A Review and Prospects for Nb3sn Superconductor Development
Total Page:16
File Type:pdf, Size:1020Kb
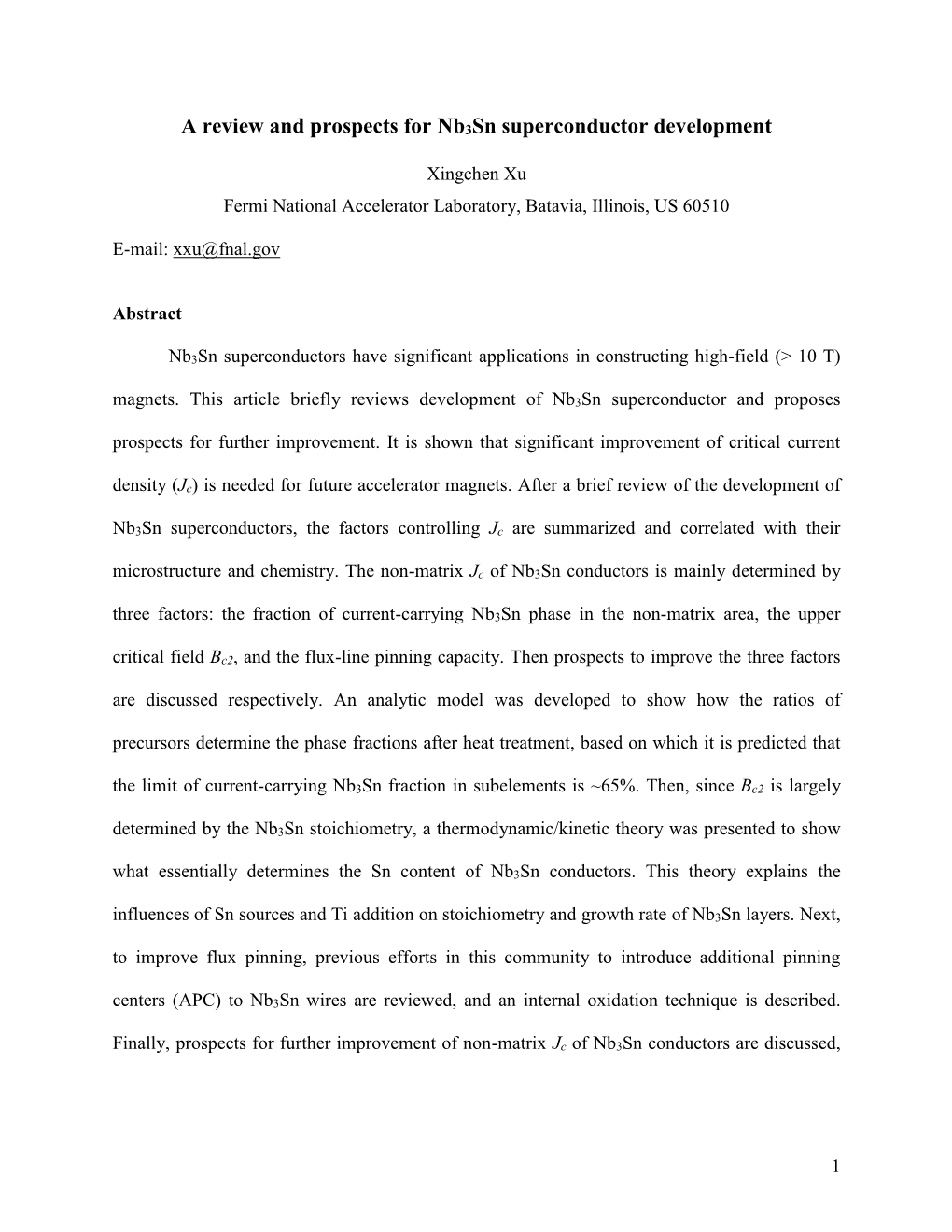
Load more
Recommended publications
-
Applications of High Temperature Superconductors
FEATURES Applications of high temperature superconductors T.M. Silver, s.x. Dou and J.x. fin Institute for Superconducting and Electronic Materials, University ofWollongong, Wollongong, NSW2522, Australia ost ofus are familiar with the basic idea ofsuperconductivi magnetic separators, these losses may account for most of the M ty, thata superconductor can carrya currentindefinitely in a energy consumed in the device. Early prototypes for motors, closed loop, without resistance and with no voltage appearing. In transmission lines and energy storage magnets were developed, a normal metal, such as copper, the free electrons act indepen but they were never widely accepted. There were important rea dently. They will move under the influence of a voltage to form a sons for this, apart from the tremendous investment in existing current, but are scattered off defects and impurities in the metal. technology. In most superconducting metals andalloys the super This scattering results in energy losses and constitutes resistance. conductivity tends to fail in self-generated magnetic fields when In a superconducting metal, such as niobium, resistance does not the current densities through them are increased to practicallev occur, because under the right conditions the electrons no longer els. A second problem was the cost and complexity of operating act as individuals, but merge into a collective entity that is too refrigeration equipment near liquid helium temperatures large to 'see' any imperfections. This collective entity, often (4 K, -269°C). Removing one watt of heat generated at 4 K described as a Bose condensate, can be described by a single demands about 1000 W ofrefrigeration power at room tempera macroscopic quantum mechanical wave function. -
Progress in Wire Fabrication of Iron-Based Superconductors
Progress in wire fabrication of iron-based superconductors Yanwei Ma* Key Laboratory of Applied Superconductivity, Institute of Electrical Engineering, Chinese Academy of Sciences, Beijing 100190, China Abstract: Iron-based superconductors, with Tc values up to 55 K, are of great interest for applications, due to their lower anisotropies and ultrahigh upper critical fields. In the past 4 years, great progress has been made in the fabrication of iron-based superconducting wires and tapes using the powder-in-tube (PIT) processing method, including main three types of 122, 11, and 1111 iron-based parent compounds. In this article, an overview of the current state of development of iron-based superconducting wires and tapes is presented. We focus on the fabrication techniques used for 122 pnictide wires and tapes, with an emphasis on their meeting the critical current requirements for making high-performance conductors, such as a combination of using Ag sheath, addition element and optimized heat treatment to realize high Jc, ex situ process employed to reduce non-superconducting phases and to obtain a high relative density, and a texture control to improve grain connectivity. Of particular 4 2 interest is that so far transport Jc values above 10 A/cm at 4.2 K and 10 T are obtained in 122 type tapes, suggesting that they are prospective candidates for high-field applications. Finally, a perspective and future development of PIT pnictide wires are also given. * E-mail: [email protected] 1 Contents 1. Introduction ........................................................................................................... -
Hitachi's Leading Superconducting Technologies
