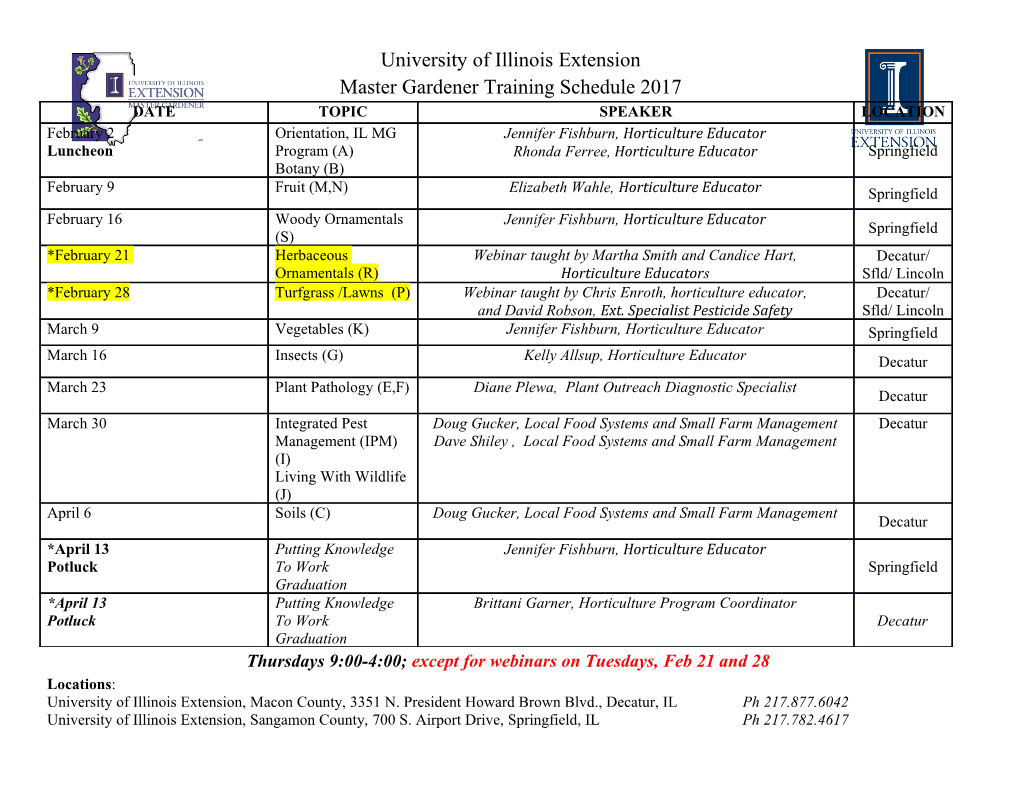
http://72.3.142.35/mghdxreader/jsp/FinalDisplay.jsp;jsessionid=aag1B0... Cataloging-in-Publication Data is on file with the Library of Congress Copyright © 2006, 1998 by Ivana Suchy. All rights reserved. Printed in the United States of America. Except as permitted under the United States Copyright Act of 1976, no part of this publication may be reproduced or distributed in any form or by any means, or stored in a data base or retrieval system, without the prior written permission of the publisher. 1 2 3 4 5 6 7 8 9 0 DOC/DOC 0 1 0 9 8 7 6 5 ISBN 0-07-146271-6 The sponsoring editor for this book was Larry S. Hager and the production supervisor was Richard C. Ruzycka. It was set in Times Roman by International Typesetting and Composition. The art director for the cover was Handel Low. Printed and bound by RR Donnelley. This book is printed on recycled, acid-free paper containing a minimum of 50% recycled, de-inked fiber. McGraw-Hill books are available at special quantity discounts to use as premiums and sales promotions, or for use in corporate training programs. For more information, please write to the Director of Special Sales, McGraw-Hill Professional, Two Penn Plaza, New York, NY 10121-2298. Or contact your local bookstore. Information contained in this work has been obtained by The McGraw-Hill Companies, Inc. (“McGraw-Hill”) from sources believed to be reliable. However, neither McGraw-Hill nor its authors guarantee the accuracy or completeness of any information published herein and neither McGraw-Hill nor its authors shall be responsible for any errors, omissions, or damages arising out of use of this information. This work is published with the understanding that McGraw-Hill and its authors are supplying information but are not attempting to render engineering or other professional services. If such services are required, the assistance of an appropriate professional should be sought. Copyright © 2006, 1998 by Ivana Suchy., McGraw-Hill 1 of 1 11/1/2007 8:46 AM Suchy_CH01.qxd 11/08/05 10:28 AM Page 1 Source: HANDBOOK OF DIE DESIGN CHAPTER 1 BASIC DIE DESIGN AND DIE-WORK INFLUENCING FACTORS 1-1 SHEET-METAL STAMPING IN COMPARISON WITH OTHER METAL FABRICATING PROCESSES In today’s practical and cost-conscious world, sheet-metal parts have already replaced many expensive cast, forged, and machined products. The reason is obviously the relative cheapness of stamped, or otherwise mass-produced parts, as well as greater control of their technical and aesthetic parameters. That the world slowly turned away from heavy, ornate, and complicated shapes, and replaced them with functional, simple, and logical forms only enhanced this tendency. Remember old bath- tubs? They used to be cast and had ornamental legs. Today they are mostly made of coated sheet metal, if not plastics. Manufacturing methods for picture frames, chandeliers, door and wall hardware, kitchen sinks, pots and pans, window frames, and doors were gradually replaced by more practical and less costly techniques. But, sheet-metal stampings can also be used to imitate handmade ornamental designs of previous centuries. Such three-dimensional decorations can be stamped in a fraction of time the repoussé artist of yesterday needed. Metal extrusions, stampings, and