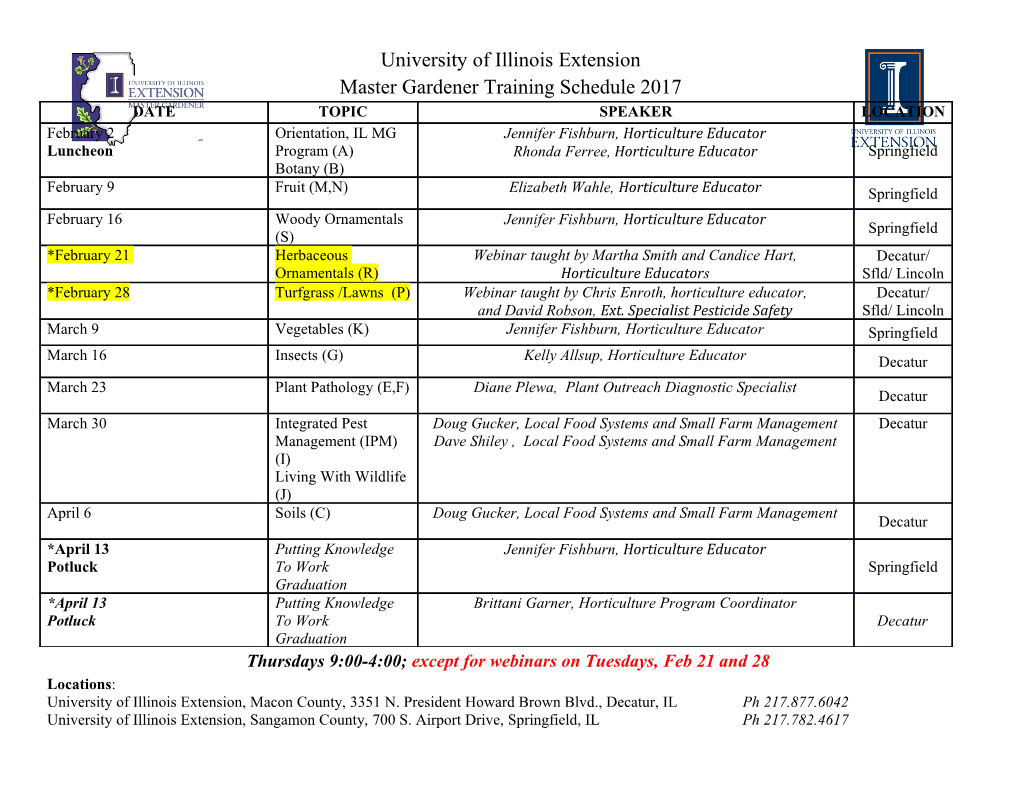
AIAA SciTech Forum 10.2514/6.2020-0011 6-10 January 2020, Orlando, FL AIAA Scitech 2020 Forum Development of an Efficient Mach=0.80 Transonic Truss-Braced Wing Aircraft Neal A. Harrison*, Michael D. Beyar†, Eric D. Dickey‡, Krishna Hoffman§ Boeing Research and Technology, Huntington Beach, CA, 92647, USA Gregory M. Gatlin** and Sally A. Viken†† NASA Langley Research Center, Hampton, VA, 23681, USA An update is presented regarding current status of work undertaken as a part of the Subsonic Ultra-Green Aircraft Research (SUGAR) Phase IV contract funded by the NASA Advanced Air Transport Technology (AATT) project. The work herein describes progress made in the current phase of study and highlights remaining challenges associated with further maturation of the Transonic Truss-Braced Wing (TTBW) concept. In SUGAR Phase IV, the development of a TTBW vehicle designed for efficient cruise operation at Mach 0.80 has been undertaken, including the development of a high-lift system design suitable for this class of aircraft. The high and low-speed aerodynamic designs were validated by wind tunnel testing at the NASA Ames Unitary Plan Wind Tunnel (UPWT) and NASA Langley 14- by 22-Foot Subsonic Tunnel, respectively. These tests were used to assess the predicted design performance, and help identify any potential design challenges and requirements for future concept development. In addition, this effort has also addressed the aeroelastic behavior of the revised TTBW configuration, and identified areas of future focus in structural development. I. Nomenclature = Vehicle angle of attack, degrees LaRC = Langley Research Center (NASA) AATT = Advanced Air Transport Technology L/D = Vehicle Lift-to-Drag ratio AAVP = Advanced Air Vehicles Program M = Mach number ANTS = Automated Navier-Stokes Two-dimensional MDM = Model Deformation Measurement Setup RANS = Reynolds-Average Navier Stokes ARC = Ames Research Center (NASA) Re = Unit Reynolds number, per Foot CD = Vehicle Drag coefficient SUGAR = Subsonic Ultra Green Aircraft Research Downloaded by Michele Dominiak on December 23, 2020 | http://arc.aiaa.org DOI: 10.2514/6.2020-0011 CFD = Computational Fluid Dynamics TTBW = Transonic Truss-Braced Wing CL = Vehicle Lift coefficient TWT = Transonic Wind Tunnel clmax = Airfoil sectional maximum lift coefficient VCK = Variable Camber Krueger DL = Doublet Lattice x/c = Chordwise length as a fraction of local wing eta = Fraction of wing semispan chord FCK = Fixed Camber Krueger y/c = Height as a fraction of local wing chord FEM = Finite Element Model UPWT = Unitary Plan Wind Tunnel (NASA) * SUGAR Project Manager, Boeing Research & Technology - Aerosciences, Senior Member AIAA † Aerodynamics Engineer, Boeing Research & Technology - Aerosciences, Member AIAA ‡ Aerodynamics Engineer, Boeing Research & Technology - Aerosciences § Structural Analysis Engineer, BR&T Advanced Structural Design ** Senior Research Engineer, Configuration Aerodynamics Branch, Mail Stop 267, AIAA Associate Fellow †† Assistant Head, Configuration Aerodynamics Branch, Mail Stop 499, AIAA Associate Fellow 1 American Institute of Aeronautics and Astronautics Copyright © 2020 by the American Institute of Aeronautics and Astronautics, Inc. Under the copyright claimed herein, the U.S. Government has a royalty-free license to exercise all rights for Governmental purposes. All other rights are reserved by the copyright