Nextsun Energy, Llc Safety and Health Program Manual
Total Page:16
File Type:pdf, Size:1020Kb
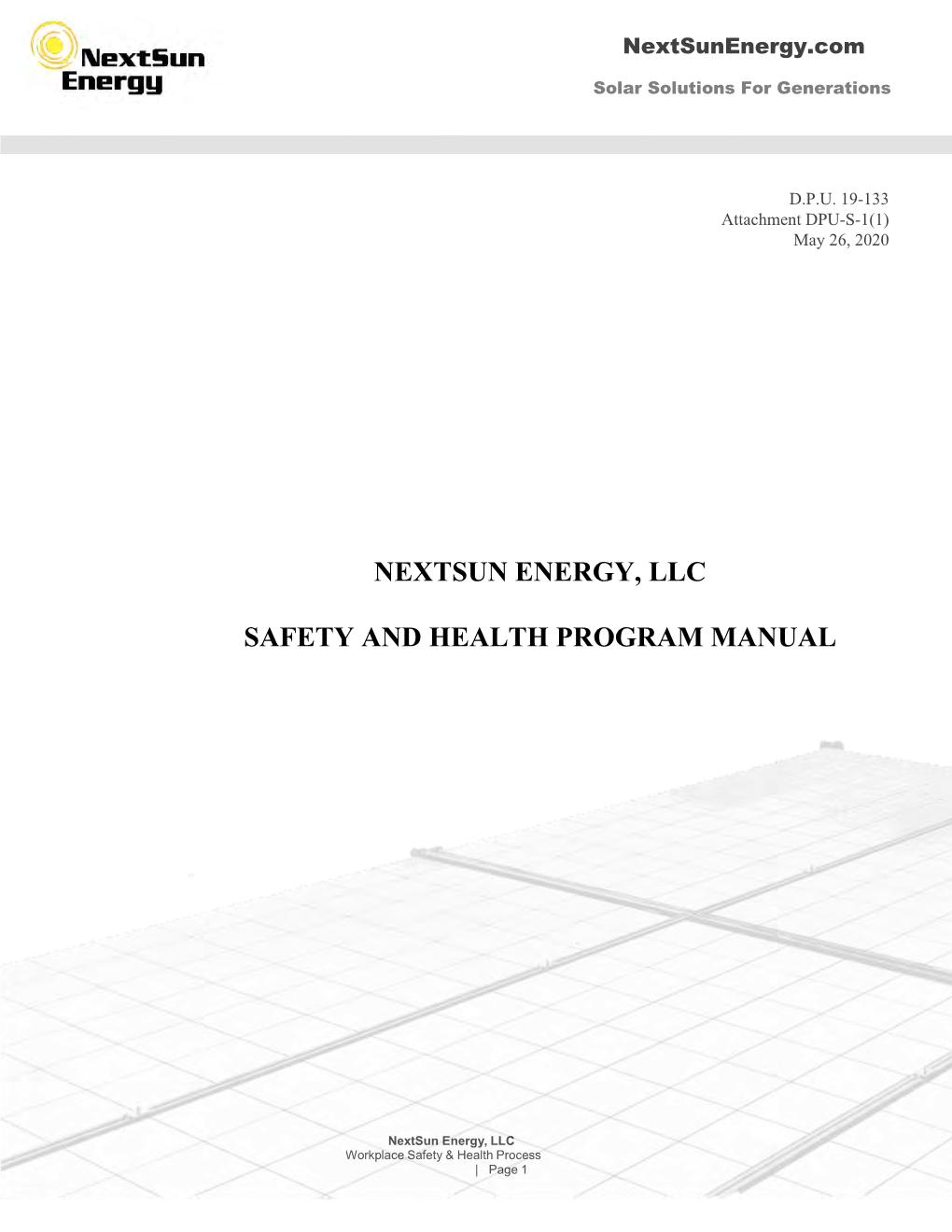
Load more
Recommended publications
-
Guidelines for Human Exposure Assessment Risk Assessment Forum
EPA/100/B-19/001 October 2019 www.epa.gov/risk Guidelines for Human Exposure Assessment Risk Assessment Forum EPA/100/B-19/001 October 2019 Guidelines for Human Exposure Assessment Risk Assessment Forum U.S. Environmental Protection Agency DISCLAIMER This document has been reviewed in accordance with U.S. Environmental Protection Agency (EPA) policy. Mention of trade names or commercial products does not constitute endorsement or recommendation for use. Preferred citation: U.S. EPA (U.S. Environmental Protection Agency). (2019). Guidelines for Human Exposure Assessment. (EPA/100/B-19/001). Washington, D.C.: Risk Assessment Forum, U.S. EPA. Page | ii TABLE OF CONTENTS DISCLAIMER ..................................................................................................................................... ii LIST OF TABLES.............................................................................................................................. vii LIST OF FIGURES ........................................................................................................................... viii LIST OF BOXES ................................................................................................................................ ix ABBREVIATIONS AND ACRONYMS .............................................................................................. x PREFACE ........................................................................................................................................... xi AUTHORS, CONTRIBUTORS AND -
Safety Manual
Eastern Elevator Safety and Health Manual January 2017 Page 1 of 125 SAFETY AND HEALTH MANUAL Index by Section Number Safety Policy ................................................................................................................. …4 Section 1: General Health and Safety Policies ............................................................. …5 Section 2: Hazard Communication ................................................................................ ..13 Section 3: Personal Protective Equipment (PPE) ......................................................... ..18 Section 4: Emergency Action Plan ................................................................................ ..31 Section 5: Fall Protection .............................................................................................. ..34 Section 6: Ladder Safety ............................................................................................... ..38 Section 7: Bloodborne Pathogens ................................................................................ ..42 Section 8: Motor Vehicle / Fleet Safety ......................................................................... ..47 Section 9: Hearing Conservation .................................................................................. ..50 Section 10: Lockout / Tagout ........................................................................................ ..53 Section 11: Fire Prevention .......................................................................................... -
A PRACTICAL GUIDE for USE of REAL TIME DETECTION SYSTEMS for WORKER PROTECTION and COMPLIANCE with OCCUPATIONAL EXPOSURE LIMITS May 2019
A PRACTICAL GUIDE FOR USE OF REAL TIME DETECTION SYSTEMS FOR WORKER PROTECTION AND COMPLIANCE WITH OCCUPATIONAL EXPOSURE LIMITS May 2019 WHITE PAPER May 2019 A PRACTICAL GUIDE FOR USE OF REAL TIME DETECTION SYSTEMS FOR WORKER PROTECTION AND COMPLIANCE WITH OCCUPATIONAL EXPOSURE LIMITS Prepared by: Energy Facility Contractor’s Group (EFCOG) Industrial Hygiene and Safety Task Group and Members of the American Industrial Hygiene Association (AIHA) Exposure Assessment Strategies Group Dina Siegel1, David Abrams 2, John Hill3, Steven Jahn2, Phil Smith2, Kayla Thomas4 1 Los Alamos National Laboratory 2 AIHA Exposure Assessment Strategies Committee 3 Savannah River Site 4 Kansas City National Security Campus A PRACTICAL GUIDE FOR USE OF REAL TIME DETECTION SYSTEMS FOR WORKER PROTECTION AND COMPLIANCE WITH OCCUPATIONAL EXPOSURE LIMITS May 2019 Table of