British Aerospace 146-200, D-AMGL No & Type of Engines
Total Page:16
File Type:pdf, Size:1020Kb
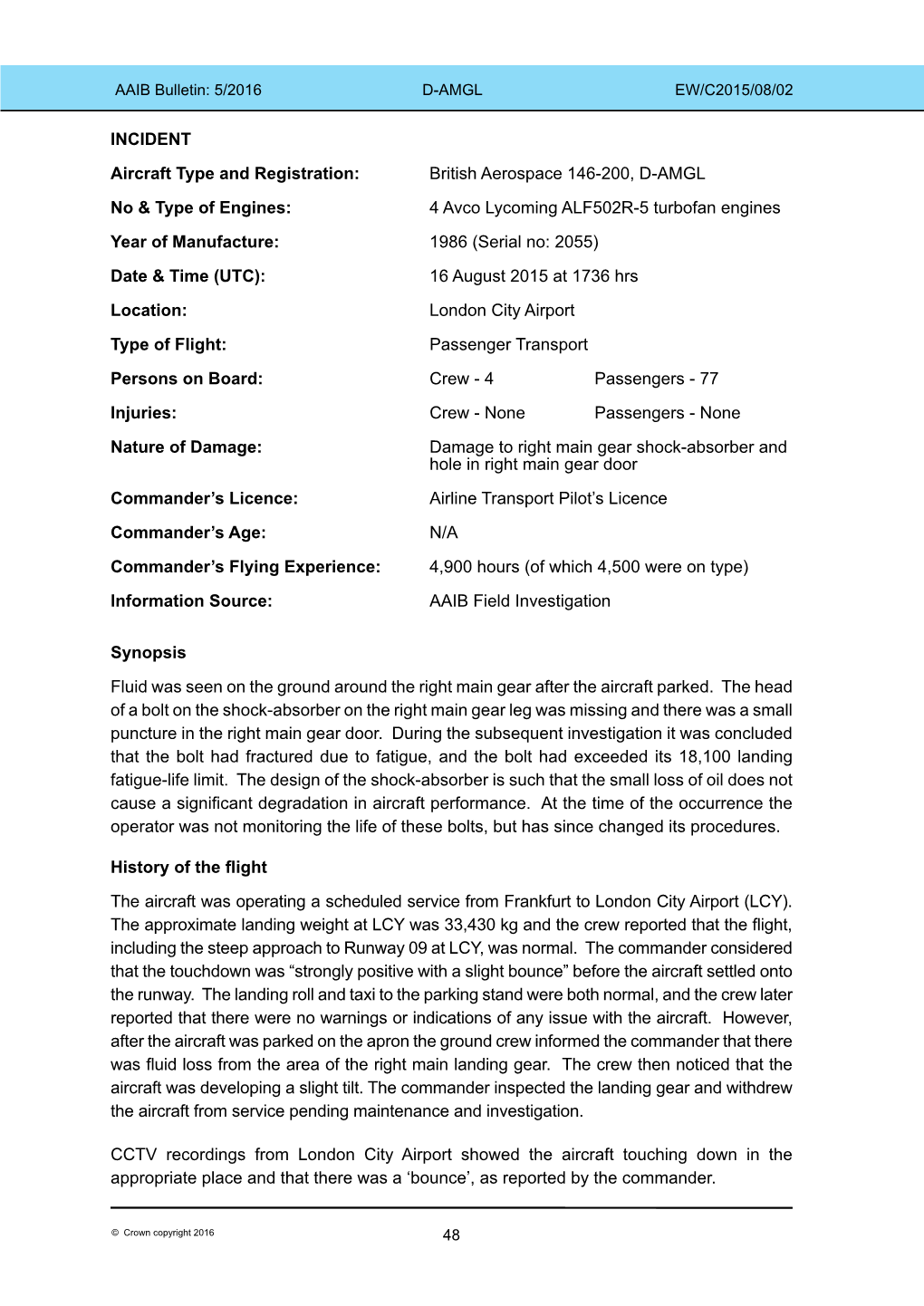
Load more
Recommended publications
-
100-150 Seat Large Civil Aircraft from Canada Conference 05-18-2017
UNITED STATES INTERNATIONAL TRADE COMMISSION In the Matter of: ) Investigation Nos.: 100-TO 150-SEAT LARGE CIVIL AIRCRAFT ) 701-TA-578 AND FROM CANADA ) 731-TTA-1368 (PRELIMINARY) Pages: 1 -289 Place: Washington, D.C. Date: Thursday, May 18, 2017 Ace-Federal Reporters, Inc. Stenotype Reporters 1625 I Street, NW Suite 790 Washington, D.C. 20006 202-347-3700 Nationwide Coverage www.acefederal.com 1 1 THE UNITED STATES INTERNATIONAL TRADE COMMISSION 2 In the Matter of: ) Investigation Nos.: 701-TA-578 3 100-TO 150-SEAT ) and 731-TA-1368 4 LARGE CIVIL AIRCRAFT ) (Preliminary) 5 FROM CANADA ) 6 7 Thursday, May 18, 2017 8 Main Hearing Room 9 U.S. International 10 Trade Commission 11 500 E Street, S.W. 12 Washington, D.C. 13 The meeting commenced, pursuant to notice, at 14 9:30 a.m., before the United States International Trade 15 Commission Investigative Staff. Michael Anderson, 16 Supervisory Investigator, presiding. 17 18 APPEARANCES: 19 On behalf of the International Trade Commission: 20 Michael Anderson, Director of Investigations, 21 (presiding) 22 Douglas Corkran, Supervisory Investigator 23 Carolyn Carlson, Investigator 24 Nannette Christ, International Economist 25 Ace‐Federal Reporters, Inc. 202‐347‐3700 2 1 APPEARANCES (Continued): 2 Charles Yost, Accountant/Auditor 3 Karl von Schriltz, Attorney/Advisor 4 Russell Duncan, Statistician 5 6 William R. Bishop, Supervisory Hearings and 7 Information Officer 8 Sharon Bellamy, Records Management Specialist 9 Tyrell Burch, Legal Document Assistant 10 11 12 13 14 15 16 17 18 19 20 21 22 23 24 25 Ace‐Federal Reporters, Inc. 202‐347‐3700 3 1 OPENING REMARKS: 2 Petitioners (Robert T. -
Report by the Senate Rural and Regional Affairs and Transport References Committee
Parliament of the Commonwealth of Australia Air Safety and Cabin Air Quality in the BAe 146 Aircraft Report by the Senate Rural and Regional Affairs and Transport References Committee OCTOBER 2000 ii © Commonwealth of Australia 2000 ISBN 0 642 71093 7 This document was produced from camera-ready copy prepared by the Senate Rural and Regional Affairs and Transport Legislation Committee, and printed by the Senate Printing Unit, Department of the Senate, Parliament House, Canberra. iii MEMBERS OF THE COMMITTEE Members Senator John Woodley AD, Queensland Chairman Senator Winston Crane LP, Western Australia Deputy Chairman Senator Jeannie Ferris LIB, South Australia Senator Michael Forshaw ALP, New South Wales Senator Sue Mackay ALP, Tasmania Senator Kerry O’Brien ALP, Tasmania Participating Members Senator Abetz Senator Faulkner Senator McLucas Senator Bartlett Senator Ferguson Senator Mason Senator Boswell Senator Gibson Senator S Macdonald Senator Brown Senator Harradine Senator Murphy Senator Buckland Senator Harris Senator Payne Senator Calvert Senator Hutchins Senator Tchen Senator Chapman Senator Knowles Senator Tierney Senator Coonan Senator Lightfoot Senator Watson Senator Crossin Senator McGauran Senator West Senator Eggleston Senator McKiernan Committee Secretariat The Senate Parliament House Canberra ACT 2600 Telephone (02) 6277 3511 Facsimile (02) 6277 5811 Internet www.aph.gov.au/senate Email [email protected] TABLE OF CONTENTS MEMBERS OF THE COMMITTEE ............................................................. iii TABLE -