Hitachi’s Leading Superconducting Technologies 290 Hitachi’s Leading Superconducting Technologies Shohei Suzuki OVERVIEW: Over 30 years have passed since Hitachi began researching Ryoichi Shiobara superconductors and superconducting magnets. Its scope of activities now encompasses everything from magnetically levitated vehicles and nuclear Kazutoshi Higashiyama fusion equipment to AC generators. Three big projects that use Hitachi Fumio Suzuki superconductors are currently underway in Japan: the Yamanashi Maglev Test Line, the Large Helical Device (LHD) for nuclear fusion and the 70- MW model of superconducting power generator. Hitachi has played a vital role in these projects with its materials and application technologies. In the field of high-temperature superconducting materials, Hitachi has made a lot of progress and has set a new world record for magnetic fields. INTRODUCTION is cryogenic stability because of the extremely low HITACHI started developing superconducting temperatures, but we have almost solved this problem technology in the late 1950’s. At first, it focused on by developing fine multiple-filament superconductors superconducting magnets for magneto-hydro- and various materials for stabilization matrixes, both dynamics (MHD) power generators, but eventually of which operate at liquid helium temperature (4 K), broadened its research to applications such as as well as superconductor integration technology and magnetically levitated vehicles, nuclear fusion precise winding technology. These new developments equipment, and high energy physics. Recently have led to a number of large projects in Japan. They Hitachi’s activities have spread to the medical field are (1) the world’s largest (70 MW) model super- (magnetic-resonance-imaging technology) and other conducting generator for generating electric power, (2) fields (AC power generators and superconducting the Yamanashi Maglev Test Line train, which may magnetic energy storage). -
Design of a Superconducting DC Wind Generator
Design of a superconducting DC wind generator zur Erlangung des akademischen Grades eines DOKTOR-INGENIEURS von der Fakultät für Elektrotechnik und Informationstechnik des Karlsruher Instituts für Technologie (KIT) genehmigte DISSERTATION von M. Eng. Yingzhen Liu geb. in: Hebei, China Tag der mündlichen Prüfung: 26. 01. 2018 Hauptreferent: Prof. Dr.-Ing. Mathias Noe Korreferent: Prof. Dr.-Ing. Martin Doppelbauer Acknowledgement This thesis was written at the Institute for Technical Physics at Karlruhe Institute of Technology and it cannot be finished without the help of my colleugues. I would like to thank my supervisor Prof. Dr.-Ing Mathias Noe, who provides me with the opportunity to pursue my PhD in Karlsruhe Institute of Technology. His continuous support, advice and insight have helped me to reach a higher research level. I highly appreciated the constructive feedback and helpful guaidance given by Prof. Noe at a regular meeting evey two to three weeks during my whole PhD period. In order to ensure the scientific quality of my work, Prof. Noe also encourages me to participate in interna- tional conferences, workshops and seminars, which benefit me a lot. My special gratitude goes to my second referee Prof. Dr.-Ing Martin Doppelbauer for his useful lessons, advice and discussions on electric machines, and the excellent and professional environment he offered to study the iron material properties. Specially, I would like to thank Prof. Doppelbauer for his scientific input and linguistic improve- ments, that helped a great deal to finish the final version of this thesis. I would like to thank my external referee Prof. Jean Lévêque for his scientific and practical comments which help me a lot to improve my thesis. -
