(12) Patent Application Publication (10) Pub. No.: US 2010/0129587 A1 Terauchi (43) Pub
Total Page:16
File Type:pdf, Size:1020Kb
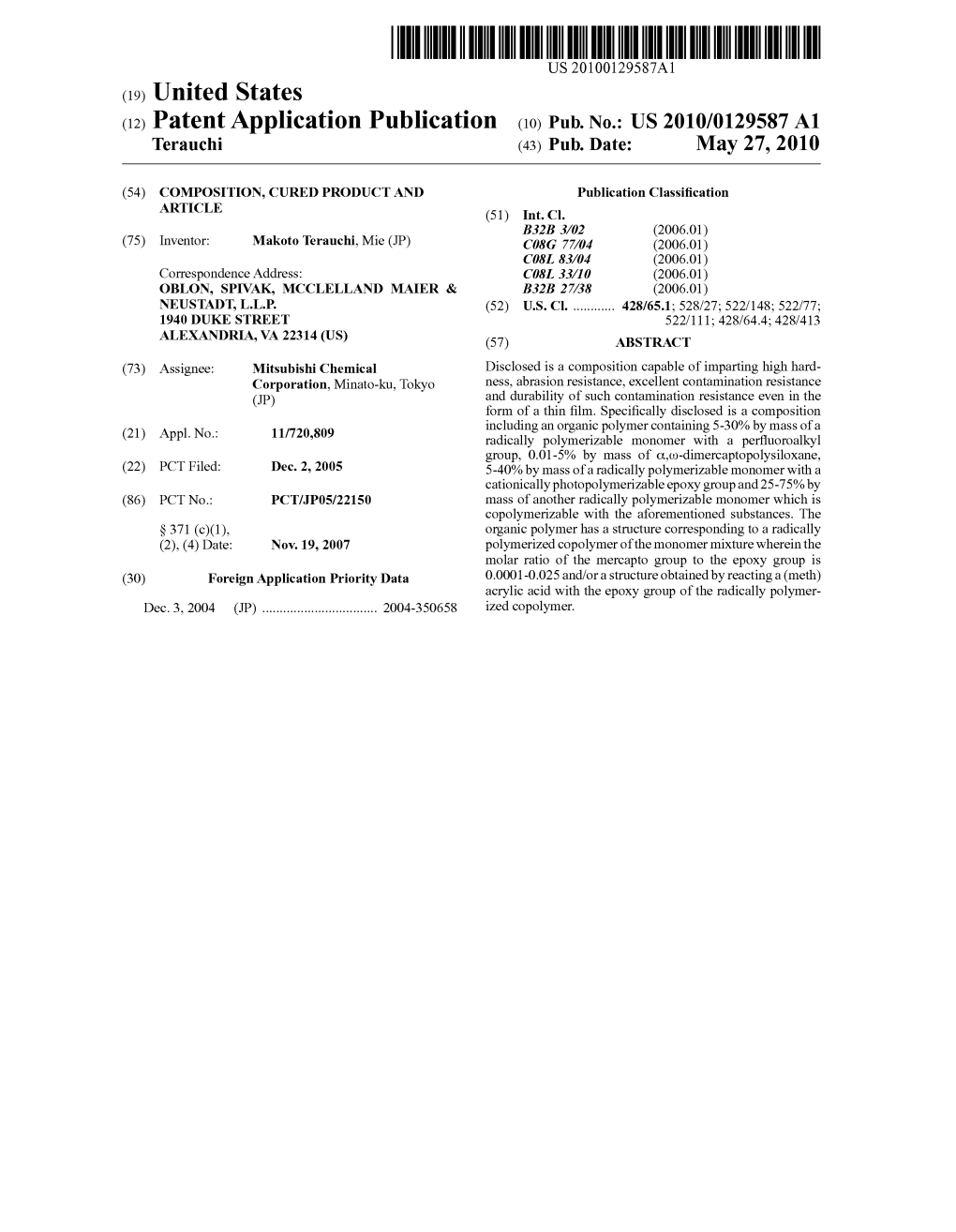
Load more
Recommended publications
-
Department of Materials Science U a L
A N N Department of Materials Science U A L R E P O R Glass and Ceramics T 2 0 1 5 Preface In June 2015 we could welcome our new colleague Prof. Kyle G. Webber heading the func- tional ceramics department. Together with two research fellows from his DFG funded Emmy- Noether-Group he started his research activities in the field of ferroelectric ceramics. After transfer of unique experimental facilities from TU Darmstadt to FAU Erlangen his experimental equipment is ready for work. In the glass department (Prof. Dominique de Ligny) research centers on a better understanding of light interaction with glass as well as response to external stress. Laser glass interaction is ex- plored for new functionalization of glass by surface texturing. The disordered structure of glass imposes the development of specific instrumentation as vibrational spectroscopy. A new setup coupling Raman and Brillouin spectroscopy as well as a calorimeter allows new and unique pro- spective ways. In the biomaterials department (Prof. Stephan E. Wolf), the DFG funded Emmy-Noether- Research Group on biomimetic materials started the research activities after completing the refur- nishment of the laboratories. Work is focused on identifying the process-structure-property rela- tionships in biominerals and subsequent in vitro mimesis by biomimetic crystallization at ambient conditions. Initial results were published in Nature Communications (see publications). Work of the research group on cellular ceramics (Dr. Tobias Fey) is centered on microstruc- ture characterisation applying X-ray microtomography and testing of the mechanical and thermal properties of cellular ceramics. Massive strain amplification lattice structures were investigated by experimental and theoretical approaches. -
Sol-Gel 1 Sol-Gel
Sol-gel 1 Sol-gel In materials science, the sol-gel process is a method for producing solid materials from small molecules. The method is used for the fabrication of metal oxides, especially the oxides of silicon and titanium. The process involves conversion of monomers into a colloidal solution (sol) that acts as the precursor for an integrated network (or gel) of either discrete particles or network polymers. Typical precursors are metal alkoxides. Stages in the process In this chemical procedure, the 'sol' (or solution) gradually evolves towards the formation of a gel-like diphasic system containing both a liquid phase and solid phase whose morphologies range from discrete particles to continuous polymer networks. In the case of the colloid, the volume fraction of particles (or particle density) may be so low that a significant amount of fluid may need to be removed initially for the gel-like properties to be recognized. This can be accomplished in any number of ways. The simplest method is to allow time for sedimentation to occur, and then pour off the remaining liquid. Centrifugation can also be used to accelerate the process of phase Schematic representation of the different stages separation. and routes of the sol-gel technology. Removal of the remaining liquid (solvent) phase requires a drying process, which is typically accompanied by a significant amount of shrinkage and densification. The rate at which the solvent can be removed is ultimately determined by the distribution of porosity in the gel. The ultimate microstructure of the final component will clearly be strongly influenced by changes imposed upon the structural template during this phase of processing. -
Contents I Programme 3
