Development and Large Volume Production of Extremely High Current Density Yba2cu3o7 Superconducting Wires for Fusion A
Total Page:16
File Type:pdf, Size:1020Kb
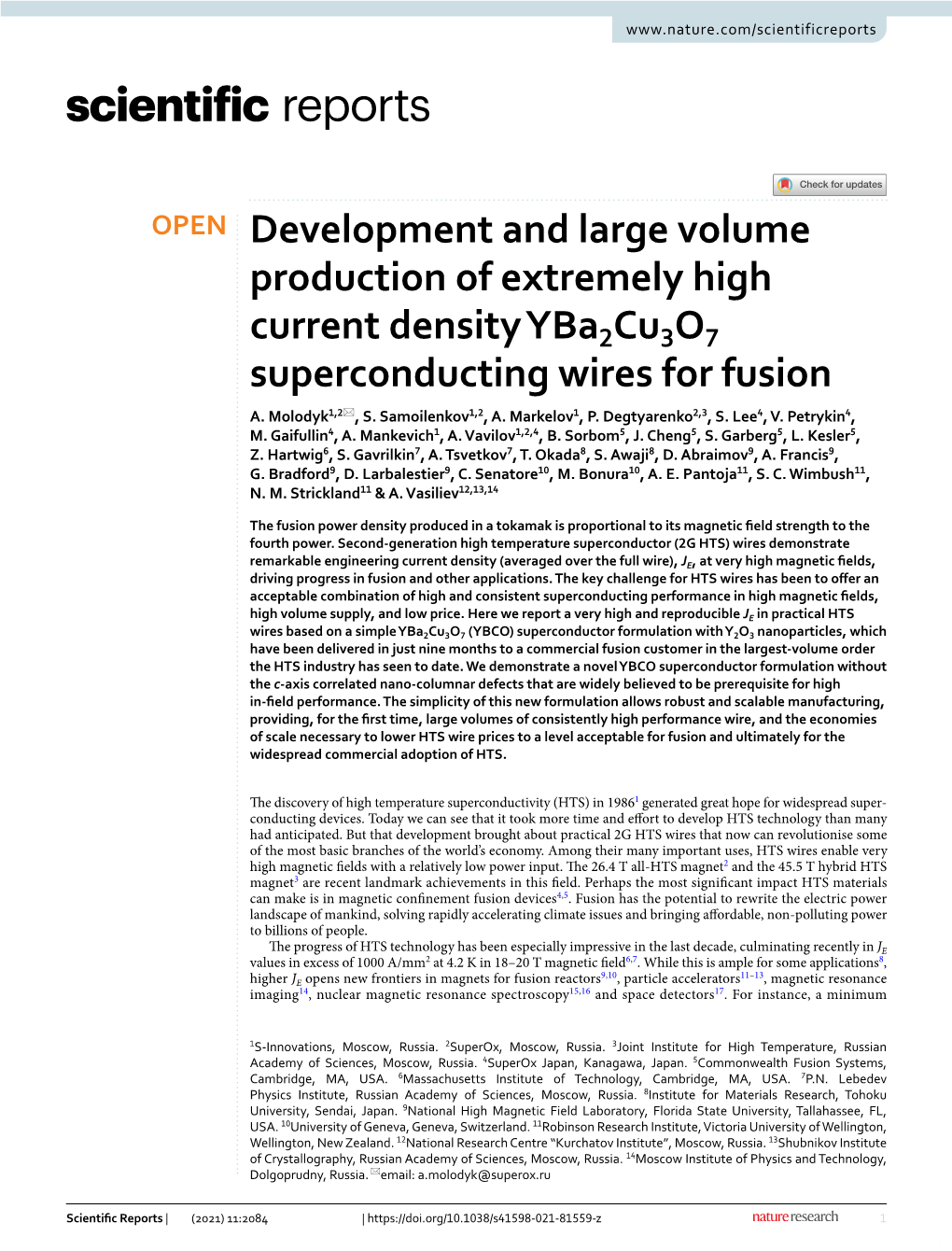
Load more
Recommended publications
-
Progress in Wire Fabrication of Iron-Based Superconductors
Progress in wire fabrication of iron-based superconductors Yanwei Ma* Key Laboratory of Applied Superconductivity, Institute of Electrical Engineering, Chinese Academy of Sciences, Beijing 100190, China Abstract: Iron-based superconductors, with Tc values up to 55 K, are of great interest for applications, due to their lower anisotropies and ultrahigh upper critical fields. In the past 4 years, great progress has been made in the fabrication of iron-based superconducting wires and tapes using the powder-in-tube (PIT) processing method, including main three types of 122, 11, and 1111 iron-based parent compounds. In this article, an overview of the current state of development of iron-based superconducting wires and tapes is presented. We focus on the fabrication techniques used for 122 pnictide wires and tapes, with an emphasis on their meeting the critical current requirements for making high-performance conductors, such as a combination of using Ag sheath, addition element and optimized heat treatment to realize high Jc, ex situ process employed to reduce non-superconducting phases and to obtain a high relative density, and a texture control to improve grain connectivity. Of particular 4 2 interest is that so far transport Jc values above 10 A/cm at 4.2 K and 10 T are obtained in 122 type tapes, suggesting that they are prospective candidates for high-field applications. Finally, a perspective and future development of PIT pnictide wires are also given. * E-mail: [email protected] 1 Contents 1. Introduction ........................................................................................................... -
Selected High-Temperature Superconducting Electric Power Products
Selected High-Temperature Superconducting Electric Power Products Prototypes are outperforming design goals full-scale utility applications are moving onto the power system and ... Modernizing the Existing Electricity Infrastructure Superconductivity Program for Electric Systems•• Office of Power Delivery U.S. Department of Energy January 2000 HIGH TEMPERATURE SUPERCONDUCTING POWER PRODUCTS CAPTURE THE ATTENTION OF UTILITY ENGINEERS AND PLANNERS Soon superconductors could be so common that we will drop the “super” and refer to them simply as conductors Critical Role of Wire The application of superconductors to electric power systems has been pursued for more than 30 years. This persistence is starting to pay off and utilities that once politely acknowledged the long-term potential of superconducting applications are now paying close attention to several prototype devices that are being tested or are nearing testing on utility systems. What has prompted this interest is the development of electric wires that become superconducting when cooled to the affordable operating-temperature realm of liquid nitrogen as well as the development of coils, magnets, conductors, and machines and power components made with these wires. Superconducting wires have as much as 100 times the current carrying capacity as (Courtesy of American Superconductor Corp.) ordinary conductors. Flexible HTS conductors promise reduced A Real Need operating costs and many other benefits when incorporated into electric power devices. They can change the way power is managed and The timing is right for superconducting solutions consumed. to emerging business problems. Power generation and transmission equipment is aging and must be replaced. Environmental considerations are increasing. Utilities are changing the way they evaluate capital investments. -