Selected High-Temperature Superconducting Electric Power Products
Selected High-Temperature Superconducting Electric Power Products Prototypes are outperforming design goals full-scale utility applications are moving onto the power system and ... Modernizing the Existing Electricity Infrastructure Superconductivity Program for Electric Systems•• Office of Power Delivery U.S. Department of Energy January 2000 HIGH TEMPERATURE SUPERCONDUCTING POWER PRODUCTS CAPTURE THE ATTENTION OF UTILITY ENGINEERS AND PLANNERS Soon superconductors could be so common that we will drop the “super” and refer to them simply as conductors Critical Role of Wire The application of superconductors to electric power systems has been pursued for more than 30 years. This persistence is starting to pay off and utilities that once politely acknowledged the long-term potential of superconducting applications are now paying close attention to several prototype devices that are being tested or are nearing testing on utility systems. What has prompted this interest is the development of electric wires that become superconducting when cooled to the affordable operating-temperature realm of liquid nitrogen as well as the development of coils, magnets, conductors, and machines and power components made with these wires. Superconducting wires have as much as 100 times the current carrying capacity as (Courtesy of American Superconductor Corp.) ordinary conductors. Flexible HTS conductors promise reduced A Real Need operating costs and many other benefits when incorporated into electric power devices. They can change the way power is managed and The timing is right for superconducting solutions consumed. to emerging business problems. Power generation and transmission equipment is aging and must be replaced. Environmental considerations are increasing. Utilities are changing the way they evaluate capital investments. -
Protection of Superconducting Magnet Circuits
Protection of superconducting magnet circuits M. Marchevsky, Lawrence Berkeley National Laboratory M. Marchevsky – USPAS 2017 Outline 1. From superconductor basics to superconducting accelerator magnets 2. Causes and mechanisms of quenching 3. Quench memory and training 4. Detection and localization of quenches 5. Passive quench protection: how to dump magnet energy 6. Active protection: quench heaters and new methods of protection (CLIQ) 7. Protection of a string of magnets. Hardware examples. 8. References and literature M. Marchevsky – USPAS 2017 Discovery of superconductivity H. K. Onnes, Commun. Phys. Lab.12, 120, (1911) M. Marchevsky – USPAS 2017 A first superconducting magnet Lead wire wound coil Using sections of wire soldered together to form a total length of 1.75 meters, a coil consisting of some 300 windings, each with a cross-section of 1/70 mm2, and insulated from one another with silk, was wound around a glass core. Whereas in a straight tin wire the threshold current was 8 A, in the case of the coil, it was just 1 A. Unfortunately, the disastrous effect of a magnetic field on superconductivity was rapidly revealed. Superconductivity disappeared when field Leiden, 1912 reached 60 mT. H. Kamerlingh Onnes, KNAWProceedings 16 II, (1914), 987. Comm. 139f. Reason: Pb is a “type-I superconductor”, where magnetic destroys superconductivity at once at Bc=803 G. Note: this magnet has reached 74% of its “operational margin” ! M. Marchevsky – USPAS 2017 First type-II superconductor magnet 0.7 T field George Yntema, Univ. of Illinois, 1954 • The first successful type-II superconductor magnet was wound with Nb wire It was also noted that “cold worked” Nb wire yielded better results than the annealed one… But why some superconductors work for magnets and some do not? And what it has to do with the conductor fabrication technique? M. -
