Thermodynamic Analysis and System Design of a Novel Split Cycle Engine Concept
Total Page:16
File Type:pdf, Size:1020Kb
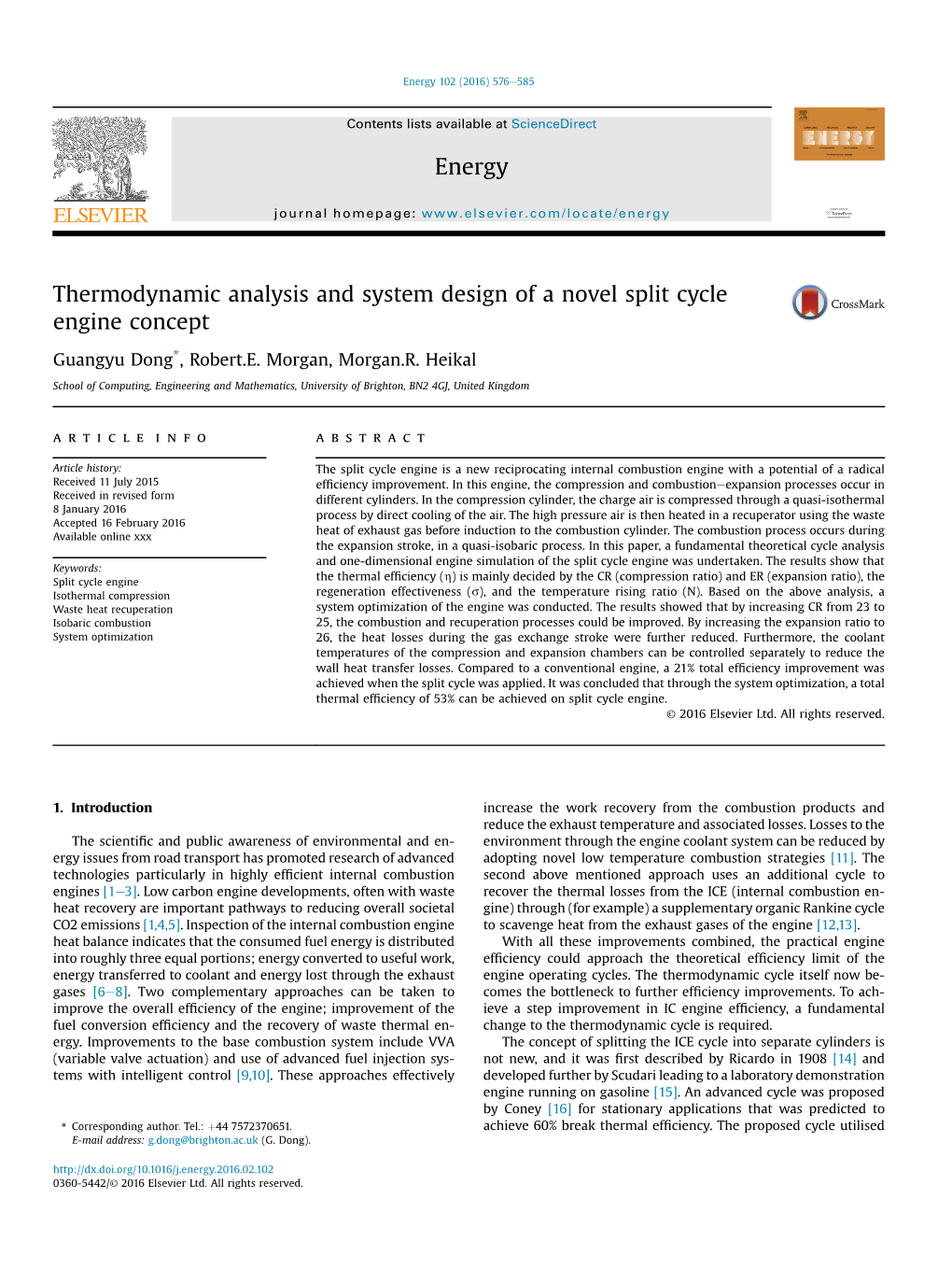
Load more
Recommended publications
-
The Recuperated Split Cycle – Experimental Combustion Data from a Single Cylinder Test Rig
2017-24-0169 The recuperated split cycle – experimental combustion data from a single cylinder test rig Author, co-author ( Do NOT enter this information. It will be pulled from participant tab in MyTechZone ) Affiliation ( Do NOT enter this information. It will be pulled from participant tab in MyTechZone ) Critical deadlines – Review ready 16 th March, final manuscript 10 th June Abstract research in the field. Significant benefits through vehicle and system measures, such as kinetic energy recovery and improved aerodynamics are expected to deliver substantial improvements but the primary The conventional Diesel cycles engine is now approaching the source of loss in the system, the prime mover, is more challenging. practical limits of efficiency. The recuperated split cycle engine is an Reductions in powertrain friction and improvements in combustion alternative cycle with the potential to achieve higher efficiencies than efficiency are likely to deliver brake efficiencies as high as 50% from could be achieved using a conventional engine cycle. In a split cycle conventional compression ignition technologies [1]. The addition of engine, the compression and combustion strokes are performed in waste heat recovery will also drive performance beyond 50%, but there separate chambers. This enables direct cooling of the compression is a broad consensus that brake efficiencies in the range of 50-55% cylinder reducing compression work, intra cycle heat recovery and low represents the technology limit from an advanced compression ignition heat rejection expansion. Previously reported analysis has shown that propulsion system with waste heat recovery. brake efficiencies approaching 60% are attainable, representing a 33% improvement over current advanced heavy duty diesel engine. -
Scuderi Split Cycle Engine: a Review
Int. J. Mech. Eng. & Rob. Res. 2013 Anshul Jangalwa et al., 2013 ISSN 2278 – 0149 www.ijmerr.com Vol. 2, No. 4, October 2013 © 2013 IJMERR. All Rights Reserved Review Article SCUDERI SPLIT CYCLE ENGINE: A REVIEW Anshul Jangalwa1*, Aditya Kumar Singh1, Akshay Jain1 and Ankit Barua1 *Corresponding Author: Anshul Jangalwa, [email protected] Internal Combustion engines have become a very important prime movers in today’s life, there study is also an active field of research for many automobile industries and also has its environmental concerns. IC engines are used not only in automobile industries but are also used in transportation in sea as well as air, as a prime mover for electric generators and in industrial applications. There efficiencies and there environmental impacts are very crucial. A new IC engine developed by the Scuderi group called ‘Scuderi Split Cycle Engine’ is described in this review paper. It is more efficient than a conventional engine and also have less emissions. Keywords: Conventional engine, Efficiency, Split cycle INTRODUCTION different groups all over the world. Various Scuderi Split-cycle engines divides the four engineers and scientists worked on it to strokes of intake, compression, power, and explore the possibility of the split cycle engine. exhaust into two separate but paired cylinders. But, none has matched the efforts and the The first cylinder is used for intake and results obtained by Late Carmelo J. Scuderi. compression. The compressed air is then He gave his entire life for the Scuderi split cycle transferred through a crossover passage from engine. The Scuderi Group, an engineering the compression cylinder into the expansion and licensing company based in West cylinder, where combustion and exhaust occur. -
