Handbook of Die Design, 2Nd Edition
Total Page:16
File Type:pdf, Size:1020Kb
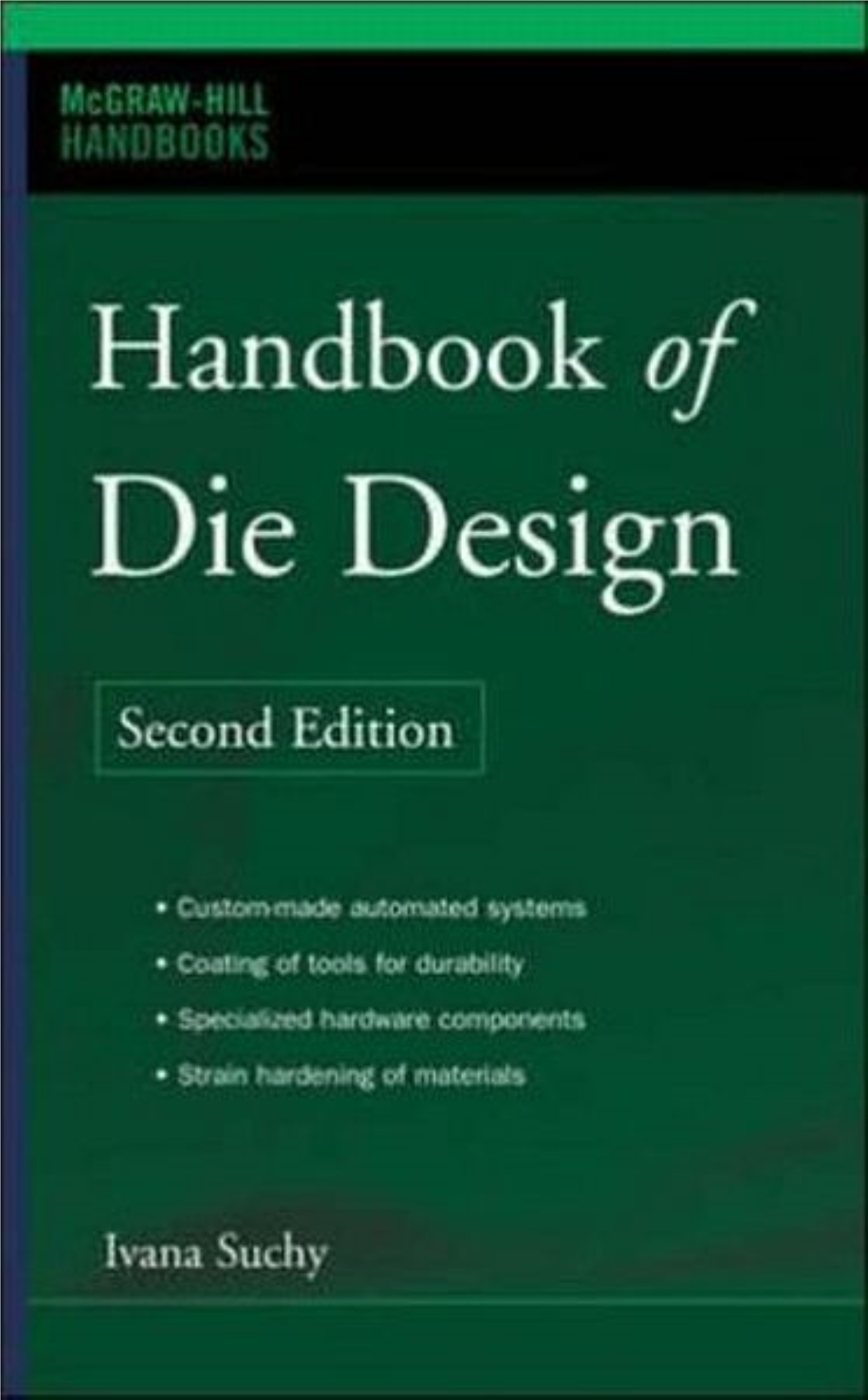
Load more
Recommended publications
-
Integrating Cold Forging and Progressive Stamping for Cost
Precision Cold Forging Progressive Stamping Enables Cost Effective Production of Complex Parts Overview Both Cold Forging and Precision Stamping are proven technologies used in the fabrication of parts for a wide range of industries. Many of our previous Tech Bulletins have detailed the benefits of each technology, and in several cases, these processes are thought of as an either- or choice. This Tech Bulletin provides insights into how combining these technologies in a process known as Precision Cold Forging Progressive Stamping can provide significant synergies and additional benefits for the cost-effective production of complex parts that cannot easily be created by either technique alone. What is Cold Forging? As detailed in other Interplex Tech Bulletins, Cold Forging is essentially an impact forming process in which billets of raw material are compressed and reformed into a part’s desired shape. Cold Forging offers the key benefits of lower costs, rapid high-volume throughput, high part strength, and very efficient material utilization. This, in comparison to processes like machining that remove Figure 1 – Cold Forged significant amounts of raw material rather than simply reforming all the Automotive Seat Belt Gear material into the desired shape. What is Precision Stamping? Precision Stamping is another proven technology that uses a press and die to form sheet metal, blanks or coil material into desired shapes. Variations of the stamping process can effectively yield several different output results including bending, embossing, flanging, coining, etc. Like Cold Forging, Precision Stamping typically offers high material utilization with minimal waste and can also deliver high-volume production results. -
Minting America: Coinage and the Contestation of American Identity, 1775-1800
ABSTRACT MINTING AMERICA: COINAGE AND THE CONTESTATION OF AMERICAN IDENTITY, 1775-1800 by James Patrick Ambuske “Minting America” investigates the ideological and culture links between American identity and national coinage in the wake of the American Revolution. In the Confederation period and in the Early Republic, Americans contested the creation of a national mint to produce coins. The catastrophic failure of the paper money issued by the Continental Congress during the War for Independence inspired an ideological debate in which Americans considered the broader implications of a national coinage. More than a means to conduct commerce, many citizens of the new nation saw coins as tangible representations of sovereignty and as a mechanism to convey the principles of the Revolution to future generations. They contested the physical symbolism as well as the rhetorical iconology of these early national coins. Debating the stories that coinage told helped Americans in this period shape the contours of a national identity. MINTING AMERICA: COINAGE AND THE CONTESTATION OF AMERICAN IDENTITY, 1775-1800 A Thesis Submitted to the Faculty of Miami University in partial fulfillment of the requirements for the degree of Master of Arts Department of History by James Patrick Ambuske Miami University Oxford, Ohio 2006 Advisor______________________ Andrew Cayton Reader_______________________ Carla Pestana Reader_______________________ Daniel Cobb Table of Contents Introduction: Coining Stories………………………………………....1 Chapter 1: “Ever to turn brown paper -
1 Modeling and Optimization in Manufacturing by Hydroforming and Stamping
