Preparation of Papers for AIAA Journals
Total Page:16
File Type:pdf, Size:1020Kb
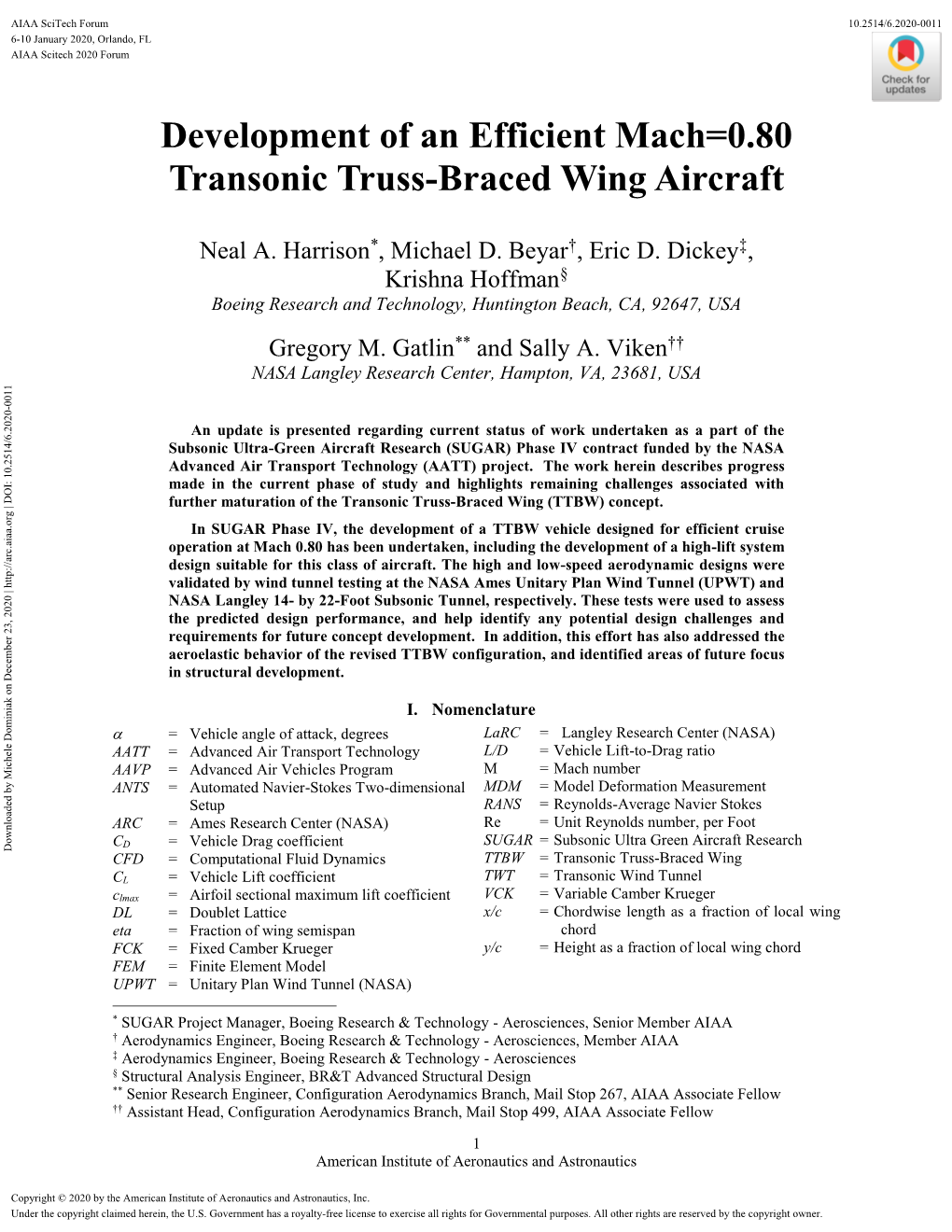
Load more
Recommended publications
-
Hangar 9 Ultimate Manual
TM® WE GET PEOPLE FLYING 46% TOC Ultimate 10-300 ASSEMBLY MANUAL Specifications Wingspan ..........................................................................................100 in (2540 mm) Length ................................................................................................110 in (2794 mm) Wing Area.........................................................................................3310 sq in (213.5 sq dm) Weight ...............................................................................................40–44 lb (18–20 kg) Engine.................................................................................................150–200cc gas engine Radio ..................................................................................................6-channel w/15 servos Introduction Thank you for purchasing the Hangar 9® 46% TOC Ultimate. Because size and weight of this model creates a higher degree for potential danger, an added measure of care and responsibility is needed for both building and flying this or any giant-scale model. It’s important that you carefully follow these instructions, especially those regarding hinging and the section on flying. Like all giant-scale aerobatic aircraft, the Hangar 9® TOC Ultimate requires powerful, heavy-duty servos. Servos greatly affect the flight performance, feel and response of the model. To get the most out of your Ultimate, it’s important to use accurate, powerful servos on all control surfaces. In the prototype models, we used JR 8411 digital servos with excellent -
Aircraft Circular No. 103
NATIONAL ADVISORY COifuciITTEE FOR AERONAUTICS. AIRCRAFT CIRCULAR NO. 103. THE BRISTOL II BULLDOG" (BRITISH)* - A Single-seat All-Steel Fighter. The Bristol "Bulldog" was designed on the Bristol princi ples of metal construction by The Bristol Aeroplane Co., Ltd. The entire structural portion is of high tensile steel (Figs. 1, 2, and 3). The airplane is powered with the IIBristolll Jupiter radial air-cooled engine, either the "Bristolll Jupiter Series VII supercharged engine, when exceptional. speed and performance at high altitudes are espeGially required, or the IIBristol" Jupiter Series VI.A engine when the normal operating area of the airplane is not expected to exceed, say, 15,000 feet. The two types of engine are entirely interchangeable when desired. The speeds maintained at altitudes with the rate of climb. and the ceiling are given in tables at conolusion of this Circular. Fu s e I age The fuselage structure comprises three ·main parts, the front and rear portions and the stern frrune. Of these, the front ~or tion and the stern frame are constructed of high tensile tubes and the rear portion of members built up of high tensile steel str ip in special "Bristolll sections. Front end.- This portion extends from the front bulkhead *From circular issued by The Bristol Aeroplane Co., Ltd., England. N.A.C.A. Aircraft Circular No. 103 2 to the end of the tubular longerons, and acc~mmodates the pilot1s seat, controls lli~d most of the military equipment, etc. No bracing wires are fitted in the side frames and transverse brac ing is fitted only in the foremost panel. -
Aircraft Circulaels National Advisory Committee For