Combustion Characteristics of a Spark-Ignited Split-Cycle Engine Fuelled with Methane
Article citation info: CAMERON I., SOBIESIAK A. Combustion characteristics of a spark-ignited split-cycle engine fuelled with methane. Combustion Engines. 2015, 161(2), 33-41. ISSN 2300-9896. Iain CAMERON PTNSS-2015-204 Andrzej SOBIESIAK Combustion characteristics of a spark-ignited split-cycle engine fuelled with methane This paper begins with a brief introduction to the operating principles of a split-cycle engine that utilizes a valved, intermediary volume to connect the two engine cylinders. Results from experimental testing of the engine fueled with pure methane are presented with a particular emphasis on the combustion duration and phasing. Two different methods of analysing the combustion duration – the mass fraction burn (MFB) and normalized pressure ratio (PRN) – are given. Testing was performed at wide open throttle (WOT) for engine speeds ranging from 850–1200 rpm, and air-fuel equiva- lence ratios from 0.8–1.0. The results indicate that the main combustion duration is very rapid for all conditions tested, despite late combustion phasing. Changes in spark timing were shown to have a considerable impact on IMEP but did not greatly effect the burn duration. Cyclic variability of IMEP was found to be less than 4% for all cases, except when operation was leaner than ø = 0.85, indicating good combustion stability. Key words: spark ignition engines, split-cycle, methane, natural gas, CNG, fast burn, turbulence 1. Introduction [9, 10]. The majority of these engines rely on squish vol- The use of natural gas (NG) as a transportation fuel is umes and/or specially designed piston cavities to generate supported by many appealing attributes associated with the turbulence at TDC. -
The Split Cycle Engine and Its Impact on the Vehicle Cooling System
The split cycle engine and its impact on the vehicle cooling system R E Morgan, G Dong, and M R Heikal Centre for Automotive Engineering, University of Brighton Abstract The split cycle engine represents a radical departure from conventional internal combustion engines. In the split cycle engine, the compression and combustion processes occur in different cylinders, enabling extreme charge air cooling, intra cylinder waste heat recovery and independent optimisation of the compression and combustion chambers. Combining these benefits, thermal efficiencies of over 50% and approaching 60% in some applications are theoretically possible. The split cycle engine is of particular interest in commercial vehicle applications where load factors are high and savings in fuel consumption of major economic benefit to end users. The energy balance of the split cycle engine is markedly different to conventional engines with significantly more energy being rejected through charge air cooling but correspondingly less through the engine cooling system. How the charge air is cooled will affect how thermal energy is rejected to the environment and the consequential impact on the vehicle cooling system. In this paper, the split cycle engine will be described and the energy balance compared with a conventional heavy duty diesel engines. Methods of charge air cooling; through multi stage compression with intercooling, direct cooling with a water spray and by the injection of a cryogenic liquid spray will be discussed. The overall energy balance, impact on powertrain efficiency and heat exchanger sizing for the water spray cooling case is compared with a comparable diesel engine. Finally, the consequences of the split cycle on component thermal loading will be discussed and strategies for controlling critical component temperatures described. -