13 1 Modeling and Optimization in Manufacturing by Hydroforming and Stamping Hakim Naceur1 and Waseem Arif2 1Université Polytechnique Hauts-de-France, CNRS, INSA Hauts-de-France, UMR 8201-LAMIH, F-59313 Valenciennes, France 2University of Gujrat, Mechanical Engineering Department, Gujrat, Pakistan 1.1 Introduction Due to the strict environmental policies and shortage of energy, the manufacturing industries are pressurized to cut down the raw material cost and to save energy. This is particularly true in the automotive industry, where manufacturers are obliged to develop advanced techniques to reduce the pollution by reducing the fuel con- sumption without significant increase in the cost. Among all the manufacturing techniques, the stamping and hydroforming methods hold a top position among the cold sheet metal forming processes due to the versatility of components that can be produced and high production rates [1]. Stamping and hydroforming processes are intensively used in various industrial sectors such as transportation, car body in white (Figure 1.1), household appliances, metal packaging, etc. The use of fluid pressure has been remarkably increased in sheet metal form- ing processes since it allows a superior final surface quality of the workpiece than standard deep drawing process [2–4]. In particular, sheet hydroforming process has great potential to manufacture body-in-white parts with consistently extreme level of ultimate tensile strength, reduced weight, geometrical accuracy, and minimum tol- erances. It has certain advantages, e.g. more uniform thickness distribution of the final workpiece component, lower tooling cost, and versatility to produce partswith different geometries using the same setup [5]. The worldwide acknowledgment of these two sheet metal forming processes is largely due to the external pressure from the government legislators to develop lightweight products. -
UP-6178F Lab Tape Casting Machine
UP-6178F Lab Tape Casting Machine Description: Laboratory tape casting machine is suitable for mixing, plasticizing and extruding of TPU, engineering plastics, modified plastics, masterbatch and other high polymer. It has the characteristics of uniform dispersion, plasticizing and coloring, filling and modification. It is mainly used in the fields of casting film product forming, casting material formulation development, casting material performance research, etc., such as transporting materials to casting machine to produce casting film products, etc. Suitable for laboratory test and quality control, teaching research and small-scale production. Introduction: This machine is single layer casting and sheet extrusion equipment. It is suitable for the testing and evaluation of the casting performance of polymer materials, the research and development of new product formula, etc. it is the first choice of equipment for major manufacturers and scientific research institutions. Application scope: 1. Test and evaluation of casting performance of polymer materials 2. R & D of new product formula 3. Optimization of production process parameters 4. Small scale production of thin film 5. Quality control Parameters: Single screw extruder: 1. Screw: ¢ 20mm PE, EVA, special screw 2. Screw speed: 0-95rpm frequency conversion speed regulation 3. Length diameter ratio: 1:28 4. Screw material: 38CrMoAl chrome molybdenum alloy, surface treated by tempering, nitriding, chrome plating, polishing and ultra precision grinding, hardness HRC 5. 55 ~ 60, roughness Ra ≤ 0.4 μ m, nitriding layer depth ≥ 0.6mm 6. Barrel material: 38CrMoAl chrome molybdenum alloy, surface treated by tempering, nitriding, chrome plating, polishing and ultra precision grinding, hardness HRC 7. 55 ~ 60, roughness Ra ≤ 0.4 μ m, nitriding layer depth ≥ 0.6mm 8. -
How to Collect Coins a Fun, Useful, and Educational Guide to the Hobby