AIRCRAFT CIRCULAELS NATIONAL ADVISORY COMMITTEE FOR AERONAUTICS No 119 THE AVRO TRAINER AIBPLAE (ERI T IS H) A Training Biplane Washington June, 1930 NATIONAL ADVISORY COlvilvITTEE FOR AERONAUTICS. AIRCRAFT CIRCULAR NO. 119. THE "AVRO TRAINER" AIRPLANE (BRITIsH)* A Training Biplane. Although the "Trainer" has scarcely a single dimension in common with the "504," the "family likeness" is quite striking. The two most marked changes are: the different shape of the rudder and the different landing gear. This airplane is primarily intended for training purposes and the requirements of -training have quite obviously been kept prominently in view throughout the design. Large, comfortable cockpits, good view, effective windshields, wide track are some of the features (Figs. 1, 3, 4) of the "Trainer." Constructional Features One of the innovations introduced in the "Avro Trainer" is that it is of all-metal construction (with exception of the fabric covering and the wooden fairings of the fuselage) in order to conform to thb requirements of the Air Ministry. In the tt Trainer" fuselage the modern form of Avro welded tube construction is employed (Figs. 5,6). Uniform stress is not easy of attainment in any aIrcraft structure, and the welded tube fuselage is no exception. In the "Trainer," however, an approach towards it has been made , by *From Flight, My 2, 1930. N.A.C.A. Aircraft Circular No. 119 2 having the longerons of thee different diameters, largest in front, medium from cockpits to about halfway towards the tail, and smallest in the tail end. The smaller tube is inserted a short distance into the larger, and the joint is then welded. -
A Design Study of a Proposed Four-Seat, Amateur-Built Airplane
University of Tennessee, Knoxville TRACE: Tennessee Research and Creative Exchange Masters Theses Graduate School 8-2003 A Design Study of a Proposed Four-Seat, Amateur-Built Airplane D. Andrew Moore University of Tennessee - Knoxville Follow this and additional works at: https://trace.tennessee.edu/utk_gradthes Part of the Mechanical Engineering Commons Recommended Citation Moore, D. Andrew, "A Design Study of a Proposed Four-Seat, Amateur-Built Airplane. " Master's Thesis, University of Tennessee, 2003. https://trace.tennessee.edu/utk_gradthes/2113 This Thesis is brought to you for free and open access by the Graduate School at TRACE: Tennessee Research and Creative Exchange. It has been accepted for inclusion in Masters Theses by an authorized administrator of TRACE: Tennessee Research and Creative Exchange. For more information, please contact [email protected]. To the Graduate Council: I am submitting herewith a thesis written by D. Andrew Moore entitled "A Design Study of a Proposed Four-Seat, Amateur-Built Airplane." I have examined the final electronic copy of this thesis for form and content and recommend that it be accepted in partial fulfillment of the requirements for the degree of Master of Science, with a major in Mechanical Engineering. Dr. Gary Flandro, Major Professor We have read this thesis and recommend its acceptance: Dr. Louis Deken, Dr. Peter Solies Accepted for the Council: Carolyn R. Hodges Vice Provost and Dean of the Graduate School (Original signatures are on file with official studentecor r ds.) To the Graduate Council: I am submitting herewith a thesis written by D. Andrew Moore entitled “A Design Study of a Proposed Four-Seat, Amateur-Built Airplane.” I have examined the final electronic copy of this thesis for form and content and recommend that it be accepted in partial fulfillment of the requirements for the degree of Master of Science, with a major in Mechanical Engineering. -
Explanatory Note to TCDS IM.A.120 – Boeing 737 Issue 11