Sn and Ti DIFFUSION, PHASE FORMATION, STOICHIOMETRY, and SUPERCONDUCTING PROPERTIES of INTERNAL-Sn-TYPE Nb3sn CONDUCTORS
Sn AND Ti DIFFUSION, PHASE FORMATION, STOICHIOMETRY, AND SUPERCONDUCTING PROPERTIES OF INTERNAL-Sn-TYPE Nb3Sn CONDUCTORS A Thesis Presented in Partial Fulfillment of the Requirements for The Degree of Master of Science in the Graduate School of the Ohio State University By Rakesh Kumar Dhaka, B. Tech. ***** The Ohio State University 2007 Masters Examination Committee Professor Mike Sumption, Adviser Professor John Morral, Adviser Professor Katharine Flores ABSTRACT In the present work the diffusion of Sn through the interfilamentary matrix within a subelement and the formation of the associated Cu-Sn intermetallics were observed experimentally for several different Nb3Sn internal-Sn type strands during the pre- reaction part of the heat treatment. An analytical-based model was then developed to determine the time and temperature dependence of Sn-diffusion through the Cu matrix of Nb3Sn subelements. The output of the model is in the form of radial positions of , and phases as a function of time during pre-reaction heat treatment process. These predicted radial positions can be used to determine the optimum heat treatment parameters. The model was then compared to the experimental results. Experimental results for Ti-bearing superconductor strands were also discussed. Following the pre-reaction heat treatment studies, the effects of Titanium doping in presence of Tantalum on the kinetics of Nb3Sn formation and superconducting properties of internal-tin type strands were examined. A series of internal-tin type Nb3Sn sublements which had Nb-7.5wt%Ta filaments and various levels of Ti doping were investigated. Titanium was introduced into the Sn core of the subelements such that the core contained 0 at% to 2.8 at% Ti before reaction. -
Superconducting Magnets for Fusion
Magnets and magnetic materials Superconducting magnets for fusion The ITER's mission is to prove that magnetic confinement fusion will be a candidate source of energy by the second half of the twenty-first century. The tokamak, which is scheduled to begin operations in 2016 at the Cadarache site in the Bouches-du-Rhône, represents a key step in the development of a current-generating fusion reactor. ITER Considerable expertise acquired through its partnership with Euratom on the Tore Supra project has led the CEA to play a central role in the Overview of the magnetic design and development of the three field system equipping the ITER reactor. giant superconducting systems that will generate the intense magnetic fields vital to plasma confinement and stabilisation. he magnetic confinement fusion of thermo- magnetic field system comprises three giant super- Tnuclear plasmas requires intense magnetic fields. conducting systems: the toroidal magnetic field sys- The production of these magnetic fields in the large tem (TF), the poloidal magnetic field system (PF), and vacuum chamber (837 m3) of the ITER International the central solenoid (CS); Focus B, Superconductivity Thermonuclear Experimental Reactor, currently being and superconductors, p. 16. It could be said to repre- built at the Cadarache site in the Bouches-du-Rhône sent the backbone of the tokamak (Figure 1). is in itself a major technological challenge. The ITER's Superconductivity for fusion applications Up to the early 1980s, all magnetic confinement machines relied on resistive magnets, which were CS system generally built using silver-doped copper in order to TF system improve their mechanical properties. -