owner. II. Introduction The objective of the NASA Advanced Air Vehicles Program (AAVP) is to advance technologies that show significant potential for revolutionary improvements in aircraft efficiency, emissions, noise, and safety as compared to conventional cantilever-wing aircraft. Within this program, the Advanced Air Transport Technology (AATT) project matures fixed-wing commercial transport technologies that offer the greatest potential to meet these objectives. The AATT project’s target metrics for dramatic reductions in noise, emissions, and fuel consumption as a function of near, mid, and far-term objectives are shown in Figure 1. TECHNOLOGY GENERATIONS TECHNOLOGY Technology Readiness Level = 5/6 BENEFITS Near-Term Mid-Term Far-Term 2015-2025 2025-2035 2035+ Noise 22 – 32 dB 32 – 42 dB 42 – 52 dB (cum below Stage 4) LTO NOx Emissions 70 – 75% 80% >80% (cum below CAEP 6) Cruise NOx Emissions 65 – 70% 80% >80% (rel. to 2005 best in class) Aircraft Fuel/Energy Consumption 40 – 50% 50 – 60% 60 – 80% (rel. to 2005 best in class) Figure 1. NASA Subsonic Transport System-Level Metrics/Goals (1) In December 2016 Boeing was awarded the SUGAR Phase IV contract to continue to investigate the enabling potential of Transonic Truss-Braced Wing (TTBW) technology to help satisfy the NASA objectives. Summaries of the work completed in previous phases of the SUGAR program may be found in open literature (2-6). In SUGAR Phase IV, the goal was to investigate and adapt the TTBW concept to transonic Mach numbers more consistent with today’s commercial transport aircraft. Specifically, the TTBW concept was updated to operate at a cruise Mach number of 0.80. This work began by updating the preliminary Mach 0.80 design completed during SUGAR Phase III, and then extended to a detailed aerodynamic design of the configuration at both high and low-speeds, including the development of a laminar-flow compatible high-lift system. Both the high and low-speed designs underwent aerodynamic validation in a series of wind tunnel tests. The high-speed (transonic) design was tested in the NASA Ames 11-Foot Unitary Plan Wind Tunnel (UPWT) located at Moffett Field, CA beginning in July 2019, while the low-speed design was tested in the NASA Langley Research Center’s 14- by 22-Foot Subsonic Tunnel beginning in September 2019. In addition to aerodynamic development, the updated concept’s structure was investigated. Aero-structural optimization was performed to study the trades between strut structural weight and vehicle aerodynamic performance. This included studies to examine the effect of variation in the location of the jury strut and the impact of using different strut construction materials. A global Finite Element Model (FEM) was constructed and used for updated structural Downloaded by Michele Dominiak on December 23, 2020 | http://arc.aiaa.org DOI: 10.2514/6.2020-0011 sizing and weight estimates based on the revised loads. This design was then assessed for its aeroelastic behavior and performance. In addition, several conceptual designs of key structural joints were investigated. 