forgings, frequently quite complex and elaborate, are used to replace handmade architectural elements. Metal tubing, metal spun products, formings, and drawn parts are often but cheaper substitutes of other, more expensive merchandise. Metal stampings, probably the most versatile products of modern technology, are used to replace parts previously welded together from several components. A well-designed sheet-metal stamping can sometimes eliminate the need for riveting or other fastening processes (Fig. 1-1). Stampings can be used to improve existing designs that often are costly and labor-intensive. Even products already improved upon, with their production expenses cut to the bone, can often be further improved, further innovated, further decreased in cost. The metal stamping die (Fig. 1-2) is an ideal tool that can produce large quantities of parts that are consistent in appearance, quality, and dimensional accuracy. It is a press tool capable of cutting the metal, bending it, drawing its shape into considerable depths, embossing, coining, finishing the edges, curling, and otherwise altering the shape and the outline of the metal part to suit the wildest imaginable design concepts. Figure 1-3 shows samples of these products. 1 Downloaded from Digital Engineering Library @ McGraw-Hill (www.digitalengineeringlibrary.com) Copyright © 2004 The McGraw-Hill Companies. All rights reserved. Any use is subject to the Terms of Use as given at the website. Suchy_CH01.qxd 11/08/05 10:28 AM Page 2 BASIC DIE DESIGN AND DIE-WORK INFLUENCING FACTORS 2 CHAPTER ONE FIGURE 1-1 Threaded part, replaced by other, less expensive means. The word “die” in itself means the complete press tool in its entirety, with all the punches, die buttons, ejectors, strippers, pads, and blocks, simply with all its components assembled together. When commenting on these little technical ingenuities, it is important to stress the role of designers of such products, both artistic and technical. Their thorough knowledge of the manufacturing field will definitely enhance not only the appearance, but the functionality, overall manufacturability, and cost of these parts. FIGURE 1-2 Metal stamping dies. Downloaded from Digital Engineering Library @ McGraw-Hill (www.digitalengineeringlibrary.com) Copyright © 2004 The McGraw-Hill Companies. All rights reserved. Any use is subject to the Terms of Use as given at the website. Suchy_CH01.qxd 11/08/05 10:28 AM Page 3 BASIC DIE DESIGN AND DIE-WORK INFLUENCING FACTORS BASIC DIE DESIGN AND DIE-WORK INFLUENCING FACTORS 3 FIGURE 1-3 Various sheet-metal products. Metal stamping die production output can be enormous, with huge quantities of high- quality merchandise, as shown in Figs. 1-3 and 1-4; pouring forth from the press. For that reason technical ignorance is not readily excusable, as the equal quantities of rejects can be generated just the same way. 1-1-1 Grain of Material Often, parts produced by various manufacturing methods can be redesigned to suit the sheet-metal mass production (Fig. 1-5). FIGURE 1-4 Metal-stamped replacements. Downloaded from Digital Engineering Library @ McGraw-Hill (www.digitalengineeringlibrary.com) Copyright © 2004 The McGraw-Hill Companies. All rights reserved. Any use is subject to the Terms of Use as given at the website. Suchy_CH01.qxd 