British Aerospace Jetstream 3102, G-CCPW.Pdf
AAIB Bulletin: 9/2006 G-CCPW EW/C2006/03/06 INCIDENT Aircraft Type and Registration: British Aerospace Jetstream 3102, G-CCPW No & Type of Engines: 2 Garrett AiResearch TPE331-10UGR-516H turboprop engnes Year of Manufacture: 987 Date & Time (UTC): 7 March 2006 at 905 hrs Location: Belfast Cty Arport Type of Flight: Publc Transport (Passenger) Persons on Board: Crew - 2 Passengers - 6 Injuries: Crew - None Passengers - None Nature of Damage: Damage to propellers and three runway lghts Commander’s Licence: Arlne Transport Plot’s Lcence Commander’s Age: 34 years Commander’s Flying Experience: 2,600 hours (of whch 370 were on type) Last 90 days - 110 hours Last 28 days - 40 hours Information Source: Aircraft Accident Report Form submitted by the pilot and further enqures by the AAIB Synopsis While taxiing along Runway 04 to line up on Runway 22 up, the arcraft was cleared by ATC to enter, back track the arcraft’s nose wheel left the paved surface at the and line up on Runway 22. He planned to use the turning end of the runway. Damage was caused to the aircraft’s circle at the threshold of Runway 22 to turn the aircraft propellers and three runway lights. around. Due to the weather, he was using the windscreen wipers intermittently. History of the flight The crew were operatng ther thrd sector of the day from The commander taxied the aircraft slowly down the Belfast City Airport to Ronaldsway, Isle of Man. The centre of Runway 04 towards the threshold of Runway 22 commander was the PF for this sector and taxied the and he could see contnuously the red stop-end lghts aircraft. -
Aircraft Preparation Occurrence Involving Bae 146-300, VH-NJZ Sydney Airport, New South Wales, on 22 January 2019
Aircraft preparation occurrence involving BAe 146-300, VH-NJZ Sydney Airport, New South Wales, on 22 January 2019 ATSB Transport Safety Report Aviation Occurrence Investigation AO-2019-006 Final – 23 June 2020 Released in accordance with section 25 of the Transport Safety Investigation Act 2003 Publishing information Published by: Australian Transport Safety Bureau Postal address: PO Box 967, Civic Square ACT 2608 Office: 62 Northbourne Avenue Canberra, Australian Capital Territory 2601 Telephone: 1800 020 616, from overseas +61 2 6257 2463 (24 hours) Accident and incident notification: 1800 011 034 (24 hours) Email: [email protected] Website: www.atsb.gov.au © Commonwealth of Australia 2020 Ownership of intellectual property rights in this publication Unless otherwise noted, copyright (and any other intellectual property rights, if any) in this publication is owned by the Commonwealth of Australia. Creative Commons licence With the exception of the Coat of Arms, ATSB logo, and photos and graphics in which a third party holds copyright, this publication is licensed under a Creative Commons Attribution 3.0 Australia licence. Creative Commons Attribution 3.0 Australia Licence is a standard form license agreement that allows you to copy, distribute, transmit and adapt this publication provided that you attribute the work. The ATSB’s preference is that you attribute this publication (and any material sourced from it) using the following wording: Source: Australian Transport Safety Bureau Copyright in material obtained from other agencies, private individuals or organisations, belongs to those agencies, individuals or organisations. Where you want to use their material you will need to contact them directly. -