Sn and Ti DIFFUSION, PHASE FORMATION, STOICHIOMETRY, and SUPERCONDUCTING PROPERTIES of INTERNAL-Sn-TYPE Nb3sn CONDUCTORS
Sn AND Ti DIFFUSION, PHASE FORMATION, STOICHIOMETRY, AND SUPERCONDUCTING PROPERTIES OF INTERNAL-Sn-TYPE Nb3Sn CONDUCTORS A Thesis Presented in Partial Fulfillment of the Requirements for The Degree of Master of Science in the Graduate School of the Ohio State University By Rakesh Kumar Dhaka, B. Tech. ***** The Ohio State University 2007 Masters Examination Committee Professor Mike Sumption, Adviser Professor John Morral, Adviser Professor Katharine Flores ABSTRACT In the present work the diffusion of Sn through the interfilamentary matrix within a subelement and the formation of the associated Cu-Sn intermetallics were observed experimentally for several different Nb3Sn internal-Sn type strands during the pre- reaction part of the heat treatment. An analytical-based model was then developed to determine the time and temperature dependence of Sn-diffusion through the Cu matrix of Nb3Sn subelements. The output of the model is in the form of radial positions of , and phases as a function of time during pre-reaction heat treatment process. These predicted radial positions can be used to determine the optimum heat treatment parameters. The model was then compared to the experimental results. Experimental results for Ti-bearing superconductor strands were also discussed. Following the pre-reaction heat treatment studies, the effects of Titanium doping in presence of Tantalum on the kinetics of Nb3Sn formation and superconducting properties of internal-tin type strands were examined. A series of internal-tin type Nb3Sn sublements which had Nb-7.5wt%Ta filaments and various levels of Ti doping were investigated. Titanium was introduced into the Sn core of the subelements such that the core contained 0 at% to 2.8 at% Ti before reaction. -
High Performance Magnesium Diboride (Mgb ) Superconductors
High Performance Magnesium Diboride (MgB2) Superconductors: Towards the Prospect for Commercialization M.S.A. Hossain (ARC DECRA Fellow) The Australian National University– 16/04/2014 Research Programs at ISEM/AIIM Faculty . Applied Superconductivity Group • Bulk • Wire • Tape • Cable • Thin Film . Energy Storage Group . Spintronics and Electronic Materials Group . Thin Film Technology Group . Terahertz Science, Solid State Physics Group . Nanostructure Materials Group . Advanced Photovoltaic Materials Group ISEM Performance Profile highlight ISEM Team: 40 research staff (12 ARC fellows) and more than 80 PhD Seven research program centred on energy and electronics Electrification Program leader in Automotive CRC 2020 More than 50% citations in Li ion battery and superconductivity from ISEM in Australia ISEM is ranked at first place in magnesium diboride supercondcutors and eighth place in Li ion battery research in terms of outputs since 2001 105 PhD graduates widely spread across five continents since 1994 50 ARC fellowship awards to ISEM since 1995 80 ARC projects since 2000 12% publications, 15% ARC funding and 24% citations of UoW are from ISEM $80m for building & $20m for facilities for research infrastructure Member of CoE, ANFF and Flagship Bao Steel Joint Centre with other 3 Universities; Network with more than 50 institutions world-wide Strong links with more than 10 industry partners ERA assessment ranked at 5 for materials engineering, materials chemistry, physical chemistry and interdisciplinary engineering of UOW Superconductivity? Applications • Making a good superconducting product is a formidable interdisciplinary problem Wire cost Wire performance Engineering Cryogenics MgB2 Very simple crystal structure Very high current densities Polycristalline materials observed in films carry large currents Moderately high Tc Tc of 39K Factor of 10 larger than in bulks; room for large improvement in wires still available from R&D MgB2 presents very Good mechanical properties Potentially high critical field 60 1.2 promising features Sample No. -
