III-V Metamorphic Materials and Devices for Multijunction Solar
Total Page:16
File Type:pdf, Size:1020Kb
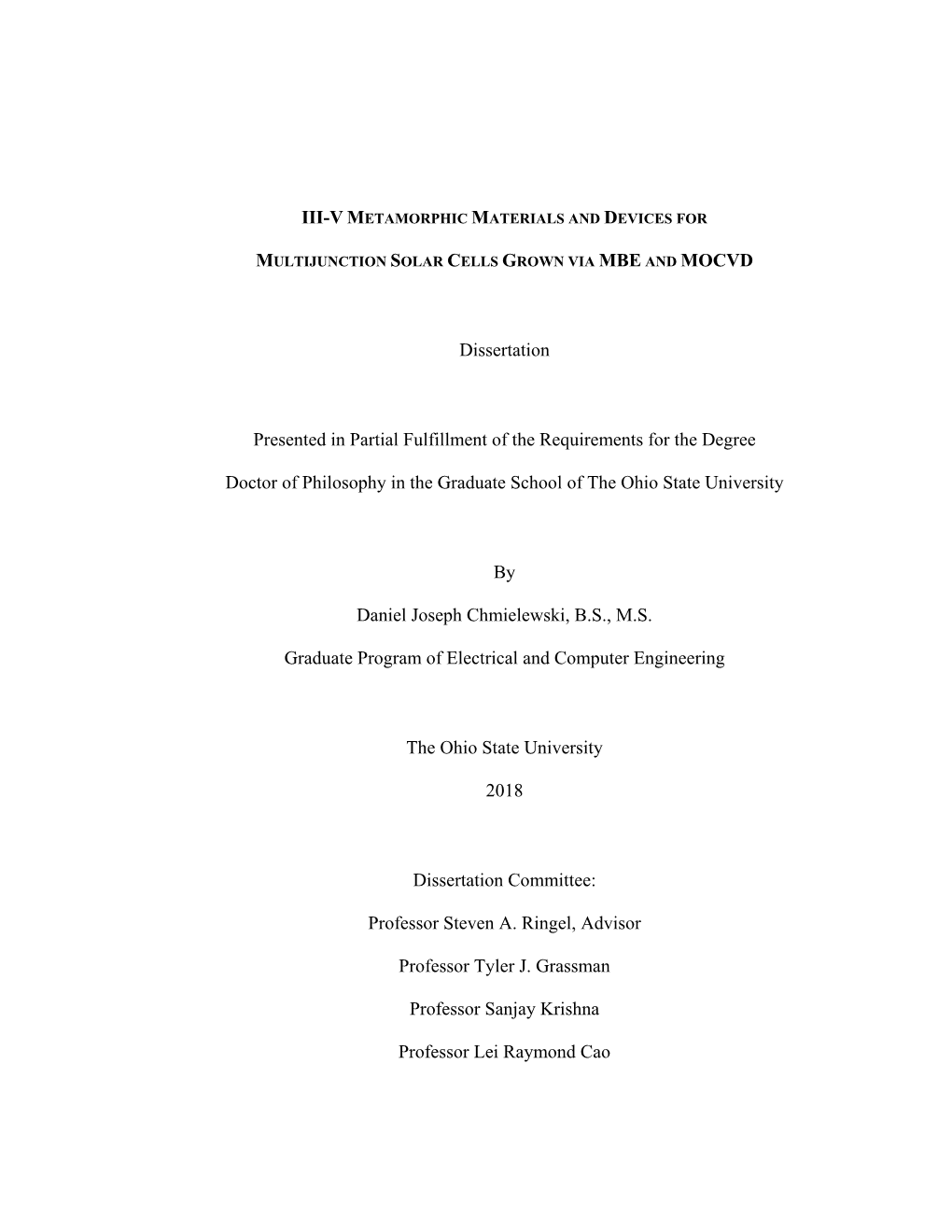
Load more
Recommended publications
-
Residential Provider Compliance Status Report
Respect & DD HCBS Provider Status Legal / Corporate Control of Freedom from Privacy (including Choice of Furnishing & Residency Name Setting Name County Integration Choices Schedule Coercion/ locking door) Roommate Decorating Access to Food Visitors Agreement Current Status Information Source HCBS Setting Type ABEBE, HUNDE OATFIELD CLACKAMAS COMPLIANT NEW SITE / INITIAL FOSTER CARE - REVIEW ADULT ABEBE, YESHIHAREG FARGO MULTNOMAH PENDING INCOMPLETE SURVEY FOSTER CARE - REGULATORY ADULT ONSITE REVIEW ABRAHAM, GEMECHU FOREST GALE WASHINGTON PENDING COMPLIANT NEW SITE / INITIAL FOSTER CARE - REGULATORY REVIEW ADULT ONSITE REVIEW ADAIR, DAVID OAK HILL DOUGLAS PENDING COMPLIANT SURVEY FOSTER CARE - REGULATORY ADULT ONSITE REVIEW ADAIR, DAVID OAK HILL DOUGLAS COMPLIANT COMPLIANT ON-SITE REVIEW FOSTER CARE - 09/29/2016 ADULT ADAMS, SHARON L WHISTLE DESCHUTES PENDING INCOMPLETE SURVEY FOSTER CARE - REGULATORY ADULT ONSITE REVIEW ADULT LEARNING 111TH MULTNOMAH DOES NOT MEET DOES NOT MEET DOES NOT MEET DOES NOT MEET PENDING REMEDIATION SURVEY RESIDENTIAL - SYSTEMS OR INC EXPECTATION EXPECTATION EXPECTATION EXPECTATION REGULATORY ADULT ONSITE REVIEW ADULT LEARNING 111TH MULTNOMAH COMPLIANT COMPLIANT ON-SITE REVIEW RESIDENTIAL - SYSTEMS OR INC 10/18/2016 ADULT ADULT LEARNING 120TH MULTNOMAH DOES NOT MEET DOES NOT MEET PENDING REMEDIATION SURVEY RESIDENTIAL - SYSTEMS OR INC EXPECTATION EXPECTATION REGULATORY ADULT ONSITE REVIEW ADULT LEARNING 120TH MULTNOMAH DOES NOT MEET COMPLIANT REMEDIATION ON-SITE REVIEW RESIDENTIAL - SYSTEMS OR INC EXPECTATION -
Three-Dimensional Metallo-Dielectric Selective Thermal Emitters With
View metadata, citation and similar papers at core.ac.uk brought to you by CORE provided by UPCommons. Portal del coneixement obert de la UPC Manuscript post-print for self-archiving purposes Solar Energy Materials and Solar Cells 134, 22—28 (2015) doi:10.1016/j.solmat.2014.11.017 Three-Dimensional Metallo-Dielectric Selective Thermal Emitters With High-Temperature Stability for Thermophotovoltaic Applications. Moisés Garín a*, David Hernández a, Trifon Trifonov a,b, Ramón Alcubilla a,b a Grup de Recerca en Micro i Nanotecnologies, Departament d’Enginyeria Electrònica, Universitat Politècnica de Catalunya, Jordi Girona 1-3 Mòdul C4, Barcelona 08034, Spain. b Centre de Recerca en Nanoenginyeria, Universitat Politècnica de Catalunya, Pascual i Vilà 15, Barcelona 08028, Spain. * E-mail: [email protected] Keywords: selective thermal emitters, thermophotovoltaics, photonic crystals, macroporous silicon ABSTRACT Selective thermal emitters concentrate most of their spontaneous emission in a spectral band much narrower than a blackbody. When used in a thermophovoltaic energy conversion system, they become key elements defining both its overall system efficiency and output power. Selective emitters' radiation spectra must be designed to match their accompanying photocell's band gap and, simultaneously, withstand high temperatures (above 1000 