The Connection
The Connection ROYAL AIR FORCE HISTORICAL SOCIETY 2 The opinions expressed in this publication are those of the contributors concerned and are not necessarily those held by the Royal Air Force Historical Society. Copyright 2011: Royal Air Force Historical Society First published in the UK in 2011 by the Royal Air Force Historical Society All rights reserved. No part of this book may be reproduced or transmitted in any form or by any means, electronic or mechanical including photocopying, recording or by any information storage and retrieval system, without permission from the Publisher in writing. ISBN 978-0-,010120-2-1 Printed by 3indrush 4roup 3indrush House Avenue Two Station 5ane 3itney O72. 273 1 ROYAL AIR FORCE HISTORICAL SOCIETY President 8arshal of the Royal Air Force Sir 8ichael Beetham 4CB CBE DFC AFC Vice-President Air 8arshal Sir Frederick Sowrey KCB CBE AFC Committee Chairman Air Vice-8arshal N B Baldwin CB CBE FRAeS Vice-Chairman 4roup Captain J D Heron OBE Secretary 4roup Captain K J Dearman 8embership Secretary Dr Jack Dunham PhD CPsychol A8RAeS Treasurer J Boyes TD CA 8embers Air Commodore 4 R Pitchfork 8BE BA FRAes 3ing Commander C Cummings *J S Cox Esq BA 8A *AV8 P Dye OBE BSc(Eng) CEng AC4I 8RAeS *4roup Captain A J Byford 8A 8A RAF *3ing Commander C Hunter 88DS RAF Editor A Publications 3ing Commander C 4 Jefford 8BE BA 8anager *Ex Officio 2 CONTENTS THE BE4INNIN4 B THE 3HITE FA8I5C by Sir 4eorge 10 3hite BEFORE AND DURIN4 THE FIRST 3OR5D 3AR by Prof 1D Duncan 4reenman THE BRISTO5 F5CIN4 SCHOO5S by Bill 8organ 2, BRISTO5ES -
Qinetiq Group Plc – Notice of Annual General Meeting Ordinary
This document is important and requires your immediate attention. If you are in any doubt as to the action you should take, you should immediately consult your stockbroker, solicitor, accountant or other professional advisor duly authorised under the Financial Services and Markets Act 2000. If you have sold or otherwise transferred all your shares in the Company, please send this document, and the accompanying form of proxy, to the purchaser or transferee or the stockbroker, bank or other agent through whom the sale or transfer was effected for onward transmission to the purchaser or transferee. QinetiQ Group plc – Notice of Annual General Meeting NOTICE IS HEREBY GIVEN that the Annual General Meeting of QinetiQ Group plc (the Company) will be held at the offices of Ashurst LLP, Fruit and Wool Exchange, 1 Duval Square, London E1 6PW on Wednesday 24 July 2019 at 11.00am, or at any adjournment thereof, to consider and, if thought fit, to pass the following 21 resolutions. Resolutions 1 to 16 (inclusive) will be proposed as ordinary resolutions and will be passed if more than 50% of the total votes cast are in favour of each such resolution. Resolutions 17 to 21 (inclusive) will be proposed as special resolutions and will be passed if not less than 75% of the total votes cast are in favour of each such resolution. Voting on all resolutions will be conducted by way of poll rather than a show of hands. Ordinary Resolutions Resolution 1 – Report and Accounts a) to make political donations to political parties and/or independent To receive the accounts and the reports of the Directors and the auditor election candidates not exceeding £100,000 in total; thereon for the financial year ended 31 March 2019. -