Superconducting Magnets for Accelerators Lecture
Superconductivity for accelerators - why bother? Abolish Ohm's Law • no power consumption (although do need refrigeration power) • high current density compact windings, high gradients • ampere turns are cheap, so don’t need iron (although often use it for shielding) Consequences • lower power bills • higher magnetic fields mean reduced bend radius smaller rings reduced capital cost new technical possibilities (eg muon collider) • higher quadrupole gradients higher luminosity Martin Wilson Lecture 1 slide 1 JUAS February 2013 Plan of the Lectures 1 Introduction to Superconductors 4 Quenching and Cryogenics • critical field, temperature & current • the quench process • superconductors for magnets • resistance growth, current decay, temperature rise • manufacture of superconducting wires • quench protection schemes • high temperature superconductors HTS • cryogenic fluids, refrigeration, cryostat design 2 Magnetization, Cables & AC losses 5 Practical Matters • superconductors in changing fields • filamentary superconductors and magnetization • LHC quench protection • coupling between filaments magnetization • current leads • why cables, coupling in cables • accelerator magnet manufacture • AC losses in changing fields • some superconducting accelerators 3 Magnets, ‘Training’ & Fine Filaments Tutorial 1: Fine Filaments • coil shapes for solenoids, dipoles & quadrupoles • how filament size affects magnetization • engineering current density & load lines Tutorial 2: Quenching • degradation & training minimum quench energy • current decay -
High Performance Magnesium Diboride (Mgb ) Superconductors
High Performance Magnesium Diboride (MgB2) Superconductors: Towards the Prospect for Commercialization M.S.A. Hossain (ARC DECRA Fellow) The Australian National University– 16/04/2014 Research Programs at ISEM/AIIM Faculty . Applied Superconductivity Group • Bulk • Wire • Tape • Cable • Thin Film . Energy Storage Group . Spintronics and Electronic Materials Group . Thin Film Technology Group . Terahertz Science, Solid State Physics Group . Nanostructure Materials Group . Advanced Photovoltaic Materials Group ISEM Performance Profile highlight ISEM Team: 40 research staff (12 ARC fellows) and more than 80 PhD Seven research program centred on energy and electronics Electrification Program leader in Automotive CRC 2020 More than 50% citations in Li ion battery and superconductivity from ISEM in Australia ISEM is ranked at first place in magnesium diboride supercondcutors and eighth place in Li ion battery research in terms of outputs since 2001 105 PhD graduates widely spread across five continents since 1994 50 ARC fellowship awards to ISEM since 1995 80 ARC projects since 2000 12% publications, 15% ARC funding and 24% citations of UoW are from ISEM $80m for building & $20m for facilities for research infrastructure Member of CoE, ANFF and Flagship Bao Steel Joint Centre with other 3 Universities; Network with more than 50 institutions world-wide Strong links with more than 10 industry partners ERA assessment ranked at 5 for materials engineering, materials chemistry, physical chemistry and interdisciplinary engineering of UOW Superconductivity? Applications • Making a good superconducting product is a formidable interdisciplinary problem Wire cost Wire performance Engineering Cryogenics MgB2 Very simple crystal structure Very high current densities Polycristalline materials observed in films carry large currents Moderately high Tc Tc of 39K Factor of 10 larger than in bulks; room for large improvement in wires still available from R&D MgB2 presents very Good mechanical properties Potentially high critical field 60 1.2 promising features Sample No. -
