Horizontal Drilling by Lynn Helms
Total Page:16
File Type:pdf, Size:1020Kb
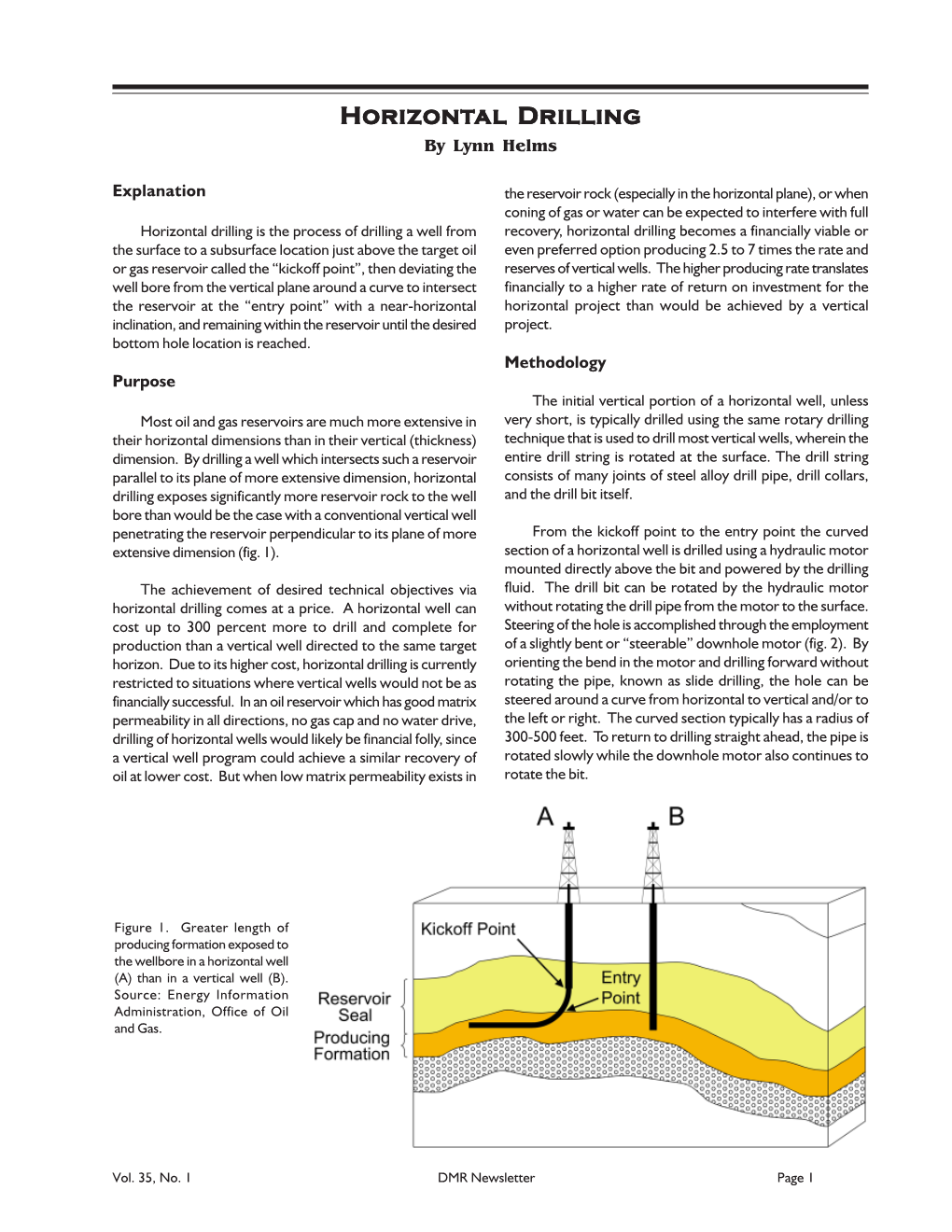
Load more
Recommended publications
-
Petroleum Extension-The University of Texas at Austin ROTARY DRILLING SERIES
Petroleum Extension-The University of Texas at Austin ROTARY DRILLING SERIES Unit I: The Rig and Its Maintenance Lesson 1: The Rotary Rig and Its Components Lesson 2: The Bit Lesson 3: Drill String and Drill Collars Lesson 4: Rotary, Kelly, Swivel, Tongs, and Top Drive Lesson 5: The Blocks and Drilling Line Lesson 6: The Drawworks and the Compound Lesson 7: Drilling Fluids, Mud Pumps, and Conditioning Equipment Lesson 8: Diesel Engines and Electric Power Lesson 9: The Auxiliaries Lesson 10: Safety on the Rig Unit II: Normal Drilling Operations Lesson 1: Making Hole Lesson 2: Drilling Fluids Lesson 3: Drilling a Straight Hole Lesson 4: Casing and Cementing Lesson 5: Testing and Completing Unit III: Nonroutine Operations Lesson 1: Controlled Directional Drilling Lesson 2: Open-Hole Fishing Lesson 3: Blowout Prevention Unit IV: Man Management and Rig Management Unit V: Offshore Technology Lesson 1: Wind, Waves, and Weather Lesson 2: Spread Mooring Systems Lesson 3: Buoyancy, Stability, and Trim Lesson 4: Jacking Systems and Rig Moving Procedures Lesson 5: Diving and Equipment Lesson 6: Vessel Inspection and Maintenance Lesson 7: Helicopter Safety Lesson 8: Orientation for Offshore Crane Operations Lesson 9: Life Offshore Lesson 10: Marine Riser Systems and Subsea Blowout Preventers Petroleum Extension-The University of Texas at Austin Library of Congress Cataloging-in-Publication Data Vieira, João Luiz, 1958– Controlled directional drilling / by João Luiz Vieira. — 4th ed. p. cm. — (Rotary drilling series ; unit 3, lesson 1) Rev. ed. of: Controlled directional drilling. 1984 Includes index. ISBN-10 0-88698-254-5 (alk. paper) ISBN-13 978-0-88698-254-6 (alk. -
Feeds & Speeds — Drilling Or Reaming General Purpose
CL RLD ASS WO FEEDS & SPEEDS — DRILLING OR REAMING GENERAL PURPOSE OR COOLANT FED FEED RATE (INCHES PER REVOLUTION) M AD E IN USA HOLE DIAMETER IN INCHES CUTTING SPEED (SFM) 1/8 1/4 3/8 1/2 5/8 3/4 1 11/4 11/2 STARTING RANGE* GEN. COOL- GEN. COOL- GEN. COOL- GEN. COOL- GEN. COOL- GEN. COOL- GEN. COOL- GEN. COOL- GEN. COOL- CHIP BRINELL TOOL. MATERIAL BEING MACHINED MATERIAL EXAMPLES CHIP DESCRIPTION GENERAL COOLANT PUR- ANT PUR- ANT PUR- ANT PUR- ANT PUR- ANT PUR- ANT PUR- ANT PUR- ANT PUR- ANT CLASS HARDNESS APPLIC. PURPOSE FED POSE FED POSE FED POSE FED POSE FED POSE FED POSE FED POSE FED POSE FED POSE FED ALUMINUM ALLOY 308.0, 356.0, 360.0, 380.0, 383.0, 390.0, 30-150 DISCONTINUOUS FLAKY OR DRILL 250-350 375-550 .003 – .005 .004 .007 .005 .008 .006 .010 .006 .011 .007 .014 .009 .017 – .019 – CAST AND WROUGHT 2024, 3003, 4032, 5052, 6061, 7075 (500 kg) LONG STRINGY REAM 150-250 200-300 .004 – .006 .008 .008 .010 .011 .013 .012 .015 .013 .017 .016 .021 .019 .022 .020 .024 COPPER ALLOY 101, 110, 115, 120, 130, 142, 155, 170, 172, 175, 40-200 LONG CONTINUOUS DRILL 125-190 225-300 .002 – .005 .004 .007 .005 .008 .006 .009 .007 .010 .008 .012 .010 .014 – .016 – TOUGH 195, 425, 610, 630, 655, 725, 805, 826, 910 (500 kg) REAM 50-90 70-105 .005 – .006 .008 .008 .010 .010 .013 .011 .014 .012 .016 .014 .018 .016 .019 .017 .020 LEAD ALLOY Alloys 7, 8, 13, 15 10-20 DISCONTINUOUS DRILL 350-450 400-500 .003 – .005 .004 .006 .006 .007 .007 .008 .008 .009 .009 .013 .013 .015 – .017 – 20 1Sb, 4Sb, 6Sb, 8Sb, 9Sb (500 kg) TIGHTLY CURLED REAM 150-250 200-300 -