(Nb-Ti) Superconducting Joints for Persistent-Mode Operation
www.nature.com/scientificreports OPEN Niobium-titanium (Nb-Ti) superconducting joints for persistent-mode operation Received: 21 June 2019 Dipak Patel1,2, Su-Hun Kim1,3, Wenbin Qiu1, Minoru Maeda4, Akiyoshi Matsumoto2, Accepted: 26 August 2019 Gen Nishijima2, Hiroaki Kumakura2, Seyong Choi4 & Jung Ho Kim1 Published: xx xx xxxx Superconducting joints are essential for persistent-mode operation in a superconducting magnet system to produce an ultra-stable magnetic feld. Herein, we report rationally designed niobium- titanium (Nb-Ti) superconducting joints and their evaluation results in detail. For practical applications, superconducting joints were fabricated by using a solder matrix replacement method with two types of lead-bismuth (Pb-Bi) solder, including Pb42Bi58 as a new composition. All the joints attained a critical current of >200 A below 1.43 T at 4.2 K. Our optimized superconducting joining method was tested in a closed-loop coil, obtaining a total circuit resistance of 3.25 × 10−14 Ω at 4.2 K in self-feld. Finally, persistent-mode operation was demonstrated in an Nb-Ti solenoid coil with a persistent-current switch. This work will pave the way to developing high-performance Nb-Ti superconducting joints for practical applications. Superconducting magnets are used to produce a strong magnetic feld in a compact system, which otherwise cannot be attained using conventional copper (Cu) based magnets. Niobium-titanium (Nb-Ti) with a critical temperature (Tc) of 9.2 K is usually used to fabricate superconducting magnets for various practical applications. One of the distinct features of Nb-Ti that makes it ideal for most commercial applications is the possibility to produce reliable “superconducting joints”. -
Thermal Analysis and Simulation of the Superconducting Magnet in the Spinquest Experiment at Fermilab
Thermal Analysis and Simulation of the Superconducting Magnet in the SpinQuest Experiment at Fermilab Z. Akbar∗and D. Keller† University of Virginia November 18, 2020 Abstract The SpinQuest experiment at Fermilab aims to measure the Sivers asymmetry for theu ¯ and d¯ sea quarks in the range of 0.1 < xB < 0.5 using the Drell-Yan production of dimuon pairs. A nonzero Sivers asym- metry would provide an evidence for a nonzero orbital angular momentum of sea quarks. The proposed beam intensity is 1.5 × 1012 of 120 GeV unpo- larized proton/sec. The experiment will utilize a target system consisting 4 of a 5T superconducting magnet, NH3 and ND3 target material, a He evaporation refrigerator, a 140 GHz microwave source and a large pump- ing system. The expected average of the target polarization is 80% for the proton and 32% for the deuteron. The polarization will be measured with three NMR coils per target cell. A quench analysis and simulation of the superconducting magnet is performed to determine the maximum intensity of the proton beam be- fore the magnet transitions to a resistive state. Simulating superconduc- tor as they transition to a quench is notoriously very difficult. Here we approach the problem with the focus on producing an estimate of the maximum allowable proton beam intensity given the necessary instru- mentation materials in the beam-line. The heat exchange from metal to helium goes through different transfer and boiling regimes as a function of temperature, heat flux, and transferred energy. All material proper- ties are temperature dependent. A GEANT-4 based simulation is used to calculate the heat deposited in the magnet and the subsequent cooling processes are modeled using the COMSOL Multiphysics simulation pack- age. -