Explanatory Note to TCDS IM.A.120 – Boeing 737 Issue 11 This annex to the EASA TCDS IM.A.120 was created to publish selected special conditions / deviations / equivalent safety findings that are part of the applicable certification basis: Table of Contents: Certification Review Items: A-10: Additional requirements for import ...........................................................................................3 A. 11-02: Pressurised Cabin Loads ......................................................................................................5 A. 11-04: Emergency Landing Dynamic Loads ...................................................................................6 A. 11-05: Fatigue and Damage Tolerance ............................................................................................7 A. 11-06: Fasteners ...............................................................................................................................9 A. 11-08: Lift and Drag Device Indicator ..........................................................................................10 A. 11-11: Doors ..................................................................................................................................11 A. 11-12: Seat, Berths, Safety Belts and Harness ..............................................................................12 A. 11-13: Direct view and cabin attendant seat ..................................................................................13 A. 11-16: Equipment Systems and Installations ................................................................................14 -
Aviation Transportation Safety Investigation Report A18O0106
Air Transportation Safety Investigation Report A18O0106 IN-FLIGHT SEPARATION OF RIGHT WING Quad City Challenger II (advanced ultralight), C-IGKT North Bay, Ontario, 14.3 nm E 30 July 2018 History of the flight On 29 July 2018, 2 privately operated Quad City Ultralight Aircraft Corporation (Quad City) Challenger II advanced ultralight aircraft equipped with amphibious floats departed Ottawa/Rockcliffe Airport (CYRO), Ontario, for a daytime visual flight rules cross-country flight to North Bay Airport (CYYB), Ontario. While en route, the 2 aircraft encountered strong winds and turbulence, and the pilots decided to land on the Ottawa River, near Mattawa, Ontario. During the landing, the occurrence aircraft (registration C-IGKT, serial number CH2-1199-1919) touched down hard. After a short lunch break, the pilots inspected the 2 aircraft and then flew to CYYB without further incident. On 30 July 2018, the 2 aircraft departed CYYB at 09321 and climbed to between 1800 and 2000 feet above sea level for the return flight to CYRO. At approximately 0950, the occurrence aircraft’s right wing separated from the aircraft when it was over Talon Lake, Ontario, 14.3 nautical miles east of CYYB. The aircraft entered an uncontrolled descent and collided with terrain in a wooded area. A post- impact fire ensued. The pilot was fatally injured. The aircraft was destroyed by impact forces and the post-impact fire. The pilot of the other aircraft overflew the occurrence site and landed on Talon Lake. At 0959, he met a local resident, who called 911 to report the accident. There was no emergency locator transmitter on board, and none was required by regulations. -
Conceptual Design of a Strut-Braced Wing Configuration
