at core.ac.uk brought to you by CORE provided by AIS Electronic Library (AISeL) Association for Information Systems AIS Electronic Library (AISeL) Pacific Asia Conference on Information Systems PACIS 2015 Proceedings (PACIS) 2015 CPS Platform Approach to Industrial Robots: State of the Practice, Potentials, Future Research Directions Martin Mikusz University of Stuttgart, [email protected] Akos Csiszar University of Stuttgart, [email protected] Follow this and additional works at: http://aisel.aisnet.org/pacis2015 Recommended Citation Mikusz, Martin and Csiszar, Akos, "CPS Platform Approach to Industrial Robots: State of the Practice, Potentials, Future Research Directions" (2015). PACIS 2015 Proceedings. 176. http://aisel.aisnet.org/pacis2015/176 This material is brought to you by the Pacific Asia Conference on Information Systems (PACIS) at AIS Electronic Library (AISeL). It has been accepted for inclusion in PACIS 2015 Proceedings by an authorized administrator of AIS Electronic Library (AISeL). For more information, please contact [email protected]. CPS PLATFORM APPROACH TO INDUSTRIAL ROBOTS: STATE OF THE PRACTICE, POTENTIALS, FUTURE RESEARCH DIRECTIONS Martin Mikusz, Graduate School of Excellence for advanced Manufacturing Engineering, GSaME, University of Stuttgart, Germany, [email protected] Akos Csiszar, Graduate School of Excellence for advanced Manufacturing Engineering, GSaME, University of Stuttgart, Germany, [email protected] Abstract Approaches, such as Cloud Robotics, Robot-as-a-Service, merged Internet of Things and robotics, and Cyber-Physical Systems (CPS) in production, show that the industrial robotics domain experiences a paradigm shift that increasingly links robots in real-life factories with virtual reality. -
Implementing Speed and Separation Monitoring in Collaborative Robot Workcells
Robotics and Computer-Integrated Manufacturing 44 (2017) 144–155 Contents lists available at ScienceDirect Robotics and Computer-Integrated Manufacturing journal homepage: www.elsevier.com/locate/rcim Implementing speed and separation monitoring in collaborative robot workcells Jeremy A. Marvel n, Rick Norcross U.S. National Institute of Standards and Technology, 100 Bureau Drive, Stop 8230, Gaithersburg, MD 20899, USA article info abstract Article history: We provide an overview and guidance for the speed and separation monitoring methodology as pre- Received 4 March 2015 sented in the International Organization of Standardization's technical specification 15066 on colla- Received in revised form borative robot safety. Such functionality is provided by external, intelligent observer systems integrated 7 July 2016 into a robotic workcell. The SSM minimum protective distance function equation is discussed in detail, Accepted 1 August 2016 with consideration for the input values, implementation specifications, and performance expectations. We provide analytical analyses and test results of the current equation, discuss considerations for im- Keywords: plementing SSM in human-occupied environments, and provide directions for technological advance- Robot safety ments toward standardization. Speed and separation monitoring Published by Elsevier Ltd. 1. Introduction collaborative workspace, below which a safety-rated, controlled stop is issued. The fourth limits the momentum of a robot such Occupational health and safety organizations rely on national that contact with an operator will not result pain or injury. and international standards to provide guidance for maintaining This report focuses on the third collaborative scenario: “speed safe working environments. For robot workcells, these standards and separation monitoring” (SSM). From ISO/TS 15066, the mini- require the separation of man and machine by means of physical mum protective distance, S, at time t0 is barriers with safeguarded entryways. -
ISO Update Supplement to Isofocus
ISO Update Supplement to ISOfocus July 2021 International Standards in process ISO/CD Road vehicles — Environmental conditions and 16750-4 testing for electrical and electronic equipment An International Standard is the result of an agreement between — Part 4: Climatic loads the member bodies of ISO. A first important step towards an Interna- ISO/CD Road vehicles — Environmental conditions and tional Standard takes the form of a committee draft (CD) - this is cir- 16750-5 testing for electrical and electronic equipment culated for study within an ISO technical committee. When consensus — Part 5: Chemical loads has been reached within the technical committee, the document is TC 23 Tractors and machinery for agriculture sent to the Central Secretariat for processing as a draft International Standard (DIS). The DIS requires approval by at least 75 % of the and forestry member bodies casting a vote. A confirmation vote is subsequently ISO/CD 11471 Agricultural tractors and machinery — Cod- carried out on a final draft International Standard (FDIS), the approval ing of remote hydraulic power services and criteria remaining the same. controls ISO/CD Tractors and machinery for agriculture and 11783-7 forestry — Serial control and communications data network — Part 7: Implement messages application layer ISO/CD Agricultural machinery and tractors — Safety 18497-1 of partially automated, semi-autonomous and autonomous machinery — Part 1: Machine design principles and vocabulary CD registered TC 24 Particle characterization including sieving Period from 01 June to 01 July 2021 ISO/DTS 4807 Reference materials for particle size measure- ment - Specification of requirements These documents are currently under consideration in the technical committee. -
Standards Analysis Ict Sector Luxembourg