Contents 1.0 Executive Summary 2.0 Introduction 3.0 Discussion 3.1 Occupational Exposure Assessment 3.2 Regulatory Compliance 3.3 Occupational Exposure Limits 3.4 Traditional Use of Real Time Detection Systems 3.5 Use and Limitations of Real Time Detection Systems 3.6 Use of Real Time Detection Systems for Compliance 3.7 Documentation/Reporting of Real Time Detection Systems Results 3.8 Peak Exposures Data Interpretations 3.9 Conclusions 4.0 Matrices 5.0 References 6.0 Attachments Page | 2 A PRACTICAL GUIDE FOR USE OF REAL TIME DETECTION SYSTEMS FOR WORKER PROTECTION AND COMPLIANCE WITH OCCUPATIONAL EXPOSURE LIMITS May 2019 1.0 Executive Summary This white paper presents practical guidance for field industrial hygiene personnel in the use and application of real time detection systems (RTDS) for exposure monitoring. -
Supplementary File 2: Assessment of Quality and Bias
Supplementary File 2: Assessment of quality and bias In preparing the tool, it was not possible to identify a dominant factor for which studies should be controlled for, instead recognising several key variables. Comparability was therefore scored against a single criterion of ‘effectively controlling for relevant factors’, meaning a maximum of eight points, rather than nine, were available. Where a nested cohort or matched case group was identified within an interventional study, it was agreed that the quality of the study as applied to impact of ETS would be appraised, and not the main interventional study outcomes. This acknowledged that high quality trials not relevant to the impact of ETS exposure could contain poor quality cohorts that were appropriate for inclusion, or vice versa. A point was awarded for satisfactory response on each question, indicated by a tick in the relevant table. Cohort Outcome Measures Domain and outcomes Point Representativeness of the exposed cohort A Truly representative of the paediatric population undergoing surgery B Somewhat representative of the paediatric population undergoing surgery C Selected subgroup of the population undergoing surgery D No description of the cohort selection process Selection of the non-exposed cohort A Drawn from the same community as the exposed cohort B Drawn from a different source C No description of the derivation of the non-exposed cohort Ascertainment of exposure A Secure record (e.g. surgical record, biological test) B Structured interview C Written self-report of self-completed questionnaire D No description Demonstration that outcome of interest was not present at start of the study A Yes B No Comparability of cohorts on the basis of the design or analysis A Study controls for reasonable factors (e.g. -
Exposure Assessment Concepts
This work is licensed under a Creative Commons Attribution-NonCommercial-ShareAlike License. Your use of this material constitutes acceptance of that license and the conditions of use of materials on this site. Copyright 2006, The Johns Hopkins University, Patrick Breysse, and Peter S. J. Lees. All rights reserved. Use of these materials permitted only in accordance with license rights granted. Materials provided “AS IS”; no representations or warranties provided. User assumes all responsibility for use, and all liability related thereto, and must independently review all materials for accuracy and efficacy. May contain materials owned by others. User is responsible for obtaining permissions for use from third parties as needed. Exposure Assessment Concepts Patrick N. Breysse, PhD, CIH Peter S.J. Lees, PhD, CIH Johns Hopkins University Section A Introduction Origin of Hygiene Hygeia was the Greek goddess of health Rene Dubos wrote: “For the worshippers of Hygeia, health is … a positive attribute to which men are entitled if they govern their lives wisely” Prevention is key 4 Exposure—Definition Contact between the outer boundary of the human body (skin, nose, lungs, GI tract) and a contaminant Requires the simultaneous presence of a contaminant and the contact between the person and that medium Quantified by concentration of contaminant and time and frequency of contact 5 Route of Exposure Inhalation Ingestion Dermal Direct injection Inhalation is most common in workplace—but not in general environment Moving towards concept of total exposure 6 Exposure Assessment Magnitude – Concentration in media (ppm, f/cc) Duration – Minutes, hours, days, working life, lifetime Frequency – Daily, weekly, seasonally 7 Types of Air Sampling: Time Source: U.S. -