BAE Undertakings of the Merger Between British Aerospace Plc And
ELECTRONIC SYSTEMS BUSINESS OF THE GENERAL ELECTRIC COMPANYPLC UNDERTAKINGS GIVEN TO THE SECRETARY OF STATE FOR TRADE AND INDUSTRY BY BRITISH AEROSPACE PLC PURSUANT TO S75G(l) OF THE FAIR TRADING ACT 1973 WHEREAS: (a) On 27 April 1999 British Aerospace pic ("BAE SYSTEMS") agreed with The General Electric Company pic ("GEC") the proposed merger ("the merger") of GEC's defence electronics business Marconi Electronic Systems ("MES") with BAE SYSTEMS; (b) The merger came within the jurisdiction of Council Regulation (EEC) No. 4064/89 on the control of concentrations between undertakings ("the EC Merger Regulation"); (c) Article 296 (ex Article 223) of the EC Treaty permits any Member State to take such measures as it considers necessary to protect its essential security interests which are connected with the production of or trade in arms, munitions and war material; (d) BAE SYSTEMS was requested, under the former Article 223(I)(b) of the EC Treaty, not to notify the military aspects of the merger to the European Commission under the EC Merger Regulation; (e) The military aspects of the merger were consequently considered by Her Majesty's Government under national merger control law; (f) The Secretary of State has power under section 75(1) of the Fair Trading Act 1973 to make a merger reference to the Competition Commission and, under section 7SG(l), to accept undertakings as an alternative to making such a reference; (g) The Secretary of State has requested that the Director General of Fair Trading seek undertakings from BAE SYSTEMS in order to remedy or prevent the adverse effects ofthe merger. -
Government and British Civil Aerospace 1945-64.Pdf
Journal of Aeronautical History Paper No. 2018/04 Government and British Civil Aerospace 1945-64 Professor Keith Hayward Preface This paper is something of a trip down an academic memory lane. My first book, published in the early 1980s, carried a similar title, albeit with a longer time span. While it had the irreplaceable benefit of some first hand memories of the period, the official record was closed. A later history of the UK aircraft industry did refer in part to such material dating from the 1940s, but access to the ‘secret’ historical material of the 1950s and beyond was still blocked by the then “Thirty Year” rule. By the time the restrictions were relaxed to a “Twenty Year” rule or even more by the liberality offered by “Freedom of Information” legislation, I had moved on to the more pressing demands of analysing the world aerospace industry for the SBAC. 1 My years at the Royal Aeronautical Society afforded a bit more scope. Discovery of an archive on the formation of the British Aircraft Corporation, and published by the Royal Aeronautical Society’s Journal of Aeronautical History 2, stimulated a hankering to open more musty files on the 1950s. This led to a series of articles published in the Aviation Historian. However much this satisfied an initial hankering to look back to a critical period in UK aerospace, there were gaps to be filled in the narrative and the analysis. With the encouragement of the Editorial Board of the Journal of Aeronautical History, I have endeavoured to provide a more coherent overview of government policy towards the civil sector. -