11/08/05 10:28 AM Page 4 BASIC DIE DESIGN AND DIE-WORK INFLUENCING FACTORS 4 CHAPTER ONE FIGURE 1-5 Additional sheet-metal replacements. When designing such replacements, there are several aspects to be evaluated. The first and probably the most important is the grain of material (Fig. 1-6). Sheet metal of every form, be it a strip or a sheet, displays a definite grain line. It is the direction along which the material was produced in the mill-rolling process. In coils, the grain direction always runs lengthwise, parallel with the longer edge. The grain direction FIGURE 1-6 Grain of materal in sheet-metal strip. Downloaded from Digital Engineering Library @ McGraw-Hill (www.digitalengineeringlibrary.com) Copyright © 2004 The McGraw-Hill Companies. All rights reserved. Any use is subject to the Terms of Use as given at the website. Suchy_CH01.qxd 11/08/05 10:28 AM Page 5 BASIC DIE DESIGN AND DIE-WORK INFLUENCING FACTORS BASIC DIE DESIGN AND DIE-WORK INFLUENCING FACTORS 5 in sheets may vary, and designers must always make themselves familiar with it prior to planning a production run of any kind. In contrast, cast or forged parts display a different grain direction, and in sintered pow- der metal parts the grain is completely gone. For this reason, each of these manufacturing methods can be used to produce items for different applications. For example, a part, shown in Fig. 1-7, will display a different reaction to various forces and stresses when made by the forging method than when obtained through other manu- facturing processes. Where the forging would possess a great resistance to tensile and compressive forces along the A-A line, the same part, when made from sintered powder metal, may break or collapse under the same force. With this shape being cast, the location of the gate is of extreme importance, as it influ- ences the part’s sturdiness in various directions. In the casting gated at the longer end (as pictured in Fig. 1-7b), the opposite end will be more susceptible to breakage, as the molten metal will reach that portion later, when already cooling down. The existence of an open- ing in that area will divide the flow of material and thus create a so-called knit line, along which a separation, resulting in defects and possible breakage, may occur. The same casting, when gated in the middle (Fig. 1-7c), will have an equal breakage proneness at both ends. However, these ends will be somewhat sturdier, as the molten metal will reach them sooner than in the case of Fig. 1-7b. Of course, the existence of openings may have the same detrimental effect described earlier. A similar product, made of sheet metal, as pictured in Fig. 1-8, will also display a grain- dependent behavior; the part with the lengthwise grain will be considerably sturdier along the A-A line of force than the same shape positioned across the grain line. Where used sensibly, the grain in sheet-metal material can serve as a backbone of future products. In formed parts where bends are oriented perpendicularly to the grain of mater- ial, such bends are rarely seen cracking or becoming distorted, and the whole structural FIGURE 1-7 Forces applied to a casting.
Details
-
File Typepdf
-
Upload Time-
-
Content LanguagesEnglish
-
Upload UserAnonymous/Not logged-in
-
File Pages714 Page
-
File Size-