K) for long operation times. The advent of nanophotonics has allowed the engineering of very selective emitters and absorbers; however, thermal stability remains a challenge since 1 of 22 nanostructures become unstable at temperatures much below the melting point of the used materials. In this paper we explore an hybrid 3D dielectric-metallic structure that combines the higher thermal stability of a monocrystalline 3D Silicon scaffold with the optical properties of a thin Platinum film conformally deposited on top. -
15Th Workshop on Crystalline Silicon Solar Cells and Modules: Materials and Processes
A national laboratory of the U.S. Department of Energy Office of Energy Efficiency & Renewable Energy National Renewable Energy Laboratory Innovation for Our Energy Future th Proceedings 15 Workshop on Crystalline NREL/BK-520-38573 Silicon Solar Cells and Modules: November 2005 Materials and Processes Extended Abstracts and Papers Workshop Chairman/Editor: B.L. Sopori Program Committee: M. Al-Jassim, J. Kalejs, J. Rand, T. Saitoh, R. Sinton, M. Stavola, R. Swanson, T. Tan, E. Weber, J. Werner, and B. Sopori Vail Cascade Resort Vail, Colorado August 7–10, 2005 NREL is operated by Midwest Research Institute ● Battelle Contract No. DE-AC36-99-GO10337 th Proceedings 15 Workshop on Crystalline NREL/BK-520-38573 Silicon Solar Cells and Modules: November 2005 Materials and Processes Extended Abstracts and Papers Workshop Chairman/Editor: B.L. Sopori Program Committee: M. Al-Jassim, J. Kalejs, J. Rand, T. Saitoh, R. Sinton, M. Stavola, R. Swanson, T. Tan, E. Weber, J. Werner, and B. Sopori Vail Cascade Resort Vail, Colorado August 7–10, 2005 Prepared under Task No. WO97G400 National Renewable Energy Laboratory 1617 Cole Boulevard, Golden, Colorado 80401-3393 303-275-3000 • www.nrel.gov Operated for the U.S. Department of Energy Office of Energy Efficiency and Renewable Energy by Midwest Research Institute • Battelle Contract No. DE-AC36-99-GO10337 NOTICE This report was prepared as an account of work sponsored by an agency of the United States government. Neither the United States government nor any agency thereof, nor any of their employees, makes any warranty, express or implied, or assumes any legal liability or responsibility for the accuracy, completeness, or usefulness of any information, apparatus, product, or `process disclosed, or represents that its use would not infringe privately owned rights. -
Perovskite Solar Cells with Large Area CVD-Graphene for Tandem
View metadata, citation and similar papers at core.ac.uk brought to you by CORE provided by HZB Repository 1 Perovskite Solar Cells with Large-Area CVD-Graphene 2 for Tandem Solar Cells 3 Felix Lang *, Marc A. Gluba, Steve Albrecht, Jörg Rappich, Lars Korte, Bernd Rech, and 4 Norbert H. Nickel 5 Helmholtz-Zentrum Berlin für Materialien und Energie GmbH, Institut für Silizium 6 Photovoltaik, Kekuléstr. 5, 12489 Berlin, Germany. 