Hydraulic Fracturing
www.anadarko.com | NYSE: APC The Equipment: From Rig to Producing Well Hydraulic Fracturing Producing Well: 20+ Years Drilling Rig Anadarko Petroleum Corporation 13 www.anadarko.com | NYSE: APC Horizontal Drilling . Commences with Common Rotary Vertical Drilling . Wellbore then Reaches a “Kickoff Kickoff Point Point” ~6,300 feet Entry Point . Drill Bit Angles Diaggyonally Until ~7,000 feet the “Entry Point” . Wellbore Becomes Fully Horizontal to Maximize Contact Lateral Length with Productive Zones Anadarko Petroleum Corporation 14 www.anadarko.com | NYSE: APC Horizontal Drilling – Significant Surface‐Space Reduction Traditional Vertical Wells Horizontal Drilling Anadarko Petroleum Corporation www.anadarko.com | NYSE: APC Hydraulic Fracturing . Essential Technology in Oil and Natural Gas Production from Tight Sands and Shales . Involves Injecting a Mixture of Water, Sand and a Relatively Small Multiple Layers of 1+ Mile Separates Aquifer Amount of Additives Protective from Fractured Formation Under Pressure into Steel and Cement Targeted Formations . Pressure Creates Pathways, Propped Open by Sand, for Oil or Natural Gas to Flow to the Wellbore Anadarko Petroleum Corporation 16 www.anadarko.com | NYSE: APC Hydraulic Fracturing Equipment Water tanks Blender Blender Frac Van ellheadW ellheadW SdtkSand tanks Pump trucks 17 Anadarko Petroleum Corporation 17 www.anadarko.com | NYSE: APC Hydraulic Fracturing Technology Equipment Water Tanks Pump Trucks Sand Movers Blenders Frac Design Primarily Water and Sand Additives Include: . Gel (ice cream) . Biocide (bleach) . Friction reducer (polymer used in make‐up, nail and skin products) Anadarko Publicly Shares the Ingredients of All Hydraulic Fracturing Operations at www.FracFocus.org Anadarko Petroleum Corporation 18 www.anadarko.com | NYSE: APC Hydraulic Fracturing is Transparent . -
Information on Hydraulic Fracturing
an open pathway to the well. This allows the oil migration of fluids associated with oil and gas and gas to seep from the rock into the pathway, development. After it is determined that the well up the well and to the surface for collection. In is capable of producing oil or natural gas, a Colorado, the targeted formations for hydraulic production casing is set to provide an added fracturing are often more than 7,000 feet layer of separation between the oil or natural underground, and some 5,000 feet below any gas stream and freshwater aquifer. A well drinking water aquifers. survey called a cement bond log is performed to ensure the cement is properly sealed around the The process of hydraulic fracturing has been casing. Additionally, the COGCC requires that used for decades in Colorado, dating to the prior to hydraulic fracturing, the casing be 1970s. Hydraulic fracturing continues to be pressure tested with fluid to the maximum Colorado Department of Natural Resources refined and improved and is now standard for pressure that will ever be applied to the casing. virtually all oil and gas wells in our state, and The well’s construction design is reviewed by across much of the country. Hydraulic fracturing the professional engineering staff at the has made it possible to get the oil and gas out of COGCC. Any flaw in the design will be Information on rocks that were not previously considered as corrected prior to issuing the required drilling likely sources for fossil fuels. permit. Hydraulic Fracturing Common questions and answers about Q: What kinds of fluids do operators use to What is hydraulic fracturing? hydraulic fracturing. -