22 June2017 Aviation on Sustainable UTIAS NationalColloquium Bombardier Aerospace Engineering,Product Development Advanced Design Specialist Engineering Graham Potter Configuration Strut-Braceda Wing Conceptual Design of PRIVATE AND CONFIDENTIAL © Bombardier Inc. or its subsidiaries. All rights reserved. Environmentally Focused Aircraft Study Environmentally Focused 2 § § § Aircraft requirements: Technology assumption: Environmentally Focused Aircraft (EFA) study objective: § § § EIS Based on existing Bombardier products Consistent with EIS 2030-2035 by evaluating alternative long-rangeSignificantly business jet reduce and environmental commercial impact aircraft configurations (emissions, local air quality and community noise) Entry-Into-Service Business Jet Commercial Aircraft PRIVATE AND CONFIDENTIAL © Bombardier Inc. or its subsidiaries. All rights reserved. The History of the Strut-Braced Wing 3 Hurel-Dubois HD.31 Hurel-Dubois Shorts 360 Hurel-Dubois HD.31 Cessna Caravan PRIVATE AND CONFIDENTIAL © Bombardier Inc. or its subsidiaries. All rights reserved. Recent Research Efforts Research Recent 4 Boeing/NASA Boeing/NASA Virginia Tech Virginia ONERA PRIVATE AND CONFIDENTIAL © Bombardier Inc. or its subsidiaries. All rights reserved. WhyStrut-Braced a Configuration? 5 § § § § configuration equivalent conventional burn savings compared to Other studies suggest 5-10% fuel induced drag ratios with large reductionsin to Allows optimization higher aspect given aspect ratio allows reducedwingweightata Strut-braced configuration wing and drag compromiseweight between wing Optimum aspect ratio wing is a Wing Weight Aspect Ratio PRIVATE AND CONFIDENTIAL © Bombardier Inc. or its subsidiaries. All rights reserved. WhyStrut-Braced a Configuration? 6 § Start witha geometryconventional wing PRIVATE AND CONFIDENTIAL © Bombardier Inc. or its subsidiaries. All rights reserved. WhyStrut-Braced a Configuration? 7 § § Add astrut Start witha geometryconventional wing WING WEIGHT FUEL BURN PROFILE DRAG PRIVATE AND CONFIDENTIAL © Bombardier Inc. -
2021-20201020010 Date: June 29, 2021
No.: 2021-20201020010 Date: June 29, 2021 http://www.faa.gov/aircraft/safety/programs/sups/upn AFFECTED PRODUCTS Single engine service kits are being manufactured by Robair for installation on type- certificated products. The kits are applicable to Cessna/Textron Aviation Inc. (Cessna) airplane model numbers listed in Airworthiness Directive (AD) 2020-18-01. The AD identifies the fuselage bulkhead is prone to cracking at the wing strut fuselage attach point. The AD specifies if cracks are discovered, the Cessna Single Engine Service Kit must be installed. The Cessna Single Engine Service Kit reinforces the fuselage bulkhead at the wing strut fuselage attach point. The table below lists the applicable kit part numbers: Nomenclature Robair/Cessna Part Number Cessna Single Engine Service Kit SK182-115 Cessna Single Engine Service Kit SK206-42C Cessna Single Engine Service Kit SK206-42D Cessna Single Engine Service Kit SK207-19 Cessna Single Engine Service Kit SK207-19A Cessna Single Engine Service Kit SK210-156 The Cessna Single Service Kits produced by Robair are not part marked nor serialized. PURPOSE This notification advises all aircraft owners, operators, manufacturers, maintenance organizations, parts suppliers and distributors regarding the unapproved status of Cessna Single Engine Service Kits produced and sold by Robair Repair LLC without Federal Aviation Administration (FAA) production approval. BACKGROUND Information received during an FAA Suspected Unapproved Parts (SUP) investigation conducted on December 9, 2020, that Robair Repair LLC located at 6381 NW Aileron Ct, Silverdale, Washington, 98383, is manufacturing Cessna Single Engine Service Kits. Robair Repair LLC has been selling them new without FAA Parts Manufacturing Approval (PMA). -
Nasa Tn 0-5971 Longitudinal Aerodynamic