Community Exposure Assessment (Excluding Health
(excluding health Community Exposure Assessment care providers) Physical distance >2 Duration of interaction1 Ventilation3 Source control and PPE Risk assessment metres maintained2 Case and contact are both wearing masks (cloth or medical); OR Case is wearing both a mask (cloth or Low risk medical) and a face shield4 regardless of PPE worn by (self-monitor)5 <15 minutes (except No Regardless of contact; OR Contact is wearing both a mask and eye for very brief ventilation protection regardless of PPE worn by case interactions such as High risk passing by someone) Either case or contact is not wearing a mask (self-isolate)6 Regardless of Low risk Yes Regardless of PPE worn by either case or contact ventilation (self-monitor) Case and contact are both wearing masks (cloth or medical); OR Case is wearing both a mask (cloth or Low risk medical) and a face shield regardless of PPE worn (self-monitor) Well by contact; OR Contact is wearing both a mask and ventilated eye protection regardless of PPE worn by case No High risk Either case or contact is not wearing a mask (self-isolate) Poorly High risk Regardless of PPE worn by either case or contact ventilated (self-isolate) 15 minutes – 1 hour Well Low risk Regardless of PPE worn by either case or contact ventilated (self-monitor) Case and contact are both wearing masks (cloth or medical); OR Case is wearing both a mask (cloth or Low risk Yes medical) and a face shield regardless of PPE worn (self-monitor) Poorly by contact; OR Contact is wearing both a mask and ventilated eye protection regardless of PPE worn by case High risk Either case or contact is not wearing a mask (self-isolate) COVID-19 Info-Line 905-688-8248 press 7 Toll-free: 1-888-505-6074 niagararegion.ca/COVID19 Created December 2020. -
VHA Dir 7702, Industrial Hygiene Exposure Assessment Program
Department of Veterans Affairs VHA DIRECTIVE 7702 Veterans Health Administration Transmittal Sheet Washington, DC 20420 April 29, 2016 INDUSTRIAL HYGIENE EXPOSURE ASSESSMENT PROGRAM 1. REASON FOR ISSUE: The Veterans Health Administration (VHA) has developed this program to meet Occupational Safety and Health (OSH) requirements established by VA Directive 7700, Occupational Safety and Health. This Directive specifies actions and expected performance criteria for Industrial Hygiene programs. 2. SUMMARY OF CONTENTS: Hazardous exposures adversely impact VHA staff, patients, and visitors. This Directive establishes VHA policy for implementing the Industrial Hygiene Exposure Assessment Program. The Program establishes the responsibilities and procedures for preventing adverse health effects from occupational exposures, ensures compliance with laws and regulations mandating a safe and healthful working environment, and provides a comprehensive approach for prioritizing and managing occupational exposure risks. The systemic approach described in this Directive will allow designated staff to anticipate, recognize, evaluate, and control occupational exposure hazards present in VHA facilities. 3. RELATED ISSUES: VA Directive 7700 and VHA Directive 7701. 4. RESPONSIBLE OFFICE: The Director, Office of Occupational Safety Health and Green Environmental Management (GEMS) Programs (10NA8) is responsible for the contents of this Directive. Questions may be referred to 202-632-7889. 5. RESCISSIONS: None. 6. RECERTIFICATION: This VHA Directive is due to be recertified on or before the last working day of April 2021. David J. Shulkin, M.D. Under Secretary for Health DISTRIBUTION: Emailed to the VHA Publication Distribution List on 5/3/2016. T-1 April 29, 2016 VHA DIRECTIVE 7702 INDUSTRIAL HYGIENE EXPOSURE ASSESSMENT PROGRAM 1. PURPOSE This Veterans Health Administration (VHA) Directive provides VHA policy for implementing the elements of the Industrial Hygiene (IH) program. -
Environmental Compliance (Ec)