Manual Borehole Drilling As a Cost-Effective Solution for Drinking
water Review Manual Borehole Drilling as a Cost-Effective Solution for Drinking Water Access in Low-Income Contexts Pedro Martínez-Santos 1,* , Miguel Martín-Loeches 2, Silvia Díaz-Alcaide 1 and Kerstin Danert 3 1 Departamento de Geodinámica, Estratigrafía y Paleontología, Universidad Complutense de Madrid, Ciudad Universitaria, 28040 Madrid, Spain; [email protected] 2 Departamento de Geología, Geografía y Medio Ambiente, Facultad de Ciencias Ambientales, Universidad de Alcalá, Campus Universitario, Alcalá de Henares, 28801 Madrid, Spain; [email protected] 3 Ask for Water GmbH, Zürcherstr 204F, 9014 St Gallen, Switzerland; [email protected] * Correspondence: [email protected]; Tel.: +34-659-969-338 Received: 7 June 2020; Accepted: 7 July 2020; Published: 13 July 2020 Abstract: Water access remains a challenge in rural areas of low-income countries. Manual drilling technologies have the potential to enhance water access by providing a low cost drinking water alternative for communities in low and middle income countries. This paper provides an overview of the main successes and challenges experienced by manual boreholes in the last two decades. A review of the existing methods is provided, discussing their advantages and disadvantages and comparing their potential against alternatives such as excavated wells and mechanized boreholes. Manual boreholes are found to be a competitive solution in relatively soft rocks, such as unconsolidated sediments and weathered materials, as well as and in hydrogeological settings characterized by moderately shallow water tables. Ensuring professional workmanship, the development of regulatory frameworks, protection against groundwater pollution and standards for quality assurance rank among the main challenges for the future. -
Drilling Deeper
Drilling deeper Nia Kajastie looks at the evolution of underground drilling machinery and technologies, as well as the latest equipment releases for exploration, development and production applications Nia Kajastie 19 Dec 2016 10:00 Feature Underground drilling is a vital part of exploration and hard-rock mining activities across a wide range of applications, from diamond coring, short-hole drilling for development and long-hole drilling for production, to ground support to install rock bolts or cable bolts, secondary drilling and blasting to reduce oversize, or simply utility drilling. In line with the variety of possible functions, the Figure 1A Joy DR-1SB hydraulic jumbo drill, which features Intelsense drilling control system and hydrostatic drive for a requirements of drilling equipment for lower profile and tighter turning radius exploration, development and production are dependent on a number of factors. When it comes to exploration drilling, for example, target hole depths and core size are critical to choosing the best rig and tooling. The size of the drilling stations or tunnels is also important to the selection process. According to Boart Longyear, tooling is specific to the core size required. Rods come in different lengths – so you can use 5ft (1.5m) rods if you are drilling in a confined space. Likewise, core barrels come in 5ft or 10ft lengths (1.5m and 3m). On smaller, less powerful rigs, the company recommends freer cutting bits, while also considering the geological formation. The other factor to consider when selecting the right method, rig and tooling is the angle or dip of the hole. -