NASA TECHNICAL NOTE NASA TN 0-5971 P_ I Z COPy Z LONGITUDINAL AERODYNAMIC CHARACTERISTICS OF A TWIN-TURBOFAN SUBSONIC TRANSPORT WITH NACELLES MOUNTED UNDER THE WINGS by Francis J. Capone Langley Research Center Hampton, Va. 23365 NATIONALAERONAUTICSAND SPACEADMINISTRATION• WASHINGTON,D. C. ° OCTOBER1970 1, Report No, 2, Government Accession No. 3, Recipient's Catalog No. NASA TN D-5971 4, Title and Subtitle 5. Report Date LONGITUDINAL AERODYNAMIC CHARACTERISTICS OF A October 1970 TWIN-TURBOFAN SUBSONIC TRANSPORT WITH NACELLES 6. Performing Organization Code MOUNTED UNDER THE WINGS 7. Author(s) 8. Performing Organization Report No. Francis J. Capone L-7141 10. Work Unit No. 9. Performing Organization Name and Address 737-01-10-03 NASA Langley Research Center 11. Contract or Grant No Hampton, Va. 23365 13, Type of Report and Period Covered 12. Sponsoring Agency Name and Address Technical Note National Aeronautics and Space Administration 14. Sponsoring Agency Code Washington, D.C. 20546 15. Supplementary Notes 16. Abstract An investigation has been conducted in the Langley 16-foot transonic tunnel to deter- mine the longitudinal aerodynamic characteristics of a 0.062-scale, twin-turbofan subsonic transport at Mach numbers from 0.55 to 0.85 and angles of attack from about -2 ° to 6 °. The Reynolds number based on wing mean aerodynamic chord varied from 2.25 × 106 to 2.70 × 106. The effects of model-component buildup, horizontal-tail effectiveness, boundary- layer transition, and wing and nacelle modifications were measured. The model was mounted by using a sting-strut arrangement with the strut entering the model through the underside of the fuselage approximately 65 percent of the fuselage length rearward of the model nose. -
Aircraft Circulars National Advisory Co}Ittee for Aeronautics
AIRCRAFT CIRCULARS NATIONAL ADVISORY CO}ITTEE FOR AERONAUTICS No. 21 THE A.N.E.C. IV "1ISSEL THRUSH" LIGHT AI&NE From "Flight," September 9, 1926 Washington November, 1926 NATIONAL ADVISORY COMMITTEE FOR AERONAUTICS. AIRCRAFT CIRCULAR NO. 21. THE A.N.E.C. IV "MISSEL THRUSH" LIGHT AIRPLANE.* In-the "Missel Thrush" the Air Navigation and Engineering Co., Ltd., have produced an entirely new type of light airplane,, having not only high efficiency but very comfortable accommoda- tions for pilot and passenger when making long flights. In short, it is an attemp t to produce an inexpensive comfortable efficient and safe airplane, suitable for private ownership and operation. It is a two-seater tractor fuselage biplane, with single I interplane struts and is, as may be seen from Figs. I and 2, an exceptionally retty and well-proportioned airplane. While, generally speaking, the construction of the "Missel Thrush" is a perfectly straightforward job, following orthodox practice, and in consequence permitting one of the main aims of the con- structors to be accomplished, viz., cheap and quantity produc- tion, its detail design is not lacking in originality. Great simplicity is the keynote eveywhere. Furthermore, this simplicity has not by any means been achieved by sacrificing strength, and this applies also in re- spect to the light weight obtaining throughout this airplane, another outstanding feature. * From "Flight," September 9, 1926. N.A.C.A. Aircraft Circular Noii 21 2 Constructional Features Turning to actual construction, it will not be possible, owing to lack of space, to describe every detail but to limit the description, briefly, to the more noteworthy features. -
300/-400/-500 Series Flammable Material Locations