$4.95 Valuable Tips & Information! LITTLETON’S HOW TO CCOLLECTOLLECT CCOINSOINS ✓ Find the answers to the top 8 questions about coins! ✓ Are there any U.S. coin types you’ve never heard of? ✓ Learn about grading coins! ✓ Expand your coin collecting knowledge! ✓ Keep your coins in the best condition! ✓ Learn all about the different U.S. Mints and mint marks! WELCOME… Dear Collector, Coins reflect the culture and the times in which they were produced, and U.S. coins tell the story of America in a way that no other artifact can. Why? Because they have been used since the nation’s beginnings. Pathfinders and trendsetters – Benjamin Franklin, Robert E. Lee, Teddy Roosevelt, Marilyn Monroe – you, your parents and grandparents have all used coins. When you hold one in your hand, you’re holding a tangible link to the past. David M. Sundman, You can travel back to colonial America LCC President with a large cent, the Civil War with a two-cent piece, or to the beginning of America’s involvement in WWI with a Mercury dime. Every U.S. coin is an enduring legacy from our nation’s past! Have a plan for your collection When many collectors begin, they may want to collect everything, because all different coin types fascinate them. But, after gaining more knowledge and experience, they usually find that it’s good to have a plan and a focus for what they want to collect. Although there are various ways (pages 8 & 9 list a few), building a complete date and mint mark collection (such as Lincoln cents) is considered by many to be the ultimate achievement. -
Improved Coining Force Calculations Through Incorporation of Key Process Parameters Dominique Cotton, André Maillard, Joël Kaufmann
Improved coining force calculations through incorporation of key process parameters Dominique Cotton, André Maillard, Joël Kaufmann To cite this version: Dominique Cotton, André Maillard, Joël Kaufmann. Improved coining force calculations through incorporation of key process parameters. IDDRG, Oct 2020, BUSAN, South Korea. pp.012003, 10.1088/1757-899X/967/1/012003/meta. hal-03117270 HAL Id: hal-03117270 https://hal.archives-ouvertes.fr/hal-03117270 Submitted on 21 Jan 2021 HAL is a multi-disciplinary open access L’archive ouverte pluridisciplinaire HAL, est archive for the deposit and dissemination of sci- destinée au dépôt et à la diffusion de documents entific research documents, whether they are pub- scientifiques de niveau recherche, publiés ou non, lished or not. The documents may come from émanant des établissements d’enseignement et de teaching and research institutions in France or recherche français ou étrangers, des laboratoires abroad, or from public or private research centers. publics ou privés. IOP Conference Series: Materials Science and Engineering PAPER • OPEN ACCESS Improved coining force calculations through incorporation of key process parameters To cite this article: D Cotton et al 2020 IOP Conf. Ser.: Mater. Sci. Eng. 967 012003 View the article online for updates and enhancements. This content was downloaded from IP address 195.221.202.65 on 15/01/2021 at 13:35 International Deep-Drawing Research Group (IDDRG 2020) IOP Publishing IOP Conf. Series: Materials Science and Engineering 967 (2020) 012003 doi:10.1088/1757-899X/967/1/012003 Improved coining force calculations through incorporation of key process parameters D Cotton1,3, A Maillard2, and J Kaufmann2 1 Arts et Métiers Institute of Technology, LABOMAP, HESAM University, 71250 Cluny, France 2 CETIM – Technical Centre for Mechanical Industries – France 3 Author to whom any correspondence should be addressed E-mail address: [email protected] Abstract. -
Boilermaker Health & Safety Manual