Xxxciclo Del Dottorato Di Ricerca in Ingegneria E Architettura
UNIVERSITÀ DEGLI STUDI DI TRIESTE XXX CICLO DEL DOTTORATO DI RICERCA IN INGEGNERIA E ARCHITETTURA CURRICULUM INGEGNERIA MECCANICA, NAVALE, DELL’ENERGIA E DELLA PRODUZIONE WASTE HEAT RECOVERY WITH ORGANIC RANKINE CYCLE (ORC) IN MARINE AND COMMERCIAL VEHICLES DIESEL ENGINE APPLICATIONS Settore scientifico-disciplinare: ING-IND/09 DOTTORANDO SIMONE LION COORDINATORE PROF. DIEGO MICHELI SUPERVISORE DI TESI PROF. RODOLFO TACCANI CO-SUPERVISORE DI TESI DR. IOANNIS VLASKOS ANNO ACCADEMICO 2016/2017 Author’s Information Simone Lion Ph.D. Candidate at Università degli Studi di Trieste Development Engineer at Ricardo Deutschland GmbH Early Stage Researcher (ESR) in the Marie Curie FP7 ECCO-MATE Project Author’s e-mail: • Academic: [email protected] • Industrial: [email protected] • Personal: [email protected] Author’s address: • Academic: Dipartimento di Ingegneria e Architettura, Università degli Studi di Trieste, Piazzale Europa, 1, 34127, Trieste, Italy • Industrial: Ricardo Deutschland GmbH, Güglingstraße, 66, 73525, Schwäbisch Gmünd, Germany Project website: • ECCO-MATE Project: www.ecco-mate.eu Official acknowledgments: The research leading to these results has received funding from the People Programme (Marie Curie Actions) of the European Union’s Seventh Framework Programme FP7/2007-2013/ under REA grant agreement n°607214. Abstract Heavy and medium duty Diesel engines, for marine and commercial vehicles applications, reject more than 50-60% of the fuel energy in the form of heat, which does not contribute in terms of useful propulsion effect. Moreover, the increased attention towards the reduction of polluting emissions and fuel consumption is pushing engine manufacturers and fleet owners in the direction of increasing the overall powertrain efficiency, still considering acceptable investment and operational costs. -
Pathways to the Ultra- Efficient Powertrain – Towards 60% Efficiency
Pathways to the ultra- efficient powertrain – towards 60% efficiency Future Powertrain 2017 Dr Robert Morgan Deputy Head, AEC University of Brighton Advanced Engineering Centre 2 University of Brighton Improving thermal efficiency through fundamental understanding of the in cylinder processes Confidential Copyright University of Brighton 2016 Are we at to the end of the road? 3 Wartsila RT-flex58T Mechanical losses 3% Finite combustion 3% Mercedes F1 Blowby 1% Cycle to Cycle variations 2% Gas exchange 2% Heat transfer 7% TOTAL 18% Stone 2012 Confidential Copyright University of Brighton 2016 4 Changing the rules – the split cycle engine, a new thermodynamic cycle Independent 1. Isothermal compression Less work of compression optimisation of the 2. Isobaric heating Pre combustion waste compression & heat recovery expansion cylinders 3. Mixed cycle heat addition 4. Expansion Confidential Copyright University of Brighton 2016 5 Why hasn't it been done before? 1909 Ricardo “Dolphin” engine 1 2004 “ISOENGINE” 2 Several engines with split compressor and combustion cylinders have been proposed Only the Isoengine recovered heat between the chambers Scuderi Engine 3 1 Engines and Enterprise: The Life and Work of Sir Harry Ricardo 2 nd Ed 2Isoengine data analysis and future design options. Coney et al. CIMAC Congress 2004, Paper 83, Koyoto 3http://www.scuderigroup.com/engine-development/ Confidential Copyright University of Brighton 2016 There are multiple challenges in practically 6 implementing the recuperated split cycle engine Effective isothermal -