Synthesis and Characterization of Superconducting Ferropnictide Bulks and Wires Jeremy Weiss
Florida State University Libraries Electronic Theses, Treatises and Dissertations The Graduate School 2015 Synthesis and Characterization of Superconducting Ferropnictide Bulks and Wires Jeremy Weiss Follow this and additional works at the FSU Digital Library. For more information, please contact [email protected] FLORIDA STATE UNIVERSITY THE GRADUATE SCHOOL SYNTHESIS AND CHARACTERIZATION OF SUPERCONDUCTING FERROPNICTIDE BULKS AND WIRES By JEREMY WEISS A Dissertation submitted to the Department of Materials Science and Engineering in partial fulfillment of the requirements for the degree of Doctor of Philosophy Degree Awarded: Spring Semester, 2015 Jeremy Weiss defended this dissertation on April 9, 2015. The members of the supervisory committee were: Eric Hellstrom Professor Directing Dissertation Gregory Boebinger University Representative David Larbalestier Committee Member Theo Siegrist Committee Member Per Arne Rikvold Committee Member The Graduate School has verified and approved the above-named committee members, and certifies that the dissertation has been approved in accordance with university requirements. ii This dissertation is dedicated to the memory of Professor James Brooks who served on this dissertation advisory committee until his passing in Fall 2014 iii ACKNOWLEDGMENTS Firstly, I would like to thank David Larbalestier for giving me the undergraduate opportunity to do the preliminary lab work that sparked an interest in applied research and ultimately lead to the following dissertation. To vaguely paraphrase the first toast of his I heard; an observation relevant to my developing career: “We never could have guessed that we would have ended up here, but we stumble through life as opportunities present themselves and it really is fascinating how it seems to work out for us.” It was David who introduced me to Jianyi Jiang who mentored me for two and a half years as an undergraduate. -
CERN-ACC-2020-0021.Pdf
CERN – EUROPEAN ORGANIZATION FOR NUCLEAR RESEARCH CLIC – Note – 1160 PERFORMANCE OF MGB2 SUPERCONDUCTOR DEVELOPED FOR HIGH-EFFICIENCY KLYSTRON APPLICATIONS H. Tanaka3, T.Suzuki3, M. Kodama3, T. Koga3, H. Watanabe3, A. Yamamoto1,2 and S. Michizono2 1CERN, Geneva, Switzerland 2KEK, Tsukuba, Japan 3Hitachi, Tokyo, Japan Abstract An 8-km long MgB2 wire for a prototype klystron magnet was made and evaluated. The wire was made by a typical in situ method; it has 10 filaments and 0.67 mm in outer diameter. The homogeneity of Ic of this wire was evaluated by several methods. Deviation of Ic values in short sample wires was very small. In addition, the current sharing temperature of the MgB2 magnet (made of two reels of wire 2.9 km long each) agreed well with the estimated value of the Ic-B-T properties in short sample wires. Based on the obtained results, it can be said that the Ic properties of the entire wire length are quite uniform. CERN-ACC-2020-0021 17/09/2020 Presented at the Magnet Technology Conference, Vancouver, Canada, 23-27 Sep 2019 Geneva, Switzerland September 2020 IEEE TRANSACTIONS ON APPLIED SUPERCONDUCTIVITY, VOL. 30, NO. 4, JUNE 2020 6200105 Performance of MgB2 Superconductor Developed for High-Efficiency Klystron Applications Hideki Tanaka , Takaaki Suzuki, Motomune Kodama, Tomoyuki Koga, Hiroyuki Watanabe , Akira Yamamoto, and Shinichiro Michizono Abstract—An8-kmlongMgB2 wire for a prototype klystron cooling the Joule heat of the magnet [9], and in the case of a magnet was made and evaluated. The wire was made by a typical Nb-Ti superconducting magnet without liquid helium, the AC in situ method; it has 10 filaments and 0.67 mm in outer diame- plug power is 6 kW,as shown in a previous study [10]. -