Boilermakers Health & Safety Manual ihsa.ca Boilermakers Health & Safety Manual Infrastructure Health & Safety Association 5110 Creekbank Road, Suite 400 Mississauga, Ontario L4W 0A1 Canada 1-800-263-5024 ihsa.ca 1 Boilermakers Health & Safety Manual IHSA has additional information on this and other topics. Visit ihsa.ca or call Customer Service at 1-800-263-5024. The contents of this publication are for general information only. This publication should not be regarded or relied upon as a definitive guide to government regulations or to safety practices and procedures. The contents of this publication were, to the best of our knowledge, current at the time of printing. However, no representations of any kind are made with regard to the accuracy, completeness, or sufficiency of the contents. The appropriate regulations and statutes should be consulted. Readers should not act on the information contained herein without seeking specific independent legal advice on their specific circumstance. The Infrastructure Health & Safety Association is pleased to answer individual requests for counselling and advice. This manual was developed, reviewed, and endorsed by the Boilermakers Labour-Management Health and Safety Committee in association with IHSA. Manual IHSA editor: Lori-Lynn Bonnell, design and illustrations: Philippa Giancontieri; project manager: Mike Russo. The Infrastructure Health & Safety Association would like to thank the members of the working group for contributing their knowledge, experience, and time to produce a health and safety manual that will benefit both labour and management in the boilermaker sector. The working group included representatives from the Boilermaker Contractors’ Association (BCA) as well as: · Marty Albright – Alstom Power Canada Inc. -
Fire Protection of Steel Structures: Examples of Applications
Fire protection of steel structures: examples of applications Autor(en): Brozzetti, Jacques / Pettersson, Ove / Law, Margaret Objekttyp: Article Zeitschrift: IABSE proceedings = Mémoires AIPC = IVBH Abhandlungen Band (Jahr): 7 (1983) Heft P-61: Fire protection of steel structures: examples of applications PDF erstellt am: 06.10.2021 Persistenter Link: http://doi.org/10.5169/seals-37489 Nutzungsbedingungen Die ETH-Bibliothek ist Anbieterin der digitalisierten Zeitschriften. Sie besitzt keine Urheberrechte an den Inhalten der Zeitschriften. Die Rechte liegen in der Regel bei den Herausgebern. Die auf der Plattform e-periodica veröffentlichten Dokumente stehen für nicht-kommerzielle Zwecke in Lehre und Forschung sowie für die private Nutzung frei zur Verfügung. Einzelne Dateien oder Ausdrucke aus diesem Angebot können zusammen mit diesen Nutzungsbedingungen und den korrekten Herkunftsbezeichnungen weitergegeben werden. Das Veröffentlichen von Bildern in Print- und Online-Publikationen ist nur mit vorheriger Genehmigung der Rechteinhaber erlaubt. Die systematische Speicherung von Teilen des elektronischen Angebots auf anderen Servern bedarf ebenfalls des schriftlichen Einverständnisses der Rechteinhaber. Haftungsausschluss Alle Angaben erfolgen ohne Gewähr für Vollständigkeit oder Richtigkeit. Es wird keine Haftung übernommen für Schäden durch die Verwendung von Informationen aus diesem Online-Angebot oder durch das Fehlen von Informationen. Dies gilt auch für Inhalte Dritter, die über dieses Angebot zugänglich sind. Ein Dienst der ETH-Bibliothek ETH Zürich, Rämistrasse 101, 8092 Zürich, Schweiz, www.library.ethz.ch http://www.e-periodica.ch J% IABSE periodica 2/1983 IABSE PROCEEDINGS P-61/83 69 Fire Protection of Steel Structures — Examples of Applications Protection contre le feu des structures acier — Quelques exemples d'applications Brandschutz der Stahlkonstruktionen — Einige Anwendungsbeispiele Jacques BROZZETTI Margaret LAW Dir., Dep. -