6. the BOREHOLE ENVIRONMENT 6.1 Introduction 6.2 Overburden
Petrophysics MSc Course Notes The Borehole Environment 6. THE BOREHOLE ENVIRONMENT 6.1 Introduction Wireline logging has a single clearly defined purpose: to give accurate and representative data on the physical properties of the rock formations and fluids encountered in a borehole. The tools used to take these readings have to cope with extremely tough conditions downhole, particularly, high temperatures and pressures, inhospitable chemical conditions and the physical constraints imposed by the physics of the measurements and the borehole geometry. It should also be remembered that we are interested in the properties of the rocks in undisturbed conditions, and the act of drilling the borehole is the single most disturbing thing that we can do to a formation. 6.2 Overburden Pressures The formations in the sub-surface are at raised pressure, and are occupied by fluids which are also at high pressure. The pressure that a rock is subjected to at a given depth is determined by the weight of the rock above it, and hence the density of that rock. This is called the overburden pressure or sometimes the lithostatic pressure (note that, to a first approximation, the overburden pressure is the same in all directions (isotropic)). We can write an equation to describe the overburden pressure (6.1) Pover = rrock g h where, Pover = the overburden pressure at depth h rrock = the mean rock density above the depth in question g = the acceleration due to gravity h = the depth to the measurement point. Clearly the rock above a given depth will have a varied lithology and porosity and hence a varying density. -
Drilling and Completion Services Cost Index Q2 2015
Drilling and Completion Services Cost Index Q2 2015 Prepared by Spears and Associates, Inc. 8908 S. Yale, Suite 440 Tulsa, OK 74137 www.spearsresearch.com July 2015 Drilling and Completion Services Cost Index: Q2 2015 Introduction The Drilling and Completion Services (DCS) Cost Index tracks and forecasts price changes for products and services used in drilling and completing new wells in the US. The DCS Cost Index is a tool for oil and gas companies, oilfield equipment and service firms, and financial institutions interested in benchmarking and forecasting well costs. Methodology Spears and Associates undertakes a quarterly survey of independent well engineering and wellsite supervision firms to collect “spot market” drilling and completion services price information for a specific set of commonly drilled wells in the US. The information in the “well profile” survey is collected in the form of detailed drilling and completion services cost estimates based on current unit prices and usage rates in each location at the end of the quarter. The well profiles are equally-weighted in calculating an average price change per quarter for the drilling and completion services cost components. A “total well cost” price change is calculated for each well profile covered by the survey which reflects the weighted average price change for each component of the well’s cost. An overall “total well cost” price change is calculated, with each well profile equally weighted, to determine the “composite well cost” index shown in this report. All cost items are indexed to 100 as of Q1 2008. “Spot” prices tracked by the DCS Cost Index are those in effect at the end of each quarter and as such may differ from prices averaged across the entire quarter. -