Development of High Temperature Superconductors for Wind Energy
Development of High Temperature Superconductors for Wind Energy Venkat Selvamanickam Department of Mechanical Engineering Advanced Manufacturing Institute Texas Center for Superconductivity University of Houston http://www2.egr.uh.edu/~vselvama/ Iowa State University, February 6, 2017 1 Outline • Superconductors for energy applications • High Temperature Superconductor Wire Manufacturing • Enhanced HTS Wire for Wind Energy and other Applications • Path Forward: High-yield Manufacturing of High Performance Superconductors 6/9/2017 2 2 Superconductors for energy applications 3 Two-thirds of primary energy is lost in electricity generation/use https://flowcharts.llnl.gov/ 4 High temperature superconductors : Unique materials with great potential Resistance High Temperature Superconductor (HTS) Low Temperature Superconductor (LTS) Conductor e.g. Copper Zero resistance !!! Temperature Liquid helium (4 K) Liquid nitrogen (77 K) RoomTemperature (300 K) Current carrying capability of copper ~ 100 A/cm2 Current carrying capability of superconductor ~ 5,000,000 A/cm2 5 Low Temperature Superconductors are widely used in medical applications Medical Devices: MRI http://www.magnet.fsu.edu/education/tutorials/magnetacademy/mri/index.htm MRI is a $ 3B industry enabled by superconductors. Low Temperature Superconductors enable Maglev transportation 7 Courtesy of Herman ten Kate Superconducting powerlines for long distance transmission of renewable energy • 5 to 10 times more capacity than comparable conventional cables Can be used in existing underground conduits saves trenching costs • Much reduced right of way (25 ft for 5 GW, 200 kV compared to 400 feet for 5 GW, 765 kV for conventional overhead lines) 12,000 miles of new transmission lines needed for 20% Wind Energy 9 Significant opportunities for CO2 reductions by wind energy 10 Large and high power wind turbines preferred for reducing cost of wind energy = M. -
Superconductivity
Superconductivrty - Wikipedia, the free encyclopedia http://en. wikipedia. org/rviki/S uperconductivity Superconductivity From Wikipedia, the free encyclopedia Superconductivity occurs in certain materials at very low temperatures. When superconductive, a material has an electrical resistance of exactly zero and no interior magnetic field (the Meissner effect). It was discovered by Heike Kamerlingh Onnes in 1911. Like ferromagnetism and atomic spectral lines, superconductivity is a quantum mechanical phenomenon. It cannot be understood simply as the idealization of "perfect conductivity" in classical physics. A magnet levitating above a high-temperature The electrical resistivity of a metallic conductor decreases gradually as superconductor, cooled with the temperature is lowered. However, in ordinary conductors such as liquid nitrogen. Persistent copper and silveE this decrease is limited by impurities and other electric current florvs on the surface of the superconductor, defects. Even near absolute zero, a real sample of copper shows some acting to exclude the magnetic resistance. In a superconductor however, despite these imperfections, field of the magnet (the the resistance drops abruptly to zero when the material is cooled below Meissner effect). This current its critical temperature. An electric current flowing in a loop of effectively forms an electromagnet that repels the superconducting wire can persist indefinitely with no power rour"".[1] masnet. Superconductivity occurs in many materials: simple elements like tin and aluminium, various metallic alloys and some heavily-doped semiconductors. Superconductivity does notoccurin noble metals like gold and silver, norinpure samples of ferromagnetic metals. In 1986, it was discovered that some cuprate-perovskite ceramic materials have critical temperatures of more than 90 kelvin. -