Contents I Programme 3 II Talks 17 III Posters 93 Index 139 1 2 Part I Programme 3 16.00 Sunday, 17 March Uli Buchenau Opening Chairman: Giulio Monaco 16.15 FromFrancesco in-silico Sciortino intuitions to experimental realizations with limited-valence 16.35DNA-made nanoparticles Philipp Maass 16.55Non-equilibrium phase transitions in driven Brownian motion HeterogeneousFelix Lehmkühler local order in soft matter systems studied by X-ray cross 17.15correlation methods Roberta Angelini 17.30Phase behaviour and rheology of multi-responsive soft microgels Lara Frenzel Anomalous Dynamics of Concentrated Silica-PNIPAm Nanogels 17.45 - 18.15 Coffee Break 4 Chairman: Walter Kob 18.15 Aleksandar Matic 18.35Structure and dynamics of ionic liquids and other highly concentrated electrolytes Stefano Mossa 18.55The fate of an ionic liquid confined in a nanopore Luca Leuzzi 19.15Learning Transmission Matrices in Complex and Random Media Charlotte Petersen 19.30Anomalous transport in soft percolating host structures InfluenceDmitriy Sokolov of deposition temperature and impurities on the refractive indices of thin films of methanol and ethanol 20.15 21.15 Dinner Poster session 5 Monday, 18 March Chairman: Uli Buchenau Morning 8.30 HowMiguel universal Angel Ramos are "universal" anomalous properties of glasses at low tempera- 8.50tures? Multi-scaleRoberto Piazza relaxation in aging gels: from localized plastic events to system- 9.10spanning "quakes" Magdaleno Medina-Noyola 9.30Interference between the glass, gel, and gas-liquid transitions Federico Zontone 9:45Short-time dynamics of confined colloids probed by high-energy coherent X-rays Raffaele Pastore 10.00Influence of wall heterogeneity on polymer nano-sandwiches MeasuringMarco Leonetti intensity correlation length in the bulk of a strongly scattering material 10.15 - 10.45 Coffee Break 6 Chairman: Josep Lluis Tamarit 10.45 Walter Kob 11.05On the structure of liquids: More order than expected ABeatrice microscopic Ruta picture of the atomic motion during polyamorphism in an ultra- 11.25viscous liquid Tristan A. -
The Role of Local Structure in Dynamical Arrest
Physics Reports 560 (2015) 1–75 Contents lists available at ScienceDirect Physics Reports journal homepage: www.elsevier.com/locate/physrep The role of local structure in dynamical arrest C. Patrick Royall a,b,c,∗, Stephen R. Williams d a HH Wills Physics Laboratory, Tyndall Avenue, Bristol, BS8 1TL, UK b School of Chemistry, University of Bristol, Cantock Close, Bristol, BS8 1TS, UK c Centre for Nanoscience and Quantum Information, Tyndall Avenue, Bristol, BS8 1FD, UK d Research School of Chemistry, The Australian National University, Canberra, ACT 0200, Australia article info a b s t r a c t Article history: Amorphous solids, or glasses, are distinguished from crystalline solids by their lack of long- Accepted 17 November 2014 range structural order. At the level of two-body structural correlations, glassformers show Available online 4 December 2014 no qualitative change upon vitrifying from a supercooled liquid. Nonetheless the dynamical editor: Randall Kamien properties of a glass are so much slower that it appears to take on the properties of a solid. While many theories of the glass transition focus on dynamical quantities, a solid's Keywords: resistance to flow is often viewed as a consequence of its structure. Here we address the Geometric frustration viewpoint that this remains the case for a glass. Recent developments using higher-order Locally favoured structures Model glassforming systems measures show a clear emergence of structure upon dynamical arrest in a variety of glass formers and offer the tantalising hope of a structural mechanism for arrest. However a rigorous fundamental identification of such a causal link between structure and arrest remains elusive. -