Best Research Support and Anti-Plagiarism Services and Training
CleanScript Group – best research support and anti-plagiarism services and training List of oil field acronyms The oil and gas industry uses many jargons, acronyms and abbreviations. Obviously, this list is not anywhere near exhaustive or definitive, but this should be the most comprehensive list anywhere. Mostly coming from user contributions, it is contextual and is meant for indicative purposes only. It should not be relied upon for anything but general information. # 2D - Two dimensional (geophysics) 2P - Proved and Probable Reserves 3C - Three components seismic acquisition (x,y and z) 3D - Three dimensional (geophysics) 3DATW - 3 Dimension All The Way 3P - Proved, Probable and Possible Reserves 4D - Multiple Three dimensional's overlapping each other (geophysics) 7P - Prior Preparation and Precaution Prevents Piss Poor Performance, also Prior Proper Planning Prevents Piss Poor Performance A A&D - Acquisition & Divestment AADE - American Association of Drilling Engineers [1] AAPG - American Association of Petroleum Geologists[2] AAODC - American Association of Oilwell Drilling Contractors (obsolete; superseded by IADC) AAR - After Action Review (What went right/wrong, dif next time) AAV - Annulus Access Valve ABAN - Abandonment, (also as AB) ABCM - Activity Based Costing Model AbEx - Abandonment Expense ACHE - Air Cooled Heat Exchanger ACOU - Acoustic ACQ - Annual Contract Quantity (in reference to gas sales) ACQU - Acquisition Log ACV - Approved/Authorized Contract Value AD - Assistant Driller ADE - Asphaltene -
Well Logging
University of Kirkuk / Faculty of Science / Applied geology department rd 3 year 2020 WELL LOGGING Dr. Radhwan Khaleel Hayder INTRODUCTION: -What is a “Log” and ‘’Well Logging’’. LOG OR WELL LOGGING (THE BOREHOLE IMAGE): - Data are organized and interpreted by depth and represented on a graph called a log (a record of information about the formations through which a well has been drilled). - Visual inspection of samples brought to the surface (geological logs). Example cuttings and corres. - Study of the physical properties of rocks and the fluids through which the bore hole is drilled. - Traditionally logs are display on girded papers. Now a days the log may be taken as films, images and in digital format. - Some types of well logs can be done during any phase of a well's history: drilling, completing, producing or abandoning. -Well logging is performed in boreholes drilled for the oil and gas, groundwater, mineral, environmental and geotechnical studies. -The first electrical resistivity well log was taken in France, in 1927. THE IMPORTANCE OF WELL LOGGING: 1-Determination of lithology. 2-Determination of reservoir characteristics (e.g. porosity, saturation, permeability). 3-Determination formation dip and hole size. 4-Identification of productive zones, to determine depth and thickness of zones. 5-Distinguish between oil, gas, or water in a reservoir, and to estimate hydrocarbon reserves. 6-Geologic maps developed from log interpretation help with determining facies relationships and drilling locations. 1 ADVANTAGES AND LIMITATIONS OF WELL LOGGING: Advantages: 1- Continuous measurements. 2- Easy and quick to work with. 3- Short time acquisition. 4- Economical. Limitations: 1- Indirect measurements. -
Drilling Fluid Systems & Products