A Comparison of Thixocasting and Rheocasting
A Comparison of Thixocasting and Rheocasting Stephen P. Midson The Midson Group, Inc. Denver, Colorado USA Andrew Jackson Arthur Jackson & Co., Ltd. Brighouse UK Abstract The first semi-solid casting process to be commercialized was thixocasting, where a pre-cast billet is re-heated to the semi-solid solid casting temperature. Advantages of thixocasting include the production of high quality components, while the main disadvantage is the higher cost associated with the production of the pre-cast billets. Commercial pressures have driven casters to examine a different approach to semi-solid casting, where the semi-solid slurry is generated directly from the liquid adjacent to a die casting machine. These processes are collectively referred to as rheocasting, and there are currently at least 15 rheocasting processes either in commercial production or under development around the world. This paper will describe technical aspects of both thixocasting and rheocasting, comparing the procedures used to generate the globular, semi-solid slurry. Two rheocasting processes will be examined in detail, one involved in the production of high integrity properties, while the other is focusing on reducing the porosity content of conventional die castings. Key Words Semi-solid casting, thixocasting, rheocasting, aluminum alloys 22 / 1 Introduction Semi-solid casting is a modified die casting process that reduces or eliminates the porosity present in most die castings [1] . Rather than using liquid metal as the feed material, semi-solid processing uses a higher viscosity feed material that is partially solid and partially liquid. The high viscosity of the semi-solid metal, along with the use of controlled die filling conditions, ensures that the semi-solid metal fills the die in a non-turbulent manner so that harmful gas porosity can be essentially eliminated. -
Coining's Micro Stamping Capabilities
ELECTRONIC COMPONENTS AND PACKAGING Coining Inc. Micro-Stampings Overview www.ametek.com © 2015 by AMETEK, Inc. All rights reserved. ELECTRONIC COMPONENTS AND PACKAGING Micro-Stampings and Solder Preforms More Than 100 Presses 3 ton to 85 ton High speed (>2000 strokes/min) High precision, 4 post presses Hot presses for stamping Mo, W, etc. www.ametek.com © 2015 by AMETEK, Inc. All rights reserved. ELECTRONIC COMPONENTS AND PACKAGING Coining Differentiators Material Processing Capability In-house advanced casting, rolling and cladding Plating to customer specifications Custom alloys available Tool & Die Capability More than 15,000 dies on-hand Customized designs available Tooling designed to match material characteristics Progressive stamping up to 16 stations Deep draw designs available In-house EDM based tool manufacturing Parts Delivered Clean Room Ready Industry Leading Applications Support Team www.ametek.com © 2015 by AMETEK, Inc. All rights reserved. ELECTRONIC COMPONENTS AND PACKAGING Applications Support Experienced Engineering Team Our material scientists and manufacturing engineers have more than 100 years experience Analytical Capabilities ICP (Inductively Coupled Plasma) for elemental analysis of melts ICP DSC (Differential Scanning Calorimetry) to evaluate proper melting point and characteristics XRF (X-Ray Fluorescence) to verify thickness of plated coatings Wetting Tests to ensure optimal wetting and spread of solder alloys SEM with EDS capability for detailed metallurgical analysis and FA SEM LECO O2, N2, C and S analyzers www.ametek.com © 2015 by AMETEK, Inc. All rights reserved. ELECTRONIC COMPONENTS AND PACKAGING Stampings Capabilities Capabilities Include Stamping Coining Drawing Punching A Wide Varity Of High Precision Parts Available From simple to complex shapes Thicknesses less than 1 mil All Tooling Designed, Manufactured & Maintained In-House Enables rapid prototyping Ensures prime condition of tooling www.ametek.com © 2015 by AMETEK, Inc. -