Undergraduate Research
UNDERGRADUATE RESEARCH SUMMER POSTER SESSION ABSTRACT BOOK Wednesday, July 31, 2019 Interdisciplinary Life Sciences Building Lobby Morning Session 10:00 AM – 12:00 PM Afternoon Session 3:00 PM – 5:00 PM LAUNCH UNDERGRADUATE RESEARCH LAUNCH Undergraduate Research Summer Poster Session Wednesday, July 31, 2019 Interdisciplinary Life Sciences Building Lobby Morning Session 10:00 AM – 12:00 PM Featured Summer Programs: 1. Aggie Research Program 2. Aggie STEM 3. Astronomical Research and Instrumentation (Physics & Astronomy REU) 4. CARTEEH 5. Chemistry REU 6. Cyclotron REU 7. Energy and Propulsion REU 8. Engineering Undergraduate Summer Research Grant (USRG) Program 9. Halliburton Engineering Global Program 10. IIT Kanpur/TAMU Exchange Program 11. Metrology and Non-Destructive Inspection REU 12. TTI Safe-D Afternoon Session 3:00 PM – 5:00 PM Featured Summer Programs: 1. Aggie Creative Collective 2. Atmospheric Science in the Gulf Coast Region (ATMO REU) 3. Biochemistry REU 4. Biomechanical Environments Laboratory (BMEL) Undergraduate Research Program 5. College of Architecture SURE 6. College of Medicine Summer Undergraduate Research Program 7. Costa Rica REU 8. Glasscock Summer Scholars 9. Observing the Ocean REU 10. Ocean and Coastal Research Experiences for Undergraduates (OCEANUS) REU 11. SURE EnMed 12. Summer Undergraduate Research Program in Genetics and Genomics 13. U.S. Department of Agriculture Water Quality REU Table of Contents Morning Session (10:00 AM – 12:00 PM) Poster 1. Jesse Martinez Page 2 Reaching Higher Blocking Temperatures for Single-Molecule Magnets using Borolide Capping Ligands Poster 2. Andrew Brown Page 2 Morphological and Electronic Properties of Diacetylene-thiol Assemblies on Au(111) Surfaces Poster 3. -
View of Titanium Zirconium (Tizr) Alloys for Use in Endosseous Dental Implants
Anuradha Tiwari et al, Int. Journal of Pharmaceutical Sciences and Medicine (IJPSM), Vol.4 Issue. 7, July- 2019, pg. 1-21 ISSN: 2519-9889 Impact Factor: 3.426 GEL LOADED DENTAL IMPLANT: A DEMIURGIC DRUG DELIVERY SYSTEM FOR TREATMENT OF GINGIVITIS Anuradha Tiwari*; Deepak Kumar Gupta@; Raju Choukse; Sourabh Jain; Rakesh Patel; Karunakar Shukla DR. APJ ABDUL KALAM UNIVERSITY, BYPASS ROAD, ARANDIA VILLAGE, POST JHALARIA, INDORE (M.P) – 452016 @ [email protected], Tel- +918827666607 ABSTRACT- The main objective of the project was to develop a dental implant for the patients suffering from oral gingivitis caused by bacterial infection, trauma etc. Person suffering from Gingivitis has chance to miss the medication during travel. For optimization of formula for the gel six batches were taken in which different amount of drug and polymer were added and observation were recorded. Six batches of gel were prepared by changing the polymer ratio. Six batches of gel were prepared by changing the polymer ratio. Three batches consist of carbopol whereas three batches consist of chitosan. Triclosan was added in all gel was subjected to in-vitro characterization it was observed that the in case batches containing chitosan, the gel formed by hazy and it contain come particulate matter also whereas the gel formed in case of carbopol were clear. Formulation f1 and f2 were less viscous and gel did not formed completely whereas formulation f4, f5, and f6, the gel formed was also less viscous as well as hazy. This could be due to the incorporation of chitosan in f4, f5, and f6 formulation which derived from chitin and it may not imbibe large amount of water to result in formulation of efficient gel. -
Feasibility Studies for Encapsulated Cell Bioaugmentation Of