7 8 ABSTRACT: Perovskite solar cells with transparent contacts may be used to compensate 9 thermalization losses of silicon solar cells in tandem devices. This offers a way to outreach 10 stagnating efficiencies. However, perovskite top cells in tandem structures require contact layers 11 with high electrical conductivity and optimal transparency. We address this challenge by 12 implementing large area graphene grown by chemical vapor deposition as highly transparent 13 electrode in perovskite solar cells leading to identical charge collection efficiencies. Electrical 14 performance of solar cells with a graphene-based contact reached those of solar cells with 15 standard gold contacts. The optical transmission by far exceeds that of reference devices and 16 amounts to 64.3 % below the perovskite band gap. Finally, we demonstrate a four terminal 17 tandem device combining a high band gap graphene-contacted perovskite top solar cell 18 (Eg=1.6 eV) with an amorphous/crystalline silicon bottom solar cell (Eg=1.12 eV). 19 1 1 TOC GRAPHIC. 2 3 4 Hybrid perovskite methylammonium lead iodide (CH3NH3PbI3) attracts ever-growing interest 5 for use as a photovoltaic absorber.1 Only recently, Jeon et al. -
Neutron Transmutation Doping of Silicon at Research Reactors
Silicon at Research Silicon Reactors Neutron Transmutation Doping of Doping Neutron Transmutation IAEA-TECDOC-1681 IAEA-TECDOC-1681 n NEUTRON TRANSMUTATION DOPING OF SILICON AT RESEARCH REACTORS 130010–2 VIENNA ISSN 1011–4289 ISBN 978–92–0– INTERNATIONAL ATOMIC AGENCY ENERGY ATOMIC INTERNATIONAL Neutron Transmutation Doping of Silicon at Research Reactors The following States are Members of the International Atomic Energy Agency: AFGHANISTAN GHANA NIGERIA ALBANIA GREECE NORWAY ALGERIA GUATEMALA OMAN ANGOLA HAITI PAKISTAN ARGENTINA HOLY SEE PALAU ARMENIA HONDURAS PANAMA AUSTRALIA HUNGARY PAPUA NEW GUINEA AUSTRIA ICELAND PARAGUAY AZERBAIJAN INDIA PERU BAHRAIN INDONESIA PHILIPPINES BANGLADESH IRAN, ISLAMIC REPUBLIC OF POLAND BELARUS IRAQ PORTUGAL IRELAND BELGIUM QATAR ISRAEL BELIZE REPUBLIC OF MOLDOVA BENIN ITALY ROMANIA BOLIVIA JAMAICA RUSSIAN FEDERATION BOSNIA AND HERZEGOVINA JAPAN SAUDI ARABIA BOTSWANA JORDAN SENEGAL BRAZIL KAZAKHSTAN SERBIA BULGARIA KENYA SEYCHELLES BURKINA FASO KOREA, REPUBLIC OF SIERRA LEONE BURUNDI KUWAIT SINGAPORE CAMBODIA KYRGYZSTAN CAMEROON LAO PEOPLES DEMOCRATIC SLOVAKIA CANADA REPUBLIC SLOVENIA CENTRAL AFRICAN LATVIA SOUTH AFRICA REPUBLIC LEBANON SPAIN CHAD LESOTHO SRI LANKA CHILE LIBERIA SUDAN CHINA LIBYA SWEDEN COLOMBIA LIECHTENSTEIN SWITZERLAND CONGO LITHUANIA SYRIAN ARAB REPUBLIC COSTA RICA LUXEMBOURG TAJIKISTAN CÔTE DIVOIRE MADAGASCAR THAILAND CROATIA MALAWI THE FORMER YUGOSLAV CUBA MALAYSIA REPUBLIC OF MACEDONIA CYPRUS MALI TUNISIA CZECH REPUBLIC MALTA TURKEY DEMOCRATIC REPUBLIC MARSHALL ISLANDS UGANDA -
Thin Crystalline Silicon Solar Cells Based on Epitaxial Films Grown at 165°C by RF-PECVD
CORE Metadata, citation and similar papers at core.ac.uk Provided by HAL-Polytechnique Thin crystalline silicon solar cells based on epitaxial films grown at 165 C by RF-PECVD Romain Cariou, Martin Labrune, Pere Roca I Cabarrocas To cite this version: Romain Cariou, Martin Labrune, Pere Roca I Cabarrocas. Thin crystalline silicon solar cells based on epitaxial films grown at 165 C by RF-PECVD. Solar Energy Materials and Solar Cells, Elsevier, 2011, 95 (8), pp.2260-2263. <10.1016/j.solmat.2011.03.038>. <hal-00749873v3> HAL Id: hal-00749873 https://hal-polytechnique.archives-ouvertes.fr/hal-00749873v3 