STANDARDS ANALYSIS ICT SECTOR LUXEMBOURG Version 8.0 · November 2017 · ISSN 2354-483X 2 WHITE PAPER · DIGITAL TRUST · Version 3.0 · October 2016 FOREWORD Technical standardization and standards play ILNAS carries out different legal missions in the an important role in the support of economy field of ICT. In addition, through the development. They can provide, for example, a "Luxembourg’s policy on ICT technical guide of the best practices for services and standardization 2015-2020", ILNAS product development, governance, quality and commissioned the Economic Interest Grouping assessment guarantee, safety, etc. Nowadays, “Agence pour la Normalisation et l’Économie de almost every professional sector relies on la Connaissance” (ANEC GIE) to strengthen standards to perform its daily activities and the national ICT sector involvement in provide services in an efficient manner. standardization work. Standards remain under a voluntary application scheme, but often they are a real added value ILNAS, with the support of ANEC GIE, has in order to comply with legislation. They can be launched several activities dedicated to considered as a source of benefits in each strengthen and develop the ICT-related sector of the economy, what is particularly true standardization landscape at the national level in the Information and Communication in terms of education and involvement of Technology (ICT) sector, which supports all the stakeholders, such as the creation of a other economic developments. University certificate Smart ICT for Business Innovation in collaboration with the University of The ICT sector has gained more and more Luxembourg. This first development was importance in the society as a whole in the last reinforced in May 2017 by the launch of a decades. -
On Healthcare Robots
ON HEALTHCARE ROBOTS Concepts, definitions, and considerations for healthcare robot governance Eduard Fosch-Villaronga & Hadassah Drukarch eLaw Center for Law and Digital Technologies Leiden University, The Netherlands Author details Dr. Eduard Fosch-Villaronga, Assistant Professor, eLaw Center for Law and Digital Technologies, Leiden University, the Netherlands, [email protected]. Hadassah Drukarch, Research Assistant, eLaw Center for Law and Digital Technologies, Leiden University, the Netherlands, [email protected]. May 2021 2 Disclaimer This report was funded by the LEaDing Fellows Marie Curie COFUND fellowship, a project that has received funding from the European Union's Horizon 2020 research and innovation programme under the Marie Skłodowska-Curie Grant Agreement No. 707404. This report's contents are the authors' sole responsibility and do not necessarily reflect the views of the European Commission. The opinions expressed here are those of the authors only and do not necessarily reflect the authors' organizations. Contents of this publication may be quoted or reproduced, provided that the source of information is acknowledged. Acknowledgments This report was funded by the LEaDing Fellows Marie Curie COFUND fellowship, a project that has received funding from the European Union's Horizon 2020 research and innovation programme under the Marie Skłodowska-Curie Grant Agreement No. 707404. The authors would like to thank Mrs. Aline-Priscilla Messi and Mrs. Rosalie ten Wolde for their help on the first draft of some parts of this report during their student assistantship as part of the Honors College Law at Leiden University during March-Aug 2020. The authors would also like to thank T.J.C. -
ISO 10218-1:2011 B8cbccb118cd/Iso-10218-1-2011
INTERNATIONAL ISO STANDARD 10218-1 Second edition 2011-07-01 Robots and robotic devices — Safety requirements for industrial robots — Part 1: Robots Robots et dispositifs robotiques — Exigences de sécurité pour iTeh STlesA NrobotsDA industrielsRD P —R EVIEW Partie 1: Robots (st andards.iteh.ai) ISO 10218-1:2011 https://standards.iteh.ai/catalog/standards/sist/514dc52b-e620-4f18-bbae- b8cbccb118cd/iso-10218-1-2011 Reference number ISO 10218-1:2011(E) © ISO 2011 ISO 10218-1:2011(E) iTeh STANDARD PREVIEW (standards.iteh.ai) ISO 10218-1:2011 https://standards.iteh.ai/catalog/standards/sist/514dc52b-e620-4f18-bbae- b8cbccb118cd/iso-10218-1-2011 COPYRIGHT PROTECTED DOCUMENT © ISO 2011 All rights reserved. Unless otherwise specified, no part of this publication may be reproduced or utilized in any form or by any means, electronic or mechanical, including photocopying and microfilm, without permission in writing from either ISO at the address below or ISO's member body in the country of the requester. ISO copyright office Case postale 56 • CH-1211 Geneva 20 Tel. + 41 22 749 01 11 Fax + 41 22 749 09 47 E-mail [email protected] Web www.iso.org Published in Switzerland ii © ISO 2011 – All rights reserved ISO 10218-1:2011(E) Contents Page Foreword ............................................................................................................................................................iv Introduction.........................................................................................................................................................v -
Safety System Design in Human-Robot Collaboration Implementation for a Demonstrator Case in Compliance with ISO/TS 15066
DEGREE PROJECT IN MECHANICAL ENGINEERING, SECOND CYCLE, 30 CREDITS STOCKHOLM, SWEDEN 2019 Safety system design in human-robot collaboration Implementation for a demonstrator case in compliance with ISO/TS 15066 CAROLIN SCHAFFERT KTH ROYAL INSTITUTE OF TECHNOLOGY SCHOOL OF INDUSTRIAL ENGINEERING AND MANAGEMENT Safety system design in human-robot collaboration Implementation for a demonstrator case in compliance with ISO/TS 15066 Carolin Schaffert Master of Science Thesis TPRMM 2019 KTH Industrial Engineering and Management Production Engineering SE-100 44 Stockholm 1 Abstract A close collaboration between humans and robots is one approach to achieve flexible production flows and a high degree of automation at the same time. In human-robot collaboration, both entities work alongside each other in a fenceless, shared environment. These workstations combine human flexibility, tactile sense and intelligence with robotic speed, endurance, and accuracy. This leads to improved ergonomic working conditions for the operator, better quality and higher efficiency. However, the widespread adoption of human-robot collaboration is limited by the current safety legislation. Robots are powerful machines and without spatial separation to the operator the risks drastically increase. The technical specification ISO/TS 15066 serves as a guideline for collaborative operations and supplements the international standard ISO 10218 for industrial robots. Because ISO/TS 15066 represents the first draft for a coming standard, companies have to gain knowledge in applying ISO/TS 15066. Currently, the guideline prohibits a collision with the head in transient contact. In this thesis work, a safety system is designed which is in compliance with ISO/TS 15066 and where certified safety technologies are used. -