Feasibility Studies for Encapsulated Cell Bioaugmentation of Contaminated Aquifers by Peyman Moslemy Department of Chemical Engineering McGill University, Montreal January 2002 A thesis submitted to the Faculty of Graduate Studies and Research in partial fulfillment of the requirements of the degree of Doctor of Philosophy © Peyman Moslemy 2002 National Library Bibliothèque nationale 1+1 of Canada du Canada Acquisitions and Acquisitions et Bibliographie Services services bibliographiques 395 Wellington Street 395, rue Wellington Ottawa ON K1A ON4 Ottawa ON K1 A ON4 canada canada The author bas granted a non L'auteur a accordé une licence non exclusive licence allowing the exclusive permettant à la National Library ofCanada to Bibliothèque nationale du Canada de reproduce, loan, distribute or sell reproduire, prêter, distribuer ou copies ofthis thesis in microform, vendre des copies de cette thèse sous paper or electronic formats. la forme de microfiche/film, de reproduction sur papier ou sur format électronique. The. author retains ownership ofthe L'auteur conselVe la propriété du copyright in this thesis. Neither the droit d'auteur qui protège cette thèse. thesis nor substantial extracts from it Ni la thèse ni des extraits substantiels may be printed or otherwise de celle-ci ne doivent être imprimés reproduced without the author's ou autrement reproduits sans son pemnsslOn. autorisation. 0-612-78740-0 Canada Preface The manuscript-based thesis option was chosen according to the following thesis preparation guideline given by the Faculty of Graduate Studies and Research: As an alternative to the traditional thesis format, the dissertation can consist of a collection ofpapers ofwhich the student is an author or co-author. -
From Molecular Architecture and Electrostatic Interactions to Underwater Adherence of Hydrogels Francisco Javier Cedano Serrano
From molecular architecture and electrostatic interactions to underwater adherence of hydrogels Francisco Javier Cedano Serrano To cite this version: Francisco Javier Cedano Serrano. From molecular architecture and electrostatic interactions to underwater adherence of hydrogels. Polymers. Sorbonne Université, 2019. English. NNT : 2019SORUS056. tel-02968194 HAL Id: tel-02968194 https://tel.archives-ouvertes.fr/tel-02968194 Submitted on 15 Oct 2020 HAL is a multi-disciplinary open access L’archive ouverte pluridisciplinaire HAL, est archive for the deposit and dissemination of sci- destinée au dépôt et à la diffusion de documents entific research documents, whether they are pub- scientifiques de niveau recherche, publiés ou non, lished or not. The documents may come from émanant des établissements d’enseignement et de teaching and research institutions in France or recherche français ou étrangers, des laboratoires abroad, or from public or private research centers. publics ou privés. Sorbonne Université ED 397 : Physique et Chimie des Matériaux Laboratoire Sciences et Ingénierie de la Matière Molle (SIMM) – ESPCI Paris From molecular architecture and electrostatic interactions to underwater adherence of hydrogels Par Francisco J. CEDANO-SERRANO Thèse de doctorat de Chimie et Physico-chimie des Polymères Dirigée par Yvette TRAN, Dominique HOURDET et Costantino CRETON Présentée et soutenue publiquement le 13/05/2019 Devant un jury composé de : RESTAGNO, Frédéric Chargé de recherche CNRS. Université Paris-Saclay. Rapporteurs GEOGHEGAN, Mark Professeur. University of Sheffield. DEL CAMPO BÉCARES, Aránzazu Professeur. Saarland University. Examinatrices LINDNER, Anke Professeur. Université Paris Diderot. CRETON, Costantino Directeur de recherche CNRS. ESPCI Paris. Directeur de thèse HOURDET, Dominique Professeur. Sorbonne Université. ESPCI Paris. Co-directeurs de thèse TRAN, Yvette Maître de Conférences. -
Redalyc.Indications and Restorative Techniques for Glass Ionomer Cement