Submitted on 14 May 2013 HAL is a multi-disciplinary open access L'archive ouverte pluridisciplinaire HAL, est archive for the deposit and dissemination of sci- destin´eeau d´ep^otet `ala diffusion de documents entific research documents, whether they are pub- scientifiques de niveau recherche, publi´esou non, lished or not. The documents may come from ´emanant des ´etablissements d'enseignement et de teaching and research institutions in France or recherche fran¸caisou ´etrangers,des laboratoires abroad, or from public or private research centers. publics ou priv´es. Thin crystalline silicon solar cells based on epitaxial films grown at 165°C by RF-PECVD Romain Carioua),*, Martin Labrunea),b), P. Roca i Cabarrocasa) aLPICM-CNRS, Ecole Polytechnique, 91128 Palaiseau, France bTOTAL S.A., Gas & Power, R&D Division, Tour La Fayette, 2 Place des Vosges, La Défense 6, 92 400 Courbevoie, France Keywords Low temperature, Epitaxy; PECVD; Si thin film; Solar cell Abstract We report on heterojunction solar cells whose thin intrinsic crystalline absorber layer has been obtained by plasma enhanced chemical vapor deposition at 165°C on highly doped p-type (100) crystalline silicon substrates. -
Metal Assisted Synthesis of Single Crystalline Silicon Nanowires At
dicine e & N om a n n a o t N e f c o h Md Asgar et al., J Nanomed Nanotechnol 2014, 5:4 l n Journal of a o n l o r g u DOI: 10.4172/2157-7439.1000221 y o J ISSN: 2157-7439 Nanomedicine & Nanotechnology Research Article Open Access Metal Assisted Synthesis of Single Crystalline Silicon Nanowires at Room Temperature for Photovoltaic Application Md Asgar A1, Hasan M2, Md Huq F3* and Zahid H Mahmood4 1Department of Electronics and Communication Engineering, Jatiya Kabi Kazi Nazrul Islam University, Trishal, Mymensingh, Bangladesh 2Department of Electrical and Electronic Engineering, Shahjalal University of Science and Technology, Kumargaon, Sylhet-3114, Bangladesh 3Department of Nuclear Engineering, University of Dhaka, Dhaka 1000, Bangladesh 4Department of Applied Physics Electronics and Communication Engineering, University of Dhaka, Dhaka-1000, Bangladesh Abstract Synthesis of single crystalline silicon nanowires (SiNWs) array at room temperature by metal assisted chemical etching and its optical absorption measurements have been reported in this article. It has been confirmed that, SiNWs were formed uniformly on p-type silicon substrate by electroless deposition of Cu and Ag nanoparticles followed by wet chemical etching in (Hydrogen Fluoride) HF based Fe(NO3)3 solution. Synthesized SiNW structures were analyzed and investigated by Scanning Electron Microscopy (SEM) and Ultraviolet-Visible (UV-VIS) spectrophotometer. Formation of SiNWs is evident from the SEM images and morphology of the structures depends upon the concentration of chemical solution and etching time. The synthesized SiNWs have shown strong broadband optical absorption exhibited from UV- spectroscopy. More than 82% absorption of incident radiation is found for Cu treated samples and a maximum of 83% absorption of incident radiation is measured for Ag synthesized samples which is considerably enhanced than that of silicon substrate as they absorbed maximum of 43% of incoming radiation only. -