LANL Waste Characterization, Reduction, and Repackaging Facility DOE ORR 7/21 OCCUPATIONAL AND INDUSTRIAL SAFETY AND HYGIENE PROGRAM (OSH) OBJECTIVE OSH.1: LANS has established and implemented Occupational and Industrial Safety and Hygiene (OISH) programs to ensure safe accomplishment of work at WCRR. Sufficient numbers of qualified personnel as well as adequate facilities and equipment are available to support WCRRF operations. (CRs 1, 4, 6, and 7) CRITERIA 1. The IH Program has conducted current and comprehensive exposure assessments. An adequate monitoring program is in place including equipment. (Exposure to radioactive contamination will be evaluated in the Radiological Protection Functional Area). (TSR; 10 CFR 851, CRD 18) 2. The Occupational Safety program has incorporated hazards and appropriate controls for the WCRR work activities such as ladder safety, electrical, Lockout/Tagout, hotwork, and vehicular safety. (TSR; 10 CFR 851) 3. Hoisting and rigging program complies with TSR requirements concerning spotters (TSR 5.6.10) and engineered lifts (5.10.3). Forklift management and operational procedures comply with TSR controls. (TSR; 10 CFR 851) 4. Adequate numbers of Industrial Hygiene and Occupational Safety professionals are assigned and perform effectively (work place surveillances, work package reviews, walk-down, etc). 5. Adequate facilities are available to ensure WCRRF operational support in the area of occupational and industrial safety. 6. The level of knowledge of occupational and industrial safety personnel concerning their roles and responsibilities for WCRR operations is adequate. (DOE O 440.1A, DOE O 5480.20A) APPROACH Requirement: • 10 CFR 851, Worker Safety and Health Program Document Review: • Review Contractor Management Self Assessment Report (MSA), and Contractor Operational Readiness Review (CORR) Report and corrective actions for all findings to determine if: – All Pre-Start Findings are resolved and the corrective actions are appropriate for the issue determined. -
Microplastics Expert Workshop Report
Microplastics Expert Workshop Report Trash Free Waters Dialogue Meeting Convened June 28-29, 2017 EPA Office of Wetlands, Oceans and Watersheds Primary Author: Margaret Murphy, AAAS S&TP Fellow Report Date: December 4, 2017 1 EPA Microplastics Expert Workshop Report Executive Summary Recent global efforts to better understand microplastics distribution and occurrence have detailed both the ubiquity of microplastics and the uncertainties surrounding their potential impacts. In light of this scientific uncertainty, the US Environmental Protection Agency (EPA) convened a Microplastics Expert Workshop in June 2017 to identify and prioritize the scientific information needed to understand the risks posed by microplastics (broadly defined as plastic particles <5 mm in size in any one dimension (Arthur et al. 2009)) to human and ecological health in the United States. The workshop gave priority to gaining greater understanding of these risks, while recognizing that there are many research gaps needing to be addressed and scientific uncertainties existing around microplastics risk management (e.g., waste management/recycling/ circular economy principles, green chemistry approaches to developing alternatives to current-use plastics). The workshop participants adopted a risk assessment-based approach and addressed four major topics: 1) microplastics methods, including deficits and needs; 2) microplastics sources, transport and fate; and 3) the ecological and 4) human health risks of microplastics exposure. A framework document was developed prior to the workshop to guide discussion. During the workshop, the participants recommended adopting a conceptual model approach to illustrate the fate of microplastics from source to receptor. This approach is helpful in describing the various scientific uncertainties associated with answering the overarching questions of the ecological and human health risks of microplastics, the degree to which information is available for each, and the interconnections among these uncertainties. -
Supplemental File: Occupational Exposure Assessment