Investigation Report of the Aircraft Accident Investigation Bureau
Federal Department of Environment, Transport Energy and Communications No. u1793 Investigation Report of the Aircraft Accident Investigation Bureau on the accident to aircraft AVRO 146-RJ100, HB-IXM, operated by Crossair under flight number CRX 3597, on 24 November 2001 near Bassersdorf/ZH This report has been prepared for the purpose of accident/incident prevention. The le- gal assessment of accident/incident causes and circumstances is no subject of the ac- cident investigation (Art. 24 Air Navigation Law). The language of the valid formulation of this report is German. Within 30 days after receipt of the investigation report, any person giving proof of a well-founded interest in the investigation result may request the report to be examinated by the Review Board (Eidg. Flug- unfallkommission – EFUK) for completeness and conclusiveness. Bundeshaus Nord, CH-3003 Berne Investigation report CRX 3597 Ve 23.01.04 Table of contents Brief presentation........................................................................................................10 Investigation ...............................................................................................................11 1 Factual information ..........................................................................13 1.1 Prior history and history of the flight ..........................................................13 1.1.1 Prior history...................................................................................................................13 1.1.1.1 Aircraft .....................................................................................................................13 -
GKN Aerospace-A Global First Tier Provider
GKN Aerospace-A global First Tier Provider SW Regional Development Agency & Japanese Aerospace Mission – Great Nagoya 23rd March 2010 1 Agenda Presentations • GKN Aerospace & Composite Capability • Filton • Research & Technology Initiatives Q&A, Open Discussion & Lunch Site Tour • Manufacturing • A380 FTE Assembly • Systems 2 GKN plc GKN can trace its roots directly to the origins of the industrial revolution Once the world leader in iron and steel production The business changed its focus over the last 25 years of the Dowlais Ironworks, Mid 19th Century 20th century Now a leading supplier to the world's automotive and aerospace primes Strategic focus on high growth and high technology 3 GKN: leadership in four specialist, global sectors $7616M- 2008 Revenue Automotive – sales $4032m Powder Metallurgy – sales $1019m OffHighway – sales $912m Aerospace – sales $1653m 4 GKN Global Footprint Zimbabwe Argentina USA Australia United Kingdom Austria Thailand Belgium Taiwan Brazil Switzerland Canada Sweden Czech Republic Spain Chile South Africa China Slovenia Colombia Singapore Denmark Portugal France Poland Finland Philippines Operating in over 30 countries Norway Germany Namibia 35,500 people in subsidiaries Greece Netherlands and Hong Kong Mexico joint ventures India Malaysia Republic of Ireland Korea Israel Japan Italy 5 GKN Aerospace $2.4Bn 2009 Market Business Mix Sector Customer Base 6 GKN Aerospace Organisation Integrated Aerostructures Propulsion Systems Special Products $1.6BN $500M $300M • Focussed business sector groups • Coordinated -
Desind Finding