RSBO Revista Sul-Brasileira de Odontologia ISSN: 1806-7727 [email protected] Universidade da Região de Joinville Brasil Piola Rizzante, Fabio Antonio; Schlögel Cunali, Rafael; Soares Bombonatti, Juliana Fraga; Correr, Gisele Maria; Castiglia Gonzaga, Carla; Yoshio Furuse, Adilson Indications and restorative techniques for glass ionomer cement RSBO Revista Sul-Brasileira de Odontologia, vol. 12, núm. 1, enero-marzo, 2015, pp. 79- 87 Universidade da Região de Joinville Joinville, Brasil Available in: http://www.redalyc.org/articulo.oa?id=153040039010 How to cite Complete issue Scientific Information System More information about this article Network of Scientific Journals from Latin America, the Caribbean, Spain and Portugal Journal's homepage in redalyc.org Non-profit academic project, developed under the open access initiative ISSN: Electronic version: 1984-5685 RSBO. 2015 Jan-Mar;12(1):79-87 Literature Review Article Indications and restorative techniques for glass ionomer cement Fabio Antonio Piola Rizzante1 Rafael Schlögel Cunali2 Juliana Fraga Soares Bombonatti1 Gisele Maria Correr1 Carla Castiglia Gonzaga2 Adilson Yoshio Furuse1 Corresponding author: Adilson Yoshio Furuse Departamento de Dentística, Endodontia e Materiais Odontológicos Faculdade de Odontologia de Bauru, Universidade de São Paulo E-mail: [email protected] 1 Department of Operative Dentistry, Endodontics and Dental Materials, Bauru School of Dentistry – Bauru – SP – Brazil. 2 Graduate Program in Dentistry, Positivo University – Curitiba – PR – Brazil. Received for publication: October 20, 2014. Accepted for publication: November 24, 2014. Abstract Keywords: glass ionomer cements; Introduction: Due to its chemical, mechanical and biological biocompatible properties, the glass ionomer cements (GIC) consist in one of the materials; dental most versatile direct restorative materials, with many potential restoration, permanent. -
View Article: Root Caries in the Geriatricpopulation: Epidemiology, Etiology, Diagnosis, Treatment Planning and Modalities of Treatment
AN INVESTIGATION OF EFFECTS OF NOVEL POLYMERIC STRUCTURES ON PHYSICAL PROPERTIES OF CONVENTIONAL GLASS-IONOMER CEMENTS THESIS Presented in Partial Fulfillment of the Requirements for the Degree Master of Science in the Graduate School of The Ohio State University By Alireza Moshaverinia, DDS ***** The Ohio State University 2009 Dissertation Committee: Dr. Scott R. Schricker, Adviser Dr. William A. Brantley Approved by Dr. William M. Johnston Dr. Dr Sarandeep S. Huja ____________________ Adviser Dentistry Graduate Program Copyright by Alireza Moshaverinia 2009 ABSTRACT Glass-ionomer cements were first introduced to dentistry in late 1960’s. They have proven to be useful in various areas of dental science, such as restorative dentistry. As aqueous polyelectrolyte systems, glass-ionomer cements have unique properties such as adhesion to moist tooth structure without any pretreatment, prolonged fluoride release which inhibits recurrent caries, acceptable aesthetics and biocompatibility, making these materials popular and desirable for restorative dentistry. However, they have some deficiencies such as poor mechanical properties and water sensitivity. Recently, there have been significant changes and modifications in the formulations of the acid and basic parts of the glass-ionomers, leading to enhanced mechanical and handling properties of the material. The overall objective of this study was the modification of the glass- ionomer cement composition in order to enhance their mechanical and handling properties. N-vinylpyrrolidone (NVP) and N-vinylcaprolactam (NVC) were incorporated into glass-ionomer polymeric structure and the effects on mechanical and surface properties of the resulting cements were investigated. The effects of these novel formulations on mechanical and handling properties of glass-ionomer cements were studied. -