Modeling Techniques for Multijunction Solar Cells Meghan N
NUSOD 2018 Modeling Techniques for Multijunction Solar Cells Meghan N. Beattie Karin Hinzer Matthew M. Wilkins SUNLAB, Centre for Research in SUNLAB, Centre for Research in SUNLAB, Centre for Research in Photonics Photonics Photonics University of Ottawa University of Ottawa University of Ottawa Ottawa, Canada Ottawa, Canada Ottawa, Canada [email protected] Christopher E. Valdivia SUNLAB, Centre for Research in Photonics University of Ottawa Ottawa, Canada Abstract—Multi-junction solar cell efficiencies far exceed density of defects at the interface [4]. Many of these defects those attainable with silicon photovoltaics. Recently, this propagate towards the surface, resulting in threading technology has been applied to photonic power converters with dislocations that inhibit minority carrier collection [3] In this conversion efficiencies higher than 65%. These devices operate research, we are investigating the use of a voided germanium well in part because of luminescent coupling that occurs in the interface layer to intercept dislocations before they reach the multijunction device. We present modeling results to explain surface, enabling epitaxial growth of high quality Ge, IV how this boosts device efficiencies by approximately 70 mV per (e.g. SiGeSn), and III-V (e.g. InGaAs, InGaP) junction in GaAs devices. Luminescent coupling also increases semiconductors on Si substrates. efficiency in devices with four more junctions, however, the high cost of materials remains a barrier to their widespread By modelling multijunction solar cell designs on Si use. Substantial cost reduction could be achieved by replacing substrates, we investigate the impact of threading the germanium substrate with a less expensive alternative: dislocations on device performance. With highly doped Si, silicon. -
Thin Film Cdte Photovoltaics and the U.S. Energy Transition in 2020
Thin Film CdTe Photovoltaics and the U.S. Energy Transition in 2020 QESST Engineering Research Center Arizona State University Massachusetts Institute of Technology Clark A. Miller, Ian Marius Peters, Shivam Zaveri TABLE OF CONTENTS Executive Summary .............................................................................................. 9 I - The Place of Solar Energy in a Low-Carbon Energy Transition ...................... 12 A - The Contribution of Photovoltaic Solar Energy to the Energy Transition .. 14 B - Transition Scenarios .................................................................................. 16 I.B.1 - Decarbonizing California ................................................................... 16 I.B.2 - 100% Renewables in Australia ......................................................... 17 II - PV Performance ............................................................................................. 20 A - Technology Roadmap ................................................................................. 21 II.A.1 - Efficiency ........................................................................................... 22 II.A.2 - Module Cost ...................................................................................... 27 II.A.3 - Levelized Cost of Energy (LCOE) ....................................................... 29 II.A.4 - Energy Payback Time ........................................................................ 32 B - Hot and Humid Climates ........................................................................... -