INTERNAL COMBUSTION ENGINES STILL DELIVER of the Compressor Cylinder Can Be Re- Duced to Eliminate Some of the Negative Work of the Compression Stroke
redictions regarding the DIFFERENT demise of the internal DIFFERENT combustion engine (ICE) have a long history. The steadily growing number of STROKES: hybrid and full electric ve- STROKES: hicles on the road has only added fuel to Pthe fire, so to speak. But while naysayers have been trying to decide how many more years the ICE has left, engineers INTERNALINTERNAL and visionaries at several different com- panies have been looking for ways to ex- tend its life well into the future. They’ve accomplished this by completely reimag- COMBUSTIONCOMBUSTION ining how an ICE works and what it looks like. In this article, we’ll examine the new technologies that have been developed ENGINESENGINES by these companies. Simple inline or V- type piston engines are definitely not in- cluded in this group. It’s anyone’s guess how many (or if any) of these designs STILL DELIVER will ever end up in a mass-produced ve- STILL DELIVER hicle that you’ll see in your shop. For BBYY KKARLARL SSEYFERTEYFERT now, it’s interesting to see how far you can go with air, a little bit of fuel and a TheThe growinggrowing numbernumber ofof alternativealternative great deal of ingenuity. EcoMotors International (www.eco powertrainpowertrain vehiclesvehicles maymay havehave youyou motors.com) has developed an opposed- thinkingthinking you’llyou’ll soonsoon bebe anan electricelectric piston, opposed-cylinder (OPOC) engine that will run on a number of different engineerengineer ratherrather thanthan aa technician.technician. FearFear fuels, including gasoline, diesel and ethanol. The original OPOC engine de- not.not. TheThe internalinternal combustioncombustion engineengine sign has a long history dating back to the isn’t ready to fade into obscurity. -
Eight Companies Determined to Change Diesel Engines Forever
Reinventing Diesel: Eight Companies Determined to Change Diesel Engines Forever By Jason Thompson Diesel Power, March, 2012 Right now, internal-combustion engines (ICE) are hot—hotter than battery-powered vehicles, hotter than hybrids, hotter than anything else on the market for that matter. Though gasoline- fueled engines represent the bulk of the internal-combustion engines on the road, new high-tech diesels are coming on strong. Traditionally, diesel engines have been simple and robust powerplants. They’ve changed very little and only in small increments since their creation in 1893. That slow-and-steady trend appears to be changing in today’s marketplace. Engineers in Detroit are looking into new compression-ignition concepts, Navistar is investing in innovative up-starts, Cummins is working on new engine architectures, and the Japanese automakers are coming to market with small, lightweight diesels. It turns out the idealized transition toward fleets of battery-powered electric vehicles isn’t as rapid as some media outlets would have you believe. Trust us when we say internal combustion is here to stay for a long time to come. Eight Paths To The Future Of Diesel The next generation of diesel engines will follow the principles of thermodynamics much closer. New control strategies and faster computer processors will allow combustion to be more precise than Rudolf Diesel could have ever dreamed. A few years ago, some of the engines we’re about to show you were only theories and CAD renderings, but today they’re starting to materialize. The following is a look into the future of what diesel engines might look like. -