Mechanical Design and Construction of Superconducting E-Lens Solenoid Magnet System for RHIC Head-On Beam-Beam Compensation
1PoCB-08 1 Mechanical Design and Construction of Superconducting e-Lens Solenoid Magnet System for RHIC Head-on Beam-Beam Compensation M. Anerella, W. Fischer, R. Gupta, A. Jain, P. Joshi, P. Kovach, A. Marone, A. Pikin, S. Plate, J. Tuozzolo, P. Wanderer Abstract —Each 2.6-meter long superconducting e-Lens magnet assembly consists of a main solenoid coil and corrector coils mounted concentric to the axis of the solenoid. Fringe field and “anti-fringe field” solenoid coils are also mounted coaxially at each end of the main solenoid. Due to the high magnetic field of 6T large interactive forces are generated in the assembly between and within the various magnetic elements. The central field uniformity requirement of ± 0.50% and the strict field straightness requirement of ± 50 microns over 2.1 meters of length provide additional challenges. The coil construction details to meet the design requirements are presented and discussed. The e-Lens coil assemblies are installed in a pressure vessel cooled to 4.5K in a liquid helium bath. The design of the magnet adequately cools the superconducting coils and the power leads using the available cryogens supplied in the RHIC tunnel. The mechanical design of the magnet structure including thermal considerations is also presented. Index Terms —Accelerator, electron lens, solenoids, superconducting magnets. Fig. 1. Longitudinal section view of e-Lens solenoid II. MAIN SOLENOID DESIGN I. INTRODUCTION The main solenoid design is comprised of eleven “double To increase the polarized proton luminosity in RHIC, a layers” of rectangular monolithic conductor, 1.78 mm wide superconducting electron lens (e-Lens) magnet system is being and 1.14 mm tall, with a 3:1 copper to superconductor ratio. -
Superconductors: the Next Generation of Permanent Magnets
1 Superconductors: The Next Generation of Permanent Magnets T. A. Coombs, Z. Hong, Y. Yan, C. D. Rawlings fault current limiters, bearings and motors. Both fault current Abstract—Magnets made from bulk YBCO are as small and as limiters and bearings are enabling technologies and a great compact as the rare earth magnets but potentially have magnetic deal of successful research has been devoted to these areas[4- flux densities orders of magnitude greater than those of the rare 8]. With motors, though, we are seeking to supplant an earths. In this paper a simple technique is proposed for existing and mature technology. Therefore the advantages of magnetising the superconductors. This technique involves repeatedly applying a small magnetic field which gets trapped in superconductors have to be clearly defined before the superconductor and thus builds up and up. Thus a very small superconducting motors can become widely accepted. magnetic field such as one available from a rare earth magnet The principle advantages of a superconducting motor or can be used to create a very large magnetic field. This technique generator are size, weight and efficiency. Which of these is which is applied using no moving parts is implemented by the most important depends on the application. In a wind generating a travelling magnetic wave which moves across the turbine for example power to weight ratio is paramount. Any superconductor. As it travels across the superconductor it trails flux lines behind it which get caught inside the superconductor. weight in the nacelle has to be supported and considerable With each successive wave more flux lines get caught and the savings can be made if the machine is lighter especially if it field builds up and up.