Portable Hand Power Threader 1/2” - 2”
PORTABLE HAND POWER THREADER 1/2” - 2” Read this Operator’s Manual carefully before using this tool. Failure to understand and follow the contents of this manual may result in electrical shock, fire and/or serious personal injury. ITEM NUMBER: 3306601 Standard Equipment Specifications: PT ® Portable Hand Power Drive Threading Capacity: Pipe 1/2" through 2" •Six Die heads with Dies: 1/2”, 3/4”, 1”, 1-1/4”, 1-1/2”, 2” Motor Type: Universal •Support Arm Power: 1000 Watts •Sturdy Plastic Carrying Case Volts: 110V / 60Hz. Switch: heavy load, with safety lock. Reduction Gearbox: Cast aluminum alloy. Body: Hardened fiberglass plastic shell. Length: 19.5” Weight: 14 lbs. FOR PRODUCT OR WARRANTY INFORMATION CONTACT ARGCO - PIPINGTOOLS DIVISION PHONE: 800-854-1015 • FAX: 760-727-3270 2610 COMMERCE WAY • VISTA, CA 92081 www.pipingtools.com PT ® POWER HAND THREADER General Safety Information • When operating a power tool outside, use an outdoor extension cord marked “W-A” or “W”. These cords are rated for outdoor use and reduce the risk of electrical shock. Read and understand all instructions. • Use only three-wire extension cords which have three-prong Failure to follow all instructions listed below may grounding plugs and three-pole receptacles which accept the tool’s result in electric shock, fire, and/or serious plug. Use of other extension cords will not ground the tool and personal injury. increase the risk of electrical shock. • Use proper extension cords. (See chart.) Insufficient conductor size Work Area Safety will cause excessive voltage drop and loss of power. • Keep your work area clean and well lit. -
Qualification of Test Method for Package Perforation Evaluation
Rochester Institute of Technology RIT Scholar Works Theses 4-8-2016 Qualification of estT Method for Package Perforation Evaluation Di Wang Follow this and additional works at: https://scholarworks.rit.edu/theses Recommended Citation Wang, Di, "Qualification of estT Method for Package Perforation Evaluation" (2016). Thesis. Rochester Institute of Technology. Accessed from This Thesis is brought to you for free and open access by RIT Scholar Works. It has been accepted for inclusion in Theses by an authorized administrator of RIT Scholar Works. For more information, please contact [email protected]. Qualification of Test Method for Package Perforation Evaluation By DI WANG A Thesis Submitted in Partial Fulfillment of the Requirements for the Degree of Master of Science in Packaging Science Department of Packaging Science College of Applied Science and Technology Rochester Institute of Technology Date of Submission: 04/08/2016 Committee Approval: Deanna Jacobs Date Thesis Advisor Changfeng Ge Date Thesis Advisor Kathy Myers Date Committee Member Carol Herring Date Committee Member Abstract The purpose of this paper was to develop a new test method for packaging perforation evaluation to replace the current test method due to the human variables during test and the inconsistency of test results. First, an end user survey was conducted to find out a typical opening pattern which was used by most of the consumers when opening the packaging perforation. Second, the typical opening pattern was further analyzed by an experiment. The opening process was recorded as videos and the relationship between displacement and time was analyzed in Matlab. It was found that the opening process of typical opening pattern was consist of horizontal direction movement and vertical direction movement.