Garfias Master Thesis
Eindhoven University of Technology MASTER ReBCO-based superconducting switch for high current applications Garfias Davalos, D.A. Award date: 2018 Link to publication Disclaimer This document contains a student thesis (bachelor's or master's), as authored by a student at Eindhoven University of Technology. Student theses are made available in the TU/e repository upon obtaining the required degree. The grade received is not published on the document as presented in the repository. The required complexity or quality of research of student theses may vary by program, and the required minimum study period may vary in duration. General rights Copyright and moral rights for the publications made accessible in the public portal are retained by the authors and/or other copyright owners and it is a condition of accessing publications that users recognise and abide by the legal requirements associated with these rights. • Users may download and print one copy of any publication from the public portal for the purpose of private study or research. • You may not further distribute the material or use it for any profit-making activity or commercial gain Department of Applied Physics ReBCO-based superconducting switch for high current applications MSc Science and Technology of Nuclear Fusion Diego Armando Garfias Dávalos Supervisors: H.H.J ten Kate (UT,CERN) and A. Dudarev (CERN) N.J. Lopes Cardozo (TU/e) Eindhoven, Netherlands. November 2018 Project developed at the Experimental Physics Department ATLAS Detector Operation Group (EP - ADO) Contents List of Figures iii List of Tables vi Glossary vii Acronyms viii Abstract viii 1 Introduction 1 1.1 Brief energy panorama . -
Ultra-Lightweight Superconducting Wire Based on Mg, B, Ti and Al P
www.nature.com/scientificreports OPEN Ultra-lightweight superconducting wire based on Mg, B, Ti and Al P. Kováč 1, I. Hušek1, A. Rosová1, M. Kulich1, J. Kováč1, T. Melišek1, L. Kopera 1, M. Balog2 & P. Krížik2 Received: 4 April 2018 Actually, MgB2 is the lightest superconducting compound. Its connection with lightweight metals like Accepted: 5 July 2018 Ti (as barrier) and Al (as outer sheath) would result in a superconducting wire with the minimal mass. Published: xx xx xxxx However, pure Al is mechanically soft metal to be used in drawn or rolled composite wires, especially if applied for the outer sheath, where it cannot provide the required densifcation of the boron powder inside. This study reports on a lightweight MgB2 wire sheathed with aluminum stabilized by nano-sized γ-Al2O3 particles (named HITEMAL) and protected against the reaction with magnesium by Ti difusion barrier. Electrical and mechanical properties of single-core MgB2/Ti/HITEMAL wire made by internal magnesium difusion (IMD) into boron were studied at low temperatures. It was found that the ultra- lightweight MgB2 wire exhibited high critical current densities and also tolerances to mechanical stress. This predetermines the potential use of such lightweight superconducting wires for aviation and space applications, and for powerful ofshore wind generators, where reducing the mass of the system is required. Although many superconducting elements and compounds have been discovered1, only few of them can be used for thermally and mechanically stabilized long length wires with high current densities. Instead of high power cables and high feld magnets, superconducting wires make possible the design of powerful and lightweight superconducting stators and rotors for aircraf engines and generators2,3.