Master's Thesis
Potential Future Engine Cycles for Improved Thermal Efficiency Analysis of Various Internal Waste Heat Recovery Cycles with Minimal Deviation From Common Engine Architectures MICHAEL J. DENNY Department of Applied Mechanics Combustion Division Chalmers University of Technology Gothenburg, Sweden 2014 Master's Thesis 2014:32 Potential Future Engine Cycles for Improved Thermal Efficiency Analysis of Various Internal Waste Heat Recovery Cycles with Minimal Deviation From Common Engine Architectures MICHAEL J. DENNY © MICHAEL J. DENNY, 2014 Master's Thesis 2014:32 ISSN 1652-8557 Department of Applied Mechanics Combustion Division Chalmers University of Technology SE-412 96 G¨oteborg Sweden Telephone: + 46 (0)31-772 1000 Thesis performed at: Volvo Car Corporation Advanced Engine Engineering Dept. 97624 PO Box PV4B SE-405 31 G¨oteborg Sweden Printed by: Chalmers Reposervice G¨oteborg, Sweden 2014 Abstract A comparative 1-D analysis is undertaken between a baseline internal combustion engine (ICE) and several ICE operating cycle concepts which are intended to produce higher brake efficiencies than the baseline which runs on an Otto cycle. The baseline is a spark ignition gasoline engine representative of modern naturally aspirated automotive engines in its architecture and implemented technologies. Engine models are created and compared in the 1-D engine simulation software program GT-Power created by Gamma Technologies. After calibrating the performance of each model with the same resolution and tuning strategies, the result is that all of the concepts are less efficient than the base- line engine. Each engine concept requires additional hardware to separate the processes of the cycle within the engine. These components add to the mechanical friction, flow, and heat losses within the engine, and in some cases manage only to transfer exergy into different forms, not reduce it in a positive way. -
Internal Combustion Engine
Internal combustion engine “ICEV” redirects here. For the form of water ice, see Ice more familiar four-stroke and two-stroke piston engines, V. For the high speed train, see ICE V. along with variants, such as the six-stroke piston engine An internal combustion engine (ICE) is a heat engine and the Wankel rotary engine. A second class of internal combustion engines use continuous combustion: gas tur- bines, jet engines and most rocket engines, each of which are internal combustion engines on the same principle as previously described.[1][2] Firearms are also a form of in- ternal combustion engine.[2] Internal combustion engines are quite different from external combustion engines, such as steam or Stirling engines, in which the energy is delivered to a working fluid not consisting of, mixed with, or contaminated by combustion products. Working fluids can be air, hot wa- ter, pressurized water or even liquid sodium, heated in a boiler. ICEs are usually powered by energy-dense fuels such as gasoline or diesel, liquids derived from fossil fu- els. While there are many stationary applications, most ICEs are used in mobile applications and are the domi- nant power supply for vehicles such as cars, aircraft, and boats. Typically an ICE is fed with fossil fuels like natural gas or petroleum products such as gasoline, diesel fuel or fuel oil. There’s a growing usage of renewable fuels like biodiesel for compression ignition engines and bioethanol Diagram of a cylinder as found in 4-stroke gasoline engines.: or methanol for spark ignition engines. Hydrogen is C – crankshaft. -
Split Cycle Engine Sudeer Gowd Patil1, Martin A.J.2, Ananthesha3 1- M.Sc