2 American Institute of Aeronautics and Astronautics III. Design and Test of Mach 0.80 TTBW This paper outlines the tasks and objectives undertaken as a part of the SUGAR Phase IV contract. The primary objectives funded under this study are: 1) Design a TTBW configuration that can operate efficiently at a cruise Mach = 0.80, and validate the high- speed aerodynamic performance in a transonic wind tunnel test. 2) Develop a high-lift system for the TTBW vehicle, and validate the aerodynamic performance in a low-speed wind tunnel test. 3) Develop and compare an advanced tube-and-wing configuration of equivalent technology level to meet the same mission requirements as the TTBW vision vehicle. 4) Identify remaining technical challenges associated with application of TTBW technology to modern commercial aircraft, and develop a roadmap for the continued systematic reduction in risk. The period of performance for Phase IV extended from January 2017 to March 2020. The overall timeline of the SUGAR program, including previous phases of study and key test campaigns is shown in Figure 2. Figure 2. SUGAR Program timeline including key test campaigns As shown above, the SUGAR program has now completed five major wind tunnel tests of the TTBW configuration. The demonstrations began with the non-linear aeroelastics test in the NASA Langley Research Center (LaRC) Transonic Dynamics Tunnel (TDT) in 2013, and was followed by three transonic performance wind tunnel tests at the NASA Ames Research Center (ARC) UPWT. Most recently, a low-speed test was conducted at the NASA Downloaded by Michele Dominiak on December 23, 2020 | http://arc.aiaa.org DOI: 10.2514/6.2020-0011 LaRC 14- by 22-Foot Subsonic Tunnel to investigate the performance of the configuration’s high-lift system. This test, completed in November 2019, represented the first time the TTBW’s high-lift potential was measured in a high- fidelity wind tunnel test. The following sections will describe in more detail the individual design and test efforts that comprised the Phase IV work. A. Mach 0.80 TTBW Configuration Update In SUGAR Phase III a preliminary Mach 0.80 design was created. The new geometry was based on a modification of the Phase III Mach=0.745 vehicle, with changes to wing sweep and airfoil thickness, as well as a rebalancing of the aircraft center of gravity realized by a shift in the wing root and landing gear locations. The wing and strut structural tie-in locations and wing planform were frozen for the study. Spanwise location of the wing-strut interface was maintained at ~58% span. 3 American Institute of Aeronautics and Astronautics Figure 3. Comparison of the M=0.745 Phase III Planform to the Final M=0.80 Phase IV Planform As shown in Figure 3, the most notable difference between the Phase III and IV designs was an ‘unstacking’ of the wing and inboard strut. By shifting the wing root forward the inboard strut no longer laid directly underneath the wing. As a result the aerodynamic interaction between these surfaces was (locally) reduced. The changes to the configuration layout were also found to have several additional positive effects, including: 1) Reduced compressibility drag – the unstacked geometry has a naturally improved vehicle cross-sectional area distribution as compared to the Phase III design. 2) Protection of the inboard strut during high-lift operations – by placing the inboard strut aft of the inboard wing-body attachment it is partially protected from large variations in flow onset angle since the wing acts like a flow-straightener. As a result, the inboard strut is less likely to separate during high-lift operations.
Details
-
File Typepdf
-
Upload Time-
-
Content LanguagesEnglish
-
Upload UserAnonymous/Not logged-in
-
File Pages14 Page
-
File Size-