NATIONAL AIR AND SPACE ARCHIVES Herbert Stephen Desind Collection Accession No. 1997-0014 NASM 9A00657 National Air and Space Museum Smithsonian Institution Washington, DC Brian D. Nicklas © Smithsonian Institution, 2003 NASM Archives Desind Collection 1997-0014 Herbert Stephen Desind Collection 109 Cubic Feet, 305 Boxes Biographical Note Herbert Stephen Desind was a Washington, DC area native born on January 15, 1945, raised in Silver Spring, Maryland and educated at the University of Maryland. He obtained his BA degree in Communications at Maryland in 1967, and began working in the local public schools as a science teacher. At the time of his death, in October 1992, he was a high school teacher and a freelance writer/lecturer on spaceflight. Desind also was an avid model rocketeer, specializing in using the Estes Cineroc, a model rocket with an 8mm movie camera mounted in the nose. To many members of the National Association of Rocketry (NAR), he was known as “Mr. Cineroc.” His extensive requests worldwide for information and photographs of rocketry programs even led to a visit from FBI agents who asked him about the nature of his activities. Mr. Desind used the collection to support his writings in NAR publications, and his building scale model rockets for NAR competitions. Desind also used the material in the classroom, and in promoting model rocket clubs to foster an interest in spaceflight among his students. Desind entered the NASA Teacher in Space program in 1985, but it is not clear how far along his submission rose in the selection process. He was not a semi-finalist, although he had a strong application. -
Aircraft Family Concept for High Performance Transport Aircrafts
INTERNATIONAL JOURNAL OF MECHANICS Aircraft Family Concept for High Performance Transport Aircrafts Prasetyo Edi Boeing-MD-95-20/-30/-50, IPTN's N-2130, Fairchild Abstract— The objective of this research is to make a feasibility Dornier's 728JET and Bombardier's Canadair Regional Jet study of the aircraft family concepts using a combined Hybrid Laminar (CRJ) Series 700 programmed. Flow Control - Variable Camber Wing (HLFC-VCW) for a high Only three models of the above aircrafts are smaller than performance Advanced Technology Regional Aircraft (ATRA). The 120-seats, the Avro RJ-70/-85/-100/-115, the Fokker-70/-100 prediction of ATRA’s performance used computational fluid dynamic and empirical methods. The aircraft family concept using a combined and the Boeing 737-500/-600. The Avro RJ and the Boeing HLFC–VCW is feasible for ATRA aircraft family from aerodynamic 737 family are 6 abreast seating, while the Fokker family is 5 point of view. abreast seating. In order to increase their profit, many Aircraft Keywords— Aircraft family concept, high performance transport manufacturers , i.e. : Airbus, Boeing, McDonnell Douglas, aircraft, hybrid laminar flow control, variable camber wing, Fokker, British Aerospace, IPTN/IAe, etc., have developed aerodynamics, aircraft design, advanced technology, regional aircraft. their aircraft family based on one wing and one fuselage cross section to reduce development costs. For one fuselage cross I. INTRODUCTION section aircraft family, alternatives concepts for Regional PPROXIMATELY 65% of the world's commercial jet Airliner family are : Afleet consists of narrow-body, single-aisle aircraft with a 1. fixed wing geometry on mid-size, then direct operating cost capacity of 70 to 170 seats.