PEER REVIEW DRAFT - DO NOT CITE OR QUOTE United States Office of Chemical Safety and Environmental Protection Agency Pollution Prevention Draft Risk Evaluation for Carbon Tetrachloride Supplemental File: Occupational Exposure Assessment CASRN: 56-23-5 January 2020 PEER REVIEW DRAFT -DO NOT CITE OR QUOTE TABLE OF CONTENTS/ ABBREVIATIONS ....................................................................................................................................7 EXECUTIVE SUMMARY .......................................................................................................................9 1 INTRODUCTION ............................................................................................................................11 1.1 Overview .....................................................................................................................................11 1.2 Scope ...........................................................................................................................................11 1.3 General Approach and Methodology for Occupational Exposures ............................................17 Process Description and Worker Activities ........................................................................... 17 Number of Workers and Occupational Non-Users ................................................................ 17 Inhalation Exposure Assessment Approach and Methodology ............................................. 17 1.3.3.1 General Approach .......................................................................................................... -
Exposure Assessments: a How to Guide Dave Huizen, CIH Grand Valley State University Exposure Assessment: a How to Guide
Exposure Assessments: A How to Guide Dave Huizen, CIH Grand Valley State University Exposure Assessment: A How to Guide Participant Take-Aways from this Presentation: Understand why qualitative exposure assessments should be used Describe AIHA’s Basic Workplace Characterization Explore Qualitative Assessment Tools Review AIHA’s new Exposure Assessment Checklist Tool Exposure Assessment: A How to Guide How do we traditionally define industrial hygiene exposure assessment? What do we think is done? Exposure Assessment: A How to Guide We often think exposure assessment is primarily quantitative measurement. Air sampling, noise measurements, etc. How good are quantitative measurements? Of 1.4 million samples from OSHA nearly 50% are non-detects 20% of the samples above are double the exposure limit1. Are we spending too many resources assessing exposure quantitatively? Exposure Assessment: A How to Guide How much time do you spend with qualitative assessment tools before moving to quantitative methods? Exposure Assessment: AIHA’s Basic Characterization of Workplace First Step in Exposure Assessment: Gather Information Goal: Collect Information on workplace, work force, agents, etc. Sources of Information SDSs Workers Walk-around Surveys Engineers Records – drawings, process, medical, employment, maintenance, monitoring Literature search OELs Exposure Assessment: AIHA’s Basic Characterization of Workplace Questions to Ask: What are the hazardous agents? In what quantities? What are the health effects? What are the -
Guidelines for Statistical Analysis of Occupational Exposure Data
GUIDELINES FOR STATISTICAL ANALYSIS OF OCCUPATIONAL EXPOSURE DATA FINAL by IT Environmental Programs, Inc. 11499 Chester Road Cincinnati, Ohio 45246-0100 and ICF Kaiser Incorporated 9300 Lee Highway Fairfax, Virginia 22031-1207 Contract No. 68-D2-0064 Work Assignment No. 006 for OFFICE OF POLLUTION PREVENTION AND TOXICS U.S. ENVIRONMENTAL PROTECTION AGENCY 401 M STREET, S.W. WASHINGTON, D.C. 20460 August 1994 DISCLAIMER This report was developed as an in-house working document and the procedures and methods presented are subject to change. Any policy issues discussed in the document have not been subjected to agency review and do not necessarily reflect official agency policy. Mention of trade names or products does not constitute endorsement or recommendation for use. i CONTENTS FIGURES.......................................................... v TABLES........................................................... vi ACKNOWLEDGMENT................................................vii INTRODUCTION.................................................... 1 A. Types of Occupational Exposure Monitoring Data ...................... 1 B. Types of Occupational Exposure Assessments ........................ 2 C. Variability in Occupational Exposure Data ........................... 3 D. Organization of This Report .................................... 4 STEP 1: IDENTIFY USER NEEDS........................................ 9 STEP 2: COLLECT DATA............................................. 15 A. Obtaining Data From NIOSH ................................... 15