Crystalline-Silicon Solar Cells for the 21St Century
May 1999 • NREL/CP-590-26513 Crystalline-Silicon Solar Cells for the 21st Century Y.S. Tsuo, T.H. Wang, and T.F. Ciszek Presented at the Electrochemical Society Annual Meeting Seattle, Washington May 3, 1999 National Renewable Energy Laboratory 1617 Cole Boulevard Golden, Colorado 80401-3393 NREL is a U.S. Department of Energy Laboratory Operated by Midwest Research Institute ••• Battelle ••• Bechtel Contract No. DE-AC36-98-GO10337 NOTICE This report was prepared as an account of work sponsored by an agency of the United States government. Neither the United States government nor any agency thereof, nor any of their employees, makes any warranty, express or implied, or assumes any legal liability or responsibility for the accuracy, completeness, or usefulness of any information, apparatus, product, or process disclosed, or represents that its use would not infringe privately owned rights. Reference herein to any specific commercial product, process, or service by trade name, trademark, manufacturer, or otherwise does not necessarily constitute or imply its endorsement, recommendation, or favoring by the United States government or any agency thereof. The views and opinions of authors expressed herein do not necessarily state or reflect those of the United States government or any agency thereof. Available to DOE and DOE contractors from: Office of Scientific and Technical Information (OSTI) P.O. Box 62 Oak Ridge, TN 37831 Prices available by calling 423-576-8401 Available to the public from: National Technical Information Service (NTIS) U.S. Department of Commerce 5285 Port Royal Road Springfield, VA 22161 703-605-6000 or 800-553-6847 or DOE Information Bridge http://www.doe.gov/bridge/home.html Printed on paper containing at least 50% wastepaper, including 20% postconsumer waste CRYSTALLINE-SILICON SOLAR CELLS FOR THE 21ST CENTURY Y.S. -
Efficient Er/O Doped Silicon Light-Emitting Diodes at Communication Wavelength by Deep Cooling
Efficient Er/O Doped Silicon Light-Emitting Diodes at Communication Wavelength by Deep Cooling Huimin Wen1,#, Jiajing He1,#, Jin Hong2,#, Fangyu Yue2* & Yaping Dan1* 1University of Michigan-Shanghai Jiao Tong University Joint Institute, Shanghai Jiao Tong University, Shanghai, 200240, China. 2Key Laboratory of Polar Materials and Devices, Ministry of Education, East China Normal University, Shanghai, 200241, China. #These authors contributed equally * To whom correspondence should be addressed: [email protected], [email protected] Abstract A silicon light source at communication wavelength is the bottleneck for developing monolithically integrated silicon photonics. Doping silicon with erbium ions was believed to be one of the most promising approaches but suffers from the aggregation of erbium ions that