Klucel™ Hydroxypropylcellulose
Klucel™ hydroxypropylcellulose Physical and chemical properties 1 2 Table of Contents 1. Introduction ................................4 4.3.6 Viscosity Stability of Solutions 14 2. Chemistry ..................................4 4.3.6.1 Hydrolysis and Oxidation 14 3. Grades and Viscosity Types . .6 4. Physical Properties . .6 4.3.6.2 Biological Stability ......15 4.1 Moisture Absorption ......................7 4.3.7 Preservatives ...............15 4.2 Dispersion and Dissolution . .7 4.3.8 Surface and Interfacial Tension 15 4.2.1 In Water. 7 4.2.2 In Organic Liquids. 8 4.3.9 Organic Solvent Solution .....15 4.3 Properties of Solutions. .9 4.3.9.1 Effect of Concentration 4.3.1 Aqueous Solutions. 9 and Viscosity Type. .... 15 4.3.1.1 Effect of Concentration and 4.3.9.2 Viscosity and Precipitation Viscosity Type. 9 Temperature ...........15 4.3.1.2 Rheology. 10 4.3.10 Recommended Defoamers. 16 4.3.2 Effect of Temperature 4.4 Melt Rheology ....................16 on Viscosity ........................10 5. Applications .........................17 4.3.3 Cloud Point 5.1 Tablet Binding. 17 (Precipitation Temperature) ..........10 5.2 Modified-release Matrix Former . 18 4.3.3.1 Cloud Point Versus 5.3 Hot-melt Extrusion for Controlled- Molecular Weight . 10 release Applications ...............18 4.3.3.2 Effect of pH on Cloud Point. 11 5.4 Continuous Granulation . 19 4.3.4 Polymer Hydration ..................11 5.5 Film Coatings .....................19 4.3.4.1 Effect of pH on Hydration ........11 6. Packaging, Regulatory Status, 4.3.4.2 Effect of Ionic Strengthon Toxicology, Safety. 20 Hydration ......................12 6.1 Packaging and Shipping ...........20 4. -
Modification of Float Glass Surfaces by Ion Exchange
Modification of Float Glass Surfaces by Ion Exchange Linnaeus University Dissertations No 89/2012 MODIFICATION OF FLOAT GLASS SURFACES BY ION EXCHANGE STEFAN KARLSSON LINNAEUS UNIVERSITY PRESS MODIFICATION OF FLOAT GLASS SURFACES BY ION EXCHANGE Doctoral dissertation, School of School of Engineering, Linnaeus University 2012 ISBN: 978-91-86983-62-8 Printed by: Ineko AB, Kållered ABSTRACT Karlsson, Stefan, (2012). Modification of Float Glass Surfaces by Ion Exchange. Linnaeus University Dissertations No 89/2012. ISBN: 978-91-86983-62-8. Written in English. Glass is a common material in each person’s life, e.g. drinking vessels, windows, displays, insulation and optical fibres. By modifying the glass surface it is possible to change the performance of the entire glass object, generally known as Surface Engineering. Ion exchange is a convenient technique to modify the glass surface composition and its properties, e.g. optical, mechanical, electrical and chemical properties, without ruining the surface finish of the glass. This thesis reports the findings of two different research tasks; characterisation of the single-side ion exchange process and the novel properties induced. The characterisation of the ion exchange process was mainly performed by utilising a novel analytical equipment: the Surface Ablation Cell (SAC), allowing continuous removal of the flat glass surface by controlled isotropic dissolution. SAC-AAS has provided concentration vs. depth profiles of float glass ion exchanged with K+, Cu+, Rb+ and Cs+. In addition, SEM-EDX has provided concentration vs. depth profiles of Ag+ ion exchanged samples and validation of a copper concentration vs. depth profile. From the concentration vs. depth profiles, the effective diffusion coefficients and activation energies of the ion exchange processes have been calculated.