Study on Performance Characteristics of Scuderi – Split Cycle Engine Sudeer Gowd Patil1, Martin A.J.2, Ananthesha3 1- M.Sc. [Engg.] Student, 2-Asst. Professor, 3-Asst.Professor, Department of Automotive and Aeronautical Engineering, M. S. Ramaiah School of Advanced Studies, Bangalore 560 058 Abstract Many decades, the internal combustion engines are the promising prime movers on the earth. Many technologies like Gasoline Direct Injection (GDI), Common Rail Diesel Injection (CRDI) have been invented to enhance the performance and to reduce the pollutants from the internal combustion engines. Many split cycle concepts have developed but could not succeed. For the first time the Scuderi group has invented a new concept of split - cycle engine, in which the air is compressed in one cylinder and transferred to the other cylinder, which is in phase with the first cylinder through the crossover passage and ignited when the piston is moving away from TDC promising to enhance the performance and reduce the pollutants. So a detailed computational study of the Scuderi split cycle engine is essential for better understanding of the concept. In this study work, the CFD analysis is carried out for both the conventional spark ignited engine and the Scuderi split cycle engine of approximately same volume and for same amount of charge. The geometrical models required for the analysis have been modeled in CATIA V5R18 environment and the CFD analysis is carried out in the 3-D Ricardo VECTIS platform as it has inbuilt automatic dynamic mesh generation. The analyses are carried out to understand the combustion phenomena for different speeds. -
Double Compression Expansion Engine: Evaluation of Thermodynamic Cycle and Combustion Concepts
Double Compression Expansion Engine: Evaluation of Thermodynamic Cycle and Combustion Concepts Dissertation by Vijai Shankar Bhavani Shankar In Partial Fulfillment of the Requirements For the Degree of Doctor of Philosophy King Abdullah University of Science and Technology, Thuwal, Kingdom of Saudi Arabia © November, 2019 Vijai Shankar Bhavani Shankar All rights reserved EXAMINATION COMMITTEE PAGE This dissertation of Vijai Shankar Bhavani Shankar is approved by the examination committee. Committee Chairperson: Dr. Mani Sarathy Committee Members: Dr. Bengt Johansson, Dr. Himanshu Mishra, Dr. Jamie Turner 2 ABSTRACT Double Compression Expansion Engine: Evaluation of Thermodynamic Cycle and Combustion Concepts Vijai Shankar Bhavani Shankar The efficiency of an internal combustion (IC) engine is governed by the thermodynamic cycle underpinning its operation. The thermodynamic efficiency of these devices is primarily determined by the temperature gradient created during the compression process. The final conversion efficiency also known as brake thermal efficiency (BTE) of IC engines, however, also depend on other processes associated with its operation. BTE is a product of the combustion, thermodynamic, gas-exchange, and mechanical efficiencies. The improvement of BTE through maximation of any one of the four efficiencies is reduced by its implication of the other three. Split-cycle engine provides an alternative method of improving the engine efficiency through over- expansion of combustion gases by transferring it to a cylinder of greater volume. The operation of split-cycle engines is based on either the Brayton or the Atkinson Cycles. Atkinson Cycle has been demonstrated in IC engines without the split-cycle architecture but is limited by the reduced energy density. Double Compression Expansion Engine (DCEE) provides a method of accomplishing the Atkinson Cycle without the constraints faced in conventional engine architectures.