are efficient non-radiative centers, formed during the standard rapid thermal treatment. Here, we apply a deep cooling process following the high- temperature annealing to suppress the aggregation of erbium ions by flushing with Helium gas cooled in liquid nitrogen. The resultant light emitting efficiency is increased to a record 14% at room temperature, two orders of magnitude higher than the sample treated by the standard rapid thermal annealing. The deep-cooling-processed Si samples were further made into light-emitting diodes. Bright electroluminescence with a spectral peak at 1.54 µm from the silicon-based diodes was also observed at room temperature. With these results, it is promising to develop efficient silicon lasers at communication wavelength for the monolithically integrated silicon photonics. The monolithic integration of fiber optics with complementary metal-oxide- semiconductor (CMOS) integrated circuits will significantly speed up the computing and data transmission of current communication networks.1-3 This technology requires efficient silicon-based lasers at communication wavelengths.4, 5 Unfortunately, silicon is an indirect bandgap semiconductor and cannot emit light at communication wavelengths. -
A New Strategy of Bi-Alkali Metal Doping to Design Boron Phosphide Nanocages of High Nonlinear Optical Response with Better Thermodynamic Stability
A New Strategy of bi-Alkali Metal Doping to Design Boron Phosphide Nanocages of High Nonlinear Optical Response with Better Thermodynamic Stability Rimsha Baloach University of Education Khurshid Ayub University of Education Tariq Mahmood University of Education Anila Asif University of Education Sobia Tabassum University of Education Mazhar Amjad Gilani ( [email protected] ) University of Education Original Research Full Papers Keywords: Boron phosphide (B12P12), Bi-alkali metal doping, Nonlinear optical response (NLO), Density functional theory Posted Date: February 11th, 2021 DOI: https://doi.org/10.21203/rs.3.rs-207373/v1 License: This work is licensed under a Creative Commons Attribution 4.0 International License. Read Full License Version of Record: A version of this preprint was published at Journal of Inorganic and Organometallic Polymers and Materials on April 16th, 2021. See the published version at https://doi.org/10.1007/s10904-021-02000-6. A New Strategy of bi-Alkali Metal Doping to Design Boron Phosphide Nanocages of High Nonlinear Optical Response with Better Thermodynamic Stability ABSTRACT: Nonlinear optical materials possess high rank in fields of optics owing to their impacts, utilization and extended applications in industrial sector. Therefore, design of molecular systems with high nonlinear optical response along with high thermodynamic stability is a dire need of this era. Hence, the present study involves investigation of bi-alkali metal doped boron phosphide nanocages M2@B12P12 (M=Li, Na, K) in search of stable nonlinear optical materials. The investigation includes execution of geometrical and opto-electronic properties of complexes by means of density functional theory (DFT) computations. Bi-doped alkali metal atoms introduce excess of electrons in the host B12P12 nanocage.