AIRPLANE RESCUE AND FIRE FIGHTING INFORMATION 737-100/-200/-300/-400/-500737 (tab) SERIES FLAMMABLE MATERIAL LOCATIONS 390/492/984 GAL - 1476/1862/3725 L 1 WINGLETS (AS INSTALLED) OPTIONAL AUXILIARY FUEL TANK IN LWR AFT CARGO COMPARTMENT VENT SURGE TANK SYSTEM A, B AND STANDBY HYDRAULIC RESERVOIRS IN WHEEL WELL AUXILIARY POWER UNIT OIL TANK FUEL TANK No. 2 PORTABLE OXYGEN BOTTLES LOCATION VARIES THROUGHOUT 1499 GAL - PASSENGER CABIN 5674 L APU FUEL LINE APU EMERGENCY CONTROL PANEL LOCATED IN THE RIGHT WHEEL WELL AREA 1 HYDRAULIC BRAKE ACCUMULATORS CREW OXYGEN BOTTLE IN WHEEL WELL FWD CARGO AREA 2313 GAL - 8755 L FUEL TANK No. 1 VENT SURGE TANK PASSENGER OXYGEN (OPTIONAL) 1499 GAL - 5674 L PORTABLE OXYGEN BOTTLE BEHIND FIRST OFFICER HOT BRAKES Normal cooling: Move aircraft to a suitable location and allow brakes to cool on their own. Water mist: Can be deployed from turret or handline. CENTER FUEL TANK ENGINE OIL TANK Fans: Placing fans may place firefighters very close to the hazard zone. RIGHT SIDE EACH ENGINE - CFM-56 WHEEL FIRE (LEFT SIDE ALL Apply large amounts of water initially with turrets. Transition to handline application to continue and OTHERS) maintain a cooling effect. Wheels are equipped with fusible plugs designed to melt and deflate the tire when the CAUTION: Rescue crews wearing full PPE to include SCBA’s must use caution when moving across temperature is excessive. sections of aircraft that have been exposed to fatigue or fire as the result of an accident. Crews need to verify the integrity of the surface area before moving their weight and WARNING: Approach landing gear trucks from forward or aft at a 45 degree angle when equipment across it. -
Chapter 11 Transition to Complex Airplanes
Chapter 11 Transition to Complex Airplanes Introduction A high-performance airplane is defined as an airplane with an engine capable of developing more than 200 horsepower. A complex airplane is an airplane that has a retractable landing gear, flaps, and a controllable pitch propeller. In lieu of a controllable pitch propeller, the aircraft could also have an engine control system consisting of a digital computer and associated accessories for controlling the engine and the propeller. A seaplane would still be considered complex if it meets the description above except for having floats instead of a retractable landing gear system. 11-1 i ii Tapered Delta Sweptback Figure 11-1. Airfoil types. Transition to a complex airplane, or a high-performance axis. Wing flaps acts symmetrically about the longitudinal airplane, can be demanding for most pilots without previous axis producing no rolling moment; however, both lift and drag experience. Increased performance and complexity both increase as well as a pitching moment about the lateral axis. require additional planning, judgment, and piloting skills. Lift is a function of several variables including air density, Transition to these types of airplanes, therefore, should be velocity, surface area, and lift coefficient. Since flaps increase accomplished in a systematic manner through a structured an airfoil’s lift coefficient, lift is increased. [Figure 11-3] course of training administered by a qualified flight instructor. As flaps are deflected, the aircraft may pitch nose up, nose Airplanes can be designed to fly through a wide range of down or have minimal changes in pitch attitude. Pitching airspeeds. High speed flight requires smaller wing areas and moment is caused by the rearward movement of the moderately cambered airfoils whereas low speed flight is wing’s center of pressure; however, that pitching behavior obtained with airfoils with a greater camber and larger wing depends on several variables including flap type, wing area.