User Guide KINOVA® Gen3 Ultra Lightweight Robot
User Guide KINOVA® Gen3 Ultra lightweight robot 5 | kinovarobotics.com Contents Introduction............................................................................................................................................................... 6 Welcome.......................................................................................................................................................................6 Intended domains of application........................................................................................................................ 6 About this document...............................................................................................................................................6 Acronyms and abbreviations................................................................................................................................6 Warranty...................................................................................................................................................................... 9 EU Declaration of Incorporation..........................................................................................................................9 FCC Declaration of Comformity.......................................................................................................................... 11 Safety directives and warnings......................................................................................................................... 12 Disclaimer................................................................................................................................................................. -
CEN/WS COVR Safety in Close Human-Robot Interaction: Procedures For
CEN WORKSHOP AGREEMENT Date: 2021 - 06 - 01 CWA XXXXX: 2021 Secretariat: UNI Safety in close human-robot interaction: procedures for validation tests ICS: CCMC will prepare and attach the official title page. CWA XXXX:2021 (E) Contents Page 1 European foreword ............................................................................................................................................ 3 2 Introduction .......................................................................................................................................................... 4 3 1 Scope .......................................................................................................................................................... 5 4 2 Normative references .......................................................................................................................... 5 5 3 Terms and definitions ......................................................................................................................... 6 6 4 Robot categories and general concepts of safety-related processes .................................. 8 7 4.1 Robot categorization ........................................................................................................................... 8 8 4.2 Robots under Machinery Directive ................................................................................................ 9 9 4.2.1 Industrial robots .................................................................................................................................. -
2.7. Iso/Ts 15066 (Iso Tc 184/Sc 2)
POLITECNICO DI TORINO Repository ISTITUZIONALE Human-Robot Collaboration in Automotive Industry Original Human-Robot Collaboration in Automotive Industry / Heydaryan, Sahar. - (2018 Jun 25). Availability: This version is available at: 11583/2710819 since: 2018-07-13T00:39:32Z Publisher: Politecnico di Torino Published DOI:10.6092/polito/porto/2710819 Terms of use: Altro tipo di accesso This article is made available under terms and conditions as specified in the corresponding bibliographic description in the repository Publisher copyright (Article begins on next page) 10 October 2021 Doctoral Dissertation Doctoral Program in Mechanical Engineering (30th Cycle) Human-Robot Collaboration in Automotive Industry Sahar Heydaryan * * * * * * Supervisor Prof. Giovanni Belingardi. Doctoral Examination Committee: Prof. Dario Croccolo, Referee, Università di Bologna Prof. Francesco Caputo, Referee, Università della Campania Prof. Ivan Macuzic, Referee, University of Kragujevac Prof. Micaela Demichela, Referee, Politecnico di Torino Prof. Maria Pia Cavatorta, Referee, Politecnico di Torino Politecnico di Torino 2018 ii This thesis is licensed under a Creative Commons License, Attribution - Noncommercial - NoDerivative Works 4.0 International: see www.creativecommons.org. The text may be reproduced for non-commercial purposes, provided that credit is given to the original author. I hereby declare that, the contents and organisation of this dissertation constitute my own original work and does not compromise in any way the rights of third parties, including those relating to the security of personal data. ………………………………..... Sahar Heydaryan Turin, April 30, 2018 iii Summary Human–Robot Collaboration is a new trend in the field of industrial and service. Application of human-robot-collaboration techniques in automotive industries has many advantages on productivity, production quality and workers’ ergonomic; however, workers’ safety aspects play the vital role during this collaboration.