Drilling Fluid Systems & Products Drilling Solutions Version 6 Table of contents Overview 2 Integrated Solutions 6 Integrated Borehole Strengthening Solutions (I-BOSS) 6 OPTI-STRESS 8 Drilling Fluid Simulation Software 9 OPTIBRIDGE 9 PRESS PRO RT 10 VIRTUAL HYDRAULICS 12 Drilling Fluid Systems & Products 13 Water-Base Systems DRILPLEX 13 DRILPLEX AR PLUS 14 DURATHERM 15 ENVIROTHERM NT 16 GLYDRIL 18 K-MAG 19 KLA-SHIELD 20 POLY-PLUS 21 ULTRADRIL 22 Oil-base Systems ECOGREEN 24 ENVIROVERT 25 MEGADRIL 26 RHADIANT 27 RHELIANT 28 VERSACLEAN/VERSADRIL 29 Synthetic-Base Systems PARALAND 30 PARATHERM/VERSATHERM 31 Non-Aqueous Systems WARP Advanced Fluids Technology 32 Drilling Fluid Products 34 Product Summaries 34 Drilling Fluid Systems & Products Version 6 1 Overview The M-I SWACO solutions mindset permeates our company and positively influences the problem-solving orientation we have toward our clients, the solutions we deliver, our new-technology advancement, people development within our company and our future strategies. Starting with the basic building blocks of Before people work for M-I SWACO, training for the job at hand, M-I SWACO instructors quickly bring new specialists a Schlumberger company, we screen up to speed in the disciplines required for them to deliver maximum value them not only for current skills from our products and services. M-I SWACO ensures customers around and experience, but also for their the world get the highest level of service by standardizing training courses to willingness to learn new things, solve meet the universal expectations of all operators. Where locale dictates problems and help others. Once they certain specialized practices, M-I SWACO trainers prepare field join the M-I SWACO organization, personnel for those details as well. -
Characterisation and Management of Drilling Fluids and Cuttings in the Petroleum Industry
Information sheet Environmental Protection Act 1994 Characterisation and management of drilling fluids and cuttings in the petroleum industry 1 Introduction This information sheet describes the process for petroleum and gas operators to: assess and characterise waste drilling fluids and cuttings (which for this information sheet also includes rock materials, solids and fines); and develop ways to manage wastes produced from drilling activities that address environmental risks and are consistent with the requirements of Queensland's environmental legislation. There are various drilling fluid systems used in the petroleum industry including freshwater, saltwater, oil, synthetic-based and pneumatic (e.g. air, foam) fluid systems (West et al., 2006). The term 'mud' is frequently used interchangeably with the term 'fluid'. The term 'mud' is used because of the thick consistency of the fluid system (Caenn, 2011). In general, drilling fluids in the petroleum industry are used to aid tools during the drilling of wells. The main functions of drilling fluids are: carrying cuttings from the hole cooling and cleaning the drill bit reducing friction maintaining the stability of the bore maintaining down-hole hydrostatic pressure to be non-damaging to the formation. Drilling fluids contain a variety of specialty chemicals (called ‘additives’) each having a different purpose. For example: killing bacteria and adjusting pH (West et al., 2006) controlling viscosity, reducing fluid loss to the formation and inhibiting equipment corrosion (Ghazia, 2011). The additives in drilling fluids are adjusted according to the physicochemical conditions of geological formations which invariably change with depth (Ghazia, 2011). In addition, drilling fluids are to be non-hazardous to the environment and personnel.